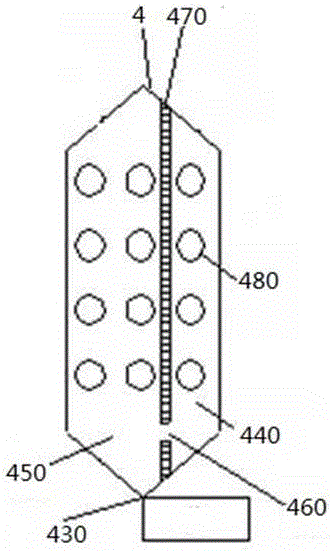
本实用新型属于垃圾热解
技术领域:
,主要是一种垃圾热解和裂解系统,用于制取清洁可燃气。
背景技术:
:随着我国现代化进程的加速,城市生活垃圾已经成为制约绿色城市快速发展的一个重要因素。目前,世界各国城市垃圾处理方式主要包括卫生填埋、焚烧、堆肥、热解以及垃圾综合处理等。而我国相关的垃圾分类、垃圾综合利用技术滞后,目前垃圾的主要处理方式为卫生填埋为主,焚烧、堆肥等方式为辅。并且,随着科技进步和环保意识的增强,“焚烧法”和“填埋法”给环境带来的破坏作用及威胁人类的身体健康已越来越被人们认识到。目前,垃圾热解处理技术主要有耦合流化床热解工艺、卧式垃圾连续焚烧工艺等等。垃圾热解处理技术是指将垃圾在的无氧或缺氧的状态下加热,使之分解。在热解过程中,其中间产物趋向于两极化变化:一种是从大分子裂解为小分子的裂解过程、另一种是小分子聚合为大分子的缩聚过程。在低温干燥阶段,垃圾中所含的外水和毛细结构吸附的水分首先被加热蒸发,其次物质中的结构水受热分解。随着水分的蒸发和热解干馏温度的升高,垃圾热解进入干馏阶段。干馏阶段主要发生内部水和CO2的析出、脱氧、脱硫等反应。由于我国垃圾分类措施不完善,致使垃圾本身成分异常复杂,常含有厨余物、塑料、废旧电池、电路板等等。同时发现垃圾热解产生的焦油成分亦异常复杂,成分分析发现焦油中含有上百种中物质,包括各种有机酸、酚类、酮类、醛类、PAHs等,其中氯元素和重金属元素普遍偏高,含水量大约20%,热值约13~18MJ/Kg,同时因硫化物含量高而导致恶臭,综合利用难度大。诸多因素致使我国垃圾热解、垃圾综合利用技术很难取得重大突破。因此,如何设计一种高效生产清洁可燃气成为本领域亟需解决的问题。技术实现要素:本实用新型针对现有技术的不足,设计并开发一种垃圾热解和裂解系统,该反应系统可进行热解和裂解两种作业,热解室产生的油气,可以进入裂解室进行深度裂解,将大分子的焦油分子裂解为小分子的气态烃类,该反应器可产生大量的裂解气,从而避免了生产热解油难以利用的问题,真正的实现了垃圾无害化处理和二噁英零排放,变废为宝,满足和解决了我国垃圾综合处理的技术需求。为解决上述技术问题,本实用新型采用的技术方案为:本实用新型提供了一种垃圾热解和裂解系统,根据本实用新型的实施例,该系统包括:料斗;进料器,所述进料器与所述料斗连接;热解和裂解反应器,包括:进料口、热解室、裂解室和裂解气出口,所述进料口设置在所述热解室的顶壁上,所述裂解气出口设置在所述裂解室的侧壁上;以及:蓄热式辐射管,所述蓄热式辐射管沿所述反应器的高度方向多层布置在所述热解室和所述裂解室内部,每层具有多根沿水平方向布置的所述蓄热式辐射管;隔热砖墙,所述隔热砖墙设置在所述反应器横向宽度的2/3处,竖直地贯穿于所述反应器内,将所述反应器的内部空间分隔成所述热解室和所述裂解室;连通构件,所述连通构件设置在所述隔热砖墙的下部,用于将所述热解室产生的油气,通过所述连通构件,通入到所述裂解室;喷淋塔,所述喷淋塔与所述裂解气出口连接;干燥器,所述干燥器与所述喷淋塔连接;燃气罐,所述燃气罐与所述干燥器连接。发明人发现,根据本实用新型实施例的系统工艺简单,操作方便,该反应系统可进行热解和裂解两种作业,热解室产生的油气,可以进入裂解室进行深度裂解,将大分子的焦油分子裂解为小分子的气态烃类,产生大量的裂解气,从而避免了生产热解油难以利用的问题,真正的实现了垃圾无害化处理和二噁英零排放,变废为宝,满足和解决了我国垃圾综合处理的技术需求。同时,该反应器采用了蓄热式辐射管加热技术无需气、固热载体加热,提高了反应器的热效率的同时简化了系统工艺。根据本实用新型的实施例,所述连通构件为设置在所述隔热砖墙上的包括多个孔的孔带;或者所述连通构件为所述隔热砖墙纵向长度上,位于下部位置的开口。根据本实用新型的实施例,所述隔热砖墙的厚度为5-15cm,所述孔带的高度为3-15cm,所述孔的直径为1-3cm,所述开口的高度为3-15cm。根据本实用新型的实施例,所述系统进一步包括燃气引风机,其中,所述燃气引风机一端与所述喷淋塔的出口连接,另一端与所述燃气罐进口连接。根据本实用新型的实施例,所述系统还包括压缩脱水器,所述压缩脱水器与所述料斗相连;气化炉,所述气化炉分别与所述蓄热式辐射管的燃气入口和半焦输送装置连接。根据本实用新型的实施例,所述系统还包括废热锅炉,所述废热锅炉与所述蓄热式辐射管的烟气出口相连接。根据本实用新型的实施例,所述料斗通过所述进料器与所述进料口相连。根据本实用新型的实施例,所述系统还包括半焦出口,所述半焦出口设置在所述热解室的下部,所述半焦出口与所述半焦输送装置连接。在本实用新型的另一个方面,本实用新型提供了一种利用前面所述的系统进行垃圾热解和裂解的方法。根据本实用新型的实施例,该方法包括以下步骤:a.将垃圾颗粒通过进料口加入到反应器中,在所述反应器的热解室中完成热解过程;b.热解产生的油气,通过所述反应器隔热砖墙上设置的连通构件,进入到所述反应器的裂解室;c.所述热解产生的油气在所述裂解室内完成热裂解过程,产生裂解气;d.所述裂解气通过裂解气出口进入到喷淋塔中,对所述裂解气进行净化处理;e.经净化的净裂解气进入干燥器中,对净裂解气进行干燥处理;f.干燥后的裂解气经燃气引风机进入燃气罐中,进行储存。根据本实用新型的实施例,所述步骤a中,所述垃圾颗粒从所述反应器上部的所述进料口加入到所述反应器中,并被所述反应器内的蓄热式辐射管打散,热解半焦从所述反应器底部的半焦出口排出;所述步骤a中,所述垃圾颗粒被所述反应器热解室中的所述蓄热式辐射管加热到500-600℃,所述步骤b中,所述热解油气被所述反应器裂解室中的所述蓄热式辐射管加热到650-900℃;优选的,所述垃圾颗粒的粒度为10mm以下。本实用新型的有益效果在于:1)采取蓄热式辐射管下行床工艺加热10mm以下的垃圾,温度分布均匀,加热效果好,反应系统结构简单,操作方便;2)反应器分为热解室和裂解室,热解室产生的油气,可在裂解室进行深度裂解,大分子的焦油分子裂解为小分子的气态烃类;3)该反应系统可产生大量的裂解气产品,避免了热解油难以利用的问题,真正实现了垃圾的无害化处理,变废为宝;4)垃圾低温热解,实现了二噁英零排放;5)一个炉体内可进行两种作业,合二为一,节省建造成本和占地面积。附图说明图1为本实用新型垃圾热解和裂解系统的结构图。图2为本实用新型垃圾热解和裂解系统的反应器结构图。图3为本实用新型反应器中的隔热砖墙的正视图。其中,1.压缩脱水器;2.料斗;3.进料器;4.蓄热式下行床反应器;410.裂解气出口;411.烟气出口;420.进料口;421.空气入口;422.燃气入口;430.半焦出口;440.裂解室;450.热解室;460.连通构件;470.隔热砖墙;480.蓄热式辐射管;5.喷淋塔;6.干燥器;7.燃气引风机;8.燃气罐;9.气化炉;10.螺旋输送机;11.废热锅炉。具体实施方式为了使本领域技术人员更好地理解本实用新型的技术方案,下面结合具体实施例对本实用新型作进一步的详细说明。下面描述的实施例是示例性的,仅用于解释本实用新型,而不能理解为对本实用新型的限制。实施例中未注明具体技术或条件的,按照本领域内的文献所描述的技术或条件或者按照产品说明书进行。根据本实用新型的一个方面,本实用新型提供了一种垃圾热解和裂解系统,图1为垃圾热解和裂解系统的结构图,如图1所示,该系统包括料斗2、进料器3,所述料斗2和所述进料器3连接;热解和裂解反应器4,所述热解和裂解反应器4包括:进料口420、热解室450、裂解室440、裂解气出口410、蓄热式辐射管480、隔热砖墙470、连通构件460,其中,所述进料口设置在所述热解室的顶壁上,所述裂解气出口设置在所述裂解室的侧壁上,所述隔热砖墙竖直地贯穿于所述反应器内,将所述反应器的内部空间分隔成所述热解室和所述裂解室,所述连通构件设置在所述隔热砖墙上,将热解室和裂解室连通,优选的,所述连通构件设置在所述隔热砖墙的下部,用于将所述热解室产生的油气,通过所述连通构件,通入到所述裂解室;喷淋塔5,所述喷淋塔与所述裂解气出口连接;干燥器6,所述干燥器与所述喷淋塔连接;燃气罐8,所述燃气罐与所述干燥器连接。发明人发现,根据本实用新型实施例的系统工艺简单,操作方便,该反应系统可进行热解和裂解两种作业,热解室产生的油气,可以进入裂解室进行深度裂解,将大分子的焦油分子裂解为小分子的气态烃类,产生大量的裂解气,从而避免了生产热解油难以利用的问题,真正的实现了垃圾无害化处理和二噁英零排放,变废为宝,满足和解决了我国垃圾综合处理的技术需求。同时,该反应器采用了蓄热式辐射管加热技术无需气、固热载体加热,提高了反应器的热效率的同时简化了系统工艺。根据本实用新型的具体实施例,适用于该垃圾热解和裂解系统的垃圾的具体粒径不受特别限制,根据本实用新型的实施例,垃圾可以为块状也可以为小颗粒,在本实用新型的一些优选实施例中,该反应器采用的垃圾颗粒的粒度为10mm以下,由此,可以充分利用小颗粒垃圾,资源利用率高,且能够解决大量堆积污染环境的问题。根据本实用新型的具体实施例,适用于该系统的所述反应器4的炉型不受特别限制,可以是蓄热式下行床热解和裂解反应器4也可以是其它类型,如非蓄热式或非移动式等,只要能通过隔热砖墙一体化的分割为热解室和裂解室即可。在本实用新型的一些优选实施例中,该反应器4采用蓄热式下行床反应器4。根据本实用新型的具体实施例,图2为该垃圾热解和裂解系统的热解和裂解反应器结构图,如图2所示,所述隔热砖墙设置在反应器内,优选的,位于反应器横向宽度的2/3处,隔热砖墙的厚度为5-15cm。隔热砖墙竖直地贯穿于反应器内,将反应器的内部空间分隔成热解室和裂解室,该结构使得在一个炉体内设置了热解室和裂解室,热解室产生的油气,可以进入裂解室进行深度裂解,将大分子的焦油分子裂解为小分子的气态烃类,产生大量的裂解气,从而避免了生产热解油含尘的问题。并且,一个炉体内可进行两种作业,合二为一,节省建造成本和占地面积。根据本实用新型的具体实施例,所述连通构件460的具体种类不受特别限制,只要可以将热解室和裂解室连通,从而将热解室产生的油气通入到裂解室即可。在本实用新型的一些实施例中,图3为从反应器的左向右看时,隔热砖墙的正视图,如图3所示,连通构件可以为设置在隔热砖墙上的包括多个孔的孔带,优选情况下,所述孔带的高度为3-15cm,所述孔的直径为1-3cm。连通构件也可以为隔热砖墙纵向长度上,位于下部位置的开口,优选情况下,所述开口的高度为3-15cm。根据本实用新型的具体实施例,如图1所示,所述进料口设置在热解室上部的顶壁上,料斗通过进料器与所述进料口相连。根据本实用新型的实施例,如图1所示,该系统可以进一步包括:压缩脱水器1、料斗和进料器,所述压缩脱水器的出口与所述料斗的入口连接,所述料斗的出口与所述进料器的入口连接,所述进料器的出口与所述进料口连接。根据本实用新型的实施例,压缩脱水器的具体种类不受特别限制,只要可以将筛选后的有机垃圾有效地进行脱水处理即可。根据本实用新型的实施例,进料器的具体种类不受特别限制,只要可以将料斗中的垃圾颗粒有效地输送至反应器中即可。在本实用新型的一些实施例中,进料器可以为星形送料机或螺旋送料机,优选情况下,进料器可以为螺旋送料机。由此,能够实现对热加料的自动化输送,输送量可控,且设备结构简单,操作方便。根据本实用新型的具体实施例,如图1所示,所述反应器进一步还包括半焦出口430,所述半焦出口设置在所述热解室的下部,所述半焦出口与所述半焦输送装置10连接。由此,可以利用半焦输送装置将反应器中获得的半焦进行输送。半焦输送装置的具体种类不受特别限制,包括但不限于星形或螺旋输送机10。由此,能够实现对半焦的自动化输送,且输送量可控,设备结构简单,操作方便。根据本实用新型的实施例,参照图2,所述反应器内部布置有多层沿所述反应器的高度方向布置在所述热解室和所述裂解室内部的蓄热式辐射管,每层蓄热式辐射管可以包括多个彼此平行且沿水平方向间隔分布的蓄热式辐射管。根据本实用新型的实施例,所述热解室和裂解室内分别分布了至少一根所述蓄热式辐射管,优选的,所述至少一根蓄热式辐射管均匀分布。蓄热式辐射管能够有效用于对热解料和裂解室内的油气进行加热,使其进行热解和裂解反应,具体地,可以向蓄热式辐射管内通入可燃气和空气,使可燃气燃烧实现对热解料和裂解室内的油气的加热功能。该反应器采用蓄热式辐射管加热技术,无需气、固热载体加热,热解气不会被稀释,热值高,且反应器内温度分布均匀,表面温差小,排烟温度低,热效率高,提高了反应器的热效率的同时简化了系统工艺,反应系统结构简单,操作方便。根据本实用新型的实施例,在所述反应器的热解室中,热解料自上而下运动,所述反应器中设置的蓄热式辐射管可以将热解料打散使其均匀分布。根据本实用新型的实施例,蓄热式辐射管的形状不受特别限制,在本实用新型的一些实施例中,可以为圆柱形,由此有利于热解料的打散,实现混合热解料在热解室中的均匀分散。辐射管的水平间距为200-500mm,垂直间距为200-700mm,辐射管层数为10-25层,反应器宽度为2-6m,反应器高度为3-20m。另外,蓄热式辐射管可以为均匀布置的单向蓄热式辐射管,管壁温度利用燃气调节阀控制在500~700℃范围,物料在反应器中自上而下停留1-50分钟,并加热到500~600℃,完成热解过程。同时,蓄热式辐射管可以采取定期换向的燃烧方式,使得单根蓄热式辐射管的表面温差只有30摄氏度左右,没有局部高温区,由此,有利于提高热效率。根据本实用新型的具体实施例,所述反应器设有燃气入口422、空气入口421以及烟气出口411,其中,燃气入口和烟气出口分别与蓄热式辐射管连接,分别用于通入可燃气和排出烟气,空气入口分别与气源和蓄热式辐射管连接,用于将气源产生的空气通入蓄热式辐射管中。由此,可以通过燃气入口将热解室中获得半焦输送至气化炉中,对半焦进行气化处理,以获得可燃气和灰渣,得到的可燃气可以通过燃气入口进入到蓄热式辐射管中,同时,可以通过空气入口来使用风机向蓄热式辐射管中通入空气,使可燃气燃烧对热解室中的热解料进行加热。另外,通过烟气出口将蓄热式辐射管中的烟气输送到废旧锅炉中,回收烟气,使烟气不会排放到空气中。由此,可以对半焦进行充分的利用,不造成浪费,经济性好,并且,对烟气进行回收,不造成环境污染,绿色环保。根据本实用新型的实施例,如图1所示,该系统可以进一步包括:喷淋塔,所述喷淋塔设置在所述裂解室的裂解气出口和所述干燥器之间。所述喷淋塔的入口与所述裂解室的裂解气出口连接,所述喷淋塔的出口与所述干燥器的入口连接。喷淋塔的具体种类不受特别限制,只要能够洗涤净化裂解气即可。根据本实用新型的实施例,如图1所示,该系统可以进一步包括:干燥器,所述干燥器设置在所述喷淋塔和所述燃气罐之间。所述干燥器的入口与所述喷淋塔的出口连接,所述喷淋塔的出口与所述燃气罐的入口连接。干燥器的具体种类不受特别限制,只要能够干燥裂解气即可。根据本实用新型的实施例,如图1所示,该系统可以进一步包括:燃气引风机7,其中,所述燃气引风机布置在所述干燥器和所述燃气罐之间。所述燃气引风机入口与所述干燥器的出口连接,所述燃气引风机出口与所述燃气罐进口连接。根据本实用新型的实施例,如图1所示,该系统可以进一步包括:燃气罐,所述燃气罐设置在所述燃气引风机的一端。所述燃气罐的入口与所述燃气引风机的出口连接。燃气罐的具体种类不受特别限制,只要能够储存裂解气即可。根据本实用新型的实施例,如图1所示,该系统可以进一步包括:气化炉9,所述气化炉设置在所述蓄热式辐射管的燃气入口和半焦输送装置之间。所述气化炉入口与所述半焦输送装置的出口连接,所述气化炉出口与所述蓄热式辐射管的燃气入口连接。气化炉的具体种类不受特别限制,只要能够将半焦进行气化处理,以获得可燃气和灰渣即可,并且,气化后得到的灰渣排出,得到的可燃气可以通过蓄热式辐射管的燃气入口进入到蓄热式辐射管中,通过可燃气燃烧对热解室中的热解料进行加热。由此,能够实现对半焦进行充分的利用,不造成浪费,经济性好。根据本实用新型的实施例,如图1所示,该系统可以进一步包括:废热锅炉11,所述废热锅炉设置在所述蓄热式辐射管的烟气出口一端。所述废热锅炉的入口与所述蓄热式辐射管的烟气出口相连接。废旧锅炉的具体种类不受特别限制,只要能够回收烟气即可。由此,对烟气进行回收,不造成环境污染,绿色环保。在本实用新型的另一个方面,本实用新型提供了一种利用前面所述的系统进行垃圾热解和裂解的方法。根据本实用新型的实施例,该方法包括以下步骤:a.将垃圾颗粒通过进料口加入到反应器中,在所述反应器的热解室中完成热解过程。其中,所述垃圾经过压缩脱水器脱水处理后,经过料斗进入进料器,再从反应器上部的进料口加入到蓄热式下行床反应器中,并被所述反应器内的蓄热式辐射管打散,热解半焦从反应器底部的半焦出口排出,并经半焦输送装置(优选为螺旋输送机)排出。根据本实用新型的具体实施例,适用于该垃圾热解和裂解系统的垃圾的具体粒径不受特别限制,根据本实用新型的实施例,垃圾可以为块状也可以为小颗粒,在本实用新型的一些优选实施例中,该反应器采用的垃圾颗粒的粒度为10mm以下,由此,可以充分利用小颗粒垃圾,资源利用率高,且能够解决大量堆积污染环境的问题。根据本实用新型的实施例,在热解室中,垃圾颗粒自上而下运动,热解室中设置的15蓄热式辐射管可以将垃圾颗粒打散使其均匀分布,垃圾颗粒在反应器中自上而下停留1-50分钟,垃圾颗粒被反应器热解室中的蓄热式辐射管加热到500~600℃。具体的,可以通过燃气阀控制蓄热式辐射管管壁的温度在500~700℃范围,并加热到500~600℃,完成热解过程。b.热解产生的油气,通过所述反应器隔热砖墙上设置的连通构件,进入到所述反应器的裂解室。根据本实用新型的实施例,隔热砖墙设置在反应器内,优选的,位于反应器横向宽度的2/3处,隔热砖墙的厚度为5-15cm,隔热砖墙竖直地贯穿于反应器内,将反应器的内部空间分隔成热解室和裂解室,该结构使得在一个炉体内设置了热解室和裂解室,热解室产生的油气,可以进入裂解室进行深度裂解,将大分子的焦油分子裂解为小分子的气态烃类。由此,一个炉体内可进行两种作业,合二为一,节省建造成本和占地面积。根据本实用新型的实施例,连通构件可以为设置在隔热砖墙上的包括至少一个孔的孔带,也可以为隔热砖墙纵向长度上,位于下部位置的开口。具体的,热解产生的油气,通过反应器隔热砖墙下部的孔带或者开口,进入到裂解室。c.所述热解产生的油气在所述裂解室内完成热裂解过程,产生裂解气。根据本实用新型的实施例,所述裂解室内分布了至少一根蓄热式辐射管,优选的,所述至少一根蓄热式辐射管均匀分布。蓄热式辐射管能够有效用于对裂解室内的油气进行加热,使其进行裂解反应。在本实用新型的一些优选实施例中,热解油气被反应器裂解室中的蓄热式辐射管加热到650-900℃,具体地,可以通过燃气阀控制蓄热式辐射管管壁的温度为650~900℃,垃圾颗粒在反应器中迅速被加热至650-900℃,完成热裂解过程,由此,大分子的焦油分子裂解为小分子的气态烃类,产生大量的裂解气,避免了生产热解油难以利用的问题,真正实现了垃圾的的无害化处理和二噁英零排放,变废为宝。由此,真正实现了垃圾的清洁高效利用。d.所述裂解气通过裂解气出口进入到喷淋塔中,对所述裂解气进行净化处理。根据本实用新型的实施例,与裂解气出口连接的是喷淋塔,所述的喷淋塔是用于将裂解气出口排出的裂解气进行洗涤净化处理。具体的,裂解气通过裂解气出口进入喷淋塔,进行洗涤净化处理,得到净化后的净裂解气,从而避免了生产热解油含尘的问题,真正实现了垃圾的清洁高效利用。e.经净化的净裂解气进入干燥器中,对所述净裂解气进行干燥处理。根据本实用新型的实施例,与喷淋塔相连的还有干燥器,所述干燥器是用于干燥净化后的净裂解气,净化后的净裂解气进入干燥器进行干燥处理,得到干燥的裂解气。f.干燥后的裂解气经燃气引风机进入燃气罐中,进行储存。根据本实用新型的实施例,与干燥器相连的还有燃气罐,所述燃气罐是用于储存裂解气的,干燥后的裂解气经燃气引风机送入燃气罐,进行储存。实施例一:(1)经过剔除不易热解或者不能热解的物质后破碎至粒度≤10mm的垃圾,进入压缩脱水器1中,压缩脱水后的垃圾送入料斗2中经进料器3进入蓄热式下行床反应器4,下行床反应器4被隔热砖墙分为热解室和裂解室。(2)热解室中均匀布置了单向蓄热式辐射管,管壁温度利用燃气调节阀控制在500~700℃范围,垃圾在反应器中自上而下停留1-50分钟,并加热到500~600℃,完成热解过程。(3)热解产生的油气,通过反应器下部隔热砖墙的开口,进入到裂解室,裂解室中均匀布置了单向蓄热式辐射管,管壁温度利用燃气调节阀控制在650~900℃范围,热解油气在裂解室内被加热到650-900℃,完成热裂解过程,大分子的焦油分子裂解为小分子的气态烃类,产生大量的裂解气,避免了热解油难以利用的问题,真正实现了垃圾的的无害化处理和二噁英零排放,变废为宝。(4)裂解气通过反应器出口,进入喷淋塔5中洗涤净化,洗涤后的净裂解气进入干燥器6中进行干燥处理,干燥后的裂解气经燃气风机7送入燃气罐8,可用于生产人造天然气等产品。(5)垃圾热解产生的半焦,通过螺旋输送机10送入气化炉9,气化气可供给辐射管燃烧,气化后的灰渣排出。(6)蓄热式辐射管燃烧产生的烟气,进入废热锅炉11回收热量,产生高品质蒸汽。发明人发现,根据本实用新型实施例的系统结构简单,操作方便,温度分布均匀,加热效果好。反应器分为热解室和裂解室,热解室产生的油气,可以进入裂解室进行深度裂解,将大分子的焦油分子裂解为小分子的气态烃类,产生大量的裂解气,从而避免了生产热解油含尘的问题,真正实现了垃圾的的无害化处理和二噁英零排放,变废为宝。并且,该系统中将一个炉体内设置了热解室和裂解室,使得一个炉体内可进行两种作业,合二为一,节省建造成本和占地面积。同时,该反应器采用了蓄热式辐射管加热技术无需气、固热载体加热,提高了反应器的热效率的同时简化了系统工艺。利用垃圾热解和裂解系统对垃圾进行处理,原料的基础数据见表1。表1:垃圾基础数据。某城市生活垃圾含水量为51%。项目织物塑料纸木材厨余渣土玻璃、金属总计湿基4.9721.3517.765.9821.2316.6312.08100利用该反应系统处理垃圾,得到的气体产品产率为40%,热解焦油几乎全部裂解为气态产物,产气率高。在本实用新型的描述中,需要理解的是,术语“第一”、“第二”仅用于描述目的,而不能理解为指示或暗示相对重要性或者隐含指明所指示的技术特征的数量。由此,限定有“第一”、“第二”的特征可以明示或者隐含地包括一个或者更多个该特征。在本实用新型中,除非另有明确的规定和限定,术语“安装”、“相连”、“连接”、“固定”等术语应做广义理解,例如,可以是固定连接,也可以是可拆卸连接,或成一体;可以是机械连接,也可以是电连接;可以是直接相连,也可以通过中间媒介间接相连,可以是两个元件内部的连通或两个元件的相互作用关系。对于本领域的普通技术人员而言,可以根据具体情况理解上述术语在本实用新型中的具体含义。在本实用新型中,除非另有明确的规定和限定,第一特征在第二特征“上”或“下”可以是第一和第二特征直接接触,或第一和第二特征通过中间媒介间接接触。而且,第一特征在第二特征“之上”、“上方”和“上面”可是第一特征在第二特征正上方或斜上方,或仅仅表示第一特征水平高度高于第二特征。第一特征在第二特征“之下”、“下方”和“下面”可以是第一特征在第二特征正下方或斜下方,或仅仅表示第一特征水平高度小于第二特征。在本说明书的描述中,参考术语“一个实施例”、“一些实施例”、“示例”、“具体示例”、或“一些示例”等的描述意指结合该实施例或示例描述的具体特征、结构、材料或者特点包含于本实用新型的至少一个实施例或示例中。在本说明书中,对上述术语的示意性表述不必针对的是相同的实施例或示例。而且,描述的具体特征、结构、材料或者特点可以在任一个或多个实施例或示例中以合适的方式结合。此外,在不相互矛盾的情况下,本领域的技术人员可以将本说明书中描述的不同实施例或示例以及不同实施例或示例的特征进行结合和组合。尽管上面已经示出和描述了本实用新型的实施例,可以理解的是,上述实施例是示例性的,不能理解为对本实用新型的限制,本领域的普通技术人员在本实用新型的范围内可以对上述实施例进行变化、修改、替换和变型,同时,对于本领域的一般技术人员,依据本申请的思想,在具体实施方式及应用范围上均会有改变之处。当前第1页1 2 3