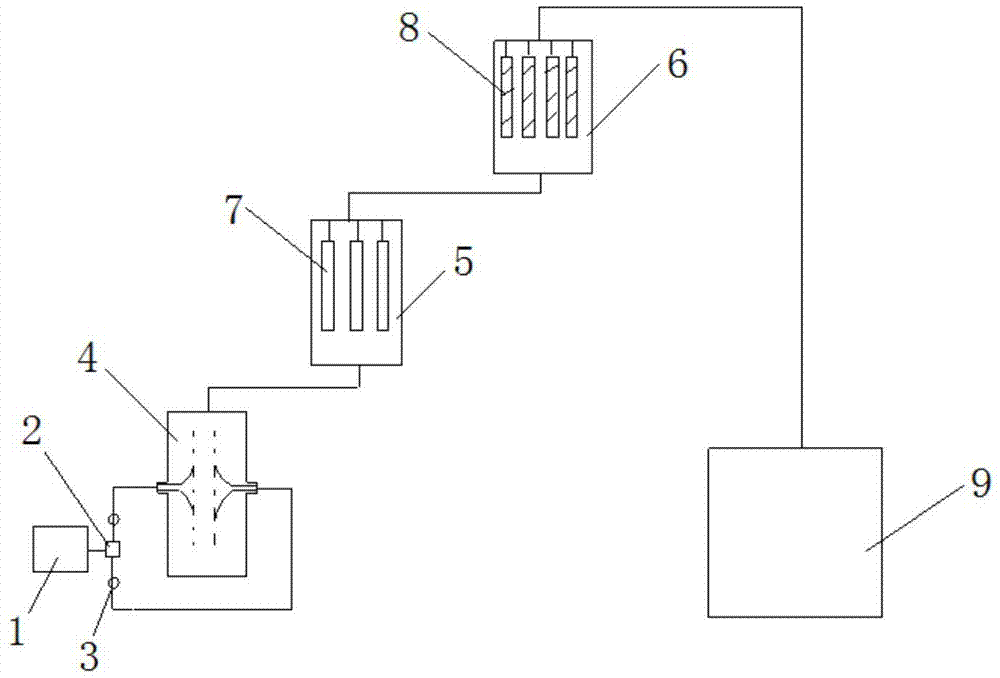
本发明涉及清洁能源
技术领域:
,具体涉及一种复合乳化剂及其在生产微乳化柴油中的应用。
背景技术:
乳化柴油,也就是燃料油掺水燃烧,虽然已经不是一个新课题,但却又在不断赋予新思维,新的发展动力。早在国际燃烧协会第一次年会上,已经确定把它作为三大节能措施之一。我国也在连续几个五年建设计划期间将其列入发展项目,因而掀起了一波又一波的研究热潮。通过不断的理论研讨以及科研院校的大量实验,众多专家学者对于乳化柴油的节能减排特性,结论高度一致。水虽然不是燃料,但在发动机高温高压燃烧过程中,会发生一系列附加的化学反应,会形成大量的o、h和oh自由基,这些活性物质会大大活化整个燃烧过程,抑制未燃烧碳的提前排放,使之更完全燃烧,减少了能量损失。水在一切固体和液体中比热最大的特性,可以迅速吸收动力部件的热量而减少相互间的膨胀性摩擦,降低了自耗功而节能。含水燃料的自供氧效应,可减少碳氢燃料的局部过热、缺氧、脱氢、裂解结焦,使燃烧室壁面各处和喷油头等突出部位温度均化,保证机械整体工作正常,从而有利于节省燃料。水的沸点低于柴油,汽化蒸发早,汽化膨胀爆破油包水膜,使燃料经喷嘴雾化后发生的再次雾化(即微爆效应),进一步提高了燃料利用率而节能。无数科研结论和实际应用都证实了柴油掺水燃烧可以减少有害气体排放30%以上。但是,油与水毕竟是两种互不相容的液体,要把它们完全互溶,难度是不言而喻的。由于水比柴油的密度大,加上水的凝聚作用,在重力场和凝聚的双重作用下,水在油内会自发的下沉、聚集、分层,直至最后破乳而与油分离。因此,大多数研制的乳化柴油都存在不能较长时间储存,易于分层的问题,这大大限制了乳化柴油的应用。目前,提高乳化柴油稳定性的研究主要是寻找新型的乳化剂或各种乳化剂复配物。但是,现有的乳化剂产品乳化稳定性不够好,稳定时间大部分只有十天或半个月,难以作为商品周转使用;而且,现有的乳化剂产品多是以精炼石油制品和高级脂肪酸作为原料,导致乳化剂的价格昂贵,生产乳化柴油的成本居高不下。技术实现要素:针对上述现有技术的不足,本发明的目的是提供一种复合乳化剂,该复合乳化剂是以低品质油脂为原料,经化学改性和酰胺化反应制备而成,有效降低了乳化剂的生产成本。利用该复合乳化剂制备的微乳化柴油,其稳定性能和燃烧性能均得到极大的提高。为实现上述目的,本发明采用如下技术方案:本发明的第一方面,提供一种复合乳化剂的制备方法,包括如下步骤:(1)以低品质油脂为原料,进行预处理;(2)向预处理后的低品质油脂中加入溶解有金属钠的甲醇,进行甲酯化改性,得到脂肪酸甲酯;(3)向脂肪酸甲酯中加入由有机胺和无机氨组成的复合胺化剂,以金属钠作为催化剂,进行酰胺化反应,制备得到复合乳化剂。优选的,步骤(1)中,所述低品质油脂包括:地沟油、动物屠宰场的下水油、皮革厂回收油、食物油精炼产生的酸化油以及不宜食用的蓖麻油、小桐子油和高凝点棕榈油。优选的,步骤(1)中,预处理的方法为:将低品质油脂进行机械过滤,除去杂质;加入占低品质油脂重量3-5%的化学氧化剂,加热到70-80℃,搅拌反应15-20分钟,离心分离脱除水分和未反应完全的化学氧化剂。进一步优选的,所述化学氧化剂由以下原料制成:双氧水2-4份、过碳酸钠0.5-1.5份、钛盐0.001份。优选的,步骤(2)中,所述溶解有金属钠的甲醇的加入量占预处理后的低品质油脂重量的15-25%;所述金属钠的溶解量为预处理后的低品质油脂和甲醇总重量的0.3-0.7%。优选的,步骤(2)中,甲酯化改性的温度条件为40-45℃。优选的,步骤(3)中,所述复合胺化剂由二乙醇胺和氢氧化铵组成;所述二乙醇胺的加入量为脂肪酸甲酯重量的6-10%,所述氢氧化铵的加入量为脂肪酸甲酯重量的8-12%。优选的,步骤(3)中,金属钠的加入量为脂肪酸甲酯重量的0.1%。本发明的第二方面,提供上述方法制备的复合乳化剂。本发明制备的复合乳化剂包含:脂肪酸甲酯酰胺和脂肪酸铵。本发明的第三方面,提供一种制备上述复合乳化剂的连续流反应系统,所述连续流反应系统包括:依次连接的撞击流反应器、微波反应器和超声波反应器。上述复合乳化剂在制备乳化柴油中的应用也是本发明的保护范围。本发明的第四方面,提供一种微乳化柴油,所述微乳化柴油是通过在柴油中加入上述的复合乳化剂、水、助溶水剂、稳定剂和水裂解催化剂后混合均匀而制得。优选的,所述微乳化柴油由以下重量份的原料制成:柴油72-85份、水8-15份、复合乳化剂5-8份、助溶水剂1.5-3.5份、稳定剂0.5-1.2份、水裂解催化剂0.01-0.05份。更优选的,所述微乳化柴油由以下重量份的原料制成:柴油78-80份、水9-12份、复合乳化剂6-7份、助溶水剂2-3份、稳定剂0.7-1份、水裂解催化剂0.02-0.03份。上述微乳化柴油中,优选的,所述助溶水剂由正丙醇、正丁醇和正戊醇按体积比0.5:1:0.5混合而成。所述稳定剂为蓖麻油甲酯酰胺。所述水裂解催化剂为钛酸盐和高锰酸盐中的一种或两种以任意比混合而成;优选的,所述水裂解催化剂为钛酸盐和高锰酸盐按质量比1:1混合而成。本发明的第五方面,提供上述微乳化柴油的制备方法,包括以下步骤:将柴油、水、复合乳化剂、助溶水剂、稳定剂和水裂解催化剂混合,在撞击流反应器中进行反应,将混合后的物料经过转子流量计分成等量两股液流,从撞击流反应器两端同轴相向高速进入到中心区碰撞,然后经静态混合器引入储油罐中,即得到微乳化柴油。本发明的有益效果:(1)本发明以地沟油等大宗不宜食用的动植物油脂为原料,经有效的化学改性后制备得到复合乳化剂,实现了资源的合理化利用,降低了乳化剂的生产成本。(2)利用本发明的复合乳化剂制备的乳化柴油具有微乳的特性,澄清透明,为热力学稳定体系,稳定性高,可放置3个月以上。(3)使用本发明的微乳化柴油可使得排气烟度大幅降低,氮化物和碳化物的排放量也均有下降,具有非常显著的减排效果。(4)本发明利用撞击流反应器、微波反应器和超声波反应器组合成一条连续流化学生产线,实施工业化生产。上述生产线首先是利用撞击流反应器动能推动反应液体形成湍流,经微波反应器快速加热,产生加热效应,使反应液分子间发生碰撞摩擦,极大的提高了反应活性及反应速率;反应液体在撞击流的继续推动下,再经超声波的声空化效应。由于微波反应器的反应活化能的大小,对反应液体的极性大小有一定的选择性,而超声波声场的反应活性具有广谱性,二者的活化能量性质不同,故双方具有互补性。联合使用时在改善加热和能量转移等,能够发挥各自优势,提高能量的使用效率,降低能量消耗,改善产物收率和质量。撞击流混合反应、微波加热反应和超声波化学反应联用技术是一种有重要应用前景的高效绿色的环保工业技术。附图说明图1:本发明的连续流反应系统结构示意图;图中,1-配料罐,2-离心泵,3-转子流量计,4-撞击流反应器,5-微波反应器,6-超声波反应器,7-微波发生器件,8-超声波发射组件,9-储料罐。图2:hlb值与乳化稳定期关系图;图中,a-蓖麻油甲酯酰胺,b-低品质甲酯酰胺。具体实施方式应该指出,以下详细说明都是例示性的,旨在对本申请提供进一步的说明。除非另有指明,本文使用的所有技术和科学术语具有与本申请所属
技术领域:
的普通技术人员通常理解的相同含义。正如
背景技术:
部分所介绍的,现有的制备乳化柴油用的乳化剂,其稳定性欠佳,生产成本高,导致乳化柴油难以大面积推广使用。基于此,本发明的目的是提供一种以低品质油脂制备的复合乳化剂,降低了乳化剂的生产成本,同时实现了大宗废油脂的资源化利用和无害化处理。在本发明的一种实施方案中,给出了以低品质油脂为原料制备复合乳化剂的方法,包括以下步骤:(1)原料预处理:将低品质油脂进行机械过滤,除去杂质;加入占低品质油脂重量3-5%的化学氧化剂,加热到70-80℃,搅拌反应15-20分钟,离心分离脱除水分和未反应完全的化学氧化剂。(2)甲酯化改性:向预处理后的低品质油脂中加入溶解有金属钠的甲醇,进行甲酯化改性,得到脂肪酸甲酯;所述溶解有金属钠的甲醇的加入量占预处理后的低品质油脂重量的15-25%;所述金属钠的溶解量为预处理后的低品质油脂和甲醇总重量的0.3-0.7%。(3)向脂肪酸甲酯中加入由有机胺和无机氨组成的复合胺化剂,以金属钠作为催化剂,进行酰胺化反应,制备得到复合乳化剂。本发明的“低品质油脂”包括:地沟油、动物屠宰场的下水油、皮革厂回收油、食物油精炼产生的酸化油及不宜食用的蓖麻油、小桐子油(麻疯果油)、高凝点棕榈油等一些不宜食用的动植物油脂。与商品乳化剂使用的高级油脂原料相比,若以“低品质油脂”为原料直接同有机胺进行酰胺化反应,制备脂肪酸酰胺乳化剂生产乳化柴油,则其稳定性达不到要求,而且,其酸值、凝点、粘度等一些指标也不宜放在柴油里面使用。这也是“低品质油脂”综合利用的难点所在。为解决这一技术难题,本发明先对“低品质油脂”进行预处理,然后进行化学改性,制成“脂肪酸甲酯”作为中间体,然后在金属钠(溶解在甲醇中)催化剂作用下,将此中间体与有机胺和高浓度无机氨组成的复合胺化剂中进行酰胺化反应,制成含有“脂肪酸甲酯酰胺”和“脂肪酸铵”的复合乳化剂。上述预处理的过程中,用于改性的化学氧化剂由以下原料制成:双氧水2-4份、过碳酸钠0.5-1.5份、钛盐0.001份。其中,“钛盐”可以选自钛酸盐、1-丁醇钛盐或硫酸氧钛。以本发明制备的复合乳化剂生产乳化柴油,可以显著提高乳化柴油的稳定性能和燃烧性能。我们知道,物质之间发生化学反应必须满足两个基本条件:即参与反应物分子之间发生碰撞(接触);碰撞分子必须具有足够能量。本发明中使用甲醇与低质油脂进行甲酯化反应改性,而甲醇与脂肪酸(油脂)是两种互不相溶的液体,如果在传统的釜式反应器或者流化床反应器中加工,相互分子间碰撞几率小,特别是碰撞的分子缺乏足够的能量,所以反应动力小,速度慢、时间长(一般都要以小时计),能耗高,劳动力消耗多,设备利用率低,产品转化率低,结果就是提高了生产成本。为了提高反应效率,降低生产成本,实现工业化大生产,本发明将撞击流反应器、微波反应器和超声波反应器偶联组合成一条连续流反应系统(如图1所示),充分发挥各反应器各自的优势。本发明中用甲醇对低质油脂改性变成脂肪酸甲酯中间体,进而将此中间体在有机、无机氨混合胺化剂中酰胺化反应,制成脂肪酸甲酯酰胺和脂肪酸铵复合乳化剂,都是在该连续流反应系统中进行的。为了能使甲醇和油脂两种不互溶的液体一开始就混合良好,本发明选择撞击流反应器,撞击流混合反应器的工作原理并不复杂,就是将经过过滤、除去水杂、脱色脱胶后的低级油脂,在配料罐中和甲醇及催化剂预混合后,通过输液泵分成两股等量的在同一轴线上相向高速液流,在撞击流反应器两端的进料口同时进入,在反应器中心剧烈碰撞,使得撞击之后的高速流体由轴向转变为脉动运动,产生出一个湍动非常剧烈的撞击区域,在这个区域内,流场湍动作用明显,剧烈的剪切作用,将液体微团粉碎得十分微小,这样不仅增大了固定液体体积下的接触面积以及传质推动力,改善了液体混合状态,强化了过程的传递质量效果;而且大大提升“甲酯化反应”以及后续“烷醇酰胺化反应”的速率及转化率。反应液体从撞击区形成湍流场,经过t形管将湍流引向微波反应器进行加热反应。微波作为一种加热能源已经被广泛应用于从无机反应到有机的反应,从简单分子反应到复杂反应的各个化工领域。人们已经发现微波能可以显著加速有机化学合成反应。微波能渗入物质分子内部,由电子、离子的移动或缺陷偶极子的极化而被吸收,转变成热量,形成物料内外部整体加热的效果。降低了热损,减少了加热时间,可达到快速加热节能的效果。微波对化学反应场的强化作用,一方面是反应吸收微波能量后分子运动加剧;另一方面是微波场对离子或极性分子的电场力,强迫其按电磁波作用的方式运动,这也足以说明微波加热反应有选择性,显然微波加热的方式更适合平行的或自动连续的工艺方式进行。本发明将具有广谱适应性的超声波反应器串联在微波反应器后面。超声波反应器具有方向性好,穿透力强的特点,使从具有选择性反应的微波反应器出来的流体在其中继续进行反应。反应物在超声波声场的作用下,产生高频震荡,生长和崩溃闭合的动力学过程,空化泡溃败时,能在极短的时间内在空化泡周围极小的空间产生局部的高温和高压,高温使反应物的活性增加,促使自由基的形成和裂解反应的发生;高压致使冲击波和微射流的发生;从而导致分子之间产生强烈的碰撞,进而促使甲酯化以及后续(酰胺化)反应的高速进行。最终完成劣质油脂的甲酯化改性,然后在另一组相同流程相同组成的反应系统中,以相同的操作方式,不同的溶液配方和控制条件下完成微乳化柴油主乳化剂—“脂肪酸甲酯酰胺”的反应过程,从而完成本发明的复合乳化剂的制备工作。需要说明的是,本发明的连续流反应系统中,所述撞击流反应器、微波反应器和超声波反应器均可以选择现有技术中已有的反应器。本发明是将上述各反应器进行优化组合,形成一条适于工业化生产的反应系统。在本发明的另一种实施方案中,给出了一种微乳化柴油产品,该微乳化柴油产品是以上述的复合乳化剂作为主剂,以中碳醇(丙醇、丁醇、戊醇)复配作为助溶剂,在本发明偶联生产线上制作的蓖麻油甲酯酰胺为稳定剂,以微量高锰酸盐和钛酸盐作为水裂解催化剂,经混合制备得到。本发明之所以选择蓖麻油甲酯酰胺作为稳定剂是因为:(1)蓖麻油甲酯酰胺的粘度系数高于一般的长链脂肪酸,一般长链脂肪酸的粘度系数在20℃时为0.68pa.s,而它要0.99pa.s,说明液体内存在相对运动时,蓖麻油甲酯酰胺的反抗变形的能力比一般长链脂肪酸强许多。(2)在hlb值与乳化稳定期关系图上同样反映出蓖麻油甲酯酰胺的稳定性表现宽泛。(见图2)所述蓖麻油甲酯酰胺采用如下方法进行制备:(1)以蓖麻油为原料,首先进行与其它低品质油脂相同的预处理。(2)进行甲酯化改性,甲酯化改性条件与与其它低品质油脂相同,制备得到蓖麻油甲酯。(3)向蓖麻油甲酯中加入由有机胺和无机氨组成的复合胺化剂,以金属钠作为催化剂,进行酰胺化反应,制备得到蓖麻油甲酯酰胺。对于本发明微乳化柴油的生产,可以采用撞击流反应器串联sk型静态混合器的生产线制作微乳化柴油稳定产品。为了使得本领域技术人员能够更加清楚地了解本申请的技术方案,以下将结合具体的实施例详细说明本申请的技术方案。本发明实施例和对比例中所用的试验材料均为本领域常规的试验材料,均可通过商业渠道购买得到。实施例1:复合乳化剂的制备1.地沟油的预处理:将地沟油进行机械过滤,除去杂质。加入占地沟油重量4%化学氧化剂,加热到75℃。搅拌反应20分钟,离心分离脱除水分和未反应完全的少量化学氧化剂。化学氧化剂的配方:双氧水3份、过碳酸钠1份、钛盐0.001份。在室温条件下混合搅拌均匀即可。2.地沟油的甲酯化改性:在本发明的连续流反应系统(图1)中进行甲酯化改性。先将经预处理后的地沟油放入配料罐1中,然后将占预处理后地沟油重量20%的溶解有催化剂金属钠的甲醇加入预处理后的地沟油中(金属钠的溶解量为预处理后的地沟油和甲醇总量的0.5%)加热到40℃,搅拌5分钟,检查开启全线阀门,启动离心泵2,将油脂和甲醇的混合液分成等量的两股液流,经转子流量计3从两侧相向高速进入撞击流反应器4。在撞击流反应器4的中心区域剧烈相撞,使得撞击之后高速流体由轴向变为脉动运动,产生出一个湍动非常剧烈的撞击区域。在这个区域内,流场湍动作用明显,大大改善了油脂和甲醇的混合状态,强化了过程的传递质量效果。接着反应液体进入圆柱形微波反应器5底部,微波反应器5的反应釜内安装多组微波发生器件7,每组器件都伸入各自的陶瓷隔离套管内,陶瓷隔离套管上端悬装在釜顶安装板上,下端伸入反应液体内。陶瓷套管不吸收阻挡微波,仅起到将微波发生器组件与反应液体隔离开的作用。反应液体在微波釜中加热(温度控制在40-45℃),旋转上升、反应10分钟,到达釜顶出液管。再从超声波反应器6底部进入,超声波反应器6的反应釜顶部安装有多组超声波发射组件8,超声波反应器6的反应釜也是圆柱形,故反应液体同样旋转上升,在声场空泡效应作用下进一步酯化反应。10分钟后从超声波反应器6的顶部出料进入储料罐9,在10分钟内完成全部甲酯化改性,最后在萃取离心机萃取提纯,取出轻相为脂肪酸甲酯,重相为粗甘油及水分。3.制备复合乳化剂:同样利用本发明连续流反应系统,先将已制备的脂肪酸甲脂按计算量放进配料罐1中,加入脂肪酸甲脂量8%的二乙醇胺,再加入脂肪酸甲脂量10%含量40%的氢氧化铵,最后加入脂肪酸甲脂量0.1%溶解在甲醇里的金属钠,加热到50℃,搅拌5分钟,开启全线阀门,启动离心泵2,将反应液分成等量的两股液流,经转子流量计3高速进入撞击流反应器4,在撞击流反应器4的中心区域剧烈相撞,使得撞击之后的高速流体由轴向变为脉动运动,产生出一个湍动非常剧烈的撞击区域。在这个区域内,流场湍动作用明显,大大改善了甲酯和二乙醇胺及氢氧化铵的混合状态,强化了过程的传递质量效果。接着反应液体进入圆柱形微波反应器5底部,反应液体在微波釜中加热,温度控制在95-100℃,旋转上升,反应10分钟,到釜顶出液管。再从超声波反应器6底部进入。超声波反应器6的反应釜也是圆柱形,故反应液体同样旋转升流,在声空泡效应作用下进一步酰胺化反应。10分钟后从超声波反应器6的顶部出料进入储料罐9,可以在10分钟内完成按常规需两个小时才能完成的酰胺化反应。(在常规条件下油脂与二乙醇胺的酰胺化反应,温度要达到110℃反应两小时。油脂与氢氧化铵反应2mpa压力下150℃反应两小时)。实施例2:微乳化柴油的制备1.原料组成:柴油80份、水10份、复合乳化剂6.5份、助溶水剂2.5份、稳定剂0.8份、水裂解催化剂0.02份。其中,复合乳化剂由实施例1制备得到;助溶水剂由正丙醇、正丁醇和正戊醇按体积比0.5:1:0.5混合而成;稳定剂为蓖麻油甲酯酰胺,由蓖麻油在本发明的连续流反应系统中制备得到;水裂解催化剂由钛酸盐和高锰酸盐按质量比为1:1组成。2.制备工艺:将柴油、水、复合乳化剂、助溶水剂、稳定剂和水裂解催化剂放入配料罐中,在室温条件下搅拌3-5分钟,混合均匀,启动离心泵,把混合后的物料经过转子流量计分成等量两股液流,从撞击流反应器两端同轴相向高速进入到中心区碰撞,然后经sk型静态混合器引入储油罐,即得到微乳化柴油成品。实施例3:微乳化柴油的制备:1.原料组成:柴油72份、水12份、复合乳化剂7份、助溶水剂3.5份、稳定剂0.5份、水裂解催化剂0.05份。其中,复合乳化剂由实施例1制备得到;助溶水剂由正丙醇、正丁醇和正戊醇按体积比0.5:1:0.5混合而成;稳定剂为蓖麻油甲酯酰胺,由蓖麻油在本发明的连续流反应系统中制备得到;水裂解催化剂由钛酸盐和高锰酸盐组成,两者的质量比为1:1。2.制备工艺同实施例2,制备得到微乳化柴油。实施例4:微乳化柴油的制备:1.原料组成:柴油85份、水8份、复合乳化剂5份、助溶水剂1.5份、稳定剂1.2份、水裂解催化剂0.01份。其中,复合乳化剂由实施例1制备得到;助溶水剂由正丙醇、正丁醇和正戊醇按体积比0.5:1:0.5混合而成。稳定剂为蓖麻油甲酯酰胺,是以蓖麻油为原料,在本发明的连续流反应系统中进行制备,制备方法同实施例1的复合乳化剂的制备。水裂解催化剂由钛酸盐和高锰酸盐组成,两者的质量比为1:1。2.制备工艺同实施例2,制备得到微乳化柴油。对比例1:乳化剂的制备1.地沟油的预处理:将地沟油进行机械过滤,除去杂质。2.将预处理后的地沟油与二乙醇胺的酰胺化反应,反应温度110℃,反应时间两小时,制备得到乳化剂。对比例2:微乳化柴油的制备将实施例2中的“复合乳化剂”替换为对比例1制备的“乳化剂”,其余同实施例2,制备得到微乳化柴油。对比例3:微乳化柴油的制备将实施例2中的“复合乳化剂”替换为市售的柴油乳化剂,其余同实施例2,制备得到微乳化柴油。对比例4:微乳化柴油的制备将实施例2中的“稳定剂”省略,其余同实施例2,制备得到微乳化柴油。对比例5:微乳化柴油的制备将实施例2中的“水裂解催化剂”省略,其余同实施例2,制备得到微乳化柴油。试验例1:稳定性能测试将实施例2、对比例2-对比例5制备的微乳化柴油,于室温下静置,观察其稳定性。结果发现,实施例2制备的微乳化柴油放置3个月以上未出现分层变质的现象;对比例2制备的微乳化柴油在放置20天后开始出现分层变质的现象;对比例3制备的微乳化柴油在放置30天后开始出现分层变质的现象;对比例4制备的微乳化柴油在放置32天后开始出现分层变质的现象;对比例5制备的微乳化柴油在放置35天后出现分层变质的现象。以上结果表明,本发明制备的微乳化柴油的稳定性得到显著的提高。试验例2:燃烧性能测试试验柴油机压缩比21.6,标定功率/转速为3.8kw/2400r·min-1,结果见表1。表1:燃烧性能测试结果项目nox(g/kw.h)co(g/kw.h)烟度实施例20.80.31.0对比例21.91.43.1对比例31.71.32.8对比例42.11.53.4对比例52.01.43.2由表1可以看出,与对比例制备的乳化柴油相比,本发明制备的微乳化柴油的燃烧性能得到极大提高,氮氧化物、co的排放量明显降低,具有非常显著的减排效果。以上所述仅为本申请的优选实施例而已,并不用于限制本申请,对于本领域的技术人员来说,本申请可以有各种更改和变化。凡在本申请的精神和原则之内,所作的任何修改、等同替换、改进等,均应包含在本申请的保护范围之内。当前第1页12