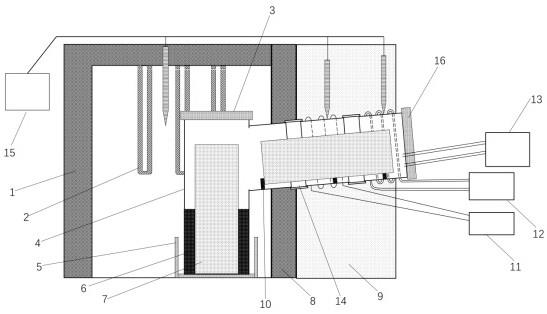
1.本发明属于耐火材料技术领域,主要涉及一种耐火材料抗熔渣和蒸汽侵蚀性试验方法及试验装置。
背景技术:2.耐火材料是高温窑炉中重要的组成,其具有较高的耐火度,故而常作为高温窑炉向火面的炉衬材料;由于高温窑炉常作为冶金、煤气化、玻璃等的制备容器,过程中炉衬材料必然与炉内原料或渣进行接触,该过程是多因素耦合的复杂过程,具体表现包括熔渣对材料表面的化学侵蚀;炉内固、液、气体沿材料气孔对材料内部的物理渗透;以及化学侵蚀和物理渗透引发的材料物理、化学性质改变,最终可能引起材料的损毁。为了提升耐火材料在高温窑炉中的服役寿命,对于耐火材料高温抗渣性能的试验和评价一直是炉衬耐火材料服役性能的重要参考指标之一。
3.现行国家标准gb/t8931-2007 耐火材料抗渣性试验方法提出多种抗渣性试验方法,其中应用最为广泛的是静态坩埚法,其将耐火材料制备成一定规格的坩埚,在坩埚中填入渣,热处理至一定温度使高温下熔渣与坩埚壁直接接触反应并沿坩埚气孔向坩埚内部渗透,根据接触面侵蚀面积和渗透层面积来判定材料的抗渣性能。该方法简单易操作,可以直观对比渣对不同种耐火材料的侵蚀和渗透程度,试验可重复性强,然而其也具有一定的局限:一方面,坩埚热处理时需整体放入炉膛内,靠炉体发热元件加热,坩埚壁不存在温度梯度,从而渣与材料的反应处于单一影响因素下;另一方面,试验仅可模拟渣在高温下对于材料表面的侵蚀行为和材料内部的渗透行为,对于实际生产中存在的气相侵蚀或渗透无法正确捕捉。另一种较为常用的抗渣性试验方法为回转渣蚀法,其将多块耐火材料切割拼凑成中空的棱柱型,并置于回转炉内部,通过单向火焰加热炉体,在试验过程中炉体不断转动,通过人工加渣、倒渣的方式模拟渣对材料的侵蚀和渗透行为。该方法可以模拟熔渣对于材料表面的冲刷作用,是一种动态抗渣试验方法,较之静态法更为贴合实际工况,然而其也具有局限性,主要包括:一、由于试验材料被制备为中空棱柱型,整个试验过程为敞开式,温度波动难以控制,过程气氛难以调控;二、熔渣与材料仅有直接接触,不存在多相侵蚀过程,尤其是气相会随敞开环境流失;三、试验时间跨度长,试验成本过高,试验风险较大。
4.抗渣性为耐火材料关键的服役性能,由于渣与材料作用过程为多因素共同影响,研究人员基于现行标准对抗渣性试验做出了针对性的优化和改进。中国专利一种耐火材料高温抗侵蚀试验方法及试验装置(申请号 201110331284.9)提出一种将材料悬挂并整体浸入坩埚容器中,容器中为熔渣,悬挂材料不断旋转来模拟材料受渣冲刷的效果,为一种动态抗渣性试验方法,其相对回转渣蚀法气氛和温度更为可控,但是仍存在仅有液相熔渣与材料接触的问题;中国专利一种耐火材料抗渣试验方法(申请号 201610018216.x)提出一种采用中频炉加热的静态抗渣性试验方法,其将材料制成环状壁,围绕组成中空圆环,在圆环内填入铁块和渣,利用中频炉电磁加热的方式,熔化铁块,使抗渣试验的温度由内及外传递,可实现材料环状壁上的温度梯度变化,但由于铁块等金属的熔化温度在1450℃以上,其
抗渣性试验温度必须高于铁块熔化温度,导致其使用范围受到影响。
5.危险废物处理用回转窑系统为近年来受关注较高的危废窑炉炉型,其工作温度普遍在800℃~1200℃,用以处理塑料、造纸废料废液、污泥等多种危险废物。由于处理物料的种类繁杂,其燃烧后灰渣的化学组成复杂,尤其是塑料与造纸业废料废液中存在大量的碱金属氧化物和卤素盐类,因为工作温度偏低,灰渣中的氧化物类物相难以熔化,但碱金属氧化物和卤素盐类如nacl,熔点800℃左右在较低温度即可转变为液相甚至气相,该类物质的渗透性能远高于氧化物熔渣,可直接渗透进入材料骨料的晶间,与晶粒发生反应,从而破坏骨料的结构;另一方面,由于高温窑炉炉衬材料普遍存在由内及外的温度梯度,在不同温度下,碱金属氧化物和卤素盐类与材料的接触形式和侵蚀反应类型、生成物区别很大,由此造成的材料热膨胀性能改变可导致材料不同部位的热膨胀失配,从而发生物理破坏。该窑炉的灰渣侵蚀、渗透机理与现有其他高温窑炉受熔渣侵蚀、渗透的机理截然不同,依托于现有抗渣性试验方法难以直观评价危废回转窑用耐火材料的抗渣性能,主要体现在:一、反应物形式区别,由于窑炉温度低,危废回转窑内起渗透作用的物质主要是低熔点的碱金属氧化物和卤素盐类等,氧化物类物质由于未到熔点只可能与材料表面发生接触,现有如静态坩埚法难以实现固、液、气相渣与材料的多相接触;二、温度梯度影响,现有抗渣性试验方法中,多数为热源由外及内加热坩埚或材料试样,材料本身处于某一特定试验温度,难以评价温度梯度对于材料和渣接触、反应类型的影响,前述提到的中国专利201610018216.x虽然采用内加热方式实现温度梯度影响,但其由于铁块熔点限制难以适用于危废回转窑较低的工作温度。
技术实现要素:6.为解决上述技术问题,本发明的目的是提出一种耐火材料抗熔渣和蒸汽侵蚀性的试验方法及试验装置,使其实现一定的温度梯度下渣的固、液、气3种形态同时与耐火材料的接触反应,对不同温度梯度下渣与耐火材料接触情况和反应类型进行评价。
7.本发明为完成上述目的采用如下技术方案:一种耐火材料抗熔渣和蒸汽侵蚀性试验方法,试验方法用于表征高温熔渣及其产生的蒸汽在重力和温度梯度下对静止耐火材料试样的化学反应、溶解和渗透;耐火材料的显气孔率10%~20%、常温耐压强度大于等于1.0mpa;熔渣是氧化物混合物、无机盐类或二者的混合物;所述的试验方法是将周围填充有渣样的待检测耐火材料圆柱体试样固定在密封组件中,将密封组件一端置于炉膛加热区,另一端伸出炉墙,对耐热钢密封组件进行加热过程中形成熔渣及其蒸汽并在耐火材料试样上产生温度梯度,以评价特定温度和时间范围内熔渣及蒸汽对耐火材料的侵蚀性;所述的密封组件为由2段圆筒构成的l型拼接体,包括相互连通的垂直段和水平段,垂直段装入的耐火待测试样浸入渣液中进行熔体抗渣侵蚀,水平段装入的试样进行抗蒸汽渗入侵蚀;所述的耐火材料试样在试验中存在温度差异,垂直段试样处于恒定温度,水平段试样具有从接近垂直段到远离垂直段的温度梯度;所述试验方法的试验结果处理为试验结束炉温达室温后取出垂直段和水平段试样,测量计算试验前后试样的质量变化、体积变化、直径变化,也可辅助扫描电镜、x射线衍射的仪器分析手段,评价和对比不同材料的抗熔渣及蒸汽侵蚀性能;所述的一种耐火材料抗熔渣和蒸汽侵蚀性试验方法,具体步骤如下:
第一步,制备2支材质和尺寸相同的圆柱体耐火材料试样,圆柱体尺寸为φ50~100mm
×
h100~230mm,测定试样的初始质量、体积、直径,从同规格样品上取样进行显微结构、相组成分析;第二步,将2支圆柱体分别置入耐热钢密封容器的垂直段和水平段中,然后向垂直段中加入试验渣,填渣量为垂直段圆柱体高度的1/2~2/3,密封;第三步,将装有试样和渣的密封容器置入试验装置,垂直段置于有发热体的炉膛内,水平段伸出窑墙或窑门;第四步,加热炉膛至试验温度并保温,试验温度为800~1200 ℃,保温时间为3~24 h;第五步,自然降温后从试验装置中取出密封容器,拆除后取出耐火材料试样进行质量、体积、直径的测定,或借助仪器进行分析,给出抗侵蚀性评价。
8.一种耐火材料抗熔渣和蒸汽侵蚀性试验方法,步骤第五步借助仪器进行分析,根据填渣量高度将垂直段试样沿圆柱体试样侧面按有无直接接触渣而进行切割;对切开的未直接接触渣试样和直接接触渣试样分别沿其轴线方向等分切开;对直接接触渣试样分别进行侵蚀面积、渗透面积计算,并采用扫描电子显微镜和能谱分析设备分析其侵蚀区域和渗透区域的微观形貌和物相组成,对未直接接触渣试样进行蒸汽渗透面积计算,并采用扫描电子显微镜和能谱分析设备分析其渗透区域和未渗透区域的微观形貌和物相组成;将水平段试样沿试样侧面三等分切开,分别在切后圆柱中心钻取圆柱试样,测试其热膨胀性,分别对剩余试样沿其轴线方向等分切开,采用与垂直段未直接接触渣试样分析手段相同的方法对其渗透区域和未渗透区域进行分析。根据各试样分析结果综合评价试样抗熔渣及蒸汽侵蚀性能的优劣。
9.提出一种耐火材料抗熔渣和蒸汽侵蚀性试验方法,采用两端l式密封容器可同时容纳垂直段和水平段两根试样,通过将垂直段置于可加热炉膛内并采用炉门砖对炉膛进行封闭可保证密封容器垂直段试样整体处于某一设定温度,而水平段伸出炉门可营造水平方向由高至低的自然温度梯度,更贴近热工装置中耐火材料实际工况;对密封容器水平段伸出炉门砖部分采用保温材料进行填充,是为了进一步固定密封容器且避免水平段热量散失过快而造成的试样温度梯度失真;要求耐火材料试样为圆柱型,其原因是使熔渣、蒸汽与试样在各处均匀接触,渗透与侵蚀行为可由外至内均匀发生,避免由试样形状而造成的不均匀侵蚀,也利于耐火材料试样在试验前后体积、直径等的测量精度;要求耐火材料试样具有一定的直径,其原因是避免由于熔渣、蒸汽侵蚀过快,影响材料分析时对于侵蚀区域、渗透区域和未反应区域的区分,要求耐火材料试样具有一定高度是因为高度不足可能致使水平段试样热传递过程过快难以营造温度梯度变化,若高度太高又会导致制备试样难度增加,且配套使用的密封容器原料消耗、炉膛尺寸的大小随之增加,不利于控制试验成本;要求填渣量在一定范围,其原因是避免填渣过少,熔渣和蒸汽含量过低,发生侵蚀和渗透的程度难以进行有效评价,也避免填渣过多导致垂直段试样与固、液、气3种形态渣接触的试验要求相抵触;要求试验温度在800℃~1200℃,其原因是若温度过低,则渣中熔点较低的盐类难以液化或气化,熔点较高的氧化物更加难以形成熔渣,与试验目的相悖,若温度过高则会导致采用耐热钢为原料的密封容器软化、氧化、剥落等,影响试验效果。
10.一种耐火材料抗熔渣和蒸汽侵蚀性试验装置,试验装置所具有的常压热处理电炉
的内部空腔形成炉膛;炉膛内壁有保温炉衬,其加热方式为采用发热元件在炉膛内部进行电加热;采用热电偶及温度显示装置对各温度段的温度进行监控;所述的炉膛内放置有试验容器,所述的试验容器为由耐1200℃高温的合金钢制成,容器壁厚3-5mm,为两段圆柱型容器,由垂直段、水平段和底座组成,垂直段的内径φ70~120mm,高度h为140~270mm,垂直段上口具有带螺纹的旋盖,水平段为采用刚玉陶瓷管与试验容器材料组合套装的断桥式结构:第一、三、五段为试验容器材料,其中第一段与垂直段连通,第三段的规格为:φ70~120mm
×
h40~80mm,第二、四段为刚玉陶瓷管,刚玉陶瓷管内径与其余三段材料外径相同,规格为内径φ73~125mm
×
h20~30mm,刚玉陶瓷管壁厚3-5mm,水平段侧口具有带螺纹的旋盖,其具有孔洞,可接入尾气处理装置;所述的水平段第一、三、五段材料内具有挡板和衬垫;试验时炉膛采用与保温内衬相同材料的具有孔洞的炉门砖和耐火纤维进行炉门的填充和封堵,用以对炉膛进行保温并固定试验容器。
11.所述试验容器的底座,是耐1200℃高温的合金钢材质制成的坩埚;其目的是防止试验中渣液突发性外漏而污染炉膛。
12.所述试验容器的水平段,冷端高、热端低,其与水平面有5~10
°
的倾角,其目的是便于冷凝后的渣液或水回流。
13.所述试验容器的水平段,其伸出炉门砖的部分可配置电热丝及加热装置或水冷管及水冷系统,用以对温度梯度进行可控调节,其中电热丝与水平段间需绝缘纤维隔离,以防止加热装置无法正常运行;在水平段伸出炉门砖的区域额外设置发热丝和水冷管可根据试验需要实现可控的温度梯度调节,也能够模拟某些实际窑炉中因炉体转动或开、停车导致的温度循环及温度波动,更为贴合窑炉的实际工况。
14.所述的耐火材料抗熔渣和蒸汽试验装置,根据炉膛尺寸,可同时放置多组试验容器,以进行多材料间相同试验条件下的平行试验。
15.一种耐火材料抗熔渣和蒸汽侵蚀性试验装置,采用相互连通的两段圆柱型合金钢材质作为试验容器,设计成圆柱形容器是为了营造试样与渣的均匀接触环境,采用合金钢作为容器材质是为了避免氧化物类熔渣接触试验容器壁后与试验容器发生反应影响容器使用寿命和试验结果;要求试验容器具有的垂直段和水平段具有一定的尺寸规格是保证试验材料可以放置于容器内部且留有一定的填渣空间,避免填渣量过多或过少,影响试验结果;在试验容器水平段设计合金钢材质与刚玉陶瓷管材质相互配合套用的“断桥式”结构是为了避免全部采用金属材质而在水平段形成热桥,从而影响试验材料正常的温度梯度由热端至冷端变化,并通过设计挡板结构和衬垫结构使试验试样可以固定并较少直接接触金属材质容器壁;在试验容器水平段配置电热丝和水冷管可以根据试验需要控制温度梯度变化,并通过设置于装置各处的热电偶实时进行试样温度数据的收集。
16.本发明提出一种耐火材料抗熔渣及蒸汽侵蚀试验方法及试验装置,能更为贴切的模拟实际应用高温环境下含盐熔体及蒸汽对窑炉炉壁的侵蚀和渗透,更为准确全面的评价耐火材料在中低温窑炉中的抗渣性能。试验方法易操作、直观,试验装置简单、安全。
附图说明
17.图1为本发明试验装置的结构示意图。
18.图2 为本发明试验方法中试验试样的分析方法示意图。
19.图中:1、刚玉莫来石炉,2、发热元件,3、旋盖,4、试验容器,5、底座,6、试样,7、试验渣,8、炉门砖,9、耐火纤维,10、挡板和衬垫,11、电热丝及加热装置,12、水冷管及水冷系统,13、尾气处理装置,14、刚玉陶瓷管,15、热电偶及温度显示装置,16、带螺纹的旋盖,17、垂直段试样,18、水平段试样,19、侵蚀面积,20、渗透面积,21、蒸汽渗透面积,22、圆柱试样,23、渗透区域。
具体实施方式
20.结合附图和具体实施例对发明加以详细说明:实施例1:如图1所示,一种耐火材料抗熔渣及蒸汽侵蚀试验装置,加热炉为内部具有空腔的电炉,炉膛内壁为刚玉莫来石炉衬1,采用二硅化钼棒作为加热炉的发热元件2;在炉膛内部中心位置设置有一套k型热电偶组15对炉膛内温度进行监控;炉膛内放置有采用310s耐热钢制成的试验容器4,容器壁厚5mm,为两段圆柱型容器,由垂直段、水平段和底座5组成,垂直段规格为内径φ80mm*h180mm,垂直段上口具有带螺纹的旋盖3结构,水平段为采用刚玉陶瓷管14与试验容器材料组合套装的断桥式结构,第一、三、五段为试验容器材料,其中第一段与垂直段连通,三段规格为φ80mm*h65mm,第二、四段为刚玉陶瓷管,刚玉陶瓷管内径与其余三段材料外径相同,规格为内径φ85mm*h30mm,刚玉陶瓷管壁厚5mm,第一、三、五段与刚玉陶瓷管互相套入的长度为5mm;水平段侧口具有带螺纹的旋盖16结构,其具有孔洞,在孔洞中接入气管并连通尾气处理装置13,用以对试验中产生的废气进行过滤、收集并平衡试验容器内外压力;水平段第一、三、五段材料内具有挡板和衬垫10结构;试验时炉膛采用具孔洞的刚玉莫来石材质炉门砖8进行封堵,其孔洞直径为95mm,打孔角度为5
°
,套入试验容器水平段后孔洞缝隙用耐火纤维封堵,炉门砖外探出的试验容器水平段外由耐火纤维9进行填充和固定,分别在水平段第三和第五段合金钢材质段设置两支k型热电偶组,进行温度实时监控。
21.试验容器底座,为内径φ90mm,壁厚5mm的310s耐热钢坩埚制成,焊接于试验容器垂直段底部;试验容器水平段,具有5
°
的倾角,便于渣液、蒸汽等冷凝后回流;垂直段上口旋盖、水平段侧口旋盖、水平段挡板和水平段衬垫,均采用310s耐热钢材质制成;试验容器水平段,其伸出炉门砖的部分第三段配置了镍铬材质电热丝及加热装置11,第五段配置了冷却水管及循环水冷系统12,其中第三段金属管外包覆有绝缘纤维,避免电热丝与金属管直接接触;该装置可容纳两套试验容器供试验所用,两套试验容器的设置方式及规格尺寸、配套装置均一致。
22.危废处理回转窑系统的最高运行温度为1100℃左右,进行危废焚烧处理过程中,其底渣和飞灰中存在有大量的碱金属氧化物和无机盐类,对于炉衬耐火材料的侵蚀和渗透十分严重,无机盐类渗透后对于材料物理性质,尤其是热膨胀性质的影响尤甚,炉内由于炉体旋转带来的温度循环和温度波动极大,热膨胀性质的改变严重影响了材料的结构稳定。采用上述耐火材料抗熔渣及蒸汽侵蚀试验装置对铬刚玉砖显气孔率16%、常温耐压强度
96mpa的在此工况下的抗侵蚀性能进行评价。
23.具体试验步骤如下:第一步,对待测铬刚玉砖的显微结构和相组成进行分析,其主要物相包括al2o
3-cr2o3固溶体、刚玉和单斜锆;将铬刚玉砖制备成2支φ50mm*150mm的圆柱体试样,分别设置为a试样和b试样,测定其质量和试样上中下侧直径;第二步,将a试样置于试验容器的垂直段,将b试样置于试验容器的水平段,确定试样固定且位置合适后,向垂直段中加入试验渣,试验渣为该危废回转窑收集的底渣和飞灰,渣熔点1180℃,填渣量为75mm,即a试样高度的1/2,将垂直段上口旋盖拧紧密封;第三步,将试验容器置于加热炉炉膛内,试验容器的水平段伸出炉门,采用带有孔洞的炉门砖对加热炉进行封堵,将试验容器水平段侧口旋盖拧紧,接入尾气处理系统的气管,在水平段伸出炉门砖部分用耐火纤维进行填充和固定;第四步,试验温度设置为1100℃,加热炉膛至1100℃并保温5h;第五步,保温结束后使炉膛自然降温,取出试验容器,并取出a、b两试样,分别测定其试验后质量和上中下侧直径;借助仪器对a、b试样进行进一步分析。
24.a、b两试样试验前后的质量、直径等变化情况如表1所示。
25.表1 试样试验前后质量、直径变化对比数据后发现,试样a、b在试验后均发生增重,其中a试样增重更多,由于a试样有1/2试样直接与渣接触,渣中液相物质对材料的渗透是导致其增重的主要原因;a试样在中段和下段的直径变化较大,中段处于固、液、气3种形态渣共同作用位置,试样发生了膨胀。
26.结合仪器对a、b两种试样做进一步分析,如图2所示,将垂直段a试样17沿圆柱体侧面等分切割分为a1垂直段上半部和a2垂直段下半部;对切开的上下侧试样沿其轴线方向等分切开;对a1试样分别进行侵蚀面积19、渗透面积20计算,测得侵蚀面积9.6%,渗透面积39.8%,并采用扫描电子显微镜和能谱分析设备分析其侵蚀区域和渗透区域的微观形貌和物相组成,发现侵蚀主要发生在材料的表面处,材料的基质和颗粒均受到了一定程度的侵
蚀,一部分颗粒有溶解趋势,渗透进入材料内部的主要由玻璃相、nacl为主,渗透区域材料受侵蚀的现象较少;切开a2试样后发现无法直接观测到渗透区域,故采用扫描电子显微镜和能谱分析设备分析其渗透区域和未渗透区域的微观形貌和物相组成,发现试样接近填渣高度的位置出现了颗粒的剧烈反应,渗透进入材料的物相依然以玻璃相和nacl为主,材料颗粒发生了明显的膨胀裂纹,形成了霞石类物质,材料无论内外均出现了渗透现象,说明蒸汽的渗透程度很大。将b试样18沿试样侧面三等分切开为b1水平段高温端、b2水平段中段、b3水平段低温端,分别在切后圆柱中心钻取圆柱试样22规格为φ10mm*h50mm,测试其1100℃时的热膨胀率,结果为:b1:1.204%;b2:1.039%;b3:1.028%,对比未试验试样热膨胀率为1.005%,说明受蒸汽渗透后,材料的物理性质受到了一定程度的影响,且由于温度梯度存在,不同段试样其热膨胀率的变化并不一致;分别对剩余试样沿其轴线方向等分切开,采用与垂直段未直接接触渣试样分析手段相同的方法对其渗透区域23和未渗透区域进行分析,结果发现渗透物相主要以nacl和kcl等盐类为主,有部分na2o和k2o出现,材料受侵蚀影响较小,材料结构未发生明显变化。
27.通过对试样的分析可以发现,材料在与气、固、液3种形式渣接触时,受到的侵蚀最为严重,材料发生明显膨胀,结构出现破坏;盐类与碱金属蒸汽在对于材料的渗透较为深入,主要改变了材料的热膨胀性。基于此材料不同区域的侵蚀、渗透机理可对其服役性能优化改进方向提供参考和理论依据。
28.实施例2:为了对比铬刚玉砖与硅莫砖在危废回转窑中的抗侵蚀性能,采用如实施例1的试验方法及装置,区别在于启用两套试验容器,分别放置2组待测试样,即铬刚玉砖和硅莫砖,试验条件1200℃并保温12h。
29.实施例3:为了模拟危废回转窑中由炉体转动带来的温度波动,采用如实施例1的试验方法及装置,区别在于试验温度设置为1000℃保温12h,在水平段第三段位置设置发热丝以加热20min1100℃、停止20min循环热处理。
30.实施例4:为对比不同渣对于材料的侵蚀及渗透性能影响,采用如实施例1的试验方法及装置,区别在于启用两套试验容器,采用相同的铬刚玉砖作为试样材料,分别采用cl含量12.5%、na含量3.8%的渣a与cl含量1.6%、na含量21.7%的渣b作为试验用渣。试验条件为800℃保温24h。
31.实施例5:为对比不同含量氧化铬含量的铬刚玉砖抗渣性,尤其是受熔渣侵蚀的影响,采用如实施例1的试验方法及装置,区别在于1试验容器及炉门砖采用以下规格:容器垂直段采用2520合金制备,规格:内径φ120mm*h140mm,壁厚3mm;容器水平段第一、三、五段采用2520合金制备,壁厚3mm,其中第一段与垂直段连同,规格:内径φ120mm*h50mm;容器水平段第二、四段采用刚玉陶瓷管制备,壁厚3mm,规格:内径φ123mm*h30mm;水平段倾角为10
°
,便于渣冷却后迅速回流;炉门砖打孔直径为130mm,倾角10
°
,打孔数量3个;容器水平段,第五段配置了镍铬材质电热丝及加热装置,第五段金属管外包覆有绝缘纤维,
避免电热丝与金属管直接接触;2炉膛内可放置3套试验容器;3待测试样分别为氧化铬含量5%、12%和27%的铬刚玉材料,所制备的圆柱体试样规格为:φ100mm*120mm;4试验渣填渣量为垂直段待测试样高度的2/3;5试验温度条件为1200℃保温5h;6试验时第五段电热丝持续以350℃加热容器壁,营造恒定的容器冷端温度;7试验后测定试验材料的质量、直径,进一步对垂直段式样进行沿轴线的等分切割,观察垂直段材料受熔渣侵蚀和渗透的情况,对水平段试样进行热膨胀性测试。根据垂直段材料的受熔渣侵蚀和渗透的面积,判断各材料抗渣性的优劣。
32.实施例6:为模拟真实服役条件下危废回转窑炉衬材料的温度梯度,采用如实施例1的试验方法及装置,区别在于:1试验容器及炉门砖采用以下规格:容器垂直段采用310s合金钢制备,规格:内径φ75mm*h270mm,壁厚5mm;容器水平段第一、三、五段采用310s合金钢制备,壁厚5mm,其中第一段与垂直段连同,规格:内径φ75mm*h80mm;容器水平段第二、四段采用刚玉陶瓷管制备,壁厚3mm,规格:内径φ80mm*h25mm;水平段倾角为7
°
;炉门砖打孔直径为87mm,倾角7
°
;容器水平段,第三段和第五段配置了镍铬材质电热丝及加热装置,金属管外包覆有绝缘纤维,避免电热丝与金属管直接接触;2炉膛可放置一套试验容器;3待测铬刚玉材料所制备的圆柱体试样的规格为:φ65mm*h230mm;4试验温度条件设置为1000℃保温12h;5试验过程中,第三段外电热丝保持750℃加热;第五段外电热丝保持500℃加热,以模拟真实条件下的温度梯度变化情况。