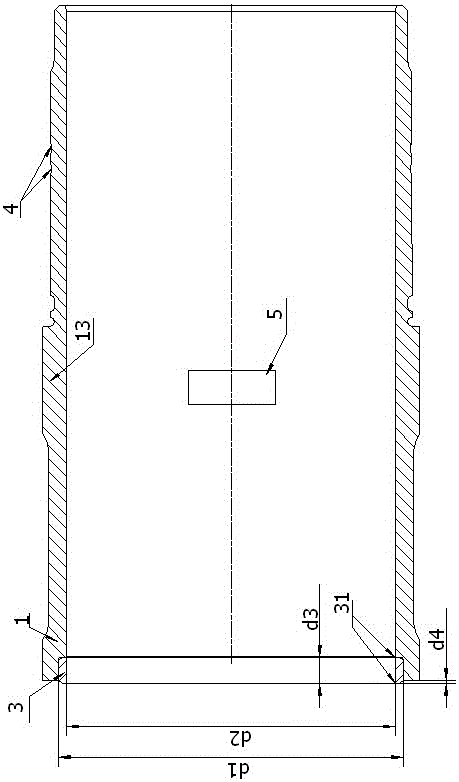
本实用新型涉及汽车发动机领域,具体涉及一种环保型发动机气缸套。
背景技术:气缸套是一个圆筒形零件,置于机体的气缸体孔中,上由气缸盖压紧固定。活塞在其内孔作往复运动,其外有冷却水冷却。气缸套的功用有:1.与缸盖、活塞共同构成气缸工作空间。2.筒形活塞柴油机的气缸套承受活塞侧推力,成为活塞往复运动的导程。3.将活塞组件及本身的热量传给冷却水,使之工作温度适当。4.二冲程柴油机的气缸套布置有气口,由活塞启闭,实现配气。气缸套内表受高温高压燃气直接作用,并始终与活塞环及活塞裙部发生高速滑动摩擦。外表与冷却水接触,在较大温差下产生严重热应力,受冷却水腐蚀。活塞对缸套的侧推力不仅加剧其内表摩擦,并使其产生弯曲。侧推力改变方向时,活塞还撞击缸套。此外还受到较大的安装预紧力。气体压力使气缸壁产生切向拉应力和径向压应力,并且在内表面最大,这种应力都是高频脉动应力。因缸壁内外温差产生极大的热应力,一般温度下使内表面产生压应力而冷却面存在拉应力。但在特高气温下,近内表面金属蠕变塑性变形,而冷却后即在内表面形成残余拉应力,这种随起动、停车变化引起的低频应力会使材料疲劳。现有的气缸套存在着燃油燃烧不充分,造成积碳较多,积碳会引起磨粒磨损,影响内燃机的使用寿命。
技术实现要素:本实用新型为了解决现有技术中的不足之处,提供一种环保型发动机气缸套,能够使燃油燃烧充分,减少积碳及减少由于积碳引起的磨粒磨损,延长了内燃机的使用寿命。为解决上述技术问题,本实用新型采用如下技术方案:一种环保型发动机气缸套,包括气缸套本体,所述气缸套本体的支撑肩内孔部位装配有抗磨环,抗磨环外圆与所述气缸套本体呈间隙配合;抗磨环的上端面高出支撑肩上端面并形成气缸套凸台,抗磨环的上端面与缸盖端面相配合;抗磨环高出支撑肩上端面的外圆部位与气缸垫内孔配合;抗磨环的内孔设置有网纹,该网纹的纹理呈螺旋纹状。所述抗磨环的内孔的上下两端均设置有倒角。所述抗磨环的内孔的上下两端的倒角相同,且均为锐角。所述抗磨环的上端面高出支撑肩上端面1.12mm~1.30mm;抗磨环的外圆直径为119mm~119.25mm;抗磨环的高度为8.5mm~10mm;抗磨环内孔直径为113mm~113.8mm,抗磨环内孔直径比所述气缸套本体内孔直径小0.2mm~1mm。所述抗磨环由灰铸铁材料制成。所述气缸套本体的裙部外圆处加工有标识槽。本实用新型的有益效果是:本实用新型的环保型发动机气缸套由装配在支撑肩内孔部位的抗磨环和与之配合的气缸套本体组合而成装配在支撑肩内孔部位的抗磨环和与之配合的气缸套本体组合,抗磨环外圆与气缸套本体呈小间隙配合,能够使燃油燃烧充分,减少积碳及减少由于积碳引起的磨粒磨损,延长了内燃机的使用寿命。抗磨环的上面高出气缸套支撑肩上面1.12mm至1.30mm,代替气缸套的凸台,端面与缸盖端面配合;抗磨环的外圆直径为119mm至119.25mm,使外圆与气缸垫内孔配合;抗磨环的高度为8.5mm至10mm;抗磨环内孔直径为113mm-113.8mm,比气缸套内孔直径小0.2mm至1mm;抗磨环的内孔倒角部位要求保留锐角;抗磨环的材料选用普通灰铸铁材料;抗磨环的内外表面由数控车一次上车加工而成,既保证了内外圆的同轴度又保证内孔纹理呈螺旋纹状。气缸套内孔网纹为:Rpk<0.25um,Rk<0.5um,Rvk:1.5-2.5um,Rvk/Rk>2。抗磨环内孔网纹采用细平台珩磨网纹,沟槽多而浅,既能够保证内孔润滑需要又能避免多余润滑油参与燃烧,降低氮氧化合物的排放。由于在气缸套支撑肩内部装配的抗磨环内孔比缸套内孔直径小,能够阻碍活塞环上行时多余的润滑油参与燃烧,又能够阻碍高温燃气下行使润滑油恶化变质。当抗磨环槽内壁的积碳达到一定厚度时,能够利用活塞头部上行时把多余积碳吹出气缸套,能够有效避免磨粒磨损,提高气缸套使用寿命。附图说明图1是本实用新型实施例一的结构示意图;图2是图1中B—B剖面示意图;图3是本实用新型实施例二的结构示意图;图4是图1中A—A剖面示意图。具体实施方式实施例一:如图1至图2所示,本实用新型的一种环保型发动机气缸套,包括气缸套本体1,所述气缸套本体1的支撑肩13内孔部位装配有抗磨环3,抗磨环3外圆与气缸套本体1呈间隙配合;抗磨环3的上端面高出支撑肩13上端面并形成气缸套凸台,抗磨环3的上端面与缸盖端面相配合;抗磨环3高出支撑肩13上端面的外圆部位与气缸垫内孔配合;抗磨环3的内孔设置有网纹,该网纹的纹理呈螺旋纹状。所述抗磨环3的内孔的上下两端均设置有倒角31,上下两端的倒角31相同,且均为锐角。所述抗磨环3的上端面高出支撑肩13上端面的距离d4为1.12mm~1.30mm;抗磨环3的外圆直径d1为119mm~119.25mm;抗磨环3的高度d3为8.5mm~10mm;抗磨环3内孔直径d2为113mm~113.8mm,抗磨环3内孔直径比气缸套本体1内孔直径小0.2mm~1mm。所述气缸套本体1的裙部外圆处加工有标识槽4,气缸套本体1中支撑外圆处设有标识专利号的标识牌5。本实用新型的环保型发动机气缸套右装配在支撑肩13内孔部位的抗磨环3和与之配合的气缸套本体1组合而成,抗磨环3外圆与气缸套本体1呈小间隙配合,能够使燃油燃烧充分,减少积碳及减少由于积碳引起的磨粒磨损,延长了内燃机的使用寿命。抗磨环3的上端面高出支撑肩13上端面1.12mm至1.30mm,代替气缸套的凸台,抗磨环3的上端面与缸盖端面配合;抗磨环3的外圆直径为119mm至119.25mm,使外圆与气缸垫内孔配合;抗磨环3的高度为8.5mm至10mm;抗磨环3内孔直径为113mm至113.8mm,比气缸套内孔直径小0.2mm至1mm;抗磨环3的内孔倒角部位要求保留锐角;抗磨环3的材料选用普通灰铸铁材料;抗磨环的内外表面由数控车一次上车加工而成,既保证了内外圆的同轴度又保证内孔纹理呈螺旋纹状。气缸套内孔网纹为:Rpk<0.25um,Rk<0.5um,Rvk:1.5-2.5um,Rvk/Rk>2。抗磨环内孔网纹采用细平台珩磨网纹,沟槽多而浅,既能够保证内孔润滑需要又能避免多余润滑油参与燃烧,降低氮氧化合物的排放。由于在气缸套支撑肩内部装配的抗磨环内孔比缸套内孔直径小,能够阻碍活塞环上行时多余的润滑油参与燃烧,又能够阻碍高温燃气下行使润滑油恶化变质。当抗磨环槽内壁的积碳达到一定厚度时,能够利用活塞头部上行时把多余积碳吹出气缸套,能够有效避免磨粒磨损,提高气缸套使用寿命。实施例二如图3至图4所示,该实施例与实施例一的不同之处在于:本实施例的所述气缸套本体1的水道壁11上设置有水道壁增强结构,水道壁增强结构包括环绕水道壁11外周面设置的增强套12,增强套12的内周面与水道壁11的壁面固定连接,增强套12的外周面设置为锥面,锥面朝向所述气缸套本体1的上端部,该锥面与水道壁11的壁面连接处平滑过渡。所述气缸套本体1的支撑肩13下端面处设置有垫圈2,垫圈2选用铜垫,垫圈2套设在所述气缸套本体1上。所述增强套12的轴向长度H1为40mm,垫圈2的轴向厚度H2为0.813mm。本实用新型在实施例一的基础上增加了水道壁增强设计及气缸套支撑肩下端面增加铜垫两种结构设计,增加了气缸套整体刚度,减小了气缸套工作时振动,以实现来抗穴蚀,而且上述两种设计都是在不改变发动机设计的基础上实现。气缸套本体1的水道壁11上设置有水道壁增强结构,该水道壁增强设计在水道壁11出现穴蚀的部位设计一个锥面,这样既能增加此部位的强度,减少气缸套工作时受冲击产生振动幅度,又能使冷却液水流发生变化,减少水孔部位水流的连续冲击及增加冷却效果。气缸套本体1的支撑肩13下端面处设置有垫圈2,垫圈2套设在所述气缸套本体上,垫圈2选用铜垫,通过在气缸套支撑肩下端面设计一个铜垫,利用铜材料的良好延展性,减少发动机气缸套工作过程中的振动幅度。以上实施例仅用以说明而非限制本实用新型的技术方案,尽管参照上述实施例对本实用新型进行了详细说明,本领域的普通技术人员应当理解:依然可以对本实用新型进行修改或者等同替换,而不脱离本实用新型的精神和范围的任何修改或局部替换,其均应涵盖在本实用新型的权利要求范围当中。