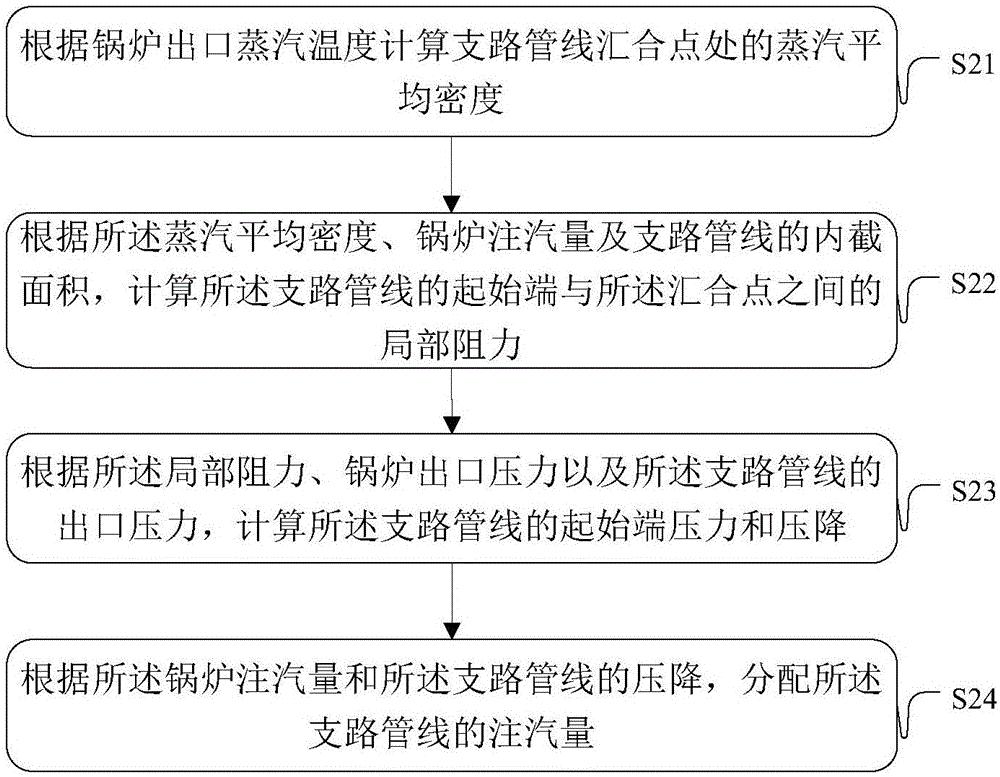
本发明涉及油藏开采
技术领域:
,尤其涉及一种确定注汽管热损失的方法及装置。
背景技术:
:稠油是指地层条件下粘度大于50mp·s(毫帕·秒),或油层温度下脱气原油粘度为1000至10000mp·s的高粘度重质原油。由于稠油粘度较大,因此流动性能较差,甚至在某些油层条件下不能流动,给稠油的开采带来了困难。在石油开采过程中,由于稠油具有高粘度和高凝固点等特性,在储层和井筒中流动性差,采用常规开采方式的采收率较低,一般无法保证正常的经济产量。为了保证合理的采收率,往往通过降低原油粘度的方式进行开采。由于稠油的粘度对温度非常敏感,随着温度增加,粘度极大降低,流动也阻力减小,因此目前常用的开采稠油的方式主要有注蒸汽热采技术,包括蒸汽吞吐、蒸汽驱、SAGD(蒸汽辅助重力泄油技术)。具体的,所述注蒸汽热采技术主要是通过将锅炉产生的高温、高压湿饱和蒸汽,经过地面管线传输至井口,再由井口通过井筒传输后注入稠油油层,以达到降低稠油粘度的目的。目前蒸汽的注汽方式主要有一炉一注、多炉一注和一炉多注等,对应的注汽管网结构包括单一注汽管线、星状管网、树枝状管网等。在计算地面管线热损失的过程中,目前只有一炉一注单一管线的计算方法,即从注汽锅炉到井口只有一条管线,管线不存在分支及汇入情况。但是大多数注汽开采是采用星状或树枝状的管网结构,目前单一注汽管线热损失计算方法已不再适用星状或树枝状的管网结构。技术实现要素:本申请的目的在于提供一种确定注汽管热损失的方法及装置,可以用于进一步提高热损失计算结果的准确性。为了实现上述目的,本发明提供了一种确定注汽管热损失的方法及装置,所述方法及装置具体是这样实现的:一种确定注汽管热损失的方法,所述方法包括:根据锅炉出口蒸汽温度、压力、干度、锅炉注汽量以及支路管线的出口压力和内截面积,计算所述支路管线的起始端压力、注汽量;按照预设步长对所述支路管线进行分段,以所述支路管线的起始端压力、注汽量为起始条件,通过对蒸汽压力、温度、干度进行迭代计算,依次分段确定单位预设步长的支路管线的热损失。一种确定注汽管热损失的装置,所述装置包括:注汽量分配单元,用于根据锅炉出口蒸汽温度、压力、干度、锅炉注汽量以及支路管线的出口压力和内截面积,计算所述支路管线的起始端压力、注汽量;热损失计算单元,用于按照预设步长对所述支路管线进行分段,以所述支路管线的起始端压力、注汽量为起始条件,通过对蒸汽压力、温度、干度进行迭代计算,依次分段确定单位预设步长的支路管线的热损失。本发明提供的确定注汽管热损失的方法及装置,可以根据锅炉出口蒸汽温度、压力、干度等已知参数值,对锅炉注汽量进行均衡分配,使得每个支路管线获取合理的注汽量。按照预设步长对所述支路管线进行分段,并以所述支路管线的起始端压力、注汽量为起始条件,通过对蒸汽压力、温度、干度进行迭代计算,依次分段确定单位预设步长的支路管线的热损失。分段计算所述支路管线的热损失,可以使得热损失计算结果更加准确,通过对参数蒸汽压力、温度、干度进行三次迭代计算,进一步提高热损失计算结果的准确性。附图说明为了更清楚地说明本申请实施例或现有技术中的技术方案,下面将对实施例或现有技术描述中所需要使用的附图作简单地介绍,显而易见地,下面描述中的附图仅仅是本申请中记载的一些实施例,对于本领域普通技术人员来讲,在不付出创造性劳动性的前提下,还可以根据这些附图获得其他的附图。图1是本发明提供的确定注汽管热损失方法的一种实施例的流程图;图2是本发明提供的计算所述支路管线注汽量方法的一种实施例的流程图;图3是本发明提供的计算支路管线汇合点处蒸汽平均密度方法的一种实施例的流程图;图4是本发明提供的计算单位支路管线热损失量方法的一种实施例的方法流程图;图5是本发明提供的计算单位支路管线的压力降方法的一种实施例的方法流程图;图6是本发明提供的井口压力迭代计算方法的一种实施例的方法流程图;图7是本发明提供的确定注汽管热损失装置的一种实施例的模块结构示意图;图8是本发明提供的注汽量分配单元的一种实施例的模块结构示意图;图9是本发明提供的密度计算单元的一种实施例的模块结构示意图;图10是本发明提供的热损失计算单元的一种实施例的模块结构示意图;图11是本发明提供的参数预置单元的一种实施例的模块结构示意图;图12是本发明提供的确定注汽管热损失装置的另一种实施例的模块结构示意图。具体实施方式为了使本
技术领域:
的人员更好地理解本申请中的技术方案,下面将结合本申请实施例中的附图,对本申请实施例中的技术方案进行清楚、完整地描述,显然,所描述的实施例仅仅是本申请一部分实施例,而不是全部的实施例。基于本申请中的实施例,本领域普通技术人员在没有做出创造性劳动前提下所获得的所有其他实施例,都应当属于本申请保护的范围。图1是本发明提供的确定注汽管热损失方法的一种实施例的方法流程图,如图1所示,所述方法可以包括:S1:根据锅炉出口蒸汽温度、压力、干度、锅炉注汽量以及支路管线的出口压力和内截面积,计算所述支路管线的起始端压力、注汽量。在注蒸汽热采稠油的过程中,蒸汽的压力、温度、干度等热力参数会由于地面管线输送过程中产生的热损失和压力损失而发生变化。其中热损失的大小直接影响了注入井筒底部的蒸汽的热力状态,从而决定注蒸汽热采效果的好坏。所述干度是指每千克湿蒸汽中含有干蒸汽的质量百分数的大小,对于注蒸汽热采而言,干度越大,越有利于提高注蒸汽热采的效果。在注蒸汽热采时,需要计算地面管线内蒸汽的热力参数:压力、温度、干度、热损失,基于计算出的热力参数,对地面管线进行改进,以最大限度地减小蒸汽运移过程中的热量损失,提高蒸汽干度,从而提高注蒸汽开采稠油的效果。本实施例中的稠油开采注汽结构可以为呈星状管网分布的一炉多注结构,在该结构中,锅炉出口的蒸汽注入各个支路管线中。所述支路管线与钻井相连接,在钻井井口可以测量得到支路管线的出口压力。本发明提供一种计算所述支路管线注汽量方法的一种实施例,图2是本发明提供的计算所述支路管线注汽量方法的一种实施例的方法流程图,如图2所示,所述根据锅炉出口蒸汽温度、锅炉出口蒸汽压力、锅炉注汽量以及支路管线的内截面积,计算所述支路管线的注汽量可以包括:S21:根据锅炉出口蒸汽温度计算支路管线汇合点处的蒸汽平均密度。本实施例中的锅炉出口蒸汽温度、锅炉出口蒸汽压力、锅炉注汽量以及支路管线的内截面积等参数值均可以直接测得。所述支路管线汇合点为所述锅炉的出口处,本实施例中的蒸汽平均密度为所述锅炉出口处的蒸汽的平均密度。本发明提供一种计算支路管线汇合点处蒸汽平均密度方法的一种实施例,图3是本发明提供的计算支路管线汇合点处蒸汽平均密度方法的一种实施例的方法流程图,如图3所示,所述根据锅炉出口蒸汽温度计算支路管线汇合点处的蒸汽平均密度包括:S31:根据锅炉出口蒸汽温度计算支路管线汇合点处的蒸汽液相密度、蒸汽汽相密度、蒸汽液相粘度以及蒸汽汽相粘度。在本发明的一个实施例中,所述蒸汽液相密度、蒸汽汽相密度、蒸汽液相粘度以及蒸汽汽相粘度的计算公式可以分别为:ρl=(0.9967-4.615×10-5Tb-3.063×10-6Tb2)×103(1)Zg=1.012-4.461×10-4Tb+2.98×10-6Tb2-1.663×10-8Tb3(3)μg=(0.36Tb+88.37)×10-4(5)其中,ρl为蒸汽液相密度,单位为kg/m3,ρg为蒸汽液相密度,单位为kg/m3,Zg为气体压缩因子,Tb为锅炉出口温度,μl为蒸汽液相粘度,单位为mp·s,μg为蒸汽汽相粘度,单位为mp·s。S32:根据所述支路管线汇合点处的蒸汽液相密度、蒸汽汽相密度以及所述锅炉出口干度计算所述支路管线汇合点处的体积含气率。在本发明的一个实施例中,所述汇合点处的体积含气率的计算公式可以为:其中,Hg为所述汇合点处的体积含气率,xb为锅炉出口干度,ρl为蒸汽液相密度,单位为kg/m3,ρg为蒸汽液相密度,单位为kg/m3。S33:根据所述体积含气率计算所述支路管线汇合点处的蒸汽平均密度。在本发明的一个实施例中,所述支路管线汇合点处的蒸汽平均密度的计算公式可以为:ρm=Hgρg+(1-Hg)ρl(7)其中,ρm为所述支路管线汇合点处的蒸汽平均密度,Hg为所述汇合点处的体积含气率,ρl为蒸汽液相密度,单位为kg/m3,ρg为蒸汽液相密度,单位为kg/m3。S22:根据所述蒸汽平均密度、锅炉注汽量及支路管线的内截面积,计算所述支路管线的起始端与所述汇合点之间的局部阻力。在本发明的一个实施例中,可以通过所述支路管线平均流速计算所述支路管线的起始端与所述汇合点之间的局部阻力,其中,所述支路管线平均流速的计算公式可以为:其中,vm为所述支路管线的平均流速,单位为m/s,G为锅炉注汽量,A为所述支路管线的内截面积,A=πri2,其中ri为所述支路管线的内截面半径。在本发明的一个实施例中,所述支路管线的起始端与所述汇合点之间的局部阻力的计算公式可以为:其中,△pb为所述支路管线的起始端与所述汇合点之间的局部阻力,△pw为液体单向流的局部压强损失,单位为Pa,B为中间参数,X为马蒂内利参数,△pw、B、X的计算公式可以分别为:其中,ζ为局部阻力系数,vm为所述支路管线的平均流速,g为重力加速度,xb为锅炉出口干度,ρl为蒸汽液相密度,单位为kg/m3,ρg为蒸汽液相密度,单位为kg/m3,μl为蒸汽液相粘度,单位为mp·s,μg为蒸汽汽相粘度,单位为mp·s。S23:根据所述局部阻力、锅炉出口压力以及所述支路管线的出口压力,计算所述支路管线的起始端压力和压降。本实施例中,可以根据所述支路管线的起始端与所述汇合点之间的局部阻力、锅炉出口压力以及所述支路管线的出口压力,计算所述支路管线的起始端压力和压降,具体的,在本发明的一个实施例中,所述支路管线的起始端压力的计算公式为:pstart=pb-Δpb(13)其中,pstart为所述支路管线的起始端压力,pb为锅炉出口压力,△pb为所述支路管线的起始端与所述汇合点之间的局部阻力。根据所述支路管线的起始端压力,可以计算所述支路管线的压降,所述压降的计算公式可以为:Δp=pstart-p(14)其中,Δp为所述支路管线的压降,p为所述支路管线的出口压力。S24:根据所述锅炉注汽量和所述支路管线的压降,分配所述支路管线的注汽量。本实施例中,可以根据所述支路管线的压降,可以计算得到所述支路管线的注汽量,所述注汽量的计算公式可以为:其中,Gj为所述支路管线的注汽量,其中j为所述支路管线在所有支路管线中的编号,Δpj为所述支路管线的压降,G为锅炉注汽量,N为所有支路管线的个数。本实施例中,可以根据锅炉出口蒸汽温度、压力、干度、锅炉注汽量等已知参数数据对锅炉注汽量进行合理分配,使得各个支路管线获取与其出口压力、管线尺寸相匹配的注汽量,可以降低传输过程中的热损失。S2:按照预设步长对所述支路管线进行分段,以所述支路管线的起始端压力、注汽量为起始条件,通过对蒸汽压力、温度、干度进行迭代计算,依次分段确定单位预设步长的支路管线的热损失。本实施例中,可以按照预设步长对所述支路管线进行分段,以所述支路管线的起始端压力、注汽量为起始条件,通过对蒸汽压力、温度、干度进行迭代计算,依次分段确定单位预设步长的支路管线的热损失。所述支路管线的起始端压力、注汽量可以在S1中计算得到。在本申请的一个实施例中,提供一种计算单位支路管线热损失量的方法,图4是本发明提供的计算单位支路管线热损失量方法的一种实施例的方法流程图,如图4所示,所述按照预设步长对所述支路管线进行分段,以所述支路管线的起始端压力、干度、注汽量为起始条件,通过对蒸汽压力、温度、干度进行迭代计算,依次分段确定单位预设步长的所述支路管线的热损失可以包括:S41:从所述支路管线的起始端获取预设步长的单位支路管线,设置所述单位支路管线的预设干度降、预设外壁温度、预设压力降,根据所述支路管线的起始端压力、干度、注汽量,计算所述单位支路管线的压力降。本实施例中,可以设置所述支路管线的预设步长为Δz,按照步长Δz对所述支路管线进行分段,得到若干个单位支路管线,本实施例从最靠近锅炉的单位支路管线开始,逐个向井口方向顺延的单位支路管线进行处理。本发明提供一种计算所述单位支路管线的压力降的方法,图5是本发明提供的计算单位支路管线的压力降方法的一种实施例的方法流程图,如图5所示,所述计算所述单位支路管线的压力降可以包括:S51:根据所述支路管线的起始端压力、干度、注汽量计算所述单位支路管线的蒸汽平均密度、摩擦系数。本实施例中,采用迭代的计算方法获取所述单位支路管线的压力降,预先设置所述单位支路管线的预设干度降为Δxi、预设外壁温度Tw、预设压力降△pi,其中i为所述单位支路管线在所述支路管线中的编号。在本发明的一个实施例中,所述单位支路管线的终端压力、温度、干度的计算公式可以分别为:pi=pi-1-△pi(16)Ti=195.94pi0.225-17.8(17)xi=xi-1-△xi(18)其中,pi,Ti,xi分别为所述单位支路管线的终端压力、温度、干度,pi-1,xi-1分别为所述单位支路管线的起始端压力、干度,当i=1时,pi-1,xi-1分别为所述支路管线的起始端压力、干度。计算所述单位支路管线的平均压力、温度、干度,所述公式可以为:pavi=(pi-1+pi)/2(19)Tavi=(Ti-1+Ti)/2(20)xavi=(xi-1+xi)/2(21)其中,pavi,Tavi,xavi分别为所述单位支路管线的平均压力、温度、干度。本实施例中,可以利用公式(1)-(7),将所述参数Tavi分别替换公式(1)-(5)中的Tb,将xavi分别替换公式(6)中的xb,计算得到所述单位支路管线的蒸汽平均密度ρ′m,并根据下述公式计算得到所述单位支路管线的平均粘度μ′m:μ′m=Hg′μ′g+(1-H′g)μ′l(22)其中,H′g为所述单位支路管线的平均体积含气率,μ′l为所述单位支路管线的平均蒸汽液相粘度,单位为mp·s,μ′g为所述单位支路管线的平均蒸汽汽相粘度,单位为mp·s。本实施例中,将公式(8)参数ρ′m替换成ρm,可以计算得到所述单位支路管线的平均流速v′m,根据所述单位支路管线的内截面半径ri、蒸汽平均流速v′m、蒸汽平均密度ρ′m、蒸汽平均粘度μ′m可以计算得到所述单位支路管线的雷诺数Re,计算公式为:本实施例中,根据所述单位支路管线的雷诺数Re,可以计算所述单位支路管线的摩擦系数,表1是管线雷诺数与摩擦系数计算公式关系对应表,表1中的Ra为已知参数管壁粗糙度,d为所述单位支路管线的内截面直径。表1管线雷诺数与摩擦系数计算公式关系对应表S52:计算所述单位支路管线在起始端压力、干度下的起始平均流速,在终端压力、干度下的终端平均流速。本实施中,利用公式(1)-(3)、(6)、(7)、(17)计算所述单位支路管线在起始端压力pi-1、干度xi-1下的起始平均流速vi-1,在终端压力pi、干度xi下的终端平均流速vi,具体计算过程在此不再赘述。S53:根据所述单位支路管线的蒸汽平均密度、摩擦系数、起始平均流速、终端平均流速,计算所述单位支路管线的压力降。本实施例中,根据所述单位支路管线的蒸汽平均密度ρ′m、摩擦系数fm、起始平均流速vi-1、终端平均流速vi,计算所述单位支路管线的压力降△pi',计算公式可以为:其中,K为常数,fm为摩擦系数,ρ′m为蒸汽平均密度,Δz为预设步长,vi-1为起始平均流速,vi为终端平均流速,ri为所述单位支路管线的内截面半径,g为重力加速度,θ为所述单位支路管线的倾角,Gj为所述支路管线的注汽量,A为所述单位支路管线的内截面面积。S42:当所述压力降与所述预设压力降之间的误差小于第一阈值时,根据所述预设外壁温度、空气温度以及所述单位支路的内、外截面半径,计算所述单位支路管线的外壁温度。计算所述单位支路管线的压力降△pi'与预设压力降△pi之间的误差,若所述误差大于等于第一阈值,重新设置所述预设压力降△pi的值,例如,可以设置△pi=△pi',返回至步骤S51,进行迭代计算。若所述阈值小于第一阈值,则进行温度迭代计算。具体地,可以根据所述预设外壁温度Tw、空气温度Ta、所述单位支路的内截面半径ri、外截面半径ro计算所述单位支路管线的单位长度上的热阻值,所述热阻值的计算公式可以为:其中,R1为对流层的对流换热热阻,R2为污垢层的对流换热热阻,R3为管壁热阻,R4为绝热层热阻,R5为低速气膜层热阻,hf为液膜层对流换热系数,单位为kcal/(m2·h·℃),hp为污垢层对流换热系数,单位为kcal/(m2·h·℃),ri、ro为所述单位支路的内、外截面半径,rins为绝热层的外半径,λp为管线的导热系数,单位为kcal/(h·m·℃),λins为绝热层的导热系数,单位为kcal/(h·m·℃),hfc为绝热层外表面上强迫对流热系数,单位为kcal/(m2·h·℃)。本实施例中,hfc=hfc'+hfc",即hfc由对流换热系数hfc'和辐射换热系数hfc"组成,计算公式分别为:其中,C为常数,λa为空气的导热系数,单位为kcal/(h·m·℃),Re为雷诺数,Re=νaDs/υa,νa为风速,单位为m/s,υa为空气的运动粘度,单位为m2/s,Ds为绝热层外径,单位为m,n的值可以根据雷诺值的大小进行选取,表2为雷诺数与常数C、n之间的对应关系表:表2雷诺数与常数C、n之间的对应关系表Re5-8080-5×1035×103-5×104>5×104C0.810.6250.1970.023n0.400.460.60.8其中,ε为管壁外黑度,Ta为空气温度,单位为℃,Tw为绝热层外壁温度,单位为℃。本实施例中,忽略所述对流层和污垢层的对流换热热阻R1和R2,则可以计算得到所述单位支路管线上的单位长度、单位时间的热损失q,单位为kcal/(h·m),计算公式为:另外,假设所述管线的绝热层外表面温度为Tw',那么,所述单位支路管线上的单位长度、单位时间的热损失q的计算公式还可以为:已知Ts、Ta、R3、R4、R5,根据公式(28)、(29),可以计算得到Tw'。S43:当所述外壁温度与所述预设外壁温度之间的误差小于第二阈值时,根据所述支路管线的起始端压力、所述预设压力降计算所述单位支路管线的干度降。本实施例中,计算所述绝热层外壁温度为Tw'与预设外壁温度Tw之间的误差,若所述误差大于等于第二阈值,重新设置所述外壁温度Tw的值,例如,可以设置Tw=Tw',返回至步骤S42,进行迭代计算。当所述外壁温度Tw'与所述预设外壁温度Tw之间的误差小于第二阈值时,根据所述支路管线的起始端压力、所述预设压力降计算所述单位支路管线的干度降。具体地,可以计算所述单位支路管线的饱和水、饱和蒸汽的热焓,在将所述饱和水、饱和蒸汽的热焓对蒸汽压力进行求导,具体公式可以为:hg=(12500+1.88Tavi-3.7×10-6Tavi3.2)/4.186(31)其中,hl、hg为饱和水、饱和蒸汽的热焓,单位为kcal/kg,Tavi为所述单位支路管线的平均温度。根据所述饱和水、饱和蒸汽的热焓计算所述单位支路管线的干度降,所述干度的计算公式可以为:C1=G(hg-hl)(35)需要说明的是,公式(35)-(37)中的G为所述支路管线的注汽量。S44:当所述干度降与所述预设干度降之间的误差小于第三阈值时,计算所述单位支路管线的热损失量。本实施例中,计算(xi-xi-1)与预设干度降Δxi之间的误差,若所述误差大于等于第三阈值,重新设置所述外壁温度Δxi的值,例如,可以设置Δxi=xi-xi-1,返回至步骤S2,进行迭代计算。当所述干度降与所述预设干度降之间的误差小于第三阈值时,计算所述单位支路管线的热损失量,所述热损失量Δqi的计算公式为:Δqi=qi-qi-1=q×△z×4.186/3600(38)其中,qi-1为所述单位支路管线上的起始端热损失,当i=1时,qi-1=0,q为所述单位支路管线上的单位长度、单位时间的热损失,△z为所述支路管线的步长,也是所述单位支路管线的长度。在本发明的一个实施例中,还可以进一步对所述热损失的计算过程进行迭代,本发明还提供一种井口压力迭代计算的方法,图6是本发明提供的井口压力迭代计算方法的一种实施例的方法流程图,如图6所示,所述方法可以包括:S61:计算所述支路管线的终端压力。按照预设步长将所述支路管线进行分成若干段单位支路管线,逐个计算各个单位支路的热损失以及单位支路管线的终端压力、干度、温度,计算公式为(16)-(18)。所述支路管线的终端压力为所述支路管线中最接近井口的单位支路管线的终端压力。S62:计算所述终端压力与实测井口压力之间的误差。S63:当所述误差小于第四阈值时,累加分段确定的单位预设步长的支路管线的热损失,生成所述支路管线的热损失。计算所述终端压力与实测井口压力之间的误差,当所述误差大于等于第四阈值时,可以设置返回至步骤S2,并设置当所述终端压力大于实测井口压力时,增加公式(24)中的K值,当所述终端压力小于实测井口压力时,减小公式(24)中的K值。当所述误差小于第四阈值时,累加分段确定的单位预设步长的支路管线的热损失,生成所述支路管线的热损失,所述热损失的计算公式为:其中,N为对所述支路管线按照步长划分的单位支路管线的段数。整个一炉多注的星状管网的热损失总量的计算公式为:其中,M为所述一炉多注的星状管网中的支路管线的个数。本发明提供的确定注汽管热损失的方法,可以根据锅炉出口蒸汽温度、压力、干度等已知参数值,对锅炉注汽量进行均衡分配,使得每个支路管线获取合理的注汽量。按照预设步长对所述支路管线进行分段,并以所述支路管线的起始端压力、注汽量为起始条件,通过对蒸汽压力、温度、干度进行迭代计算,依次分段确定单位预设步长的支路管线的热损失。分段计算所述支路管线的热损失,可以使得热损失计算结果更加准确,通过对参数蒸汽压力、温度、干度进行三次迭代计算,进一步提高热损失计算结果的准确性。本发明另一方面还提供一种确定注汽管热损失的装置,图7是本发明提供的确定注汽管热损失装置的一种实施例的模块结构示意图,结合附图7,该装置70包括:注汽量分配单元71,用于根据锅炉出口蒸汽温度、压力、干度、锅炉注汽量以及支路管线的出口压力和内截面积,计算所述支路管线的起始端压力、注汽量;热损失计算单元72,用于按照预设步长对所述支路管线进行分段,以所述支路管线的起始端压力、注汽量为起始条件,通过对蒸汽压力、温度、干度进行迭代计算,依次分段确定单位预设步长的支路管线的热损失。可选的,在本发明的一个实施例中,图8是本发明提供的注汽量分配单元的一种实施例的模块结构示意图,如图8所示,所述注汽量分配单元71可以包括:密度计算单元81,用于根据锅炉出口蒸汽温度计算支路管线汇合点处的蒸汽平均密度;局部阻力计算单元82,用于根据所述蒸汽平均密度、锅炉注汽量及支路管线的内截面积,计算所述支路管线的起始端与所述汇合点之间的局部阻力;压降计算单元83,用于根据所述局部阻力、锅炉出口压力以及所述支路管线的出口压力,计算所述支路管线的起始端压力和压降;注汽量计算单元84,用于根据所述锅炉注汽量和所述支路管线的压降,分配所述支路管线的注汽量。可选的,在本发明的一个实施例中,图9是本发明提供的密度计算单元的一种实施例的模块结构示意图,如图9所示,所述密度计算单元81可以包括:基本参数计算单元91,用于根据锅炉出口蒸汽温度计算支路管线汇合点处的蒸汽液相密度、蒸汽汽相密度、蒸汽液相粘度以及蒸汽汽相粘度;体积含气量计算单元92,用于根据所述支路管线汇合点处的蒸汽液相密度、蒸汽汽相密度以及所述锅炉出口干度计算所述支路管线汇合点处的体积含气率;平均密度计算单元93,用于根据所述体积含气率计算所述支路管线汇合点处的蒸汽平均密度。可选的,在本发明的一个实施例中,图10是本发明提供的热损失计算单元的一种实施例的模块结构示意图,如图10所示,所述热损失计算单元72可以包括:参数预置单元101,用于从所述支路管线的起始端获取预设步长的单位支路管线,设置所述单位支路管线的预设干度降、预设外壁温度、预设压力降,根据所述支路管线的起始端压力、干度、注汽量,计算所述单位支路管线的压力降;外壁温度计算单元102,用于当所述压力降与所述预设压力降之间的误差小于第一阈值时,根据所述预设外壁温度、空气温度以及所述单位支路的内、外截面半径,计算所述单位支路管线的外壁温度;干度降计算单元103,用于当所述外壁温度与所述预设外壁温度之间的误差小于第二阈值时,根据所述支路管线的起始端压力、所述预设压力降计算所述单位支路管线的干度降;单位热损失计算单元104,用于当所述干度降与所述预设干度降之间的误差小于第三阈值时,计算所述单位支路管线的热损失量。可选的,在本发明的一个实施例中,图11是本发明提供的参数预置单元的一种实施例的模块结构示意图,如图11所示,所述参数预置单元101可以包括:摩擦系数计算单元111,用于根据所述支路管线的起始端压力、干度、注汽量计算所述单位支路管线的蒸汽平均密度、摩擦系数;流速计算单元112,用于计算所述单位支路管线在起始端压力、干度下的起始平均流速,在终端压力、干度下的终端平均流速;压力降计算单元113,用于根据所述单位支路管线的蒸汽平均密度、摩擦系数、起始平均流速、终端平均流速,计算所述单位支路管线的压力降。可选的,在本发明的一个实施例中,图12是本发明提供的确定注汽管热损失装置的另一种实施例的模块结构示意图,结合附图12,该装置120还包括:终端压力计算单元121,用于计算所述支路管线的终端压力;误差计算单元122,用于计算所述终端压力与实测井口压力之间的误差;热损失总量计算单元123,用于当所述误差小于第四阈值时,累加分段确定的单位预设步长的支路管线的热损失,生成所述支路管线的热损失。本发明提供的确定注汽管热损失的装置,可以根据锅炉出口蒸汽温度、压力、干度等已知参数值,对锅炉注汽量进行均衡分配,使得每个支路管线获取合理的注汽量。按照预设步长对所述支路管线进行分段,并以所述支路管线的起始端压力、注汽量为起始条件,通过对蒸汽压力、温度、干度进行迭代计算,依次分段确定单位预设步长的支路管线的热损失。分段计算所述支路管线的热损失,可以使得热损失计算结果更加准确,通过对参数蒸汽压力、温度、干度进行三次迭代计算,进一步提高热损失计算结果的准确性。本说明书中的各个实施例均采用递进的方式描述,每个实施例重点说明的都是与其他实施例的不同之处,各个实施例之间相同相似的部分互相参见即可。尤其,对于系统实施例而言,由于其基本相似于方法实施例,所以描述的比较简单,相关之处参见方法实施例的部分说明即可。虽然通过实施例描绘了本申请,本领域普通技术人员知道,本申请有许多变形和变化而不脱离本申请的精神,希望所附的权利要求包括这些变形和变化而不脱离本申请的精神。虽然本申请提供了如实施例或流程图所述的方法操作步骤,但基于常规或者无创造性的劳动可以包括更多或者更少的操作步骤。实施例中列举的步骤顺序仅仅为众多步骤执行顺序中的一种方式,不代表唯一的执行顺序。在实际中的装置或客户端产品执行时,可以按照实施例或者附图所示的方法顺序执行或者并行执行(例如并行处理器或者多线程处理的环境)。上述实施例阐明的装置或模块,具体可以由计算机芯片或实体实现,或者由具有某种功能的产品来实现。为了描述的方便,描述以上装置时以功能分为各种模块分别描述。在实施本申请时可以把各模块的功能在同一个或多个软件和/或硬件中实现。当然,也可以将实现某功能的模块由多个子模块或子单元组合实现。本申请中所述的方法、装置或模块可以以计算机可读程序代码方式实现控制器按任何适当的方式实现,例如,控制器可以采取例如微处理器或处理器以及存储可由该(微)处理器执行的计算机可读程序代码(例如软件或固件)的计算机可读介质、逻辑门、开关、专用集成电路(ApplicationSpecificIntegratedCircuit,ASIC)、可编程逻辑控制器和嵌入微控制器的形式,控制器的例子包括但不限于以下微控制器:ARC625D、AtmelAT91SAM、MicrochipPIC18F26K20以及SiliconeLabsC8051F320,存储器控制器还可以被实现为存储器的控制逻辑的一部分。本领域技术人员也知道,除了以纯计算机可读程序代码方式实现控制器以外,完全可以通过将方法步骤进行逻辑编程来使得控制器以逻辑门、开关、专用集成电路、可编程逻辑控制器和嵌入微控制器等的形式来实现相同功能。因此这种控制器可以被认为是一种硬件部件,而对其内部包括的用于实现各种功能的装置也可以视为硬件部件内的结构。或者甚至,可以将用于实现各种功能的装置视为既可以是实现方法的软件模块又可以是硬件部件内的结构。当前第1页1 2 3