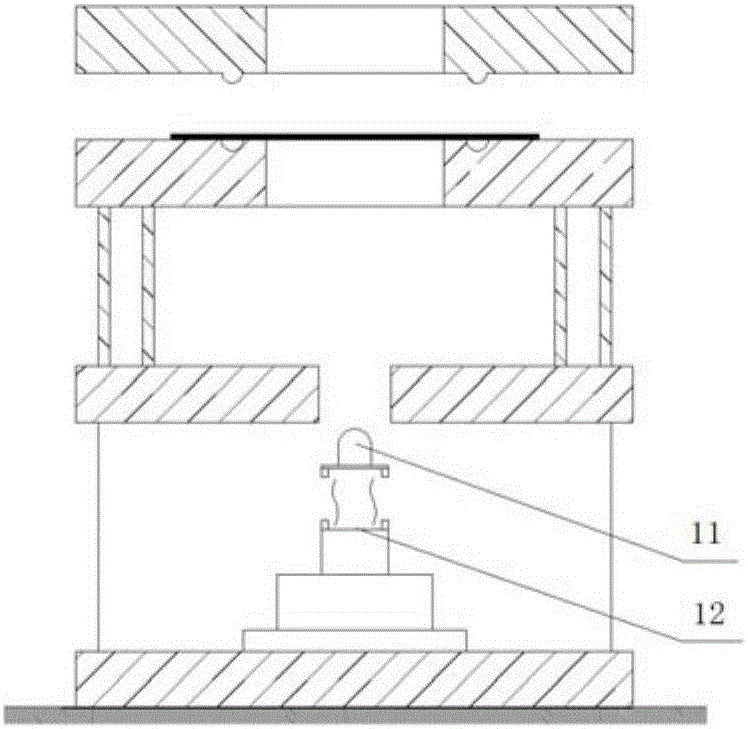
本实用新型属于金属板料成形加工技术领域,具体涉及一种获得复杂加载条件下成形极限图的试验装置。
背景技术:
:
成形极限图(Forming Limit Diagram,FLD),是板料在不同应变路径以及不同摩擦条件下的局部失稳时其极限应变e1、e2(工程应变)或ε1、ε2(真实应变)构成的条带形区域或曲线,该条形带或曲线将整个图形区域分成三部分:安全区、破裂区及临界区,FLD能全面反映板料在单向和双向拉应力作用下的局部成形极限,是对板料成形性能的一种定量描述,是对冲压工艺成败性的一种判断曲线,在板料实际冲压生产成形以及板料数值模拟分析两个方面都有其重要应用。
板料成形极限曲线FLD的测定方法通常有理论计算及试验获得两种方法。理论计算是基于屈服准则、塑性本构关系,以拉伸失稳准则进行解析的。基于板料塑性变形基本理论,计算需从板料初始变形状态考虑,即需考虑板料的初始屈服准则,包括各向同性屈服准则和各向异性屈服准则,其中还需考虑材料在变形过程中的应变强化规则以及它的后继屈服函数,继而分析板料的失稳状态。失稳主要表现为拉伸失稳,应用广泛的包括Swift分散性失稳理论和Hill提出的集中失稳理论,而Hill理论又包括Hill48、Hill79、Hill93等针对不同板料提出的不同理论;此外还有M-K凹槽理论、国内陈光南提出的C-H理论等一系列板料失稳理论分析准则。
FLD的试验获得需采用标准实验装置,通过改变试件宽度和润滑条件,基于网格应变分析技术,获得极限应变数据并通过计算所需应变值建立FLD。根据试件受力方式不同,构建FLD的方法分为“曲面法”和“平板面法”,曲面法主要有Heckler试验法、Nakazim试验法;平板面法主要有A-B试验法、M-K试验法等,其中Nakazim试验法应用较多,利用该方法建立的FLD需要加工一系列矩形试样,矩形试样长度均为180mm,宽度从180mm到20mm,每次递减20mm,即每获得一种板料的FLD需加工至少9个不同的板料试样;或需加工9个不同尺寸骨形试样,且Nakazim试验法是在线性加载(比例加载或简单加载)或近似线性加载的情况下得到的FLD。
由上可知,现有获得FLD的方法存在以下技术问题:
1、理论计算时没有确定的理论系统来确定某种板料的成形极限图,计算过程复杂,容易出错,且计算之前还需通过材料的性能实验获取所需的某些材料性能值,如加工硬化指数、厚向异性系数等。
2、试验法需要加工不同尺寸的板料,即需要多种试样。
3、无论是试验获得还是通过理论计算,一般都是按照线性加载得到的FLD,然而实际生产中板料成形并非都是简单加载的,如一些复杂的、需多工步成形的零件。理论和试验均表明:同一种板料,采用不同的加载方式,其FLD有很大不同。
为解决上述FLD的应变加载路径相关性问题,提出了用成形极限应力图(forming limit stress diagram,FLSD)以替代FLD。FLSD是在FLD试验的基础上考虑板料变形的极限应力与极限应变关系,通过应力应变转化得到。为验证FLSD的加载路径无关性,在试验及模拟时必须实现非线性加载,即复杂加载,通过对不同的加载方式获得的FLD、FLSD比较,可得出结论。
现有的实现复杂加载路径的方法有:单向拉伸平行预加载后胀形至板料失稳、单向拉伸垂直预加载后胀形至板料失稳、双向拉伸预加载后胀形至板料失稳、平面应变预加载后胀形至板料失稳等。实现复杂加载路径的方法实质上是分为两个试验,即先预变形后胀形,两个试验不是同时进行,没有考虑板料加工后的时效,而大部分零件成形均为一次成形或间隔时间很短,故上述复杂加载条件可能会由于时效对试验结果造成一定的影响。
技术实现要素:
:
本实用新型的目的在于提供一种获得复杂加载条件下成形极限图的试验装置,本实用新型所提供的试验装置是在原有包括多功能板料成形机的基础上改装凸模装置,其它装置及模具为原有设备。
本实用新型所提供的一种获得复杂加载条件下成形极限图的试验装置包括多功能板料成形机及成形模具;所述多功能板料成形机包括成形机基体7、液压顶杆及液压控制系统;所述成形模具包括带有压边筋的凹模1、带有压边筋的压边圈3、可拆卸外板6及特制凸模;所述特制凸模包括小凸模11和大凸模4,所述小凸模11的上端为半球形凸模,所述小凸模11的下端设有卡箍接口5,所述卡箍接口5用于与连接凸模的能够垂直运动的液压顶杆10对接,所述小凸模11是对板料进行预变形的一种特制模具;所述大凸模4的内部为能够与所述小凸模11套接的孔腔,所述大凸模4的外部为半球形凸模;所述液压顶杆包括连接压边圈的能够垂直运动的液压顶杆9及连接凸模的能够垂直运动的液压顶杆10;所述连接凸模的能够垂直运动的液压顶杆10的上端设有与所述小凸模11进行连接的卡箍连接装置12,所述连接凸模的能够垂直运动的液压顶杆10连接所述小凸模11和大凸模4后将液压力传递到小凸模11和大凸模4上,完成胀形试验。
本实用新型用于获得复杂加载条件下成形极限图的试验方法的具体步骤如下:
(1)制备板料试样,统一裁剪为180*180mm的方形板料并印制网格。
(2)凸模位置调零:将所述小凸模11与所述连接凸模的能够垂直运动的液压顶杆10进行对接,然后将所述大凸模4套接在所述小凸模11上,将所述大凸模4调整至所述凹模1的下方,将该位置设为位移零点位置,用于后期调整所述大凸模4及小凸模11的运行速度。
(3)放置板料:将步骤(1)印制好网格的板料8按照标准顺序依次对中放置在所述压边圈3上。
(4)小凸模胀形板料:将初始压边力设为X后,上升所述压边圈3,使所述板料8与所述凹模1接触,此时所述压边圈3与所述凹模1上对接的压边筋2压住所述板料8,随着所述小凸模11行程的增加,所述板料8的法兰区金属向变形区流动,当所述小凸模11上升至一定高度h时,停止小凸模胀形板料,h表示所述小凸模11从接触所述板料8至完成对板料胀形后的行程距离,然后将所述小凸模11下降至能手动安装所述大凸模4的位置。
所述初始压边力X=(10-20)*α*t2,式中α:板料的屈服强度(MPa);t:板料的厚度(mm)。
(5)大凸模胀形板料:将所述大凸模4套接在所述小凸模11上,并将压边力调至最大值,此时所述板料8的法兰区金属不再向变形区流动,所述板料8随所述大凸模4行程的增加直至破裂,该破裂处能够获得极限应变值及其它试验数据,完成一种应力状态的试验。
(6)下降所述大凸模4及压边圈3至能够将所述板料8取出的高度,关闭系统电源,取出所述板料8,测量相关数据。
(7)更换板料,卸下所述大凸模4,改变所述小凸模11的上升高度h及初始压边力X,重复所述步骤(3)-(6),记录不同的应变状态下板料极限应变值,完成成形极限图的试验测定。
本实用新型提供的一种获得复杂加载条件下成形极限图的试验装置可一步实现复杂加载,无需在胀形前对板料进行相应的预变形,避免了上述时效问题以及相对繁杂的试验过程;本实用新型用于试验测试所需板料均采用同一尺寸,无需加工多种尺寸板料,可批量加工,节省试验时间,缩短试验周期。
附图说明:
图1:为本实用新型的结构示意图;
图2:为本实用新型中小凸模与液压顶杆卡箍连接结构示意图;
图3:为本实用新型中凸模更换时小凸模位置示意图;
图4:为方形板料示意图;
图5:为骨形板料示意图。
图中:1:凹模;2:压边筋;3:压边圈;4:大凸模;5:卡箍接口;6:可拆卸外板;7:多功能板料成形机基体;8:板料;9:连接压边圈的能够垂直运动的液压顶杆;10:连接凸模的能够垂直运动的液压顶杆;11:小凸模;12:卡箍连接装置。
具体实施方式:
本实用新型所提供的一种获得复杂加载条件下成形极限图的试验装置包括多功能板料成形机及成形模具;多功能板料成形机包括成形机基体7、液压顶杆及液压控制系统;成形模具包括带有压边筋的凹模1、带有压边筋的压边圈3、可拆卸外板6及特制凸模;特制凸模包括小凸模11和大凸模4,小凸模11的上端为半球形凸模,所述小凸模11的下端设有卡箍接口5,所述卡箍接口5用于与连接凸模的能够垂直运动的液压顶杆10对接,所述小凸模11是对板料进行预变形的一种特制模具;大凸模4的内部为能够与所述小凸模11套接的孔腔,所述大凸模4的外部为半球形凸模,所述大凸模4的球头直径a按照胀形试验模具标准制作,大凸模直径是小凸模的2-3倍;所述液压顶杆包括连接压边圈的能够垂直运动的液压顶杆9及连接凸模的能够垂直运动的液压顶杆10;所述连接凸模的能够垂直运动的液压顶杆10的上端设有与所述小凸模11进行连接的卡箍连接装置12,所述连接凸模的能够垂直运动的液压顶杆10连接所述小凸模11和大凸模4后将液压力传递到小凸模11和大凸模4上,完成胀形试验。
本实用新型用于获得复杂加载条件下成形极限图的试验方法具体步骤如下:
1、制备板料试样,板料厚度是1mm,屈服强度是160MPa,统一裁剪为180*180mm的方形板料。
2、凸模位置调零:对接小凸模与液压顶杆,套接大凸模与小凸模(大凸模直径100mm,小凸模直径40mm),将大凸模高度调整至凹模下方约10mm处,将该位置设为位移零点位置,以便后期适当调整凸模运行速度。
3、放置板料:将印制好网格的板料按照标准的顺序依次对中放置在压边圈上。
4、小凸模胀形板料:上升压边圈,使板料与凹模接触,将初始压边力设为2400N,小凸模上升拉深板料:随着小凸模行程的增加法兰区金属可向变形区流动,当小凸模上升至一定高度h时,小凸模上升高度h=(0-10)*t,t:板料的厚度(mm)(h分别是0,2,4,6,8,10mm);之后小凸模下降至能手动安装大凸模的位置。
5、大凸模胀形板料:大凸模套接小凸模,并将压边力调至最大值,此时法兰区金属不再向变形区流动,板料随大凸模行程的增加直至破裂,该破裂处可获得极限应变值及其他试验数据,完成一种应力状态的试验。
6、下降大凸模、下降压边至能将板料取出的高度,关闭系统电源,取出板料,测量相关数据。
7、更换板料,改变小凸模上升高度h,重复上述步骤3-6,记录不同的应变状态下板料极限应变值,完成成形极限图FLD的试验测定。