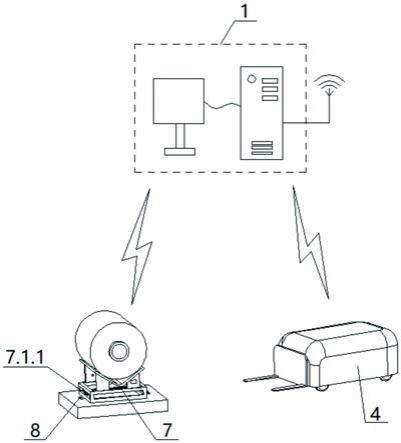
1.本发明涉及铝箔轧制车间物料运输技术领域,具体涉及一种铝箔轧制车间自动化物流系统及运行方法。
背景技术:2.现有铝箔轧制车间物料的运输仍采用天车吊运,天车在吊运物料时会发生摆动,必须有工作人员参与吊运工作,且存在运输效率低、吊运人员工作强度大、危险度高的问题;铝箔轧制生产过程物流自动化是铝箔生产企业发展的一个必然趋势,但目前尚没有铝箔轧制生产过程物流自动化的解决方案,同时如何通过低成本改造实现现有铝箔轧制生产过程物流自动化也是一个有待解决问题。
技术实现要素:3.为了克服背景技术中的不足,本发明公开了一种铝箔轧制车间自动化物流系统及运行方法,包括控制中心、智能叉车、智能托盘、托盘定位传感器;托盘定位传感器固定设置在铝箔轧制车间地面的设定位置,智能托盘与托盘定位传感器通过超高频射频信号通信,确定自身位置信息;智能托盘通过自身设置的应变传感器,确定自身是否放置有铝箔成品及铝箔成品重量的状态信息;智能托盘将自身的位置信息及状态信息通过微功率无线通信传输给控制中心,由控制中心通过微功率无线控制智能叉车对智能托盘进行搬运,实现铝箔轧制车间生产过程物流的自动化。
4.为了实现所述发明目的,本发明采用如下技术方案:一种铝箔轧制车间自动化物流系统,包括控制中心、智能叉车、智能托盘、托盘定位传感器;托盘定位传感器设有若干个,其固定设置在铝箔轧制车间地面的设定位置,智能托盘与托盘定位传感器通过超高频射频信号通信,确定自身位置信息;智能托盘与控制中心之间通过微功率无线通信连接,将自身位置信息及状态信息传输到控制中心;控制中心是铝箔轧制车间自动化物流系统的核心,其存储有铝箔轧制车间内所有智能托盘及智能叉车的状态及位置信息,控制中心根据生产及出货需求综合判断做出决策,生成搬运指令;搬运指令包括需搬运智能托盘的现有坐标及目的坐标,控制中心通过微功率无线通信将搬运指令传输给选定的智能叉车,选定的智能叉车根据需搬运智能托盘的现有坐标和目的坐标,自动完成搬运任务。
5.进一步的,智能叉车上设置有控制装置、惯性导航装置、机器视觉辅助定位装置及微功率无线通信装置,控制装置中设置有铝箔轧制车间导航地图,导航地图内存储有所有智能托盘存放位的坐标信息;当需要搬运智能托盘时,控制中心发出包含需搬运智能托盘的现有坐标和目的坐标的搬运指令至选定的智能叉车,智能叉车的控制装置根据需搬运智能托盘的现有坐标和目的坐标,及控制装置内置的铝箔轧制车间导航地图,自动生成搬运路线,智能叉车在惯性导航装置的引导下,沿着搬运路线完成智能托盘搬运任务;惯性导航装置还用于实时动态定位智能叉车自身坐标,并定时将自身实时坐标和状态传输给控制中心;机器视觉辅助定位装置设有两个,一个设置在智能叉车前部,用于智能叉车行进避障及
叉起智能托盘搬运时的辅助定位,通过机器视觉辅助定位装置拍摄到的智能托盘的实际位置,自动矫正智能叉车与智能托盘的位置关系,防止智能托盘摆放位置出现偏差时,智能叉车无法顺利铲起智能托盘;另一个机器视觉辅助定位装置设置在智能叉车底部,其用于侦测设置在智能叉车停车位处设置的十字光标,当智能叉车处于工作状态时其处于关闭状态,当智能叉车处于非工作状态时,会自动驶回智能叉车停车位,打开设置在智能叉车底部的机器视觉辅助定位装置,通过智能叉车底部的机器视觉辅助定位装置检测智能叉车停车位的十字光标,用于自身坐标的校准,消除智能叉车在工作过程中惯性导航装置中产生的累计误差。
6.进一步的,智能托盘包括托盘底座、支撑柱、托盘,支撑柱固定设置在托盘底座上部,托盘固定设置在支撑柱上部;托盘底座的一侧面设置有托盘定位/通信装置,托盘定位/通信装置上设置有阅读器天线b、微功率无线通信天线,托盘底座的相对另一侧面设置有阅读器天线a,阅读器天线a、阅读器天线b用于与智能托盘放置位置两侧的托盘定位传感器通信,通过读取智能托盘放置位置两侧托盘定位传感器内部的id号,确定智能托盘自身放置位置的坐标信息,微功率无线通信天线用于与控制中心通信;支撑柱内侧面固定设置有应变传感器,当智能托盘上放置有铝箔成品时,应变传感器有相应的信号输出,将所有应变传感器的输出结果转换为所承载的重量后进行累加,即可计算出智能托盘上所放置铝箔成品的重量;位于同一侧的支撑柱,其中一个支撑柱外侧面固定设置有电子标签,电子标签采用电子纸,电子纸显示内容包括托盘定位/通信装置自身id号、自身当前位置坐标、自身所放置成品重量、成品放置时间等信息,以上信息用文字和二维码两种方式同时显示,用于异常情况下通过人工对智能托盘的相关信息进行核对,也可以通过二维码扫描、微功率无线通信将智能托盘的相关信息重新录入控制中心。
7.进一步的,托盘定位传感器包括传感器基座、uhf rfid定位标签;传感器基座为梯形块状,其梯形顶面上设有基座主槽,梯形两侧面上分别设有基座天线槽;uhf rfid定位标签包括定位标签主体、定位标签天线,定位标签天线设有两个,位于定位标签主体两侧,为“h”形薄膜状;定位标签主体固定设置在基座主槽中,定位标签天线固定设置在基座天线槽中;补充说明的是,仅使用uhf rfid定位标签粘贴在地面,即可实现托盘定位传感器的功能,但考虑到将uhf rfid定位标签直接粘贴在地面时,如果有重物压在uhf rfid定位标签上,可能会造成uhf rfid定位标签内芯片的损坏,所以增加传感器基座并将对uhf rfid定位标签设置在传感器基座的凹槽中对其进行保护;将定位标签天线设置在传感器基座的斜面中,目的是增加定位标签天线对托盘定位/通信装置发射电磁波的反射面积,以达到更加稳定、可靠的通信效果;另外,设置传感器基座也是作为智能叉车在放置智能托盘时的视觉定位基准,在放置智能托盘时,通过设置在智能叉车前部的机器视觉辅助定位装置采集智能托盘放置区域两侧的传感器基座位置,校准智能叉车与智能托盘放置区域的相对位置,保证智能托盘放置位置的准确性。
8.进一步的,托盘定位/通信装置包括外壳及托盘定位/通信模块,托盘定位/通信模块固定设置在外壳内;托盘定位/通信模块包括阅读器、单片机、显示驱动模块、采样模块、信号放大/滤波模块、信号切换模块、应变传感器、无线通信模块、加速度传感器;阅读器、单片机、采样模块、信号放大/滤波模块、信号切换模块、应变传感器依次电性连接;单片机还分别与显示驱动模块、信号切换模块、无线通信模块、加速度传感器电性连接;显示驱动模
块与电子标签电性连接;阅读器与阅读器天线a、阅读器天线b电性连接;正常情况下托盘定位/通信模块的单片机处于休眠模式,加速度传感器处于工作模式,无线通信模块处于间断侦听模式,其余模块均处于断电状态(电子标签处于断电模式时仍能显示相关信息),以节省电源消耗,延长电池待机时间;无线通信模块处于间断侦听模式,是为了监听控制中心的广播命令,如初始化广播指令;当智能托盘的状态或位置发生改变时,如在智能托盘上放置铝箔成品、或智能叉车搬运智能托盘时,智能托盘会发生振动或位移,此时加速度传感器输出信号唤醒单片机,单片机控制对各功能模块上电,使托盘定位/通信模块处于正常工作状态;托盘定位/通信模块处于正常工作状态时,阅读器通过阅读器天线a、阅读器天线b发出射频信号,检测智能托盘位置坐标是否发生改变,如果阅读器无法同时收到两个相邻的托盘定位传感器传回的id号,且加速度传感器持续有信号输出,表示智能托盘处于运输状态;如果阅读器同时收到两个相邻的托盘定位传感器传回的id号,但其信号强度在发生改变,且加速度传感器持续有信号输出,表示智能托盘正处于进入智能托盘放置位置状态;如果如果阅读器同时收到两个相邻的托盘定位传感器传回的id号,且id号有变化,且信号强度稳定,且加速度传感器无信号输出,表示智能托盘处于新的坐标位置,此时无线通信模块工作,将智能托盘自身id号及两个新的托盘定位传感器的id号传输给控制中心,控制中心更新其内部存储的信息,保证铝箔轧制车间内所有智能托盘的位置信息始处于最新状态;当加速度传感器输出信号状态经历一次由静止
‑
振动
‑
静止的变化过程,单片机均执行一次状态检测过程,通过采样模块采集所有应变传感器的输出,将所有应变传感器的输出结果转换为所承载的重量后进行累加,判断智能托盘的状态是否发生变化;如果计算出智能托盘的状态发生变化,则通过微功率无线通信上传至控制中心,控制中心更新其内部存储的信息,保证铝箔轧制车间内所有智能托盘的状态信息始处于最新状态。
9.进一步的,铝箔轧制车间规划设有生产区、智能叉车停放区、物料存放区、出货区;生产区设置有轧制生产机台,轧制生产机台侧边对应设有一个暂存位,暂存位两侧对称设置有托盘定位传感器,传感器内均设有自身的id码,暂存位用于暂时放置轧制生产机台生产出的铝箔成品;智能叉车停放区设有若干智能叉车停放位,智能叉车停放位内设有智能叉车坐标校准基准,智能叉车坐标校准基准设为白色十字光标,具有良好的反光能力,智能叉车自动驶回智能叉车停车位时,通过设置在智能叉车底部的机器视觉辅助定位装置检测智能叉车停车位的十字光标,用于自身坐标的校准,消除智能叉车在工作过程中惯性导航装置中产生的累计误差;物料存放区设有若干物料存放位,出货区设有若干出货位,物料存放位、出货位两侧对称设置有托盘定位传感器,传感器内均设有自身的id码;铝箔轧制车间以其中一个智能叉车停放位内的智能叉车坐标校准基准为坐标原点,建立铝箔轧制车间的平面坐标系,暂存位、智能叉车停放位、物料存放位、出货位均设有在平面坐标系中的平面坐标;暂存位、物料存放位、出货位的平面坐标与其两侧设置的托盘定位传感器的id号相对应,智能托盘上设置的托盘定位/通信装置与暂存位、物料存放位、出货位两侧设置的托盘定位传感器交互通信,得到托盘定位传感器的id号,即得到智能托盘自身放置位置的坐标信息。
10.进一步的,阅读器天线a、阅读器天线b与定位标签天线之间的通信距离为50厘米;设置此通信距离的目的是防止托盘定位/通信装置与暂存位、物料存放位、出货位两侧设置的托盘定位传感器通信时,出现通信串扰干扰。
11.一种铝箔轧制车间自动化物流系统的运行方法,包括智能托盘自身坐标及状态的确定方法、智能叉车运行控制方法;智能托盘自身坐标的确定方法:智能托盘正常情况下放置在暂存位或物料存放位内,智能托盘通过托盘定位/通信模块与暂存位或物料存放位或出货位两侧的托盘定位传感器通信,读取托盘定位传感器内的id码,根据读取到的暂存位或物料存放位两侧托盘定位传感器的id码,确定自身所在暂存位或物料存放位的平面坐标,此坐标即为智能托盘的自身坐标,智能托盘将自身坐标通过微功率无线通信上传至控制中心;智能托盘自身状态的确定方法:智能托盘自身状态是指智能托盘上是否放置有铝箔成品及铝箔成品的重量;智能托盘通过托盘定位/通信模块的加速度传感器检测到的振动或位移信号,作为判断自身状态是否发生变化的触发信号,以便唤醒托盘定位/通信模块;托盘定位/通信模块对所有应变传感器的输出进行检测,将所有应变传感器的输出结果转换为所承载的重量后进行累加,计算出智能托盘上所放置铝箔成品的重量,并通过微功率无线通信上传至控制中心;智能叉车运行控制方法:控制中心存储有所有智能托盘的状态信息及位置信息,根据生产及出货需求,控制中心做出决策生成搬运指令,搬运指令包括需搬运智能托盘的现有坐标及目的坐标;搬运指令通过微功率无线传输至智能叉车,智能叉车的控制装置根据需搬运智能托盘的现有坐标和目的坐标及控制装置内置的铝箔轧制车间导航地图,自动生成搬运路线,惯性导航装置控制智能叉车沿着搬运路线完成智能托盘的搬运任务。
12.进一步的,智能托盘在进入暂存位、物料存放位、出货位时,通过托盘定位/通信模块接收到的暂存位或物料存放位或出货位两侧的托盘定位传感器反射回的信号强度变化,判断智能托盘进入暂存位、物料存放位、出货位的深度是否到位;其具体过称为:智能托盘在进入暂存位、物料存放位、出货位时,当阅读器天线a、阅读器天线b与暂存位、物料存放位、出货位两侧的托盘定位传感器距离小于50厘米时,阅读单元接收到托盘定位传感器反射回的射频信号,且射频信号的强度(rssi)随阅读器天线a、阅读器天线b与托盘定位传感器之间的距离发生变化;当射频信号的强度(rssi)达到最大值时,表示智能托盘进入暂存位、物料存放位、出货位的深度到位,此时智能叉车停止前进,放下智能托盘并退出。
13.进一步的,智能托盘在进入暂存位、物料存放位、出货位时,通过托盘定位/通信模块接收到的暂存位或物料存放位或出货位两侧的托盘定位传感器反射回的信号强度差,判断智能托盘是否处于暂存位、物料存放位、出货位宽度方向的中间位置;其具体方法为:当智能托盘放置在暂存位、物料存放位、出货位时,如果智能托盘与暂存位、物料存放位、出货位两侧的距离不相等时,阅读器天线a、阅读器天线b接收到的射频信号强度(rssi)将不相等,通过计算阅读器天线a、阅读器天线b接收到的射频信号强度(rssi)的差值,即可获得阅读器天线a、阅读器天线b与两侧托盘定位传感器的距离差,此距离差表示智能托盘偏离暂存位、物料存放位、出货位宽度方向中间位置的程度;此距离差传输到控制中心,由控制中心判断是否超出设定阈值,如果超出设定阈值,控制中心发出控制指令给智能叉车,重新矫正智能托盘的放置位置,直至托盘定位/通信模块接收到的暂存位或物料存放位或出货位两侧的托盘定位传感器反射回的信号强度差在设定阈值范围内。
14.由于采用如上所述的技术方案,本发明具有如下有益效果:本发明公开的一种铝箔轧制车间自动化物流系统及运行方法,包括控制中心、智能叉车、智能托盘、托盘定位传
感器;托盘定位传感器固定设置在铝箔轧制车间地面的设定位置,智能托盘与托盘定位传感器通过超高频射频信号通信,确定自身位置信息;智能托盘通过自身设置的传感器,确定自身是否放置有铝箔成品及铝箔成品重量的状态信息;智能托盘将自身的位置信息及状态信息通过微功率无线通信传输给控制中心,由控制中心通过微功率无线控制智能叉车对智能托盘进行搬运,实现铝箔轧制车间生产过程物流的自动化;本发明的铝箔轧制车间自动化物流系统不仅适用于新建铝箔轧制车间,而且适用现有已经建成生产的铝箔轧制车间的物流系统自动化改造;在对现有铝箔轧制车间的物流系统自动化改造时,通过在生产车间的地面设置托盘定位传感器及对现有托盘进行智能化改造,即可实现运输托盘的定位问题;通过增加控制中心,实现对铝箔轧制车间所有托盘信息的掌控;通过增加智能叉车,实现对托盘的自动运输;在整个铝箔轧制车间物流系统自动化改造中,仅智能叉车的成本较高,而定位传感器、托盘智能化改造、及控制中心投入的成本极低,同时改造工程量极小,因此具有实施简单、总体成本可控的优点。
附图说明
15.图1为铝箔轧制车间自动化物流系统原理示意图;图2为智能托盘外观示意图一;图3为智能托盘外观示意图二;图4为托盘定位传感器外观示意图;图5为托盘定位传感器结构爆炸示意图;图6为uhf rfid定位标签外形示意图;图7为托盘定位/通信模块原理方框图;图8为铝箔轧制车间平面规划示意图;图9为物料存放区托盘定位传感器布置示意图;图10为暂存位托盘定位传感器布置示意图。
16.图中:1、控制中心;2、生产区;2.1、轧制生产机台;2.2、暂存位;3、智能叉车停放区;3.1、智能叉车停放位;3.2、智能叉车坐标校准基准;4、智能叉车;5、物料存放区;5.1、物料存放位;6、物流动线;7、智能托盘;7.1、托盘底座;7.1.1、托盘定位/通信装置;7.1.2、阅读器天线a; 7.2、支撑柱;7.2.2、应变传感器;7.2.1、电子标签;7.3、托盘;8、托盘定位传感器;8.1、传感器基座;8.1.1、基座主槽;8.1.2、基座天线槽;8.2、uhf rfid定位标签;8.2.2、定位标签主体;8.2.1、定位标签天线;9、出货区;9.1、出货位。
具体实施方式
17.通过下面的实施例可以详细的解释本发明,公开本发明的目的旨在保护本发明范围内的一切技术改进。
18.一种铝箔轧制车间自动化物流系统,包括控制中心1、智能叉车4、智能托盘7、托盘定位传感器8;托盘定位传感器8设有若干个,其固定设置在铝箔轧制车间地面的设定位置,智能托盘7与托盘定位传感器8通过超高频射频信号通信,确定自身位置信息;智能托盘7与控制中心1之间通过微功率无线通信连接,将自身位置信息及状态信息传输到控制中心1;智能叉车4与控制中心1通过微功率无线通信连接,控制中心1根据铝箔轧制车间智能托盘7
的位置信息及状态信息控制智能叉车4对智能托盘7进行搬运;智能叉车4上设置有控制装置、惯性导航装置、机器视觉辅助定位装置,控制装置中设置有铝箔轧制车间导航地图;当需要搬运智能托盘7时,控制中心1发出包含需搬运智能托盘7的现有坐标和目的坐标的搬运指令至智能叉车4,智能叉车4的控制装置根据需搬运智能托盘7的现有坐标和目的坐标,及控制装置内置的铝箔轧制车间导航地图,自动生成搬运路线,完成智能托盘7搬运任务;惯性导航装置用于定位智能叉车4自身坐标;机器视觉辅助定位装置设有两个,一个设置在智能叉车4前部,用于智能叉车4行进避障及智能托盘7搬运时的辅助定位,另一个设置在智能叉车4底部,用于自身坐标的校准;智能托盘7包括托盘底座7.1、支撑柱7.2、托盘7.3,支撑柱7.2固定设置在托盘底座7.1上部,托盘7.3固定设置在支撑柱7.2上部;托盘底座7.1的一侧面设置有托盘定位/通信装置7.1.1,托盘底座7.1的相对另一侧面设置有阅读器天线a7.1.2,托盘定位/通信装置7.1.1上设置有阅读器天线b、微功率无线通信天线;支撑柱7.2内侧面固定设置有应变传感器7.2.2;位于同一侧的支撑柱7.2,其中一个支撑柱7.2外侧面固定设置有电子标签7.2.1;托盘定位传感器8包括传感器基座8.1、uhf rfid定位标签8.2;传感器基座8.1为梯形块状,其梯形顶面上设有基座主槽8.1.1,梯形两侧面上分别设有基座天线槽8.1.2;uhf rfid定位标签8.2包括定位标签主体8.2.2、定位标签天线8.2.1,定位标签天线8.2.1设有两个,位于定位标签主体8.2.2两侧,为“h”形薄膜状;定位标签主体8.2.2固定设置在基座主槽8.1.1中,定位标签天线8.2.1固定设置在基座天线槽8.1.2中;托盘定位/通信装置7.1.1包括外壳及托盘定位/通信模块,托盘定位/通信模块固定设置在外壳内;托盘定位/通信模块包括阅读器、单片机、显示驱动模块、采样模块、信号放大/滤波模块、信号切换模块、应变传感器、无线通信模块、加速度传感器;阅读器、单片机、采样模块、信号放大/滤波模块、信号切换模块、应变传感器依次电性连接;单片机还分别与显示驱动模块、信号切换模块、无线通信模块、加速度传感器电性连接;显示驱动模块与电子标签(7.2.1)电性连接;阅读器与阅读器天线a7.1.2、阅读器天线b电性连接;无线通信模块与微功率无线通信天线电性连接;铝箔轧制车间规划设有生产区2、智能叉车停放区3、物料存放区5、出货区9;生产区2设置有轧制生产机台2.1,轧制生产机台2.1侧边对应设有一个暂存位2.2,暂存位2.2两侧对称设置有托盘定位传感器8;智能叉车停放区3设有若干智能叉车停放位3.1,智能叉车停放位3.1内设有智能叉车坐标校准基准3.2;物料存放区5设有若干物料存放位5.1,出货区9设有若干出货位9.1,物料存放位5.1、出货位9.1两侧对称设置有托盘定位传感器8;以其中一个智能叉车停放位3.1内的智能叉车坐标校准基准3.2为坐标原点建立平面坐标系,暂存位2.2、智能叉车停放位3.1、物料存放位5.1均设有在平面坐标系中的平面坐标;暂存位2.2、物料存放位5.1两侧设置的托盘定位传感器8内均设有自身的id码,暂存位2.2、物料存放位5.1两侧托盘定位传感器8内的id码对应一个暂存位2.2或物料存放位5.1的平面坐标;阅读器天线a7.1.2、阅读器天线b与定位标签天线8.2.1之间的通信距离为50厘米。
19.一种铝箔轧制车间自动化物流系统的运行方法,包括智能托盘7自身坐标及状态的确定方法、智能叉车4运行控制方法;
智能托盘7自身坐标的确定方法:智能托盘7正常情况下放置在暂存位2.2或物料存放位5.1内,智能托盘7通过托盘定位/通信模块与暂存位2.2或物料存放位5.1或出货位9.1两侧的托盘定位传感器8通信,读取托盘定位传感器8内的id码,根据读取到的暂存位2.2或物料存放位5.1两侧托盘定位传感器8的id码,确定自身所在暂存位2.2或物料存放位5.1的平面坐标,此坐标即为智能托盘7的自身坐标,智能托盘7将自身坐标通过微功率无线通信上传至控制中心1;智能托盘7自身状态的确定方法:智能托盘7自身状态是指智能托盘7上是否放置有铝箔成品及铝箔成品的重量;智能托盘7通过托盘定位/通信模块的加速度传感器检测到的振动或位移信号,作为判断自身状态是否发生变化的触发信号,托盘定位/通信模块对所有应变传感器的输出进行检测,将所有应变传感器的输出结果转换为所承载的重量后进行累加,计算出智能托盘7上所放置铝箔成品的重量,并通过微功率无线通信上传至控制中心1;智能叉车4运行控制方法:控制中心1存储有所有智能托盘7的状态信息及位置信息,根据生产及出货需求,控制中心1做出决策生成搬运指令,搬运指令包括需搬运智能托盘7的现有坐标及目的坐标;搬运指令通过微功率无线传输至智能叉车4,智能叉车4的控制装置根据需搬运智能托盘7的现有坐标和目的坐标及控制装置内置的铝箔轧制车间导航地图,自动生成搬运路线,控制智能叉车4完成智能托盘7的搬运任务;智能托盘7在进入暂存位2.2、物料存放位5.1、出货位9.1时,通过托盘定位/通信模块接收到的暂存位2.2或物料存放位5.1或出货位9.1两侧的托盘定位传感器8反射回的信号强度变化,判断智能托盘7进入暂存位2.2、物料存放位5.1、出货位9.1的深度是否到位;智能托盘7在进入暂存位2.2、物料存放位5.1、出货位9.1时,通过托盘定位/通信模块接收到的暂存位2.2或物料存放位5.1或出货位9.1两侧的托盘定位传感器8反射回的信号强度差,判断智能托盘7是否处于暂存位2.2、物料存放位5.1、出货位9.1宽度方向的中间位置。
20.铝箔轧制车间自动化物流系统在初次启用时,由人工将智能托盘放置在暂存位2.2、物料存放位5.1中,并将智能叉车设置在智能叉车停放位3.1;控制中心发出初始化广播指令,采集所有智能托盘的位置及状态信息,并初始化智能叉车的原始坐标信息与铝箔轧制车间平面坐标系保持一致;当某一轧制生产机台2.1生产即将完成,需要下料时,通知控制中心1;控制中心1检索所有智能托盘7的位置及状态信息,选择距离轧制生产机台2.1最近的空置智能托盘7,并将空置智能托盘7的现有坐标信息及目的坐标信息(轧制生产机台对应侧边的暂存位坐标)传输给选定的智能叉车4;智能叉车4的控制装置根据需搬运智能托盘7的现有坐标和目的坐标,及控制装置内置的铝箔轧制车间导航地图,自动生成搬运路线,由惯性导航装置引导智能叉车4循着搬运路线,完成智能托盘7搬运任务;完成搬运任务后的智能叉车4继续执行控制中心1传输的新的搬运指令;智能托盘7被放置在轧制生产机台2.1对应侧边的暂存位2.2后,智能托盘7通过托盘定位/通信装置7.1.1与暂存位2.2两侧的盘定位传感器8通信交互,得到新的位置坐标,并传输到控制中心;当铝箔成品放置在智能托盘7上时,智能托盘7发生振动或位置偏移,托
盘定位/通信装置7.1.1重新检测应变传感器7.2.2的输出并计算出铝箔成品的重量,并将智能托盘7新的状态信息传输给控制中心1;控制中心1收到智能托盘7的新的状态信息后,判断位于暂存位2.2内的智能托盘7完成铝箔成品的装载,检索所有智能托盘7的位置信息,判断出空置物料存放位5.1,将暂存位2.2内完成铝箔成品装载的智能托盘7的现有坐标及空置物料存放位5.1的目的坐标传输给选定的智能叉车4;智能叉车4的控制装置根据需搬运智能托盘7的现有坐标和目的坐标,及控制装置内置的铝箔轧制车间导航地图,自动生成搬运路线,由惯性导航装置引导智能叉车4循着搬运路线,完成智能托盘7搬运任务;完成搬运任务后的智能叉车4继续执行控制中心1传输的新的搬运指令;智能托盘7被放置在空置物料存放位5.1后,智能托盘7通过托盘定位/通信装置7.1.1与暂存位2.2两侧的盘定位传感器8通信交互,得到新的位置坐标;并且托盘定位/通信装置7.1.1重新检测应变传感器7.2.2的输出并计算出铝箔成品的重量,并将智能托盘7新的坐标及状态信息传输给控制中心1;智能叉车4在工作过程中,定时将自身位置坐标及状态(繁忙或空闲)传输给控制中心1;当智能叉车4无新的搬运指令时,自动返回智能叉车停车位3.2,通过设置在智能叉车4底部的机器视觉辅助定位装置检测智能叉车停车位的十字光标,用于自身坐标的重新校准,消除智能叉车4在工作过程中惯性导航装置中产生的累计误差。
21.本发明未详述部分为现有技术。