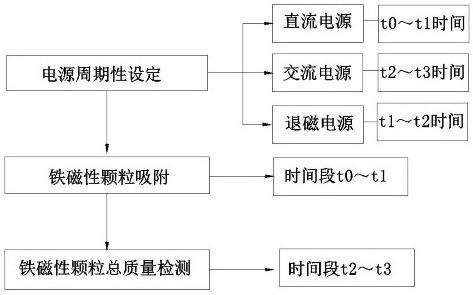
1.本发明涉及无损检测技术领域,具体涉及在线监测油液中铁磁性颗粒的检测技术,特别是涉及一种油液铁磁性颗粒的检测方法及其检测装置。
背景技术:2.在动力装置的润滑系统中(如飞机发动机),通常是通过定量检测油液中金属磨屑的含量,来评估油液质量和动力装置寿命故障,尤其是检测铁磁性颗粒个数以及对单位油液体(如地面油液定量检测)的铁磁性颗粒质量的检测是常规的检测要求。
3.目前,由于市面上对铁磁性颗粒的检测技术通常是以光学方法为主,光谱分析对颗粒的大小和空间分布相对比较简单,而对物质的质量分析并不容易,需要分析物质的吸收光谱等参数来确定颗粒的不同材质,在分析计算颗粒质量的过程上比较繁杂,而且由于颗粒的不同形状并不容易实现,要同时分析得到油液中颗粒数量和质量二项指标并不容易。
4.针对以上缺点问题,本发明采用如下技术方案。
技术实现要素:5.本发明的目的提供一种油液铁磁性颗粒的检测方法及其检测装置,公开的技术方案如下:一种油液铁磁性颗粒的检测方法,用于长期在线动力系统油液中的铁磁性颗粒数量和质量的检测分析,通过涡流绝对式检测传感器在一个周期内吸附铁磁性颗粒和检测分析周期内铁磁性金属磨粒的总质量,包括,检测方法具体步骤如下:a.电源周期性设定:设定涡流绝对式检测传感器线圈(l3)上直流电源和交流电源的各个通电时间,以直流电源通电时间(t0~t1)和交流电源通电时间(t2~t3)合并为一个周期,作为周期性反复运行;b.铁磁性颗粒吸附:在周期性直流电源通电时间(t0~t1)段中,对涡流绝对式检测传感器线圈(l3)上通于直流电,吸附油液中的一个周期时间(t0~t1)段内通过油液管道的铁磁性颗粒;c.铁磁性颗粒总质量检测:在周期性交流电源通电时间(t2~t3)段中,对涡流绝对式检测传感器线圈(l3)上通于交流电,检测在周期时间(t0~t1)段被吸附铁磁性颗粒的总质量。
6.其中,还包括通过设置于油液流动方向涡流检测线圈(l3)上游前端的一对差分式电磁检测线圈(l1、l2)检测计算输油管中铁磁性金属磨粒的个数,结合c步骤中周期时间段内检测的铁磁性颗粒的总质量,分析评估同周期内的铁磁性金属磨粒大概质量平均值。
7.以及,本发明中还包括一个周期内设置于吸附铁磁性颗粒的直流电源时间段(t0~t1)与涡流检测的交流电源时间段(t2~t3)之间的时间段(t1~t2)内的退磁过程,所述的退磁过程可以设置为在涡流绝对式检测传感器线圈(l3)上通于衰减振荡电源。
8.还包括每一个周期中直流电源通电时间(t0~t1)段的电流值大小的设定和选择的步骤,通过数字式模拟验证铁磁性颗粒质量大小对应于被吸附的所需磁力的电流值大小,设定和选择需要评估分析的铁磁性颗粒质量所相对应的直流电源电流值。
9.其中,包括抽取两个以上的周期(t0~t3)时间段作为一个大的周期时间段,在一个大的周期时间段内,分别将每个小周期(t0~t3)时间段内的直流电源值以大小顺序排列设定,选择用于按照颗粒质量值大小顺序的检测评估分析。可以设定为按照铁磁性颗粒质量值从小颗粒到大颗粒的顺序吸附分析,从而分别排列的评估分析小颗粒浓度值或百分量和大颗粒浓度值或百分量。小颗粒浓度值的分析为润滑油的污染程度分析,以确定是否进行润滑油更换;大颗粒浓度值的分析为动力装置故障分析,以评估确定动力装置是否存在故障风险。
10.以及,通常情况下,直流通电吸附铁磁性颗粒的时间(t0~t1)段的时间长度远远大于交流涡流检测时间(t2~t3)段的时间长度。可以设定为直流通电吸附铁磁性颗粒的时间(t0~t1)段的时间长度选择为100秒以上,而交流涡流检测时间(t2~t3)段的时间长度设定为0.01秒,或者以此倍数差的大概时间长度进行设定。
11.其中,同一周期中直流通电吸附铁磁性颗粒的时间(t0~t1)段与交流涡流检测时间(t2~t3)段之间间隔的时间(t1~t2)段小于等于交流涡流检测时间(t2~t3)段。
12.另外,本发明还公开一种油液铁磁性颗粒数量质量的检测装置,用于长期在线动力系统管道(1)中油液的铁磁性颗粒数量和质量的检测,通过导线(21)连接于检测仪器(2),所述检测装置(3)包括支架(31)、涡流传感器线圈l3(32)和一对差动式电磁检测线圈l1、l2 (33),其特征在于所述支架(31)为空心圆柱形结构,所述涡流传感器线圈(32)缠绕于支架(31)的外围。
13.其中,加载于涡流传感器线圈(32)的电源v为周期重复变换式切换电源,每一个周期内均为用于吸附铁磁性颗粒的第一时间段(t0~t1)的直流电源v1切换至用于涡流检测的第二时间段(t2~t3)的交流电源v2,且第一时间段(t0~t1)远远大于第二时间段(t2~t3)。
14.以及,还包括一对差动式电磁检测线圈(33),所述一对差动式电磁检测线圈(33)缠绕的长度小于涡流传感器线圈(32),在油液流向上游部分交叠缠绕,由可被磁化的磁芯层(34)间隔设置于涡流传感器线圈(32)内部层中。
15.据以上技术方案,本发明具有以下有益效果:一、本发明在涡流检测线圈的电源中设定为t0~t1为单位时间吸附颗粒的直流电源时间段和t2~t3期间涡流绝对式检测的交流时间段,实现评估一个周期时间内的铁磁性颗粒总质量。
16.二、本发明还采用二组电磁检测线圈串联其中l1/l2组成差分常规电磁检测,用于计算通过输油管中铁磁性金属磨粒的个数,可以计算分析评估单个铁磁性颗粒的质量平均值。
17.三、本发明将多个小周期时间段t0~t3合并为一个大周期,在一个大周期内的每个小周期的直流电源的电流值为顺序排列,分别吸附不同大小质量的铁磁性金属颗粒,可以非常方便的分别计算分析大小不同的铁磁性金属颗粒情况,方便的将油液污染情况的评估预警和动力装置的寿命故障预警轻松的分开,为监视检测系统分析更加的简单而容易实
现。
18.四、本发明监测装置中,铁磁性颗粒计数的一对差分式电磁检测线圈的内圈部分重叠的设置于涡流检测线圈的油液流动方向的上游端,不但实现准确的吸附前计数,而且设置于内外圈之间隔层的磁芯层结构形成磁通量的差异化,更加实现了电磁检测的精确度,各线圈磁通量的差异化有效的提高了检测装置的灵敏度,非常完美的对管道中的在线油液铁磁性颗粒的数量和质量进行双重检测评估分析。
附图说明
19.图1为本发明最佳实施例的流程示意图;图2为本发明最佳实施例的一个周期电源电流示意图;图3为本发明最佳实施例的一个周期电源增加退磁电源的电流示意图;图4为本发明最佳实施例的两个周期组合成一个大周期的电流示意图;图5为本发明最佳实施例的三个周期组合成一个大周期的电流示意图;图6为本发明最佳实施例的另一种三个周期组合成一个大周期的电流示意图;图7为本发明最佳实施例的检测方法流程线圈顺序示意图;图8为本发明最佳实施例的检测装置结构示意图;图9为本发明最佳实施例的检测装置结构剖视示意图。
具体实施方式
20.下面结合附图和具体实施方式,对本发明做进一步说明。
21.如图1至图7所示,一种油液铁磁性颗粒的检测方法,用于长期在线动力系统油液中的铁磁性颗粒数量和质量的检测分析,通过涡流绝对式检测传感器在一个周期内吸附铁磁性颗粒和检测分析周期内铁磁性金属磨粒的总质量,包括,检测方法具体步骤如下:a.电源周期性设定:设定涡流绝对式检测传感器线圈(l3)上直流电源和交流电源的各个通电时间,以直流电源通电时间(t0~t1)和交流电源通电时间(t2~t3)合并为一个周期,作为周期性反复运行;b.铁磁性颗粒吸附:在周期性直流电源通电时间(t0~t1)段中,对涡流绝对式检测传感器线圈(l3)上通于直流电,吸附油液中的一个周期时间(t0~t1)段内通过油液管道的铁磁性颗粒;c.铁磁性颗粒总质量检测:在周期性交流电源通电时间(t2~t3)段中,对涡流绝对式检测传感器线圈(l3)上通于交流电,检测在周期时间(t0~t1)段被吸附铁磁性颗粒的总质量。
22.如图7中所示,还包括通过设置于油液流动方向涡流检测线圈(l3)上游前端的一对差分式电磁检测线圈(l1、l2)检测计算输油管中铁磁性金属磨粒的个数,结合c步骤中周期时间段内检测的铁磁性颗粒的总质量,分析评估同周期内的铁磁性金属磨粒大概质量平均值。
23.以及,如图3所示,本发明中还包括一个周期内设置于吸附铁磁性颗粒的直流电源时间段(t0~t1)与涡流检测的交流电源时间段(t2~t3)之间的时间段(t1~t2)内的退磁过程,所述的退磁过程可以设置为在涡流绝对式检测传感器线圈(l3)上通于衰减振荡电
源。
24.如图4、5、6所示,还包括每一个周期中直流电源通电时间(t0~t1)段的电流值大小的设定和选择的步骤,通过数字式模拟验证铁磁性颗粒质量大小对应于被吸附的所需磁力的电流值大小,设定和选择需要评估分析的铁磁性颗粒质量所相对应的直流电源电流值。
25.其中,包括抽取两个以上的周期(t0~t3)时间段作为一个大的周期时间段,在一个大的周期时间段内,分别将每个小周期(t0~t3)时间段内的直流电源值以大小顺序排列设定,选择用于按照颗粒质量值大小顺序的检测评估分析。可以设定为按照铁磁性颗粒质量值从小颗粒到大颗粒的顺序吸附分析,从而分别排列的评估分析小颗粒浓度值或百分量和大颗粒浓度值或百分量。小颗粒浓度值的分析为润滑油的污染程度分析,以确定是否进行润滑油更换;大颗粒浓度值的分析为动力装置故障分析,以评估确定动力装置是否存在故障风险。如图4中所示为两个周期(t10~t13)和周期(t20~t23)合并为一个大周期,其中在第一小周期(t10~t11)的直流电流值小于在第二小周期(t20~t21)的直流电流值,即实现第一小周期吸附小质量铁磁性颗粒进行检测分析,而在第二小周期吸附大质量铁磁性颗粒进行检测分析,分别评估检测油液污染程度和动力装置寿命故障。如图5中所示,由三个小周期(t10~t13)、周期(t20~t23)和周期(t30~t33)合并为一个大周期,电源电流值顺序递增排列设定,可以实现顺序的分析评估不同质量大小铁磁性颗粒的参数情况。如图6中所示,三个小周中,电源电流值顺序递减排列设定,同样可以进行不同磁吸力的情况下,不同质量的铁磁性颗粒的参数分析。
26.如图2至6中所示,每个直流电源时间为远大于交流涡流检测时间,通常情况下,直流通电吸附铁磁性颗粒的时间(t0~t1)段的时间长度远远大于交流涡流检测时间(t2~t3)段的时间长度。可以设定为直流通电吸附铁磁性颗粒的时间(t0~t1)段的时间长度选择为100秒以上,而交流涡流检测时间(t2~t3)段的时间长度设定为0.01秒,或者以此倍数差的大概时间长度进行设定。
27.其中,同一周期中直流通电吸附铁磁性颗粒的时间(t0~t1)段与交流涡流检测时间(t2~t3)段之间间隔的时间(t1~t2)段小于等于交流涡流检测时间(t2~t3)段。
28.另外,如图8和图9所示,本发明还公开一种油液铁磁性颗粒数量质量的检测装置,用于长期在线动力系统管道1中油液的铁磁性颗粒数量和质量的检测,通过导线21连接于检测仪器2,所述检测装置3包括支架31、涡流传感器线圈(l3) 32和一对差动式电磁检测线圈(l1、l2)33,其特征在于所述支架31为空心圆柱形结构,所述涡流传感器线圈32缠绕于支架31的外围。
29.其中,检测装置的电源设计为连接于线圈中的plc单片机来进行程序性的设定和控制。
30.其中,加载于涡流传感器线圈32的电源v为周期重复变换式切换电源,每一个周期内均为用于吸附铁磁性颗粒的第一时间段(t0~t1)的直流电源v1切换至用于涡流检测的第二时间段(t2~t3)的交流电源v2,且第一时间段(t0~t1)远远大于第二时间段(t2~t3)。
31.以及,还包括一对差动式电磁检测线圈33,所述一对差动式电磁检测线圈33缠绕的长度小于涡流传感器线圈32,在油液流向上游部分交叠缠绕,由可被磁化的磁芯层34间
隔设置于涡流传感器线圈32内部层中。
32.以上为本发明的其中一种实施方式。此外,需要说明的是,凡依本专利构思所述的构造、特征及原理所做的等效或简单变化,均包括于本专利的保护范围内。