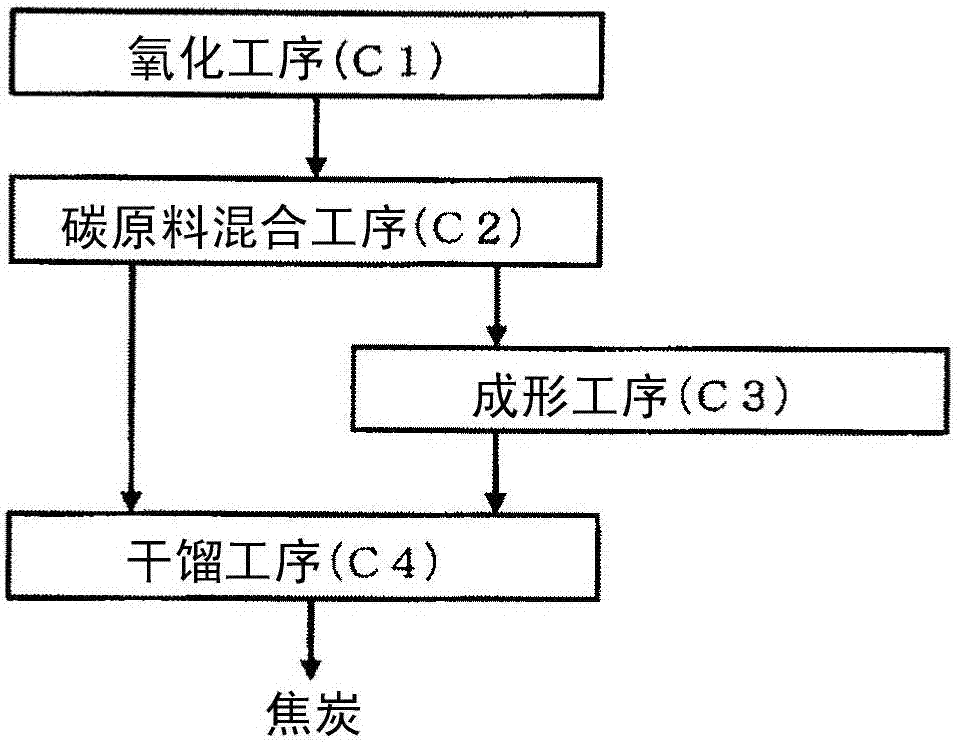
本发明涉及焦炭的制造方法和焦炭。更详细地说,本发明涉及适合于有色金属精炼用还原材的焦炭的制造方法和焦炭。
背景技术:一直以来,作为铝和钛等有色金属的精炼中的还原材,使用的是焦炭。特别是加热生石油焦炭而得到的煅烧焦炭(所谓煅烧炭),由于廉价而通用。作为煅烧焦炭的原料的生石油焦炭,是由原油精制石油的过程中产生的副产物。因此煅烧焦炭的性状依赖于原油。例如煅烧焦炭中所含的杂质(硫、镍、钒、钠等)来自于作为其原料的原油。由于这样的杂质成为污染源,所以,例如作为精炼用焦炭使用时,期望尽可能减少杂质(特别是硫分,下同)。然而,近年来产出的原油因为杂质含量多,所以难以提供杂质含量少的焦炭。因此,作为杂质含量少的碳原料,将实质上不含灰分的无灰煤作为焦炭原料而加以利用受到研究。例如在专利文献1中,公开有一种用于燃料、焦炭原料、化学原料等的无灰煤的制造方法。无灰煤本来热流动性高,不管炼焦煤的品位如何,均具有在200~300℃下熔融的性质。另外,无灰煤具有若加热到400℃左右则膨胀的性质。因此若成形无灰煤并高温加热进行干馏处理,则无灰煤熔融而不能维持成形体的形状,软化熔融性构成问题。另外,无灰煤经高温加热会发泡膨胀,从干馏装置中溢出,或附着在干馏装置内壁而不能排出,或者所得到的焦炭成为海绵状的多孔质体而体积密度显著降低等膨胀性也成为问题。因此,由于无灰煤在软化熔融性和膨胀性上存在问题,所以难以作为焦炭原料使用。针对这样的问题,本发明人等提出无灰煤的改质技术(专利文献2)。具体来说,公开有一种具有如下要旨的碳原料的制造方法,其包括如下工序:对于含有煤和芳香族溶剂的浆料进行加热处理的浆料加热工序;将在所述浆料加热工序经过加热处理的浆料分离成溶解有煤的液体成分、和由灰分与不溶煤构成的固体成分的分离工序;从所述液体成分中除去芳香族溶剂,取得无灰煤的无灰煤取得工序;对于在所述无灰煤取得工序中取得的无灰煤进行加热处理而作为碳原料的无灰煤加热工序,所述无灰煤加热工序中得到的碳原料的挥发分,在根据JISM8812所规定的方法进行测量时,低于35质量%并且在24质量%以上。根据这一技术,通过含有浆料加热工序、分离工序、无灰煤取得工序、和将挥发分调整到规定范围的无灰煤加热工序,则能够制造低灰、并具有优异的自烧结性的碳材料。现有技术文献专利文献专利文献1:日本国特开2001-26791号公报专利文献2:日本国特开2009-144130号公报发明要解决的课题专利文献2的技术,虽然对自烧结性的改善起到了优异的效果,但是因为在无灰煤的改质上费事,所以生产率不一定好,改质的无灰煤比较高价。
技术实现要素:本发明着眼于上述这样的情况而形成,其目的在于,提供一种比以往更廉价地制造高纯度焦炭的方法和高纯度焦炭。用于解决课题的手段能够达成上述课题的本发明的焦炭的制造方法,具有如下要旨:对于以下混合物进行干馏,所述混合物含有无灰煤、对于无灰煤进行氧化处理而得到的氧化无灰煤、生石油焦炭,相对于所述无灰煤、所述氧化无灰煤和所述生石油焦炭的合计100质量份,所述无灰煤的含量为5~40质量份,且所述无灰煤和所述氧化无灰煤的合计含量为30~70质量份。在本发明中,以下均为优选的实施方式:在成形所述混合物之后进行干馏;所述氧化无灰煤的氧增加率为2~10%;所述氧化处理为空气氧化;所述氧化处理以150℃以上且低于燃点的温度进行。另外,所述干馏以分室炉进行,以回转窑进行也是优选的实施方式。在本发明中,也包括对如下混合物进行干馏而得到的焦炭,该混合物含有无灰煤、对无灰煤进行氧化处理而得到的氧化无灰煤、生石油焦炭,相对于所述无灰煤、所述氧化无灰煤和所述生石油焦炭的合计100质量份,所述无灰煤的含量为5~40质量份,且所述无灰煤与所述氧化无灰煤的合计含量为30~70质量份。发明效果根据本发明的制造方法,能够使用生石油焦炭廉价地制造高纯度焦炭。另外根据本发明,能够提供高纯度焦炭。附图说明图1是说明无灰煤的制造工序的一例的流程图。图2是说明本发明的焦炭的制造工序的一例的流程图。具体实施方式本发明人等为了将生石油焦炭用于碳原料而廉价地提供高纯度的焦炭,反复潜心研究。其结果得到以下的结论。无灰煤的杂质含量极少,将无灰煤混合在生石油焦炭中,对于焦炭的杂质含量的减少有用。不过如现有技术指出的那样,无灰煤在软化熔融性和膨胀性方面存在问题。因此,由本发明人等研究的结果可知,如果对于无灰煤进行氧化处理,则能够改善无灰煤的软化熔融性和膨胀性。氧化无灰煤原本为微粉状,粘结性差,因此在氧化无灰煤和生石油焦炭的混合物中,若干馏则所得到的焦炭成为粉状,容易从干馏装置中耗散,另外也产生焦炭的体积密度变低这样的问题。为了解决这样的问题而潜心研究,其结果可知,通过成为含有无灰煤、氧化无灰煤、生石油焦炭的混合物,无灰煤能够作为结合氧化无灰煤和生石油焦炭的粘合剂发挥功能,抑制焦炭的粉化等问题。而且发现,通过使用以后述规定的含量含有无灰煤、氧化无灰煤和生石油焦炭的混合物,可以抑制所得到的焦炭的熔融和膨胀,能够廉价地提供高纯度的焦炭。以下,对于本发明的焦炭的制造方法,基于图1、图2所示的流程图进行说明。首先,对于本发明中使用的无灰煤进行说明。所谓无灰煤,是指灰分为5质量%以下,优选为3质量%以下的煤。优选的是以815℃加热煤,使之灰化时的残留无机物(硅酸、氧化铝、氧化铁、石灰、氧化镁、碱金属等)的灰分的浓度极少的煤作为无灰煤。具体来说,灰分浓度更优选为5000ppm以下(质量基准),进一步优选为2000ppm以下。另外无灰煤没有丝毫水分,比炼焦煤显示出更高的热流动性。<无灰煤的制造工序>无灰煤能够以各种公知的制造方法取得,例如,能够从煤的溶剂萃取物中除去溶剂而获得。例如,无灰煤可以经过下述S1~S3的工序(参照图1)制造,但下述无灰煤的制造工序(S1~S3)能够适当变更,也可以根据需要附加各种处理工序。例如在制造无灰煤时,在不对所述各工序造成不良影响的范围内,也可以在所述各工序之间或前后含有粉碎炼焦煤的煤粉碎工序、除去灰尘等废物的除去工序、使得到的无灰煤干燥的干燥工序等其他的工序。<浆料加热工序:S1>浆料加热工序(S1),是混合煤和芳香族溶剂而调制浆料,并进行加热处理,将煤成分萃取到芳香族溶剂中的处理。作为原料的煤(以下,也称为“炼焦煤”)的种类没有特别限定。例如可以使用烟煤、次烟煤、褐煤、亚煤(日文:亚炭)等各种公知的煤。从经济性的观点出发,相比使用高价的烟煤等高品位煤,优选使用次烟煤、褐煤、亚煤等劣质煤。作为芳香族溶剂,如果具有溶解煤的性质则没有特别限定。作为芳香族溶剂,可例示苯、甲苯、二甲苯等单环芳香族化合物,和萘、甲基萘、二甲基萘、三甲基萘等双环芳香族化合物等。另外,在双环芳香族化合物中,包含其他具有脂肪族侧链的萘类,另外,包含其中具有联苯、长链脂肪族侧链的烷基苯。在本发明中,优选作为非供氢性溶剂的双环芳香族化合物。所谓非供氢性溶剂,是主要由煤的碳化生成物精制的、以双环芳香族为主的作为溶剂的煤衍生物。优选非供氢性溶剂的理由在于,非供氢性溶剂即使在加热状态仍稳定,与煤的亲和性优异,因此被溶剂萃取的煤成分的比例(以下,也称“萃取率”)高,另外,是可以通过蒸馏等的方法很容易回收的溶剂,此外回收的溶剂能够循环使用。还有,若芳香族溶剂的沸点过低,则加热萃取时或后述的分离工序(S2)中所需压力变高,另外在回收芳香族溶剂的工序中因挥发造成的损失增大,芳香族溶剂的回收率降低。此外,加热萃取中的萃取率也降低。另一方面,若芳香族溶剂的沸点过高,则分离工序(S2)中的从液体成分中或者从固体成分中分离芳香族溶剂困难,溶剂的回收率降低。芳香族溶剂的沸点优选为180~330℃。相对于芳香族溶剂的煤浓度没有特别限定。虽然根据炼焦煤的种类也有所不同,但若对于芳香族溶剂的煤浓度低,则相对于芳香族溶剂的量,萃取到芳香族溶剂中的煤成分的比例变少,不经济。另一方面,虽然煤浓度越高越优选,但若过高,则浆料的粘度变高,浆料的移动和分离工序(S2)中的液体成分与固体成分的分离容易变得困难。煤浓度以干煤基准计,优选为10质量%以上,更优选为20质量%以上,优选为50质量%以下,更优选为35质量%以下。若浆料的加热处理(加热萃取)温度过低,则不能充分弱化构成煤的分子间的键合,作为炼焦煤使用劣质煤时,不能提高以后述的无灰煤取得工序(S3)取得的无灰煤的再固化温度。另一方面,若加热处理温度过高,则煤的热分解反应将非常活跃,生成的热分解基团发生复合,因此萃取率降低。浆料加热温度优选为350℃以上,更优选为380℃以上,优选为420℃以下。加热时间(萃取时间)没有特别限定,但若萃取时间变长,则热分解反应过度进行,自由基聚合反应进行,萃取率降低。例如,如果是上述加热温度,则优选为120分钟以下,更优选为60分钟以下,进一步优选为30分钟以下,优选为10分钟以上。加热萃取后,为了抑制热解反应,优选冷却至370℃以下。另外冷却时的温度的下限优选为300℃以上。若冷却至低于300℃,则芳香族溶剂的溶解力降低,发生暂时萃取的煤成分的再析出,无灰煤的收率降低。加热萃取优选在非氧化性气氛中进行。具体来说,优选在氮等不活泼气体的存在下进行。加热萃取时若与氧接触,则有可能起火,因此很危险,另外是因为使用氢时成本高。加热萃取中的压力,也会根据加热萃取时的温度、使用的芳香族溶剂的蒸气压而不同,但压力比芳香族溶剂的蒸气压低时,芳香族溶剂挥发而无法锁定为液相,不能进行萃取。另一方面,若压力过高,则机器的成本、运转成本变高,不经济。优选的压力大致为1.0~2.0MPa。<分离工序:S2>分离工序(S2),是将浆料加热工序(S1)中经加热处理的浆料分离成液体成分和固体成分的工序。所谓液体成分,是含有被芳香族溶剂萃取的煤成分的溶液。所谓固体成分,是含有不溶于芳香族溶剂的灰分和不溶煤的浆料。作为由分离工序(S2)将浆料分离成液体成分与固体成分的方法,未特别限定,能够采用过滤法、离心分离法、重力沉降法等公知的分离方法。在本发明中优选使用可以进行流体的连续操作、低成本且适于大量的处理的重力沉降法。利用重力沉降法时,从重力沉降槽的上部,能够得到含有被芳香族溶剂萃取的煤成分的溶液即液体成分(以下,也称为“上清液”),从重力沉降槽的下部,能够得到含有不溶于溶剂的灰分和煤的浆料即固体成分(以下,也称为“固体成分浓缩液”)。然后,如以下说明的,使用蒸馏法等从该上清液中分离·回收芳香族溶剂,能够得到灰分浓度极低的无灰煤(无灰煤取得工序(S3))。<无灰煤取得工序:S3>无灰煤取得工序(S3),是从上清液分离芳香族溶剂而取得灰分浓度极低的无灰煤的工序。从上清液分离芳香族溶剂的方法未特别限定,能够使用一般的蒸馏法、蒸发法(喷雾干燥法等)等。另外,分离并回收的芳香族溶剂能够反复使用。通过芳香族溶剂的分离·回收,能够由上清液得到无灰煤。得到的无灰煤除了用作本发明的混合物的原料以外,也能够用作氧化无灰煤的原料。<其他的工序>根据需要,也可以从固体成分浓缩液中分离芳香族溶剂,制造灰分被浓缩的萃余煤(萃余煤取得工序)。从固体成分浓缩液分离芳香族溶剂的方法与从所述液体成分取得无灰煤的无灰煤取得工序(S3)同样,能够使用一般的蒸馏法、蒸发法。<焦炭的制造工序>以下,基于图2说明本发明的焦炭的制造方法。制造焦炭时,在不对各工序造成不良影响的范围,在各工序之间或前后,也可以包括例如将各种原料等加以粉碎的粉碎工序、除去灰尘等废物的除去工序、对于所得到的焦炭实施各种处理的工序等其他的工序。<氧化工序:C1>氧化工序,是对于无灰煤进行氧化处理而得到氧化无灰煤的工序。通过对无灰煤进行氧化处理,无灰煤得到改质,能够改善软化熔融性和膨胀性。无灰煤的氧化方法未特别限制,希望利用例如氧、臭氧、二氧化氮、空气等氧化性气氛进行的氧化,优选将空气中的氧作为氧化剂的空气氧化。氧化无灰煤的氧增加率没有特别限定,但若氧增加率过低,则无灰煤的改质效果不充分,干馏时由于软化熔融性和膨胀性而发生问题。另一方面,若氧增加率过高,则收率降低而不经济。因此氧增加率为2%以上,优选为3%以上,优选为10%以下,更优选为5%以下。还有,在本发明中,设定无灰煤的氧增加率时,经氧化处理而仍具有比设定值低的氧增加率的无灰煤不作为本发明的氧化无灰煤处理。另外,将氧增加率比设定值低的无灰煤作为碳原料使用时,作为本发明的无灰煤处理。在本发明中所谓氧增加率,就是基于JISM8813(含氧率的计算方法)测量氧化处理前后的无灰煤的含氧率,并计算出(氧化无灰煤的含氧率一无灰煤的含氧率)的值。氧化时保持的温度(以下记为氧化温度)以能够得到希望的氧增加率的方式适当调整即可。若氧化温度低,则无灰煤的氧化不足,有时上述改质效果无法得到充分发挥。另外若氧化温度低,则达成希望的氧增加率耗时,生产率劣化。另一方面,若氧化温度过高,则氧化速度变得过快,难以控制无灰煤的氧化度。氧化温度优选为150℃以上,更优选为200℃以上,优选低于无灰煤的燃点,更优选为350℃以下。氧化时间(规定的温度下的保持时间)以能够得到规定的氧增加率的方式适当调整即可。若氧化时间短,则无灰煤的氧化不足。另一方面,若氧化时间长,则无灰煤过剩地被氧化,收率降低而成为成本增加要因。例如上述温度范围内的优选的氧化时间为0.5小时以上,更优选为1小时以上,优选为6小时以下,更优选为3小时以下。氧化后冷却至室温即可。还有,供于氧化处理的无灰煤的粒径(当量圆直径,以下,关于粒径均相同)没有特别限定。若无灰煤的粒径过大,则无灰煤内部无法被充分氧化,干馏时有可能发生熔融等。另一方面,若无灰煤的粒径过小,则处理性劣化。无灰煤的平均粒径优选为3mm以下,更优选为1mm以下,优选为0.2mm以上,更优选为0.3mm以上。另外从氧化促进的观点出发,最大粒径也优选为3mm以下,更优选为1mm以下,进一步优选为0.5mm以下。<碳原料混合工序:C2>碳原料混合工序,是混合上述无灰煤、上述氧化无灰煤和生石油焦炭而取得混合物(以下,称为“混合碳原料”)的工序。所谓生石油焦炭,就是在石油精炼工序中,用于以高温(例如500℃以上)加热蒸馏残渣,使之热分解而制造轻质油的设备(焦化设备)中,与轻质油一起副生出的固体物质。在本发明中,生石油焦炭可以使用各种市售的公知的生石油焦炭。优选的生石油焦炭的挥发分为5~20质量%,硫分为2~5质...