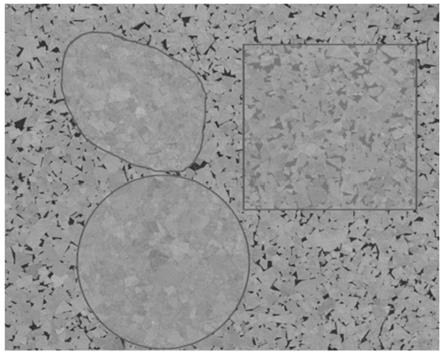
[0001]
本发明涉及测试分析领域,具体涉及一种超细硬质合金中钴相均匀度的测定方法。
背景技术:[0002]
目前,在印制电路板行业高速发展的前提下,对微钻产品品质的要求越来越高,相应的检测分析能力亟需提高。微钻用超细硬质合金(晶粒度≤0.6μm的硬质合金)材质主要由碳化钨和钴组成,对于超细硬质合金中的碳化钨相的显微结构分析行业内比较重视,检测手段和检测水平比较成熟。对超细硬质合金中的钴相显微结构的检测和分析,行业内缺乏有效的检测分析手段,目前通常只能通过对检测图片的比对方式进行分析。另外,目前国内外对于超细硬质合金中钴相显微组织结构尚无检测标准
[0003]
cn103913475a公开了一种测定wc-co硬质合金中钴相结构的方法,包括抛光wc-co硬质合金试样测试面的步骤、电解去除试样表层wc晶粒的步骤、清洁试样表面的步骤和用xrd测试wc-co硬质合金试样中钴相的结构、晶粒大小和/或晶面间距。该方法是先利用电解方法除去wc-co硬质合金试样表层wc晶粒,再对试样表面进行xrd分析,由于消除了试样表层wc相的影响,可以得到完全的钴相衍射图谱,在此基础上便能精确地测定钴相的相结构、晶粒大小和晶面间距等参数,具有工艺简便,方法可靠的特点。
[0004]
cn103592323a公开了一种硬质合金粘结相中钨的固溶度的分析检测方法,依次包括:制备出待测样品的金相抛光面;采用分离技术将金相抛光面上的硬质相剥离并清除表面杂质及氧化层;采用纯co粘接相样品优化x射线能谱仪校准设置;选择成分已知的钴基合金样品作为分析标样,根据标样的理论值与实际测试、zaf基体校正法,求出校正因子并作为标样数据库保存,根据标样的检测结果确定待测样品分析的最佳扫描电镜工作参数;以固溶w5%的钴基合金所建立的数据及相应参数作为x射线能谱定量标准数据库文件,对待测样品不同视场下多次多点测量,其算术平均值即为待测样品粘结相中固溶钨的含量,不仅实现了硬质合金粘结相中钨的固溶度分析检测且准确度高。
[0005]
然而对超细硬质合金中的钴相显微结构的检测和分析,行业内缺乏有效的检测分析手段,目前通常只能通过对检测图片的比对方式进行分析。另外,目前国内外对于超细硬质合金中钴相显微组织结构尚无检测标准。
技术实现要素:[0006]
鉴于现有技术中存在的问题,本发明的目的在于提供一种超细硬质合金中钴相均匀度的测定方法,通过该测定方法可以判断钴相质量分布的均匀性,同时还可以测出合金中钴相的质量百分含量。
[0007]
为达此目的,本发明采用以下技术方案:
[0008]
本发明提供了一种超细硬质合金中钴相均匀度的测定方法,所述测定方法包括如下步骤:
[0009]
(1)将超细硬质合金样品进行抛光,之后随机选取3个位点进行背散射拍摄;
[0010]
(2)在拍摄得到的每个照片中随机选取3个面积相等的分区,计算各个分区的钴含量,然后计算所得数据的c
pk
值,若c
pk
值>1.33则分布均匀。
[0011]
本发明提供的方法通过选择特定的位点个数及各照片中特定的分区个数,利用c
pk
值来确定超细硬质合金中的钴相的均匀性,同时还可以实现对超细硬质合金中钴相和/或碳化钨相的含量测定,检测精度高。
[0012]
作为本发明优选的技术方案,步骤(1)所述抛光为依次进行的机械抛光和化学抛光。
[0013]
优选地,所述化学抛光为在抛光布上加金刚石研磨液进行抛光。
[0014]
作为本发明优选的技术方案,步骤(1)所述抛光后样品表面的粗糙度ra≤0.05μm,例如可以是0.05μm、0.048μm、0.046μm、0.044μm、0.042μm、0.040μm、0.038μm、0.036μm、0.034μm、0.032μm、0.03μm、0.028μm、0.026μm、0.024μm、0.022μm、0.02μm或0.01μm等,但不限于所列举的数值,该范围内其他未列举的数值同样适用。
[0015]
作为本发明优选的技术方案,步骤(1)所述背散射拍摄中的放大倍数为4500-6000倍,例如可以是4500倍、4600倍、4700倍、4800倍、4900倍、5000倍、5100倍、5200倍、5300倍、5400倍、5500倍、5600倍、5700倍、5800倍、5900倍或6000倍等,但不限于所列举的数值,该范围内其他未列举的数值同样适用。
[0016]
作为本发明优选的技术方案,步骤(1)所述背散射拍摄中的放大倍数为4900-5300倍。
[0017]
作为本发明优选的技术方案,步骤(2)中所述3个分区的总面积为照片面积的60-80%,例如可以是60%、61%、62%、63%、64%、65%、66%、67%、68%、69%、70%、71%、72%、73%、74%、75%、76%、77%、78%、79%或80%等,但不限于所列举的数值,该范围内其他未列举的数值同样适用。
[0018]
随机选取三个位置进行图片采集,再在图片中随机选取60-80%的区域进行钴相分析,这种以样本估计总体的方法可以直观地计算出硬质合金的总体钴相分布情况,且能大大节约时间成本与人力成本。
[0019]
作为本发明优选的技术方案,步骤(2)所述钴含量的计算包括:采用图像识别软件计算各分区中钴相的面积占比,然后用钴相的相对密度计算合金中钴相的质量百分比。
[0020]
作为本发明优选的技术方案,所述钴相的面积占比计算中利用软件的分割染色功能,将碳化钨相和钴相分割成对比强烈的颜色,利用软件的分析功能计算钴相颜色所占图片的面积比。
[0021]
作为本发明优选的技术方案,所述钴相的相对密度为钴密度与碳化钨密度和钴密度的和的比值。
[0022]
作为本发明优选的技术方案,所述测定方法包括如下步骤:
[0023]
(1)将超细硬质合金样品进行抛光至ra≤0.05μm,之后随机选取3个位点进行背散射拍摄;所述抛光为依次进行的机械抛光和化学抛光;所述背散射拍摄中的放大倍数为4500-6000倍;
[0024]
(2)在拍摄得到的每个照片中随机选取3个面积相等的分区,计算各个分区的钴含量,然后计算所得数据的c
pk
值,若c
pk
值>1.33则分布均匀;3个分区的总面积为照片面积的
60-80%;
[0025]
所述钴含量的计算包括:采用图像识别软件计算各分区中钴相的面积占比,然后用钴相的相对密度计算合金中钴相的质量百分比;所述钴相的相对密度为钴密度与碳化钨密度和钴密度的和的比值;
[0026]
所述钴相的面积占比计算中利用软件的分割染色功能,将碳化钨相和钴相分割成对比强烈的颜色,利用软件的分析功能计算钴相颜色所占图片的面积比。
[0027]
本发明中各分区钴含量计算如式i:
[0028]
w
co
=ρ
co/co+wc
×
s
co
ꢀꢀꢀꢀꢀꢀꢀꢀꢀꢀꢀꢀꢀꢀꢀꢀꢀꢀꢀꢀꢀꢀꢀ
(i)
[0029]
式中:w
co
为钴相的质量百分比;ρ
co/co+wc
为钴的相对密度;s
co
为照片中钴相的体积占比。
[0030]
本发明中钴的相对密度ρ
co/co+wc
采用式ii计算:
[0031]
ρ
co/co+wc
=ρ
co
/(ρ
co
+ρ
wc
)
ꢀꢀꢀꢀꢀꢀꢀꢀꢀꢀꢀꢀꢀꢀꢀꢀꢀꢀꢀꢀꢀ
(ii)
[0032]
式中:ρ
co
为钴的密度;ρ
wc
为碳化钨的密度。
[0033]
本发明中c
pk
值的计算采用式iii计算:
[0034]
c
pk
=min((usl-x)/3σ,(x-lsl)/3σ)
ꢀꢀꢀꢀꢀꢀꢀꢀꢀꢀꢀꢀꢀꢀꢀ
(iii)
[0035]
式中:usl为规格上限;lsl为规格下限;σ为数据的标准差;x为数据的平均值。
[0036]
本发明中,规格上下限要根据硬质合金的整体钴含量确定,例如8%质量比的硬质合金,一般选择3%为规格下限,13%为规格上限,整体极差10%。
[0037]
本发明中背散射模式下拍摄的硬质合金显微组织,碳化钨相会呈白色,钴相会呈黑色。将拍好的扫描电镜图片导入到图像识别分析软件中,识别出呈黑色的钴相,并计算出黑色区域的面积占比。
[0038]
本发明中三个分区取点/划区计算时取20-25个点或划分20-25个等面积的区域进行计算。
[0039]
与现有技术方案相比,本发明具有以下有益效果:
[0040]
本发明提供的方法通过选择特定的位点个数及各照片中特定的分区个数,利用c
pk
值来确定超细硬质合金中的钴相的均匀性,同时还可以实现对超细硬质合金中钴相和/或碳化钨相的含量测定,提高了测量精度。
附图说明
[0041]
图1是本发明实施例1中选择的位点1的sem照片;
[0042]
图2是本发明实施例1中选择的位点2的sem照片;
[0043]
图3是本发明实施例1中选择的位点3的sem照片。
[0044]
下面对本发明进一步详细说明。但下述的实例仅仅是本发明的简易例子,并不代表或限制本发明的权利保护范围,本发明的保护范围以权利要求书为准。
具体实施方式
[0045]
为更好地说明本发明,便于理解本发明的技术方案,本发明的典型但非限制性的实施例如下:
[0046]
实施例1
[0047]
本实施例提供一种超细硬质合金中钴相均匀度的测定方法,所述测定方法包括如下步骤:
[0048]
(1)将超细硬质合金样品(依据制备过程推算钴含量为6.2%)进行抛光至ra为0.05μm,之后随机选取3个位点进行背散射拍摄,如图1、2及3所示;所述抛光为依次进行的机械抛光和化学抛光;所述背散射拍摄中的放大倍数为5000倍;
[0049]
(2)在拍摄得到的每个照片中随机选取3个面积相等的分区,计算各个分区的钴含量,然后计算所得数据的c
pk
值,3个分区的总面积为照片面积的70%;
[0050]
所述钴含量的计算包括:采用图像识别软件计算各分区中钴相的面积占比,然后用钴相的相对密度计算合金中钴相的质量百分比;所述钴相的相对密度为钴密度与碳化钨密度和钴密度的和的比值;
[0051]
所述钴相的面积占比计算中利用软件的分割染色功能,将碳化钨相和钴相分割成对比强烈的颜色,利用软件的分析功能计算钴相颜色所占图片的面积比。
[0052]
所得c
pk
值为1.7>1.33,钴相分布均匀,钴相的质量百分含量为6%。
[0053]
实施例2
[0054]
本实施例提供一种超细硬质合金中钴相均匀度的测定方法,所述测定方法包括如下步骤:
[0055]
(1)将超细硬质合金样品(依据制备过程推算钴含量为8.8%)进行抛光至ra为0.04μm,之后随机选取3个位点进行背散射拍摄;所述抛光为依次进行的机械抛光和化学抛光;所述背散射拍摄中的放大倍数为4500倍;
[0056]
(2)在拍摄得到的每个照片中随机选取3个面积相等的分区,计算各个分区的钴含量,然后计算所得数据的c
pk
值,3个分区的总面积为照片面积的80%;
[0057]
所述钴含量的计算包括:采用图像识别软件计算各分区中钴相的面积占比,然后用钴相的相对密度计算合金中钴相的质量百分比;所述钴相的相对密度为钴密度与碳化钨密度和钴密度的和的比值;
[0058]
所述钴相的面积占比计算中利用软件的分割染色功能,将碳化钨相和钴相分割成对比强烈的颜色,利用软件的分析功能计算钴相颜色所占图片的面积比。
[0059]
所得c
pk
值为1.5>1.33,钴相分布均匀,钴相的质量百分含量为9%。
[0060]
实施例3
[0061]
本实施例提供一种超细硬质合金中钴相均匀度的测定方法,所述测定方法包括如下步骤:
[0062]
(1)将超细硬质合金样品(依据制备过程推算钴含量为5.8%)进行抛光至ra为0.01μm,之后随机选取3个位点进行背散射拍摄;所述抛光为依次进行的机械抛光和化学抛光;所述背散射拍摄中的放大倍数为6000倍;
[0063]
(2)在拍摄得到的每个照片中随机选取3个面积相等的分区,计算各个分区的钴含量,然后计算所得数据的c
pk
值,3个分区的总面积为照片面积的60%;
[0064]
所述钴含量的计算包括:采用图像识别软件计算各分区中钴相的面积占比,然后用钴相的相对密度计算合金中钴相的质量百分比;所述钴相的相对密度为钴密度与碳化钨密度和钴密度的和的比值;
[0065]
所述钴相的面积占比计算中利用软件的分割染色功能,将碳化钨相和钴相分割成
对比强烈的颜色,利用软件的分析功能计算钴相颜色所占图片的面积比。
[0066]
所得c
pk
值为2>1.33,钴相分布均匀,钴相的质量百分含量为6%。
[0067]
对比例1
[0068]
与实施例1的区别仅在于选取3个面积不相等的分区(总面积和实施例1相同),所得c
pk
值为1<1.33,钴相分布不均匀,钴相的质量百分含量为6.2%。
[0069]
对比例2
[0070]
与实施例1的区别仅在于选取2个位点进行背散射拍摄,所得c
pk
值为1.1<1.33,钴相分布不均匀,钴相的质量百分含量为6.4%。
[0071]
对比例3
[0072]
与实施例1的区别仅在于选取5个位点进行背散射拍摄,所得c
pk
值为1.2<1.33,钴相分布不均匀,钴相的质量百分含量为6.3%。
[0073]
上述实施例中规格上限usl的取值为12%,规格下限lsl的取值为2%。
[0074]
通过上述实施例和对比例的结果可知,本发明提供的方法通过选择特定的位点个数及各照片中特定的分区个数,利用c
pk
值来确定超细硬质合金中的钴相的均匀性,同时还可以实现对超细硬质合金中钴相和/或碳化钨相的含量测定,提高了测量精度。
[0075]
申请人声明,本发明通过上述实施例来说明本发明的详细结构特征,但本发明并不局限于上述详细结构特征,即不意味着本发明必须依赖上述详细结构特征才能实施。所属技术领域的技术人员应该明了,对本发明的任何改进,对本发明所选用部件的等效替换以及辅助部件的增加、具体方式的选择等,均落在本发明的保护范围和公开范围之内。
[0076]
以上详细描述了本发明的优选实施方式,但是,本发明并不限于上述实施方式中的具体细节,在本发明的技术构思范围内,可以对本发明的技术方案进行多种简单变型,这些简单变型均属于本发明的保护范围。
[0077]
另外需要说明的是,在上述具体实施方式中所描述的各个具体技术特征,在不矛盾的情况下,可以通过任何合适的方式进行组合,为了避免不必要的重复,本发明对各种可能的组合方式不再另行说明。
[0078]
此外,本发明的各种不同的实施方式之间也可以进行任意组合,只要其不违背本发明的思想,其同样应当视为本发明所公开的内容。