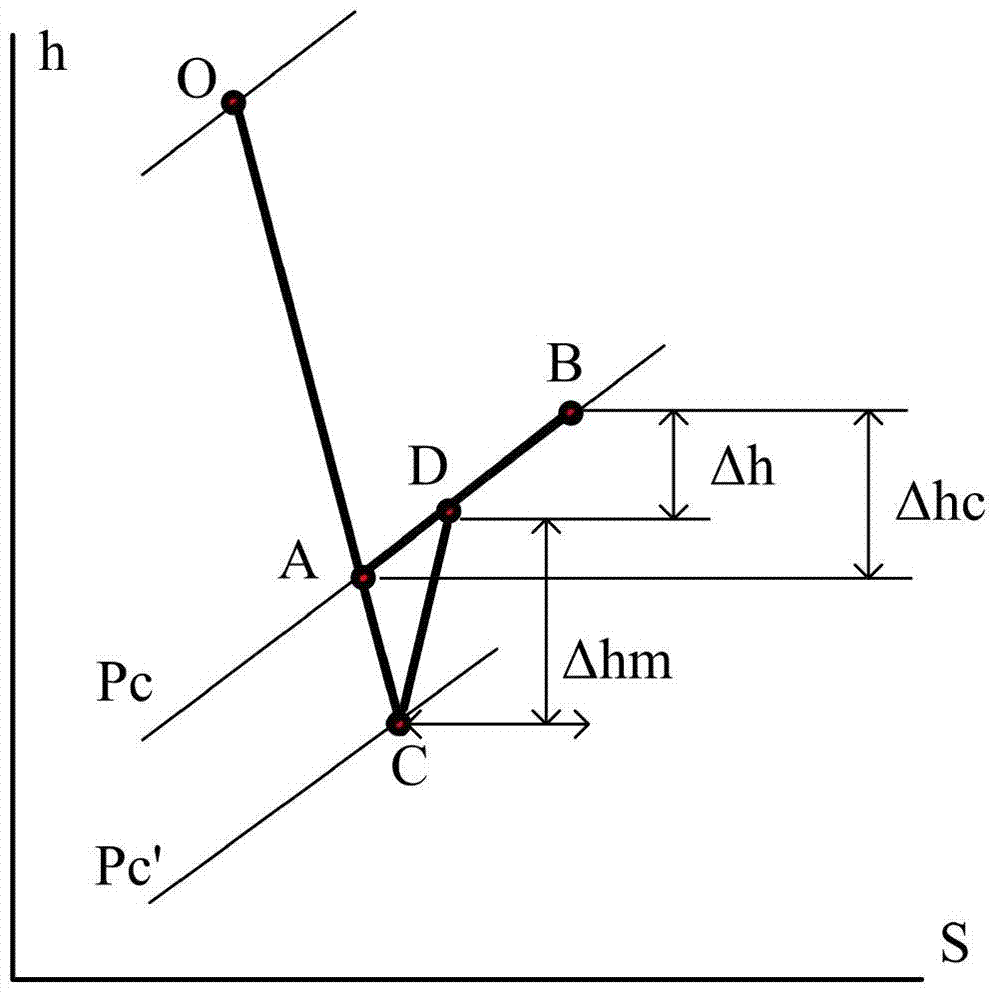
本发明属于汽轮机排汽余速损失利用技术领域,具体涉及一种利用汽轮机排汽余速损失的导流器。
背景技术:余速损失是汽轮机的主要能量损失,特别是现代大型汽轮机低压缸,由于离开末级动叶的蒸汽流速高达数百米,使其余速损失高达20kJ/kg以上,从而大大影响了低压缸相对内效率。传统的扩压通道虽然可利用高速蒸汽动能,但由于其扩张角很小,需要很长的通道才能取得效果,从而使汽轮机主轴长度大大增加,缺乏可行性。
技术实现要素:为了克服上述现有技术存在的问题,本发明的目的在于提供一种利用汽轮机排汽余速损失的导流器,通过特殊设计的结构可在较短的通道内获得显著的扩压效果,从而有效利用汽轮机的余速损失。计算表明,对现代大型火电机组,采用该技术可在不大幅度增加机组投资的前提下使汽轮发电机组的热耗率明显下降,具有显著的节能效益。为实现以上目的,本发明采用的技术方案为:一种利用汽轮机排汽余速损失的导流器,所述导流器1布置在汽轮机末级动叶2的下游,固定在汽轮机汽缸3上,所述导流器1由多个截面为S形的环形导流片5套接组成,相邻的环形导流片5沿径向通过多个截面为流线形的固定器6实现固定,相邻的环形导流片5之间形成导流通道4;所述导流通道4入口的方向与汽轮机末级叶片2后汽流速度的方向相同,出口的方向为水平方向;所述导流通道4从入口到出口采用渐扩通道。所述导流通道4出口截面积之和与其入口截面积之和的比值为1.5~2。所述固定器6的数量为4~8根。和现有技术相比较,本发明具备如下优点:1、本发明导流器采用在汽轮机的扩压段内增加若干个环形导流片,采用若干个环形导流片将扩压段分为多组子通道(称为导流通道),使相邻两个环形导流片之间的夹角减小;这样,每个导流通道的夹角较小,以解决大角度扩压段里边界层脱离所形成的漩涡问题,全部导流通道的等效夹角较大,以满足较大扩压的要求;从而,可在不显著增加汽轮机主轴长度的条件下利用扩压过程回收汽轮机末级排汽的余速损失,使汽轮机的热耗率明显下降,具有显著的节能效益,并且易于实施、投资远小于常规低压缸通流部分改造。2、除了用于汽轮机排汽余速损失回收之外,本发明也可用于燃气轮机排气余速损失回收、多级轴流式压缩机排气余速回收。本发明还可用于喷射装置,以减小扩压段长度,从而缩小喷射装置体积、实现喷射装置的紧凑化。附图说明图1为本发明导流器结构示意图,其中,图1a为导流器轴向剖面图,图1b为导流器径向剖面图。图2为采用扩压法回收余速损失的焓熵图(即h-s图)。图3为导流器的原理图,其中图3a为大角度扩压段,图3b为增加了导流片的扩压段,图3c为导流片光滑处理即S形的环形导流片的扩压段。具体实施方式为了使本发明的目的、技术方案及优点更加清楚简明,以下结合附图及实施例,对本发明进行进一步详细说明。应当理解,此处所描述的具体实施例仅仅用以解释本发明,并不用于限定本发明。如图1中图1a和图1b所示,本发明一种利用汽轮机排汽余速损失的导流器,所述导流器1布置在汽轮机末级动叶2的下游,固定在汽轮机汽缸3上,所述导流器1由多个截面为S形的环形导流片5套接组成,相邻的环形导流片5沿径向通过多个截面为流线形的固定器6实现固定,相邻的环形导流片5间形成导流通道4;所述导流通道4入口的方向与汽轮机末级叶片2后汽流速度的方向相同,出口的方向为水平方向;所述导流通道4从入口到出口采用渐扩通道。作为本发明的优选实施方式,所述导流通道4出口截面积之和与其入口截面积之和的比值为1.5~2,解决扩压通道长度过大问题。作为本发明的优选实施方式,所述固定器6的数量通常为4~8根。下面详细说明本发明的工作原理。为减小汽轮机排汽的余速损失,现代汽轮机排汽的切向速度很小,即离开末级动叶的蒸汽基本沿轴向运动,因此可采用扩压通道,通过降低排汽的轴向速度来提高排汽的压力。采用该措施以后,如汽轮机最终排汽压力不变,则离开末级动叶的排汽压力即可降低,从而增大蒸汽在汽轮机中的做功。图2给出了这一过程的h-s图,其中A为汽轮机末级动叶的原出口状态点,B为将排汽动能转化为蒸汽内能后汽轮机的原排汽状态点,A、B两点的焓差Δhc为原余速损失;C为采用排汽扩压后末级动叶的出口状态点,D为经过排汽扩压且将排汽动能转化为蒸汽内能后后排汽的状态点,C、D两点的焓差Δhm为采用排汽扩压后余速损失。假设改造前后离开汽轮机末级动叶的排汽速度相同,则Δhc=Δhm。由于扩压过程的不可逆损失小,因此D点位于B点之下,其焓差Δh即为所回收的余速损失之值。因此,采用排汽扩压后,汽轮机的排汽焓下降、蒸汽在汽轮机中的实际做功增加、相对内效率提高,其实质是利用排汽动能压缩排汽来降低余速损失。汽轮机排汽一般为亚音速,采用渐扩通道即可实现排汽的减速扩压。由于余速损失与排汽速度的平方成正比,而在体积流量一定的情况下排汽速度与其截面积成反比,因此较小的排汽截面增加即可明显地降低余速损失、获得显著的减速扩压效果。但蒸汽在扩压通道内流动时易出现边界层分离现象、使流动损失增大,因而传统的扩压通道需要取较小的扩张角(一般不超过8°)来保证扩压效果。对某600MW机组低压缸排汽采用传统扩压通道,则需要长约4米的扩压通道才能使截面积增加1倍,为此汽轮机主轴长度需要增加约8米,缺乏工程实用性。为了解决扩压通道长度过大问题,必须要采用大角度的扩压段,如图3a所示。为了解决大角度扩压段里边界层脱离所形成的漩涡问题,本发明提出在扩压段内增加若干个导流片,即采用若干个导流片将扩压段分为多组子通道,使相邻两个导流片之间的夹角减小,以满足扩压的要求,如图3b所示。为进一步减小流动损失,可对导流片进行光滑处理,从而得到如图3c所示的S形导流片。采用上述方法,在保证扩张角不变的情况下,采用1个导流片可使扩压通道长度减少为1/2,采用N组导流片可使扩压通道长度减少至1/(N+1),从而可大大减少扩压段的长度。以上述600MW为例,采用10片导流片即可使用于低压缸排气的扩压段长度降低至0.5m以下,整个机组主轴长度增加不超过1m,完全具有可行性。如原排汽速度为200m/s(对应的余速损失为20kJ/kg),则排汽速度减少至100m/s,相应的余速损失为5kJ/kg;设扩压段效率为80%,则低压缸排汽焓值可降低12kJ/kg,低压缸效率提高约3%。该技术亦可用于高压缸及中压缸排汽余速回收,对600MW汽轮机进行初步计算,可使汽轮发电机组的热耗率下降1%、煤耗率下3g/(kW·h)左右,具有显著的节能效益。