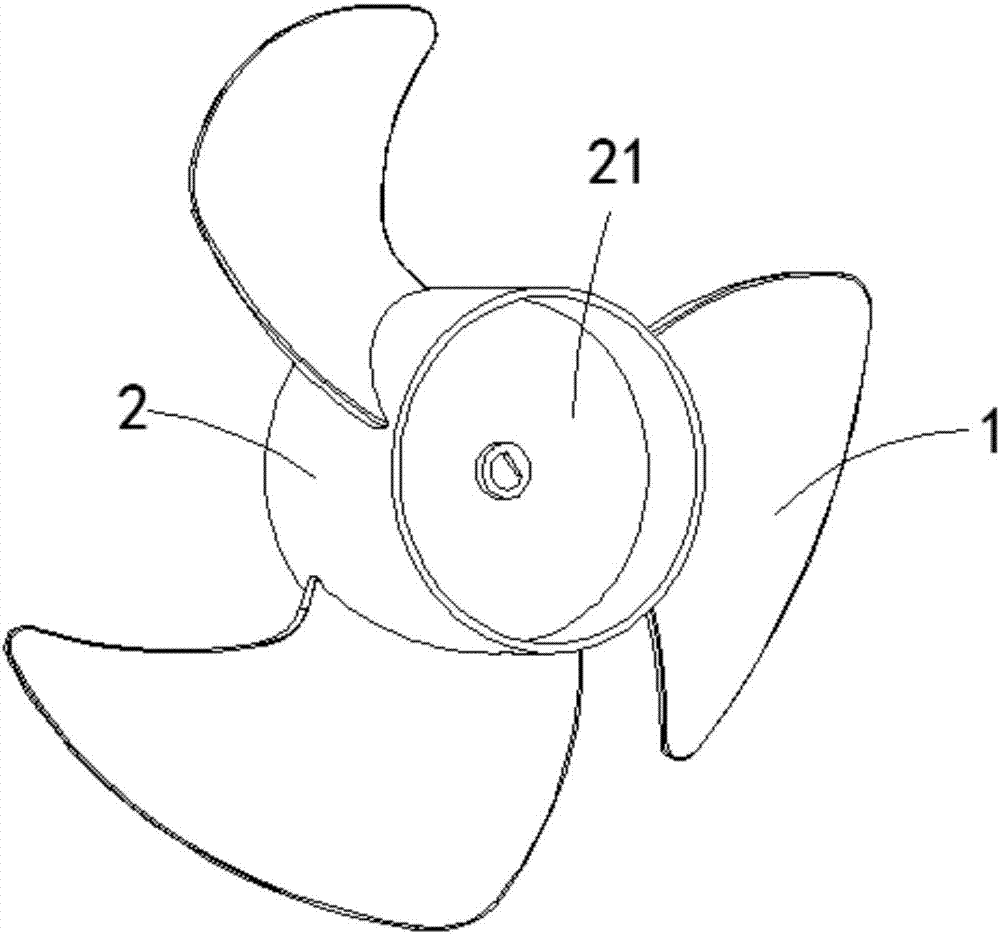
本实用新型涉及一种扇叶,尤其是一种超静音扇叶及风扇。
背景技术:
:在风扇的工作过程中,同等功率下风扇的风量大小主要取决于风扇扇叶的形状、数量以及其配合。为了获取较大的风量,现有的扇叶面积较大,故对风扇的尺寸有一定限制;且为了适配这一类扇叶的形状,扇叶采用的扭转角度并不能达到最佳,从而使得风扇在高速旋转工作时,伴随着较大的噪音。技术实现要素:本实用新型要解决的技术问题是提供一种风速风量大,噪音小的超静音扇叶及风扇。为解决上述技术问题,本实用新型提供的技术方案为:一种超静音扇叶,包括扇叶1,所述扇叶1包括用于与轮毂2连接的连接部100,以及过渡部200和端部300,所述连接部100具有与所述轮毂2相抵的连接边101及从所述连接边101的两端引出的第一侧边104和第二侧边105,所述第一侧边104和所述第二侧边105向远离所述轮毂2的方向延伸,所述扇叶1的中部下凹以形成下凹部400,所述下凹部400自所述连接部100向所述端部300延伸,使所述扇叶1的截面为弧形,所述第一侧边104和所述第二侧边105在所述过渡部200处的最大间距为最小间距的1.2至1.7倍。进一步地,所述扇叶1的中部下凹以形成下凹部400,所述下凹部400自所述连接部100向端部300延伸。进一步地,所述端部300上形成有带有圆弧状过渡的尖端301。进一步地,所述第一侧边104向内凹陷弯曲,所述第二侧边105向外凸出弯曲,且所述第一侧边104与所述第二侧边105在所述端部300汇合以形成所述尖端301。进一步地,一种超静音扇叶,以及用于连接扇叶1与转动电机的轮毂2,所述扇叶1在所述轮毂2的周围均匀排布。进一步地,包括三个均匀排布在所述轮毂2周围的所述扇叶1,所述轮毂2内对应设置有三个加强筋25,每一所述加强筋25的延伸方向和与之对应的扇叶1的延伸方向一致。进一步地,所述轮毂2还包括主体21、固定在所述主体上的电机限位座23、开设于所述电机限位座23且沿所述主体轴向贯穿的连接孔22,以及沿所述主体21的端面侧缘朝远离所述主体21一侧延伸的连接件24,所述连接件24与所述电机限位座23同侧,且所述电机限位座23和所述连接件24之间形成有用于容纳所述加强筋25的容纳腔。进一步地,当所述超静音风扇为8寸时,以所述轮毂2的中心为圆心,依次以100mm、125mm、150mm、175mm为直径作圆,沿各圆在所述扇叶1的过渡部200上截取四个截面;所述四个截面均为圆弧状,对应的弦长依次为64.4mm、79.9mm、95.3mm、109.1mm。进一步地,所述四个截面的安装角度依次为41.7°、38.3°、35.0°、31.9°。进一步地,当每一所述截面对应的弦长不变时,所对应的安装角度可在-15°~15°范围内变化。本实用新型的有益效果为:(1)扇叶独特的设计角度,使得扇叶旋转的时候所受到的空气阻力极小,容易切风,能够有效的提高风扇的功率,配合直流马达或者交流马达使用,都有风量大、风速高、噪音低等特点,适合节能产品使用,低碳、环保。(2)扇叶的中部下凹以形成下凹部,使扇叶的每一截面均为弧形,从而增大扇叶与空气的接触面积,从而提升风量、优化了流场,抑制了风扇噪声的产生。(3)第一侧边和第二侧边在过渡部处的最大间距为最小间距的1.2至1.7倍,进一步优化扇叶在轮毂上的安装角度,获得更大的风量和更低的噪音。(4)在扇叶的内端及外端均作了倒圆处理,叶片的厚度较为均匀,不仅增强了扇叶与轮毂的连接强度,而且结构美观、制造方便,提高了风量,降低了噪声。附图说明图1为本实用新型超静音扇叶一个优选实施例的结构示意图;图2为本实用新型超静音风扇一个优选实施例的正面结构示意图;图3为图2中超静音风扇的反面结构示意图;图4为图2中超静音风扇的侧面结构示意图;图5为图2中超静音风扇的主视图;图6为图5中超静音风扇的四个截面的安装角度和截面弦长的示意图。附图标记包括:1-扇叶100-连接部101-连接边102-第一边角103-第二边角104-第一侧边105-第二侧边200-过渡部300-端部301-尖端400-下凹部2-轮毂21-主体22-连接孔23-电机限位座24-连接件25-加强筋具体实施方式以下结合附图对本实用新型进行详细的描述。应当理解,此处所描述的具体实施例仅仅用以解释本实用新型,并不用于限定本实用新型。图1是本实施例超静音扇叶的结构示意图,如图1所示,该扇叶1大致为对号状,包括连接部100,过渡部200和端部300。连接部100用于与轮毂2相连,具有一个连接边101,在将扇叶1固定在轮毂2上时,连接边101与轮毂2紧抵。可以理解的是,连接边101上可以设置用于固定在轮毂2内的凸起(图中未示出),从而通过卡合、螺纹结构等常见的连接方式将扇叶1固定在轮毂2上。连接边101的两端分别形成有第一边角102和第二边角103,且连接部100沿第一边角102以及第二边角103向远离轮毂2的方向延伸而形成第一侧边104和第二侧边105。第一侧边104和第二侧边105朝远离连接部100的方向延伸,先形成过渡部200并最终汇合至终点形成端部300。第一侧边104由第一边角102引出,且向内凹陷弯曲,呈现弧形。对应的,第二侧边105由第二边角103引出并向外凸出弯曲,第二侧边105与第一侧边104在端部300汇合相连以形成一个带有圆弧过渡的尖端301。在本实施例中,结合图6,扇叶1的中部下凹以形成下凹部400,该下凹部400自连接部100向端部300延伸,即扇叶1并不是平面结构,其每一截面均为弧形。通过这一截面为弧形的下凹结构可增大扇叶与空气的接触面积,从而提升风量。因此,在本实施例中,通过下凹部400的弧形结构,使得扇叶在平面上的投影面积相同的情况下,显著增大扇叶与空气的接触面积。本实用新型还提供了一种超静音风扇,包括前述扇叶1和轮毂2。图2-5示出了本实用新型一个优选实施例中的超静音风扇。如图2-5所示,该扇叶1通过连接部100均匀的安装在轮毂2的周围,同时,可以看出扇叶1倾斜的安装在轮毂2的周面上。本实施例中,该风扇优选包括三个扇叶1,单数的设计可以降低噪声的数值。轮毂2包括主体21、连接孔22、电机限位座23、连接件24和加强筋25。主体21大致为圆柱体结构,该主体21优选为与扇叶1成一体成型结构。电机限位座23与主体21固定连接。电机限位座23的设置,可以增强轮毂2与转动电机之间的连接强度,使得轮毂2转动的更稳定。在本实施例中,电机限位座23优选地呈环形结构。且该电机限位座23在本实施例中优选地和主体21一体成型。连接孔22开设在该电机限位座23上,并沿主体21的轴向贯穿,其主要用于供转动电机(图中未示出)穿设固定,以随着转动电机的转动来带动轮毂2转动。连接件24大致为筒状结构,其沿主体21的端面侧缘朝远离主体21的一侧延伸。连接件24与电机限位座23位于同侧,电机限位座23与连接件24之间形成一环形容纳腔。加强筋25固定在该环形容纳腔内,其主要用于增强风扇工作过程中的平稳性。本实用新型中,加强筋25为三个,三个加强筋25均匀分布在该环形容纳腔内并与扇叶1一一对应,且每一加强筋25的延伸方向和与之对应的扇叶1的延伸方向一致。本实施例中,由于扇叶1大致为对号状,第一侧边104和第二侧边105在过渡部200处的最大间距为最小间距的1.2至l.7倍,进一步优化安装角度,获得更大的风量和更低的噪音。以常见的8寸风扇为例,以轮毂2的中心为圆心,依次以100mm、125mm、150mm、175mm为直径作圆,沿各圆在扇叶1上截取如图5所示的四个截面。由于下凹部400的存在,从Y轴方向看去,四个截面均为圆弧状,对应的弦长依次为64.4mm、79.9mm、95.3mm、109.1mm。本实施例中所涉及的安装角度即指各截面弧线所对应的弦与X轴之间的夹角。按照由轮毂2指向远离轮毂2的方向,上述四个截面的安装角度依次为41.7°、38.3°、35.0°、31.9°。各截面所对应的弦长不变,上述各安装角度可在-15°~15°范围内调整,即安装角度可根据实际需要在逆时针15°至顺时针15°范围内变化。这一安装结构能获得稳定的流畅,减小扇叶1内端的负荷。可以理解的是,对上述16寸风扇的扇叶1可进行等比例的放大或缩小,在此不作具体限定。表1测试数据对比档位风速(m/min)风量(m3/min)转速(RPM)噪音(dB)超静音扇叶H185.227.3162052.9其他扇叶H163.618.2164055.4表1为本实用新型的超静音扇叶与普通扇叶的数据对比,从表中可以看出本实用新型所述的超静音扇叶风速、风量、噪音等指标均优于市面上的普通风扇,具有鲜明的风速、风量大,噪音小的特点。以上内容仅为本实用新型的较佳实施例,对于本领域的普通技术人员,依据本实用新型的思想,在具体实施方式及应用范围上可以作出许多变化,只要这些变化未脱离本实用新型的构思,均属于本实用新型的保护范围。当前第1页1 2 3