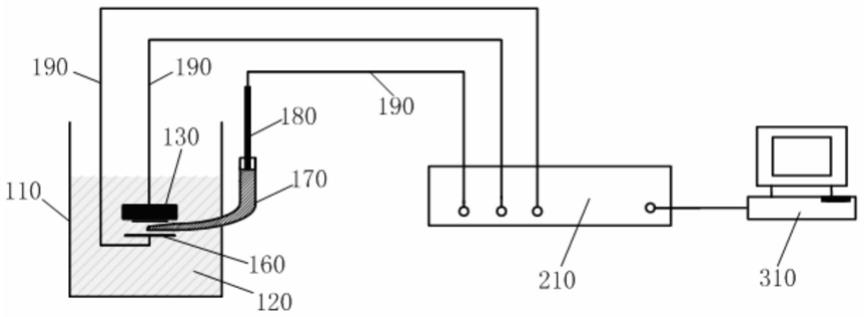
1.本发明属于环境腐蚀评价技术领域,涉及轴承表面防锈油膜层防护效果的电化学评价装置与方法。
背景技术:2.由于受周围环境中水汽、氧气、酸、碱、盐和基材中碳化物等物质的影响,轴承表面在储存、运输和使用过程中会发生物理化学变化而出现漆锈现象,从而影响轴承表面状态的均匀性与完整性,进一步影响轴承服役过程中的稳定性、精度和使用寿命。涂敷防锈油膜层是隔离轴承表面与周围腐蚀环境的常用防护手段之一,也是最直接、最具经济性的防护手段。然而,不同种类防锈油膜层对轴承的防护效果不同,且腐蚀环境变化也使得防锈油膜层表现出不一样的防护效果。传统的评价防锈油膜层防护效果的方法主要有湿热试验、盐雾试验和叠片试验,但这些评价方法都具有耗时的缺点,且不能准确反映不同腐蚀环境对同一防锈油膜层防护效果的影响,使得评价结果往往与腐蚀环境中轴承表面防锈油膜层的实际防护效果不符。因此,开发省时快捷且灵敏度高的轴承表面防锈油膜层防护效果的评价装置与方法具有重要意义。
技术实现要素:3.为解决上述技术问题,本发明提供一种轴承表面防锈油膜层防护效果的电化学评价装置与方法,适用于储存、运输、服役过程中轴承表面不同种类防锈油膜层防护效果的评价,以及腐蚀环境变化对防锈油膜层防护效果影响的评价,具有灵敏度高、省时、高效特点。
4.本发明提供一种轴承表面防锈油膜层防护效果的电化学评价装置,包括:三电极系统单元、电化学工作站和数据处理单元,三电极系统单元与电化学工作站连接,电化学工作站与数据处理单元连接;
5.所述三电极系统单元包括:电解池、轴承钢样品与防锈油膜层复合电极、辅助电极、盐桥和参比电极;电解池内盛装有腐蚀模拟溶液,所述轴承钢样品与防锈油膜层复合电极和辅助电极设置于腐蚀模拟溶液内并通过导线与电化学工作站连接,所述盐桥一端设于腐蚀模拟溶液内,另一端通过参比电极与电化学工作站连接;
6.所述电化学工作站用于实时测量所述轴承钢样品与防锈油膜层复合电极在腐蚀模拟溶液中的开路电位信号与电化学阻抗谱信号;
7.所述数据处理单元包括:处理器和阻抗谱等效电路模型拟合模块;所述处理器用于实时记录与显示所述开路电位信号和电化学阻抗谱信号;所述阻抗谱等效电路模型拟合模块用于对测量到的电化学阻抗谱信号进行等效电路模型拟合,以获取反映表面吸附能力的常相位角元件的电化学参数。
8.在本发明的轴承表面防锈油膜层防护效果的电化学评价装置中,所述电解池为透明玻璃制圆桶状容器;所述腐蚀模拟溶液的体积不少于电解池容积的2/3。
9.在本发明的轴承表面防锈油膜层防护效果的电化学评价装置中,所述轴承钢样品
与防锈油膜层复合电极设置于所述腐蚀模拟溶液内,并通过导线引出电解池顶端预留开口连接至所述电化学工作站的工作电极输入端;所述辅助电极设置于所述腐蚀模拟溶液内,并通过导线引出电解池顶端预留开口连接至所述电化学工作站的辅助电极输入端;所述盐桥的一端通过电解池侧面预留豁口设置于所述腐蚀模拟溶液内,另一端曝露于所述电解池周围的空气环境中并通过饱和kcl溶液连接于所述参比电极;所述参比电极连接于所述电化学工作站的参比电极输入端。
10.在本发明的轴承表面防锈油膜层防护效果的电化学评价装置中,所述轴承钢样品与防锈油膜层复合电极包括:绝缘件、轴承钢样品和防锈油膜层;所述轴承钢样品包裹固定在绝缘件中,所述轴承钢样品的一端面为工作面,从绝缘件的上表面露出,所述防锈油膜层平铺覆盖在轴承钢样品的工作面上,防锈油膜层的面积不小于轴承钢样品的工作面的面积;所述轴承钢样品的非工作面引出一根导线与电化学工作站的工作电极输入端相连;所述防锈油膜层的平铺量为5-10μl/cm2。
11.在本发明的轴承表面防锈油膜层防护效果的电化学评价装置中,视所述防锈油膜层与所述腐蚀模拟溶液的密度比,将所述轴承钢样品与防锈油膜层复合电极正置或倒置于所述腐蚀模拟溶液内;防锈油膜层的密度大于腐蚀模拟溶液的密度时,轴承钢样品与防锈油膜层复合电极正置于腐蚀模拟溶液中,轴承钢样品的工作面朝向电解池的顶部;防锈油膜层的密度小于腐蚀模拟溶液的密度时,轴承钢样品与防锈油膜层复合电极倒置于腐蚀模拟溶液中,轴承钢样品的工作面朝向电解池的底部。
12.在本发明的轴承表面防锈油膜层防护效果的电化学评价装置中,所述辅助电极为单侧面积大于4cm2的铂片,并通过导线引出电解池顶端预留开口连接于电化学工作站的辅助电极输入端。
13.在本发明的轴承表面防锈油膜层防护效果的电化学评价装置中,所述盐桥由一端孔径为1.5mm另一端孔径为15mm且长度为12-15cm的牛角状玻璃管和内部凝固状kcl-琼脂混合物组成。
14.在本发明的轴承表面防锈油膜层防护效果的电化学评价装置中,所述参比电极为饱和甘汞电极或ag/agcl参比电极。
15.在本发明的轴承表面防锈油膜层防护效果的电化学评价装置中,所述盐桥和辅助电极都位于所述轴承钢样品与防锈油膜层复合电极的工作面一侧,且所述盐桥位于所述辅助电极与轴承钢样品与防锈油膜层复合电极之间,互不接触。
16.本发明还提供一种轴承表面防锈油膜层防护效果的电化学评价方法,包括如下步骤:
17.(1)通过电化学工作站测量轴承钢样品与防锈油膜层复合电极在腐蚀模拟溶液中的实时开路电位值,通过处理器记录和显示所测的开路电位值演化结果,当开路电位值漂移量稳定在
±
10mv时,测量结束;
18.(2)开路电位测量结束后,轴承钢样品与防锈油膜层复合电极在腐蚀模拟溶液中已达到电化学稳定状态;电化学工作站进入电化学阻抗谱测量模式,测量频率范围为100khz-10mhz,扰动信号为10mv;通过处理器记录和显示测量到的电化学阻抗谱演化结果;
19.(3)电化学阻抗谱测量结束后,通过阻抗谱等效电路模型拟合模块对测量到的电化学阻抗谱进行等效电路模型拟合分析,得到反映防锈油膜层与轴承钢样品表面吸附能力
的常相位角元件的电化学参数;同时,得到反映轴承钢样品基体阳极溶解反应发生难易程度的电荷转移电阻值;
20.(4)根据等效电路模型拟合得到的不同防锈油膜层覆盖下轴承钢样品在腐蚀模拟溶液中的常相位角元件的电化学参数值和电荷转移电阻值,比较不同防锈油膜层对轴承钢样品防护效果的差异;根据等效电路模型拟合得到的相同防锈油膜层覆盖下轴承钢样品在不同腐蚀模拟溶液中的常相位角元件的电化学参数值和电荷转移电阻值,比较腐蚀环境变化对相同防锈油膜层防护效果的影响。
21.与现有技术相比,本发明的轴承表面防锈油膜层防护效果的电化学评价装置与方法,至少具有以下优点及有益效果:
22.(1)本发明轴承表面防锈油膜层防护效果的电化学评价装置,适用于储存/运输/服役过程中轴承表面不同种类防锈油膜层防护效果的评价,以及腐蚀环境变化对防锈油膜层防护效果影响的评价;
23.(2)本发明轴承表面防锈油膜层防护效果的电化学评价装置,可以根据实际储存/运输/服役过程中环境污染物种类及浓度变化配制不同的腐蚀模拟溶液,使得轴承表面防锈油膜层防护效果的评价更接近于实际腐蚀环境中的真实情况;
24.(3)本发明轴承表面防锈油膜层防护效果的电化学评价装置,具有结构简单,实验方法可靠,步骤合理,可操作性强,方便实用的优点;
25.(4)本发明轴承表面防锈油膜层防护效果的电化学评价装置,适用于储存/运输/服役过程中轴承表面不同种类防锈油膜层防护效果的评价,以及腐蚀环境变化对防锈油膜层防护效果影响的评价,具有灵敏度高、省时和高效特点。
附图说明
26.图1为本发明一实施例的轴承表面防锈油膜层防护效果的电化学评价装置的示意图;
27.图2为图1中轴承钢样品与防锈油膜层复合电极的结构示意图;
28.110-电解池;120-腐蚀模拟溶液;130-轴承钢样品与防锈油膜层复合电极;131-轴承钢样品;132-防锈油膜层;140-绝缘件;150-工作面;160-辅助电极;170-盐桥;180-参比电极;190-导线;210-电化学工作站;310-数据处理单元。
具体实施方式
29.为了便于理解本发明,下面将参照相关附图对本发明进行更全面的描述。附图中给出了本发明的较佳实施例。但是,本发明可以以许多不同的形式来实现,并不限于本文所描述的实施例。相反地,提供这些实施例的目的是使对本发明的公开内容的理解更加透彻全面。
30.需要说明的是,当一个元件被认为是“连接”另一个元件,它可以是直接连接到另一个元件或者可能同时存在居中元件。
31.除非另有定义,本文所使用的所有的技术和科学术语与属于本发明的技术领域的技术人员通常理解的含义相同。本文中在本发明的说明书中所使用的术语只是为了描述具体的实施例的目的,不是旨在于限制本发明。本文所使用的术语“和/或”包括一个或多个相
关的所列项目的任意的和所有的组合。
32.如图1所示,本发明的轴承表面防锈油膜层防护效果的电化学评价装置,包括:三电极系统单元、电化学工作站210和数据处理单元310。三电极系统单元与电化学工作站210连接,电化学工作站210与数据处理单元310连接。
33.三电极系统单元包括:电解池110、轴承钢样品与防锈油膜层复合电极130、辅助电极160、盐桥170和参比电极180。电解池110内盛装有腐蚀模拟溶液120,轴承钢样品与防锈油膜层复合电极130和辅助电极160设置于腐蚀模拟溶液120内并通过导线190与电化学工作210站连接,所述盐桥170一端设于腐蚀模拟溶液120内,另一端通过参比电极180与电化学工作站210连接。
34.电化学工作站210用于实时测量所述轴承钢样品与防锈油膜层复合电极130在腐蚀模拟溶液120中的开路电位信号与电化学阻抗谱信号。数据处理单元310包括:处理器和阻抗谱等效电路模型拟合模块。处理器用于实时记录与显示所述开路电位信号和电化学阻抗谱信号。阻抗谱等效电路模型拟合模块用于对测量到的电化学阻抗谱信号进行等效电路模型拟合,以获取反映表面吸附能力的常相位角元件的电化学参数并进行显示。
35.如图1所示,电解池110为透明玻璃制圆桶状容器,根据轴承储存/运输/服役环境及所含污染物种类与浓度的不同,配制不同的腐蚀模拟溶液120。腐蚀模拟溶液120的体积不少于电解池110容积的2/3。轴承钢样品与防锈油膜层复合电极130设置于所述腐蚀模拟溶液120内,并通过导线190引出电解池顶端预留开口连接至所述电化学工作站210的工作电极输入端。所述辅助电极160设置于所述腐蚀模拟溶液120内,并通过导线190引出电解池顶端预留开口连接至所述电化学工作站210的辅助电极输入端。所述盐桥170的一端通过电解池110侧面预留豁口设置于所述腐蚀模拟溶液120内,另一端曝露于所述电解池周围的空气环境中并通过饱和kcl溶液连接于所述参比电极180。所述参比电极180连接于所述电化学工作站210的参比电极输入端。
36.如图2所示,轴承钢样品与防锈油膜层复合电极130包括:绝缘件140、轴承钢样品131和防锈油膜层132。轴承钢样品131包裹固定在绝缘件140中,轴承钢样品131的一端面为工作面150,其面积为1cm2,工作面150从绝缘件140的上表面露出。防锈油膜层132平铺覆盖在轴承钢样品131的工作面上,防锈油膜层132的面积不小于轴承钢样品131的工作面150的面积。轴承钢样品131的任意非工作面引出一根导线190与电化学工作站210的工作电极输入端相连。所述防锈油膜层的平铺量为5-10μl/cm2为最佳,最大不超过15μl/cm2。
37.具体实施时,根据防锈油膜层132与所述腐蚀模拟溶液120的密度比,将轴承钢样品与防锈油膜层复合电极130正置或倒置于所述腐蚀模拟溶液120内。以免防锈油膜层132在所述腐蚀模拟溶液120浮力的作用下脱离所述轴承钢样品131工作面150表面。具体设置方式为:当防锈油膜层132的密度大于腐蚀模拟溶液120的密度时,轴承钢样品与防锈油膜层复合电极130正置于腐蚀模拟溶液120中,轴承钢样品131的工作面150朝向电解池110的顶部。当防锈油膜层132的密度小于腐蚀模拟溶液120的密度时,轴承钢样品与防锈油膜层复合电极130倒置于腐蚀模拟溶液120中,轴承钢样品131的工作面150朝向电解池110的底部。
38.如图1所示,辅助电极160为单侧面积大于4cm2的铂片,并通过导线190引出电解池顶端预留开口连接于电化学工作站210的辅助电极输入端。盐桥170由一端孔径为1.5mm另
一端孔径为15mm且长度为12-15cm的牛角状玻璃管和内部凝固状kcl-琼脂混合物组成。kcl-琼脂为:将3g琼脂和97g去离子水水浴加热至完全溶解,然后加入30gkcl,充分搅拌后趁热用滴管或虹吸加入预先准备好的牛角状玻璃管中,凝固后即可。所述参比电极180为饱和甘汞电极或ag/agcl参比电极。
39.如图1所示,盐桥170和辅助电极160都位于所述轴承钢样品与防锈油膜层复合电极130的工作面150一侧,且盐桥170位于所述辅助电极160与轴承钢样品与防锈油膜层复合电极130之间,互不接触。
40.本实施的轴承表面防锈油膜层防护效果的电化学评价装置在用于轴承表面防锈油膜层防护效果电化学评价时,涉及了一种防护效果的电化学评价方法,具体包括如下步骤:
41.如图1所示,通过电化学工作站210测量轴承钢样品与防锈油膜层复合电极130在腐蚀模拟溶液120中的实时开路电位值,通过处理器记录和显示所测的开路电位值演化结果,当开路电位值漂移量稳定在
±
10mv时,测量结束;
42.开路电位测量结束后,轴承钢样品与防锈油膜层复合电极130在腐蚀模拟溶液120中已达到电化学稳定状态;电化学工作站210进入电化学阻抗谱测量模式,测量频率范围为100khz-10mhz,扰动信号为10mv;通过处理器记录和显示测量到的电化学阻抗谱演化结果;
43.电化学阻抗谱测量结束后,通过阻抗谱等效电路模型拟合模块对测量到的电化学阻抗谱进行等效电路模型拟合分析,得到反映防锈油膜层与轴承钢样品表面吸附能力的常相位角元件的电化学参数;同时,得到反映轴承钢样品基体阳极溶解反应发生难易程度的电荷转移电阻值;
44.根据等效电路模型拟合得到的不同防锈油膜层覆盖下轴承钢样品在腐蚀模拟溶液中的常相位角元件的电化学参数值和电荷转移电阻,比较不同防锈油膜层对轴承钢样品防护效果的差异;根据等效电路模型拟合得到的相同防锈油膜层覆盖下轴承钢样品在不同腐蚀模拟溶液中的常相位角元件的电化学参数值和电荷转移电阻值,比较腐蚀环境变化对相同防锈油膜层防护效果的影响。
45.以下是本发明的设计原理和设计思想:
46.(1)开路电位和电化学阻抗谱是评价有机涂层耐蚀性常用的电化学方法,且具有无损评价的特点;根据开路电位测量,可以判断轴承钢样品与防锈油膜层复合电极在腐蚀模拟溶液中的电化学稳定性;根据电化学阻抗谱测量,可以判断防锈油膜层在轴承钢样品表面吸附能力的变化,以及轴承钢样品发生阳极溶解反应的难以程度。
47.(2)利用防锈油中油溶性缓蚀剂分子的偶极性特性,可以实现轴承钢样品与防锈油膜层复合电极130在腐蚀模拟溶液120中的开路电位测量和电化学阻抗谱测量。
48.(3)通过对测量到的电化学阻抗谱进行等效电路模型拟合分析,可以得到防锈油膜层与轴承钢样品表面吸附电容值的变化,以及轴承钢样品基体发生阳极溶解反应时的电荷转移电阻值变化。
49.(4)根据不同防锈油膜层在轴承钢样品表面吸附电容值和电荷转移电阻值的变化,可以评价不同防锈油膜层对轴承钢样品防护效果的差异;根据不同腐蚀模拟溶液中同一防锈油膜层在轴承钢样品表面吸附电容值和电荷转移电阻值的变化,可以评价腐蚀环境变化对同一防锈油膜层防护效果的影响。
50.以上所述仅为本发明的较佳实施例,并不用以限制本发明的思想,凡在本发明的精神和原则之内,所作的任何修改、等同替换、改进等,均应包含在本发明的保护范围之内。