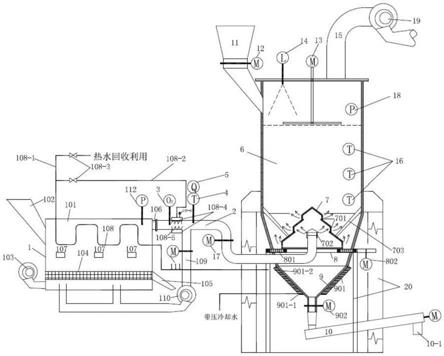
1.本发明属于生物质综合利用设备技术领域,尤其涉及生物质经裂解气化后同时生产可燃气和生物质炭一种设有独立氧化炉的生物质气化热炭联产系统。
背景技术:2.生物质气化,从产物残渣分,可以分为产炭和不产炭,前者对生物质利用率低,后者生物质利用率高;从生物质料在气化过程中的运动形态,可以分为移动床和固定床,前者气化效率高,但是产炭的品质最低,后者气化效率低,但是产炭品质高于前者。
3.在建设要求产炭的生物质气化系统时,固定床是主导技术方案。
4.固定床生物质气化,根据产气与生物质料的移动方向,可以分为上吸式和下吸式,其区别是,气化过程中,生物质均为自上向下移动,上吸式固定床气体全部自下向上抽吸、排出,而下吸式固定床气体自上向下抽吸、排出。
5.从反应机理上,上吸式固定床生物质气化自上而下分为预热、裂解、还原、氧化过程,下吸式固定床自上而下分为预热、裂解、氧化、还原过程。其中氧化过程放热,其他过程均吸热,没有氧化过程释放的热量,其他过程将难以完成,氧化过程提供的热量多少,是决定气化速率的主要因素。
6.目前国内热炭联产采用的常规技术,无论是哪种床型,四个反应过程全部在一个容器内完成,四个反应过程无法独立控制,因此调节、控制范围窄、调节速度慢,同时,氧化产物(灰分)掺杂在产品炭中,产炭率低、产炭品质差。
7.由于其反应机理的限制,下吸式固定床产生的可燃气热值高,但是只有颗粒度较细、可氧化性较好、可气化性较好的生物质才能采用下吸式,且调节范围最窄、调节速度最慢;上吸式固定床虽然可控性好于下吸式固定床,但因为料层中水分不参与反应,因此产气热值低于下吸式,同时,如果颗粒大、氧化性差,或调节超出允许范围,还有可能导致气化过程难以连续生产。
技术实现要素:8.本发明的目的在于解决现有技术中生物质气化裂解效率低、可调节性差、生物质炭品质差的技术问题,提出一种设有独立氧化炉的生物质气化热炭联产系统。
9.本发明提供的技术方案如下:
10.一种设有独立氧化炉的生物质气化热炭联产系统,其特征在于,包括独立设置的氧化炉和气化炉,所述氧化炉和所述气化炉通过烟气管连接,所述烟气管上设有烟气管阀门,所述烟气管还与烟气循环管的一端连接,所述烟气循环管的另一端与所述氧化炉的氧化腔室连通,所述烟气循环管上分别设有烟气循环阀和烟气循环风机,所述烟气管在所述烟气管阀门与所述氧化炉之间的管路上分别设有氧气检测装置、温度传感器和流量计。
11.优选的,所述气化炉为上吸式固定床气化炉。上吸式固定床可控性好,对生物质颗粒度、可氧化性、可气化要求低。
12.优选的,所述气化炉底部设有第一炉排,所述第一炉排将所述气化炉分为上腔体和下腔体,所述上腔体内固定有布气装置,所述烟气管穿过所述气化炉炉壁通入至所述布气装置内部,所述烟气管出口设有布气板。布气板使烟气进入布气装置前先实现一级布气,烟气通过布气装置与生物质反应,实现二级布气,进一步增加烟气与气化炉内生物质的接触面积,提高烟气热能利用效率,加快反应速度。
13.优选的,所述布气装置为多层宝塔形状,每一层设有若干布气孔,所述布气装置底部为封闭结构,所述布气装置通过钢筋固定在所述气化炉内壁。宝塔形状增加的布气装置的布气面积,即增加了布气孔的数量。
14.优选的,第一炉排底部设置有出料斗,所述第一炉排与出料斗之间的空间形成所述下腔体,所述出料斗外壁设有空心水冷壁,所述空心水冷壁分别设有进水口和出水口。空心水冷壁内进入冷水出料漏斗内的炭料进行降温,防止烫伤。
15.优选的,所述出水口与设置在所述氧化炉外壁的水管入口相连,所述水管具有第一支管和第二支管,所述第一支管与热用户连接,所述第二支管与所述烟气管连通,所述第一支管与第二支管上分别设有水管阀。出水口的流出的水吸收了出料斗传递的热量,在氧化炉外壁进一步吸收热量,产生的热水一方面用于热用户使用,另一方面可用于烟气管内水汽化产生水蒸汽参与后级反应。
16.优选的,所述出料斗底部设有出料阀,所述出料阀下方设有螺旋输送机,所述气化炉上部设有气化料进料斗,所述气化炉顶部盖板分别设有超声波料位计、旋转电动刮板和抽出风管,所述抽出风管上设有引风机。气化料从气化料漏斗进入气化炉反应腔内,旋转电动刮板将其表面刮平,通过超声波料位计检测料位高度,决定是否进料,反应生成的炭进入出料漏斗后,打开出料阀,在螺旋输送机的作用下从炭料出口排出;反应生成的炭燃气在引风机的作用下从抽出风管抽出。
17.优选的,所述氧化炉包括氧化腔室,所述氧化腔室上部侧璧设有氧化料进口和烟气出口,所述烟气出口与所述烟气管连接,所述氧化腔室内部下方设有第二炉排,所述第二炉排与排渣口连接,所述氧化腔室底部外壁设有进风机,所述氧化腔室上还设有压力表。氧化料从氧化料进口进入到氧化炉的氧化腔室中,开启进风机通入空气,氧化料燃烧后产生的烟气经烟气管计入气化炉,反应燃烧产生的残渣通过第二炉排从排渣口排出。
18.一种设有独立氧化炉的生物质气化热炭联产系统的工作方法,包括如下步骤:
19.将生物质在氧化炉氧化燃烧后,以烟气形式产生大量热和二氧化碳,烟气经烟气管进入气化炉;
20.通过调节氧化炉的进气量、进料量、排渣速度,及烟气管上氧气检测装置、温度传感器、流量计上读数,可以调节进入气化炉的热量和二氧化碳量,从而调节气化炉内后级气化的强度和反应程度;
21.当烟气温度未达到后级反应温度时,,开启烟气循环阀和烟气循环风机,使得部分烟气经烟气循环管回流至氧化炉被再次加热后,被用于后级反应。
22.优选的,一种设有独立氧化炉的生物质气化热炭联产系统的工作方法,包括如下步骤:
23.a:启动时,氧化炉内少量进气、维持最低燃烧状态,并通过温度传感器监督烟气保持温度低于气化炉内生物质裂解温度、通过流量计累计烟气流量,直至烟气将气化炉内全
部空气替代时,再逐步加大氧化炉进气量;
24.b:正常运行时,维持氧化炉进气量低于氧化炉内燃料充分燃烧所需要的进气量,通过氧气检测装置监控烟气中不含或含微量氧气,调节氧化炉进气量以调整烟气的温度和流量,以使得烟气的热量满足后级生物质气化过程的需要;
25.在使用过程中,当燃烧过程达到最大设定值,仍不能满足后级生物质气
26.化所需热量时,通过如下任意一种或几种方式调节:
27.改用热值更高的生物质作为氧化燃料;
28.在气化炉允许进气量范围内,增加氧化炉进气量,使得气化炉内底部的生物质也能部分氧化,即气化炉内也有氧化放热过程发生,进而提高整个装置的生物质可燃气产气量;
29.开启烟气循环管,使得部分烟气再循环被加热,被用于后级反应;
30.在烟气温度超过一定温度的条件下,可以向烟气中喷入一定量水,水在烟气管内汽化后,进入气化炉,参与气化中还原反应,提高可燃气的热值;
31.当气化炉要求极低负荷时,可以将烟气管阀门开度关小,同时打开烟气循环阀、启动烟气循环风机,使得氧化炉处于基本维持状态,在需要增加气化输出时,无需重新点火,仅需关闭或关小烟气循环风机、烟气循环阀、开大烟气管阀门即可。
32.通过采用以上技术手段,达到技术效果如下:
33.1、氧化炉独立设置,氧化过程(燃烧)独立进行,独立控制,可以很容易控制反应强度,通过对氧化炉反应强度控制,可以方便、宽范围、快速地调节、控制生物质气化生产过程,实现了高质量的气炭联产;
34.2、氧化过程(燃烧)产生的灰分,不会掺杂在产炭中,因此产炭率、产炭品质远高于一般固定床,更加高于移动床;
35.3、在氧化炉产生的高温烟气中,进入气化炉之前,喷入一定量的水,经在烟气管道内高温气化后,在气化炉内参与后续生物质气化还原反应,可获得更高热值的可燃气;
36.4、本发明根据不同生物质气化需要的热量,通过调整生物质氧化料的品种、烟气管的氧气量、流量、向烟气中喷水等方式,使得进入气化炉烟气的热量可调,实现一种床型可以对任何生物质进行气化;
37.5、在高价值生物质作为气化原料时,氧化炉内生物质可以选择与氧化炉内气化料不一样的生物质,以降低成本,或获得更高的烟气热量,提高热炭联产产能;
38.6、常规固定床,在启动阶段,可燃气与新鲜空气混合,温度不可控,容易发生爆燃安全事故,本发明氧化炉独立设置,没有未燃尽可燃气,因而不会发生爆燃;在启动阶段,氧化炉负荷逐步拉升,体现在以二氧化碳为主的氧化炉排气气量和气温逐步升高,氧化炉内积存的空气呈被逐步替代、温度逐步提高的过程,氧化炉内可燃气浓度达到爆燃范围时,氧化炉内已无氧气,可杜绝氧化炉发生爆燃事故;
39.7、氧化炉至气化炉布气点之前,采用微正压运行,即便系统不严密,泄漏至大气的是二氧化碳为主的氧化炉排气,不具有可燃性;气化炉气化料上层开始,采用微负压运行,即便系统不严密,不会有可燃气泄漏至大气中,同时,因为气化炉内发生还原反应为吸热反应,产生的可燃气温度较低,达不到爆燃点,因此,即便泄漏进少量空气,也不会发生爆燃,整个系统的安全性可得到有效保障;
40.8、排炭前用冷却水,降低排炭温度,回收利用余热的同时,还可降低因出炭温度过高导致的人员和设备事故可能性;
41.9、与现有气化装置比,特别设置有紧急停机机制。当需要紧急停机时,停止进料,切断氧化炉向气化炉供气、供热。由于气化炉反应为还原吸热反应,没有热源,反应会很快停止,且温度快速下降,可防止事故发生和扩大;而氧化炉不对外输出烟气后,二氧化碳快速抑制氧化燃烧过程而停炉。常规方案在紧急停炉时,因为进入的空气中含有氧气,即便切断外部进气,还会继续反应,直至进入设备内的空气全部消耗完后,才会真正停炉,过程长,温度高,可能发生事故或扩大事故。
附图说明
42.图1是本发明的结构示意图;
43.图中:1、氧化炉;101、氧化腔室;102、氧化料进口;103、进风机;104、第二炉排;105、排渣口;106、烟气出口;107、观察口;108、水管;108-1、第一支管;108-2、第二支管;108-3、水管阀;108-4、水套;108-5、雾化装置;108-6、压力泵;109、烟气循环管;110、烟气循环风机;111、烟气循环阀;112、压力表;2、烟气管;3、氧气检测装置;4、温度传感器;5、流量计;6、气化炉;7、烟气布气装置;701、布气孔;702、布气板;703、钢筋;8、第一炉排;801、孔;802、电动齿轮;9、出料斗;901、空心水冷壁;901-1、进水口;901-2、出水口;902、出料阀;10、螺旋输送机;10-1、炭料出口;11、气化进料口;12、电动闸板;13、旋转电动刮板;14、超声波料位计;15、抽出风管;16、插入式温度传感器;17、烟气管阀门;18、压力计,19、引风机;20、支架。
具体实施方式
44.如图1所示,一种设有独立氧化炉的生物质气化热炭联产系统,其特征在于,包括独立设置的氧化炉和气化炉,所述氧化炉和所述气化炉6通过烟气管2连接,所述烟气管2上设有烟气管阀门17,所述烟气管2还与烟气循环管109的一端连接,所述烟气循环管109的另一端与所述氧化炉1的氧化腔室101连通,所述烟气循环管109上分别设有烟气循环阀111和烟气循环风机110,所述烟气管2在所述烟气管阀门17与所述氧化炉1之间的管路上分别设有氧气检测装置3、温度传感器4和流量计5,所述气化炉6为上吸式固定床气化炉。
45.所述气化炉6底部设有第一炉排8,所述第一炉排8将所述气化炉分为上腔体和下腔体,所述上腔体内固定有布气装置7,所述烟气管2穿过所述气化炉6炉壁通入至所述布气装置7内部,所述烟气管2出口设有布气板702,所述布气装置7通过钢筋703固定在所述气化炉6内壁,所述布气装置7为多层宝塔形状,每一层设有若干布气孔701,所述布气装置7底部为封闭结构。所述烟气管2穿过所述气化炉6炉壁通过焊接等方式密封设置。
46.所述布气装置7底部为钢板,烟气管2穿过钢板深入布气装置7内部,烟气管与钢板通过法兰或者焊接的方式与钢板密封设置。
47.所述第一炉排8为圆周型炉排,其周边一圈设有与气化料粗细程度一致的孔801,第一炉排8在电动齿轮802的驱动下进行转动,从而实现反应生成的炭料的排放。
48.所述布气装置7设置在所述第一炉排8的上方,并且不遮挡所述第一炉排8的孔801,所述布气装置7底部可与所述第一炉排8的顶部接触,但不固定。所述烟气管2进入所述
布气装置7之前先穿过所述第一炉排8中心,所述烟气管2与所述第一炉排8不固定,所述第一炉排8相对烟气管2可做圆周运动。
49.所述第一炉排8底部设置有出料斗9,所述第一炉排8与出料斗9之间的空间形成所述下腔体,所述出料斗9外壁设有空心水冷壁901,所述空心水冷壁901分别设有进水口901-1和出水口901-2。所述出水口901-2与设置在所述氧化炉1外壁的水管108入口相连,所述水管108出口具有第一支管108-1和第二支管108-2,所述第一支管108-1与热用户连接,所述第二支管108-2与所述烟气管2连通,所述第一支管108-1与第二支管108-2上分别设有水管阀108-3。
50.为了增加水与烟气的接触面积,增加水的汽化效率,所述烟气管2外壁设有水套108-4,所述水套108-4入口与所述第二支管108-2出口连接,所述水套108-4出口与所述烟气管2连接,所述水套108-4出口处还设有若干雾化装置108-6。为了加大雾化效果,所述水套108-4还设有压力泵108-6。
51.所述出料斗9底部设有出料阀902,所述出料阀902下方设有螺旋输送机10,所述气化炉6上部设有气化料进料斗11,所述气化炉顶部盖板分别设有超声波料位计14、旋转电动刮板13和抽出风管15,所述抽出风管15上设有引风机19,采用负压抽吸方式将可燃气抽吸输送至需要利用的地点。所述超声波料位计14,用于测量气化炉6内的料位高度,所述旋转电动刮板13用于刮平气化炉6内生物质气化料表面。
52.气化炉6侧壁上下排列设有多个插入式温度传感器16,用于测量气化炉6内部不同料位高度的温度;气化炉6侧壁、料位高度以上部位设有压力计18,用于测量气化炉内可燃气压力。
53.所述氧化炉1包括氧化腔室101,所述氧化腔室101上部侧璧设有氧化料进口102和烟气出口106,所述烟气出口106与所述烟气管2连接,所述氧化腔室101内部下方设有第二炉排104,所述第二炉排104与排渣口105连接,所述氧化腔室101底部外壁设有进风机103,所述氧化腔室101上还设有压力表112用于监控氧化腔室101的压力,所述氧化腔室101上还设有若干个观察口107,用于观察氧化炉2内燃烧情况。
54.所述气化炉6底部设有支架20,用于支撑和固定。
55.每个生物质气化生产生物质可燃气和生物质炭的过程,都包括氧化、还原、气化裂解、预热干燥四个过程,其中只有氧化过程放热,其他过程都是吸热,但氧化过程实际是消耗生物质的过程,并不产生可燃气,如果氧化反应彻底的话,也不生产生物质炭。如果没有氧化过程产生的热量或者外部补充热量,其他几个过程将难以发生或难以持续。氧化过程温度可达1000~1200℃,主要反应式如下:
56.c(生物质)+o2(空气)=co2+热量
57.还原过程一般在700~900℃是效果最好,主要反应式如下:
58.c(生物质)+co2(前级烟气)+热量=2co(可燃气成分)
59.c(生物质)+h2o(前级烟气中喷入)+热量=co+h2(可燃气成分)
60.c(生物质)+h2+热量=ch4(可燃气成分)
61.生物质裂解过程一般在300~700℃时发生,主要是生物质有机质成分的高温降解,生成可燃性挥发物、ch4、h2、co、薪柴(ch
1.4o0.6
)、以及少量的二氧化碳等。
62.预热干燥过程不产生新物资,只是生物质中的水分吸热挥发的过程。
63.本发明在氧化炉内是生物质氧化过程,其产物是高温热风和不参与反应的灰渣;气化炉内的反应结果自下而上是还原、气化裂解、预热干燥。
64.结合图1,简述一种设有独立氧化炉的生物质气化热炭联产系统的工作原理:
65.将生物质在氧化炉1氧化燃烧后,以烟气形式产生大量热和二氧化碳,烟气经烟气管2进入气化炉6,被用于后级反应,生物质不能参与反应的物质形成炉渣排出;
66.通过调节氧化炉1的进气量、进料量、排渣速度,及烟气管2上氧气检测装置3、温度传感器4、流量计5上读数,可以调节进入气化炉6的热量和二氧化碳量,从而调节气化炉6内后级气化的强度和反应程度;
67.当烟气温度未达到后级反应温度时,可开启烟气循环阀111和烟气循环风机110,使得部分烟气经烟气循环管109回流至氧化炉1被再次加热后,被用于后级反应。
68.具体的,所述设有独立氧化炉的生物质气化热炭联产系统的工作方法,包括如下步骤:
69.a:通过氧化料进料口向氧化腔室101中加入氧化料,启动时,打开进风机103,氧化炉1内少量进气、维持最低燃烧状态,并通过温度传感器4监督烟气保持温度低于气化炉6内生物质裂解温度、通过流量计5累计烟气流量,直至烟气可气化炉6内全部将空气替代时,再逐步加大氧化炉1进气量;
70.b:正常运行时,维持氧化炉1进气量低于氧化炉1内燃料充分燃烧所需要的进气量,通过氧气检测装置3监控烟气中不含或含微量氧气,调节氧化炉1进气量以调整烟气的温度和流量,以使得烟气的热量满足后级生物质气化过程的需要;
71.c:当燃烧过程达到最大设定值,仍不能满足后级生物质气化所需热量时,通过以下任意一种或几种方式进行调节:
72.a改用热值更高的生物质作为氧化燃料;
73.b在气化炉6允许进气量范围内,增加氧化炉1进气量,使得气化炉6内底部的生物质也能部分氧化,即气化炉6内也有氧化放热过程发生,进而提高整个装置的生物质可燃气产气量;
74.c开启烟气循环管109,使得部分烟气再循环被加热,再次被用于后级反应;
75.d在烟气温度超过一定温度的条件下,可以向烟气中喷入一定量水,水在烟气管2内汽化后,进入气化炉6,参与气化中还原反应,提高可燃气的热值;
76.d:当气化炉6要求极低负荷时,如维持热备用状态,可以将烟气管阀门17开度关小,同时打开烟气循环阀111、启动烟气循环风机110,使得氧化炉1处于基本维持状态,在需要增加气化输出时,无需重新点火,仅需关闭或关小烟气循环风机110、烟气循环阀111、开大烟气管阀门17即可;
77.e:打开气化料进料口11的电动闸板12,气化料经过气化料进料口11进入气化炉6内,料位计14随时测量料位高度,当料位高度达到设定值范围时,启动旋转电动刮板13,直至料位稳定且在允许范围内,关闭电动闸板12,导入氧化炉1烟气,开启可燃气抽出风管15上引风机19,启动气化过程;氧化炉1烟气经过烟气布气装置7的两级布气,充分渗入气化料层中,发生还原和裂解反应,产生的可燃气在引风机19的作用下从抽出风管15被吸走;
78.f:生物质气化自下而上完成,通过插入式温度传感器16观察气化炉6内不同高度、部位的温度变化,可以判断底部生物质是否已经充分“炭化”;当判断已“炭化”时,启动电动
齿轮802驱动第一型炉排8运动,排出炭料至出料斗9;开启出料阀902和螺旋输送机10,经炭料出口10-1向外部排出炭料。
79.当排出一定炭料后,超声料位计14测量的气化料料位降低,当降低一定值时,启动进料操作。
80.连续或断续重复步骤d~f,即可实现连续对外生产提供可燃气和连续或间断对外生产提供生物质炭。
81.整个生产过程中,保持冷取水不断,可防止出炭温度过高。
82.氧化炉压力表112监督到氧化炉1内压力过高时,降低进气风机103输出功率,超过允许设定值上限时,停止进气风机103运行。
83.气化炉压力计18监督到气化炉室压力过低、其他参数正常时,可采取降低引风机19输出功率、减少可燃气抽吸,或加大氧化炉进风机103输出功率的方式调节;气化炉压力计18监督到气化炉压力过高、其他参数正常时,可采取增加引风机19输出功率、加大可燃气抽吸,或降低氧化炉进风机103输出功率方式调节。
84.整套系统采用全自动控制运行,并设有手动紧急停机功能;同时,在关键参数,如氧化炉压力、气化炉压力过高,气化炉压力压力过低,设置有保护值,超过该设定值,且进风机103、引风机19调节范围已到边界时,系统自动紧急停机。
85.当需要紧急停机时,停止氧化炉1和气化炉6进料,关闭烟气管阀门17,开启烟气循环阀111和烟气循环风机110,关闭氧化炉进风机103、关闭可燃气抽出引风机19、关闭出料阀902和螺旋输送机10,保持冷却水常开。