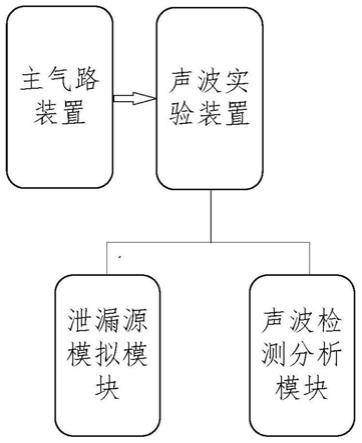
1.本发明涉及地下管廊安全监测技术领域,尤其涉及一种管廊燃气管道泄漏的实验系统及方法。
背景技术:2.地下综合管廊施工场地狭小且施工较为复杂,普遍存在的地下管道的检查,维护,保养等问题亟待解决。由于燃气属于特殊的一类传输介质,《建筑设计防火规范》中规定,天然气的火灾特性为甲类,爆炸极限很低,属于易燃易爆危险气体,极易引发爆炸、火灾等危害城市公共安全的恶性事件,造成不良影响。
3.燃气管道入综合管廊后,燃气管道在铺设以及使用过程中,燃气管道因施工、锈蚀、人为破坏等原因造成燃气泄漏,则会有更多制约检修的因素存在。一种是燃气管道泄漏逸出的有毒气体,检修和维护人员在综合管廊内排查检修时,可能会出现中毒的情况。另一种危害,由于综合管廊中电缆的存在,可能会出现火花,燃气与空气混合的达到一定程度时,遇到电火花时,会着火引起爆炸,对公共安全造成极大的伤害。
4.泄漏的燃气在受限空间内与空气混合达到爆炸极限后极易引发爆炸,造成不良影响。如果在管道泄漏早期,能够及时发现管道泄漏位置,并进行处理,可以最大程度的减小损失和影响。特别是,在城市化高速发展的今天,城市管线探测的环境越来越苛刻。
技术实现要素:5.基于现有技术的上述情况,本发明的目的在于提供一种管廊燃气管道泄漏的实验系统及方法,通过搭建廊燃气管道泄漏的实验系统,实现了对地下综合管廊燃气管道燃气泄漏过程的物理模拟,以对管廊燃气管道泄漏的各项参数进行精确分析。
6.为达到上述目的,根据本发明的一个方面,提供了一种管廊燃气管道泄漏的实验系统,包括主气路装置和声波实验装置;其中,
7.所述主气路装置对管廊燃气管道的结构进行模拟;
8.所述声波实验装置与所述主气路装置连接,在主气路装置模拟出的管廊燃气管道中,模拟燃气泄漏过程,并对燃气泄漏向泄露转化过程的声波进行监测和分析。
9.进一步的,所述主气路装置包括压缩机、冷干机、过滤器、储气罐、若干阀门、若干数据监测传感器、以及管道。
10.进一步的,所述主气路装置中,气路分流为4路,分别为架空钢管道、架空pe管道、埋土钢管道、埋土pe管道供气。
11.进一步的,所述若干数据监测传感器包括:声波监测传感器、温度传感器、超压传感器、以及压力传感器。
12.进一步的,所述声波实验装置包括泄漏源模拟模块和声波检测分析模块。
13.进一步的,所述泄漏源模拟模块通过改变泄漏源的各项参数以及管道的各项参数,以模拟不同工况。
14.进一步的,所述声波检测分析模块,检测不同工况下燃气泄漏压力和气流流速随速度的变化规律。
15.进一步的,所述声波检测分析模块,对管道燃气泄漏过程的各声学物理参量进行对比分析,得到声波信号在时域、频域和空域的分布特征。
16.根据本发明的另一个方面,提供了一种采用如本发明第一个方面所述的管廊燃气管道泄漏实验系统进行实验的方法,包括步骤:
17.对管廊燃气管道的结构进行模拟;
18.在所模拟出的管廊燃气管道中,模拟燃气泄漏过程;
19.对燃气泄漏向泄露转化过程的声波进行检测和分析。
20.进一步的,所述检测和分析包括检测不同工况下燃气泄漏压力和气流流速随速度的变化规律,以及对管道燃气泄漏过程的各声学物理参量进行对比分析,得到声波信号在时域、频域和空域的分布特征。
21.综上所述,本发明提供了一种管廊燃气管道泄漏的实验系统及方法,通过搭建管廊燃气管道泄漏的实验系统,以对管廊燃气管道的结构、以及燃气泄漏过程进行模拟,并对燃气泄漏向泄露转化过程的声波进行检测和分析,检测不同工况下燃气泄漏压力和气流流速随速度的变化规律,以及对管道燃气泄漏过程的各声学物理参量进行对比分析,得到声波信号在时域、频域和空域的分布特征,分析燃气管道泄漏前后空气介质中的声场和温度场特征,从而得到判别泄漏场源位置的敏感参数,总结出泄漏点的判识标准,以提高溯源定位的识别率和精度。
附图说明
22.图1是本发明主气路装置的布局示意图;
23.图2是本发明管廊燃气管道泄漏实验系统的构成框图;
24.图3是本发明管廊燃气管道泄漏实验系统的布置示意图;
25.图4是三维燃气舱模型示意图;
26.图5是声发射波形傅立叶变换过程图;
27.图6是管廊燃气管道泄漏实验系统的实验方法的实施流程图。
具体实施方式
28.为使本发明的目的、技术方案和优点更加清楚明了,下面结合具体实施方式并参照附图,对本发明进一步详细说明。应该理解,这些描述只是示例性的,而并非要限制本发明的范围。此外,在以下说明中,省略了对公知结构和技术的描述,以避免不必要地混淆本发明的概念。
29.下面结合附图对本发明的技术方案进行详细说明。根据本发明的一个实施例,提供了一种管廊燃气管道泄漏的实验系统,在搭建该实验系统之前,在实验室内进行燃气管材强度极限等基本力学参数测试,掌握燃气管道在附加外载荷非协调变形、腐蚀及初始细微缺陷作用下的破坏特征,分析管道失效模式,揭示城市管廊管道燃气泄漏通道形成机理,为实验系统的搭建提供基础。该实验系统的构成框图如图2所示,包括主气路装置和声波实验装置。其中,主气路装置对管廊燃气管道的结构进行模拟,主气路装置的布局示意图如图
1所示,主气路装置包括压缩机、冷干机、过滤器、储气罐、若干阀门、若干数据监测传感器、以及管道,过滤器的进出口管道均设置球阀。气体经压缩机加压,通过冷干机和过滤器除去水分和油脂,流出至缓冲储气罐。气体从缓冲罐流出至测试管段,阀门及质量流量计用来调节气体流量。气体从测试管段流出经过质量流量计及阀门流入高压罐随后通过减压阀放空。
30.在该主气路装置中,气路分流为4路,分别为架空钢管道、架空pe管道、埋土钢管道、埋土pe管道供气。其中若干数据监测传感器包括有温度传感器、超压传感器以及压力传感器。其中,通过在回路中设置储气罐二级储能,使管道中的压力基本保持平衡,实现模型中气路的独立控制。通过数据监测传感器实现对管道内气体参数(例如流量、压力、温度、超压等)的实时采集,便于控制实验参数。本实施例提供的该实验系统能够实现便捷更改泄漏点物理形态,设置声波传感器置入系统,实现纵向与横向的阵列布置。图3示出了本发明管廊燃气管道泄漏实验系统中传感器的布置示意图。在管道泄漏点右侧,距泄漏点0.1米处纵向布置多个压力传感器,例如可以为4个,用于监测泄露过程中的压力变化;在管道泄漏点左侧0.1米处,纵向布置多个超压传感器及温度传感器,例如为4个,用以监测超压及温度的变化。声波传感器置于测试管段设备的顶部,用于监测泄漏过程中声波参量的变化。
31.图4示出了燃气舱模型示意图,对地下综合管廊燃气舱内天然气泄漏扩散进行模拟,包括通过调研地下综合管廊燃气管道布置、管道直径、长度、压力等参数,在实验室建立管廊燃气管道泄漏的实验系统,泄漏口均为竖直向上喷射泄漏,机械进风口、排风口分别设置在实验系统的两端。
32.声波实验装置与所述主气路装置连接,在主气路装置模拟出的管廊燃气管道中,模拟燃气泄漏过程,并对燃气泄漏向泄露转化过程的声波进行检测和分析。声波实验装置包括泄漏源模拟模块和声波检测分析模块。泄漏源模拟模块以不同孔径的穿孔螺母为泄漏源,安装在管道指定位置,以实现对单点或多点的燃气泄漏模拟。通过开展系列实验,测试分析不同类型传感器接收到的信号特征,确定适合的频率范围,优化实验参数。通过改变泄漏速度、管道压力、泄漏源物理形态(例如圆孔、扁孔等)等,实现不同类型泄漏裂纹、不同工况的模拟,对比分析不同条件下声波参量的变化规律。声波检测模块对管道燃气泄漏过程的声波能量、撞击、幅度、振铃数等声学物理参量进行对比分析,得到声波信号在时域和频域的分布特征。研究单纯形算法在误差空间中的转换形式的特征,分析发散问题的内在机制,将l1范数和单纯形算法相结合,建立基于l1范数的单纯形微孔泄漏定位方法。具体来说,可以采用声发射监测仪进行声波检测,获得了声发射信号在时域、频域、空域的特征,以及管道破裂过程声发射信号的频域分析。采用快速傅里叶变换方法,对声发射波形数据进行变换,获得该波形数据的二维频谱图,如图5所示,其功率值最大处对应的频率为主频值,次之则为次主频值。
33.根据本发明的另一个实施例,提供了一种管廊燃气管道泄漏实验系统的实验方法,该方法的实施流程图如图6所示,包括步骤:
34.对管廊燃气管道的结构进行模拟;
35.在所模拟出的管廊燃气管道中,模拟燃气泄漏过程;
36.对燃气泄漏向泄露转化过程的声波进行检测和分析。
37.其中,所述检测和分析包括检测不同工况下气流流速随速度的变化规律,以及对
管道燃气泄漏过程的各声学物理参量进行对比分析,得到声波信号在时域、频域和空域的分布特征。
38.综上所述,本发明涉及一种管廊燃气管道泄漏的实验系统及方法,通过搭建管廊燃气管道泄漏的实验系统,以对管廊燃气管道的结构、以及燃气泄漏过程进行模拟,并对燃气泄漏向泄露转化过程的声波进行检测和分析,检测不同工况下气流流速随速度的变化规律,以及对管道燃气泄漏过程的各声学物理参量进行对比分析,得到声波信号在时域、频域和空域的分布特征,分析了燃气管道泄漏前后空气介质中的声场和温度场特征,从而得到判别泄漏场源位置的敏感参数,总结出泄漏点的判识标准,以提高溯源定位的识别率和精度。
39.应当理解的是,本发明的上述具体实施方式仅仅用于示例性说明或解释本发明的原理,而不构成对本发明的限制。因此,在不偏离本发明的精神和范围的情况下所做的任何修改、等同替换、改进等,均应包含在本发明的保护范围之内。此外,本发明所附权利要求旨在涵盖落入所附权利要求范围和边界、或者这种范围和边界的等同形式内的全部变化和修改例。