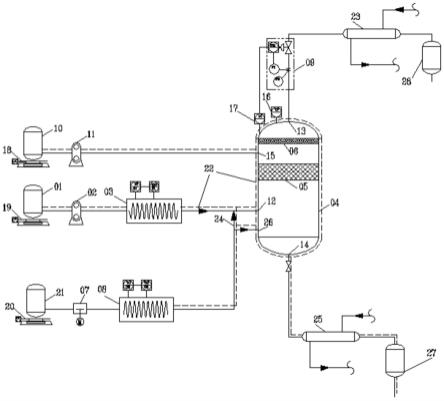
1.本发明涉及石油化工领域的一种石油烃分离实验装置,实现石油烃混合组分分离成两个组分。
背景技术:2.石油烃分离装置在工业上常见的有常压蒸馏装置,通过侧线从分馏塔取出物流取热冷却后在上方回流到分馏塔,可将原油切割成汽油,煤油,轻柴油,重柴油和重油等四五种以上产品,而每两种产品之间分离都需要一定的塔板数,采用单塔多侧线的结构形式,需要侧线换热流程,结构复杂,另外已有分馏实验装置都是常压或减压条件,不能加压分馏;如果取消侧线取热系统,简单的闪蒸,分离精度很差,分离出的组分重叠会大于60℃以上,不适合作为实验室石油烃分离获取不同馏程范围原料的需求。
3.石油烃分离装置相关专利有cn210384895u,该专利提供了一种将轻、重组分分离的装置,但该装置实际是常见的“初馏塔”的方案,该装置如果用于实验室处理量很小的获取不同馏程范围的石油烃存在如下缺陷:1、使用塔顶分离出的产物冷却成液体回流到分馏塔,这样塔顶产品必须冷却成液体,无法气体外输;2、由于回流的介质是塔顶分离出的低沸点组分,返回塔内受热后容易气化,难以保持液体在分馏塔内向下回流,对沸点更高的组分分离作用小,3、该装置塔顶产物冷却后必须有侧线外送,返回分馏塔的回流量无法测量和控制;4、该装置无法进行不同操作压力条件下的调节和准确控制石油烃分离;5、石油烃进料管线的压力可控,但温度不可控,则分离条件不可控;6、分离罐的压力不可控,更无法与下游反应装置,如提升管反应装置,联运。
4.已有分馏装置或方法,都是通过使用分馏物侧线取热冷却回流实现精确分馏的,一是需要设置侧线分馏物或产物换热系统,二是回流原料性质不能选择控制,限制了分离条件和效果。
5.如何实现不依靠分离塔内或产物侧线换热冷却回流实现石油烃双组分分离,如何保证分离精度,如何实现分离条件的可调可控、分离结果的可调,如何实现实验室公斤/小时级别的处理量的分离并精确计量,尤其是如何实现低沸点组分气体直接输出进反应器是没有先例的。
技术实现要素:6.本发明的目的是提供一种石油烃分离实验装置,既能满足实验室对不同馏程范围石油烃作为实验原料的需求,又可以与下游提升管装置联运并能保证反应装置平稳操作,实现原料油闪蒸分离后直接作为催化裂化/催化裂解反应装置进料。
7.本发明所提供的石油烃分离实验装置,包括进料部分,闪蒸分离部分和控制部分;所述石油烃分离装置分离罐顶部设置回流原料,提高分离效果;具体采用从回流原料罐经管线输送回流原料或在原料油加热炉前从原料油中直接经管线分流一部分到分离罐顶部,作为回流原料,或/和向分离罐顶部注水实现低沸点组分分离;
所述进料部分包括被分离的石油烃或原料油进料部分,以及低温石油烃回流进料部分,和/或水(回流)进料部分;所述被分离的石油烃或原料油进料部分,设置有原料罐,原料油泵和原料油加热炉,依次通过管线连通原料油入口,所述原料罐放置于原料油电子称上进行进料量测量,实现原料油进料量的精确计量;或者单独设置回流部分,所述低温石油烃回流进料部分,设置有回流原料罐和回流泵,所述回流原料罐和回流泵依次通过管线连通回流口,或者所述回流原料罐一端连通原料罐,另一端和回流泵依次通过管线连通回流口,所述回流原料罐置于回流电子称上进行回流量测量,具体实施时,原料油加热后进入原料油入口,或原料油加热前,分出一路经过回流原料罐、回流泵,进入回流口;或者所述低温石油烃回流进料部分,由所述原料罐和原料油泵用管线与回流口连接构成,即直接从原料油泵出口(原料加热炉前)用管线与回流口连接,用部分原料油作为回流进料,实现原料油直接用于分离罐回流原料;优选回流原料使用水,回流原料罐和回流泵依次通过管线连通分离罐回流口,实现回流水进入分离罐;具体实施时,还可设置水(回流)进料部分,由储水罐通过管线连通分离罐顶部或回流口构成,具体实施时,根据实施需要可设置相应的泵;所述闪蒸分离部分包括分离罐,所述原料油入口、蒸汽进料入口和回流口均设置于所述分离罐上;所述分离罐竖直放置;分离罐设置有气体产物出口和液体产物出口,所述分离罐顶部或气体产物出口设有温度变送器、压力变送器和压力控制器;具体实施时,蒸汽进料入口位于原料油入口下方,来自汽提水汽化加热炉的汽提蒸汽进入到分离罐下部的液体物流中,向上流动,与来自原料油入口和回流口的重质石油烃接触,进一步提高轻油拔出率;所述分离罐分离的气体组分从分离罐顶部的气体产物出口从管线流出分离罐,然后气体状态或者进入催化裂解实验装置反应器,或者进入气体产物收集部分,或者从气体产物收集部分经管线进入催化裂解实验装置反应器;所述分离罐分离出的高沸点组分或重油从液体产物出口流出分离罐,然后经管线或者进入催化裂解实验装置反应器,或者进入液体产物收集部分,或者进入液体产物收集部分后再进入催化裂解或催化裂化实验装置反应器;所述控制部分,包括原料罐计量控制、回流原料罐计量控制、原料油泵的泵控制、回流泵的控制、分离罐及各连接管线上设置的加热炉或热补偿带温度控制,以及上述加热炉或热补偿带对应设置的温度控制器。
8.上述的石油烃分离实验装置,进一步地,所述石油烃分离装置的进料部分还包括汽提水进料部分,所述石油烃分离装置采用向原料油中注水或蒸汽,或向分离罐底部液体内注入水或蒸汽进行石油烃低沸点组分分离;所述汽提水进料部分,设置有水罐,水泵和水汽化加热炉,汽提水从水罐依次通过管线经过水泵和水汽化加热炉形成加热的蒸汽,再通过蒸汽进料入口进入分离罐,或/和加热后的蒸汽依次通过管线经汽提水管线和原料油管线连接线连通原料油入口和原料油混合后进入分离罐,使汽提水蒸汽并入加热后的原料油管线,或者同时实现汽提水蒸汽并入加热后原料油的进料;或者所述水泵和分离罐底部连通,水从水泵出口进入分离罐底部;所述水罐置于水电子称上进行蒸汽流量或水流量的测量,实现汽提水或蒸汽进料的精确计量。具体实施时,汽提水加热后以水蒸气状态进入蒸汽
进料入口,和/或加热后以水蒸气状态与加热后的原料油液体混合,一并通过原料油入口。
9.上述的石油烃分离实验装置,优选地,设置气体产物收集部分和/或液体产物收集部分;所述气体产物收集部分包括轻质油或气体产物冷却器、轻质油组分罐、管线、管线电补热、管线外温度热电偶及温度控制,在气体产物出口和轻质油组分罐之间的管线上设置轻质油或气体产物冷却器,或/和在气体产物出口与催化裂解实验装置反应器之间设置连接管线,所述管线和连接管线上设热补偿、温度热电偶;所述液体产物收集部分包括重质油收集罐、重质油冷却器、管线、管线温度补偿和温度热电偶;在液体产物出口和重质油组分罐间的管线上设置重质油冷却器,或/和在液体产物出口与催化裂解实验装置反应器或催化裂化实验装置反应器之间设置连接管线,所述管线和连接管线外设热补偿和温度热电偶。
10.上述的石油烃分离实验装置,优选地,分离罐内设填料和除沫器或液体聚结器;所述除沫器或液体聚结器设在填料上方或分离罐顶部;所述原料油入口和蒸汽进料入口位于所述填料下方,所述回流口位于填料和除沫器或液体聚结器之间或两层填料之间。具体实施时,回流口位于填料上方、除沫器或液体聚结器下方,或填料层之间,来自回流口的石油烃与分离后上升的轻组分接触,重组分石油烃向下流动,轻质石油烃是气相,向上流动,实现上升气体组分和液体组分的逆流流动,进一步分离轻质石油烃携带的重组分;优选地,填料为规整填料或散装填料,规整填料为一块或多块;散装填料为鲍尔环或/和狄克松环。
11.上述的石油烃分离实验装置,优选地,被分离的石油烃或原料油进料部分的原料油为原油,脱盐脱水后的原油,或其他来源的馏程在50℃~500℃混合石油烃;经原料油加热炉加热后的原料油温度为120℃~500℃。更优选的,加热后的原料油温度为120℃~400℃。
12.上述的石油烃分离实验装置,优选地,所述低温石油烃回流进料部分的回流原料为水,原油,脱盐脱水后的原油或馏程在200℃~500℃的混合石油烃中的一种或几种;回流原料的回流量占原料进料量的0~50%。回流原料储存在回流原料罐内。
13.上述的石油烃分离实验装置,优选地,分离罐的压力由位于气体产物出口管线上或分离罐顶的压力控制器控制,压力控制范围在-60kpa(表压)~800 kpa(表压)。具体实施时,如果要与下游的催化裂化/催化裂解反应装置联运时,分离罐压力须大于反应装置的压力,以保证反应装置的平稳操作。
14.上述的石油烃分离实验装置,优选地,由水罐通过水泵、水汽化加热炉后进入分离罐的汽提蒸汽量占闪蒸分离及产物收集部分中闪蒸原料油量的0.1%(wt)~50%(wt),汽提蒸汽的温度为100℃~500℃。
15.上述的石油烃分离实验装置,优选地,在所述水泵和原料油加热炉之间设置连通管线,具体实施时,水罐、水泵、原料油加热炉依次通过管线连通原料油入口,使液体水并入未加热的原料油管线,混合后在原料油加热炉加热后经原料油入口进入分离罐。
16.上述的石油烃分离实验装置,优选地,在所述轻质油组分罐和重质油组分罐之间设置混合管线,所述混合管线与原料罐或回流原料罐连通;轻质油组分罐的油品与重质油组分罐的油品在混合管线上的轻、重组分混合处混合后,进入原料罐或回流原料罐。具体实施时,如果离线操作,即不与下游的催化裂化/催化裂解装置联运时,所述轻质油组分罐和重质油组分罐内的油品,可以卸出装置外,也可以打回流,轻质油组分罐的油品与重质油组
分罐的油品在混合管线上的轻、重组分混合处混合后,进入原料罐或回流原料罐;若与下游的催化裂化/催化裂解装置联运时,则联运前,需要轻、重组分混合处混合后,进入原料罐或回流原料罐。
17.有益效果:本发明提供的原料油分离实验装置,实现无侧线取热的原料油闪蒸分离,同时又通过以原料回流方式解决了闪蒸塔分离率低、分离精度差的问题;以原料独立回流方式双组分分离,避免了常规侧线换热回流物流性质不能选择对分离效果的限制;采用注入蒸汽的办法明显提高低沸点组分分出率并减少组分重叠;其分离罐仅需设置少量填料(或塔盘)即可达到原料油分离的目的;本发明实现了分离低沸点组分气相外输;操作压力可根据下游催化裂化装置反应压力需要调整,且无论是原料油自身携带进装置的水组分还是注入汽提蒸汽所额外添加的水组分,都将随塔顶油气一起进入下游催化裂化反应装置,节省了下游反应器蒸汽注入压力,同时提高了分离罐中轻油拔出率,改善了分离油品质量。该实验装置既能实现离线操作(即不与下游提升管装置联运),满足实验室对不同馏程范围石油烃作为实验原料的需求,又能与下游提升管反应装置联运,实现原料油闪蒸分离后直接作为反应装置进料。
附图说明
18.图1:本发明的石油烃分离实验装置实施方式一装置结构示意图;图2:本发明的石油烃分离实验装置实施方式二装置结构示意图;图3:本发明的石油烃分离实验装置实施方式三装置结构示意图。
19.图中编号:01原料罐,02原料油泵,03原料油加热炉,04分离罐,05填料,06除沫器或液体聚结器,07水泵,08水汽化加热炉,09压力控制器,10回流原料罐,11回流泵,12原料油入口,13气体产物出口,14液体产物出口,15回流口,16温度变送器17压力变送器,18回流电子称,19原料油电子称,20水电子称,21水罐,22热补偿带,23轻质油或气体产物冷却器,24汽提水管线和原料油管线连接线,25重质油冷却器,26蒸汽进料入口,27重质油组分罐,28轻质油组分罐,29轻、重组分混合处,30管线ⅰ,31管线ⅱ。
具体实施方式
20.下面结合附图及实施例对本发明做进一步说明,但并不限制本发明。
21.实施方式一:如图1所示, 一种石油烃分离实验装置,分为进料部分、闪蒸分离及产物收集部分、控制部分;进料部分分3路,包括被分离的石油烃或原料油进料部分、汽提水进料和低温石油烃回流进料部分。被分离的石油烃或原料油进料部分通过原料罐01放置于原料油电子称19上,与原料油泵02、原料油加热炉03、原料油入口12,依次通过管线连通;汽提水进料通过水罐21置于水电子称20上,与水泵07、水汽化加热炉08、蒸汽进料入口26依次管线连通,或者上述管线的汽提水同时经过汽提水管线和原料油管线连接线24进入原料油入口12;低温石油烃回流进料部分通过回流原料罐10置于回流电子称18上,与回流泵11、回流口15依次管
线连通;闪蒸分离及产物收集部分,由内置分离罐04、填料05、除沫器或液体聚结器06、重质油组分罐27、轻质油组分罐28组成,填料05和除沫器或液体聚结器06置于分离罐04内,分离罐04竖直放置,填料05位于分离罐04的中上部,除沫器或液体聚结器06位于分离罐04顶部;气体产物出口13连接到轻质油组分罐28,且连接管线上设有轻质油或气体产物冷却器23;液体产物出口14连接到重质油组分罐27,且连接管线上设有重质油冷却器25;所述分离罐出口04设有温度变送器16、压力变送器17、压力控制器09;分离罐04有5个开口,从上往下依次是气体产物出口13、回流口15、原料油入口12、蒸汽进料入口26、液体产物出口14,气体产物出口13位于罐顶并位于除沫器或液体聚结器06上方,液体产物出口14位于罐底,回流口15位于填料05和除沫器或液体聚结器06之间,原料油入口12和蒸汽进料入口26均位于填料05下方;控制部分,包括原料罐01计量控制、回流原料罐10计量控制、原料油泵02的泵头控制和回流泵11的泵头控制,分离罐04及各连接管线均设置热补偿带22及对应的温度控制器。
22.具体实施时,分别从回流口15来的回流原料、原料油入口12来的石油烃原料、蒸汽进料入口26来的汽提蒸汽进入分离罐04,分离成轻、重两种石油烃组分,轻组分石油烃经气体产物出口13、轻质油或气体产物冷却器23进入轻质油组分罐28;重组分石油烃经过液体产物出口14、重质油冷却器25进入重质油组分罐27。
23.实施方式二:如图2所示,一种石油烃分离实验装置,分为进料部分、闪蒸分离及产物收集部分、控制部分;进料部分分3路,包括被分离的石油烃或原料油进料部分、汽提水进料、低温石油烃回流进料部分。被分离的石油烃或原料油进料部分通过原料罐01放置于原料油电子称19上,与原料油泵02、原料油加热炉03、原料油入口12,依次通过管线连通;汽提水进料通过水罐21置于水电子称20上,与水泵07、水汽化加热炉08、蒸汽进料入口26或经过汽提水管线和原料油管线连接线24进入原料油入口12,依次管线连通;低温石油烃回流进料部分通过回流原料罐置10于回流电子称18上,与回流泵11、回流口15依次管线连通;闪蒸分离及产物收集部分, 由内置分离罐04、填料05、除沫器或液体聚结器06、重质油组分罐27、轻质油组分罐28组成;气体产物出口13连接到轻质油组分罐28,且连接管线上设有轻质油或气体产物冷却器23;液体产物出口14连接到重质油组分罐27,且连接管线上设有重质油冷却器25;所述分离罐出口04设有温度变送器16、压力变送器17、压力控制器09;轻质油组分罐28与重质油组分罐27内介质并线后于轻、重组分29混合处混合,进入回流原料罐10;分离罐04有5个开口,从上往下依次是气体产物出口13、回流口15、原料油入口12、蒸汽进料入口26、液体产物出口14;控制部分,包括原料罐01计量控制、回流原料罐10计量控制、原料油泵02的泵头控制和回流泵11的泵头控制,分离罐04及各连接管线均设置热补偿带22及对应的温度控制器。其他部分装置结构同实施方式一。
24.具体实施时,分别从回流口15来的回流原料、原料油入口12来的石油烃原料、蒸汽
进料入口26来的汽提蒸汽进入分离罐04,分离成轻、重两种石油烃组分,轻组分石油烃经气体产物出口13、轻质油或气体产物冷却器23进入轻质油组分罐28;重组分石油烃经过液体产物出口14、重质油冷却器25进入重质油组分罐27;具体实施时,待分离罐04温度和压力调到设定值后,气体产物出口13经管线ⅰ30切换到装置外的提升管反应装置原料入口ⅰ;液体产物出口14经管线ⅱ31切换到装置外的提升管反应装置原料入口ⅱ,实现与下游的催化裂化实验装置联运。
25.实施方式三:如图3所示, 一种石油烃分离实验装置,分为进料部分、闪蒸分离及产物收集部分、控制部分;进料部分分3路,包括被分离的石油烃或原料油进料部分、汽提水进料部分、低温石油烃回流进料部分。被分离的石油烃或原料油进料部分通过原料罐01放置于原料油电子称19上,与原料油泵02、原料油加热炉03、原料油入口12,依次通过管线连通;汽提水进料部分通过水罐21置于水电子称20上,与水泵07、水汽化加热炉08、蒸汽进料入口26或经过汽提水管线和原料油管线连接线24进入原料油入口12,依次管线连通;低温石油烃回流进料部分通过回流原料罐10置于回流电子称18上,与回流泵11、回流口15依次管线连通;闪蒸分离及产物收集部分, 由内置分离罐04、填料05、除沫器或液体聚结器06、重质油组分罐27、轻质油组分罐28组成;气体产物出口13连接到轻质油组分罐28,且连接管线上设有轻质油或气体产物冷却器23;液体产物出口14连接到重质油组分罐27,且连接管线上设有重质油冷却器25;所述分离罐出口04设有温度变送器16、压力变送器17、压力控制器09;分离罐04有5个开口,从上往下依次是气体产物出口13、回流口15、原料油入口12、蒸汽进料入口26、液体产物出口14;控制部分,包括原料罐01计量控制、回流原料罐10计量控制、原料油泵02的泵头控制和回流泵11的泵头控制,分离罐04及各连接管线均设置热补偿带22及对应的温度控制器。液体产物出口14经管线ⅱ31连通装置外的提升管反应装置原料入口ⅱ,气体产物出口13经管线ⅰ30连通装置外的提升管反应装置原料入口ⅰ,其他部分装置结构同实施方式一。
26.具体实施时,分别从回流口15来的回流原料、原料油入口12来的石油烃原料、蒸汽进料入口26来的汽提蒸汽进入分离罐04,分离成轻、重两种石油烃组分,轻组分石油烃经气体产物出口13、轻质油或气体产物冷却器23进入轻质油组分罐28;重组分石油烃经过液体产物出口14、重质油冷却器25进入重质油组分罐27;具体实施时,待分离罐04温度和压力调到设定值后,气体产物出口13经管线ⅰ30切换到提升管反应装置原料入口ⅰ;液体产物出口14经管线ⅱ31切换到提升管反应装置原料入口ⅱ,实现与下游的催化裂化实验装置联运。
27.实施例1:石油烃进料量5kg/h,分离罐(闪蒸罐)操作压力250kpa(表压);石油烃进料温度340℃、汽提水进料温度350℃,汽提水进量为300g/h,回流原料进料温度130℃,回流原料进料量为100g/h,回流原料为馏程350℃-500℃的重质石油烃。闪蒸分离后,轻质油组分罐介质温度35℃、重质油组分罐介质温度30℃;分离罐内所用填料为狄克松环;分离罐壁外全部设厚度10mm的隔热层,隔热层材料导热系数0.1;隔热层外分三段
设外补热电加热炉丝,每段最大功率0.99kw,使用功率可调;电加热炉丝采用220伏特电压供电;各设备外侧或电加热炉丝外侧设80mm厚保温层;本实施例中,反应器操作温度400℃,操作压力150kpa(表压)。