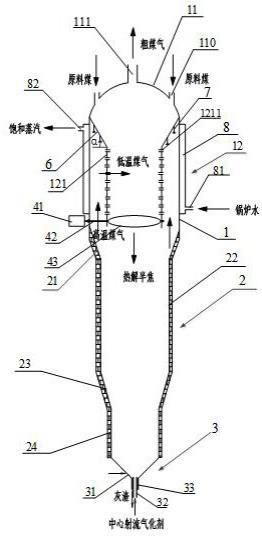
1.本实用新型涉及煤气化技术领域,具体而言,涉及一种气化炉。
背景技术:2.煤气化技术是洁净高效利用煤的一种重要方式。我国煤炭资源丰富,油气资源相对匮乏,将丰富的煤炭转化成清洁的气体和油,近年来受到众多关注及应用。流化床气化炉因炉内温度均匀,气固混合均匀、接触佳,气化效率高等原因广泛应用于煤气化工艺。但是流化床气化炉整体床层温度梯度小,原料煤入炉后直接与高温烟气或高温床料混合,热解析出的焦油在较高温度下裂解损失,导致气化炉出口粗煤气中焦油含量大大降低;且气化炉出口粗煤气温度较高,为后续废热锅炉设计、选型,后续冷却降温系统带来较多问题,粗煤气温度高、后续系统换热负荷大、设备投资高,且冷介质如水用量大,造成较高量的废水排放。
技术实现要素:3.鉴于此,本实用新型提出了一种气化炉,旨在解决现有气化炉出口粗煤气温度高、焦油含量低、后续系统投资高、换热负荷大且废水产量高的问题。
4.本实用新型提出了一种气化炉,包括:自上而下依次连通的换热区、气化反应区和排渣区;其中,所述气化反应区的顶部与所述换热区连通,用以将所述气化反应区产生的高温粗煤气输送至所述换热区;所述换热区内部设置有内筒,所述内筒与所述换热区侧壁之间具有换热空间,用以对所述气化反应区产生的高温粗煤气进行换热降温;所述换热区的顶部开设有若干原料煤进口,用以向所述换热区的内筒中输送原料煤;所述内筒的侧壁上开设有若干低温粗煤气进气孔,用以使经所述换热空间内降温后得到的低温粗煤气进入所述内筒中,并与进入所述内筒中的原料煤接触、混合,发生中低温热解反应;所述换热区的顶部还开设有粗煤气出口,用以将所述中低温热解反应产生的热解气、焦油与所述气化反应区产生的粗煤气排出所述换热区。
5.进一步地,上述气化炉中,所述换热区包括:相连通的封头和筒体;其中,
6.所述封头顶部中心设置有粗煤气出口,所述封头顶部粗煤气出口两侧分别开设有原料煤进口;所述筒体内部设置有内筒,所述内筒外壁与所述筒体内壁之间的区域形成换热空间;所述筒体的外壁设置有冷却水夹套,所述冷却水夹套的下部开设有冷却水进口,所述冷却水夹套的上部开设有饱和蒸汽出口,用以对进入所述换热空间的高温粗煤气进行冷却。
7.进一步地,上述气化炉中,所述内筒的侧壁上沿轴向开设有若干圈低温粗煤气进气孔,且各圈所述低温粗煤气进气孔的孔径自上而下逐渐增大。
8.进一步地,上述气化炉中,相邻两圈所述低温粗煤气进气孔中,位于下部的低温粗煤气进气孔的孔径为位于上部的低温粗煤气进气孔孔径的1.05
‑
1.2倍。
9.进一步地,上述气化炉中,所述换热区中靠近所述原料煤进口下方的内壁与所述
内筒的顶部之间设置有原料煤导流板。
10.进一步地,上述气化炉中,所述原料煤导流板为锥形结构,所述锥形结构的锥顶端朝向所述内筒设置且所述锥形结构的锥顶端与水平面之间的夹角为40
‑
75
°
。
11.进一步地,上述气化炉中,所述原料煤导流板上设置有若干冷却水雾化喷嘴,用以向所述换热空间内喷射雾化冷却水。
12.进一步地,上述气化炉中,所述内筒底部设置有可沿水平方向翻转的翻板阀结构,用以在所述翻板阀结构翻转至水平状态时,使得原料煤留存在所述内筒中,并与低温粗煤气接触、换热,发生中低温热解反应。
13.进一步地,上述气化炉中,所述翻板阀结构包括:外部旋转执行机构、两段联动杆和圆盘;其中,两段所述联动杆相对设置在所述圆盘的两侧,第一段所述联动杆依次可转动的穿设于所述换热区的侧壁和所述内筒的侧壁且与所述圆盘的一侧的中心部位相连接,第二段所述联动杆的一端与所述内筒的侧壁转动相连,另一段与所述圆盘另一侧的中心部位相连接;所述外部旋转执行机构与第一段所述联动杆连接,用以驱动所述联动杆带动所述圆盘翻转。
14.进一步地,上述气化炉中,所述换热区中与换热空间对应的外壁为金属壁结构,所述气化反应区和所述排渣区的外壁均由外侧金属壁面和内部耐火材料衬里构成。
15.本实用新型提供的气化炉,通过在气化反应区上部设置换热区,对气化反应区产生的高温粗煤气进行回收、降温,使得入炉原料煤与降温后的低温粗煤气接触、混合,发生中低温热解反应,大大提高了气化炉出口粗煤气中高附加值煤焦油含量、降低了粗煤气出口温度,有利于提高煤气化工艺的整体技术经济性。
附图说明
16.通过阅读下文优选实施方式的详细描述,各种其他的优点和益处对于本领域普通技术人员将变得清楚明了。附图仅用于示出优选实施方式的目的,而并不认为是对本实用新型的限制。而且在整个附图中,用相同的参考符号表示相同的部件。在附图中:
17.图1为本实用新型实施例提供的气化炉的结构示意图;
18.图2为本实用新型实施例中翻板阀的结构示意图。
具体实施方式
19.下面将参照附图更详细地描述本公开的示例性实施例。虽然附图中显示了本公开的示例性实施例,然而应当理解,可以以各种形式实现本公开而不应被这里阐述的实施例所限制。相反,提供这些实施例是为了能够更透彻地理解本公开,并且能够将本公开的范围完整的传达给本领域的技术人员。需要说明的是,在不冲突的情况下,本实用新型中的实施例及实施例中的特征可以相互组合。下面将参考附图并结合实施例来详细说明本实用新型。
20.参阅图1,本实用新型实施例的气化炉的包括:自上而下依次连通的换热区1、气化反应区2和排渣区3;其中,所述气化反应区2的顶部与所述换热区1连通,用以将所述气化反应区2产生的高温粗煤气输送至所述换热区1;所述换热区1内部设置有内筒121,所述内筒121与所述换热区1侧壁之间具有换热空间,用以对所述气化反应区2产生的高温粗煤气进
行换热降温;所述换热区1的顶部开设有若干原料煤进口110,用以向所述换热区1的内筒121中输送原料煤;所述内筒121的侧壁上开设有若干低温粗煤气进气孔,用以使经所述换热空间内降温后得到的低温粗煤气进入所述内筒121中,并与进入所述内筒121中的原料煤接触、混合,发生中低温热解反应;所述换热区1的顶部还开设有粗煤气出口111,用以将所述中低温热解反应产生的热解气、焦油与所述气化反应区产生的粗煤气排出所述换热区1。
21.具体而言,换热区1可以为直筒状结构,该直筒结构的直径较大,以便于增加换热面积,同时便于内筒121、冷却水喷嘴等结构的安装。换热区1通过气化反应区2的第一密相床层缩径段21与气化反应区2连通,以保持连接处顺畅过渡、炉内的物料无流动死区。换热区1中与换热空间对应的外壁为金属壁结构。
22.换热区1的内筒121为具有一定壁厚的金属圆柱形筒体,内筒121底部可以设置有开合度可调的盖板,以为原料煤提供停留空间。换热区1的顶部两侧设置有原料煤进口110,以将原料煤输送至换热区1内部的内筒121中,使得原料煤在内筒121中与经换热空间换热后的低温粗煤气发生中低温热解反应,热解后产生的半焦经内筒121底部输送至气化反应区2。换热区1的顶部中心可以设置有粗煤气出口111,热解反应产生的热解气、焦油与部分粗煤气可以经粗煤气出口111排出气化炉。
23.进一步的,所述内筒121底部设置有可沿水平方向翻转的翻板阀结构4,用以在所述翻板阀结构4翻转至水平状态时,使得原料煤留存在所述内筒121中,并与低温粗煤气接触、换热,发生中低温热解反应。
24.具体而言,翻板阀结构4可沿内筒121底部端面所在的水平面翻转预设角度,当翻板阀结构4水平放置时,气化反应区2产生的高温粗煤气无法进入换热区1的内筒121中,而是进入内筒121外壁与换热区1内壁间形成的换热空间中,与换热区1外部的冷却水夹套8中的冷却介质换热降温,降温后的低温粗煤气经内筒121壁面上开设的低温粗煤气进气孔进入内筒121中,与冷的原料煤接触换热,同时发生原料煤的热解反应。
25.当内筒121中的固相物质较多,换热充分后,可以间断开启翻板阀,将翻板阀结构4翻转至竖直方向,使得内筒121中的固体物料下落至下部气化反应区2的床层中,发生煤气化反应。
26.参阅图2,所述翻板阀结构4包括:外部旋转执行机构41、两段联动杆42和圆盘43;其中,两段所述联动杆42相对设置在所述圆盘43的两侧,第一段所述联动杆42依次可转动的穿设于所述换热区1的侧壁和所述内筒121的侧壁且与所述圆盘43的一侧的中心部位相连接,第二段所述联动杆42的一端与所述内筒121的侧壁转动相连,另一段与所述圆盘43另一侧的中心部位相连接;所述外部旋转执行机构41与第一段所述联动杆42连接,用以驱动所述联动杆42带动所述圆盘43翻转。
27.其中:圆盘43可以为不开设落煤孔的封闭圆盘,也可以开设有落煤孔431的半封闭圆盘结构,以在圆盘43翻转至水平方向时,仍可保持少量煤颗粒沿落煤孔下落至下部气化反应区2的床层中。落煤孔431可以为圆孔。两段联动杆42可以分别通过若干螺栓5与圆盘43相固定。
28.气化反应区2可以为直筒结构或变径筒状结构,本实施例中,气化反应区2包括:自上而下依次连通的第一密相床层缩径段21、第一密相床层直筒段22、第二密相床层缩径段23和第二密相床层直筒段24;其中,第一密相床层缩径段21口径较大的一端与所述换热区1
连通,第二密相床层直筒段24的下端与排渣区3连通。
29.较具体的,第一密相床层直筒段22的直径大于第二密相床层直筒段24的直径。第二密相床层直筒段24与排渣区3的锥形气体分布板连通,且二者的连接处保持圆滑过渡,第二密相床层直筒段24的直径与锥形气体分布板上端的直径相同。第一密相床层缩径段21和第二密相床层缩径段23可以均为圆台状结构,并且,该圆台状结构的直径较大的一端朝上设置。本实施例中,气化反应区2的各段密相床层的外壁和排渣区3的外壁可以均由外侧金属壁面和内部耐火材料衬里构成。
30.排渣区3包括:锥形气体分布板31、中心射流管32和排渣管路33;其中,所述锥形气体分布板31的口径较小的一端朝向排渣口设置,排渣管路33与锥形气体分布板31口径较小的一端连通,中心射流管32沿套设于排渣管路33内部。
31.具体而言,锥形气体分布板31的锥顶端(口径较小的一端)靠近排渣管路33设置,锥形气体分布板31的锥底端(口径较大的一端)靠近密相区设置。锥形气体分布板31的锥面上沿周向开设有多组进气孔,气化剂经气体分布板上的进气孔分布后进入气化反应区2中。
32.锥形气体分布板31可以通过排渣管路33与后续的排渣系统相连通。中心射流管32位于排渣管路33内部,且与排渣管路33同轴设置。中心射流管32与排渣管路33之间形成环隙的排渣通道。
33.中心射流管32的顶部位于锥形分布板上靠近锥顶端的一圈进气孔的下方,中心射流管32的底部延伸出至排渣管路33的排渣口下方。
34.上述显然可以得出,本实施例中提供的气化炉,通过在气化反应区上部设置换热区,对气化反应区产生的高温粗煤气进行回收、降温,使得入炉原料煤与降温后的低温粗煤气接触、混合,发生中低温热解反应,大大提高了气化炉出口粗煤气中高附加值煤焦油含量、降低了粗煤气出口温度,有利于提高煤气化工艺的整体技术经济性。
35.上述实施例中,换热区1包括:相连通的封头11和筒体12;其中,所述封头11顶部中心设置有粗煤气出口111,所述封头11顶部两侧分别开设有原料煤进口110;所述筒体12内部设置有内筒121,所述内筒121外壁与所述筒体12内壁之间的区域形成换热空间;所述筒体12的外壁设置有冷却水夹套8,用以对进入所述换热空间的高温粗煤气进行冷却。
36.具体而言,封头11可以为椭圆形结构,由外侧金属壁面和内部耐火材料衬里构成,封头11的两侧分别设置有一原料煤进口110,两个原料煤进口110可以对称设置在封头11的两侧。筒体12的外壁可以采用金属材质制成,以增加导热性能。本实施例中,换热区1的筒体12直径大于气化反应区2和排渣区3的口径。
37.内筒121与筒体12同轴设置,二者之间的间隙形成高温粗煤气的换热空间,为了保证换热效果,筒体12的外壁设置有冷却水夹套8,所述冷却水夹套8的下部开设有冷却水进口81,冷却水可以为锅炉水,所述冷却水夹套8的上部开设有饱和蒸汽出口82。冷却水夹套8的设置,能够降低气化反应区2产生的高温粗煤气的温度,同时能够实现热量的回收。
38.上述实施例中,所述内筒121的侧壁上沿轴向开设有若干圈低温粗煤气进气孔1211,且各圈所述低温粗煤气进气孔1211的孔径自上而下逐渐增大。由于当内筒121具有一定高度的原料煤床层时,从内筒121下部侧壁进入的低温粗煤气需克服更高的阻力,因此,在内筒121下部开设孔径较大的低温粗煤气进气孔1211,可以降低低温粗煤气的进入压降及阻力,从而避免低温粗煤气均从上部阻力较小的进气孔进入内筒121中,造成下部无粗煤
气进入或粗煤气气量过低,导致低温粗煤气与内筒121下部的原料煤接触换热不充分的不良后果。
39.优选的,相邻两圈所述低温粗煤气进气孔1211中,位于下部的低温粗煤气进气孔1211的孔径为位于上部的低温粗煤气进气孔1211孔径的1.05
‑
1.2倍。
40.上述各实施例中,所述换热区1中靠近所述原料煤进口110下方的内壁与所述内筒121的顶部之间设置有原料煤导流板 6。
41.具体而言,所述原料煤导流板 6的底端与所述内筒121的顶部连通,所述原料煤导流板6的顶端与所述封头11上靠近原料煤进口110的位置连通。即:封头11上位于原料煤进口110以下的内壁与所述内筒121的顶部之间设置有原料煤导流板6。优选的,原料煤进口110靠近原料煤导流板6外缘设置,以保证进入的原料煤沿着原料煤导流板6的倾斜壁面下滑、同时保持均匀分散。
42.本实施例中,原料煤导流板6为锥形结构,所述锥形结构的锥顶端朝向所述内筒121设置且所述锥形结构的锥顶端与水平面之间的夹角α为40
‑
75
°
,以防止原料煤在原料煤导流板6上堆积。原料煤下落至原料煤导流板6上时,与原料煤导流板6壁面对侧的高温粗煤气进行间接接触换热。原料煤导流板6可以采用金属材质制成。
43.进一步的,上述各实施例中,所述原料煤导流板6上设置有若干冷却水雾化喷嘴7,用以向所述换热空间内喷射雾化冷却水,以使雾化冷却水直接与高温粗煤气接触,进一步加强换热降温效果。
44.综上,本实用新型中提供的气化炉,通过在气化反应区上部设置换热区,对气化反应区产生的高温粗煤气进行回收、降温,使得入炉原料煤与降温后的低温粗煤气接触、混合,发生中低温热解反应,大大提高了气化炉出口粗煤气中高附加值煤焦油含量、降低了粗煤气出口温度,有利于提高煤气化工艺的整体技术经济性。
45.显然,本领域的技术人员可以对本实用新型进行各种改动和变型而不脱离本实用新型的精神和范围。这样,倘若本实用新型的这些修改和变型属于本实用新型权利要求及其等同技术的范围之内,则本实用新型也意图包含这些改动和变型在内。