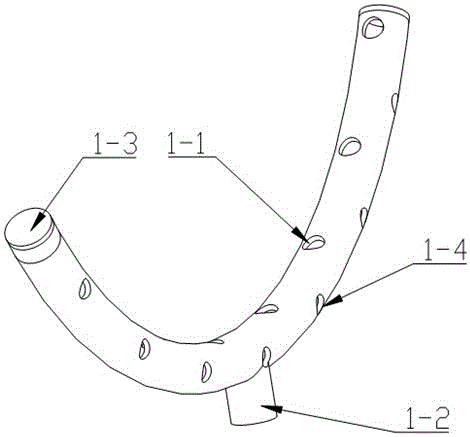
本实用新型属于高炉煤气管道粉尘清除技术领域,尤其是一种用于高炉煤气管道上,对管道内密封面沉积粉尘进行在线除尘式蝶阀。
背景技术:炼铁过程中,经过预热的空气从位于高炉下部的风口吹入,空气中的氧气在高温下与高炉内的焦炭反应生成CO,用以除去铁矿石中的氧并将铁还原出来,而反应后的气体称为高炉煤气。高炉煤气的成分主要是CO2、CO和N2,并含有水蒸气、粉尘(主要成分Fe2O3)等物质。高炉煤气管道的通风量与压力需要用金属密封阀门来调节,一般是三偏心蝶阀,以确保高炉正常生产工况的维持。高炉煤气中的粉尘易在管道蝶阀阀座密封面底部沉积,在水蒸气的作用下易产生板结现象,造成蝶阀阀板的卡塞,导致其压力调节功能的丧失,严重影响高炉炼铁活动的进行。现阶段,对于高炉煤气管道蝶阀阀座密封面底部沉积粉尘的清除,较为传统的方法主要有刮板刮削、人工振打、增加高炉定修频次等,具有自动化程度低、效率低下、人力耗费高、影响正常生产流程等缺点;较为先进的方法主要是采用超重力除尘技术,但具有除尘工序复杂、成本高、易造成高炉煤气管道腐蚀等问题。实用新型CN203768385U公开了一种高炉煤气管道粉尘吹扫装置,以氮气为工作介质,在氮气注入管道处设置阀门,控制氮气的注入;该装置能够实现对高炉煤气管道沉积粉尘的高效吹扫,但该装置不以蝶阀阀座密封面底部的沉积粉尘为清扫对象,无法实现该区域沉积粉尘的针对性清除。上述已有的高炉煤气管道沉积粉尘清除技术及装置,均不能实现蝶阀阀座密封面底部沉积粉尘的高效性、自动化、针对性和低成本清除。因此,有必要研制一种新型的蝶阀,可以对高炉煤气管道蝶阀阀座密封面沉积粉尘进行在线自动清除,解决现有技术及装置存在的问题。
技术实现要素:本实用新型要解决的技术问题是提供一种用于高炉煤气管道的在线除尘式蝶阀,该蝶阀能够实现高炉煤气管道内沉积粉尘的高效性、自动化、针对性和低成本在线清除。为解决上述技术问题,本实用新型所采取的技术方案是:一种用于高炉煤气管道的在线除尘式蝶阀,包括阀板、阀座、阀体和阀杆,所述的阀体两侧法兰均与高炉煤气管道连接,其特征在于所述的阀体进气端的下半部分内壁设有弧形风管,所述的弧形风管置于阀板和阀座的接触面处,弧形风管的弧形表面上设有风孔,弧形风管的两端通过端盖封闭,弧形风管的中部设有直风管,直风管与弧形风管连通,所述的直风管穿过阀体的侧壁,并且经连接管与处于阀体外部的氮气源连接,在氮气源和连接管之间设有压力调节阀。对上述结构作进一步限定,所述的弧形风管为不锈钢材质,弧形风管的曲率半径略小于阀板的外圈半径,弧形风管的弧度为100-150°,弧形风管按照竖直平面左右对称分布。对上述结构作进一步限定,所述的风孔包括两个以上的径向风孔和轴向风孔,径向风孔和轴向风孔均等间距分布,所述的径向风孔设于弧形风管曲率较小的内侧面,且径向风孔指向阀体的轴心,所述的轴向风孔设有靠近阀板的侧面上,且轴向风孔指向阀座与阀体的交界处。对上述结构作进一步限定,所述的径向风孔和轴向风孔交错布置。对上述结构作进一步限定,所述的压力调节阀上设有用于调节氮气进给量的调节手轮,所述的调节手轮与压力调节阀之间为旋转式配合,在压力调节阀的出口处设有压力表。对上述结构作进一步限定,所述的直风管与阀体侧壁之间为金属密封。采用上述技术方案所产生的有益效果在于:本实用新型通过在蝶阀内部设置弧形风管,弧形风管与外部的高压氮气源连接,利用高压氮气将积聚于阀体底部的沉积粉尘吹起,在管道内高炉煤气的流动作用下,粉尘被吸走,从而达到粉尘自动清除的效果,该清除装置能够解决现有粉尘清除技术存在的成本耗费高、除尘工序复杂等问题,实现蝶阀阀座密封面底部沉积粉尘的高效性、自动化、针对性和低成本清除;另外,本实用新型中的清除装置可以实现在线清除粉尘,只需利用外部的调节手柄来调节氮气压力,在打开阀门时即可实现对沉积粉尘吹扫,不需要管道或设备停机,避免影响正常生产流程。附图说明下面结合附图和具体实施方式对本实用新型作进一步详细的说明。图1是本实用新型的总体结构示意图;图2是本实用新型中弧形风管结构的示意图;图中:1、弧形风管;1-1、径向风孔;1-2、直风管;1-3、端盖,1-4、轴向风孔;2、连接管;3、压力调节阀;3-1、调节手轮;4、氮气源;5、阀座;6、阀板;7、阀体;8、阀杆;9、高炉煤气管道,10、压力表。具体实施方式本实用新型具体涉及一种用于高炉煤气管道的在线除尘式蝶阀,如附图1所示,该蝶阀具体包括阀板6、阀座5、阀体7、阀杆8以及在蝶阀上的自动清灰装置,阀体7两侧法兰均与高炉煤气管道9连接,形成蝶阀与高炉煤气管道9的连接体,高炉煤气即可通过蝶阀进行控制。本实用新型的自动清灰装置包括弧形风管1、氮气源4和压力调节阀2,由于蝶阀的下半部分容易沉积粉尘,因此把弧形风管1设置于阀体7进气端的下半部分,并固定于内壁上,弧形风管1置于阀板6和阀座5的接触面处,即蝶阀阀座密封面。为了实现向着蝶阀阀座密封面处吹出高压氮气,在弧形风管1的弧形表面上设有风孔,弧形风管1的两端通过端盖1-3封闭,弧形风管1的中部设有直风管1-2,直风管1-2与弧形风管1连通,直风管1-2穿过阀体7的侧壁,并且与处于阀体7外部的氮气源4连接,在氮气源4和直风管1-2之间设有压力调节阀3。上述结构中,通过氮气源4为弧形风管1供应高压氮气,由于设置弧形风管的位置正好是粉尘易堆积区域,在阀板6打开的情况下,这样利用弧形风管的风口吹出的高压氮气,将沉积粉尘吹起,在管道内高炉煤气的流动作用下,粉尘被吸走,从而达到粉尘清除的效果。另外,本实用新型中的氮气压力调节是置于阀体7外部,通过压力调节阀3手动调节,这样可以不影响高炉煤气管道内正常运行,可以实现在线清灰,避免影响正常生产流程,同时降低蝶阀的故障率。本实用新型中的弧形风管1为不锈钢材质,弧形风管1的曲率半径略小于阀板6的外圈半径,弧形风管1的弧度为100-150°,弧形风管1按照竖直平面左右对称分布。不锈钢材质的弧形风管1具有耐高温、耐腐蚀的特性,用于高炉煤气中,可以提高使用寿命。另外,弧形风管1的弧度设定,是根据蝶阀中积灰聚集区域,在高炉煤气靠近蝶阀时,具有沉降的趋势,因此在阀体7的下半部分设置弧形风管,其弧度控制在100-150°范围内,两侧对称分布,可以更好的对因重力沉降的积灰,在高压氮气的作用下吹起,避免沉降,从而实现清灰的目的。为了实现对蝶阀密封面处的积灰进行清理,避免影响阀门开启与关闭,对风孔的结构进行了设计,如附图2所示,风孔包括两个以上的径向风孔1-1和轴向风孔1-4,径向风孔1-1和轴向风孔1-4均等间距分布,径向风孔1-1设于弧形风管1曲率较小的内侧面,且径向风孔1-1指向蝶阀的轴心,轴向风孔1-4设有靠近阀板6的侧面上,且轴向风孔1-4指向阀座5与阀体7的交界处。利用径向风孔1-1对因重力沉降的积灰进行吹起,利用轴向风孔1-4对密封面处的积灰进行吹扫,这样在两个关键部位布设风孔,同时避免了积灰沉降以及积灰对阀门的卡死。在附图2中还可以清晰的看到,径向风孔1-1和轴向风孔1-4交错布置,即在两个径向风孔1-1之间设置一个轴向风孔1-4,这样布置是考虑弧形风管1的结构,而且要易于加工。在附图1中,在压力调节阀3上设有用于调节氮气进给量的调节手轮3-1,调节手轮3-1与压力调节阀3之间为旋转式配合,在压力调节阀3的出口处设有压力表10。利用压力调节阀3来控制除尘氮气的压力大小与开闭,设置手轮3-1,用来精确调控压力调节阀3的进给量,即精确控制除尘氮气压力的大小。由于高炉煤气的温度较高,在直风管1-2与阀体8侧壁之间的密封副不能采用普通橡胶密封,因此选用金属密封,直风管1-2和阀体8之间固结,这样避免了内部的高炉煤气不泄露,同时保证使用寿命。下面结合附图,以600mm三偏心蝶阀为例,对本实用新型的工作过程作详细说明。如图1、图2所示,本实用新型的核心部件是弧形风管1,设置为不锈钢材质,其曲率半径为290mm,弧度为120°,内外径分别为20mm和26mm;风孔1-1的直径为8mm,彼此间隔15°,均匀分布于弧形风管1的径向圆弧对称面两侧,共有8个;直风管1-2的内外径分别为19mm和25mm,分布于高炉煤气管道9的内外两侧,连接弧形风管1和连接管2;弧形风管端盖1-3位于弧形风管1的两端,起到密闭弧形风管1两端的作用。弧形风管1及直风管1-2通过焊接的方式固定于蝶阀上游,即蝶阀阀板6的左侧,高炉煤气管道9的内部,与阀座密封面5的间距为100mm,其中直风管1-2贯穿于高炉煤气管道9的内外两侧。炼铁过程中产生的高炉煤气由高炉顶部排放至高炉煤气管道9,流经蝶阀阀板6时,混杂的粉尘受到阻碍,逐步沉降于蝶阀密封面5的底部。如不及时清除,在水蒸气的作用下,容易产生板结,堵塞蝶阀阀板6的开闭运动,导致蝶阀压力调节功能的失效。根据高炉煤气管道9内高炉煤气压强0.25Mpa,以及粉尘在蝶阀阀板密封面5底部的沉降规律,通过压力调节阀3将氮气源4的出口压力调节为0.25~0.30MPa,每隔固定时间(3小时),充氮气60S。在高压氮气的冲击作用下,沉积于蝶阀阀板密封面5底部的粉尘被冲散,并在高炉煤气的流动作用下,穿过蝶阀,到达蝶阀下游,从而实现高炉煤气管道蝶阀阀座密封面底部沉积粉尘自动清除的目的。