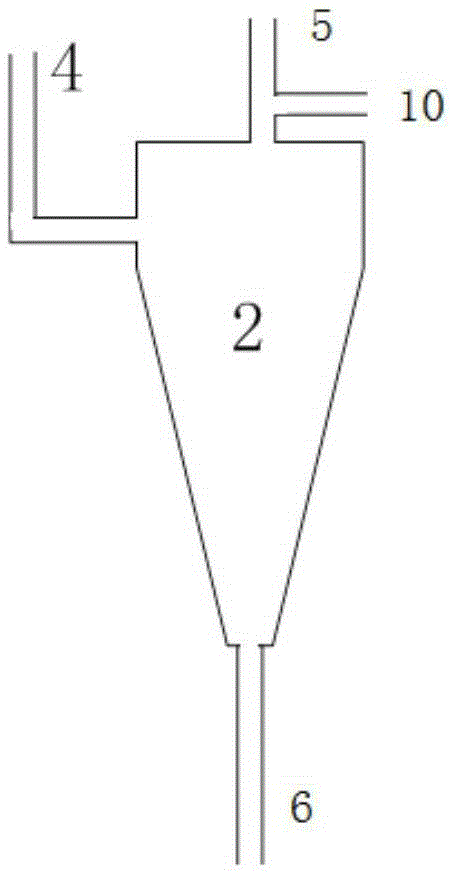
本发明涉及煤化工领域,具体地,涉及一种煤焦油全馏分的轻质化方法。
背景技术:
:煤焦油是煤在干馏和/或气化过程中副产的具有刺激性臭味、黑色或黑褐色、黏稠状的液体产品。根据工艺反应温度的不同,可分为低温煤焦油(450-650℃)、中温煤焦油(600-1000℃)和高温煤焦油(大于1000℃)。总体来看,我国煤焦油的年产量已经超过2000万吨。2011年我国高温煤焦油总产能在2200万吨左右,实际产量约为1750万吨;中低温煤焦油总产能约为600万吨,总产量达350万吨。另外,我国大量煤制天然气装置已经进入规划和建设期,作为工艺源头的移动床加压气化技术也会随之大量推广,由此伴生的中低温煤焦油数量在未来也会急剧增长。据测算,至2020年,中低温煤焦油的新增产能将达到1500万吨/年。此外,随着我国西部低阶煤的大规模开发,通过低温热解工艺提高褐煤等低阶煤的利用价值已经成为当前产业界的共识,而低温煤焦油的产量也会随之提高。在国内市场对石油产品的需求日益增加,而原油供应不足日渐突出的大背景下,通过煤焦油深加工生产车用燃料油,是对石油产品需求的重要补充。但是,从组成上看,煤焦油中含有大量的芳烃、烯烃等不饱和组分,硫、氮及氧等杂原子含量高,金属含量高,还含有一定量的水分、煤粉颗粒及其它机械杂质。这些组成特点也加大了煤焦油的加工难度,使得传统的重油加工技术难以直接用于煤焦油深加工。目前国内焦油加工装置普遍较分散、规模偏小、能耗高且严重污染环境,产品品种少,尤其是高质量、高附加值的清洁燃料产量较低,生产成本高、经济效益差。因此,开发以最大化生产清洁 车用燃料为目的的新型煤焦油加工技术具有重大的经济效益、社会效益和环保效益。根据煤焦油的组成特点,现有技术多采用悬浮床或浆态床等移动床加氢工艺进行轻质化处理。在工艺流程上大体分为以下两类,一是,原料经脱水脱灰预处理后进行蒸馏切割,重馏分进入浆态床反应器中进行反应,轻馏分与悬浮床反应后的轻油混合后进入后续固定床精制段。二是,原料经脱水脱灰后直接进入浆态床反应器中进行反应,反应后轻油进入后续固定床精制段,重油循环回浆态床反应器。然而,现有技术在对煤焦油进行加工时主要存在以下问题:第一,煤焦油原料粘度较大,其中水或固体颗粒等与煤焦油等互相包裹,分离净化难度较大,而分离出的水中含有大量的酚、多环芳烃等污染物,毒害大,处理净化难度高;第二,煤焦油原料如通过蒸馏切割,则增加了全厂能耗,而重馏分进入浆态床反应器后,易生焦组分在反应器中含量提高,既会影响装置的操作周期,也对延长催化剂使用寿命不利;第三,浆态床反应过程整体转化率不高,影响后续固定床精制段的反应苛刻度,进而导致最终产品中柴油馏分含量偏高,工艺柴汽比不合理,影响整体工艺的经济性。技术实现要素:本发明的目的是克服现有技术的上述缺陷,将煤焦油全馏分进料最大化转化为清洁汽柴油等轻质燃料,同时避免现有工艺中能耗高、操作周期短、柴汽比不合理等问题的发生。为了实现上述目的,本发明提供一种煤焦油全馏分的轻质化方法,该方法包括:将煤焦油全馏分、氢气和加氢催化剂I引入一级浆态床反应器中进 行临氢裂化反应,得到裂化反应混合物;将所述裂化反应混合物进行分离,得到第一气体、轻油相和重油相;将氢气和所述重油相引入含有内置的旋液分离器的二级浆态床反应器中进行深度加氢转化反应,并将反应后得到的贫固含量组分与所述轻油相引入固定床加氢处理单元中进行加氢处理。本发明采用两段组合式浆态床处理与固定床加氢裂化耦合的工艺流程,在保证运转周期的基础上,煤焦油全馏分直接进料,提高全厂馏分油收率,达到最大化生产清洁燃料的目的。本发明的其它特征和优点将在随后的具体实施方式部分予以详细说明。附图说明附图是用来提供对本发明的进一步理解,并且构成说明书的一部分,与下面的具体实施方式一起用于解释本发明,但并不构成对本发明的限制。在附图中:图1是本发明的一种优选实施方式的旋液分离器的结构示意图。图2是本发明的一种优选实施方式的反应器结构示意图。附图标记说明1、反应器壳体2、旋液分离器内腔3、套筒4、旋液分离器入口5、气相出口6、底流管7、气体分布器8、反应器内腔9、出气口10、产物油出口11、进气口12、卸剂口13、加剂口14、原料油入口具体实施方式以下对本发明的具体实施方式进行详细说明。应当理解的是,此处所描述的具体实施方式仅用于说明和解释本发明,并不用于限制本发明。本发明提供了一种煤焦油全馏分的轻质化方法,该方法包括:将煤焦油全馏分、氢气和加氢催化剂I引入一级浆态床反应器中进行临氢裂化反应,得到裂化反应混合物;将所述裂化反应混合物进行分离,得到第一气体、轻油相和重油相;将氢气和所述重油相引入含有内置的旋液分离器的二级浆态床反应器中进行深度加氢转化反应,并将反应后得到的贫固含量组分与所述轻油相引入固定床加氢处理单元中进行加氢处理。在本发明中,所述反应物料并不特指仅含有煤焦油全馏分、催化剂和氢气的物料,本文中的反应物料泛指参与反应过程的所有物料,包括固相、气相和液相物料,也包括反应物、生成物等。所述煤焦油全馏分可以包括煤热解、煤干馏及煤气化工艺过程中产生的煤焦油全馏分中的至少一种,所述煤焦油全馏分无需经过脱水或脱灰过程,优选经过预热后达到泵送条件即可与加氢催化剂I进入一级浆态床反应器中进行临氢裂化反应。优选地,所述加氢催化剂I为高分散铁系催化剂,所述高分散铁系催化剂既可以是含有铁系氧化物的矿物颗粒,如硫铁矿、赤铁矿、赤泥等;也可以是高分散铁系化合物粉末,如Fe2S、Fe2O3、Fe3O4等;还可以是铁系碳基负载型催化剂,载体为煤粉、活性炭、石墨及炭黑等碳基材料。上述高分散铁系催化剂控制粒径范围为10-200μm,优选粒径范围为50-120μm。相对于100重量份的所述煤焦油全馏分,特别优选所述加氢催化剂I的用量为0.1-5重量份;更优选为0.5-2重量份。所述一级浆态床反应器可以为本领域内常规的各种浆态床反应器,例如可以为CN203559012U中所述的浆态床反应器。优选地,先将所述煤焦油全馏分进行加热预处理后再引入所述一级浆态床反应器中进行反应。所述加热预处理是为了使得进入所述一级浆态床反应器中的反应物料能够更加高效地进行反应。优选所述加热预处理的条件包括温度为350-500℃;更优选为360-460℃。也可以先将部分氢气预热后引入所述一级浆态床反应器中,氢气预热温度在360-550℃之间,优选为370-500℃。总体来看,本发明所述临氢裂化反应的反应条件可以采用高苛刻度和高空速的反应条件,一方面使煤焦油全馏分中较易生焦成分在高苛刻度下发生轻质化反应,同时在催化剂或载体表面完成焦炭沉积,防止其进入后续反应单元,有利于后续的旋液分离过程的进行;另一方面通过较高的空速将生成的焦炭带出一级浆态床反应器。优选情况下,本发明的所述临氢裂化反应的条件包括:压力为15-30MPa,温度为380-450℃,液时体积空速为0.8-3.0h-1,氢油体积比为200-5000:1;更加优选情况下,所述临氢裂化反应的条件包括:压力为18-25MPa,温度为410-440℃,液时体积空速为1.0-2.5h-1,氢油体积比为1000-2500:1。将所述裂化反应混合物进行分离的方法可以有多种,例如,将所述裂化反应混合物引入热高压分离器中进行分离,得到气相和重油相,其中,该重油相中含有未转化油及加氢催化剂I颗粒;所述重油相进入二级浆态床反应器中进行进一步裂化,而气相进入低温高压分离器,得到轻油相和第一气体,轻油相直接进入固定床加氢处理单元中进行加氢处理,而所述第一气体可以循环使用。优选所述热高压分离器的操作温度为300-400℃,更优选为330-380℃。所述二级浆态床反应器中进行深度加氢转化反应的操作条件比所述一级浆态床反应器中的临氢裂化反应条件缓和。优选所述深度加氢转化反应的 条件包括:压力为10-20MPa,温度为350-430℃,液时体积空速为0.1-2.0h-1,氢油体积比为200-5000:1。更加优选所述深度加氢转化反应的条件包括:压力为13-18MPa,温度为380-410℃,液时体积空速为0.2-1.0h-1,氢油体积比为1000-2500:1。优选地,所述二级浆态床反应器中含有加氢催化剂II,所述加氢催化剂II中含有载体和活性金属元素,所述载体包括氧化硅-氧化铝和氧化铝,所述活性金属元素包括铁、钙和钼,所述加氢催化剂II为微球型,且平均粒径为20-200μm;优选为50-120μm;更优选为60-100μm。优选地,以所述加氢催化剂II的总重量计,所述活性金属元素以氧化物计的含量为10-40重量%;优选以所述加氢催化剂II的总重量计,钙和钼以氧化物计的含量分别为0.1-1重量%和5-10重量%。优选控制氢气引入所述二级浆态床反应器中的流量,使得所述贫固含量组分中的固含量不高于0.5重量%。优选控制氢气引入所述二级浆态床反应器中的流量,使得所述富固含量组分中的固含量为5-50%重量%,优选为10-40%重量%。优选地,所述二级浆态床反应器还含有:反应器壳体,该反应器壳体的下部设置有卸剂口、进气口和原料油入口,该反应器壳体的上部设置有出气口和加剂口;所述反应器壳体的内部空间构成反应器内腔;在反应器内腔中进行深度加氢转化反应的反应物料通过旋液分离器入口进入所述旋液分离器的内腔中进行分离,分离所得的富固含量组分从所述旋液分离器下部的底流管返回至所述反应器内腔中,分离所得的贫固含量组分从所述产物油出口引出至所述固定床加氢处理单元中,分离所得的气相从气相出口引出至所述旋液分离器之外。优选地,所述反应器内腔的下部还设置有使得反应物料在所述反应器内 腔中进行内循环的套筒,所述套筒的下部通过内径小于所述套筒内径且伸入所述套筒内部的导管与所述反应器壳体的进气口连通。优选地,所述套筒为一根或至少两根,至少两根的所述套筒下部的所述导管与所述进气口之间设置有气体分布器;所述氢气通过所述进气口依次引入至所述气体分布器、所述导管和所述套筒中。所述旋液分离器可以为一级或至少两级,优选至少两级的所述旋液分离器中的前一级的旋液分离器中分离得到的所述贫固含量组分进入相邻的后一级旋液分离器中,分离得到的所述富固含量组分从底流管返回至所述反应器内腔中,以及最后一级旋液分离器中分离得到的所述贫固含量组分从所述产物油出口引出至所述固定床加氢处理单元中。优选所述产物油出口设置在所述反应器壳体上。优选地,所述套筒的长度为所述二级浆态床反应器内腔的长度的2/5至4/5。所述二级浆态床反应器内腔的长度与所述二级浆态床反应器内腔的内径之比可以为5-20:1;优选为8-15:1。优选地,所述二级浆态床反应器内腔的内径为50-6000mm,进一步优选为300-5000mm。优选地,所述套筒的内径为所述二级浆态床反应器内腔的内径的1/100至3/4。优选地,所述导管伸入所述套筒内部的长度为所述套筒的长度的1/1000至1/10。所述一级浆态床反应器和所述二级浆态床反应器的内部结构可以相同或不同,优选地,本发明的所述一级浆态床反应器和所述二级浆态床反应器的内部结构相似,所不同的是,所述一级浆态床反应器中不含有旋液分离器。根据本发明的一种优选的具体实施方式,本发明所述的旋液分离器如图 1中所示,具体地:所述旋液分离器包括旋液分离器入口4、旋液分离器内腔2、气相出口5、产物油出口10和底流管6。物料通过旋液分离器入口4进入旋液分离器内腔2中利用自身的离心力进行分离,分离得到气相物从所述气相出口5引出至所述旋液分离器之外,分离得到固含量较小的组分从位于旋液分离器上部的产物油出口10引出至所述旋液分离器之外,分离得到的固含量较大的组分从位于旋液分离器下部的底流管6引出至所述旋液分离器之外。根据本发明的另一种优选的具体实施方式,本发明所述的二级浆态床反应器如图2中所示,具体地,该二级浆态床反应器包括:反应器壳体1,该反应器壳体的下部设置有卸剂口12、进气口11和原料油入口14,该反应器壳体的上部设置有出气口9和加剂口13;所述反应器壳体1的内部空间构成反应器内腔8,该反应器内腔的上部设置有旋液分离器,所述反应器内腔8中的反应物料从旋液分离器入口4进入所述旋液分离器内腔2中进行分离,分离所得的富固含量组分从所述旋液分离器下部的底流管6返回至所述反应器内腔8中,分离所得的贫固含量组分从产物油出口10引出至所述二级浆态床反应器之外,分离所得的气相从气相出口5引出至所述旋液分离器之外。该反应器内腔8的底部还设置有使得反应物料在所述反应器内腔8内进行内循环的套筒3,所述套筒3的下部通过内径小于所述套筒内径且伸入所述套筒内部的导管与所述反应器壳体1的进气口11连通。以及所述套筒3为3根,所述旋液分离器设置为两级,3个套筒下部的所述导管与所述进气口11之间设置有气体分布器7。根据上述优选的具体实施方式,加氢催化剂II和重油相分别从所述反应器壳体1的加剂口13和原料油入口14进入所述反应器内腔8中,并且氢气依次通过进气口11、气体分布器7以及导管分别引入到套筒3内,套筒内充满含有气固液三相的反应物料,引入的氢气使得套筒中的反应物料的气含量 增加,从而向上运动,并且相对地,套筒外的反应物料沿着所述套筒外壁向下运动,如此形成内循环,同时,反应器内腔8中的气固液三相的反应物料从旋液分离器入口4进入第一级的旋液分离器内腔2中进行分离,所得的气相通过气相出口5引出至所述旋液分离器之外,分离所得的富固含量组分从所述旋液分离器下部的底流管6返回至所述反应器内腔8中,分离所得的贫固含量组分引入第二级的旋液分离器内腔2中进行分离,所得的气相通过气相出口5引出至所述旋液分离器之外,分离所得的富固含量组分从第二级的旋液分离器下部的底流管6返回至所述反应器内腔8中,分离所得的贫固含量组分从产物油出口10引出至固定床加氢处理单元中进行加氢处理。从所述气相出口5引出的气相通过出气口9引出至二级浆态床反应器之外。反应完的催化剂从卸剂口12引出至二级浆态床反应器之外。优选所述二级浆态床反应器的反应器内腔中的反应物料中的加氢催化剂II的平均含量为5-50重量%,进一步优选为10-40重量%。新鲜的加氢催化剂II从二级浆态床反应器上部的加剂口进入所述二级浆态床反应器中,反应一定时间的催化剂从所述二级浆态床反应器下部卸剂口卸出,维持所述二级浆态床反应器内腔中反应物料的平均固含量基本不变。优选地,控制所述氢气进入所述二级浆态床反应器中的流量,使得所述二级浆态床反应器的反应器内腔中的反应物料在所述套筒外的向下流动的平均速率0.1-0.3m/s。优选地,控制所述氢气进入所述二级浆态床反应器中的流量,使得所述反应物料在经过所述旋液分离器入口时的速率为5-15m/s,优选为7-12m/s。为了满足后续固定床加氢处理单元的要求,优选控制产物油出口流出的贫固含量组分中的固体含量低于200ppm。所述固定床加氢处理单元中可以含有本领域内常规使用的加氢处理催化剂,使得所述贫固含量组分与所述轻油相能够进行加氢处理反应。优选将 加氢处理后得到的液体物流进行分馏,得到加氢汽油和加氢柴油等轻质油品。所述加氢处理的条件可以使用任何适用于本发明的技术,其一般操作条件为:氢分压为8-15MPa,反应温度为350-410℃,液时体积空速为0.2-1.0h-1,氢油体积比为200-1000。所述加氢处理催化剂一般以多孔氧化铝作为载体,以第VIB、第VIIB和第VIII族中的一种或多种金属或金属氧化物作为活性组分。催化剂一般采用分级装填的方法。在具体实施时,可以根据煤焦油全馏分的性质和浆态床反应器的加氢结果,调整固定床加氢处理单元的工艺条件和加氢处理催化剂的装填量及配比方式。本领域技术人员可以根据本发明的描述结合本领域内的常规技术手段确定本发明的所述二级浆态床反应器的反应器内腔的容积与所述旋液分离器的容积,优选情况下,所述旋液分离器的容积与所述浆态床反应器的反应器内腔的容积之比为1:100至1:1000。本发明的上述方法还具有如下具体的有益效果:1、煤焦油全馏分原料无需进行复杂的脱水脱灰等预处理过程,降低了原料预处理的难度,有利于降低整个工艺流程的能耗,同时避免了脱水过程带来的酚水处理难题。2、整个工艺流程实现了煤焦油全馏分的进料,不需要进行蒸馏切割,在保证整体液收提高的同时,也节约了因蒸馏过程带来的大量能量消耗。3、针对煤焦油全馏分的组成特点,设计两级浆态床工艺组合流程,有效解决了现有煤焦油浆态床加工工艺的存在的问题,本发明通过高苛刻度的一级浆态床临氢反应,在完成重组分快速裂解的同时,促使易生焦组分在煤焦油原有颗粒、催化剂颗粒或载体上的沉积,既有利于后续工艺流程的操作,也能一定程度上增大油相中的颗粒粒径,降低分离难度,提高分离效率。而且,在上述临氢过程中,完成了煤焦油全馏分原料中水分的处理,通过对其中酚类的加氢转化,避免了酚水的产生。另外,本发明通过旋液分离器及高 活性的催化剂的配合,既解决了传统浆态床加工工艺过程中的固液分离问题,有利于延长操作周期,满足后续固定床加氢处理过程对原料的要求;又能通过双功能催化剂灵活调整产品分布,有利于提高整个工艺的经济效益。以下将通过实施例对本发明进行详细描述。其中,二级浆态床反应器的反应器内腔中的反应物料中的加氢催化剂II的平均含量通过床层密度差计算得到。加氢催化剂I的用量是以煤焦油全馏分为基准且以加氢催化剂I中金属的氧化物计的。本发明使用中低温干馏生产兰炭过程中产生的焦油作为以下实施例和对比例中的煤焦油全馏分,煤焦油全馏分的性质如表1中所示。表1煤焦油全馏分煤焦油全馏分密度(20℃)/(g/cm3)1.083四组分(残炭)/重量%2.65(饱和分)/重量%36.6(水分)/重量%2.25(芳香分)/重量%21.2(灰分)/重量%0.103(胶质)/重量%37.6元素(沥青质)/重量%4.6(C)/重量%84.73馏程分布/重量%(H)/重量%10.52IBP-180℃0(S)/重量%0.14180-350℃40.30(N)/重量%0.47350-500℃53.27(O)/重量%3.47>500℃6.43(金属)/(μg/g)128.3实施例1-4用于说明本发明的方法。实施例1本实施例的二级浆态床反应器的结构如图2中所示,具体的操作方法如本发明的上述优选的具体实施方式所述。本实施例中,套筒的长度为所述二级浆态床反应器内腔的长度的3/5;套筒的内径为300mm,反应器内腔的内径为5000mm,所述导管伸入所述套筒内部的长度为200mm,底流管的长度为100mm,所述浆态床反应器内腔的长度与所述浆态床反应器内腔的内径之比为10:1。旋液分离器设置为两级,两级旋液分离器的容积相同,且各个旋液分离器的容积与浆态床反应器内腔的容积之比为1:800。控制氢气的流量,使得二级浆态床反应器的内腔中的反应物料在套筒外的向下流动的平均速率为0.2m/s。所述反应物料在经过所述旋液分离器的入口时的速率为8m/s。本实施例的一级浆态床反应器与二级浆态床反应器的结构相似,所不同的是,其中不含有旋液分离器。且一级浆态床反应器与二级浆态床反应器的反应器内腔的容积相同。本实施例中的加氢催化剂I为Fe系负载型催化剂,具体的组成为:以活性金属计,Fe含量为5.0重量%,其余为载体活性炭。所述加氢催化剂I的平均粒径为80μm。本实施例中的加氢催化剂II的组成为:以加氢催化剂II的总重量计,Fe以氧化物计的含量为25重量%,Mo以氧化物计的含量为8.0重量%,Ca以氧化物计的含量为0.8重量%,其余为基质。所述加氢催化剂II的平均粒径为100μm。固定床加氢处理单元采用小型连续固定床加氢实验装置进行加氢处理,依次装填的催化剂为中国石化催化剂分公司生产的RN-32V和RHC-131,配比为1:1。本实施例的一级浆态床反应器中的相关反应条件和结果如表2中所示;二级浆态床反应器中的相关反应条件和结果如表3中所示;固定床加氢处理单元的相关反应条件和结果如表4中所示,产品性质如表5中所示。表2表3实施例1实施例2实施例3实施例4反应条件压力/MPa18.018.020.020.0温度/℃380380400400液时体积空速/h-10.20.50.10.3氢油体积比1000100015001500反应结果/重量%气体1.041.540.961.35贫固含量组分99.0598.5299.3198.76外甩尾渣1.461.620.760.84贫固含量油相性质(S)/(μg/g)84957478(N)/(μg/g)163178145156(金属)/(μg/g)0.41.20.71.6表4实施例1实施例2实施例3实施例4反应条件压力/MPa12.014.01315温度/℃380390350360液时体积空速/h-10.60.80.80.8氢油体积比800800600600产品分布/重量%气体(C1-C4),H2O3.832.23.173.42汽油馏分(C5-180℃)24.130.3522.124.3柴油馏分(180-350℃)72.8868.4275.5873.23加氢渣油(>350℃)1.192.030.891.13表5实施例2-4实施例2-4采用与实施例1相同的工艺流程进行,所不同的是,工艺条件不同,具体地,实施例2-4的一级浆态床反应器中的相关反应条件和结果如表2中所示;二级浆态床反应器中的相关反应条件和结果如表3中所示;固定床加氢处理单元的相关反应条件和结果如表4中所示,产品性质见表5。对比例1本对比例采用内环流浆态床小型连续实验装置考察煤焦油全馏分在两级传统浆态床加氢裂化条件下的转化反应。其中使用环烷酸铁作为一级浆态床加氢裂化反应的催化剂,加入量为煤焦油全馏分原料的1.5%(以金属计),具体反应条件如表6所示。在一级浆态床加氢裂化反应后将得到的液相产物进行二级浆态床加氢裂化反应,采用异辛酸钼作为二级浆态床加氢裂化反应的催化剂,加入量为1000μg/g(以煤焦油全馏分原料计),具体条件如表6所示。以新鲜进料为100%计,两次反应的综合反应产物分布如表7,经过两次反应,产物气体收率较高,且未转化油收率也较高,影响后续固定床加氢处理反应的液体收率,进而影响整体工艺的经济性。二级反应后的产物经过过滤后,测定其中金属含量为67.2μg/g,机械杂质含量为0.15重量%。经过传统浆态床的二级反应,高分散催化剂残留在浆态床反应产品中,难以通过过滤的方式去除,影响后续固定床加氢反应。表6一级浆态床反应二级浆态床反应反应条件反应压力/MPa18.016.0反应温度/℃440400催化剂用量1.5重量%1000μg/g液时体积空速/h-12.01.0氢油体积比15001500表7产品分布/重量%气体(C1-C4),H2O10.83汽油馏分(C5-180℃)16.02柴油馏分(180-350℃)35.88蜡油馏分(350-524℃)31.4未转化油(>524℃)9.74从上述实施例和对比例的结果可以看出,采用本发明的方法在经过一级浆态床反应器的临氢裂化反应,煤焦油全馏分中绝大部分金属、灰分和水分均可以得到有效分离。提高反应温度,能提高一级浆态床反应器的脱金属效率。而且,在深度加氢转化反应过程中,在低温、低空速的条件下,利用高活性催化剂可以在脱去进料中S、N和金属的同时,对产品分布进行灵活调整,达到固定床加氢处理的进料条件。另外,经过固定床加氢处理单元中的加氢处理反应,汽油馏分的S、N含量低,辛烷值高;柴油馏分的十六烷值高,可以将煤焦油全馏分最大化地转化为优质清洁汽油或车用柴油的调和组分。以上详细描述了本发明的优选实施方式,但是,本发明并不限于上述实施方式中的具体细节,在本发明的技术构思范围内,可以对本发明的技术方案进行多种简单变型,这些简单变型均属于本发明的保护范围。另外需要说明的是,在上述具体实施方式中所描述的各个具体技术特征,在不矛盾的情况下,可以通过任何合适的方式进行组合,为了避免不必要的重复,本发明对各种可能的组合方式不再另行说明。此外,本发明的各种不同的实施方式之间也可以进行任意组合,只要其不违背本发明的思想,其同样应当视为本发明所公开的内容。当前第1页1 2 3