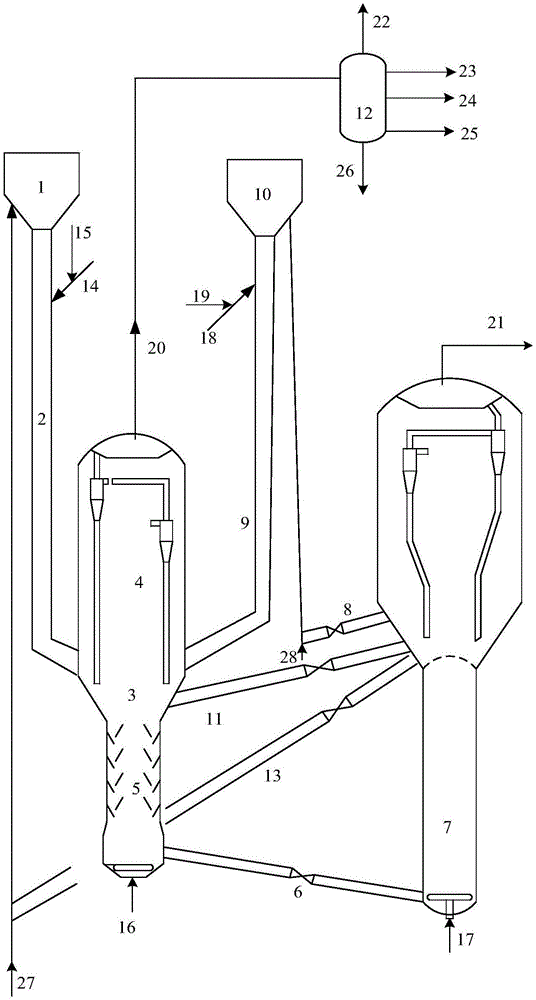
本发明涉及一种采用双下行管进行催化裂解的工艺和系统。
背景技术:
:乙烯、丙烯和丁烯等小分子烯烃是最基本的有机合成原料。目前世界范围内小分子烯烃主要的生产工艺为蒸汽裂解工艺,但是高温裂解炉易结焦,所以该工艺基本上以轻质油为原料,例如天然气、石脑油、轻质柴油,也可以加氢裂化尾油为原料。目前我国原油重质化、劣质化的趋势越发明显,石脑油等轻质油收率变低,蒸汽裂解工艺与催化重整工艺的原料供需矛盾日益严重。自二十世纪八十年代中期以来,中国石化股份有限公司石油化工科学研究院就开始从事重油制取低碳烯烃的催化裂解家族技术的研究,并成功地开发出了最大量生产丙烯的催化裂解(dcc,usp4980053和usp5670037)技术和最大量生产乙烯的催化热裂解(cpp,usp6210562)。迄今为止,此两种技术主要是用单个提升管反应器或单个提升管反应器组合密相流化床的反应器结构,提高低碳烯烃产率的同时干气和焦炭产率也偏高。近年来,采用多个反应器进行重油裂解多产低碳烯烃的技术受到较大的关注,这些技术都是为不同的原料选择不同的反应器,包括上行式反应器、下行式反应器,甚至选择不同的催化剂,保证各种原料在更适合自身特性的反应环境下进行反应。中国专利cn101074392a公开了一种利用两段催化裂解生产丙烯和高品质汽柴油的方法,该方法主要是利用两段提升管催化工艺,采用富含择形沸石的催化剂,以重质石油烃类或富含碳氢化合物的各种动植物油类为原料,针对不同性质的反应物料进行进料方式的优化组合,控制不同物料适宜的反应条件,以达到提高丙烯收率、兼顾轻油收率和质量、抑制干气和焦炭生成的目的。其具体提出第一段提升管进料为新鲜重质原料油,其下部或底部可以进轻质烃类原料;第二段提升管进料为高烯烃含量的汽油和循环油,可以分层进料或混合进料,其下部或底部可以进其他轻质烃类原料。中国专利cn101045667a提出了一种提高低碳烯烃产率的催化转化方法,该方法烃油原料经原料喷嘴注入下行式反应器内,与再生催化剂和任选的积炭催化剂接触,将裂化产物和待生催化剂分离,裂化产物分离后得到低碳烯烃,其余产物至少一部分引入提升管反应器内与再生剂接触反应,将油气与待生催化剂分离。该方法通过生成的低碳烯烃与待生剂及时分离,力图有效地抑制低碳烯烃的二次反应,提高低碳烯烃的产率。但是仅凭下行式反应器和提升管反应器难以满足重油和轻质烃类的转化率,也无法实现低碳烯烃产率的最大化,而且从该专利的实施例可以看出,低碳烯烃与干气产率比值在3以下,原料无法得到充分利用,低价值产物高。中国专利cn101210191a提出了一种下行式反应器和提升管反应器串联的催化裂化方法。预热后的原料油进入下行式反应器与来自再生器的高温再生催化剂接触,汽化并进行裂解反应,从下行式反应器出口出来的油气进入提升管反应器继续反应,从提升管反应器入口引入另一股再生催化剂,从提升管反应器出口出来的油气与催化剂进入沉降分离器分离。根据目标产品的不同,在提升管反应器可以采用与下行式反应器不同的催化剂,可以提高汽油收率,改善产品质量。但是轻烃没有进一步转化,因此低碳烯烃产率不会很高。中国专利cn102690682a提出一种生产丙烯的催化裂化方法,该方法中重质原料与以y型沸石为活性组分的第一催化剂在第一提升管中接触反应;轻质烃与以平均孔径小于0.7nm的择形沸石为活性组分的第二催化剂在第二提升管反应器内接触反应。将所得的油气引入与第二反应器串联的流化床反应器进行反应。所述催化裂化装置的汽提器用隔板分隔为两个独立汽提区,两个汽提区分别与两个提升管形成两个独立的反应、汽提和再生路线。技术实现要素:本发明的目的是提供一种采用双下行管进行催化裂解的工艺和系统,本发明的工艺和系统能够提高低碳烯烃产率的同时,减缓干气产率的增加。为了实现上述目的,本发明提供一种采用双下行管进行催化裂解的工艺,该工艺包括:a、将重质原料送入第一下行管反应器的上部与来自第一下行管反应器顶部的第一催化裂解催化剂接触并由上至下进行第一催化裂解反应,得到第一产物和第一半待生催化剂;b、将轻质原料送入第二下行管反应器的上部与来自第二下行管反应器顶部的第二催化裂解催化剂接触并由上至下进行第二催化裂解反应,得到第二产物和第二半待生催化剂;c、将步骤a中所得第一产物和第一半待生催化剂以及步骤b中所得第二产物和第二半待生催化剂送入流化床反应器中与第三催化裂解催化剂接触并进行第三催化裂解反应,得到第三产物和待生催化剂,将待生催化剂送入再生器中进行再生,得到再生催化剂。可选的,该工艺还包括步骤d:将再生器中的再生催化剂作为所述第一催化裂解催化剂、第二催化裂解催化剂和第三催化裂解催化剂分别送入所述第一下行管反应器的顶部、所述第二下行管反应器顶部和流化床反应器中。可选的,步骤d中,以单位时间内离开再生器的再生催化剂的总重量为基准,将10-70重量%的再生催化剂送入第一下行管反应器中,将20-60重量%的再生催化剂送入所述流化床反应器中,将10-40重量%的再生催化剂送入所述第二下行管反应器中。可选的,该工艺还包括:将所述第三产物送入产物分离装置进行产物分离,得到干气、液化气、汽油、柴油和油浆;将所得汽油和/或液化气作为所述轻质原料送入所述第二下行管反应器中进行所述第二催化裂解反应。可选的,该工艺还包括:将所述第三产物送入流化床反应器上部的沉降段中进行气固分离后送出所述沉降段,将待生催化剂送入流化床反应器下部的汽提段中进行汽提后送入再生器中。可选的,所述第一催化裂解反应的条件包括:温度为510-690℃,剂油比为5-20,反应时间为0.5-8秒;所述第二催化裂解反应的条件包括:温度为520-720℃,剂油比为8-26,反应时间为1-10秒;所述第三催化裂解反应的条件包括:温度为480-650℃,重时空速为1-35小时-1,反应压力为0.15-0.35兆帕。可选的,所述再生催化剂包括沸石、无机氧化物和可选的粘土;以再生催化剂的重量为基准,所述沸石的含量为1-50重量%,无机氧化物的含量为5-99重量%,粘土的含量为0-70重量%;所述沸石包括平均孔径小于0.7纳米的择型沸石和y型沸石;以干基计并以沸石总重量为基准,所述平均孔径小于0.7纳米的择型沸石为25-90重量%,所述y型沸石为10-75重量%,所述平均孔径小于0.7纳米的择型沸石为选自zsm系列沸石、zrp沸石、镁碱沸石、菱沸石、环晶石、毛沸石、a沸石、柱沸石和浊沸石中的至少一种,所述y型沸石为选自稀土y型沸石、稀土氢y型沸石、超稳y型沸石和稀土超稳y型沸石中的至少一种。可选的,所述重质原料为选自减压蜡油、常压蜡油、焦化蜡油、脱沥青油、糠醛精制抽余油、煤液化油、油砂油、页岩油、费托合成油和动植物油脂中的至少一种;所述轻质原料为富含烯烃的汽油和/或c4烃类。可选的,所述轻质原料中,c4烃类与富含烯烃的汽油的重量比为(0-2):1,引入第二下行管反应器的富含烯烃的汽油与引入第一下行管反应器的重质原料的重量比为(0.05-0.30):1。本发明还提供一种采用双下行管进行催化裂解的系统,该系统包括第一下行管反应器、流化床反应器、再生器和第二下行管反应器;所述第一下行管反应器设置有位于顶部的催化剂入口、位于上部的重质原料入口和位于底部的物料出口,所述第二下行管反应器设置有位于顶部的催化剂入口、位于上部的轻质原料入口和位于底部的物料出口,所述流化床反应器设置有催化剂入口、物料入口、催化剂出口和产物出口,所述再生器设置有催化剂入口和催化剂出口;所述第一下行管反应器的物料出口与所述流化床反应器的物料入口连通,所述第二下行管反应器的物料出口与所述流化床反应器的物料入口连通,所述再生器的催化剂入口与所述流化床反应器的催化剂出口连通,所述再生器的催化剂出口与所述流化床反应器的催化剂入口、第一下行管反应器的催化剂入口和第二下行管反应器催化剂入口连通。可选的,所述系统还包括产物分离装置,所述产物分离装置的入口与所述流化床反应器的产物出口连通,所述产物分离装置设置有干气出口、液化气出口、汽油出口、柴油出口和油浆出口,所述产物分离装置的液化气出口和/或汽油出口与所述第二下行管反应器的轻质原料入口连通。本发明基于第一下行管反应器、流化床反应器以及第二下行管反应器构成的组合反应器,通过工艺方案的优化,配备合适的催化剂,实现不同进料在合适的反应器进行催化裂解,有效提高重油转化率,促进轻质原料再次裂解,显著增加低碳烯烃产率,同时减缓干气产率的增加。本发明沿反应物料流动的方向设置第一下行管反应器和流化床反应器。利用第一下行管反应器,可以最大限度避免传统提升管反应器内催化剂返混现象,提高催化剂活性。向流化床反应器入口处补充来自于再生器的高温再生催化剂对流化床反应器的苛刻度(包括反应温度和剂油比)进行调控,强化重质原料在在流化床反应器中有效裂解为低碳烯烃和汽油烯烃能力,通过沉降段内的高效气固分离装置将反应产物与积炭的待生催化剂分离,可以使重质原料有效裂解为丙烯和汽油的同时,抑制低碳烯烃尤其丙烯在生成之后的再裂解反应。本发明将富含烯烃的汽油和/或c4烃类引入第二下行管反应器,利用第二下行管,同样可以最大限度避免传统提升管反应器内催化剂返混现象,提高催化剂活性,在促进轻汽油催化裂解提高低碳烯烃产率的同时可以减缓干气产率的提高。轻质原料反应过程中催化剂积炭量比较少,而且此待生催化剂仍有较高的活性,可引入流化床反应器中与重质原料接触并促进重质原料反应。本发明的其他特征和优点将在随后的具体实施方式部分予以详细说明。附图说明附图是用来提供对本发明的进一步理解,并且构成说明书的一部分,与下面的具体实施方式一起用于解释本发明,但并不构成对本发明的限制。在附图中:图1包括本发明工艺的一种具体实施方式的流程示意图,也包括本发明系统的一种具体实施方式的结构示意图。附图标记说明1催化剂罐2第一下行管反应器3流化床反应器4沉降段5汽提段6待生斜管7再生器8再生斜管9第二下行管反应器10催化剂罐11再生斜管12产物分离装置13再生斜管14管线15管线16管线17管线18管线19管线20管线21管线22管线23管线24管线25管线26管线27管线28管线具体实施方式以下结合附图对本发明的具体实施方式进行详细说明。应当理解的是,此处所描述的具体实施方式仅用于说明和解释本发明,并不用于限制本发明。如图1所示,本发明提供一种采用双下行管进行催化裂解的工艺,该工艺包括:a、将重质原料送入第一下行管反应器2的上部与来自第一下行管反应器2顶部的第一催化裂解催化剂接触并由上至下进行第一催化裂解反应,得到第一产物和第一半待生催化剂;b、将轻质原料送入第二下行管反应器9的上部与来自第二下行管反应器9顶部的第二催化裂解催化剂接触并由上至下进行第二催化裂解反应,得到第二产物和第二半待生催化剂;c、将步骤a中所得第一产物和第一半待生催化剂以及步骤b中所得第二产物和第二半待生催化剂送入流化床反应器3中与第三催化裂解催化剂接触并进行第三催化裂解反应,得到第三产物和待生催化剂,将待生催化剂送入再生器7中进行再生,得到再生催化剂。本发明工艺能够提高低碳烯烃产率的同时减缓干气产率的增加。根据本发明,待生催化剂需要进行再生,这是本领域技术人员所熟知的,因此,该工艺还可以包括:将所述第三产物送入流化床反应器3上部的沉降段4中进行气固分离后送出所述沉降段4,将待生催化剂送入流化床反应器3下部的汽提段5中进行汽提后送入再生器7中,进一步地该工艺还可以包括步骤d:将再生器7中的再生催化剂作为所述第一催化裂解催化剂、第二催化裂解催化剂和第三催化裂解催化剂分别送入所述第一下行管反应器2的顶部、所述第二下行管反应器9顶部和流化床反应器3中。需要说明的是,为了促进催化裂解反应的进行,多产低碳烯烃,送入各个反应器中作为第一催化裂解催化剂、第二催化裂解反应和第三催化裂解反应的再生催化剂均为未经过冷却的催化剂,即温度为500-900℃之间,优选为600-800℃之间。根据原料的不同,可以选择性地将不同重量的再生催化剂从所述再生器7送入流化床反应器3、第一下行管反应器2和第二下行管反应器9中,并优化反应的条件,步骤d中,以单位时间内离开再生器的再生催化剂的总重量为基准,可以将大于0至小于100重%,优选将10-70重量%的再生催化剂送入第一下行管反应器2中,可以将大于0至小于100重%,优选将20-60重量%的再生催化剂送入所述流化床反应器3中,可以将大于0至小于100重%,优选将10-40重量%的再生催化剂送入所述第二下行管反应器9中。本发明将轻质原料经过第二下行管反应器9和流化床反应器3中进行催化裂解,将重质原料依次经过第一下行管反应器2和流化床反应器3进行催化裂解,不仅能够对不同原料进行分别催化裂解,提高目标产物选择性,还可以将轻质原料裂解反应所得含碳量较低的第二半待生催化剂再次送入流化床反应器3进行裂解,和将再生催化剂送入流化床反应器中以提高催化剂平均活性,增加第一下行管反应器2和流化床反应器3催化裂解的转化率。根据本发明,为了将第三产物进行分离,该工艺还可以包括:将所述第三产物送入产物分离装置12进行产物分离,得到干气、液化气、汽油、柴油和油浆。所述产物分离装置12是本领域技术人员所熟知的,可以是分馏塔等。根据本发明,为了使催化裂解产物中的轻质烃类进行转化,该工艺还可以包括:将所得汽油和/或液化气作为所述轻质原料送入所述第二下行管反应器9中进行所述第二催化裂解反应。根据本发明,催化裂解是本领域技术人员所熟知的工艺,发明不再赘述,所述第一催化裂解反应的条件可以包括:温度(第一下行管反应器底部出口)为510-690℃,优选为520-650℃,剂油比为5-20,优选为7-18,重质原料进料雾化水蒸气占重质原料和雾化水蒸气重量之和的2-50重%,优选占5-15重%,反应时间为0.5-8秒,优选为1.5-4秒,引入第一下行管反应器与流化床反应器的催化剂之比为1:(1-3);所述第二催化裂解反应的条件可以包括:温度(第二下行管反应器底部出口)为520-720℃,优选为530-700℃,剂油比为8-26,优选为10-24,轻质原料进料雾化水蒸气占轻质原料和雾化水蒸气重量之和的2-50重%,优选占5-15重%,反应时间为1-10秒,优选为2-7秒;所述第三催化裂解反应的条件可以包括:温度为480-650℃,优选为500-640℃,重时空速为1-35小时-1,优选为2-33小时-1,剂油比为6-20,优选为7-18,反应压力(绝对压力,出口压力)为0.15-0.35兆帕,优选为0.2-0.35兆帕。根据本发明,用于催化裂解的催化剂是本领域技术人员熟知的,以再生催化剂为例,所述再生催化剂中的催化剂可以是由现有技术提供的催化剂的一种或几种的组合,可以商购或按照现有方法制备。一种具体实施方式,再生催化剂可以包括沸石、无机氧化物和可选的粘土;以再生催化剂的重量为基准,所述沸石的含量可以为1-50重%,无机氧化物的含量可以为5-99重%,粘土的含量可以为0-70重%。另外,为了提高丙烯产率并增加转化率,所述沸石可以包括平均孔径小于0.7纳米的择型沸石和y型沸石;以干基计并以沸石总重量为基准,所述平均孔径小于0.7纳米的择型沸石可以为25-90重%,优选为40-60重量%,所述y型沸石可以为10-75重%,优选30-60重量%。所述平均孔径小于0.7纳米的择型沸石可以为选自zsm系列沸石、zrp沸石、镁碱沸石、菱沸石、环晶石、毛沸石、a沸石、柱沸石和浊沸石中的至少一种,以及经物理和/或化学方法处理后得到的上述沸石中的一种或两种以上的混合物。zsm系列沸石可以选自zsm-5、zsm-8、zsm-11、zsm-12、zsm-22、zsm-23、zsm-35、zsm-38、zsm-48和其它类似结构的沸石中的一种或两种以上的混合物。有关zsm-5更为详尽的描述参见usp3702886,有关zrp更为详尽的描述参见usp5232675、cn1211470a、cn1611299a。所述y型沸石可以为选自稀土y型沸石(rey)、稀土氢y型沸石(rehy)、超稳y型沸石(usy)和稀土超稳y型沸石(reusy)中的至少一种。所述无机氧化物作为粘结剂,可以为二氧化硅(sio2)和/或三氧化二铝(al2o3)。所选粘土作为基质,即载体,可以为高岭土和/或多水高岭土。根据本发明,重质原料是本领域技术人员所熟知的,例如,所述重质原料为重质烃类和/或富含碳氢化合物的各种动植物油类原料,所述重质烃类可以为选自石油烃类、矿物油和合成油中的一种或一种以上的混合物。石油烃类可以是减压蜡油、常压渣油、减压蜡油掺混部分减压渣油或其它二次加工获得的烃油,所述二次加工获得的烃油如焦化蜡油、脱沥青油、糠醛精制抽余油中的一种或几种。矿物油可以为选自煤液化油、油砂油和页岩油中的一种或几种以上的混合物。合成油可以为煤、天然气或沥青经过f-t合成得到的馏分油。所述富含碳氢化合物的各种动植物油类可以为各种动植物油脂。所述重质原料优选自减压蜡油、常压蜡油、焦化蜡油、脱沥青油、糠醛精制抽余油、煤液化油、油砂油、页岩油、费托合成油和动植物油脂中的至少一种。根据本发明,引入第二下行管反应器的轻质原料优选为富含烯烃的汽油和/或c4烃,所述富含烯烃的汽油可以选自本工艺产生的汽油馏分和/或其它装置生产的汽油馏分。其它装置生产的汽油馏分可选自催化裂化粗汽油、催化裂化稳定汽油、焦化汽油、减粘裂化汽油以及其它炼油或化工过程所生产的汽油馏分中的一种或一种以上的混合物,优先选用本工艺自产的汽油馏分。所述的富含烯烃的汽油的烯烃含量可以为25-95重量%,优选为35-90重量%,最好在50重量%以上。所述富含烯烃的汽油的终馏点不超过204℃,例如可以是馏程为35-204℃的全馏程汽油馏分,也可以是其中的窄馏分,例如终馏点不超过85℃的汽油馏分,优选馏程在40-85℃之间的汽油馏分。所述c4烃是指以c4馏分为主要成分的常温、常压下以气体形式存在的低分子碳氢化合物,包括碳原子数为4的烷烃、烯烃和炔烃,可以是本工艺自产的富含c4馏分的气态烃产品,也可以是其它装置过程所产生的富含c4馏分的气态烃,其中优选本工艺自产的c4馏分。所述c4烃中,烯烃的含量大于50重量%,优选大于60重量%,最好是在70重量%以上。轻质原料中,c4烃类与富含烯烃的汽油的重量比可以为(0-2):1,优选为(0-1.2):1,更优选(0-0.8):1;引入第二下行管反应器的富含烯烃的汽油与引入第一下行管反应器的重质原料的重量比可以为(0.05-0.30):1,优选为(0.10-0.20):1。根据本发明,所述下行管反应器的出口优选低压出口分布器,其压降可以小于10kpa,所述的低压出口分布器可采用现有分布器,例如拱形分布器等。根据本发明,汽提段汽提水蒸气和反应所得的油气,引入流化床反应器的底部,穿过流化床反应器后排出反应器,可降低油气分压,缩短油气在沉降段停留时间,增产丙烯产率。如图1所示,本发明还提供一种采用双下行管进行催化裂解的系统,该系统包括第一下行管反应器2、流化床反应器3、再生器7和第二下行管反应器9;所述第一下行管反应器2设置有位于顶部的催化剂入口、位于上部的重质原料入口和位于底部的物料出口,所述第二下行管反应器9设置有位于顶部的催化剂入口、位于上部的轻质原料入口和位于底部的物料出口,所述流化床反应器3设置有催化剂入口、物料入口、催化剂出口和产物出口,所述再生器7设置有催化剂入口和催化剂出口;所述第一下行管反应器2的物料出口与所述流化床反应器3的物料入口连通,所述第二下行管反应器9的物料出口与所述流化床反应器3的物料入口连通,所述再生器7的催化剂入口与所述流化床反应器3的催化剂出口连通,所述再生器7的催化剂出口与所述流化床反应器3的催化剂入口、第一下行管反应器2的催化剂入口和第二下行管反应器9催化剂入口连通。根据本发明,所述的下行管反应器可以为选自等直径下行管、等线速下行管和变直径下行管中的一种或其中两种的组合。所述流化床反应器可以选固定流化床、散式流化床、鼓泡床、湍动床、快速床、输送床和密相床反应器中的一种。根据本发明,如图1所示,所述系统还可以包括产物分离装置12,所述产物分离装置12的入口与所述流化床反应器3的产物出口连通,所述产物分离装置12设置有干气出口、液化气出口、汽油出口、柴油出口和油浆出口。所述的产物分离装置可以为现有技术,本发明没有特殊要求。离开流化床反应器的第三产物和待生催化剂进入沉降段,沉降分离出其中携带的待生催化剂后,第三产物引入后续的产物分离装置。在产物分离装置中,第三产物经分离得到干气、液化气、汽油、柴油和油浆。根据本发明,为了提高丙烯产率,所述产物分离装置12的液化气出口和/或汽油出口可以与所述第二下行管反应器9的轻质原料入口连通。为了方便产物的分离和待生催化剂的再生,所述流化床反应器3可以包括床层反应段、设置于床层反应段下方的汽提段5和设置于床层反应段上方的沉降段4,所述床层反应段、汽提段5和沉降段4可以同轴设置且流体连通,所述床层反应段可以设置有所述流化床反应器3的催化剂入口和物料入口,所述沉降段4的顶部可以设置有所述流化床反应器3的产物出口,所述汽提段5的下部可以设置有所述流化床反应器3的催化剂出口。下面结合附图对本发明所提供的工艺予以进一步的说明。如图1所示,高温再生催化剂经再生斜管8、再生斜管11、再生斜管13分别引入第二下行管反应器9的催化剂罐10、第一下行管反应器2的催化剂罐1和流化床反应器3。预热后的重质原料经管线14与来自管线15的雾化水蒸气按一定比例混合后,注入第一下行管反应器2与经由再生斜管13并由来自管线27的提升气提升的高温再生剂接触并第一催化裂解反应,第一产物与第一半待生催化剂混合物经第一下行管反应器2的出口分布器(图中未标出)流化床反应器3。预热或不预热的富含烯烃的汽油馏分和/或c4烃类经管线18与来自管线19的雾化水蒸气按一定比例混合后,注入第二下行管反应器9,与经由再生斜管8并由来自管线28的提升气提升的高温再生催化剂混合并进行第二催化裂解反应,第二产物与第二半待生催化剂混合物经第二下行管反应器9的出口分布器(图中未标出)引入流化床反应器3,与经由再生斜管11流入的高温再生催化剂混合后继续第三催化裂解反应,最后进入沉降段4进行第三产物与待生催化剂的分离;分离所得的第三产物通过管线20进入后继的产物分离装置12。在产物分离装置12中反应产物分离出气态烃(由管线22引出)、汽油(由管线23引出)、柴油(由管线24引出)、轻循环油(由管线25引出)和油浆(由管线26引出)。管线22引出的气态烃在后续产品分离、精制后可得到聚合级丙烯产品和富含烯烃的c4馏分,其中富含烯烃的c4馏分可返回反应器再转化成乙烯和丙烯。管线23引出的汽油可部分或全部返回反应系统再转化,也可先将汽油切割为轻、重汽油馏分段,轻汽油部分或全部返回反应系统再转化,优选将轻汽油返回第二下行管反应器转化;沉降段分离得到的催化剂进入床层反应区,然后进入汽提段5,汽提蒸汽经管线16注入,与积碳的待生催化剂逆流接触,将待生催化剂所携带的反应油气尽可能地汽提出,然后经床层反应区引入沉降器,与其它油气一起经管线20引出反应器。汽提后的催化剂通过待生斜管6送入再生器7烧焦再生。含氧气体经管线17注入再生器7,再生烟气经管线21引出。再生后的催化剂经再生斜管8、再生斜管11、再生斜管13进入不同的反应器循环使用。在上述具体实施方式过程中,对管线28和管线27引入的预提升介质可以选自水蒸气、c1-c4烃类或常规催化裂解干气,本发明优选水蒸气。下面的实施例将对本发明予以进一步说明,但并不因此限制本发明。实施例和对比例中所使用的原料油和催化剂相同。所用的原料a是一种裂解原料,具体性质见表1。所采用的催化剂为中国石化齐鲁催化剂厂生产的mmc-2,含平均孔径小于0.7纳米择型沸石和y型分子筛,其具体性质见表2。对比例1试验在中型催化裂解装置中进行。该装置包含一套独立的反应再生系统:反应器为第一下行管反应器加流化床组合反应器,第一下行管内径为16毫米,长度为3200毫米,第一下行管反应器底部出口处串联流化床反应器,流化床反应器的直径(内径)为64毫米,高度为600毫米。所用的催化剂为mmc-2催化剂,对表1所示的原料进行裂解;反应后的油气与催化剂分离,催化剂进入汽提器汽提后进入再生器再生,再生后的催化剂分两路离开再生器,一路进入流化床反应器,提高流化床反应器内的反应温度和剂油比。另一路进入第一下行管反应器顶部的催化剂罐;油气进入产物分离装置。其反应操作条件以及反应结果见表3和表4。对比例2试验在中型催化裂解装置中进行。该装置包含一套独立的反应再生系统:反应器为提升管反应器加流化床组合反应器,提升管内径为16毫米,长度为3200毫米,提升管反应器顶部出口串联流化床反应器,流化床反应器的直径(内径)为64毫米,高度为600毫米。所用的催化剂为mmc-2催化剂,对表1所示的原料进行裂解;反应后的油气与催化剂分离,催化剂进入汽提器汽提后进入再生器再生,然后再次进入提升管反应器内进行反应;来自流化床反应器的反应产物入产物分离装置。其反应操作条件以及反应结果见表3和表4。实施例1参照对比例1,如图1所示,不同的是再生后的催化剂分三路离开再生器,一路进入流化床反应器,另一路进入第一下行管反应器顶部的催化剂罐,第三路进入第二下行管反应器。第二下行管反应器内径为12毫米,长度为2200毫米,采用的催化剂为mmc-2催化剂,对来自产物分离装置的富含烯烃的轻汽油(馏程为30-85℃,烯烃含量为52重量%,重量占重质原料的15重量%)作为轻质原料进行裂解,所得油气和催化剂混合物进入流化床反应器内再次进行裂解反应。分离所得催化剂去再生器烧焦再生,分离所得的油气产物与来自沉降器的油气产物混合进入产物分离装置。其反应操作条件以及反应结果见表3和表4。由表3和表4可见,与对比例2提升管反应器加流化床反应器相比,对比例1和实施例1的第一下行管反应器加流化床反应器能够减缓提升管反应器内催化剂返混等不利影响,提高低碳烯烃产率的同时减缓干气产率增加的幅度。将再生剂引入与第一下行管反应器串联的流化床反应器可以提高流化床反应器内催化剂的平均活性和反应温度,提高重油转化率和低碳烯烃产率。实施例1的第二下行管反应器内轻质原料与高温催化剂接触,保证了轻质原料的转化率,提高了低碳烯烃的产率的同时能减缓干气产率增加,低碳烯烃与干气产率的比值增加。以上结合附图详细描述了本发明的优选实施方式,但是,本发明并不限于上述实施方式中的具体细节,在本发明的技术构思范围内,可以对本发明的技术方案进行多种简单变型,这些简单变型均属于本发明的保护范围。另外需要说明的是,在上述具体实施方式中所描述的各个具体技术特征,在不矛盾的情况下,可以通过任何合适的方式进行组合,为了避免不必要的重复,本发明对各种可能的组合方式不再另行说明。此外,本发明的各种不同的实施方式之间也可以进行任意组合,只要其不违背本发明的思想,其同样应当视为本发明所发明的内容。表1项目原料a密度(20℃),克·厘米-30.91凝点,℃34四组分,重量%饱和分72.6芳香分20.9胶质6.3沥青质0.2元素组成,重量%碳86.86氢12.62硫0.46氮0.15馏程/℃初馏点27110重量%36230重量%40650重量%43770重量%46690重量%/表2催化剂名称mmc-2主要活性组分usy+zrp化学性质,重量%al2o352.3na2o0.072re2o30.82物理性质总孔体积,毫升/克0.183微孔体积,毫升/克0.024比表面,米2/克143沸石比表面,米2/克50基质比表面,米2/克105堆积密度,克/毫升0.83微反活性,重量%67表3为实施例1和对比例1-2的反应操作条件案例编号实施例1对比例1实施例2第一下行管(提升管)反应器下行管提升管下行管重质原料原料a原料a原料a催化剂mmc-1mmc-1mmc-1反应器出口温度,℃570570570反应时间,秒1.51.51.5剂油重量比12.512.512.5流化床反应器重时空速,小时-1333反应温度,℃580550580沉降器压力,兆帕(绝压)0.210.210.21第二下行管反应器轻质原料//轻质汽油催化剂//mmc-1提升管出口温度,℃//650剂油重量比22反应时间,秒//2.1轻质汽油与重质原料质量比//0.15:1表4为实施例1和对比例1-2的反应结果当前第1页12