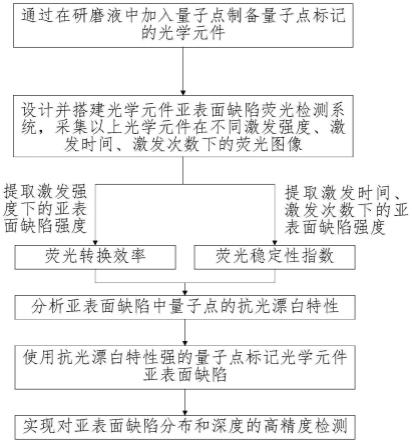
1.本发明涉及光学元件亚表面缺陷的无损检测技术领域,具体涉及一种基于量子点光漂白的光学元件亚表面缺陷检测方法及系统。
背景技术:2.随着空间望远镜、高能激光武器、惯性约束核聚变等光学系统的飞速发展,其对光学元件质量的要求越来越高。
3.光学元件在磨削、抛光等过程不可避免的会产生亚表面缺陷,影响元件的使用寿命和激光损伤阈值等性能,导致光学系统的性能下降,严重时甚至损害整个系统。例如,将天文望远镜放置在温差极大的太空环境中时,光学元件亚表面缺陷会进一步扩展到元件表面,从而严重破坏元件的表面质量,导致望远镜无法获取清晰可靠的图像。因此,光学元件亚表面缺陷的精确检测对指导光学元件加工工艺、提高光学系统的性能至关重要。
4.目前,光学元件亚表面缺陷检测方法分为破坏性检测和非破坏性检测。
5.破坏性检测常用的方法有氢氟酸腐蚀法、角度抛光法、磁流变抛光法等;其原理简单、易于实现且测试设备费用低廉,被广泛应用于无损检测有效性验证和材料质量控制,但其会在元件表面及亚表面产生附加的损伤,导致元件报废或失效,且检测效率低、测量精度过分依赖操作人员的经验。
6.非破坏性检测,如激光散射法、光学相干层析法、x射线衍射法等,能对抛光后元件的亚表面缺陷进行在线检测,但易受到元件表面粗糙度的影响,无法精确检测研磨后元件的亚表面缺陷,且不能实现对亚表面缺陷分布、深度的同时检测。因此,对研磨后光学元件的亚表面缺陷分布和深度进行无损精确检测面临严峻挑战。
7.量子点作为一种具有光致发光特性的荧光纳米颗粒,其作为荧光标记物被广泛应用于生命科学、光电子器件等领域。然而,量子点作为一种荧光材料,激发光强度过高、激发时间过长、激发次数过多都会导致其产生光漂白,不可逆的破坏激发态分子,限制测量的时间、次数以及实验的重复性,降低亚表面缺陷检测精度。因此,需要提出一种基于量子点光漂白的光学元件亚表面缺陷检测方法及系统,以实现对亚表面缺陷的高精度检测。
技术实现要素:8.有鉴于此,本发明提供一种基于量子点光漂白的光学元件亚表面缺陷检测方法及系统,可以提高光学元件亚表面缺陷检测的准确性和精确性。
9.为实现上述目的,本发明采用的技术方案为:一种基于量子点光漂白的光学元件亚表面缺陷检测方法,其特征在于:
10.s1:光学元件和量子点标记物表征
11.使用拉曼光谱仪检测待测元件的自发荧光光谱,根据元件的自荧光谱的峰值确定所使用量子点的荧光发射峰值;
12.使用荧光分光光度计检测量子点的荧光发射光谱和荧光激发光谱,据此确定量子
点的激发波长和半峰宽,确定激光器和荧光滤光片的参数;
13.s2:使用量子点标记光学元件亚表面缺陷
14.将量子点加入研磨液,使量子点在加工过程中实现对光学元件亚表面缺陷的标记,加工后的元件使用含乙醇溶液的超声波清洗仪清洗,去除表面残留量子点和污染物;
15.s3:光学元件亚表面缺陷荧光检测
16.根据荧光显微成像原理,设计搭建光学元件亚表面缺陷荧光检测系统,采用光学元件亚表面缺陷荧光检测系统实现对亚表面缺陷的检测;
17.s4:采集亚表面缺陷荧光图像
18.使用光学元件亚表面缺陷荧光检测系统采集s2中加工的光学元件在不同激发强度、激发时间、激发次数的亚表面缺陷荧光图像;
19.s5:提取缺陷荧光强度
20.将步骤s4采集的图像变为灰度图像,使用灰度值表征缺陷荧光强度值;
21.s6:定量分析亚表面缺陷中量子点的抗光漂白特性
22.通过荧光强度随激发强度的变化,计算可得荧光转换效率随激发强度的变化;通过荧光强度随激发时间和激发次数的变化,计算可得分别在激发时间和激发次数下的荧光稳定性指数,根据荧光转换效率和荧光稳定性指数综合分析量子点的抗光漂白特性;
23.s7:光学元件亚表面缺陷检测
24.使用抗光漂白特性强的量子点标记光学元件亚表面缺陷,对元件亚表面缺陷的分布和深度进行检测,具体方法为:
25.通过亚表面缺陷荧光检测系统检测的亚表面缺陷分布情况;通过激光共聚焦显微镜对s2中加工的元件进行层析扫描,获得层析深度和荧光强度的关系,通过峰值所在位置即可得的亚表面缺陷深度。
26.所述步骤6)的具体方法为:
27.荧光转换效率η为亚表面缺陷中量子点荧光强度与激发光强度的比值,有:
28.if=ηi
l
ꢀꢀ
(1)
29.其中,if为亚表面缺陷中量子点荧光强度,i
l
为激发光光强度,η为荧光转换效率。
30.荧光稳定指数β由下式计算:
[0031][0032]
其中,n是进行的实验次数,xi是第i次实验所采集的荧光图像的荧光强度,是平均荧光强度。即由下式获得:
[0033][0034]
基于量子点光漂白的光学元件亚表面缺陷检测方法中所采用的光学元件亚表面缺陷荧光检测系统,其特征在于:所述系统包括光纤耦合激光器、熔石英光学元件、微位移平台、光电探测器、荧光滤光片、光学镜头、计算机,所述的熔石英光学元件设置于微位移平台上,计算机控制微位移平台,光电探测器与计算机连接,激光器发出的激光斜射入熔石英
光学元件某处,该处的亚表面缺陷产生的荧光依次进入光学镜头、荧光滤光片和光电探测器。
[0035]
所述的荧光滤光片的参数由量子点的荧光发射光谱确定;激光器的激光波长由量子点的荧光发射光谱决定。
[0036]
与现有技术相比,本发明具有如下优点和效果:
[0037]
1)本发明使用抗光漂白特性强的量子点标记光学元件亚表面缺陷,实现对亚表面缺陷分布和深度的高精度检测,使用该方法可分析某种量子点是否适合于亚表面缺陷检测,最大限度地实现对亚表面缺陷荧光的精确检测,进一步提高亚表面缺陷检测的检测精度和灵敏度。
[0038]
2)本发明方法可确定用于亚表面缺陷检测的量子点,有利于充分探究光学元件的亚表面缺陷形成机理,指导光学元件加工工艺,实现对光学元件的超微损伤加工,进而提高光学系统的性能。
附图说明
[0039]
图1为本发明具体实施的流程图;
[0040]
图2为光学元件亚表面缺陷荧光检测系统;
[0041]
图3为熔石英光学元件亚表面缺陷的自发荧光光谱;
[0042]
图4为量子点的荧光发射光谱;
[0043]
图5光学元件亚表面缺陷荧光强度随激发强度的变化关系图;
[0044]
图6为光学元件亚表面缺陷荧光转换效率随激发强度的变化关系图;
[0045]
图7为光学元件亚表面缺陷荧光强度随激发时间的变化关系图;
[0046]
图8为光学元件亚表面缺陷荧光强度随激发次数的变化关系图;
[0047]
图9为光学元件亚表面缺陷分布图像;
[0048]
图10为光学元件亚表面缺陷层析深度与荧光强度的关系;
[0049]
图11为刻蚀速率与刻蚀时间关系。
[0050]
标记说明:1-激光器,2-激光,3-熔石英元件,4-微位移平台,5-探测器,6-荧光滤光片,7-显微镜头,8-计算机,9-混合光,10-荧光。
具体实施方式
[0051]
为了使本发明的目的、技术方案及优点更加清楚明白,以下结合附图及实施例,对本发明进行进一步详细说明。应当理解,此处所描述的具体实施例仅仅用以解释本发明,并不用于限定本发明。
[0052]
本实施例提供一种基于量子点光漂白的光学元件亚表面缺陷检测方法,本实施例以熔石英光学元件作为研究对象,使用水溶性的cuins2/zns量子点作为亚表面缺陷的荧光标记物。
[0053]
方法步骤为:
[0054]
s1:光学元件和量子点标记物表征
[0055]
采用拉曼光谱仪计检测的熔石英光学元件亚表面缺陷的自发荧光光谱如图3所示,采用荧光分光光度计检测的cuins2/zns量子点的荧光光谱如图4所示。由图3、图4可知,
两者的荧光峰值相近,均为544nm左右,可用低于530nm的光激发。
[0056]
s2:使用量子点标记光学元件亚表面缺陷
[0057]
量子点标记光学元件亚表面缺陷的步骤如下所示:
[0058]
将量子点加入金刚砂研磨液中,使用jp350g高速精磨抛光机对熔石英光学元件进行粗磨与精磨,使量子点在研磨过程中进入元件亚表面缺陷,粗磨时使用的是量子点标记的d30金刚砂研磨液,研磨速度为54rad/min,粗磨5min;精磨时使用的是量子点标记的d6金刚砂研磨液,研磨速度为54rad/min,粗磨3min;元件加工完成以后用乙醇溶液超声波清洗5min,充分去除表面杂质和残留的量子点。
[0059]
根据上述量子点标记光学元件亚表面缺陷的步骤,使用cuins2/zns量子点加工一组熔石英光学元件,此外,在相同的加工参数下加工一组不含量子点的熔石英光学元件作为对照组。
[0060]
s3:光学元件亚表面缺陷荧光检测系统设计与搭建
[0061]
根据荧光显微成像原理,设计并搭建亚表面缺陷荧光检测系统,如图2所示,本发明中采用的光学元件亚表面缺陷荧光检测系统包括光纤耦合激光器1、微位移平台4、光学镜头7、荧光滤光片6、光电探测器5,计算机8,熔石英光学元件3设置于微位移平台4上,计算机8控制微位移平台4,熔石英光学元件3上方依次设置有光学镜头7、荧光滤光片6和光电探测器5,光电探测器5与计算机8连接,激光器1发出的激光2斜射入熔石英光学元件3某处,该处的亚表面缺陷产生的荧光依次进入光学镜头7、荧光滤光片6和光电探测器5。其中荧光滤光片6的参数由量子点的荧光发射光谱确定。激光器1的激光波长由量子点的荧光发射光谱决定。
[0062]
本发明中使用量子点荧光检测光学元件亚表面缺陷的主要原理是采用激光激发光学元件亚表面缺陷中的量子点,使其产生荧光,具体实施方式如下:激光器1发出的激光2达到熔石英光学元件3,通过计算机8控制微位移平台4,实现熔石英光学元件3移动,使激光可激发任意位置的亚表面缺陷中的量子点,使其产生荧光;同时熔石英光学元件3会对激光1产生表面散射,由散射光、环境中杂散光和缺陷中荧光组成的混合光9一起进入显微镜头7,然后通过荧光滤光片6去除表面散射光和环境中的杂散光,使亚表面缺陷中的荧光10进入光电探测器5,然后探测器5将检测信号传送给计算机8,实现对亚表面缺陷的检测。
[0063]
s4:采集亚表面缺陷荧光图像
[0064]
使用亚表面缺陷荧光检测系统,在不同激发强度、激发时间、激发次数下,采集s2中加工的熔石英光学元件亚表面缺陷荧光图像,研究激发强度对量子点光漂白特性的影响时,激发强度的变化为0~90mw,每隔5mw采集一次荧光图像。
[0065]
研究激发时间对量子点光漂白特性的影响时,考虑到实际采集荧光图像在几分钟内即可完成,不需长时间连续激发荧光材料,故本实施例连续激发10min,每30s采集一次数据,使用的激发光强度为60mw。
[0066]
研究激发次数对量子点光漂白特性的影响时,为去除激发强度造成的不同量子点荧光强度差异性对量子点光漂白的特性的影响,本实施例中的激发强度为80mw,每5秒激发一次,每次激发时长为5秒,共计激发50次,每激发一次采集一次图像。
[0067]
s5:提取缺陷荧光强度
[0068]
将步骤s4采集的图像变为灰度图像,使用灰度值表征缺陷的强度值。
[0069]
s6:定量分析亚表面缺陷中量子点的抗光漂白特性
[0070]
使用荧光转换效率η定量分析激发强度对亚表面缺陷中量子点的抗光漂白特性的影响。使用荧光稳定性指数β定量分析激发时间和激发次数对亚表面缺陷中量子点的抗光漂白特性的影响。β越小,其荧光稳定性越好。
[0071]
荧光转换效率η为亚表面缺陷中量子点荧光强度与激发光强度的比值,有:
[0072]
if=ηi
l
ꢀꢀ
(1)
[0073]
其中,if为亚表面缺陷中量子点荧光强度,i
l
为激发光光强度,η为荧光转换效率。
[0074]
荧光稳定指数β可由下式计算:
[0075][0076]
其中,n是进行的实验次数,xi是第i次实验所采集的荧光图像的荧光强度,是平均荧光强度。即可由下式获得:
[0077][0078]
对不同激发光强度采集的熔石英亚表面缺陷荧光图像,其荧光强度随激发强度的变化如图5所示,然后进一步根据式(1)对图5中的数据进行计算可得荧光转换效率随激发强度的变化,如图6所示。对不同激发时间和激发次数下采集的亚表面缺陷荧光图像,其荧光强度随激发时间和激发次数的变化分别如图7和图8所示。根据(2)~(3)计算出的使用荧光稳定性指数随激发时间和激发次数的变化分别如表1。
[0079]
表1激发时间下的荧光稳定性指数
[0080][0081]
(1)激发强度对亚表面缺陷中量子点光漂白特性的影响
[0082]
由图5可知:量子点标记的亚表面缺陷荧光强度随激发光强度的增加而增加,但是逐渐会呈现荧光饱和状态;无论激发光强度为何值,cuins2/zns量子点标记的亚表面荧光强度均大于熔石英自发荧光,证明cuins2/zns量子点可以增强元件亚表面缺陷荧光,实现对熔石英亚表面缺陷的有效标记。
[0083]
从图6中荧光转换效率的变化可知,与亚表面缺陷处的自发荧光相比,cuins2/zns量子点标记的亚表面缺陷荧光更稳定,由此可知在不同激发强度下cuins2/zns量子点的抗光漂白性能更好。
[0084]
(2)激发时间对亚表面缺陷中量子点光漂白特性的影响
[0085]
由图7可知,随着激发时间的增加,cuins2/zns量子点标记的亚表面缺陷荧光强度均高于元件的自发荧光,且均保持稳定。结合表1可知,cuins2/zns量子点在激发时间下具有较强的抗光漂白特性。
[0086]
(3)激发次数对亚表面缺陷中量子点光漂白特性的影响
[0087]
由图8可知,随着激发次数的增加,元件自发荧光强度和量子点标记的亚表面缺陷荧光强度均规律性下降,但是cuins2/zns量子点、的荧光强度始终大于元件自发荧光强度。由表1可知,激发次数cuins2/zns量子点仍具有较强的抗光漂白性能。
[0088]
通过上述分析可知,cuins2/zns量子点的抗光漂白特性强。
[0089]
s7:光学元件亚表面缺陷检测
[0090]
对cuins2/zns量子点的标记光学元件和不含量子点的光学元件进行缺陷检测。
[0091]
(1)亚表面缺陷分布
[0092]
使用亚表面缺陷荧光检测系统检测的亚表面缺陷分布情况如图9所示。图9中的亚表面缺陷点数量如表2所示。
[0093]
表2图9中的亚表面缺陷点数量统计
[0094][0095]
由图9和表2可知,利用抗光漂白性能较强的cuins2/zns量子点标记的亚表面缺陷的数量大于不含量子点标记的光学元件。由此可知,抗光漂白特性较强的cuins2/zns量子点可以提高对亚表面缺陷分布的检测精度。
[0096]
(2)亚表面缺陷深度
[0097]
使用激光共聚焦显微镜对s2中加工的元件进行层析扫描,获得层析深度和荧光强度的关系,其检测结果分别如图10所示。由图10中的峰值所在位置即可得的亚表面缺陷深度,如表3所示。
[0098]
表3亚表面缺陷深度
[0099][0100][0101]
使用40%的hf溶液对s2中加工的不含量子点的元件进行阶梯性刻蚀。刻蚀速率与刻蚀时间的关系如图11所示。由图11可得亚表面缺陷深度为10.6μm。结合表4可知,抗光漂白特性较强的cuins2/zns量子点对亚表面缺陷深度的检测更精确。
[0102]
通过上述研究可知,抗光漂白特性较强的量子点可提高对亚表面缺陷分布和深度的检测精度。
[0103]
以上所述,仅为本发明的较佳实施例而已,并非用于限定本发明的保护范围。