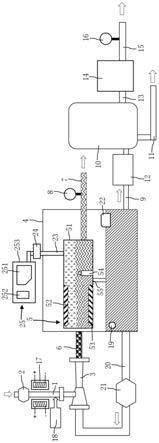
[0001]
本发明涉及油气生产技术领域,尤其涉及一种油井产出液多参数移动测量装置。
背景技术:[0002]
油田生产开发过程中,对产出液量计量和含水分析(取样化验)是监控油井生产状况的必要需求。不同的计量方式和人工取样蒸馏化验含水虽然都存在一定误差影响,但可以满足油井基本生产状况分析。
[0003]
随着油田生产精细化管理程度提高和生产分析不断深入,油井产出状况实时录取和分析的重要性日益增加。不过,现有的油气水由于分离不彻底,导致计量结果偏差较大。部分油田采油井地面工艺采用环线集油或者油井分散,常规单井固定式计量装置无法满足需求。另外,目前单井计量工艺无产出气体计量,尤其是含硫化氢油井,井口取样、更换盘根等井口操作有硫化氢中毒风险。
技术实现要素:[0004]
基于前述的现有技术缺陷,本发明实施例提供了一种油井产出液多参数移动测量装置,可较佳的解决上述问题。
[0005]
为了实现上述目的,本发明提供了如下的技术方案。
[0006]
一种油井产出液多参数移动测量装置,用于测量经由连接在井口的采油树排出的产出液中的油气水含量;包括:进液管,其进液口通过快速接头与所述采油树连接;射流泵,与所述进液管的出液口连接;分离罐,其内设有电絮凝装置;所述电絮凝装置包括:壳体、设在所述壳体内的正电极和负电极;所述壳体具有设在两相对端部的进口和出口,所述进口通过贯穿所述分离罐侧壁的射流管与所述射流泵的出口端连接,所述出口通过贯穿所述分离罐侧壁的第一油管连接至第一储油罐,所述第一油管上设油流量计;所述正电极和负电极设在靠近所述进口的位置,分别位于所述壳体的顶壁和底壁;所述壳体的底壁还设有竖直向上延伸至壳体内的溢流堰板,所述溢流堰板位于所述负电极与所述出口之间;所述壳体的底壁贯穿设有沥水孔,所述沥水孔位于所述负电极与所述溢流堰板之间;通过水管与所述分离罐底部连通的闪蒸罐,所述闪蒸罐的底部连接有第二油管,所述第二油管连接至第二储油罐;设在所述水管上的电加热器,用于将所述水管中的液体加热至超过100℃;通过闪蒸管与所述闪蒸罐连通的冷凝器,所述冷凝器的出口端连接有冷凝管,所述冷凝管上设有水流量计。
[0007]
优选地,所述进液管外包裹有加热组件,所述加热组件用于对进入所述进液管中的产出液进行加热降粘。
[0008]
优选地,所述进液管设有加药系统,用于向所述进液管中加入破乳剂;所述分离罐
中设有用于监测破乳剂浓度的浓度监测元件,所述监测元件与所述加药系统信号连接。
[0009]
优选地,所述分离罐的底部与所述射流泵的进口端之间通过回流管连接,所述回流管上设有空流泵。
[0010]
优选地,所述分离罐中设有用于监测液面高度的液位监测元件,所述液位监测元件与所述空流泵连接。
[0011]
优选地,所述壳体的顶壁连接有气管,所述气管的另一端贯穿所述分离罐的顶壁延伸至分离罐的外部;所述气管上设有气体流量计,另一端连接取样单元,所述取样单元包括与所述气管连接的取样袋以及位于所述取样袋附近的硫化氢检测元件。
[0012]
本发明通过设置电絮凝装置,采用高压脉冲电絮凝工艺,实现产出液的油、气、水三相的分离,再通过将分离后的水加热至100℃以上后再闪蒸,实现油和水的彻底分离,从而使油水的计量更加准确。
[0013]
此外,本发明实施例通过快速接头实现与采油树的可拆卸连接,从而可实现对油井产出液的移动式测量,便捷性较佳。并且,一次操作可同时测得产出液中油气水的含量,测量效率较高。
附图说明
[0014]
图1为本发明实施例的油井产出液多参数移动测量装置的结构示意图。
具体实施方式
[0015]
如图1所示,本发明实施例提供了一种油井产出液多参数移动测量装置,用于测量经由连接在井口的采油树排出的产出液中的油气水含量,包括:进液管1,其进液口通过快速接头2与采油树连接;射流泵3,与进液管1的出液口连接;分离罐4,其内设有电絮凝装置5;电絮凝装置5包括:壳体51、设在壳体51内的正电极52和负电极53;壳体51具有设在两相对端部的进口和出口,进口通过贯穿分离罐4侧壁的射流管6与射流泵3的出口端连接,出口通过贯穿分离罐4侧壁的第一油管7连接至第一储油罐(未示出),第一油管7上设油流量计8;正电极52和负电极53设在靠近进口的位置,分别位于壳体51的顶壁和底壁;壳体51的底壁还设有竖直向上延伸至壳体51内的溢流堰板54,溢流堰板54位于负电极53与出口之间;壳体51的底壁贯穿设有沥水孔55,沥水孔55位于负电极53与溢流堰板54之间;通过水管9与分离罐4底部连通的闪蒸罐10,闪蒸罐10的底部连接有第二油管11,第二油管11连接至第二储油罐;设在水管9上的电加热器12,用于将水管9中的液体加热至超过100℃;通过闪蒸管13与闪蒸罐10连通的冷凝器14,冷凝器14的出口端连接有冷凝管15,冷凝管15上设有水流量计16。
[0016]
在进一步地实施例中,进液管1外包裹有加热组件17,用于对进入进液管1中的产出液进行加热降粘,充分增加流动性。加热组件17可采用电加热装置,例如电热丝,缠绕在进液管1外,实现加热。
[0017]
进液管1设有加药系统18,用于向进液管1中加入破乳剂,使产出液中的油和水充
分混合形成小液滴,射流泵3的可辅助提高油和水的混合。进一步地,分离罐4中设有用于监测破乳剂浓度的浓度监测元件19,浓度监测元件19为浓度传感器,与加药系统18信号连接,用于根据分离罐4中的存液浓度,实现自动补充加药。
[0018]
具体而言,分离罐4的底部与射流泵3的进口端之间通过回流管20连接,回流管20上设有空流泵21。在分离作业开始之前,分离罐4中预置有存液,用于保证射流泵3的正常工作。当分离作业开始时,随着对产出液的油水分离的持续进行,分离罐4中的水(事实上,分离罐4中的水仍混合有少量的油,这也是本装置在分离罐4后设置闪蒸罐10的原因)持续增多,空流泵21将分离罐4中的水泵入射流泵3,作为射流泵3的射流介质,从而实现闭合循环,保证本装置在无外部介质的参与情况下实现自给自足的分离循环。
[0019]
加药系统18包括与浓度监测元件19信号连接的控制模块、被控制模块控制的加药泵。当浓度监测元件19检测到分离罐4中的液体中的破乳剂浓度低于设定值时,说明破乳剂被消耗殆尽,控制模块控制加药泵开启,重新向进液管中的加入破乳剂。
[0020]
在本实施例中,控制模块可以按任何适当的方式实现。具体的,例如,控制模块可以采取例如微处理器或处理器以及存储可由该微处理器或处理器执行的计算机可读程序代码(例如软件或固件)的计算机可读介质、逻辑门、开关、专用集成电路(application specific integrated circuit,asic)、可编程逻辑控制器(programmable logic controller,plc)和嵌入微控制单元(microcontroller unit,mcu)的形式,上述模块的例子包括但不限于以下微控制单元:arc 625d、atmel at91sam、microchip pic18f26k20以及silicone labs c8051f320。本领域技术人员也应当知道,除了以纯计算机可读程序代码方式实现所述控制模块的功能以外,完全可以通过将方法步骤进行逻辑编程来使得控制单元以逻辑门、开关、专用集成电路、可编程逻辑控制器和嵌入微控制单元等形式来实现相同功能。控制模块可借助grps,可将数据传送至用户手机,实现远程数据及时传送。
[0021]
在上述循环过程中,要保证分离罐4中的液位始终保持在设定高度。承接上文描述,在刨除一开始分离罐4中预置的存液的情况下,在后续分离的过程中,电絮凝装置5向分离罐4中排出的水,与空流泵21泵出的水相等,是理想或期望的结果。这样,进水量与出水量相同,分离罐4中的液位始终保持大致相等。
[0022]
因此,为实现上述目的,分离罐4中设有用于监测液面高度的液位监测元件22,液位监测元件22与空流泵21连接。空流泵21基于液位监测元件22监测到分离罐4中的液位高度,控制其转速,进而控制泵出水的速度。
[0023]
液位监测元件22为液位传感器,当液位监测元件22监测到分离罐4中的液位高度低于或高于设定值时,空流泵21的转速相应的降低或提高,从而降低或增大水的泵出速度,使分离罐4中的液位高度逐渐恢复。当液位高度恢复至设定值时,空流泵21维持其当前转速,以使分离罐4中的液位高度维持在当前值。通过上述的实时监测和反馈,使分离罐4中的液位高度始终能够保持在动态平衡。
[0024]
由上文可知,破乳后的产出液通过射流泵3进入到电絮凝装置5的壳体51内,通过设在壳体51内的正电极52和负电极53,采用高压脉冲电絮凝工艺,分离产出液中的油、气、水三相。壳体51的顶壁连接有气管23,气管23的另一端贯穿分离罐4的顶壁延伸至分离罐4的外部。气管23上设有气体流量计24,另一端连接取样单元25,取样单元25包括与气管23连接的取样袋251以及位于取样袋251附近的硫化氢检测元件252。分离出的气相进入取样单
元25,由取样袋251收集并后续接受化验,同时硫化氢检测元件252在线实时显示和报警。取样袋251和硫化氢检测元件252一同设在取样单元25的罩壳253内。
[0025]
分离罐4底部存有循环产出水,通过空流泵21进入射流泵3循环使用。由电絮凝装置5分离出来的水进入电加热器12升温后进入闪蒸罐10进行彻底的油水分离,产出水进入冷凝器14冷凝后计量,闪蒸罐10排出少量原油进入第二储油罐。
[0026]
下面介绍本发明实施例的油井产出液多参数移动测量装置的工作原理:油井产出液进入进液管1,经加热后产出液粘度降低,流动性增强。再将加药系统18加入的破乳剂,使产出液变成小液滴,再射流泵3的辅助作用下进入电絮凝装置5内。电絮凝装置5内的正负电极53分离电极高压电源的正负极,通过高压脉冲电絮凝工艺,实现油气水的三相分离。其中,气相通过气管23排出,由气体流量计24计量其流量,并由取样袋251收集进行后续化验,由硫化氢检测元件252检测是否存在气体泄漏,保证设备安全。
[0027]
随后,分离出来的油和水暂存在溢流堰板54左侧的空间内。由于水的密度大于油的密度,因此水在下层,油在上层。在上层的油超过溢流堰板54后,油就会溢流至溢流堰板54右侧的空间,经第一油管7排出,并由油流量计8计量其流量。水经沥水孔55流入分离罐4中,并流入水管9,在电加热器12的加热作用下,升温至100℃以上(一般为103℃)。随后,加热升温后的水进入闪蒸罐10,水发生闪蒸,而由于油水沸点的差异,油仍保持液滴状态。从而水变成闪蒸蒸汽进入冷凝器14,油沉积在闪蒸罐10的底部,并最终经第二油管11排出并被计量(第二油管11也同样可设置油流量计,用于计量排出的油含量)。进入冷凝器14中的闪蒸蒸汽发生冷凝后重新凝结成液态的水,经冷凝管15排出,并被水流量计16计量其流量。由此,完成对产出液中油气水三相的测量。
[0028]
由此可见,本发明通过设置电絮凝装置5,采用高压脉冲电絮凝工艺,实现产出液的油、气、水三相的分离,再通过将分离后的水加热至100℃以上后再闪蒸,实现油和水的彻底分离,从而使油水的计量更加准确。
[0029]
此外,本发明实施例通过快速接头实现与采油树的可拆卸连接,从而可实现对油井产出液的移动式测量,便捷性较佳。并且,一次操作可同时测得产出液中油气水的含量,测量效率较高。
[0030]
以上所述仅为本发明的几个实施例,本领域的技术人员依据申请文件公开的内容,可以对本发明实施例进行各种改动或变型而不脱离本发明的精神和范围。