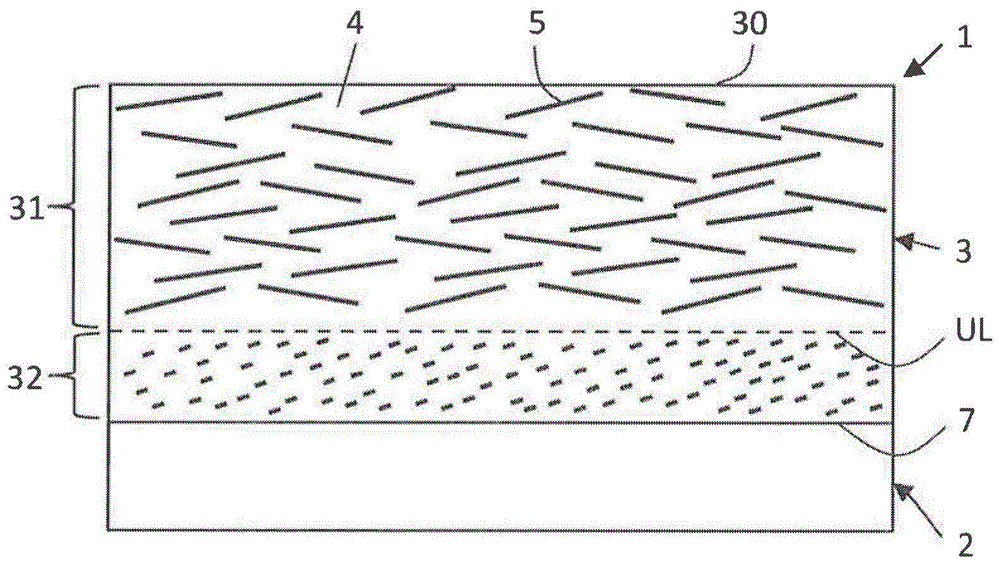
本发明涉及推力轴承用的滑动构件,详细而言,涉及具备里衬金属(日文:裏金)层、以及由合成树脂和纤维状粒子构成的滑动层的部分圆环形状的滑动构件。本发明还涉及具备该滑动构件的推力轴承。
背景技术:
:作为乏汽汽轮机或大型发电机等的旋转轴用的推力轴承,使用将多个具有部分圆环形状的轴承垫形状的滑动构件相对于旋转轴的推力环面沿周向配置的推力轴承(例如参照专利文献1)。在这样的可倾瓦块式推力轴承中,部分圆环形状的滑动构件以相对于轴构件的推力环面能自枢轴稍微摆动的方式受到支承。作为这样的推力轴承的滑动构件,已知在金属制的里衬金属层上覆盖由树脂组合物形成的滑动层而成的滑动构件,作为树脂组合物,专利文献2及专利文献3中记载了使玻璃纤维粒子、碳纤维粒子、金属间化合物纤维粒子等纤维状粒子分散在合成树脂中以提高滑动层的强度的树脂组合物。此外,专利文献4中记载了为了避免纤维强化树脂组合物具有强度的各向异性而在树脂基体中无取向、即各向同性地分散纤维状粒子的内容。此外,专利文献5中,通过使滑动层的表面侧和界面侧区域的纤维状粒子朝着与滑动层大致平行的方向分散、使中间区域内的纤维状粒子朝着与滑动层大致垂直的方向分散,防止起动时在滑动层的表面产生裂纹等损伤。现有技术文献专利文献专利文献1:日本专利特开2015-94373号公报专利文献2:日本专利特开平10-204282号公报专利文献3:日本专利特开2016-079391号公报专利文献4:日本专利特开2013-194204号公报专利文献5:日本专利特开2018-146059号公报技术实现要素:发明所要解决的技术问题乏汽汽轮机及大型发电机等在正常运转时,在轴构件的表面和滑动构件的滑动面之间形成油等的流体润滑膜,因此防止轴构件和滑动构件的表面之间直接接触。但是,在其停止时,油等的供给也停止,所以到旋转完全停止为止,轴在油等流体润滑膜耗尽的状态下继续旋转一定时间。因此,发生在轴构件表面和滑动构件的滑动面直接接触的状态下的滑动。若在这样的状态下发生滑动,则与轴构件接触的滑动面附近的树脂组合物被轴构件拖走,发生轴构件朝旋转方向的弹性变形。在该情况下,如专利文献4那样,在滑动层中无取向、即各向同性地分散纤维状粒子的情况下,滑动面附近的树脂组合物的变形量变大,在滑动层的内部产生裂纹造成的损伤的可能性增大。这与使纤维状粒子的长轴方向以朝向与滑动面垂直的方向的比例增大的方式分散的情况同样。另一方面,在使纤维状粒子以其长轴方向在与滑动面大致平行取向的纤维状粒子的比例大的方式分散在滑动层中的情况下,与滑动面平行的方向上的强度在滑动层整体中较大,所以施加于滑动层表面的负荷传递到与里衬金属层的界面。当负荷传递至界面时,由于在金属制的里衬金属层和合成树脂的滑动层之间的弹性变形量的不同而产生剪切力,以此为起点,剪切扩展,并造成剥离。此外,如专利文献5所述,在使滑动层的表面侧和界面侧区域的纤维状粒子朝着与滑动层大致平行、使中间区域内的纤维状粒子朝着与滑动层大致垂直的方向分散的情况下,在停止时油等流体润滑膜耗尽的状态下、对与直接轴的接触的状态下的滑动层施加的负荷大(大型的轴承装置的轴构件的重量大),所以相对于与滑动面平行的方向上的负荷的变形阻力小,中间区域的滑动层过度变形,判明发生新的问题,即、在中间区域内容易发生由沿着纤维状粒子的纵向的裂纹引起的损伤。因此,本发明的目的是克服现有技术的上述缺点,提供轴承装置停止时在滑动层的内部不易发生裂纹造成的损伤、且不易发生滑动层和里衬金属层的剪切的滑动构件。解决技术问题所采用的技术方案根据本发明的一个方面,提供包括里衬金属层和该里衬金属层上的滑动层的推力轴承用的滑动构件。该滑动构件具有部分圆环形状,滑动层包含合成树脂和分散在该合成树脂中的纤维状粒子。纤维状粒子具有滑动层的10~35%的体积比率。滑动层由包含滑动层的滑动面的滑动面侧区域、和包含滑动层和里衬金属层的界面的界面侧区域构成,界面侧区域的厚度(从滑动层的与里衬金属层的界面朝向滑动面侧)是滑动层的厚度的15~50%。滑动层具有第一截面和与该第一截面垂直的第二截面,上述第一截面和上述第二截面分别具有满足以下的(a)~(d)的关系的第一截面组织和第二截面组织。第一截面和第二截面分别与滑动面垂直。(a)在滑动面侧区域中,第一截面组织中的纤维状粒子的平均粒径为5~30μm,第二截面组织中的纤维状粒子的平均粒径为第一截面组织中的纤维状粒子的平均粒径的5~20%,(b)在界面侧区域中,第二截面组织中的纤维状粒子的平均粒径为5~30μm,第一截面组织中的纤维状粒子的平均粒径是第二截面组织中的纤维状粒子的平均粒径的5~20%,(c)在第一截面组织中,滑动面侧区域以相对于全部纤维状粒子为10%以上的体积比率包含长轴长度在20μm以上的纤维状粒子,长轴长度在20μm以上的纤维状粒子的分散指数在5以上,(d)在第二截面组织中,界面侧区域以相对于全部纤维状粒子为10%以上的体积比率包含长轴长度在20μm以上的纤维状粒子,长轴长度在20μm以上的纤维状粒子的分散指数在5以上,其中,分散指数由各纤维状粒子的比x1/y1的平均值表示,x1是截面组织中的纤维状粒子在与上述滑动面平行的方向上的长度,y1是截面组织中的纤维状粒子在与滑动面垂直的方向上的长度。根据本发明的一个具体例,第一截面优选与上述滑动构件的部分圆环形状的中心轴线平行。根据本发明的一个具体例,第二截面优选与上述滑动构件的部分圆环形状的中心轴线平行。根据本发明的一个具体例,第一截面组织中的滑动面侧区域内的长轴长度在20μm以上的纤维状粒子的平均长宽比优选为1.5~10,更优选平均长宽比为5~10。此外,第二截面组织中的界面侧区域内的长轴长度在20μm以上的纤维状粒子的平均长宽比优选为1.5~10,更优选平均长宽比为5~10。根据本发明的一个具体例,在第一截面组织的滑动面侧区域中,长轴长度在20μm以上的纤维状粒子相对于全部纤维状粒子的体积比率优选在30%以上。此外,在第二截面组织的界面侧区域中,长轴长度在20μm以上的纤维状粒子相对于全部纤维状粒子的体积比率优选在30%以上。根据本发明的一个具体例,纤维状粒子优选包含选自玻璃纤维粒子、陶瓷纤维粒子、碳纤维粒子、芳族聚酰胺纤维粒子、丙烯酸纤维粒子和聚乙烯醇纤维粒子的1种以上。根据本发明的一个具体例,合成树脂优选包含选自聚醚醚酮、聚醚酮、聚醚砜、聚酰胺酰亚胺、聚酰亚胺、聚苯并咪唑、尼龙、酚醛树脂、环氧树脂、聚缩醛、聚苯硫醚、聚乙烯和聚醚酰亚胺的1种以上。根据本发明的一个具体例,滑动层优选进一步包含选自石墨、二硫化钼、二硫化钨、氮化硼和聚四氟乙烯的1种以上的固体润滑剂。根据本发明的一个具体例,滑动层优选进一步以1~10体积%包含选自caf2、caco3、滑石、云母、莫来石、氧化铁、磷酸钙、钛酸钾和mo2c(碳化钼)的1种或2种以上的填充材料。根据本发明的一个具体例,里衬金属层优选在成为与滑动层的界面的表面具有多孔质金属部。本发明还提供具备多个上述滑动构件的推力轴承。附图说明图1是表示本发明的一例的滑动构件的第一截面组织的图。图2是表示本发明的一例的滑动构件的第二截面组织的图。图1a是图1的滑动构件的滑动层的滑动面侧区域的放大图。图1b是图1的滑动构件的滑动层的界面侧区域的放大图。图2a是图2的滑动构件的滑动层的滑动面侧区域的放大图。图2b是图2的滑动构件的滑动层的界面侧区域的放大图。图3是说明纤维状粒子的长宽比(a)的图。图4是说明纤维状粒子的分散指数(s)的图。图5是表示本发明的另一例的滑动构件的第一截面组织的图。图6是表示本发明的另一例的滑动构件的第二截面组织的图。图7a是说明树脂的流动的图。图7b是表示图7a的a-a截面的图。图8是本发明的滑动构件的一例的示意图。具体实施方式图8示意地表示本发明的滑动构件1的一例。该滑动构件1具有平板形状,该平板面的形状具有将圆环用两个半径切断而得的形状、即部分圆环形状。部分圆环形状的中心角度优选为25°~60°,但并不限定于该角度。滑动构件1是在具有平板的部分圆环形状的里衬金属层2上形成有滑动层3的构成。滑动层3包含合成树脂4,该合成树脂4中分散有10~35体积%的纤维状粒子5。以下,将滑动层3的表面称为“滑动面”。此外,本说明书中提及“截面”时,如无特别规定,则表示“与滑动面垂直的截面”。此外,将形成上述部分圆环形状的圆环的圆周方向简称为“周向”、将半径方向称为“径向”。将通过部分圆环形状的周向中央的径向的假想线(通过滑动构件1的板厚中心)称为“中心轴线17”。大致来讲,滑动层3包括包含滑动面30的一侧的滑动面侧区域31和包含与里衬金属层的界面7的一侧的界面侧区域32,在该两个区域中,纤维状粒子5的取向不同。在任一个区域中,存在纤维状粒子5的长轴方向整体上沿着其方向取向(即、朝着与其方向大致平行的方向的纤维状粒子的比例大)的方向,将滑动面侧区域31中的其方向称为第一方向,将界面侧区域32中的其方向称为第二方向。第一方向与第二方向大致垂直,任一方向均与滑动面30大致平行。将沿着第一方向和第二方向的(平行的)截面分别称为“第一截面”和“第二截面”,将观察各截面时的组织分别称为“第一截面组织”和“第二截面组织”。图1示意地表示本发明的一例的滑动构件的第一截面组织。此外,图2示意地表示本发明的滑动构件1的第二截面组织。滑动构件1中,滑动层3设置在里衬金属层2上,在滑动层3中,10~35体积%的纤维状粒子5分散在合成树脂4中。滑动层3被分为包含滑动面30的一侧的滑动面侧区域31、和包含与里衬金属层的界面7的一侧的界面侧区域32。界面侧区域32的厚度为滑动层3的厚度的15~50%。在滑动面侧区域31和界面侧区域32的任一区域中,优选在合成树脂4中分散有10~35体积%的纤维状粒子5。在滑动面侧区域31中,纤维状粒子5以长轴方向朝着与第一截面大致平行的方向的比例大(参照图1a、图2a)的方式分散,另一方面,在界面侧区域32中,纤维状粒子5以长轴方向朝着与第二截面大致平行的方向的比例大(参照图1b、图2b)的方式分散。当将第一截面组织中的滑动面侧区域内的纤维状粒子的平均粒径记为d1s、将第二截面组织中的滑动面侧区域内的纤维状粒子的平均粒径记为d2s、将第一截面组织中的界面侧区域内的纤维状粒子的平均粒径记为d1b、将第二截面组织中的界面侧区域内的纤维状粒子的平均粒径记为d2b时,d1s为5~30μm,d2s为d1s的5~20%,d2b为5~30μm,d1b为d2b的5~20%。将滑动构件1的纤维状粒子5的平均粒径d1s和d2b设为5~30μm的理由是因为:在平均粒径小于5μm的情况下,提高滑动层3的强度(变形阻力)的效果变小,当超过30μm时,在滑动层3受到来自轴构件的负荷的情况下,纤维状粒子5自身容易发生剪切。将滑动构件1的滑动层3中的纤维状粒子5的比例设为10~35体积%的理由是因为:若纤维状粒子5的比例小于10%,则滑动层3的强度(变形阻力)变小,相反地,若纤维状粒子5的比例超过35%,则滑动层3变脆,滑动时磨耗量容易增多。在观察滑动构件1的第一截面组织时,滑动面侧区域31以相对于全部纤维状粒子为10%以上的体积比率包含长轴长度在20μm以上的纤维状粒子。该体积比率优选在30%以上。另一方面,在观察滑动构件1的第二截面组织时,界面侧区域32以相对于全部纤维状粒子为10%以上的体积比率包含长轴长度在20μm以上的纤维状粒子。该体积比率也优选在30%以上。这里,“长轴长度”是指在截面组织中,沿着纤维状粒子的长度为最大的方向的长度。长轴长度在20μm以上的纤维状粒子具有增加滑动层3的强度、即变形阻力的效果。滑动层中,若“长轴长度在20μm以上的纤维状粒子”相对于全部纤维粒子的体积比率在10%以上,则能提高滑动面侧区域31、界面侧区域32中的“长轴长度在20μm以上的纤维状粒子”的长轴取向的方向上的强度、即变形阻力。合成树脂4优选包含选自聚醚醚酮、聚醚酮、聚醚砜、聚酰胺酰亚胺、聚酰亚胺、聚苯并咪唑、尼龙、酚醛树脂、环氧树脂、聚缩醛、聚苯硫醚、聚乙烯、和聚醚酰亚胺的1种以上。纤维状粒子5优选包含选自玻璃纤维粒子、陶瓷纤维粒子、碳纤维粒子、芳族聚酰胺纤维粒子、丙烯酸纤维粒子、和聚乙烯醇纤维粒子的1种以上。但是,合成树脂4和纤维状粒子5也可以是其他材质。滑动层3可进一步包含选自石墨、二硫化钼、二硫化钨、氮化硼、聚四氟乙烯的1种以上的固体润滑剂。通过含有该固体润滑剂,可以提高滑动层的滑动特性。此外,滑动层3可进一步以1~10体积%包含选自caf2、caco3、滑石、云母、莫来石、氧化铁、磷酸钙、钛酸钾和mo2c(碳化钼)的1种或2种以上的填充材料。通过含有该填充材料,可以提高滑动层的耐磨损性。滑动层3的厚度(即,从滑动面3和里衬金属层2的界面7到滑动面30为止之间的、与滑动面30垂直的方向上的距离)优选为0.5~6mm。在第一截面组织中,在滑动面侧区域31中分散的“长轴长度在20μm以上的纤维状粒子5”的分散指数s在5以上,在第二截面组织中,在界面侧区域32中分散的“长轴长度在20μm以上的纤维状粒子5”的分散指数s在5以上。其中,分散指数s由各纤维状粒子5的比x1/y1的平均值表示,x1是作为对象的截面组织(第一截面组织或第二截面组织)中的纤维状粒子在与滑动面30平行的方向上的长度,y1是第一截面组织或第二截面组织中的纤维状粒子5在与滑动面30垂直的方向上的长度(参照图4)。在第一截面组织中,滑动层3的滑动面侧区域31中的纤维状粒子5的分散指数s在5以上表示以纤维状粒子5的长轴方向与滑动面30平行且朝向径向的纤维状粒子的比例大的方式分散。因此,滑动面侧区域31的物性为各向异性,特别是相对于与滑动面31和第一截面平行的负荷的强度(变形阻力)增大。另一方面,在第二截面组织中,滑动层3的界面侧区域32中的纤维状粒子5的分散指数s在5以上,且以纤维状粒子5的长轴方向与滑动面30平行且朝向周向的纤维状粒子的比例大的方式分散。因此,滑动层3的界面侧区域32相对于与滑动面30和第二截面平行的负荷的强度(变形阻力)增大。如果纤维状粒子5具有上述的取向,则在轴承装置停止时,即使在轴构件与滑动层3的滑动面30直接接触的状态下发生一定时间的滑动,在包含滑动面30的滑动层3的滑动面侧区域31中相对于第一方向的负荷的强度(变形阻力)大,在界面侧区域32中相对于第二方向的负荷的强度(变形阻力)大,由此,相对于负荷的滑动层的变形阻力的强度沿大致垂直的第一方向和第二方向分散。即,施加于滑动层表面的负荷在从滑动层3的纤维状粒子的取向不同的边界部位到界面侧区域得到缓和,可以防止传递到与里衬金属层的界面,所以不易发生由金属制的里衬金属层和合成树脂的滑动层之间的弹性变形量的不同造成的剪切。此外,即使来自轴构件的大负荷(因为大型的轴承装置,轴构件的重量大)施加于滑动层,滑动面侧区域31和界面侧区域32的纤维状粒子的长轴方向与滑动面平行地取向,平行方向的强度在整个滑动层中较大,因此不易产生(沿着滑动层内的垂直方向的)内部的裂纹。根据以上的机理,本发明的滑动构件1即使在轴承装置停止时的、滑动面30与对应轴表面直接接触的状况下,也可以防止在滑动层3的内部(沿着纵向)产生裂纹等损伤,且不易发生滑动层和里衬金属层的剪切。另外,在滑动层的滑动面侧区域31、界面侧区域32中,纤维状粒子的含量可以大致相同,“长轴长度在20μm以上的纤维状粒子”的含量也大致相同。此外,在滑动层的滑动面侧区域31、界面侧区域32中分散的“长轴长度小于20μm的纤维状粒子”的分散指数与在各区域中分散的“长轴长度在20μm以上的纤维状粒子”的分散指数可以是大致相同的分散指数。在本发明的滑动构件1中,第一截面组织的滑动面侧区域的“长轴长度在20μm以上的纤维状粒子”的平均长宽比优选为1.5~10,更优选5~10,进一步优选7~10。此外,第二截面组织的界面侧区域的“长轴长度在20μm以上的纤维状粒子”的平均长宽比优选为1.5~10,更优选5~10,进一步优选7~10。平均长宽比是与纤维状粒子的取向有关的数值,如果纤维状粒子的长轴方向不是与观察的截面(径向或周向)大致平行地取向,则其长宽比是接近于1的值(例如小于1.5)。因此,如果平均长宽比小于1.5,则提高树脂层的强度(变形阻力)的效果小。在该情况下,即使使“长轴长度在20μm以上的纤维状粒子”的取向在滑动面侧区域和界面侧区域中不同,变形阻力的各向异性的差也容易变得不足够,不易获得上述效果。另一方面,若平均长宽比超过10,则滑动层在受到来自轴构件的负荷时纤维状粒子自身有可能发生剪切。里衬金属层2可以在成为与滑动层3的界面的表面上具有多孔质金属部6。图5中示意地表示使用具有多孔质金属部6的里衬金属层2的滑动构件1的一例的第一截面组织,图6中示意地表示第二截面组织。通过在里衬金属层2的表面设置多孔质金属部6,能够提高滑动层和里衬金属层的接合强度。这是因为,通过由在多孔质金属部的空孔部含浸构成滑动层的组合物产生的锚固效果,能实现里衬金属层和滑动层的接合力的强化。多孔质金属部可以通过将cu、cu合金、fe、fe合金等金属粉末烧结在金属板或条等的表面上来形成。多孔质金属部的空孔率为20~60%左右即可。多孔质金属部的厚度为50~500μm左右即可。该情况下,在多孔质金属部的表面上覆盖的滑动层的厚度设为0.5~6mm左右即可。其中,这里记载的尺寸是一例,本发明并不限定于该值,可变更为不同的尺寸。以下,对本发明的实施方式进行说明,但本发明并不局限于这些实施方式。第一实施方式在第一实施方式中,第一截面与滑动构件1的中心轴线大致平行。因此,在滑动构件1的中心轴线附近,在滑动面侧区域31内,纤维状粒子5的长轴方向朝着与中心轴线大致平行的方向的比例大,在界面侧区域32内,纤维状粒子5的长轴方向朝着与中心轴线大致垂直的方向的比例大。此外,如果滑动构件1是中心角度为25°~60°左右的部分圆环形状,则大致可以说中心轴线方向大致相当于部分圆环的径向,与中心轴线垂直的方向大致相当于周向。由此,关于滑动构件1的滑动层的纤维状粒子5的取向,可以说在滑动面侧区域31内纤维状粒子5的长轴方向朝着与径向大致平行的方向的比例大,在界面侧区域32内纤维状粒子5的长轴方向朝着与周向大致平行的方向的比例大。因此,在本实施方式的滑动构件中,在滑动面侧区域31内,径向的变形阻力大,在界面侧区域32内,周向的变形阻力大。在这样的纤维状粒子5的取向时,即使轴承装置停止时、在轴构件和滑动层3的滑动面30直接接触的状态下发生一定时间的滑动,通过使滑动层的相对于负荷的变形阻力的强度在径向和周向上分散,里衬金属层和滑动层的剪切受到抑制的效果如上所述。特别是在将滑动构件1用于推力轴承的情况下,与轴构件发生滑动的滑动方向是滑动构件1的周向,但是在本实施方式中,由于界面侧区域32的周向的变形阻力变大,所以相对于施加于滑动层3的来自轴构件的负荷,界面侧区域32的周向变形量减小,更加不容易发生由于与里衬金属层2的弹性变形量的差造成的剪切。另外,因为滑动面侧区域31和界面侧区域32的纤维状粒子的长轴方向在与滑动面平行的方向上取向,如上所述,也不容易产生滑动层内的在垂直方向上的内部裂纹。第二实施方式在第二实施方式中,第二截面与滑动构件1的中心轴线大致平行。因此,在滑动构件1的中心轴线附近,在滑动面侧区域31内,纤维状粒子5的长轴方向朝着与中心轴线大致垂直的方向的比例大,在界面侧区域32内,纤维状粒子5的长轴方向朝着与中心轴线大致平行的方向的比例大。如第一实施方式中所说明,如果滑动构件1是中心角度为25°~60°左右的部分圆环形状,则大致可以说中心轴线的方向大致相当于部分圆环的径向,与中心轴线垂直的方向大致相当于周向。因此,关于滑动构件1的滑动层的纤维状粒子5的取向,可以说在滑动面侧区域31内纤维状粒子5的长轴方向朝着与周向大致平行的方向的比例大,在界面侧区域32内纤维状粒子5的长轴方向朝着与径向大致平行的方向的比例大。因此,在实施方式2的滑动构件中,在滑动面侧区域31内,周向的变形阻力大,在界面侧区域32内,径向的变形阻力大。在该纤维状粒子5的取向时,即使轴承装置停止时、在轴构件和滑动层3的滑动面30直接接触的状态下发生一定时间的滑动,通过使滑动层的相对于负荷的变形阻力的强度在径向和周向上分散,里衬金属层和滑动层的剪切受到抑制的效果如上所述。另外,与专利文献5不同,因为滑动面侧区域31和界面侧区域32的纤维状粒子的长轴方向在与滑动面平行的方向上取向,如上所述,也不容易产生滑动层内的在垂直方向上的内部裂纹。第三实施方式在第三实施方式中,第一截面与从滑动构件1的中心轴线倾斜约40°~约50°的方向平行。在该情况下,第二截面与从滑动构件1的中心轴线朝与第一截面相反的方向倾斜约40°~约50°的方向平行。因此,关于滑动构件1的滑动层的纤维状粒子5的取向,在滑动面侧区域31内,纤维状粒子5的长轴方向朝着从中心轴线和周向倾斜约40°~约50°的方向的比例大,在界面侧区域32内,纤维状粒子5的长轴方向朝着与从滑动构件1的中心轴线和周向朝与第一截面相反的方向倾斜约40°~约50°的方向大致平行的比例大。在该纤维状粒子5的取向时,即使轴承装置停止时、在轴构件和滑动层3的滑动面30直接接触的状态下发生一定时间的滑动,通过使滑动层的相对于负荷的变形阻力的强度在径向和周向上分散,里衬金属层和滑动层的剪切受到抑制的效果如上所述。特别是在将滑动构件1用于推力轴承的情况下,因为纤维状粒子5的取向在相对于滑动方向(即、周向)朝左右倾斜约40°~约50°的2个方向上分散,所以相对于负荷的滑动层的变形阻力的强度大致均等地分散,因此分散效果提高,防止剪切发生的效果得到改善。另外,因为滑动面侧区域31和界面侧区域32的纤维状粒子的长轴方向在与滑动面平行的方向上取向,如上所述,也不容易产生滑动层内的在垂直方向上的内部裂纹。以上说明了3个实施方式,但是本发明并不限定于这些实施方式,第一截面可以采用其他任意的方向。上述滑动构件1可用于例如推力轴承。例如,该轴承具备具有圆环状的凹部的外壳。在圆环状的凹部沿周向配置多个上述滑动构件,通过这些滑动构件来支承作为对象轴的轴构件的推力环面。上述滑动构件的部分圆环形状(曲率、尺寸等)以适合于圆环状的凹部和轴构件的方式设计。但是,上述滑动构件可用于其他形态的轴承或其他的滑动用途。本发明还包含具有这样的多个上述滑动构件的推力轴承。对如上说明的滑动构件,下面按照制造工序进行详细说明。(1)纤维状粒子原材料的准备作为纤维状粒子的原材料,可使用例如人工制造的无机纤维粒子(玻璃纤维粒子、陶瓷纤维粒子等)或有机纤维粒子(碳纤维粒子、芳族聚酰胺纤维、丙烯酸纤维粒子、聚乙烯醇纤维粒子等)。(2)合成树脂原材料粒的准备作为合成树脂的原材料,优选使用平均粒径为7~30μm、长宽比为5~100的粒子。作为合成树脂,可使用包含选自聚醚醚酮、聚醚酮、聚醚砜、聚酰胺酰亚胺、聚酰亚胺、聚苯并咪唑、尼龙、酚醛树脂、环氧树脂、聚缩醛、聚苯硫醚、聚乙烯和聚醚酰亚胺的1种以上的合成树脂。(3)树脂组合物片的制造树脂组合物片由上述原材料等使用熔融混炼机、供给模具、片成形模具和冷却辊进行制作。“熔融混炼机”利用熔融混炼机,将合成树脂原材料粒、纤维状粒子原材料及其他任意材料(固体润滑剂、填充材料等)的原材料一边以230℃~390℃的温度进行加热一边混合,制作熔融状态的树脂组合物。该树脂组合物从熔融混炼机中以一定的压力被挤出。“供给模具”从熔融混炼机中被挤出的树脂组合物经由供给用模具总是以一定量供给至片成形模具。供给模具具有加热用加热器,将在供给模具内通过的树脂组合物加热至385℃~400℃的温度并维持在熔融状态。“片成形模具”树脂组合物利用片成形模具形成为片形状。从供给模具供给至片成形模具的熔融状态的树脂组合物被成形为片形状,一边将片成形模具内向出口侧移动一边慢慢地自然冷却,形成半熔融状态的片。“冷却辊”半熔融状态的树脂组合物片一边连续地与冷却辊接触而被冷却一边从“片成形模具”中拉出。冷却辊包括从上面和下面的两侧挤压树脂组合物片并使其移动的至少一对辊(上侧辊和下侧辊)。半熔融状态的树脂组合物片在从冷却辊中被拉出后,成为完全固体状态的片。另外,冷却辊利用安装在辊内的电动加热器能够控制温度,且能够利用电动加热器以可控制的方式旋转驱动。作为树脂组合物片的厚度的尺寸的一例,为1~7mm。变为固体状态的树脂组合物片被切割成适合于后述的覆盖工序中使用的里衬金属的尺寸的大小。(4)里衬金属作为里衬金属层,可以使用亚共析钢或不锈钢等的fe合金、cu、cu合金等的金属板。在里衬金属层表面、即成为与滑动层的界面的一侧可以形成多孔质金属部,多孔质金属部可具有与里衬金属层相同的组成,也可使用不同的组成或材料。(5)覆盖和成形工序将树脂组合物片接合在里衬金属层的一侧表面、或里衬金属的多孔质金属部上。然后,切割成使用形状、例如部分圆环形状后,为了使组合物的厚度均匀,对里衬金属进行加工或切削。如此,在以树脂组合物片的片成形工序中的拉出方向为部分圆环形状的规定方向的方式进行成形后,切削除去表面层,精加工成规定厚度。组织控制接着,对使纤维状粒子取向的组织控制方法进行说明。组织控制通过在上述的树脂组合物片的制造工序中设定冷却辊的温度来进行。具体而言,将上侧冷却辊的温度设定为比下侧冷却辊的温度高约50℃~60℃(170℃~180℃)。相对于此,以往的冷却辊的温度设定为上侧冷却辊和下侧冷却辊为相同温度(110℃~130℃)。半熔融状态的树脂组合物片一边与冷却辊接触而被冷却一边固化,但由于将下侧冷却辊的温度设定得比上侧冷却辊的温度低,所以树脂组合物片的下表面先开始固化。此外,因为上侧冷却辊的温度比下侧冷却辊的温度高,所以未完全固化的半熔融状态的树脂组合物容易积存在上侧冷却辊入口处(以下,也称为“树脂积存”)。图7a示意地表示该情形。树脂组合物片沿着从纸面的右侧朝向左侧的方向被抽出(抽出方向10)。将半熔融树脂组合物的流动表示为箭头11。从片成形模具12(纸面的右侧)流入的半熔融树脂组合物11在上侧冷却辊13的入口侧形成一定量的树脂积存15。形成有树脂积存15的半熔融状态的树脂组合物11(以下也称为“半熔融树脂组合物”)一边沿着与抽出方向相同的方向旋转而滞留一边被压入树脂组合物片的内部。树脂组合物片的内部因为与冷却辊不接触,所以在通过冷却辊的期间保持半熔融状态,被压入的半熔融树脂组合物11一边与已经被下侧冷却辊14固化的树脂组合物片下面部16碰撞,一边朝着树脂组合物片的宽度方向两端部广泛流动(参照图7b)并开始固化。因此,树脂组合物片的厚度方向的中央部附近的纤维状粒子容易以长轴沿着树脂组合物片的宽度方向(与抽出方向10垂直的方向)进行取向。另一方面,在树脂组合物片的表面附近(片上表面和下表面),半熔融状态的树脂组合物片一边朝着冷却辊的出口侧总是沿一方向流动,一边与冷却辊接触而固化,所以纤维状粒子容易以长轴在树脂组合物片的表面沿长轴方向(抽出方向10)进行取向。现有技术中,将上侧冷却辊和下侧冷却辊的温度设定为相同,但在该情况下,从片成形模具流入的半熔融树脂组合物不会在冷却辊入口侧形成树脂积存,而是朝着出口侧总是沿一方向流动,所以在树脂组合物片的厚度方向的全部区域中,纤维状粒子容易在长轴与树脂组合物片的表面平行的方向上取向。此外,在通过现有的通常的注塑成型法制造树脂组合物片的情况下,因为从片成形模具的供给口瞬间填充熔融状态的树脂组合物,所以熔融状态的树脂组合物之间在模具内的各处碰撞或合流。因此,在模具内熔融状态的树脂组合物沿一方向流动的部位与熔融状态的树脂组合物之间碰撞的部位处的纤维状粒子的取向方向不同,在树脂组合物片中,当从表面观察时,纤维状粒子的长轴朝着与表面平行的方向取向的部位和纤维状粒子的长轴无规取向的部位(熔接部)混合存在。此外,如现有技术文献4所述,在将由合成树脂中包含交联促进剂和纤维状粒子形成的树脂组合物通过注塑成型法来制造树脂组合物片的情况下,纤维状粒子无取向(各向同性)地分散。此外,如现有技术文献5所述,在成形模具内进行冷却、且使拉出辊的拉出速度周期性变化来制造树脂组合物片的情况下,在树脂组合物片的厚度方向的中央部区域中,纤维状粒子在长轴与树脂组合物片的表面垂直的方向上分散,另一方面,在表面附近,纤维状粒子在长轴与树脂组合物片的表面平行的方向上分散。接着,对滑动层的滑动面侧区域、界面侧区域的区分方法进行说明。使用电子显微镜以200倍拍摄滑动构件的第一截面组织和第二截面组织的多个部位的电子图像。在第一截面组织中,在滑动面附近可观察到大量朝着大致沿滑动面的方向细长延伸的纤维状粒子(参照图1a),但是在与里衬金属层的界面附近几乎没有观察到这样细长延伸的纤维状粒子,而是大部分是球状或扁球状的粒子(参照图1b)。相反地,在第二截面组织中,在滑动面附近几乎没有观察到细长延伸的纤维状粒子,而是大部分是球状或扁球状的粒子(参照图2a),但在与里衬金属层的界面附近观察到大量细长延伸的纤维状粒子(参照图2b)。这些纤维状粒子的形态不同的2个区域作为在滑动层的厚度方向上层叠的2层而形成,因此由上述的多个第一截面组织和第二截面组织来确定其边界线,描画出与滑动面平行的假想线ul(边界线)。将从滑动层的滑动面到假想线ul为止的区间作为滑动面侧区域,将从滑动层的与里衬金属层的界面到假想线ul为止的区间作为界面侧区域。在图1中以虚线表示假想线ul。另外,在里衬金属层的表面具有多孔质部的情况下,里衬金属层的表面呈凹凸状。该情况下,滑动层和里衬金属层的界面是在拍摄图像中通过里衬金属层(多孔质部)的表面的位于最接近滑动面侧的凸部的顶部且与滑动面平行的假想线。对于各截面,使用下述方法来测定用上述方向区分的滑动面侧区域和界面侧区域的纤维状粒子的平均粒径。关于纤维状粒子的平均粒径,使用上述的电子显微镜,根据滑动构件的第一截面组织和第二截面组织的多个部位的电子图像(200倍)来测定。具体而言,纤维状粒子的平均粒径如下求得:对于所得的电子图像,使用通常的图像分析方法(分析软件:image-proplus(4.5版本),普拉奈特龙株式会社((株)プラネトロン)制)测定各纤维状粒子的面积,将其换算成假定为圆时的平均直径。其中,电子图像的拍摄倍率不限定于200倍,也可变更为其他倍率。接着,对滑动层中所含的长轴长度为20μm以上的纤维状粒子的体积相对于纤维状粒子的总体积的比例的测定方法进行说明。使用通过采用电子显微镜而得的滑动构件的第一截面组织和第二截面组织的滑动面侧区域和界面侧区域的各拍摄图像,并使用通常的图像分析方法(分析软件:image-proplus(4.5版本),普拉奈特龙株式会社制)将拍摄图像中的纤维状粒子区分为长轴长度为20μm以上的纤维状粒子和除此以外的纤维状粒子。测定拍摄图像中的全部纤维状粒子的总面积和长轴长度为20μm以上的全部纤维状粒子的总面积,算出长轴长度为20μm以上的纤维状粒子相对于全部纤维状粒子的面积比率。该面积比率相当于体积比率。平均长宽比a通过使用上述的手法得到的电子图像的拍摄图像,作为长轴长度为20μm以上的各纤维状粒子的长轴长度l和短轴长度s的比(长轴长度l/短轴长度s)的平均值而求出(参照图3)。另外,纤维状粒子的长轴长度l表示上述的电子图像中的纤维状粒子的长度达到最大的位置时的长度,短轴长度s表示在与长轴长度l的方向正交的方向上的长度达到最大的位置时的长度。纤维状粒子的分散指数s如下求出:使用上述电子图像的第一截面组织的滑动面侧区域和第二截面组织的界面侧区域的拍摄图像,测定长轴长度在20μm以上的各纤维状粒子的与滑动面平行的方向上的长度x1、和与滑动面垂直的方向上的长度y1,算出以上各长度的比x1/y1的平均值(参照图4)。另外,纤维状粒子的分散指数s越接近0,则表示纤维状粒子以长轴方向在与滑动面垂直的方向上取向的方式分散,当分散指数s超过5而越大时,表示以长轴方向在与滑动面平行的方向上取向的方式分散。实施例如下所述制造了本发明的具有里衬金属层和滑动层的滑动构件的实施例1~12和比较例21~28。实施例和比较例的各滑动构件的滑动层的组成如表1所示。[表1-1]表1[表1-2]表1中示出的实施例1~12和比较例21~28中的纤维状粒子的原材料使用了平均粒径为7~35μm、平均长宽比(长轴长度/短轴长度)为5~100的粒子。作为实施例1~12和比较例21~28中的合成树脂的原材料,使用了peek(聚醚醚酮)粒子或pf(酚醛树脂)粒子。这些粒子使用平均粒径是作为原材料的纤维状粒子的平均粒径的125%的粒子。实施例5~9的固体润滑剂(mos2、gr)的原材料粒子使用平均粒径是纤维状粒子原材料的平均粒径的30%的粒子,填充材料(caf2)的原材料粒子使用平均粒径是纤维状粒子的平均粒径的25%的粒子。比较例26的交联促进剂的原材料使用了平均粒径是纤维状粒子的平均粒径的25%的粒子。以表1示出的组成比率称量上述的原材料,将该组合物预先颗粒化。将该颗粒投入熔融混炼机,依次通过供给模具、片成形模具、冷却辊,制作了树脂组合物片。另外,在实施例1~9、11、12和比较例21~25、27、28中,将熔融混炼机的加热温度设定为350~390℃,在实施例10中将加热温度设定为230~250℃。此外,关于冷却辊的温度,实施例1~12和比较例21~24中将上侧冷却辊的温度设定为180℃、将下侧冷却辊的温度设定为130℃,比较例25、27中设定为相同的温度,比较例28中将上侧冷却辊的温度设定为200℃、将下侧冷却辊的温度设定为100℃。此外,比较例26中,根据现有技术文献4、通过注塑成形制作了树脂组合物片。接着,在使树脂组合物片覆盖在fe合金制的里衬金属层的一侧表面上之后,加工成部分圆环形状,接着以使里衬金属层上的组合物达到规定的厚度的条件进行了切削加工。另外,实施例1~9、11、12和比较例21~28的里衬金属层使用了fe合金,实施例10中使用了在fe合金的表面具有cu合金的多孔质烧结部的材料。实施例1~6、10~12和比较例27的滑动构件中,以树脂组合物片和部分圆环形状的中心轴线相对于树脂组合物片在成形工序中的拉出辊处的拉出方向呈平行的方式,将树脂组合物片切割成规定的尺寸后,覆盖在里衬金属上(相当于上述实施方式1),实施例7~9和比较例21~25、28的滑动构件中,以部分圆环形状的中心轴线相对于树脂组合物片在成形工序中的拉出辊处的拉出方向呈正交的方式,将树脂组合物片切割成规定的尺寸后,覆盖在里衬金属上(相当于上述实施方式2)。制作的实施例1~12和比较例21~28的滑动构件的滑动层的厚度为3mm,里衬金属层的厚度为10mm。另外,在实施例1~12和比较例21~25、27、28中,对一侧的表面部进行切削,将厚度制成3mm。对于制作的实施例和比较例的各滑动构件,根据上述说明的测定方法,对第一截面组织和第二截面组织,测定分别分散于滑动面侧区域和界面侧区域的纤维状粒子的平均粒径,将其结果示于表1的“平均粒径”栏中。此外,测定上述说明的第一截面组织的滑动面侧区域、第二截面组织的界面侧区域中的“长轴长度在20μm以上的纤维状粒子”的平均长宽比(a),将其结果示于表1的“平均长宽比(a)”栏中。此外,根据上述说明的测定方法,测定在第一截面组织的滑动面侧区域和第二截面组织的界面侧区域中分散的“长轴长度在20μm以上的纤维状粒子”的分散指数(s),将其结果示于表1的“分散指数(s)”栏中。此外,测定上述说明的在第一截面组织的滑动面侧区域和第二截面组织的界面侧区域中分散的长轴长度在20μm以上的纤维状粒子的体积相对于纤维状粒子的总体积的比率,将其结果示于“体积比率”栏中。此外,将界面侧区域的厚度与滑动层厚度的比率示于“界面侧区域的厚度比率(%)”中。将多个成形为部分圆环形状的滑动构件组合而制成圆环形状,在表2示出的条件下进行了滑动试验。该条件再现了在大型轴承装置的运转停止时,油的供给不充分、轴构件旋转一定时间的滑动状态。将各实施例和各比较例的滑动试验后的滑动层的磨耗量示于表1的“磨耗量(μm)”栏中。此外,将滑动试验后的试验片沿着与滑动构件的中心轴线平行、且与滑动面垂直的方向切断,用光学显微镜确认在滑动层的内部有无产生“裂纹”。在表1的“内部裂纹”栏中,将确认到内部的“裂纹”的情况表示为“有”,将没有确认到内部的“裂纹”的情况表示为“无”。此外,用光学显微镜确认了在滑动层和里衬金属的界面是否发生“剪切”。在表1的“界面的剪切”栏中,将确认到界面的“剪切”的情况表示为“有”,将没有确认到界面的“剪切”的情况表示为“无”。[表2]试验机推力滑动试验机负荷70mpa转速150rpm运转时间40min油vc32给油量10cc//min给油温度60℃对应轴suj2对应轴粗糙度1.5ra根据表1示出的结果可知,实施例1~12与比较例21~24相比,滑动试验后的滑动层的磨耗量减少。此外,实施例4~9中,纤维状粒子5的平均长宽比(a)为5~10,磨耗量特别少。第一截面组织中的滑动面侧区域的“长轴长度在20μm以上的”纤维状粒子5和第二截面组织中的界面侧区域的“长轴长度在20μm以上的”纤维状粒子5的体积比率在30%以上的实施例4~9与体积比率小于30%的实施例1~3、11、12相比磨耗量少,认为其原因是如上述说明的滑动层的强度(变形阻力)提高了。此外,在实施例中,在滑动试验后的滑动层的内部没有产生裂纹和没有发生界面的剪切,认为这也是如上说明的由于滑动面侧区域和界面侧区域内的纤维状粒子的取向引起的。另外,除这里示出的实施例之外,即使对相对于滑动部旁边的中心轴线沿片的拉出方向倾斜地切割出滑动构件的试样,在实施同样的试验时,结果显示出同样的效果。相对于此,如比较例25、27所示,滑动层中所含的纤维状粒子在滑动面侧区域、界面侧区域的各区域中取向相同(相对于滑动面平行地取向)的情况下,认为施加至滑动层表面的负荷传递到与里衬金属层的界面,在界面发生了剪切。比较例21中,滑动层的滑动面侧区域和界面侧区域中所含的纤维状粒子的平均粒径小于5μm,所以提高滑动层的强度(变形阻力)的效果变低,所以认为滑动层的磨耗量增多,而且在滑动层和里衬金属的界面处发生了剪切。比较例22中,滑动层的滑动面侧区域和界面侧区域中所含的纤维状粒子的平均粒径为较大的30μm,所以在对滑动层施加来自轴构件的负荷时,纤维状粒子自身容易发生剪切,发生纤维状粒子的脱落,所以认为滑动层的磨耗量增多,而且在滑动层和里衬金属的界面处发生了剪切。比较例23中,滑动层的滑动面侧区域和界面侧区域中所含的纤维状粒子的体积小于10%,所以认为滑动层的强度(变形阻力)小,滑动层的磨耗量增多,而且在滑动层和里衬金属的界面处发生了剪切。比较例24中,滑动层的滑动面侧区域中所含的纤维状粒子的体积超过35%,所以认为滑动层变脆、滑动层的磨耗量增多、产生了滑动面的裂纹,而且在滑动层和里衬金属的界面处发生了剪切。比较例25中,由于将制作树脂组合物片时的上侧冷却辊和下侧冷却辊的温度设定为相同,所以滑动层中所含的纤维状粒子不存在滑动面侧区域、界面侧区域的区别,整体上与滑动层的滑动面大致平行地取向,所以认为负荷传递到里衬金属层的界面,在界面处发生了剪切。比较例26中,虽然通过注塑成形制作了树脂组合物片,但滑动层中所含的纤维状粒子的分散指数在滑动层的整体范围内为无取向,因此认为在从轴构件施加了负荷的情况下,在滑动层的内部产生了裂纹。比较例27中,滑动层中所含的纤维状粒子不存在滑动面侧区域、界面侧区域的区别,整体上沿着与滑动层的滑动面平行的方向取向,所以认为负荷传递到里衬金属层的界面,在滑动层和里衬金属的界面处发生了剪切。比较例28中,通过将上侧冷却辊温度和下侧辊冷却温度的差设得较大,界面侧区域较小、为小于15%(10%),所以认为施加到滑动层的负荷传递至里衬金属的界面,在滑动层和里衬金属的界面处发生了剪切。当前第1页12