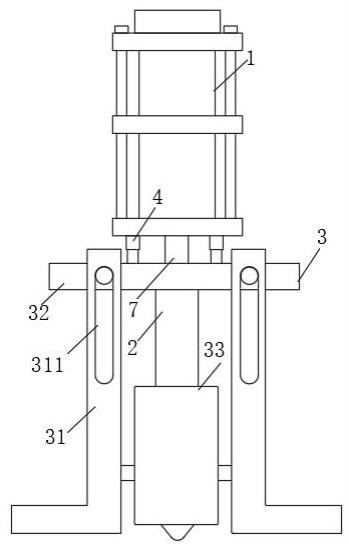
1.本发明涉及电解槽打壳技术领域,具体是一种电解槽智能打壳装置。
背景技术:2.由于在电解槽阴极上方的熔融电解质表面有一层较坚硬的电解质结壳,故投料前必须用电解槽的打壳装置先在壳面上打一孔洞作为下料;计算机控制打壳气缸及打击锤头,击破电解质表面的坚硬结壳形成孔洞,作为氧化铝投料点,每次打壳动作完成后伴随一次下料动作,这种方式能更好地实现氧化铝浓度的控制;但其在具体的使用过程中,一般的打壳锤头在惯性作用下其下降速度过快,且下降高度过深,易造成锤头表面沾染的电解质过多,影响锤头后期使用,另外,打壳动作完成后都会伴随一次下料动作,一般的打壳和下料装置是分开进行的,该种方式无法连贯进行打壳下料,不仅费时费力,易造成下料点的偏移,从而可能会造成填充的溶液滴落,影响工作效率;针对上述的技术缺陷,现提出一种解决方案。
技术实现要素:3.本发明的目的在于提供一种电解槽智能打壳装置,通过设置打壳头组件、打壳气缸和固定组件,以免导头下降高度过深而致导头完全插入电解质中,造成导头表面电解液过多而影响后期使用,通过设置挡板,保持导头表面的洁净,提高导头后期使用效率,通过设置下料组件与导料管,对电解槽打壳完毕的同时对电解槽内部进行溶液精准添加,减少溶液滴落电解槽外部的情况,打壳、下料连贯运行,提高了工作效率。
4.为实现上述目的,本发明提供如下技术方案:一种电解槽智能打壳装置,包括打壳气缸、打壳头组件和固定组件和电动推杆,所述打壳头组件通过固定组件活动安装在打壳气缸的下端,且固定组件与打壳气缸之间设置有两组电动推杆,所述打壳头组件由导杆、导头和限位杆构成,且导杆和导头均呈空心结构设置,且导头呈锥形结构固定安装在导杆的下端,所述导头下端外表面呈开口状设置,所述限位杆数量为四个,且其分别呈倾斜状固定安装在导杆两侧外表面靠近上下端的位置,四个所述限位杆划分为两组,左右两个所述限位杆为一组,且其呈左右对称,上下两组所述限位杆也呈对称;所述固定组件包括支架、横杆、限位筒和限位块,所述支架数量为两组,两组所述支架呈l形结构设置并呈左右对称,所述支架内部竖直开设有竖槽,且竖槽的两侧呈开口状,所述横杆横放在两组支架之间,且横杆的左右端分别横向贯穿两组竖槽,两组所述电动推杆活动连接在横杆与打壳气缸之间,所述限位筒固定安装在支架之间靠近下端的位置,所述导杆固定安装在横杆的下端中间位置,且导杆下端部分及导头均贯穿至限位筒的内部,所述限位筒的两侧内壁均靠近上下端的位置均固定安装有限位块,且限位块的纵剖面呈直角三角结构设置,上下两组所述限位块及左右两组限位块均相互对称。
5.进一步的,所述限位筒两侧内表面靠近下端位置均固定安装有长板,两组所述长板相对面均固定安装有挡板,且挡板横向剖切面呈半圆状,所述挡板外部靠近下端二分之一呈倾斜状并与导头外表面相贴,且挡板内表面与导头相贴面呈粗糙状设置。
6.进一步的,所述导杆的内部设置有下料机构,所述在导杆和导头之间贯穿连接有导料管,且下料机构与导料管上下对应。
7.进一步的,所述下料机构包括储料管、底板、出料孔一、横槽、滚珠、弹力带、活动板和出料孔二,所述储料管固定安装在打壳气缸下端中心位置,且储料管贯穿至导杆内部,所述底板固定安装在储料管内部靠近下端的位置,且底板上端中心位置呈突起状,所述底板上端外表面靠近突起处前后端及左右侧的位置均开设有两组出料孔一,相邻两组所述出料孔一之间及其两侧的位置均开设有横槽,所述横槽与出料孔一横向连通,所述底板的中心位置开设有圆槽,且滚珠活动安装在圆槽的内部,所述圆槽的位置与底板上端突起框的位置上下对应并连通,所述圆槽与横槽的一端槽口相连通,且滚珠与横槽内表面的另一侧位置之间固定安装有弹力带,所述弹力带中端位置固定安装有活动板,且活动板呈横向依次贯穿经过横槽及出料孔一的内部,所述活动板上端等距离开设有出料孔二,所述出料孔二与出料孔一的孔洞位置呈上下错位。
8.进一步的,所述导料管上端呈倒锥结构设置,且导料管的上端管口与底板的直径相吻合。
9.进一步的,所述导料管上端管口的中心位置横向固定安装有横条,且横条上端中心位置固定安装有抵板,且抵板与滚珠的位置上下对应,所述抵板上端外表面呈与滚珠外表面相适应的弧形面。
10.与现有技术相比,本发明的有益效果是:1、本发明中,通过打壳头组件、打壳气缸和固定组件配合使用,导杆及导头向电解槽内部插入,以限位筒内部靠近下端的两组限位块为限制,当限位杆沿着限位块的倾斜面下滑至底端时,靠近下端的两组限位杆被抵压至竖直状,并限定导杆无法继续下移,导头下降并冲击电解槽内部的壳膜,锥形结构导头可有效的将电解槽内部的硬壳击碎,同时,下端的两组限位块限制打壳头组件的下降高度,以免导头下降高度过深而致导头完全插入电解质中,造成导头表面电解液过多而影响后期使用;2、通过导头与限位筒内部的挡板配合使用,导头上升时,导头外表面与挡板上下平行移动,通过挡板内部的粗糙面,将导头外表面残存的电解质进行刮擦,电解质沿着导头的倾斜面向下掉落,以此保持导头表面的洁净,提高导头后期使用效率;3、本发明中,通过下料组件与导料管的配合使用,导料管随着打壳头组件上下运动,向上运动时,抵板顶动滚珠向上运动,连接在滚珠四周的弹力带受到牵引并向圆槽方向移动,活动板随之移动,出料孔一与出料孔二上下对齐,封闭的出料孔一打开,储料管内部的液体通过出料孔一向导料管内部集中聚集再向电解槽内部汇入,反之,当导料管随着打壳头组件归位时,滚珠及活动板均也归位,出料孔一与出料孔二上下错位并封闭,以此停止添料,在对电解槽打壳完毕的同时对电解槽内部进行溶液精准添加,减少溶液滴落电解槽外部的情况,打壳、下料连贯运行,提高了工作效率。
附图说明
11.为了便于本领域技术人员理解,下面结合附图对本发明作进一步的说明;图1为本发明的整体结构示意图;图2为本发明的局部剖面图;图3为本发明的导杆、导头、下料机构和导料管结合的局部剖面图;图4为本发明的出料管俯视剖面;图5为本发明中图3中a处放大图。
12.附图标记:1、打壳气缸;2、打壳头组件;21、导杆;22、导头;23、限位杆;3、固定组件;31、支架;311、竖槽;32、横杆;33、限位筒;34、限位块;4、电动推杆;5、长板;6、挡板;7、下料机构;71、储料管;72、底板;721、圆槽;73、出料孔一;74、横槽;75、滚珠;76、弹力带;77、活动板;78、出料孔二;8、导料管;81、横条;82、抵板。
具体实施方式
13.下面将结合本发明实施例中的附图,对本发明实施例中的技术方案进行清楚、完整地描述,显然,所描述的实施例仅仅是本发明一部分实施例,而不是全部的实施例。基于本发明中的实施例,本领域普通技术人员在没有做出创造性劳动前提下所获得的所有其他实施例,都属于本发明保护的范围。
14.实施例一:如图1-5所示,本发明提出的一种电解槽智能打壳装置,包括打壳气缸1、打壳头组件2和固定组件3和电动推杆4,打壳头组件2通过固定组件3活动安装在打壳气缸1的下端,且固定组件3与打壳气缸1之间设置有两组电动推杆4,打壳头组件2由导杆21、导头22和限位杆23构成,且导杆21和导头22均呈空心结构设置,且导头22呈锥形结构固定安装在导杆21的下端,导头22下端外表面呈开口状设置,限位杆23数量为四个,且其分别呈倾斜状固定安装在导杆21两侧外表面靠近上下端的位置,四个限位杆23划分为两组,左右两个限位杆23为一组,且其呈左右对称,上下两组限位杆23也呈对称;固定组件3包括支架31、横杆32、限位筒33和限位块34,支架31数量为两组,两组支架31呈l形结构设置并呈左右对称,支架31内部竖直开设有竖槽311,且竖槽311的两侧呈开口状,横杆32横放在两组支架31之间,且横杆32的左右端分别横向贯穿两组竖槽311,两组电动推杆4活动连接在横杆32与打壳气缸1之间,限位筒33固定安装在支架31之间靠近下端的位置,导杆21固定安装在横杆32的下端中间位置,且导杆21下端部分及导头22均贯穿至限位筒33的内部,限位筒33的两侧内壁均靠近上下端的位置均固定安装有限位块34,且限位块34的纵剖面呈直角三角结构设置,上下两组限位块34及左右两组限位块34均相互对称;工作时,将该装置放置在电解槽上端,两组支架31分别位于电解槽槽口的两侧,限位筒33及打壳头组件2对准电解槽的槽口,接着,启动打壳气缸1,打壳气缸1与外部的控制器电连接,值得一提的是,可在该打壳装置与控制器之间加装一组滤波器,滤波器用于消除操控机与智能控制装置的干扰信号,保证电解槽安全平稳运行,打壳气缸1驱动电动推杆4及横杆32向下推动,打壳头组件2受到横杆32推动也向下运动,导头22及导杆21向电解槽内部插入,以限位筒33内部靠近下端的两组限位块34为限制,当限位杆23沿着限位块34的倾
斜面下滑至底端时,靠近下端的两组限位杆23被抵压至竖直状,并限定导杆21无法继续下移,导头22下降并冲击电解槽内部的壳膜,锥形结构导头22可有效的将电解槽内部的硬壳击碎,同时,下端的两组限位块34限制打壳头组件2的下降高度,以免导头22下降高度过深而致导头22完全插入电解质中,造成导头22表面电解液过多而影响后期使用;待至硬壳击碎后,可通过打壳气缸1及电动推杆4的共同作用,驱动打壳头组件2向上运动,导头22从电解槽内部移出至限位筒33的内部,以此实现对电解槽的打壳,提高工作效率;实施例二:在实施例1中,通过对打壳头组件2的下移高度进行限定,以减少导头22下降高度过深而造成导头22沾染过多的电解质,然而当导头22不慎沾染一定量的电解质时,也需对其表面进行清理,保持其表面洁净,以降低导头22的工作效率,如图2所示,本实施例与实施例1的区别在于,限位筒33两侧内表面靠近下端位置均固定安装有长板5,两组长板5相对面均固定安装有挡板6,且挡板6横向剖切面呈半圆状,两组挡板6左右对应并包裹在导头22外部,挡板6外部靠近下端二分之一呈倾斜状并与导头22外表面相贴,且挡板6内表面与导头22相贴面呈粗糙状设置,导头22上升时,导头22外表面与挡板6上下平行移动,通过挡板6内部的粗糙面,将导头22外表面残存的电解质进行刮擦;工作时,打壳完毕,打壳气缸1带动横杆32及打壳头组件2的上移,导头22从电解槽内部抽出,并回归至两组挡板6之间,挡板6表面与导头22相贴,而导头22上升时,导头22外表面与挡板6上下平行移动,通过挡板6内部的粗糙面,将导头22外表面残存的电解质进行刮擦,电解质沿着导头22的倾斜面向下掉落,以此保持导头22表面的洁净,提高导头22后期使用效率;实施例三:在实施例1和实施例2中,通过对打壳头组件2的下移高度进行限定及对导头22表面进行清理,提高打壳效率,但在常规的电解槽打壳中,打壳与下料不能很好连贯进行,通常是打壳和下料分开进行,该种方式不仅费时费力,易造成下料点的偏移,且可能会造成填充的溶液滴落,影响工作效率;因此,可通过在导杆21内部设置下料机构7,缩短打壳和下料的间隔时间,以及保证下料打壳位置一致;如图2-5所示,本实施例与实施例1、实施例2的区别在于,导杆21的内部设置有下料机构7,在导杆21和导头22之间贯穿连接有导料管8,且下料机构7与导料管8上下对应,方便通过导料管8将液体准确引入电解槽中;下料机构7包括储料管71、底板72、出料孔一73、横槽74、滚珠75、弹力带76、活动板77和出料孔二78,储料管71固定安装在打壳气缸1下端中心位置,且储料管71贯穿至导杆21内部,底板72固定安装在储料管71内部靠近下端的位置,且底板72上端中心位置呈突起状,底板72上端外表面靠近突起处前后端及左右侧的位置均开设有两组出料孔一73,相邻两组出料孔一73之间及其两侧的位置均开设有横槽74,横槽74与出料孔一73横向连通,底板72的中心位置开设有圆槽721,且滚珠75活动安装在圆槽721的内部,圆槽721的位置与底板72上端突起框的位置上下对应并连通,圆槽721与横槽74的一端槽口相连通,且滚珠75与横槽74内表面的另一侧位置之间固定安装有弹力带76,弹力带76中端位置固定安装有活动板77,且活动板77呈横向依次贯穿经过横槽74及出料孔一73的内部,活动板77上端等距离开
设有出料孔二78,出料孔二78与出料孔一73的孔洞位置呈上下错位;导料管8上端呈倒锥结构设置,且导料管8的上端管口与底板72的直径相吻合,导料管8上升时,与底板72重合,导料管8上端管口的中心位置横向固定安装有横条81,且横条81上端中心位置固定安装有抵板82,抵板82随导料管8上升并抵触滚珠75,且抵板82与滚珠75的位置上下对应,抵板82上端外表面呈与滚珠75外表面相适应的弧形面,以此,防止滚珠75在受抵板82向上推动时发生偏移;工作时,事先对储料管71内部填充适量的氧化铝溶液,待至打壳头组件2打壳完毕后在打壳气缸1的驱动下向上滑动,直至导杆21两侧靠近上端的限位杆23分别抵压限位筒33内部靠近上端的两组限位块34,限位杆23抵压形变并沿着限位块34的倾斜面向上滑动,导杆21及导头22向上滑动,其两者之间的导料管8也随之上移并向储料管71靠近,直至限位杆23滑动至限位块34的倾斜面的顶端位置,限位杆23被抵触呈竖直状并停止滑动,以此,导料管8已插入储料管71内部,抵板82随导料管8向上移动,抵板82上端弧面与滚珠75外表面相贴,抵板82顶动滚珠75向上运动,连接在滚珠75四周的弹力带76受到牵引,并向圆槽721方向移动,而设置在弹力带76内段的活动板77也向圆槽721方向移动,原先与出料孔一73错位设置的出料孔二78随着活动板77移动,出料孔一73与出料孔二78上下对齐,封闭的出料孔一73打开,储料管71内部的液体通过出料孔一73向导料管8内部集中聚集再向电解槽内部汇入,以此,可在对电解槽打壳完毕的同时对电解槽内部进行溶液精准添加,减少溶液滴落电解槽外部的情况,打壳、下料连贯运行,提高了工作效率,待至电解槽内部溶液添加完毕,可再次通过打壳气缸1驱动打壳头组件2向下移动,此时,四组限位杆23均分别位于四组限位块34之间,打壳头组件2回归原位,下料机构7保持不动,导料管8随着打壳头组件2向下运动,导料管8远离底板72,滚珠75失去抵触向下归位,活动板77在弹力带76的弹性作用下回弹至原位,出料孔一73及出料孔二78再次错位,出料孔一73关闭,以此停止储料管71向外添料。
15.本发明的工作原理:工作时,将该装置放置在电解槽上端,两组支架31分别位于电解槽槽口的两侧,限位筒33及打壳头组件2对准电解槽的槽口,接着,启动打壳气缸1,打壳气缸1与外部的控制器电连接,值得一提的是,可在该打壳装置与控制器之间加装一组滤波器,滤波器用于消除操控机与智能控制装置的干扰信号,保证电解槽安全平稳运行,打壳气缸1驱动电动推杆4及横杆32向下推动,打壳头组件2受到横杆32推动也向下运动,导头22及导杆21向电解槽内部插入,以限位筒33内部靠近下端的两组限位块34为限制,当限位杆23沿着限位块34的倾斜面下滑至底端时,靠近下端的两组限位杆23被抵压至竖直状,并限定导杆21无法继续下移,导头22下降并冲击电解槽内部的壳膜,锥形结构导头22可有效的将电解槽内部的硬壳击碎,同时,下端的两组限位块34限制打壳头组件2的下降高度,以免导头22下降高度过深而致导头22完全插入电解质中,造成导头22表面电解液过多而影响后期使用;待至硬壳击碎后,可通过打壳气缸1及电动推杆4的共同作用,驱动打壳头组件2向上运动,导头22从电解槽内部移出至限位筒33的内部,以此实现对电解槽的打壳,提高工作效率;打壳完毕,打壳气缸1带动横杆32及打壳头组件2的上移,导头22从电解槽内部抽出,并回归至两组挡板6之间,挡板6表面与导头22相贴,而导头22上升时,导头22外表面与挡板6上下平行移动,通过挡板6内部的粗糙面,将导头22外表面残存的电解质进行刮擦,电
解质沿着导头22的倾斜面向下掉落,以此保持导头22表面的洁净,进一步提高导头22后期使用效率;事先对储料管71内部填充适量的氧化铝溶液,待至打壳头组件2打壳完毕后在打壳气缸1的驱动下向上滑动,直至导杆21两侧靠近上端的限位杆23分别抵压限位筒33内部靠近上端的两组限位块34,限位杆23抵压形变并沿着限位块34的倾斜面向上滑动,导杆21及导头22向上滑动,其两者之间的导料管8也随之上移并向储料管71靠近,直至限位杆23滑动至限位块34的倾斜面的顶端位置,限位杆23被抵触呈竖直状并停止滑动,以此,导料管8已插入储料管71内部,抵板82随导料管8向上移动,抵板82上端弧面与滚珠75外表面相贴,抵板82顶动滚珠75向上运动,连接在滚珠75四周的弹力带76受到牵引,并向圆槽721方向移动,而设置在弹力带76内段的活动板77也向圆槽721方向移动,原先与出料孔一73错位设置的出料孔二78随着活动板77移动,出料孔一73与出料孔二78上下对齐,封闭的出料孔一73打开,储料管71内部的液体通过出料孔一73向导料管8内部集中聚集再向电解槽内部汇入,以此,可在对电解槽打壳完毕的同时对电解槽内部进行溶液精准添加,减少溶液滴落电解槽外部的情况,打壳、下料连贯运行,提高了工作效率,待至电解槽内部溶液添加完毕,可再次通过打壳气缸1驱动打壳头组件2向下移动,此时,四组限位杆23均分别位于四组限位块34之间,打壳头组件2回归原位,下料机构7保持不动,导料管8随着打壳头组件2向下运动,导料管8远离底板72,滚珠75失去抵触向下归位,活动板77在弹力带76的弹性作用下回弹至原位,出料孔一73及出料孔二78再次错位,出料孔一73关闭,以此停止储料管71向外添料。
16.以上内容仅仅是对本发明结构所作的举例和说明,所属本技术领域的技术人员对所描述的具体实施例做各种各样的修改或补充或采用类似的方式替代,只要不偏离发明的结构或者超越本权利要求书所定义的范围,均应属于本发明的保护范围。
17.在本说明书的描述中,参考术语“一个实施例”、“示例”、“具体示例”等的描述意指结合该实施例或示例描述的具体特征、结构、材料或者特点包含于本发明的至少一个实施例或示例中。在本说明书中,对上述术语的示意性表述不一定指的是相同的实施例或示例。而且,描述的具体特征、结构、材料或者特点可以在任何的一个或多个实施例或示例中以合适的方式结合。
18.以上公开的本发明优选实施例只是用于帮助阐述本发明。优选实施例并没有详尽叙述所有的细节,也不限制该发明仅为的具体实施方式。显然,根据本说明书的内容,可作很多的修改和变化。本说明书选取并具体描述这些实施例,是为了更好地解释本发明的原理和实际应用,从而使所属技术领域技术人员能很好地理解和利用本发明。本发明仅受权利要求书及其全部范围和等效物的限制。