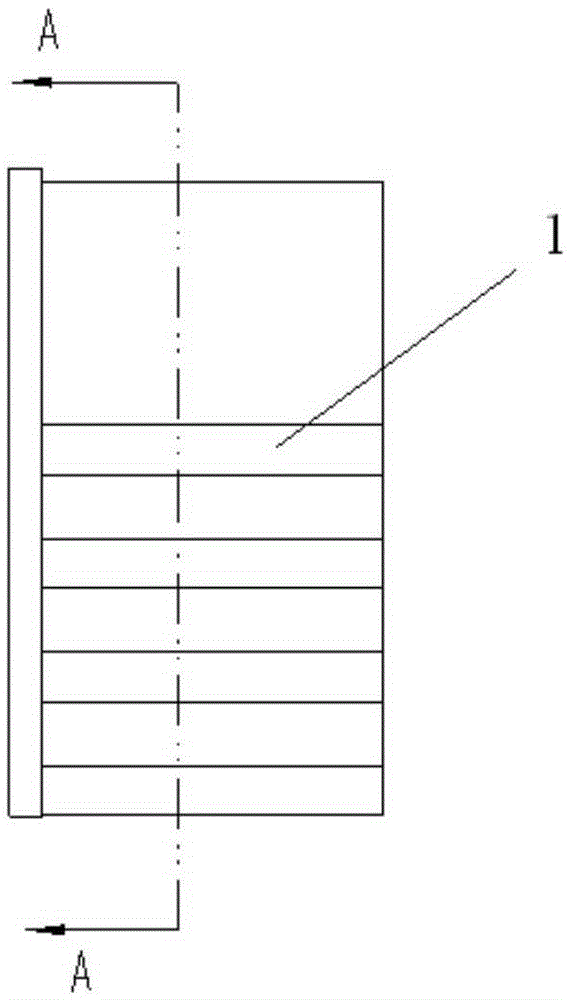
本发明涉及发动机
技术领域:
,特别是涉及一种发动机油气分离器及具有其的发动机总成。
背景技术:
:随着发动机的发展,对发动机排放要求一再提高。因此,人们对发动机的油气分离系统越来越重视,对油气分离器分离效果要求越来越苛刻。此外,油气分离器在满足法规排放要求的同时,在提高发动机的性能和提高燃油经济性发挥着不可磨灭的作用。现有发动机的油气分离器形式多样化,主要结构组成分类有迷宫挡板式结构、旋风式结构、滤纸结构、粒子电离结构等。现有发动机的油气分离器存在空间布置困难,外接管路长有结冰风险,而且低成本油气分离器分离效果差如迷宫挡板式,而分离效果较好的油气分离器相对成本较高,如粒子电离结构。因此,希望有一种技术方案来克服或至少减轻现有技术的上述缺陷中的至少一个。技术实现要素:本发明的目的在于提供一种发动机油气分离器来克服或至少减轻现有技术的上述缺陷中的至少一个。为实现上述目的,本发明提供一种发动机油气分离器,所述发动机油气分离器包括:第一分离组件;以及第二分离组件,所述第二分离组件位于所述第一分离组件的下游,且包括分离板,所述分离板上设置有多个凸起,相邻凸起之间具有气流间隙。优选地,所述多个凸起为陈列式排布。优选地,所述多个凸起从根端向末端延伸,且在延伸方向上截面积逐渐变小。优选地,所述分离板包括基板,所述多个凸起设置于所述基板上。优选地,所述所述基板与所述多个凸起一体注塑成型。优选地,所述第二分离组件进一步包括位于所述分离板上游的导流孔板,所述导流孔板上设置有多个导流孔,其中,所述导流孔对准所述分离板的中心偏上区域,且所述第二分离组件的排气区域设置在所述分离板的下方。优选地,所述发动机油气分离器进一步包括位于所述分离板下方的储油池,以及设置在所述储油池的底部处的回油单向阀,其中,所述回油单向阀包括回油阀壳体和阀片,所述回油阀壳体设置在储油池的底部处,在储油池内的机油达到设定量时,阀片打开,进行回油。优选地,所述发动机油气分离器进一步包括旁通阀,所述旁通阀的入口与所述导流孔板的上游侧连通,所述旁通阀的出口与精分离后空腔连通,在所述旁通阀两端的压力差大于等于设定阈值时,所述旁通阀导通。优选地,所述第一分离组件包括至少两个第一分离组件挡板,所述第一分离组件挡板为人字挡板,需分离的油气流经所述第一分离组件挡板之间的挡板间隙,经过初次分离后被引导至所述第二分离组件进行再次分离。优选地,相邻第一分离组件挡板之间的挡板间隙在4mm至6mm的间隙内。本发明还提供一种发动机总成,所述发动机总成包括如上所述的发动机油气分离器。本发明还提供一种车辆,所述车辆包括如上所述的发动机油气分离器或如上所述的发动机总成。在本发明的发动机油气分离器中,分离板的成本与迷宫挡板相当,但是分离效果大大优于迷宫挡板,从而使得本发明的发动机油气分离器具有较低的成本与更高的分离效果。换言之,本发明提供了一种兼顾低成本、结构简单、加工制造简易、易布置而分离效果较好的油气分离器。附图说明图1是根据本发明一实施例的发动机油气分离器的示意图。图2a是图1所示发动机油气分离器的第一分离组件挡板的示意图。图2b是沿图2a中A-A线的示意性剖视图。图3是图1所示发动机油气分离器的高效油气分离模块的示意图。图4是图3所示发动机油气分离器的分离板的示意图。图5是图1所示发动机油气分离器的回油单向阀的示意性分解图。附图标记:1第一分离组件挡板21导流孔板2第二分离组件211导流孔3PRV阀总成22底座4回油单向阀23分离板5油气入口231基板6出气管232凸起7储油池41回油阀壳体11挡板间隙42阀片具体实施方式在附图中,使用相同或类似的标号表示相同或类似的元件或具有相同或类似功能的元件。下面结合附图对本发明的实施例进行详细说明。在本发明的描述中,术语“中心”、“纵向”、“横向”、“前”、“后”、“左”、“右”、“竖直”、“水平”、“顶”、“底”“内”、“外”等指示的方位或位置关系为基于附图所示的方位或位置关系,仅是为了便于描述本发明和简化描述,而不是指示或暗示所指的装置或元件必须具有特定的方位、以特定的方位构造和操作,因此不能理解为对本发明保护范围的限制。本发明的发动机油气分离器包括:为实现上述目的,本发明提供一种发动机油气分离器,所述发动机油气分离器包括:第一分离组件;以及第二分离组件,所述第二分离组件位于所述第一分离组件的下游,且包括分离板,所述分离板上设置有多个凸起,相邻凸起之间具有气流间隙。在本发明的发动机油气分离器中,分离板的成本与迷宫挡板相当,但是分离效果大大优于迷宫挡板,从而使得本发明的发动机油气分离器具有较低的成本与更高的分离效果。换言之,本发明提供了一种兼顾低成本、结构简单、加工制造简易、易布置而分离效果较好的油气分离器。图1是根据本发明一实施例的发动机油气分离器的示意图。该发动机油气分离器是一个高效油气分离器,通常设置在气门室罩盖内。油气走向如图1中的粗箭头所示。待分离的油气先油气入口5进入从气门室罩盖内,以及经过第一分离组件的第一分离组件挡板1、第二分离组件2之后,洁净气体通过PRV 总成阀3从出气管6排出,例如进入进入增压器压前管路。在第一分离组件和第二分离组件2的下游下方都设置有储油池和/或回油通路。分离出来的油液存储在储油池中,和/或通过回油通路排出。图1所示的发动机油气分离器包括:第一分离组件和第二分离组件2。第一分离组件包括至少两个第一分离组件挡板1。第一分离组件挡板1为人字挡板,需分离的油气流经第一分离组件挡板1之间的间隙,经过初次分离后被引导至第二分离组件2,进行再次分离。油雾气体在通过人字挡板时,由于挡板与挡板间隙小会形成气体加速,较大油点在加速过程中撞击挡板并附着、聚集、沉降。从而达到分离大油滴的作用。第一分离组件挡板1的数量根据油气分离器布置空间以及发动机漏气量进行设置。优选地,相邻第一分离组件挡板1之间的挡板间隙在4mm至6mm的间隙内,例如为5mm。通过设置该优选的挡板间隙,能够在保持较快油气通过效率的情况下,获得良好的初次分离效果。如前所述,在油气走向上,第二分离组件2位于所述第一分离组件的下游,对经过第一分离组件分离后的油气进行进一步分离。具体地,第二分离组件2包括导流孔板21、底座22和分离板23。导流孔板21和分离板23固定安装在底座22上。分离板23是第二分离组件2的核心构件。参见图4,分离板23包括基板231和凸起阵列,所述凸起阵列包括从基板231伸出的多个凸起232。具体地,如图所示,凸起232为锥状凸起。也就是说,凸起232从根端(与基板231连接的一端)向末端(远离基板231的一端)延伸,且在延伸方向上截面积逐渐变小。优选地,凸起232的横截面为方形或圆形。可以理解的是,凸起232的形状也可以根据需要而设置为其他形状。在一个备选的实施例中,凸起232的横截面为方形或菱形,其横截面的两条对角线分别为竖直设置与水平设置。从而,附着在凸起上部的油液可以顺着凸起232的表面流下。在另一备选实施例中,凸起232的横截面为等边三角形,其三角形横截面的底边水平设置,此种结构也有利于附着在凸起上部的油液顺着凸起232的表面。有利的是,凸起232是中心轴线垂直于基板231。从而结构更加简单,便于注塑成型。有利的是,分离板23以注塑方式一体成型。从而,坚固耐用,且成本较低。如图3所示,第二分离组件2进一步包括位于分离板23上游的导流孔板21。导流孔板21上设置有多个导流孔211。多个导流孔211的总导流面积小 于第二分离组件2的出气区域的导流面积。第二分离组件2依靠导流孔板21使得油气流加速而撞击分离板23,从而提高油气分离效果。也就是说,经粗分离后的混合气体通过导流孔板加速撞击在分离板23上,油滴凭借惯性撞击并附着至分离板23,依靠重力聚集沉降,达到分离的目的。优选地,导流孔211的位置对准分离板23的中心区域。在另一个优选实施例中,如图1所示,导流孔211或导流孔阵列的位置对准分离板23的中心偏上区域(例如上半部区域),且第二分离组件2的排气区域设置在分离板23的下方。这样能够进一步提高分离板23的分离效率。图1所示的结构在发动机油气分离器的油气入口5与出气管6之间具有较大的驱动压差时,是特别有利的。可以理解的是,导流孔板上的导流孔通常不超出分离板的范围。参见图1,发动机油气分离器进一步包括位于所述分离板23下方的储油池7,以及设置在储油池7的底部处的回油单向阀4。如图5所示,回油单向阀4包括回油阀壳体41和阀片42。回油阀壳体41设置在储油池7的底部处。在储油池7内的机油达到设定量时,阀片42打开,进行回油。通常是回油至缸盖油腔内。回油单向阀4能够防止未分离的油气进入精分离空腔、粗分离空腔,即储油池上方的空腔及与之连通的空腔。进一步而言,单向阀防止气门室罩盖外未分离的气体窜入气门室罩盖内。换句话说,经第二分离组件2分离后的机油储存在储油池7内。当储油池7内的机油聚集到一定深度时,挤压橡胶阀片42,使得阀片42打开,储油池7内的机油经过回油阀壳体41上的孔回流至发动机储油容腔,从而起到回油作用。有利的是,阀片42以橡胶制成。但是也可以设置弹簧等其他弹性件来实现阀片42的弹性开启或关闭。优选地,所述发动机油气分离器可以进一步包括旁通阀(未图示)。旁通阀的入口与导流孔板21的上游侧连通,所述旁通阀的出口与精分离后空腔连通,在所述旁通阀两端的压力差大于等于设定阈值时,所述旁通阀导通。所述旁通阀导通,从而越过第二分离组件2的分离板23直接进入精分离后空腔,与分离后的气体混合一同流出,进入增压器压前管路。从而能够有效避免下述情况:分离功能结构受损后油气无法通过,引起曲轴箱内压力升高,导致各密封面渗油。可以理解的是,由于本发明的发动机油气分离器具有高的可靠性,堵塞的可能性较小,从而可以省略上文的旁通阀。经过测试发现,注塑分离板能够达到的分离效率与滤纸效果接近,但是使用时间长而且分离效果不会因使用时间长短而发生下降。从而,本发明的发 动机油气分离器具有永久免维护,耐腐蚀且不会出现堵塞等问题,而且发动机漏气量越大效果越明显——漏气量越大,气体流速越快,越有利于撞击分离。本发明还提供一种发动机总成,所述发动机总成包括如上所述的发动机油气分离器。本发明还提供一种车辆,所述车辆包括如上所述的发动机油气分离器或如上所述的发动机总成。整体而言,本发明的发动机油气分离器具有下述优点:1、生产成本较低,结构简单,占据发动机空间小,易集成。2、油气分离粒子大小范围广(直径0.4um以上粒子均能分离)。3、可根据不同发动机,优化设置内部结构或简单增加单体结构,提升分离效率。4、集成有回油单向阀,从而防止未分离气体窜入分离后空腔内。最后需要指出的是:以上实施例仅用以说明本发明的技术方案,而非对其限制。本领域的普通技术人员应当理解:可以对前述各实施例所记载的技术方案进行修改,或者对其中部分技术特征进行等同替换;这些修改或者替换,并不使相应技术方案的本质脱离本发明各实施例技术方案的精神和范围。当前第1页1 2 3