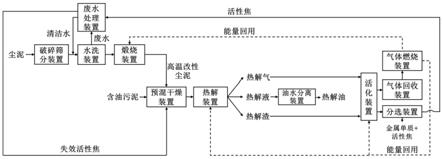
1.本发明属于工业固体废弃物资源化利用技术领域,具体涉及一种改性尘泥材料的制备与其配伍含油污泥低消耗热解制备高含量直链烷烃产物的装置及方法。
背景技术:2.工业生产过程中产生的固体废弃物称为工业固废。工业固废异质多样、成分与性质极其复杂,可以分为无机工业固废和有机工业固废两大类。尘泥和含油污泥分别是无机工业固废和有机工业固废的典型代表。
3.烧结、炼铁、炼钢等工序产生的粉尘、烟尘以及轧钢生产过程产生的轧钢铁皮等,常称为尘泥。按每吨钢产生尘泥190千克计,我国尘泥年产量在8000万吨以上。随着钢铁工业的发展,尘泥产量会逐渐增加。为了合理利用资源并保护环境消除粉尘污染,充分利用尘泥已是现代钢铁企业生产中不可缺少的一个组成部分。常规尘泥回收方式为浮/重联选工艺,浮选剂消耗量大。当下对其处理多为独立进行,缺乏其与含油污等有机工业固废有效的协同。
4.含油污泥是一种由石油烃、土壤有机质、无机矿物质、水、氮、硫、氯、重金属元素以及添加剂组成的混合物。根据产生源,含油污泥可分为油田含油污泥(oil field os)、储运含油污泥(storage and transportation os)、炼油厂含油污泥(refinery os)和事故含油污泥(accident os)。据我国生态环保部统计,中国工业操作系统中含油污泥年产量已超过600万吨,历史总存量已达到1.43亿吨。含油污泥因其可燃性、毒性、难生物降解性,生物毒性等被列入《国家危险废物名录》清单中。含油污泥平均石油含量约为10~30%,鉴于其潜在资源性及危害性并存,亟需适合含油污泥资源化处理的新技术。迄今为止,已经开发了相当多的含油污泥处理方法,其中使用较广泛的是调制-机械分离技术与热处理技术,调制机械分离技术处理后残渣含油率高,热处理技术主要包括焚烧与热解技术,焚烧技术处理资源利用效率低并且会产生二噁英等二次污染,相比于这些方法,热解技术因其自身特点而受到广泛关注。含油污泥在高温缺氧环境下分解为小分子的热解气和中分子的热解油,残渣中含油率低,并且由于反应气氛缺氧,排气量小,减轻了对大气的二次污染。但热解技术也同样具有其技术瓶颈,主要体现在含油污泥热解产物附加值低且热解过程耗能高。这是由于含油污泥黏性大,热解过程传热传质较困难。
5.直链烷烃是含油污泥热解产物之一,其在化工生产中具有重要意义。cn201120503691.9公开了一种连续分离提取石脑油中直链烷烃的装置,其指出在乙烯工业生产过程中直链烷烃作为优质裂解原料最易生成乙烯等目的产物,从而提高乙烯产率,降低劣质裂解汽油产率,降低炉管结焦量,延长开工周期,经济效益提高。此外,直链烷烃还可作为芳香化反应的中间体,并在蛋白质/维生素液浓缩物的制备中得到应用。因此,若能增加含油污泥热解油中直链烷烃含量,会极大程度提高热解油附加值。
6.cn201910885711.4公开了一种油泥热解与钢渣还原协同处置的方法,其将油泥加
热软化,与一定粒度钢渣按照合适比例混合,放置于连续热解磁选装置上加热到适宜温度,选择合适的停留时间和磁选管磁场强度,获得热解油气产品并还原钢渣。该专利通过热解的方式实现了油泥的减量化,但仍存在如下问题:钢渣的加入并未增加热解油产率,且热解油中直链烷烃含量低。这是由于常规钢渣表面被炭黑、碳质沉积物和各种结焦物质覆盖,堵塞钢渣内原有孔隙,影响含油污泥与钢渣内部活性位点接触,阻碍钢渣的催化效果,在其与含油污泥热解过程中会阻碍挥发分的析出,促进挥发分二次裂解成为小分子的热解气。
技术实现要素:7.针对上述问题和技术分析,本发明的目的是提供一种改性尘泥配伍含油污泥低消耗热解制备高含量直链烷烃产物的装置及方法。制备的改性尘泥与传统尘泥相比,去除了在其表面堆积的绝大部分炭黑、碳质沉积物和结焦物质,大幅增加了尘泥的孔隙率和表面活性,氧化铁结晶性好,取向度高。改性尘泥为含油污泥热解提供优质的催化及热载作用,极大程度提高含油污泥热解过程传热传质效果,并降低了热解过程能耗,制备的热解油富含直链烷烃成分,附加值高。热解渣与热解气送入活化装置后从固体产物中分离出金属单质与活性焦,活性焦用于废水处理装置,产气送入气体燃烧装置进行燃烧,能量回用于煅烧及热解装置。
8.本发明采用的技术方案如下:
9.一种改性尘泥配伍含油污泥低消耗热解制备高含量直链烷烃产物的装置,所述的装置包括破碎筛分装置、水洗装置、煅烧装置、预混干燥装置、热解装置、油水分离装置、活化装置、气体回收装置、气体燃烧装置、分选装置和废水处理装置;
10.所述的破碎筛分装置出口通入水洗装置;
11.所述的水洗装置的液相出口通入废水处理装置,固相出口通入煅烧装置;
12.所述的煅烧装置固相出口通入预混干燥装置;
13.所述的预混干燥装置出口通入热解装置;
14.所述的热解装置的气相出口、固相出口均通入活化装置,液相出口通入油水分离装置;
15.所述的活化装置气相出口通入气体回收装置,固相出口通入分选装置;
16.所述的气体回收装置气相出口通入气体燃烧装置;
17.所述的分选装置的活性焦出口通入废水处理装置;
18.所述的废水处理装置的液相出口通入水洗装置,固相出口通入预混干燥装置。
19.一种改性尘泥配伍含油污泥低消耗热解制备高含量直链烷烃产物的方法,具体如下:
20.(1)尘泥经破碎筛分装置破碎、筛分后送入水洗装置,水洗装置用于除去尘泥表面堵塞孔道的可溶性杂质,水洗过程中产生的废水送入废水处理装置,水洗后的尘泥送入煅烧装置,在有氧条件下煅烧,尘泥中夹杂的炭黑、碳质沉积物、结焦物质在高温下与氧气充分接触,发生氧化反应而被除去,尘泥内部堵塞的孔道被打开,大幅增加了尘泥的孔隙率和表面活性,取向度高;
21.(2)含油污泥与煅烧后的高温改性尘泥在预混干燥装置内充分混合,煅烧后的高温改性尘泥起到热固载体作用,通过热传递将自身热量传递给含油污泥,对含油污泥进行
脱水干燥并降低其粘度,干燥阶段结束后含油污泥与尘泥混合物送入热解装置,含油污泥挥发分进行开环反应,生成直链烷烃产物,同时热解渣中的焦炭及热解气中h2、co将尘泥中的金属氧化物还原为金属单质;在此过程中,尘泥改性后其内部丰富孔道能够提高热解过程的传质能力并极大程度降低了热解过程的能耗,改性尘泥兼具催化效果,促进含油污泥挥发分的开环反应,生成高含量直链烷烃产物;
22.(3)热解过程中产生的热解液经过油水分离装置,分离出水和直链烷烃热解油并将其回收,热解气与热解渣共同送入到活化装置,活化装置出口的固体经分选装置分离出金属单质及活性焦,部分活性焦送入废水处理单元,多余活性焦进行回收,活化装置出口的气体统一经气体回收装置回收后送入气体燃烧装置进行燃烧,燃烧产生的热量回用于煅烧装置、热解装置及活化装置。
23.(4)废水回收装置内利用活性焦将其内部的废水进行处理,处理后的清洁水送入水洗装置循环使用,处理过程中产生的失效活性焦送入预混干燥装置,重复干燥、热解及活化过程后再生回用。
24.所述的尘泥是指:在烧结、炼铁、炼钢等工序产生,后经布袋除尘、重力除尘、电除尘、环冷除尘等除尘器收集得到的黑褐色粉末,主要成分为铁、钙、硅、铝、镁等金属元素。
25.所述的尘泥经破碎、筛分后,尺寸为60~100目。
26.所述的水洗装置中每次清洗尘泥与水的体积比例为1:10~50,水洗次数大于3次。
27.所述煅烧装置煅烧温度为700~900℃,煅烧时间为3~6h。
28.含油污泥与煅烧后的高温改性尘泥混合比例:高温改性尘泥是含油污泥质量的5%~20%。
29.所述的含油污泥是指:原油或成品油混入泥土或其他介质中产生的油、水、固三相悬浮乳液稳定分散体系。其含水率为40.0~90.0%、含油率为15.0~50.0%、含固率为5.0~46.0%、ph介于6.5~7.5,伴有刺激性气味。
30.所述热解温度为400~700℃,热解时间为30~120min,热解保护气为氮气,流速为100~200ml/min。
31.所述油水分离装置采用离心、分液、溶剂萃取、旋转蒸发除溶剂的工艺,溶剂萃取时萃取剂为ch2cl2,旋转蒸发温度为40~60℃,真空度为0.01~0.03mpa,旋转蒸发结束标志为剩余液体质量不变化。热解油中直链烷烃含量可达40%~60%。
32.所述活化温度为800~1200℃,活化时间为3~6h。
33.所述热解渣分选装置采用重力分选工艺,利用金属单质与热解残值的密度不同,分选出金属单质及剩余残渣。
34.本发明的效果和益处:本发明同现有技术相比,提供了一种改性尘泥配伍含油污泥热解制备高含量直链烷烃产物的装置及方法,具有如下优点:
35.(1)实现含油污泥的无害化与资源化:鉴于含油污泥来源广、产量大,潜在资源性及危害性并存,亟需适合含油污泥无害化资源化处理的新技术。使用改性尘泥作为热解过程催化剂,促进了含油污泥挥发分的开环反应,生成高含量直链烷烃的热解油,提高热解油的附加值。同时,改性尘泥孔隙率和表面活性高,氧化铁结晶性好,取向度高,是热解过程优异的热固载体,其丰富孔隙增强了热解过程传热及传质效果。
36.(2)实现尘泥资源化:尘泥来源广泛,年产量大,常规回收方式为浮/重联选工艺,
浮选剂消耗量大。通过破碎筛分、水洗、煅烧、成功制备高孔隙率、高表面活性、高结晶性、高取向性的改性尘泥,用于含油污泥热解工艺,并利用含油污泥热解渣中的焦炭及热解气中h2、co等还原性物质在活化装置内将尘泥中金属氧化物还原为金属单质,实现尘泥高值化利用。
37.(3)节能、环保,经济价值高:含油污泥与煅烧后的高温改性尘泥在预混干燥装置内充分混合,煅烧后高温的改性尘泥起到热固载体作用,通过热传递将自身热量传递给含油污泥,对含油污泥进行脱水干燥并降低其粘度,降低了热解过程的能耗。活化装置出口的气体统一经气体回收装置回收后送入气体燃烧装置进行燃烧,燃烧产生的热量回用于煅烧装置、热解装置及活化装置。热解渣中的焦炭及热解气中h2、co等还原性物质将尘泥中金属氧化物还原为金属单质,热解液经油/水分离单元分离后得到高含量直链烷烃热解油,经济价值高。废水回收装置内利用活性焦将其内部的废水进行处理,处理后的清洁水送入水洗装置循环使用,处理过程中产生的失效活性焦送入预混干燥装置,重复干燥、热解及活化过程后再生回用,节约水资源,保护环境。
附图说明
38.图1是一种改性尘泥配伍含油污泥热解制备高含量直链烷烃产物的装置及方法流程示意图。
39.图2是本发明改性前与改性后尘泥材料的sem图。其中,(a)为改性前尘泥扫描电镜图(5000倍),(b)为改性前尘泥扫描电镜图(15000倍),(c)为改性后尘泥扫描电镜图(5000倍),(d)为改性后尘泥扫描电镜图(15000倍)。
40.图3是本发明改性前与改性后尘泥材料的xrd图。
具体实施方式
41.下面结合实施例对本发明进行详细说明,以使本领域技术人员更好地理解本发明,但本发明并不局限于以下实施例。
42.实施例1:
43.一种改性尘泥配伍含油污泥热解制备高含量直链烷烃产物的装置及方法,该装置包括破碎筛分装置、水洗装置、煅烧装置、预混干燥装置、热解装置、油水分离装置、活化装置、气体回收装置、气体燃烧装置、分选装置和废水处理装置;
44.实验选用的含油污泥取自辽宁省盘锦市某炼油厂罐底含油污泥,其常温状态下为黑褐色,并伴随着刺鼻的石油类气体的气味,使用卡尔菲修滴定测定含油污泥含水率,索氏提取测试含油污泥含固率,差减法计算其含油率,含油污泥含水率、含油率、含固率分别为50.98%、含油率29.60%、含固率19.42%。选用的尘泥为某钢铁企业重力除尘器除尘灰,xrf检测结果表明其fe2o3含量为70.17%。将尘泥置于球磨机中,转速300r/min,破碎60min,用筛网筛分,选取颗粒大小为60~100目的尘泥。称取20g筛分后的尘泥,使用真空抽滤方式,用去离子水洗涤尘泥6次,每次洗涤去离子水用量为1000ml,废水送入废水处理装置,水洗后的尘泥进入煅烧装置,煅烧温度为800℃,煅烧时间为4h,得到改性尘泥,改性前后尘泥材料的sem分析结果(图2)表明改性后尘泥较光滑的表面被破坏,表面变得粗糙,呈现出各种不规则的沟槽状和较大的疏松结构。改性前后尘泥材料的xrd分析结果(图3)表明改性后
尘泥物相分布清晰,氧化铁结晶性好,取向度高。与改性前相比,在2θ为33.19
°
、35.65
°
处有较强衍射峰,其对应fe2o3结构的主要特征峰。
45.称取5g含油污泥,在均质化单元后,与0.25g煅烧后的高温改性尘泥在预混干燥装置内充分混合,对含油污泥进行脱水干燥并降低其粘度,干燥阶段结束后含油污泥与尘泥混合物送入热解装置,热解温度为500℃,使用n2作为载气,流速为100ml/min,停留时间60min,得到热解气、热解液、热解渣。热解液经过油/水分离装置,在3000r/min下离心20min,分液,使用ch2cl2溶剂萃取热解油,旋转蒸发除去溶剂,旋转蒸发温度为40℃,真空度为0.02mpa,当剩余液体质量不变化时视为旋转蒸发结束。
46.另取5g含油污泥,在均质化单元后,与0.25g未活化尘泥进行热解反应,热解温度为500℃,使用n2作为载气,流速为100ml/min,停留时间60min,得到热解气、热解液、热解渣。热解液经过油/水分离装置,在3000r/min下离心20min,分液,使用ch2cl2溶剂萃取热解油,旋转蒸发除去溶剂,旋转蒸发温度为40℃,真空度为0.02mpa,当剩余液体质量不变化时视为旋转蒸发结束。
47.另取5g含油污泥,在均质化单元后,进入热解装置,热解温度为500℃,使用n2作为载气,流速为100ml/min,停留时间60min,得到热解气、热解液、热解渣。热解液经过油/水分离装置,在3000r/min下离心20min,分液,使用ch2cl2溶剂萃取热解油,旋转蒸发除去溶剂,旋转蒸发温度为40℃,真空度为0.02mpa,当剩余液体质量不变化时视为旋转蒸发结束。
48.不添加尘泥,含油污泥热解油产率为33.11%,热解渣产率为41.84%,热解气产率为4.31%,石油类化合物转化率为62.93%,使用气相色谱-质谱联用仪对热解油进行成分分析。采用流速为1.2ml/min的高纯氦气作为载气,配备有hp-5ms色谱柱(30m
×
0.25mm
×
0.25μm),色谱纯二氯甲烷作为有机溶剂,按体积比1:20将油相产物进行稀释。采用的升温程序为:40℃下保持2min,随后以4℃/min的升温速率升温至300℃,停留5min。使用nist05数据库进行化合物定性识别。结果显示,热解油中直链烷烃含量为39.08%。
49.添加0.25g未活化尘泥后含油污泥热解油产率为32.82%,热解渣产率为42.02%,热解气产率为4.65%,石油类化合物转化率为63.02%。使用气相色谱-质谱联用仪对热解油进行成分分析。采用流速为1.2ml/min的高纯氦气作为载气,配备有hp-5ms色谱柱(30m
×
0.25mm
×
0.25μm),色谱纯二氯甲烷作为有机溶剂,按体积比1:20将油相产物进行稀释。采用的升温程序为:40℃下保持2min,随后以4℃/min的升温速率升温至300℃,停留5min。使用nist05数据库进行化合物定性识别。结果显示,热解油中直链烷烃含量为39.22%。
50.添加0.25g活化尘泥后含油污泥热解油产率为37.77%,热解渣产率为38.69%,热解气产率为3.62%,石油类化合物转化率为69.61%。使用气相色谱-质谱联用仪对热解油进行成分分析。采用流速为1.2ml/min的高纯氦气作为载气,配备有hp-5ms色谱柱(30m
×
0.25mm
×
0.25μm),色谱纯二氯甲烷作为有机溶剂,按体积比1:20将油相产物进行稀释。采用的升温程序为:40℃下保持2min,随后以4℃/min的升温速率升温至300℃,停留5min。使用nist05数据库进行化合物定性识别。结果显示,热解油中直链烷烃含量为44.52%。
51.热解渣与热解气共同送入到活化装置,活化温度为1100℃,将残渣制备成活性焦后经分选装置分选出活性焦与金属单质,部分活性焦送入废水处理单元,多余活性焦进行回收,活化装置出口的气体统一经气体回收装置回收后送入气体燃烧装置进行燃烧,燃烧产生的热量回用于煅烧装置、热解装置及活化装置。废水回收装置内利用活性焦将其内部
的废水进行处理,处理后的清洁水送入水洗装置循环使用,处理过程中产生的失效活性焦送入预混干燥装置,重复干燥、热解及活化过程后再生回用。
52.实施例2:
53.称取5g含油污泥,在均质化单元后,与0.5g煅烧后的高温改性尘泥在预混干燥装置内充分混合,对含油污泥进行脱水干燥并降低其粘度,干燥阶段结束后含油污泥与尘泥混合物送入热解装置,热解温度为500℃,使用n2作为载气,流速为100ml/min,停留时间60min,得到热解气、热解液、热解渣。热解液经过油/水分离装置,在3000r/min下离心20min,分液除水,使用ch2cl2溶剂萃取热解油,旋转蒸发除去溶剂,旋转蒸发温度为40℃,真空度为0.02mpa,当剩余液体质量不变化时视为旋转蒸发结束。热解油产率为43.55%,热解渣产率为37.48%,热解气产率为2.43%,石油类化合物转化率为77.31%。使用气相色谱-质谱联用仪对热解油进行成分分析。采用流速为1.2ml/min的高纯氦气作为载气,配备有hp-5ms色谱柱(30m
×
0.25mm
×
0.25μm),色谱纯二氯甲烷作为有机溶剂,按体积比1:20将油相产物进行稀释。采用的升温程序为:40℃下保持2min,随后以4℃/min的升温速率升温至300℃,停留5min。使用nist05数据库进行化合物定性识别。结果显示,热解油中直链烷烃含量为54.30%。
54.热解渣与热解气共同送入到活化装置,活化温度为1100℃,将残渣制备成活性焦后经分选装置分选出活性焦与金属单质,部分活性焦送入废水处理单元,多余活性焦进行回收,活化装置出口的气体统一经气体回收装置回收后送入气体燃烧装置进行燃烧,燃烧产生的热量回用于煅烧装置、热解装置及活化装置。废水回收装置内利用活性焦将其内部的废水进行处理,处理后的清洁水送入水洗装置循环使用,处理过程中产生的失效活性焦送入预混干燥装置,重复干燥、热解及活化过程后再生回用。
55.表1本发明实施例1和实施例2所获得的热解油产率及直链烷烃含量
56.