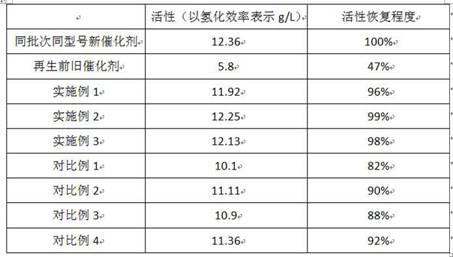
1.本发明涉及化工生产技术领域,具体涉及一种蒽醌法生产过氧化氢用催化剂的再生方法。
技术背景
2.过氧化氢是一种重要的化工产品,广泛应用于造纸、纺织、化学品合成、军工、电子、食品加工、医药、环境保护、冶金等领域。过氧化氢的生产方法主要包括电解法、蒽醌法、异丙醇法和氢氧直接合成法等,其中蒽醌法是最常用的生产方法,目前在国内外均占据主导地位。
3.蒽醌法生产过氧化氢原理是把2-乙基蒽醌(eaq)溶解在以重芳烃(ar)、磷酸三辛酯(top)等有机溶剂按一定组分配制成的混合溶剂中,制成工作液,将工作液与氢气一起通入装有催化剂的氢化塔内,在一定压力和温度下进行氢化反应,得到相应的氢蒽醌(heaq)溶液(即氢化液)。氢化液进入氧化塔,在一定压力和温度的酸性条件下,向氧化塔内通入空气,其中的氢蒽醌被空气中的氧气氧化,恢复成蒽醌,同时生成过氧化氢,氢化液转变为氧化液。利用工作液与水的密度差及过氧化氢在两者中的溶解度不同,在萃取塔内用纯水萃取氧化液中的过氧化氢,得到过氧化氢水溶液(即双氧水)。双氧水再经重芳烃(ar)净化和树脂吸附纯化处理后得到的双氧水产品。经水萃取后的工作液(即萃余液),经聚结分离器、干燥除水和活性氧化铝处理后再回到氢化工序,继续循环使用。在循环过程中,部分2-乙基蒽醌逐渐变成四氢2-乙基蒽醌(h4eaq),并积累于工作液中,它也可反复被氢化和氧化,生成过氧化氢,是生产中的重要载体之一,同时一定量四氢2-乙基蒽醌的存在,将有利于提高氢化反应速度和抑制其它副产物的生成。
4.随着生产的不断进行,工作液中累积的降解物、杂质等极易堵塞催化剂的微孔或附着在催化剂表面,造成催化剂活性降低,当活性下降到一定程度,生产难以维持时,需要进行催化剂再生。传统的再生方法是停车后将固定床内工作液用氮气吹净,通入饱和蒸汽,利用饱和蒸气洗涤附着在催化剂表面的有机物及大部分的无机盐,使催化剂表面被覆盖的活性成分重新暴露,从而恢复催化剂活性,这种处理方法再生完成后,催化剂表面仍有大量附着物难以去除,同时催化剂微孔仍然堵塞严重,催化剂活性恢复有限,一定程度上影响后续生产。
技术实现要素:5.本发明提出了一种蒽醌法生产过氧化氢用催化剂的再生方法,首先采用饱和蒸气处理去除催化剂表面部分附着物,再采用甲醇和碱液组成的洗涤液浸泡,利用甲醇溶解大部分有机降解物,同时利用碱液与部分难溶的蒽醌类衍生物、无机盐等附着物反应生成水溶性盐,两种作用协同进行,对催化剂表面及微孔内的附着物进行彻底清除,该方法对催化剂表面形成的蛋壳型附着物也有很好的清除效果,采用该方法再生的催化剂活性与新催化剂基本一致,能够使再生后的装置保持长期的高效稳定生产。
6.实现本发明的技术方案是:一种蒽醌法生产过氧化氢用催化剂的再生方法,包括如下步骤:(1)饱和蒸汽处理停止工作液和氢气进入氢化塔,关闭各旁路阀开关,用氮气将氢化塔置换合格,检查整个再生管线阀门开关情况,确保再生管线畅通,向氢化塔内通入一定量的饱和蒸汽,蒸汽压力为0.2mpa,同时通入一定量的高纯水,将蒸汽蒸煮过程温度控制在110~120℃,塔内压力控制在0.07-0.09mpa,至氢化塔出口冷凝水cod≤5000mg/l时停止蒸煮再生,用氮气将塔内蒸汽吹干并吹扫降温,吹至催化剂床层温度降至40℃以下停止通氮气;(2)洗涤液浸泡将甲醇和碱液混合,搅拌均匀制得洗涤液,从氢化塔催化剂床层上部加入配制好的洗涤液,直至洗涤液浸没全部催化剂,使催化剂处于完全浸泡状态,保持浸泡6-12h,利用甲醇溶解大部分有机降解物,同时利用碱液与部分难溶的蒽醌类衍生物、无机盐等附着物反应生成水溶性盐,两种作用同时进行,相互协同,对催化剂表面及微孔内的附着物进行彻底清除,尤其是对催化剂表面形成的蛋壳型附着物有很好的清除效果;(3)高纯水置换从氢化塔底部将浸泡后的洗涤液全部排出,关闭底部排净阀,从催化剂床层上部加入高纯水,使高纯水淹没催化剂床层后,通过床层顶部补水,底部排水的方法进行连续置换,置换过程中保持高纯水全部淹没催化剂床层,直至底部排水中甲醇含量低于1000ppm时停止进水,排净塔内高纯水,用氮气吹干,所述氮气优选为热氮气,吹扫至排出的氮气中水含量低于1000ppm时停止通氮气,保压待用;(4)甲醇回收将使用后的洗涤液进行精馏对甲醇进行回收利用,精馏后剩余废液通过静置分层,将上层有机物进行焚烧处理,废水送入污水站处理。
7.优选地,所述步骤(2)中碱液选自氢氧化钠溶液或氢氧化钾溶液。
8.更优选地,所述碱液为氢氧化钠溶液,氢氧化钠在甲醇中溶解度低,容易析出,而氢氧化钠在水中溶解度大,且甲醇与水互溶,采用水作为中间溶解剂,可以实现甲醇和氢氧化钠以溶液形式共存,所以通常采用氢氧化钠溶液与甲醇配制洗涤液,优选地,所述洗涤液中各组分的质量百分浓度分别为:氢氧化钠7.12%-9.61%,甲醇68.57%-76.2%,其余为水。
9.优选地,所述碱液选用质量分数为32%的氢氧化钠溶液,所述氢氧化钠溶液可以采用工业级氢氧化钠配制,也可以直接选用质量分数为32%的氢氧化钠溶液成品,例如工业用32%离子膜烧碱;配制所述洗涤液的甲醇选用质量分数为98%的甲醇溶液,优选质量分数为98%的工业甲醇,保证再生效果的同时可降低成本。
10.优选地,所述质量分数为98%的甲醇溶液和质量分数为32%的氢氧化钠溶液的体积比为4:1-6:1,比例过小洗涤液中甲醇浓度低,有机降解物溶解速度慢,比例过高洗涤液中氢氧化钠浓度低,氢氧化钠与难溶的蒽醌类衍生物、无机盐反应生成可溶性钠盐的速度慢,只有将体积比控制在合适的范围平衡这两个过程,才能取得较好的再生效果。
11.更优选地,所述质量分数为98%的甲醇溶液和质量分数为32%的氢氧化钠溶液的体积比为5:1。
12.本发明的有益效果是:(1)本发明先采用饱和蒸气处理去除催化剂表面部分附着
物,再采用甲醇和碱液组成的洗涤液浸泡,利用甲醇溶解大部分有机降解物,同时利用碱液与部分难溶的蒽醌类衍生物、无机盐等附着物反应生成水溶性盐,两种作用协同进行,能将催化剂表面和微孔内的附着物彻底去除;(2)催化剂表面的附着物部分区域是蛋壳型的,现有技术中的再生方法很难将此类附着物清除干净,而本发明方法对蛋壳型附着物也有很好的清除效果,经本发明方法再生的催化剂活性与新催化剂基本一致。
13.(3)使用后的洗涤液可通过精馏实现甲醇的回收利用,资源浪费小。
具体实施方式
14.下面将结合本发明实施例,对本发明的技术方案进行清楚、完整地描述,显然,所描述的实施例仅仅是本发明一部分实施例,而不是全部的实施例。基于本发明中的实施例,本领域普通技术人员在没有付出创造性劳动前提下所获得的所有其他实施例,都属于本发明保护的范围。
15.实施例1一种蒽醌法生产过氧化氢用催化剂的再生方法,包括如下步骤:(1)饱和蒸汽处理停止工作液和氢气进入氢化塔,关闭各旁路阀开关,用氮气将氢化塔置换合格,检查整个再生管线阀门开关情况,确保再生管线畅通,向氢化塔内通入饱和蒸汽,蒸汽压力为0.2mpa,同时通入高纯水,将蒸汽蒸煮过程温度控制在110~120℃,塔内压力控制在0.07-0.09mpa,蒸汽量为每吨催化剂每小时280-300kg;高纯水流量为每吨催化剂每小时600-800kg,至氢化塔出口冷凝水cod≤5000mg/l时停止蒸煮再生,用氮气将塔内蒸汽吹干并吹扫降温,氮气流量为每吨催化剂每小时60~80m3,吹至催化剂床层温度降至40℃以下停止通氮气;(2)洗涤液浸泡将质量分数为98%的工业甲醇和工业用质量分数为32%的离子膜烧碱按体积比4:1进行混合,搅拌均匀制得洗涤液,从氢化塔催化剂床层上部加入配制好的洗涤液,直至洗涤液浸没全部催化剂,使催化剂处于完全浸泡状态,保持浸泡8h;(3)高纯水置换从氢化塔底部将浸泡后的洗涤液全部排出,关闭底部排净阀,从催化剂床层上部加入高纯水,使高纯水淹没催化剂床层后,通过床层顶部补水,底部排水的方法进行连续置换,置换过程中保持高纯水全部淹没催化剂床层,直至底部排水中甲醇含量低于1000ppm时停止进水,排净塔内高纯水,采用热氮气吹干,热氮气流量为每吨催化剂每小时60-80m3,直至排出的氮气中水含量低于1000ppm时停止通氮气,保压,生产前用大流量工作液循环4小时后可投氢使用;(4)再生后催化剂活性评价采用实验用加氢反应器,直径100mm,取再生后的催化剂500g(堆积密度1l),催化剂装填高度130mm,气液上进下出;试验用工作液采用工业生产旧工作液,蒽醌含量(指2-乙基蒽醌和四氢2-乙基蒽醌的总量)180g/l,重芳烃和磷酸三辛酯的体积比为2.5:1,降解物含量低于20g/l;向氮气置换合格的反应器中通入工作液,控制流量为13l/min,使工作液在
催化剂层的喷淋密度达到100m3/(m2•
h);从反应器顶部通入氮气,氮气流量控制在5l/min,直至反应器底部排出尾气中氧气含量低于0.2%(体积百分数),保持氮气流量的同时,向反应器顶部同时通入氢气,并逐渐提高氢气量,直至反应器底部尾气中氢气含量达到60%(体积分数),记录氢气的用量,分析加氢后的工作液测得氢化效率,采用该氢化效率表示催化剂的活性,再生后的催化剂氢化效率测试结果见表1。
16.实施例2一种蒽醌法生产过氧化氢用催化剂的再生方法仅将实施例1步骤(2)中质量分数为98%的工业甲醇和工业用质量分数为32%的离子膜烧碱的体积比改为5:1,其余同实施例1。
17.再生后的催化剂氢化效率测试结果见表1。
18.实施例3一种蒽醌法生产过氧化氢用催化剂的再生方法仅将实施例1步骤(2)中质量分数为98%的工业甲醇和工业用质量分数为32%的离子膜烧碱的体积比改为6:1,其余同实施例1。
19.再生后的催化剂氢化效率测试结果见表1。
20.对比例1传统饱和蒸汽再生停止工作液和氢气进入氢化塔,关闭各旁路阀开关,用氮气将氢化塔置换合格,检查整个再生管线阀门开关情况,确保再生管线畅通,向氢化塔内通入饱和蒸汽,蒸汽压力为0.2mpa,同时通入高纯水,将蒸汽蒸煮过程温度控制在110~120℃,塔内压力控制在0.07-0.09mpa,蒸汽量为每吨催化剂每小时280-300kg;高纯水流量为每吨催化剂每小时600-800 kg,至氢化塔出口冷凝水变清后停止蒸煮再生,若冷凝水无法变清,则可用测电导率和ph值方法确定,要求冷凝水电导率小于1000μs/cm,ph值在7~8之间,用氮气将塔内蒸汽吹干并吹扫降温,氮气流量为每吨催化剂每小时60~80m3,吹至气体中水含量小于400ppm,催化剂床层温度降至50℃以下停止通氮气,氢化塔保压,生产前用大流量工作液循环4小时。
21.再生后的催化剂氢化效率测试结果见表1。
22.对比例2仅将实施例1步骤(2)中的洗涤液改为质量分数为98%的工业甲醇,其余同实施例1。
23.再生后的催化剂氢化效率测试结果见表1。
24.对比例3仅将实施例1步骤(2)中的洗涤液改为质量分数为8%的氢氧化钠溶液(采用工业级氢氧化钠配制),其余同实施例1。
25.再生后的催化剂氢化效率测试结果见表1。
26.对比例4仅将实施例1步骤(2)中的洗涤液浸泡改为先采用质量分数为98%的工业甲醇浸泡8h,再用质量分数为8%的氢氧化钠溶液(采用工业级氢氧化钠配制)浸泡8h,其余同实施例1。
27.再生后的催化剂氢化效率测试结果见表1。
28.实施例1-3和对比例1-4再生后的催化剂,与再生前旧催化剂、同批次同型号新催化剂的活性评价结果如表1所示。
29.表1不同方法再生后催化剂与再生前旧催化剂、新催化剂活性评价比较由表1可知,按照本发明方法再生处理的催化剂活性能恢复到新催化剂的99%,比按照常规方法再生处理的催化剂活性恢复程度高,对延长催化剂使用周期及使用寿命有积极作用,能够使再生后的装置保持长期的高效稳定生产,降低生产成本。
30.以上所述仅为本发明的较佳实施例而已,并不用以限制本发明,凡在本发明的精神和原则之内,所作的任何修改、等同替换、改进等,均应包含在本发明的保护范围之内。