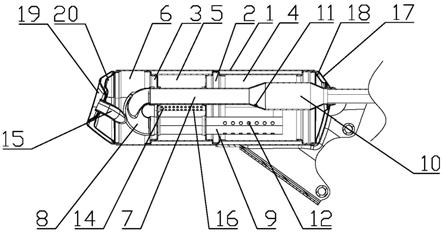
1.本实用新型属于摩托车的技术领域,涉及一种摩托车的消音器。
背景技术:2.摩托车消音器是一种允许气流通过而衰减噪声的装置,是摩托车上的重要零部件之一。消音器性能的好坏不仅影响摩托车噪声的大小,而且对发动机的功率、油耗、扭矩等性能都有较大影响。现有摩托车消音器大多由于结构设计不佳,无法合理有效的吸收由发动机运行排出的尾气及相应的噪音,导致消音器的运作噪声偏大。
技术实现要素:3.本实用新型针对现有技术的不足,提供了一种摩托车的消音器,可以更加有效的降低噪音,从而提升骑乘者的满意度,减轻环境噪音污染。
4.为解决上述技术问题,本实用新型的目的通过下述技术方案得以实现:
5.一种摩托车的消音器,包括消音器筒体,所述消音器筒体内设置有前隔板和后隔板,并将筒体内腔分割成前端的第一膨胀室、后端的第二膨胀室和中部的第三膨胀室,所述消音器筒体内设置有依次连接的通气管、回形管和第一消音管,所述通气管与第一消音管贯穿第一膨胀室、第三膨胀室和第二膨胀室,所述回形管位于第二膨胀室内,所述通气管上设置有位于第一膨胀室的触媒载体管,所述触媒载体管的后端设置有若干第一泄压孔,所述第一消音管前端位于第一膨胀室的部分设置有若干第二泄压孔。
6.优选的,所述第一泄压孔和第二泄压孔为圆形通孔;优选的,所述第一泄压孔设置有2-4个、沿周向分布;所述第二泄压孔设置有20-40个、沿周向阵列分布,所述第一泄压孔与第二泄压孔的孔径为4.5-5.5mm。
7.在上述的一种摩托车的消音器中,所述第一膨胀室、第三膨胀室和第二膨胀室的体积比是5:2:3。
8.在上述的一种摩托车的消音器中,所述消音器筒体内设置有连接第一膨胀室和第二膨胀室的第二消音管、连接第二膨胀室和第三膨胀室的第三消音管、连接第三膨胀室和外界的尾管。
9.在上述的一种摩托车的消音器中,所述第三消音管的前端与前隔板连接,第三消音管上设置有若干第三泄压孔并通过第三泄压孔与第三膨胀室连通。
10.优选的,所述第三泄压孔为圆形通孔;优选的,所述第三泄压孔设置有100-200个、沿周向阵列分布,所述第三泄压孔的孔径为2.5-3.5mm。
11.在上述的一种摩托车的消音器中,所述消音器筒体的前端设置有前盖和前盖内衬,所述消音器筒体的后端设置有后盖和后盖内衬。
12.在上述的一种摩托车的消音器中,所述消音器筒体的内壁覆盖有吸音棉,所述吸音棉的厚度为3-5mm,所述吸音棉设置在消音器筒体内壁与网板之间。
13.本实用新型增强消音的原理是:通过增加第一泄压孔,排放尾气在经过触媒载体
后会先逸出一部分气体至第一膨胀室中,通过增加第二泄压孔,排放尾气可以通过小孔位迅速在第一膨胀室内膨胀,避免因为膨胀不彻底所造成的额外噪音。通过增加第三泄压孔,使得第二膨胀室的气体缓慢通过小孔位排出到第三膨胀室,避免因为第二膨胀室的气体快速进入第三膨胀室所造成的额外噪音。
14.本实用新型和现有技术相比,具有如下有益效果:
15.1、本实用新型通过增加多点消音孔位,可以合理有效的吸收由发动机运行排出的尾气及相应的噪音,尤其是可以显著降低消音器的运行噪音,从而提升骑乘者的满意度,减轻环境噪音污染。
16.2、本实用新型改进了消音器腔体的布局,改善了消音器筒体的结构,进一步降低了消音器工作时的噪音。
附图说明
17.图1是本实用新型的立体图;
18.图2是本实用新型的剖视图;
19.图3是本实用新型内部的结构图;
20.附图标记:1、消音器筒体;2、前隔板;3、后隔板;4、第一膨胀室;5、第二膨胀室;6、第三膨胀室;7、通气管;8、回形管;9、第一消音管;10、触媒载体管;11、第一泄压孔;12、第二泄压孔;13、第二消音管;14、第三消音管;15、尾管;16、第三泄压孔;17、前盖;18、前盖内衬;19、后盖;20、后盖内衬。
具体实施方式
21.下面结合附图以具体实施例对本实用新型作进一步描述,参见图1-3:
22.一种摩托车的消音器,包括消音器筒体1,所述消音器筒体1内设置有前隔板2和后隔板3,并将筒体内腔分割成前端的第一膨胀室4、后端的第二膨胀室5和中部的第三膨胀室6,所述消音器筒体1内设置有依次连接的通气管7、回形管8和第一消音管9,所述通气管7与第一消音管9贯穿第一膨胀室4、第三膨胀室6和第二膨胀室5,所述回形管8位于第二膨胀室5内,所述通气管7上设置有位于第一膨胀室4的触媒载体管10,所述消音器筒体1内设置有连接第一膨胀室4和第二膨胀室5的第二消音管13、连接第二膨胀室5和第三膨胀室6的第三消音管14、连接第三膨胀室6和外界的尾管15。
23.本实用新型通过增加多点消音孔位:上述触媒载体管10的后端设置有若干第一泄压孔11,所述第一消音管9前端位于第一膨胀室4的部分设置有若干第二泄压孔12。通过增加第一泄压孔11,排放尾气在经过触媒载体后会先逸出一部分气体至第一膨胀室4中,通过增加第二泄压孔12,排放尾气可以通过小孔位迅速在第一膨胀室4内膨胀。
24.上述第一泄压孔11和第二泄压孔12为圆形通孔;所述第一泄压孔11设置有2个,沿周向分布,分别位于上下两侧,其孔径为5mm;所述第二泄压孔12设置有28个,沿周向阵列分布,其孔径为5mm。根据消音器的规格,也可以设置其他的数量和孔径。
25.除了第一泄压孔11和第二泄压孔12,本实施例还在第三消音管14增加了第三泄压孔16,其设置方式是:所述第三消音管14的前端与前隔板2连接,第三消音管14上设置有若干第三泄压孔16并通过第三泄压孔16与第三膨胀室6连通。通过增加第三泄压孔16,使得第
二膨胀室5的气体缓慢通过小孔位排出到第三膨胀室6。
26.上述第三泄压孔16为圆形通孔,所述第三泄压孔16设置有132个、沿周向阵列分布,所述第三泄压孔16的孔径为3mm。根据消音器的规格,也可以设置其他的数量和孔径。
27.本实施例还对消音器腔体的布局做了进一步改进:所述第一膨胀室4、第三膨胀室6和第二膨胀室5的体积比是5:2:3。以更好的降低噪音。
28.本实施例还对消音器筒体1的结构做了进一步的改进:
29.上述消音器筒体1的前端设置有前盖17和前盖内衬18,所述消音器筒体1的后端设置有后盖19和后盖内衬20。将现有消音器前盖17和后盖19的单层结构改进为双层结构,可以更有效的阻挡腔内噪音的逸出。
30.上述消音器筒体1的内壁覆盖有吸音棉,所述吸音棉的厚度为3-5mm,所述吸音棉设置在消音器筒体1内壁与网板之间,同时还增加了筒体的壁厚,通过吸音室所填充的加厚吸音材吸收排气音,而达到消音的目的。
31.本实施例的工作过程是:排放尾气经通气管7进入消音器内,依次流经通气管7(经过触媒载体管10后一部分气体由第一泄压孔11逸出至第一膨胀室4中)、回形管8及第一消音管9,并由第一消音管9的第二泄压孔12及前端进入第一膨胀室4;排放尾气在第一膨胀室4膨胀后经第二消音管13进入第二膨胀室5,再经第三消音管14上的第三泄压孔16进入第三膨胀室6,最后经尾管15排放到外界。
32.上述实施例仅为本实用新型的较佳实施例,并非依此限制本实用新型的保护范围,故:凡依本实用新型的结构、形状、原理所做的等效变化,均应涵盖于本实用新型的保护范围之内。