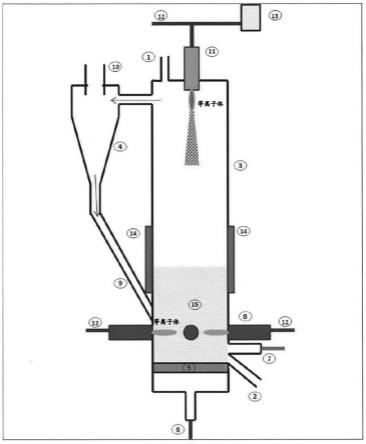
用于添加剂合成的具有复合颗粒的多材料粉末
1.本技术是申请日为2017年09月08日的pct国际专利申请pct/fr2017/052396进入中国国家阶段的中国专利申请号2017800547566、发明名称为“用于添加剂合成的具有复合颗粒的多材料粉末”的分案申请。
技术领域
2.本发明涉及制造用于不同领域(冶金、塑料加工等)用于在添加剂合成技术和喷涂表面处理技术中应用的多材料粉末。
背景技术:3.就本发明而言,术语添加剂合成技术指可以通过粉末的固结获得三维物体的任何技术。具体地,可以作为非限制性实例提及的有:3d打印技术(slm、sls等)、注塑技术(pim、mim)、粉末喷涂技术(冷喷涂、d-枪等)及常规的压实/烧结技术。
4.目前存在作为多材料粉末的不同性质的粉末的混合物或者合金粉末,不同性质的粉末的混合物根据制造方法具有或多或少均匀分散的各组分,而合金粉末中,构成合金粉末的多种元素均呈固溶体和/或确定化合物的形式。用于合成这些粉末的方法是相对来说公知的。
5.尤其,喷涂熔融金属的技术可以获得具有球形形态的致密粉末。但是,通过该技术获得的材料是纯元素,或可混合元素的单相合金,例如,某些钢,镍、铝或者钛的合金。当今这些粉末构成用于添加剂制造应用的多数供给。
6.共研磨(机械合成)技术可通过在高能量下、辅以研磨珠紧密混合不同性质的粉末来制造多材料粉末,诸如美国专利us 3,816,080、us 3,591,362和us 4,706,894中所述。通过该方法,可获得具有宽组成范围的复合颗粒。但是,通过该实施方案获得的粉末的形貌和/或粒径分布不利于其在添加剂制造中的应用。此外,通过该技术获得的颗粒由或多或少均匀分散的各种组分构成且在表面上不具有官能化的核结构。
7.喷雾-干燥技术也可通过喷雾并干燥由粉末、溶剂和有机粘合剂构成的悬浮液来制造多功能粉末,诸如美国专利us 5,122,182、us 3,617,358和us 4,915,733中所述。由此通过悬浮液中存在的元素粉末的起粘合剂作用的有机粘合剂获得来自团聚体的复合颗粒。通过该实施方案获得的颗粒具有球形形貌。但是,颗粒的粒内孔隙以及有机粘合剂的存在使这种颗粒不适用于添加剂制造。对于该实施方案,可在喷雾/干燥操作后增加借助多种技术基于颗粒温度升高的去粘和致密化颗粒的步骤。然后,可以获得足够致密且呈球形的复合颗粒,该复合颗粒可以用于喷涂表面处理方法或添加剂合成制造方法。但是,由此获得的颗粒为由非均匀分散的各种组分形成的团聚体且不具有表面上的官能化的核结构。
8.此外,干燥沉积技术,诸如化学气相沉积(通常用首字母缩略词cvd命名)或物理气相沉积(通常用首字母缩略词pvd命名),也可用在用于合成多材料粉末的颗粒状基质上。然后,这些技术通常与可以实施使颗粒状基质处于运动中的装置(诸如流化床、旋转反应腔或震动板)的方法结合,诸如美国专利us 7,632,355中具体教导的。用这些方法可在颗粒表面
获得沉积物。pvd技术高度受限,原因在于,pvd技术不能对细颗粒(直径小于100μm的颗粒)进行处理。对于这些合理的处理时间pvd技术在官能化速度方面也高度受限。如果考虑毒性及所用前体的成本,在多数情况下,cvd技术在技术上或在经济方面不具有优点。
9.最后,可通过如美国专利us 6,732,345、us 5,064,463和us 4,309457中所提及的湿化学沉积对担体颗粒进行表面处理来制造多材料颗粒。这种情况下,在颗粒表面可获得沉积物。但是,这些实施方案产生大量的对环境有害的排放且需要使用昂贵且危险的化学试剂,这使这些合成路径的工艺发展大大复杂化。这些技术可在颗粒尺度上联结不同材料。
10.但是,可能需要在颗粒尺度上不同材料联结的粉末,以实现并便于多种合金、假合金、复合物和金属陶瓷的制造。
技术实现要素:11.为此,申请人发明了一种可通过用颗粒状形式的添加剂元素来官能化颗粒或者担体颗粒的表面以获得复合颗粒从而获得层(strata)中的微观结构的方法。
12.能够拥有这样的复合颗粒的优点是多方面的:
[0013]-便于其实施,通过避免担体元素和添加剂元素的简单混合(不是用添加剂元素官能化担体元素),这种简单混合通常在储存和使用期间产生均匀性和偏析的问题,因为在颗粒尺度上获得组合物;
[0014]
显著提高材料的均匀性及用于形成这些粉末的方法的再现性;
[0015]
阻止粒内孔隙并获得由这些官能化颗粒制造的材料的特定优点微观结构;
[0016]
例如,通过具有低熔点的官能化颗粒官能化具有高熔点的担体颗粒,便于液相中的烧结过程和的扩散动力学。该实施方案特别适合于金属陶瓷的制造,
[0017]
利于固相中的变形过程,以提高喷雾制造的涂层的致密度:可以特别提及冷喷雾的情况,其中易碎的担体颗粒由易延展的担体颗粒官能化,易延展的担体颗粒提供为获得致密且粘着的沉积物所需的塑性变形。
[0018]
更具体地,本发明因此的目的在于,包括具有1μm至100μm的中值粒径分布d50的担体颗粒和具有相对于担体颗粒低10倍至1000倍的中值粒径分布d50的官能化颗粒的多材料粉末,
[0019]
所述粉末的特征在于,所述担体颗粒和所述官能化颗粒形成具有核壳结构的复合颗粒,每个复合颗粒具有:
[0020]
由担体颗粒形成的核,及
[0021]
覆盖10%至100%的担体颗粒的表面且由至少一个表面层的所述官能化颗粒构成的壳。
[0022]
由至少一个表面层的官能化颗粒构成的壳所提供的优点具体在于:
[0023]-一方面,由此形成的复合颗粒的比表面积增加,因而在烧结过程中诱导更好的反应性;
[0024]
–
另一方面,粉末层的表观密度和振实密度的增加有利于添加剂制造中的颗粒融合过程中的快速致密化。
[0025]
本发明中,假设根据本发明的多材料粉末具有数量分布,所要求保护的粒径分布范围对应于给定区间d10-d90。
[0026]
就本发明而言,术语中值粒径分布d50(或中值直径d50)是指50%的颗粒位于该尺寸以下。
[0027]
有利地,官能化颗粒具有大于或等于100nm的中值粒径分布d50,结果是壳具有大于或等于100nm的厚度。官能化颗粒的尺寸特别可以限制在纳米颗粒的使用期间与其毒性相关的卫生及安全问题。
[0028]
优选地,由官能化层覆盖的担体颗粒的比例为0.8至1,优选地,0.9至1。
[0029]
就本发明而言,对于多材料粉末样本,术语覆盖的担体颗粒的比例是指官能化颗粒的数量与总颗粒的数量的比例。该比例通过分析用显微镜拍摄的多材料颗粒的多个图像来确定。
[0030]
覆盖的担体颗粒的比例大于0.9所提供的优点与在颗粒尺度上微观结构的均匀性有关。这确保担体颗粒确实全被以同样的方式官能化。该特征直接影响由粉末获得的材料的微观结构缺陷的不存在,因此也对其性能有直接影响;这也为其特征的重现性提供了严格的保证。
[0031]
优选地,在颗粒尺度上官能化层的表面的总粗糙度rt小于10μm,优选地为0.1μm至5μm。
[0032]
粗糙表面通常包含被称为“峰”的表面微凸体和被称为“凹陷”的空腔。
[0033]
就本发明而言,术语总粗糙度rt指峰的最高点顶面和凹陷的最低底部间的最大落差。
[0034]
在颗粒尺度上官能化层的总粗糙度通过分析用显微镜拍摄的颗粒的截面图来确定。
[0035]
在颗粒尺度上官能化层的总粗糙度小于10μm所提供的优点与在官能化处理后可能变差的担体颗粒的流动特征相关。其实,在颗粒尺度上过度的总粗糙度导致粉末的流动性下降且使得其难以应用于粉末的流动特征为基本参数的添加剂合成和热喷涂技术中。另一方面,对于担体颗粒的给定的粒径分布和形貌,如果考虑到与总粗糙度相关的比表面的减小,接近于零的总粗糙度并非理想的。
[0036]
有利地,所述担体颗粒的中值粒径分布d50为1μm至45μm,这些数值可分别对应于优选的1μm的d10尺寸和45μm的d90尺寸。
[0037]
优选地,所述担体颗粒的中值粒径分布d50可为10μm至45μm,对应于特别适合于添加剂合成方法的特定粒径分布。
[0038]
复合颗粒可具有形状因子大于1的不规则形貌,或者具有形状因子接近1的基本球形形态。
[0039]
就本发明而言,术语形状因子指颗粒的被称为主轴的最大尺寸轴的大小与被称为副轴的最小尺寸轴的大小的比值。优选地,根据本发明的复合颗粒具有基本球形的形貌。
[0040]
至于可用于本发明的框架的担体颗粒,具体可提及金属颗粒、陶瓷颗粒或者有机颗粒。
[0041]
至于可用于本发明的框架的官能化颗粒,具体可提及陶瓷颗粒、和/或金属颗粒、和/或有机颗粒,和/或包括选自包括硼、碳、氧和/或氮的组的至少一种元素的颗粒。
[0042]
至于根据本发明的复合颗粒,具体可提及:
[0043]
由用于制造金属陶瓷的金属官能化的陶瓷颗粒,例如wc/co、wc/cu、wc/nicr、tic/
ni、b4c/al、fe
x
ny/ni、feα(n)/ni等;
[0044]
由用于制造陶瓷基复合材料(cmc)的陶瓷官能化的金属颗粒,例如ti/zrb2、ti/tic、ti/sic、ti/zrb2/sic、al/sic、fe/sic、ta6v/zro2、al6061/tic/wc等;
[0045]
由用于制造合金、金属间化合物和假合金的金属官能化的金属颗粒,例如w/cu、w/ni、ti/al、ti/al/c、al/cu、al/zn、cu/ni、ti/agcu、ti/mo、mg/tini、al/tini、a16061/tini/sic等;
[0046]
由陶瓷官能化的陶瓷颗粒,例如,zrb2/sic、al2o3/sio2、si3n4/sic等;
[0047]
由用于制造官能化复合物的金属官能化的有机颗粒,例如,pa/ag、pekk/ag、ptfe/ag、pe/ni等;及
[0048]
由有机材料官能化的金属颗粒或陶瓷颗粒,例如,fe3o4/pa、c/pekk、cu/pe等。
[0049]
本发明的目的还在于使用根据本发明的多材料粉末作为能用于烧结成形技术诸如添加剂合成和/或喷涂表面处理诸如火焰喷涂、hvof、等离子体喷涂或者冷喷涂的材料。
[0050]
本发明的目的还在于用于制造根据本发明(第一实施方案)的粉末的方法,包括:
[0051]
将担体颗粒引入循环流化床反应器,以通过气动装置和/或液压装置或机械装置搅拌担体颗粒,并使用加热电阻使担体颗粒温度升高;
[0052]
制造官能化颗粒在有机溶剂和有机粘结剂的混合物中的悬浮液;
[0053]
然后,在反应器中,通过将悬浮液喷涂在固体流态化的担体颗粒上在担体颗粒表面接枝官能化颗粒;
[0054]
通过在流化床反应器中升温及保温对官能化颗粒进行热处理。
[0055]
为了获得形成根据本发明的粉末的复合颗粒目的,在根据本发明的方法中实施的担体颗粒和官能化颗粒如上文所定义。
[0056]
就本发明而言,术语循环流化床是指设有一方面可在其上部分捕获颗粒另一方面将这些颗粒再次引入其下部分的系统的流化床反应器。该反应器能以两相(固/气)或三相(固/气/液)模式运行。此外,还可在大气压下由冷等离子体火炬有利地辅助,以便例如促进诸如氮、碳、硼和氧等的杂原子的扩散处理。
[0057]
本发明目的还在于用于制造根据本发明(第二实施方案)的粉末的方法,其中,采用为将官能化颗粒移植入担体颗粒表面而特意设计的高能机械反应器作为反应器。
[0058]
在该实施方案中,该方法具体如下:
[0059]
将担体颗粒和官能化颗粒引入反应器中;
[0060]
在反应器中,通过机械作用在0℃至+150℃的温度,优选地,10℃至80℃的温度,在担体颗粒上接枝官能化颗粒。
[0061]
为了获得形成根据本发明的粉末的复合颗粒的目的,在根据本发明的方法中实施的担体颗粒和官能化颗粒也如上文所定义。
[0062]
有利地,根据本发明的方法可进一步包括,在接枝步骤后,使用如上定义的循环流化床对复合颗粒进行热处理和/或表面处理的步骤。
[0063]
有利地,根据本发明的方法可进一步包括,在复合颗粒不具有球形形貌的情况下,使用热等离子体流化床对颗粒进行球化处理的步骤。
附图说明
[0064]
当参考附图阅读为提供信息的目的以非限制方式给出的以下说明时,本发明的其他特征和优点将变得更加清楚,其中:
[0065]
图1示出用于实施根据本发明的方法的第一实施方案的装置(流化床反应器)的框图;
[0066]
图2示出用于实施根据本发明的方法的第一实施方案的装置(研磨装置)的截面的框图;
[0067]
图3a至图6b为用扫描电子显微镜(sem)拍摄的根据本发明的复合颗粒的相片,其中图4b显示cu-ni粉末分析-15kev(5);
[0068]
图7a和图7b为用光学显微镜拍摄的示出由铁和铜的常规混合物(图7a)以及由用铜官能化的铁粉(图7b)通过压实/烧结制造的复合铁-铜材料的截面的显微照相照片;
[0069]
图3a至图7b在后文中的实施例中评述;
[0070]
图1和图2中示出的相同元件由相同数字标记标识。
具体实施方式
[0071]
图1示出用于实施根据本发明的方法的第一实施方案的装置(流化床反应器)的框图。由下列元件组成:
[0072]
用于填充反应器的管1,
[0073]
用于清空反应器的管2,
[0074]
圆柱体反应腔3,
[0075]
旋风分离器4,
[0076]
多孔板5,
[0077]
用于提供流化气的管6,
[0078]
喷嘴7,
[0079]
四个冷等离子体火炬8,
[0080]
用于使粉末循环的管9,
[0081]
用于排出气体的管10,
[0082]
热等离子火炬11,
[0083]
等离子气供应器12,
[0084]
粉末供应器13,
[0085]
加热电阻14,
[0086]
粉末层15。
[0087]
图2示出了用于实施根据本发明的方法的第二实施方案的装置(机械装置)的截面的框图。由如下元件组成:
[0088]
圆柱体腔3,
[0089]
转子16,由以下组成:
[0090]
轴161,
[0091]
压缩部162,及
[0092]
固定轴163,
[0093]
担体粉末和官能化粉末的混合物17,
[0094]
用于冷却水循环的双层壳18,
[0095]
用于冷却水入口和出口的管19,
[0096]
用于装载或者卸载粉末的管20。
[0097]
还在以下实施例中更加详细地示出本发明。除非另有提及,在这些实施例中的所有的百分比和份额均以重量分数表示。
[0098]
实施例
[0099]
实施例1
[0100]
使用粒径分布d50为0.9μm的钴粉末对粒径分布d50为10μm的碳化钨粉末进行官能化。
[0101]
根据第二实施方案进行操作。
[0102]
将重量比为80%wc和20%co的粉末引入高能机械装置中。循环水冷却系统使得反应腔可维持在20℃。用氩气吹扫腔体以在惰性气氛下进行操作。调节压缩部的端部使其与腔体壁的距离为1mm至3mm。腔体壁被设置以4000rpm至6000rpm的速度旋转30min至60min的反应时间。测得的腔体内温度为50℃至80℃。由此获得的复合粉末,如图3a所示,由表面被钴颗粒官能化的碳化钨颗粒组成,钴颗粒覆盖超过90%的担体颗粒的表面。
[0103]
实施例2
[0104]
根据与实施例1中相同的操作参数,使用粒径分布d50为0.9μm的铜粉末官能化与实施例1中相同的碳化钨粉末。
[0105]
由此获得的复合粉末,如图4a所示,由在表面上被铜颗粒官能化的碳化钨颗粒组成,铜颗粒覆盖超过60%的担体颗粒的表面。
[0106]
实施例3
[0107]
使用粒径分布d50为3.5μm的碳化硅粉末官能化粒径分布d50为40μm的铝粉末。
[0108]
根据与实施例1中相同的操作参数进行操作。
[0109]
将重量比为85%铝和15%sic的粉末引入高能机械装置中。
[0110]
由此获得的复合粉末,由图3b(截面图)所示,由在表面上被sic颗粒官能化(形成大于1μm的层)的铝颗粒构成。
[0111]
实施例4
[0112]
根据本发明的方法的第一实施方案,将粒径分布集中在50μm的钴合金粉末(钨铬钴合金)引入循环流化床中。
[0113]
粉末被气体流速为1000l/h至1500l/h的氮气流体化。粉末被加热到150℃至200℃的温度。通过使用喷嘴喷雾将被加入作为有机粘合剂的聚乙烯醇中的粒径分布集中在2μm的镍粉末的含水悬浮液引入流化床的腔体中。气压为3bar至8bar、流速为300l/h至700l/h的氮气作为喷雾气体。以0.8l/h至1.2l/h的流速泵送悬浮液。在喷雾操作结束后,将粉末加热至250℃至350℃的温度,该温度对应于去粘合的第一水平。
[0114]
然后,粉末经受500℃至700℃的温度的扩散热处理。最后冷却并调节(condition)粉末。
[0115]
由此获得如图5a(截面图)所示的被厚度大于2μm的镍层官能化的钴合金粉末。
[0116]
实施例5
[0117]
根据与实施例4相同的实施方案(根据本发明的方法的第一实施方案),通过使用粒径分布集中在5μm的铜粉末铜官能化同样的钴合金粉末。
[0118]
在该情况下,通过使用作为有机粘合剂的聚醋酸乙烯酯制造铜粉末在有机溶剂中的悬浮液。在喷雾操作时,钴合金粉末在80至150℃的温度维持流化。随后官能化的粉末经受与上文所述相同的热处理。
[0119]
由此获得诸如图5b(截面图)所示的由厚度大于1μm的铜层官能化的钴粉末。
[0120]
实施例6
[0121]
根据与实施例4相同的实施方案(根据本发明的方法的第一实施方案)及相同的操作参数,镍官能化粒径分布集中在40μm(d50)的铜球状粉末,镍覆盖超过95%的担体颗粒的表面,诸如图4b所示。
[0122]
实施例7
[0123]
使用粒径分布d50为2μm银粉末官能化粒径分布d50为60μm的聚酰胺粉末(pa)。
[0124]
根据本发明的方法的第二实施方案进行操作。
[0125]
将重量比为93%pa和7%银的粉末引入高能机械装置中。
[0126]
循环水冷却系统允许反应腔的冷却。调节压缩部的端部使其与腔体壁的距离为1μm至3μm。腔体壁被设置为以3000rpm至5000rpm的速度旋转10min至30min的研磨时间。测得的腔体内温度为20℃至50℃。
[0127]
由此获得的复合粉末,如图6a和图6b所示,由在表面上被银颗粒官能化的聚酰胺颗粒构成,银颗粒覆盖超过10%的担体颗粒的表面。
[0128]
实施例8
[0129]
图7a和图7b为用光学显微镜拍摄的示出了一方面由铁和铜的常规混合物(如图7a所示)和另一方面由被铜官能化的铁粉末(如图7b所示)通过压实/烧结制造的复合物铁-铜材料的截面的显微照相照片。
[0130]
在基质中在700mpa的单轴向压力下预先压缩粉末。随后,在可控气氛中在1120℃烧结所得的片体。
[0131]
具体地,图7a示出由这些铁粉末(d50为50μm)和铜粉末(d50为5μm)的常规混合物获得的材料的微观结构。
[0132]
图7b示出根据与实施例5相同的本发明的方法的实施方案由铜官能化的铁粉末获得的相同材料的微观结构。
[0133]
可直观观察到两个微观结构之间的显著差别:
[0134]
–
在由粉末混合物获得的微观结构的情况下(如图7a所示),可看到组分的非均相分布,而
[0135]
–
在由官能化粉末获得的微观结构的情况下(如图7b所示),可观察到由均相分散的铜颗粒互联的铁基质形成的特殊微观结构。