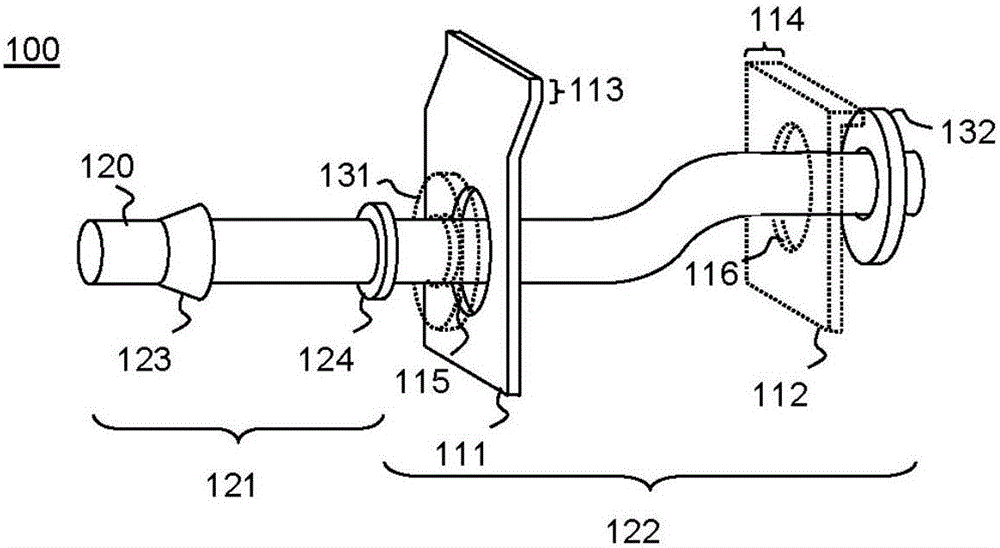
本发明涉及一种用于排气系统的可调节的安装架。
背景技术:
排气系统(也称为排气)由部件排气管和排气箱(也称为排气室)组成。排气管包括,例如,歧管、Y型管、连接管和尾管,也可以设置多个排气管。排气箱包括,例如,消声器和催化转化器,也可以设置多个排气箱。
排气系统通常安装在车辆的车身底部。该安装必须补偿排气系统由于在不同温度下的温度膨胀而产生的任何长度变化。该安装还必须以一种方式实现:当暴露至车辆的震动和冲击时,排气系统将相对于汽车的车身底部保持静止。
排气系统通常通过使用设置在车辆的车身底部的多个悬挂点安装到车辆的车身底部,O形环附接在所述悬挂点上。设置在排气系统上的对应的悬挂点被插入O形环。排气系统在车辆的车身底部上的这种类型的安装相当明显地具有相当的间隙,该间隙允许排气系统相对于车辆移动。传统上,悬挂点的形式为简单的挂钩。
现今的车辆往往有盖,排气系统的至少一个尾管穿过该盖。因此,在现今的车辆中,从使用安装在挂钩中的O形环导致的间隙往往是再也不能接受了。
已知用具有其中形成有两个或更多开口的实心体的排气系统用橡胶配件替代简单的O形环。开口通常穿透体部,其方式使开口的孔法线(垂直于由开口所限定的孔所在的平面的法线)平行。各排气系统用橡胶配件通常由橡胶、硅胶或氟橡胶制成。排气系统用橡胶配件的体部常常具有椭圆形、菱形、矩形或甚至三叶草形轮廓和(除了开口和边缘的圆角)恒定厚度。
当使用排气系统用橡胶配件时,有倒钩的安装心轴往往形成悬挂点,并且固定到车辆的车身底部并固定到排气系统的安装心轴成对地穿过相同排气系统用橡胶配件的不同的开口中。排气系统用橡胶配件的开口通常为圆形、椭圆形或拱形。
当减小排气系统和车辆的车身底部之间存在的间隙时,悬挂点在车辆的车身底部和排气系统的部件上的布置和取向的精度变得更为重要。
技术实现要素:
因此,本发明的目的是提供用于排气系统的安装架(以及因此悬挂点),其配置成不费力气且安全地固定到排气系统的部件或车辆的车身底部,并且其允许以简单方式调节其布置和取向。安装架还应该可以低成本且通用地生产。
用于排气系统的安装架的实施例包括支承件和由支承件支承的安装心轴。支承件包括第一板和与第一板隔开的第二板。板在此理解为广泛的平板状固体体部,其高度(厚度)的量为固体体部的其它尺寸(长度和宽度)的不超过30%或不超过20%或不超过10%。第一和第二板各自可以是厚度为0.2mm和3mm之间或0.5mm和3mm之间的薄金属板,或者厚度为大于3mm且小于5mm的厚板。第一和第二板各自包括用于将支承段固定在排气系统的部件上或车辆的车身底部的固定段。这种固定段可以,例如,通过弯曲相应的板而整体地形成。所述支承件可以通过固定段永久地附接到排气系统的部件(例如排气管或排气箱)或连接到车辆的车身底部。支承件在排气系统的部件或车辆的车身底部上的这种永久附接可以,例如,通过将支承件的第一和第二板的固定段焊接到排气系统的部件上或车辆的车身底部上。第一板和第二板各包括一个开口。这些开口可以具有相同或不同的横截面。沿其最大延伸的方向,安装心轴包括配置成用于贯穿排气系统用橡胶配件的第一段。安装心轴还包括与第一段不同的第二段,并且安装心轴在第二段穿过支承件的第一和第二板中的开口。安装心轴的第二段可以,例如,直接邻近安装心轴的第一段。因此,支承件的第一和第二板中的开口的直径比安装心轴的穿过相应开口的区域的直径大至少10%。可替代地,支承件的第一和第二板中的开口的直径比安装心轴的穿过相应开口的区域的直径大至少20%。还可替代地,支承件的第一和第二板中的开口的直径比安装心轴的穿过相应开口的区域的直径大至少30%。
由于在安装心轴和支承件的板中的开口之间存在相当大的间隙,安装心轴的第一段可以被精确地对准,甚至在使支承件的板固定到排气系统的部件或车身底部之后。这是基于这样的想法:首先仅支承件永久固定到受制造公差影响的排气系统的部件上或受制造公差影响的车辆的车身底部,并且安装心轴最初松动地插入支承件。然后在将支承件的板固定到排气系统的部件上或车辆的车身底部之后完成安装心轴的精确对准。这样,制造公差可以很容易地补偿制造公差。
所述支承件的第一板和第二板的固定段可相同或不同地形成。固定段可以通过折叠或凹口进一步与板的其它段分离;但是,这不是必要的。
根据一个实施例,支承件的第一板和第二板中的开口的直径比安装心轴的穿过相应开口的区域的直径大不超过150%。根据一个替代实施例,支承件的第一板和第二板中的开口的直径比安装心轴的穿过相应开口的区域的直径大不超过90%。根据一个替代实施例,支承件的第一板和第二板中的开口的直径比安装心轴的穿过相应开口的区域的直径大不超过80%。这样,确保了安装心轴被接收在支承件的板的开口中是安全固定的,尽管有间隙。
因此,支承件的第一和第二板中的开口的直径(在下面的概述中表示为“DO”)与安装心轴的穿过相应开口的区域的直径(在下面的概述中表示为“DD”)的下列依附关系是可能的。
DD+10%DD≤DO≤DD+150%DD,DD+10%DD≤DO≤DD+90%DD,
DD+10%DD≤DO≤DD+80%DD,DD+20%DD≤DO≤DD+150%DD,
DD+20%DD≤DO≤DD+90%DD,DD+20%DD≤DO≤DD+80%DD,
DD+30%DD≤DO≤DD+150%DD,DD+30%DD≤DO≤DD+90%DD,
DD+30%DD≤DO≤DD+80%DD
根据一个实施例,安装心轴在支承件的第一和第二板中的开口的区域中焊接到支承件的第一板和第二板。焊接仅在将支承件的板固定到排气系统的部件或车辆的车身底部之后,并且在对准安装心轴的第一段之后进行。通过焊接,安装心轴可以永久保持在相对于排气系统的部件或车辆的车身底部的正确位置。
根据一个替代实施例,安装心轴在第二段中包括两个间隔开的金属盘。这些金属盘的每一个都在安装心轴的圆周方向上完全包围安装心轴。根据一个实施例,金属盘因此定位在安装心轴上,使得支承件的第一板和第二板两者位于两个金属盘之间。根据另一实施例,金属盘因此定位在安装心轴上,使得支承件的第一板和第二板中的每一个都位于直接邻近两个金属盘中的一个。金属盘便于安装心轴在支承件的板上的安全固定,因为安装心轴的固定可以通过金属盘来间接地完成。由于金属盘在圆周方向上围绕安装心轴,金属盘具有比安装心轴更大的直径。金属盘可以,例如,直径比支承件的第一和第二板中的开口的直径大。
此外,比另一金属盘更接近安装心轴的第一段的金属盘可以与安装心轴整体地形成。这样,所使用的零件的数目保持很低,因为除了支承件和安装心轴之外必要的只是一个金属盘。
在金属盘之一不与安装心轴整体成形的情况下,该金属盘可具有安装心轴贯穿其中的一个穿孔。金属盘中的穿孔的直径可以是,例如,比安装心轴在第二段中的直径稍大。金属盘可以由此,通过间隙,松动地放在安装心轴上。根据一个实施例,金属盘中的穿孔的直径可以是,例如,比安装心轴在第二段的直径大0.1%至5%之间或0.5%至2%之间。
替代地,穿孔的金属盘可通过摩擦连接被连结到所述安装心轴;穿孔金属盘可因此,例如,是一个夹紧垫圈。
一旦安装心轴已经通过穿孔,穿孔金属盘可通过焊接/熔焊进一步连结到安装心轴。
一旦安装心轴已经通过穿孔,穿孔金属盘可替代地通过钎焊进一步连结到安装心轴。
一旦安装心轴已经通过穿孔,穿孔金属盘可替代地通过粘接进一步连结到安装心轴。
根据一个实施例,金属盘的每一个都焊接到支承件的第一板和第二板中最邻近该金属盘的一个。焊接仅在支承件的板固定到排气系统的部件或车辆的车身底部之后、在将安装心轴穿过板中的开口之后、和对准安装心轴的第一段之后进行。
根据一个实施例,支承件的第一板和第二板中的开口的孔法线被分隔开。支承体的第一和第二板中的开口的孔法线可以平行隔开或相对于彼此偏斜,或相交成一角度。安装心轴可以由此在第一段中直线延伸和在第二段中S形延伸。安装心轴的S形形式的曲率可以,例如,完全定位在支承件的板之间。安装心轴的S形形式便于使安装心轴安全的对准且附接到支承件的板上,尽管安装心轴和支承件的板之间有大的间隙。
根据一个实施例,支承件的第一和第二板是平行的。根据一个替代实施例,支承件的第一和第二板处于限定了小于20°的角度或小于10°的角度或小于5°的角度的平面中。这样,确保了支承件的第一和第二板的开口的孔法线沿相同方向基本对齐。
根据一个实施例,安装心轴和支承件的第一板和第二板中的开口具有圆形的横截面。根据一个替代实施例,安装心轴和支承件的第一板和第二板中的开口具有椭圆形的横截面。根据又一替代实施例,安装心轴和支承件的第一板和第二板中的开口具有三角形横截面。根据又一替代实施例,安装心轴和支承件的第一板和第二板中的开口具有四边形横截面。根据又一替代实施例,安装心轴和支承件的第一板和第二板中的开口具有多边形横截面。安装心轴的横截面的形状因此可以对应于支承件的第一板和第二板中的开口的横截面的形状。当使用非圆形的横截面时,可以防止安装心轴相对于板的极端扭转,只要安装心轴的最大直径比支承件的第一和第二板的开口的最小直径小。
根据一个实施例,安装心轴在第一段包括两个间隔开的突出部。因此,位于与另一突出部相比距离安装心轴的第二段较远的突出部包括突出部的一侧上的背离安装心轴的第二段的斜坡/斜面。该斜面便于心轴插入到排气系统用橡胶配件的开口中,同时使能够防止安装心轴从排气系统用橡胶配件的开口脱开。
根据一个实施例,所述支承件的第一板和第二板之间的距离大于30mm或大于60mm或大于90mm。根据一个实施例,支承件的第一板和第二板之间的距离小于200mm或小于150mm或小于100mm。因此,对于距离(在下面的概述中表示为“AB”,)以下尺寸是可能的:
30mm<AB<200mm,30mm<AB<150mm,30mm<AB<100mm,
60mm<AB<200mm,60mm<AB<150mm,60mm<AB<100mm,
90mm<AB<200mm,90mm<AB<150mm,90mm<AB<100mm
根据一个实施例,承载件是由片材整体地形成,并且一连接段与支承件的第一板和第二板互连。支承件可以随后通过单一钣金件的深度拉伸或折弯制成。通过形成整体的支承件,所用零件的数量进一步减少。
根据一个实施例,所述支承件的第一板的固定段平行于所述第一板对齐,由此,所述第一板比支承件的第二板更靠近安装心轴的第一段。从而,固定段可以,例如,被连结成S形。支承件的第二板的固定段还与所述第二板限定一超过60°的角度或超过80°的角度或超过90°的角度,由此,第二板比支承件的第一板距离安装心轴的第一段更远。支承件的第一板和第二板的固定段因此具有不同的取向。这样,支承件的第一板的固定段可以,例如,被固定在排气箱的前表面上,而支承件的第二板的固定段被固定到相同的排气箱的侧表面上。从而安全地保持排气箱。
根据一个实施例,支承件的第一板的固定段与第一板的开口相距比支承件的第二板的固定段与第二板的开口相距更远至少两倍,因此所述第一板的位置比支承件的第二板更接近安装心轴的第一段。通过这样的不同尺寸,支承件非常适合用于吸收转矩。
根据一个实施例,支承件和安装心轴由金属或不锈钢制成。另外,金属盘可以由不锈钢制成。
根据一个实施例,第一和第二板被相同地形成。根据一个替代实施例,第一板和第二板仅在开口的位置处不同。
用于安装排气系统用安装架的方法的实施例包括以下步骤:将支承件的第一板的第一固定段焊接到排气系统的部件上或车辆的车身底部。将支承件的第二板的第二固定段焊接到排气系统的部件上或车辆的车身底部,使得第一和第二板两者分隔开,并且使得第一和第二板两者平行或处于限定一小于20°的角度的平面中。将承载第一金属盘的安装心轴的第二段放置在支承件的板中形成的开口中,使得第一金属盘定位于支承件的两个板的外侧,其中安装心轴包括构造成贯穿排气系统用橡胶配件的第一段,以及其中支承件的板中的开口的直径比安装心轴的穿过各开口的区域的直径大至少10%。将具有中心通道的第二金属盘放置到安装心轴上,使得所述支承件的两个板位于第一和第二金属盘之间,其中每个金属板邻接支承件的相应的板。将所述安装心轴的第一段相对于所述排气系统的部件或车辆的车身底部对准。以及,将金属盘焊接到相应的板和所述安装心轴上。
在这方面,应注意的是,用于列举特征的术语“包括”、“包含”、“含有”、“具有”和“带有”,及其在本说明书或权利要求中使用的语法变型通常被认为用于指定特征的非穷举性列举,如方法步骤、部件、范围、尺寸等,不以任何形式排除一个或多个其它特征或其它或附加特征组的存在或增加。
附图说明
本发明的更多特征将从示例性实施例的以下描述以及权利要求和附图中显而易见。在附图中,相同或相似的元件被分配相同或相似的附图标记。应该注意的是,本发明并不限于本文所描述的示例性实施例的配置,而是由附带的权利要求的范围限定。根据本发明的实施方式可尤其实施于与下面描述的示例不同的数量和组合中的单独特征。在示例性实施例的以下描述中,参照所附的附图,在附图中
图1A示出了根据第一实施方式的安装架安装到消声器的示意性透视图;
图1B示出了图1A的安装架在安装到消声器之前的示意图,其中以虚线绘制的部件透明地示出;
图1C示出了图1A的安装架正在安装到消声器上的示意图;
图1D示出了图1B的安装架的剖面的示意图,额外示出了排气系统的橡胶;
图2A示出了根据第二实施例的安装架的示意性透视图,其中以虚线绘制的部件透明地示出;
图2B示出了图2A的安装架的支承件,其处于展开成一个平面的状态;
图3A示出了根据第三实施例的安装架的示意性透视图;
图3B以侧视图示出了图3A的安装架的示意图;和
图3C以另一侧视图示出了图3A的安装架的示意图。
具体实施方式
参考图1A至1D,下面描述用于排气系统的可调节安装架的第一实施方式。图1A在此示出了处于完全安装状态下的安装架,图1B示出了处于未安装状态的安装架的部件,图1C示出了安装架处于仅第一和第二板被固定到排气系统的部件的状态,以及图1D示出了通过根据图1A的已安装的安装架的剖面,尽管排气系统的部件未示出,并附加示出了通过排气系统用橡胶配件的剖面。在附图中,用虚线示出了透明地呈现的部件。
如图1B和1D中特别明显的,安装架100包括具有圆形横截面的安装心轴120。在所示的实施例中,安装心轴120由实心钢制成。
安装心轴120包括第一段121,安装心轴沿其直线延伸,并在其内形成具有倾斜截面的第一突出部123和矩形截面的第二突出部124。这两个第一和第二突出部123和124被分隔开,使得由安装心轴120贯穿的排气系统用橡胶配件300可设置在它们之间。第一突出部123的倾斜截面因此便于安装心轴120插入排气系统用橡胶配件300的开口内。排气系统用橡胶配件300中的开口在图1D中是不可见的,因为排气系统用橡胶配件300由于其弹性而紧紧环抱安装心轴120。第一和第二突出部123和124防止安装心轴相对于排气系统用橡胶配件300的过多相对运动。在示出的实施例中,第一和第二突出部123和124与安装心轴120形成为一体。
位于在安装心轴的长度方向上邻近第一段121的第二段122中,安装心轴120具有S形的特征和恒定的横截面;在第二段122中,安装心轴120因而不具有突出部。
安装架100还包括支承件110,由第一板111和第二板112形成。在所示的实施例中,第一和第二板111、112两者都由材料厚度为3mm的薄钢板制成。第一板111的横截面总的来说是S形。支承件110的第一板111的第一固定段113平行地延伸到第一板111的其中形成有开口115的部段。第二板112具有成角度的固定段114,该固定段相对于第二板112的其中形成有开口116的部段成90°的角度α。第二板112的固定段114也与第一板111的固定段113成直角。固定段113、114用于使支承件110的第一和第二板111、112紧固到排气系统的部件上,如图1A和1C所示。
如图1A和1C中可见,第一板111的固定段113通过焊缝141紧固到排气箱200的前表面上,而第二板112的固定段114通过焊缝141紧固到排气箱200的侧表面上。通过第一和第二板111、112被固定到排气箱200,支承件的第一和第二板111、112平行地布置。
可替代固定到排气系统的部件的是,支承件110的固定段113、114也可以固定到车辆的车身底部。然而,这没有在图中示出。在示出的实施例中,第一和第二板还不同地形成。但是,本发明并不限于此,因此,第一和第二板可替代地也可以相同地形成。第一和第二板可以是,例如,可替代地也都具有倾斜的固定段。
支承件110的第一和第二板111、112的每一个都具有完全穿过相应的板的开口115、116。在图1A和图1D中所示的安装架100的安装状态下,所述安装心轴120贯穿支承件110的第一和第二板111、112的开口115、116。在第一板111中形成的开口115的直径D115比安装心轴120穿过第一板111的区域的9.6mm的直径D120大18mm、因此大87%。并且,支承件110的第二板112中的开口116的直径D116比安装心轴120穿过第二板112的区域的9.6mm的直径D120大18mm、因此大87%。当安装心轴120穿过支承件110的第一和第二板111、112的开口115和116时,安装心轴120因而通过支承件110的板111、112有间隙地支承。因此,安装心轴120可以在开口115、116的纵向(并因此沿安装心轴120的纵向)对齐,但是也在横向于开口115、116的方向(以及因此在垂直于安装心轴120的纵向的方向上)对齐。安装心轴120也可以是倾斜的。如图1A和图1D可见,支承件110的第一和第二板111、112的开口115和116的孔法线是平行的。第一和第二板111、112的开口115、116的中心没有沿着共同的孔法线定位,使得开口115、116偏移地定位。
安装架100还包括第一金属盘131和第二金属盘132。在此实施例中,第一和第二金属盘131和132各自包括比安装心轴120的直径D120稍大的开口并代表独立于安装心轴120的部件。如图1B、1C和1D所示,安装心轴120穿过第一和第二金属盘131、132,使得支承110的第一和第二板111、112位于第一和第二金属盘131、132之间。在所示的实施例中,两个金属盘131和132的各自的直径都比支承件110的第一和第二板111、112的开口115、116的直径D115、D116大25mm。
当第一和第二板例如紧固在排气箱200上时,为了使安装心轴120相对于支承件110的第一和第二板111、112限定在其取向和位置上,第一和第二金属板131、132在安装心轴已经对齐之后邻接第一和第二板111、112,并借助于焊缝焊接到第一和第二板111、112。此后,安装心轴120通过环形焊缝被焊接到第一和第二金属盘131、132上。结果,安装心轴120的位置和取向相对于第一和第二板111、112永久地固定。可替代地,安装心轴120可以首先焊接到第一和第二金属盘131、132,第一和第二金属盘随后被焊接到支承件110的第一和第二板111、112上。
参考图2A和2B,下面将描述根据本发明的用于排气系统的安装架100的第二实施方式。
图2A的示意性透视图在此示出了处于未安装状态的安装架,而图2B示出了图2A中使用的安装架的支承件,其中安装架处于支承件展开成一个平面的状态。为了避免重复,仅说明与上述第一实施方式的不同之处,而其余部分参考第一实施方式的说明。
根据第二实施方式的安装架100与上面所描述的根据第一实施方式的安装架100的不同之处在于,第一金属盘131不是松动地放置在安装心轴120上,而是与安装心轴120一体地形成。这减少了所使用的零件的数量。
第二实施方式与上述第一实施方式的不同之处还在于,第二金属盘132并不松散地沿着安装心轴120移动,而是构造成夹紧垫圈,因而通过摩擦连接附接到安装心轴。为了实现这一点,第二金属盘132中的开口的直径比安装心轴120的直径D120略小。在所述开口附近,第二金属盘132具有弹性。
第二实施方式与上述第一实施方式的不同之处还在于,根据第二实施方式的支承件110整体地形成。这在图2B中最佳地可见。连接段117与支承件110的第一和第二板111、112互连。这允许支承件110通过折弯一片金属板(或薄板)而制成。折弯边缘在图2B中示出为虚线。
参考图2B,支承件110的第一板111的固定段113与第一板111中的开口115分隔一距离A113。在第二实施例中,该距离A113与上述第一实施方式中相似,显著大于支承件110的第二板112的固定段114与支承件110的第二板112中的开口116之间的距离A114。这允许将固定段113、114中的一个固定到排气箱200的正表面而另一个固定到排气箱的侧表面上,如图1A和1C所示。在图2B中,固定段113和第一板111中的开口115之间的距离A113是固定段114和第二板112中的开口116之间的距离A114的四倍。
执行根据第一和第二实施方式的安装架的安装,如下所述。
首先,支承件110的第一和第二板111、112的固定段113、114被固定到排气系统200的部件上或车辆的车身底部(未示出)。这可以例如通过焊接或粘接或钎焊来实现。实现的方式是,其中第一和第二板111、112并行或处于限定小于20°的角的平面中。接着,如果相应的第一金属盘131尚未与所述安装心轴120整体地形成,则第一金属盘131被滑动到安装心轴120上。然后,承载第一金属盘131的安装心轴120通过支承件110的第一和第二板111、112中的开口115、116插入。然后,第二金属盘132被滑动到安装心轴120上,由此第二金属盘132沿圆周方向围绕所述安装心轴120,第一和第二板111、112被定位在第一和第二金属盘131、132之间。然后,安装心轴120的位置和取向按照悬挂排气系统的要求被对准。在此之后,第一和第二金属盘131、132与相应的第一和第二板111、112抵接并环状地焊接到相邻的第一和第二板111、112和安装心轴120。
参考图3A至3C,下面说明用于排气系统的可调节的安装架的第三实施例。
因此,图3A示出了处于完全安装的状态下的安装架100的透视图,图3B示出安装架100的侧视图,其中安装架100被对准,使得安装架100的第一板111处于投影平面中,以及图3C是安装架100的另一侧视图,其中安装架100被对准,使得安装架100的第一板111和第二板112垂直于投影平面。为了便于更好地理解本发明,所选择的元件在图3B和3C中用阴影表示。如上述第一和第二实施例中,为相同的元件使用相同的阴影。此外,第一和第二板111、112中的开口115、116已用虚线标记。
如在图3A和3C中最佳可见,安装架100包括具有圆形横截面的直螺栓形式的安装心轴120。不同于上述第一和第二实施例,在第三实施例中,安装心轴120的构造成用于穿过排气系统用橡胶配件(未示出)的第一段121不位于安装架100的支承件110的邻侧,而是处于支承件110的内部。为此目的,安装心轴120包括两个分隔开的部段122',安装心轴120在该部段穿过支承件110的两个对称地形成的、平行的第一和第二板111、112。至此,支承件的第一和第二板111、112各自包括安装心轴120穿过其中的开口115、116。安装心轴120的第一段121因此位于该安装心轴120的两个第二段122'之间。可替代穿过排气系统的排气系统用橡胶配件的是,安装心轴120的第一段121也可以接合一钩状件,该钩状件通过容限元件(例如弹簧)联接到车辆的车身底部。
如第二实施方式,形成第三实施方式的支承件110的第一和第二板111、112构造成一个整体,并通过连接段117相互连接。
在第三实施方式中,第一和第二板111、112分别具有沿第一和第二板111、112的弯曲的外边缘延伸的固定段113。在图3A、3B和3C中,仅第一板111的固定段113可见,因为第二板112的固定段被第一板111隐藏。固定段的曲率适于容纳排气转换器(未示出)。
如在第一和第二实施方式中,支承件110的第一和第二板111、112中的开口115、116分别具有相同尺寸的直径D115,该直径比安装心轴120穿过第一板111和第二板112的区域的直径D120大至少10%。当安装心轴120穿过支承件110的第一和第二板111、112的开口115和116时,支承件110的板111、112从而有间隙地支承安装心轴120。因此,安装心轴120可以在横向于开口115、116的方向(以及因此在垂直于安装心轴120的纵向的方向)对齐。第一和第二板111、112的开口115、116的中心显然沿着共同的孔法线布置,使得开口115、116彼此对齐。
如在第一和第二实施方式中,以及在第三实施方式中,安装架100包括第一金属盘131和第二金属盘132。以及在第三实施例中,各金属盘131和132都具有一开口,其直径比安装心轴120的直径D120稍大并且构成独立于安装心轴120的部件。如图3A和3C所示,安装心轴120穿过第一和第二金属盘131、132,使得支承件110的第一板和第二板131、132位于第一和第二金属盘131、132之间。在所示实施例中,两个金属盘各自的直径比支承件110的第一和第二板111、112中的开口115、116的直径D115大。
为了在第一和第二板111、112例如固定到排气箱200时限定安装心轴120相对于支承件100的第一和第二板111、112的取向和位置,在安装心轴120已经对齐之后,第一和第二金属板131、132邻接相应的邻近的第一和第二板111、112,然后通过环形焊缝143焊接到第一和第二板111、112。然后,安装心轴120通过环形焊缝142焊接到第一和第二金属盘131、132。这导致安装心轴120被永久地限定相对于第一和第二板111、112的位置和取向。可替代地,安装心轴120也可以首先被焊接到第一和第二金属盘131、132,然后第一和第二金属盘131、132被焊接到支承件110的第一和第二板111、112。
根据第三实施方式的安装架100特别适合于安装排气系统的重质部件,例如重型货车所使用的那些部件。
虽然本发明的上述实施例仅通过示例进行了说明,但显然对本领域技术人员显而易见的是,可以作出许多修改、增加和替换而不脱离在下面公开的本发明的范围和要旨。
附图标记列表
100 用于排气系统的安装架
110 支承
111 支承的第一板
112 支承的第二板
113 支承的第一板的固定部
A113 第一板中固定部和开口之间的距离
114 支承的第二板的固定部
A114 第二板中固定部和开口之间的距离
α 由第二板的固定部限定的角
115 支承的第一板中的开口
D115 支承的第一板中的开口的直径
116 支承的第二板中的开口
D116 支承的第二板中的开口的直径
117 连接段
120 安装心轴
D120 安装心轴的直径
121 安装心轴的第一段
122 安装心轴的第二段
122' 安装心轴的第二段
123 安装心轴的第一突出部
124 安装心轴的第二突出部
131 第一金属盘
132 第二金属盘
141 支承与排气系统的部件之间的焊缝
142 安装心轴与金属盘之间的焊缝
143 金属盘与支承的板之间的焊缝
200 排气系统的部件
300 排气系统用橡胶配件