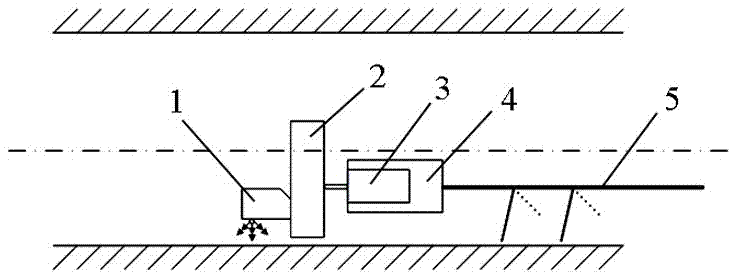
本发明涉及一种内轮廓测量技术,具体地说是一种基于激光三角法的管状物内轮廓测量方法。
背景技术:
:管状构件是指长纵深、大口径(>100mm)类的管件,在能源化工、工程制造和国防军事等领域有着广泛应用,如火炮的身管、石油天然气输油管道等。这些管状构件在使用过程中会产生不同程度的蚀化、磨损,影响其效能的发挥,有时甚至会产生安全隐患。大量实践和研究表明,火炮身管的烧蚀磨损对火炮实施精确射击具有重要影响,抽油机井采油中抽油机和油管间的偏磨会导致油管磨穿,输油管道冲蚀泄露是石油化工企业中经常发生的一种失效形态。这些现象都有可能导致重大安全事故的发生。但是盲目更换管状构件,又会带来极大的浪费,增加相应的生产成本。因此,在保证必要的安全可靠性的前提下,如何最大限度地延长各类管状构件的使用寿命,是一个值得研究的课题。管状构件的内膛测量不同于一般的工件检测,其特殊性主要原因在以下三个方面:1、管道尺寸长,管内黑暗,不易观察;2、管道内不易设置探头,不便调整测量仪;3、要求测量的精度高,不能对管内壁产生影响,以免产生测量误差。常规测量方法和测量仪器不易实现对长管内膛的高精度的自动检测,存在有检测精度低、检测效率不高、操作使用不便、系统复杂程度高和功能单一等问题。技术实现要素:本发明的目的就是提供一种基于激光三角法的管状物内轮廓测量方法和测量装置,以解决现有测量方法存在的检测精度低、检测效率不高、操作使用不便、系统复杂程度高和功能单一的问题。本发明的目的之一是这样实现的:一种基于激光三角法的管状物内轮廓测量方法,包括:a、设置管状物内轮廓测量装置:在支撑机构的前端固定有步进电机,步进电机的电机轴上通过悬臂连接激光位置传感器,所述步进电机通过驱动器与控制系统电连接;所述激光位置传感器是在机壳中分别设置有半导体激光器、发射器镜头、成像透镜和受光元件,所述发射器镜头设置在所述半导体激光器的发射光路上,所述受光元件设置在所述成像透镜的焦平面上,所述半导体激光器的发射光路与步进电机的电机轴的轴心线相垂直,所述成像透镜的成像光路与所述半导体激光器的发射光路为锐角设置。b、将所述管状物内轮廓测量装置伸入被测管状物的管状内腔中,在控制系统的控制下,步进电机带动激光位置传感器做360°的周向步进式旋转,每旋转一个步进分度,由半导体激光器向被测管状物的内壁发射一个激光束,在被测管状物的内壁照射处即形成一个光点,该光点经成像透镜聚焦后,成像在受光元件上。c、利用在受光元件上的光点成像位置及其位置偏差,计算出半导体激光器的发射头到测量面的距离d,激光位置传感器旋转360°,即得到所有步进分度内的半导体激光器发射头到被测管状物内腔的测量面之间的距离dn。d、将上述测量数据中相差为180°转角所对应的两个测量数据求和,即得到读数和bn,设电机轴到半导体激光器的发射头之间的垂直距离为r,则bn+2r即为被测管状物在该测量位置处对应截面上的一条弦的弦长ln,所有弦长中的最大的一条弦长lmax经过或无限接近被测管状物在测量位置处对应截面上的圆心,该弦长lmax即认定为被测管状物在该测量位置处对应截面上的直径,并对应求出被测管状物在该测量位置处对应截面上的圆心。e、在控制系统中的上位机上,利用已知直径的环进行系统校准,选取对应的被测管状物,输入计算参数,上位机中运行扫描模块即可对被测管状物的内腔进行整周扫描,采集到的数据经处理后带入半径计算模型,生成与步进分度对应的点,将这些点连线后,在上位机的图像显示模块中即可显示出被测管状物在该测量位置处的内轮廓图。f、对被测管状物的纵深进行上述测量,即可在上位机的图像显示模块中得到全纵深的三维测量结果。所述控制系统包括:驱动器,分别与步进电机和单片机相接,用于接受单片机的指令,驱动步进电机实现步进式转动;a/d转换器,分别与单片机和激光位移传感器相接,用于将激光位移传感器输出的反射成像信号转换成数字信号;单片机,分别与驱动器、所述a/d转换器和上位机相接,用于接收上位机指令,向驱动器发出步进电机动作信号,并将通过a/d转换器转换的反射成像数字信号通过发送给上位机;以及上位机,分别与所述单片机和所述a/d转换器相接,用于向单片机发出检测指令,并将通过a/d转换器所接收的反射成像数字信号进行数据处理和计算,从而得到管状物内轮廓的测量数据,并显示数据处理后的成像图像。本发明的目的之二是这样实现的:一种基于激光三角法的管状物内轮廓测量装置,在支撑机构的前端固定有步进电机,步进电机的电机轴上通过悬臂连接激光位置传感器,所述步进电机通过驱动器与控制系统电连接;所述激光位置传感器是在机壳中分别设置有半导体激光器、发射器镜头、成像透镜和受光元件,所述发射器镜头设置在所述半导体激光器的发射光路上,所述受光元件设置在所述成像透镜的焦平面上,所述半导体激光器的发射光路与步进电机的电机轴的轴心线相垂直,所述成像透镜的成像光路与所述半导体激光器的发射光路为锐角设置。所述控制系统包括:驱动器,分别与步进电机和单片机相接,用于接受单片机的指令,驱动步进电机实现步进式转动;a/d转换器,分别与单片机和激光位移传感器相接,用于将激光位移传感器输出的反射成像信号转换成数字信号;单片机,分别与驱动器、所述a/d转换器和上位机相接,用于接收上位机指令,向驱动器发出步进电机动作信号,并将通过a/d转换器转换的反射成像数字信号通过发送给上位机;以及上位机,分别与所述单片机和所述a/d转换器相接,用于向单片机发出检测指令,并将通过a/d转换器所接收的反射成像数字信号进行数据处理和计算,从而得到管状物内轮廓的测量数据,并显示数据处理后的成像图像。本发明测量装置的测量原理是:利用激光位移传感器中的半导体激光器向管状物的内壁垂直发出光束,成像透镜聚集目标反射的光点,并在受光元件上形成光点图像,光点在受光元件上的位置会根据目标的距离的变化而变化,控制系统对该距离变化进行计算,并转换为目标位置的测量结果。测量时,步进电机步进旋转,带动激光位移传感器步进运动,完成管道内膛在检测位置处的整周测量和纵深测量,从而完成对管状物内轮廓的测量。本发明测量装置结构简单,灵活性好,测量距离可选,测量精度高,稳定性强。传统的测量方法要求测量仪的中心轴线必须与管状物的轴心线相重合,而在实际测量时,很难做到两线重合,因而严重影响了测量准确性。本发明测量装置和测量方法只需通过支撑机构保证电机轴平行于管状物的内腔轴心线,即可完成管道内轮廓的测量,简单、方便、准确。本发明采用cmos高精度激光位移传感器和步进电机,设计了一种管状物内轮廓测量装置,该测量装置无需中心定位即可对管孔进行非接触式测量。本发明确定了在非定心条件下的管孔半径的计算模型,可准确找到被测管孔的圆心,且单次单截面整周扫描能够获得多达(与分度值相等的)6000条的测量线和测量点,可实现管孔的三维全轮廓的测量和图形显示。本发明测量装置和测量方法可为管型部件磨损和蚀化等情况提供准确可靠的判定依据,从而实现管孔类部件的寿命预测。本发明探索研究了一种管状物内径非定心非接触测量方法,设计了管状物内轮廓测量装置,该装置可对管道内表面全轮廓进行高精度测量,从而准确评估管状物的使用状态。附图说明图1是本发明测量装置的结构示意图。图2是激光位移传感器的结构示意图。图3是控制系统及关联部分的结构框图。图4是管状物内轮廓截面半径的计算示意图。图5是在管状物测量位置处的内轮廓测量结果显示图。图6是管状物内轮廓全纵深三维测量结果显示图。图7是am+x计算流程图。图中:1、激光位置传感器,2、悬臂,3、步进电机,4、固定装置,5、支撑机构,6、机壳,7、半导体激光器,8、发射器镜头,9、成像镜头,10、受光元件。具体实施方式实施例1:基于激光三角法的管状物内轮廓测量装置。如图1所示,本发明基于激光三角法的管状物内轮廓测量装置是在支撑机构5的前端固定有步进电机3,步进电机3的电机轴上通过悬臂2连接有激光位置传感器1,步进电机3通过驱动器与控制系统电连接。为适应不同范围孔径测量,激光位移传感器1可根据被测管径的不同在悬臂2上移动安装固定。对于大尺寸的被测管件,支撑机构5可以是一对简易的“人”型支架,对于小尺寸的被测管件如火炮身管等,支撑机构5可以是能够撑满炮膛的弹性伞型支架。如图2所示,激光位置传感器1的结构是,在机壳6中分别设置有半导体激光器7、发射器镜头8、成像透镜9和受光元件10,发射器镜头8设置在半导体激光器7的发射光路上,受光元件10设置在成像透镜9的焦平面上,半导体激光器7的发射光路与步进电机3的电机轴的轴心线相垂直,成像透镜9的成像光路与半导体激光器7的发射光路为锐角设置。如图3所示,控制系统包括驱动器、a/d转换器、单片机和上位机,上位机可以是笔记本电脑或是其他计算机终端。其中,驱动器分别与步进电机和单片机相接,用于接受单片机的指令,驱动步进电机实现步进式转动。a/d转换器分别与单片机和激光位移传感器相接,用于将激光位移传感器输出的反射成像信号转换成数字信号。单片机分别与驱动器、a/d转换器和上位机相接,用于接收上位机指令,向驱动器发出步进电机动作信号,并将通过a/d转换器转换的反射成像数字信号通过发送给上位机。上位机分别与单片机和a/d转换器相接,用于向单片机发出检测指令,并将通过a/d转换器所接收的反射成像数字信号进行数据处理和计算,从而得到管状物内轮廓的测量数据,并显示数据处理后的成像图像。实施例2:基于激光三角法的管状物内轮廓测量方法。参看图1、图2、图3,本发明基于激光三角法的管状物内轮廓测量方法包括以下步骤:a、设置如实施例1的管状物内轮廓测量装置。b、将上述管状物内轮廓测量装置伸入被测管状物的管状内腔中,在控制系统的控制下,步进电机3带动激光位置传感器1做360°的周向步进式旋转,每旋转一个步进分度,由半导体激光器6向被测管状物的内壁发射一个激光束,在被测管状物的内壁照射处即形成一个光点,该光点经成像透镜聚焦后,成像在受光元件10上;c、利用在受光元件10上的光点成像位置及其位置偏差,计算出半导体激光器6的发射头到测量面的距离d(图2)。激光位置传感器1旋转360°,即得到所有步进分度内的半导体激光器发射头到被测管状物内腔的测量面之间的距离dn。d、将上述测量数据中相差为180°转角所对应的两个测量数据求和,即得到读数和bn,设电机轴到半导体激光器6的发射头之间的垂直距离为r,则bn+2r即为被测管状物在该测量位置处对应截面上的一条弦的弦长ln,所有弦长中的最大的一条弦长lmax经过或无限接近被测管状物在测量位置处对应截面上的圆心,该弦长lmax即认定为被测管状物在该测量位置处对应截面上的直径,并对应求出被测管状物在该测量位置处对应截面上的圆心。e、在控制系统中的上位机中设置有校准模块、被测对象类型模块、扫描模块、数据读取模块和图像显示模块等,利用已知直径的环进行系统校准(图4),选取对应的被测管状物,输入计算参数,上位机中运行扫描模块即可对被测管状物的内腔进行整周扫描,采集到的数据经处理后带入半径计算模型,生成与步进分度对应的点,将这些点连线后,在上位机的图像显示模块中即可显示出被测管状物在该测量位置处的内轮廓图(图5)。f、对被测管状物的纵深进行上述测量,即可在上位机的图像显示模块中得到全纵深的三维测量结果和三维测量效果图(图6)。本发明测量方法的测量原理如下:1、激光三角法原理:在图2中,d0为激光器发射头到参考面间的距离,h为被测面到参考面的距离,u和v分别为参考面的物距和像距,s为测量面成像点偏离参考面成像点的距离,α为参考面漫反射光入射角,为成像角,成像透镜焦距为f。以短距离测量为例,其计算公式如下:由透镜成像原理:由相似三角形原理:由(1)式可得:将(3)式代入(2)式整理得:在(4)式中,v、α、由激光位移传感器1的内部结构决定,由此可知,激光器发射头到测量面的距离为:d=d0-h。2、首条直径的确定:将管状物内轮廓测量装置放入标准圆环(筒)试件中进行截面整周测量,多次测量取平均值,得到管状物内轮廓测量装置的固有测量误差:δ=标准值-平均值。对被测管状物进行测量时,设定步进电机3从初始位置(转角为0°)顺时针运行一个周期(一个360°的周期含有6000个步进分度),激光位移传感器1读出6000个原始数据,这里给出两个假定:1、测读数已消除δ误差;2、已剔除凹坑等大误差读数点。测量数据如表1所示表1.激光位移传感器读数表读数转角读数转角读数和a10.00°a3001180.00°b1a20.06°a3002180.06°b2a30.12°a3003180.12°b3……………………a2999179.88°a5999359.88°b2999a3000179.94°a6000359.94°b3000表1中,“读数和”是指相差180°转角的两个测量数据之和。如图4所示,过步进电机轴心的圆心o2有3000条直径,这些直径延长交被测管孔截面圆心o1,构成圆o1的3000条弦,其一般表达式为:ln=bn+2r(n=1,2…3000)(5)其中必有一条最大弦长经过或无限逼近被测管孔截面的圆心o1,该条弦可认定为圆o1的直径,即d1=lmax=bm+2r(6)其中,读数和最大值为bm,bm=am+am+3000=max(b1,b2,…,b3000)(7)式(5)、式(6)中的r为电机轴到激光发射头之间的垂直距离,是固定值。3、剩余孔径计算模型:首条直径确定后,将对应于激光位移传感器读数am的转角θm处列为新的初始位置,以该位置为起点建立剩余半径的求解计算模型。图4中,步进电机顺时针旋转θ角,激光射在管壁于p点,激光位移传感器的读数为am+x。3.1当0<θ<180°时,在△o1o2p中,由余弦定理:得到:其中,r1=d1/2;o1o2=r1–am–r。3.2当180°<θ’<360°时,激光射在管壁于p’点,在△o1o2p’中,由余弦定理:得到:3.3当θ=180°时,此时不构成三角形,o1p为已知首条直径的1/2,即:o1p=d1/2=bm/2+r故在被测管件的整个圆周范围内,令θ=0.06°·x,得到管孔半径的一般计算公式如下:4、测量结果显示:在控制系统中的上位机中包含有校准模块、被测对象类型模块、扫描模块、数据读取模块、图像显示模块等。用已知直径的环进行系统校准后,选取被测对象,输入相应参数,上位机运行扫描模块,对管孔进行整周扫描,采集到的数据经处理后带入半径计算模型,生成的6000点相连后在图像显示模块显示出被测对象的内轮廓图(图5),对被测对象的纵深进行上述测量,即可得到全纵深的三维测量结果(图6)。在数据读取模块中,由于重新定义了首条直径位置为初始位置,故在带入模型计算时不能按照原始测量数据顺序进行读取。为便于软件编程读取相应数据,以am为初始读数点,其他任意位置读数am+x的取值由图7的计算流程图给出。如图7所示,当x=3000时,θ=180°,o1p为已知;当x≠3000时,若m+x≤6000,则输出am+x的值,若m+x>6000,则将am+x-6000的值赋给am+x后再读取am+x的值。当前第1页12