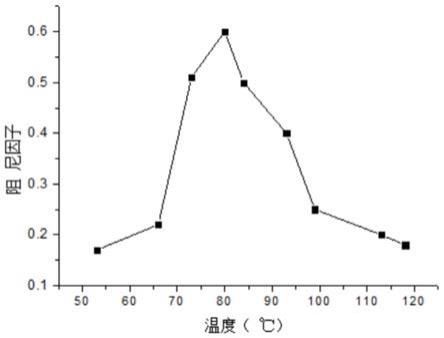
1.本发明涉及噪声振动控制领域,具体涉及一种油浸式声振抑制阻尼橡胶隔声性能评估方法及其应用。
背景技术:2.近年来,我国特高压工程建设快速发展,截止2020年底,国家电网建成投运“十三交十一直”24项特高压工程。同时,特高压输变电核心技术和设备国产化上也取得了重大突破,但在电气设备环境协调性等方面,还有尚待改进的短板,特别是以可听噪声为代表的环保问题正给电网带来不可忽视的环境压力。自2015年起,国内超高压、特高压变电站全面取消了噪声控制区,严格按照厂界噪声排放限制要求执行。其中,特高压变电站换流站被划分为ii类声环境功能区,需满足昼间厂界噪声应不高于60db(a),夜间厂界噪声应不高于50db(a),这对特高压变电站的环保达标是个不小的挑战。
3.为兼顾消防、降噪需求,特高压站一般采用声屏障、无顶盖的box
‑
in结构进行噪声控制,但工程造价高昂、低频降噪效果有限,针对声源设备的本体降噪技术逐渐成为最有效的降噪方案。变压器、电抗器等声源设备的铁心在运行时产生噪声振动,将通过绝缘油传递至油箱,因此提升油箱的降噪水平将显著控制声源设备噪声水平。
4.目前,多数设备制造厂家已针对油箱采取多项措施,包括提升油箱刚度、增设加强筋、油箱内灌沙等,但降噪效果有限。部分厂家在油箱内壁设置阻尼橡胶,与油箱组成约束阻尼构件,极大的提升了油箱整体隔声隔振性能,且不会对设备电气、绝缘性能造成影响。该方案逐渐成为变电设备本体降噪技术的研究重点。
5.但在现有研究中,大部分均只考虑当前阻尼橡胶的隔声隔振性能,但由于阻尼橡胶在变压器绝缘油中需要长时间浸泡,其在使用过程中通常难以保持较好的隔声隔振性能;尤其是变电设备的服役寿命可以长达10年,而现有公开的阻尼橡胶在达到变电设备的服役寿命时均不能满足隔声隔振性能需求。
6.并且在隔声隔振性能检测时,通常需要采用较长时间和较高温度进行老化处理,并不能有效预估该油浸式声振抑制阻尼橡胶的隔声性能。
技术实现要素:7.因此,本发明要解决的问题是现有技术无法准确预估在不同运行时间、不同运行温度条件下该油浸式声振抑制阻尼橡胶的隔声性能;提供了一种油浸式声振抑制阻尼橡胶隔声性能评估方法,有效在不进行长时间高温处理的情况下准确预估油浸式声振抑制阻尼橡胶运行过程中的隔声性能。本发明还公开了利用该评估方法进行阻尼橡胶耐老化性能调节的方法,通过该方法可以有效调节阻尼橡胶的配比,使获得的阻尼橡胶具有更优异的耐老化性能,进而满足油浸式声振抑制阻尼橡胶的耐老化性能需求。
8.一种油浸式声振抑制阻尼橡胶隔声性能评估方法,包括如下步骤:
9.获取数据:将阻尼橡胶浸泡于绝缘油中,设置多组油温和多组浸泡时间的绝缘油
老化试验条件,随后将老化试验后的阻尼橡胶与油箱壳材料组合放置于阻抗管中,测试老化试验前后阻尼橡胶的隔声性能;计算不同绝缘油老化试验条件下阻尼橡胶的隔声性能保留率f,f=绝缘油浸泡后的隔声性能/浸泡前的隔声性能;
10.建立数学模型:建立阻尼橡胶的隔声性能下降数学模型,该数学模型的表达式为:
[0011][0012]
表达式中,a为反应速率常数,h
‑1;e为活化能,j/mol;r为摩尔气体常数,r为8.314j/(mol
·
k);t为热力学温度,k;t为浸泡时间,h;f为隔声性能保留率;b为材料常数;
[0013]
获取相应阻尼橡胶的隔声性能保留率f的关系式:将数据代入数学模型中进行计算,根据该数学模型的关系式即可有效计算出在热力学温度t、浸泡时间t和隔声性能保留率f的关系式;
[0014]
获取相应阻尼橡胶在特定运行温度的绝缘油中使用特定时间时的隔声性能:将绝缘油的运行温度和运行时间代入到隔声性能保留率f的关系式中,获取隔声性能保留率f,采用初始隔声性能与隔声性能保留率f相乘,即可评估在特定运行温度的绝缘油中使用特定时间后该阻尼橡胶的隔声性能。
[0015]
所述试验条件至少包括三组热力学温度下在不同浸泡时间的隔声性能。
[0016]
在将数据代入数学模型中后,采用origin软件进行计算。
[0017]
所述阻尼橡胶的总厚度为3
‑
30mm。
[0018]
采用上述的一种油浸式声振抑制阻尼橡胶隔声性能评估方法在阻尼橡胶的耐老化性能调节上的应用。
[0019]
阻尼橡胶的耐老化性能调节的过程为:
[0020]
测试获得油浸式变电设备的近场噪声,掌握其1/3倍频程声压级和a计权声压级,确定隔声降噪量指标;
[0021]
根据所述的评估方法获取阻尼橡胶的隔声性能,判断计算得到的隔声性能是否满足隔声指标;
[0022]
如果不满足隔声指标则调整阻尼橡胶的组成和配比,直至计算得到的隔声性能满足隔声指标为止。
[0023]
按照10年服役寿命,采用关系式计算出浸泡时间为10年的隔声性能保留率f,进而采用初始隔声性能与隔声性能保留率f相乘,计算获得10年后的隔声性能,判断计算得到的隔声性能是否满足隔声指标。
[0024]
本发明技术方案,具有如下优点:
[0025]
1.本发明公开的一种油浸式声振抑制阻尼橡胶的隔声性能评估方法,可以有效预估出不同运行时间、不同运行温度条件下阻尼橡胶的隔声性能,为获得优异耐久性能的阻尼橡胶提供了有效依据;且预估出的隔声性能十分准确,具有较高的预测精度。
[0026]
2.本发明公开了利用所述的隔声性能评估方法进行油浸式声振抑制阻尼橡胶的耐老化性能调节的方法,通过该方法可以有效判断在该配比条件下阻尼橡胶的隔声性能是否能够满足隔声量指标要求,进而便于阻尼橡胶的配比优化,获得具有更优耐久性能的阻尼橡胶,节约研发成本。
[0027]
3.本发明公开的采用该耐老化性能调节的方法获得的一种油浸式声振抑制阻尼橡胶,其不仅仅具有良好的阻尼隔声隔振功能,并且在达到变电设备的服役寿命时依然能满足隔声隔振性能需求,具有较好的耐老化性能。
附图说明
[0028]
为了更清楚地说明本发明具体实施方式或现有技术中的技术方案,下面将对具体实施方式或现有技术描述中所需要使用的附图作简单地介绍,显而易见地,下面描述中的附图是本发明的一些实施方式,对于本领域普通技术人员来讲,在不付出创造性劳动的前提下,还可以根据这些附图获得其他的附图。
[0029]
图1是本发明实施例1中橡胶的阻尼因子随温度变化图;
[0030]
图2是本发明实施例1中油浸式变电设备的噪声频谱。
具体实施方式
[0031]
提供下述实施例是为了更好地进一步理解本发明,并不局限于所述最佳实施方式,不对本发明的内容和保护范围构成限制,任何人在本发明的启示下或是将本发明与其他现有技术的特征进行组合而得出的任何与本发明相同或相近似的产品,均落在本发明的保护范围之内。
[0032]
实施例中未注明具体实验步骤或条件者,按照本领域内的文献所描述的常规实验步骤的操作或条件即可进行。所用试剂或仪器未注明生产厂商者,均为可以通过市购获得的常规试剂产品。
[0033]
实施例1
[0034]
一种油浸式声振抑制阻尼橡胶,由三层结构层制备而成,第1层结构层的原料包括:60份丁腈橡胶、20份溴化丁基橡胶、20份聚丙烯、4.5份氧化锌、0.5份硫磺、1份ble防老剂、5份石蜡油、1份1,3
‑
联苯基胍和10份云母粉。
[0035]
上述油浸式声振抑制阻尼橡胶的制备方法包括以下步骤:
[0036]
1.将聚丙烯和防老剂加入转矩流变仪中,设置温度150℃,转速40r/min共混5分钟,随后加入丁腈橡胶、溴化丁基橡胶、活化剂和增塑剂再继续共混3分钟,冷却得到共混物。
[0037]
2.将步骤1中得到的共混物置于开炼机上包辊后,加入硫化剂、促进剂和填料,开炼得到预混物,然后将其剪碎。
[0038]
3.将步骤2中制备的碎片置于转矩流变仪中,设置温度150℃,转速40r/min,进行动态硫化,10分钟后获得硫化浆,将硫化浆置于平板硫化机中,并保证填充满硫化模具深度的1/3,等待其自然冷却。
[0039]
4.适当调整丁腈橡胶、溴化丁基橡胶的共混比例获得第2层结构层和第3层结构层的配比,如表1所示。重复步骤1
‑
3的加工步骤,分别制备得到第2层结构层和第3层结构层的硫化浆,并在平板硫化机中将硫化模具填充满。
[0040]
表1
[0041] 第2层结构层第3层结构层丁腈橡胶份数6060
溴化丁基橡胶份数3035聚丙烯份数3032活化剂份数5(硬脂酸)5.5(有机锌)硫化剂份数0.81防老剂份数2(ble)2.5(ble)增塑剂份数10(石蜡油)10(石蜡油)促进剂份数3(1,3
‑
联苯基胍)4(1,3
‑
联苯基胍)填料份数20(云母粉)23(炭黑)
[0042]
5.将平板硫化温度设置为150℃,预热10分钟,施加3mpa压力并保持5分钟,停止加热并保压15分钟,制备获得梯度结构的阻尼橡胶。
[0043]
本实施例中按照阻尼橡胶整体3cm厚度,设计相应的平板硫化成形模具,最终制备获得梯度结构的油浸式声振抑制阻尼橡胶。
[0044]
该阻尼橡胶与油箱壁刚性材料组成约束阻尼结构,具有良好的隔声隔振性能,橡胶阻尼因子随温度变化如图1所示。鉴于变压器、电抗器每10年一次大修,按照10年的服役寿命,评估该声振抑制模块的隔声性能,具体评估步骤如下:
[0045]
a.按照gb/t1094.10等相关方法,采用声级计测试油浸式变电设备的近场噪声,掌握其1/3倍频程声压级和a计权声压级,确定隔声降噪量指标。本步骤中所得油浸式变电设备的1/3倍频程声压级的近场噪声频谱如图2所示,根据该频谱经过a计权计算获得近场声压级62.38db(a)。原油箱结构已具备一定隔声性能,经测试为38db,为保证变压器噪声下降至57db(a)以下,油箱的隔声性能需在原有基础上提升约6db,故本次试验设置隔声量指标为44db。
[0046]
b.将制备的梯度结构阻尼橡胶浸泡于绝缘油中,浸泡时间设置为1天、3天和5天,同时采用电络铁对橡胶加热,加热温度分别设置为200℃、250℃和300℃,随后将阻尼橡胶与油箱壳材料组合放置于阻抗管中,采用《gb/z22764
‑
2011》测试隔声性能(隔声量db),隔声性能检测结果如表2所示;并计算不同试验条件下阻尼橡胶的隔声性能保留率f,f=绝缘油浸泡后的隔声性能/浸泡前的隔声性能。
[0047]
表2
[0048] 200℃250℃300℃0天4747471天46.946.646.43天46.746.245.35天45.845.445.1
[0049]
c.根据隔声测试结果,建立阻尼橡胶的隔声性能下降数学模型,该模型的表达式为:
[0050][0051]
该表达式中,a为反应速率常数,h
‑1;e为活化能,j/mol;r为摩尔气体常数,取值8.314j/(mol
·
k);t为绝缘油的热力学温度,k;t为浸泡时间,h;f为隔声性能保留率;b为材料常数。根据测试得到表2中的试验数据,将实验数据输入到origin软件中,采用origin软
件的数据拟合方法,获得该数学模型为:
[0052][0053]
d.根据变电设备油温,按照10年服役寿命,采用上述公式计算该声振抑制模块在10年后的隔声性能,经计算得到10年后的f为97%,隔声性能为47
×
97%=45.59db,满足隔声量指标要求。
[0054]
实施例2
[0055]
一种油浸式声振抑制阻尼橡胶,由三层结构层制备而成,第1层结构层的原料包括:80份丁腈橡胶、25份溴化丁基橡胶、25份聚丙烯、5份有机锌、1份硫磺、1份6
‑
乙氧基
‑
2,2,4
‑
三甲基
‑
1,2
‑
二氢化喹啉、5份邻苯二甲酸二辛酯、1份4,4'
‑
二硫代二吗啉和20份碳酸钙。
[0056]
上述油浸式声振抑制阻尼橡胶的制备方法包括以下步骤:
[0057]
1.将聚丙烯和防老剂加入转矩流变仪中,设置温度350℃,转速80r/min共混5分钟,随后加入丁腈橡胶、溴化丁基橡胶、活化剂和增塑剂再继续共混3分钟,冷却得到共混物。
[0058]
2.将步骤1中得到的共混物置于开炼机上包辊后,加入硫化剂、促进剂和填料,开炼得到预混物,然后将其剪碎。
[0059]
3.将步骤2中制备的碎片置于转矩流变仪中,设置温度350℃,转速80r/min,进行动态硫化,10分钟后将共混物置于平板硫化机中,并保证填充满硫化模具深度的1/3,等待其自然冷却。
[0060]
4.适当调整丁腈橡胶、溴化丁基橡胶的共混比例,获得第2层结构层和第3层结构层的配比,如表3所示。重复步骤1
‑
3的加工步骤,分别制备得到第2层结构层和第3层结构层的硫化浆,并在平板硫化机中将硫化模具填充满。
[0061]
表3
[0062][0063]
5.将平板硫化温度设置为150℃,预热10分钟,施加10mpa压力并保持5分钟,停止加热并保压15分钟,制备获得梯度结构的阻尼橡胶。
[0064]
按照阻尼橡胶整体3mm厚度,设计相应的平板硫化成形模具,最终制备获得梯度结构的油浸式声振抑制阻尼橡胶。
[0065]
该阻尼橡胶与油箱壁刚性材料组成约束阻尼结构,具有良好的隔声隔振性能。鉴于变压器、电抗器每10年一次大修,按照10年的服役寿命,评估该声振抑制模块的隔声性能,具体评估步骤如下:
[0066]
a.按照gb/t1094.10等相关方法,采用声级计测试油浸式变电设备的近场噪声,掌握其1/3倍频程声压级和a计权声压级,该变压器声压级60db(a),油箱结构隔声量30db,为保证变压器声压级下降至57db(a)以下,油箱隔声量需提升3db,确定隔声降噪量指标33db。
[0067]
b.将制备的梯度结构阻尼橡胶浸泡于绝缘油中,浸泡时间设置为1天、3天和5天,同时采用电络铁对橡胶加热,加热温度分别设置为200℃、250℃和300℃,随后将阻尼橡胶与油箱壳材料组合放置于阻抗管中,采用《gb/z22764
‑
2011》测试隔声性能(隔声量db),隔声性能检测结果如表4所示;并计算不同试验条件下阻尼橡胶的隔声性能保留率f,f=绝缘油浸泡后的隔声性能/浸泡前的隔声性能。
[0068]
表4
[0069]
[0070][0071]
c.根据隔声测试结果,建立阻尼橡胶的隔声性能下降数学模型,该模型的表达式为:
[0072][0073]
该表达式中,a为反应速率常数,h
‑1;e为活化能,j/mol;r为摩尔气体常数,取值8.314j/(mol
·
k);t为绝缘油的热力学温度,k;t为浸泡时间,h;f为隔声性能保留率,取值为绝缘油浸泡后的隔声性能除以浸泡前的隔声性能;b为材料常数。根据测试得到的试验数据,采用数据拟合方法,获得该数学模型为:
[0074][0075]
d.根据变电设备油温,按照10年服役寿命,采用上述公式计算该声振抑制模块在10年后的隔声性能,经计算得到10年后的f为81%,隔声性能为43
×
81%=34db,满足隔声量指标要求。
[0076]
实施例3
[0077]
一种油浸式声振抑制阻尼橡胶,由单层结构层制备而成,原料包括:60份丁腈橡胶、20份溴化丁基橡胶、20份聚丙烯、4.5份氧化锌、0.5份硫磺、1份ble防老剂、5份石蜡油、1份1,3
‑
联苯基胍和10份云母粉。
[0078]
上述油浸式声振抑制阻尼橡胶的制备方法包括以下步骤:
[0079]
1.将聚丙烯和防老剂加入转矩流变仪中,设置温度150℃,转速40r/min共混5分钟,随后加入丁腈橡胶、溴化丁基橡胶、活化剂和增塑剂再继续共混3分钟,冷却得到共混物。
[0080]
2.将步骤1中得到的共混物置于开炼机上包辊后,加入硫化剂、促进剂和填料,开炼得到预混物,然后将其剪碎。
[0081]
3.将步骤2中制备的碎片置于转矩流变仪中,设置温度150℃,转速40r/min,进行动态硫化,10分钟后获得硫化浆,将硫化浆置于平板硫化机中,并保证填充满硫化模具。施加3mpa压力并保持5分钟,停止加热并保压15分钟,获得单层结构阻尼橡胶。
[0082]
本实施例中按照阻尼橡胶整体3cm厚度,设计相应的平板硫化成形模具,最终制备获得单层结构的油浸式声振抑制阻尼橡胶。
[0083]
该阻尼橡胶与油箱壁刚性材料组成约束阻尼结构,具有良好的隔声隔振性能。鉴于变压器、电抗器每10年一次大修,按照10年的服役寿命,评估该声振抑制模块的隔声性能,具体评估步骤如下:
[0084]
a.按照gb/t1094.10等相关方法,采用声级计测试油浸式变电设备的近场噪声,掌握其1/3倍频程声压级和a计权声压级,确定隔声降噪量指标。本步骤中所得油浸式变电设
备的1/3倍频程声压级的近场声压级60.5db(a)。原油箱结构已具备一定隔声性能,经测试为34db,为保证变压器噪声下降至57db(a)以下,油箱的隔声性能需在原有基础上提升约4db,故本次试验设置隔声量指标为38db。
[0085]
b.将制备的梯度结构阻尼橡胶浸泡于绝缘油中,浸泡时间设置为1天、3天和5天,同时采用电络铁对橡胶加热,加热温度分别设置为200℃、250℃和300℃,随后将阻尼橡胶与油箱壳材料组合放置于阻抗管中,采用《gb/z22764
‑
2011》测试隔声性能(隔声量db),隔声性能检测结果如表5所示;并计算不同试验条件下阻尼橡胶的隔声性能保留率f,f=绝缘油浸泡后的隔声性能/浸泡前的隔声性能。
[0086]
表5
[0087] 200℃250℃300℃0天4242421天4241.841.53天41.741.541.35天41.541.240.9
[0088]
c.根据隔声测试结果,建立阻尼橡胶的隔声性能下降数学模型,该模型的表达式为:
[0089][0090]
该表达式中,a为反应速率常数,h
‑1;e为活化能,j/mol;r为摩尔气体常数,取值8.314j/(mol
·
k);t为绝缘油的热力学温度,k;t为浸泡时间,h;f为隔声性能保留率;b为材料常数。根据测试得到表2中的试验数据,采用数据拟合方法,获得该数学模型为:
[0091]
lnf=32.5/t
‑
0.00793lnt
‑
0.0443
[0092]
d.根据变电设备油温,按照10年服役寿命,采用上述公式计算该声振抑制模块在10年后的隔声性能,经计算得到10年后的f为96%,隔声性能为42
×
96%=40.32db,满足隔声量指标要求。
[0093]
实施例4
[0094]
一种油浸式声振抑制阻尼橡胶,由单层结构层制备而成,原料包括:75份丁腈橡胶、25份溴化丁基橡胶、4.5份氧化锌、0.5份硫磺、1份ble防老剂、5份石蜡油、1份1,3
‑
联苯基胍和10份云母粉。
[0095]
上述油浸式声振抑制阻尼橡胶的制备方法包括以下步骤:
[0096]
1.将防老剂加入转矩流变仪中,设置温度150℃,转速40r/min共混5分钟,随后加入丁腈橡胶、溴化丁基橡胶、活化剂和增塑剂再继续共混3分钟,冷却得到共混物。
[0097]
2.将步骤1中得到的共混物置于开炼机上包辊后,加入硫化剂、促进剂和填料,开炼得到预混物,然后将其剪碎。
[0098]
3.将步骤2中制备的碎片置于转矩流变仪中,设置温度150℃,转速40r/min,进行动态硫化,10分钟后获得硫化浆,将硫化浆置于平板硫化机中,并保证填充满硫化模具。施加3mpa压力并保持5分钟,停止加热并保压15分钟,获得单层结构阻尼橡胶。
[0099]
本实施例中按照阻尼橡胶整体3cm厚度,设计相应的平板硫化成形模具,最终制备
获得油浸式声振抑制阻尼橡胶。
[0100]
该阻尼橡胶与油箱壁刚性材料组成约束阻尼结构,具有良好的隔声隔振性能。鉴于变压器、电抗器每10年一次大修,按照10年的服役寿命,评估该声振抑制模块的隔声性能,具体评估步骤如下:
[0101]
a.按照gb/t1094.10等相关方法,采用声级计测试油浸式变电设备的近场噪声,掌握其1/3倍频程声压级和a计权声压级,确定隔声降噪量指标。本步骤中所得油浸式变电设备的1/3倍频程声压级的近场声压级60.5db(a)。原油箱结构已具备一定隔声性能,经测试为34db,为保证变压器噪声下降至57db(a)以下,油箱的隔声性能需在原有基础上提升约4db,故本次试验设置隔声量指标为38db。
[0102]
b.将制备的梯度结构阻尼橡胶浸泡于绝缘油中,浸泡时间设置为1天、3天和5天,同时采用电络铁对橡胶加热,加热温度分别设置为200℃、250℃和300℃,随后将阻尼橡胶与油箱壳材料组合放置于阻抗管中,采用《gb/z22764
‑
2011》测试隔声性能(隔声量db),隔声性能检测结果如表6所示;并计算不同试验条件下阻尼橡胶的隔声性能保留率f,f=绝缘油浸泡后的隔声性能/浸泡前的隔声性能。
[0103]
表6
[0104][0105][0106]
c.根据隔声测试结果,建立阻尼橡胶的隔声性能下降数学模型,该模型的表达式为:
[0107][0108]
该表达式中,a为反应速率常数,h
‑1;e为活化能,j/mol;r为摩尔气体常数,取值8.314j/(mol
·
k);t为绝缘油的热力学温度,k;t为浸泡时间,h;f为隔声性能保留率;b为材料常数。根据测试得到表2中的试验数据,采用数据拟合方法,获得该数学模型为:
[0109]
lnf=34.93745/t
‑
0.03627lnt+0.02982
[0110]
d.根据变电设备油温,按照10年服役寿命,采用上述公式计算该声振抑制模块在10年后的隔声性能,经计算得到10年后的f为75%,隔声性能为40
×
75%=30db,没有达到需要达到的隔声量指标38db,因此,采用此实施例的配方无法满足隔声量指标要求。
[0111]
为了使配方满足隔声量指标要求,可以采用本发明中的耐老化性能的调节方法进一步对一种油浸式声振抑制阻尼橡胶的组成和配比进行调节,例如改变原料的种类,例如增加原料组成聚丙烯,并优化聚丙烯、丁腈橡胶和溴化丁基橡胶之间的配比制备出新的一
种油浸式声振抑制阻尼橡胶,再次采用上述评估方法评估出该声振抑制模块的隔声性能,直至配方满足隔声量指标要求为止。
[0112]
采用上述耐老化性能的调节方法获得的能够满足隔声量指标要求的一种油浸式声振抑制阻尼橡胶的原料组成为:
[0113]
60
‑
80份丁腈橡胶、20
‑
40份溴化丁基橡胶、20
‑
50份聚丙烯、4.5
‑
5.5份活化剂、0.5
‑
1.5份硫化剂、1
‑
3份防老剂、5
‑
20份增塑剂、1
‑
5份促进剂和10
‑
30份填料。
[0114]
试验例
[0115]
采用实施例3中的方案,完成单层阻尼橡胶的制备,其老化数学模型为:
[0116]
lnf=32.5/t
‑
0.00793lnt
‑
0.0443
[0117]
根据变电设备油温,按照10年服役寿命,采用上述公式计算该声振抑制模块在10年后的隔声性能,经计算得到10年后的f为96%,隔声性能为42
×
96%=40.32db。
[0118]
按照300℃的加热温度,10天的油浸时间,将其带入上述老化模型中,计算得到的性能保留率f=96%,与在变电设备油温、浸泡10年后的性能保留率相同。故针对该阻尼橡胶,按照300℃加热温度、10天油浸时间作为试验条件,对该橡胶油浸老化后的隔声性能进行测试,其隔声量为39.8db,与老化模型的计算值相差1.3%,证明该老化模型具有较高的预测精度。
[0119]
显然,上述实施例仅仅是为清楚地说明所作的举例,而并非对实施方式的限定。对于所属领域的普通技术人员来说,在上述说明的基础上还可以做出其它不同形式的变化或变动。这里无需也无法对所有的实施方式予以穷举。而由此所引伸出的显而易见的变化或变动仍处于本发明创造的保护范围之中。