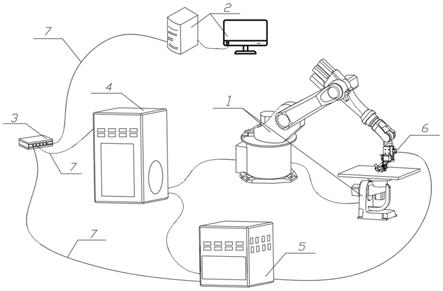
1.本发明属于增材制造技术相关技术领域,更具体地,涉及一种实时同步沉积的工业机器人熔融沉积制造系统及应用。
背景技术:2.增材制造是一种数字化成形技术,通过熔融材料的分层堆积,快速成形得到实体零件,增材制造技术具有材料利用率高、可成形复杂结构、自动化程度高一级成形效率高的特点,在快速制模、医学、生物工程、教育、建筑、工业设计等众多领域都有广泛的应用,常见的聚合物增材制造技术包括光敏树脂立体光固化(sla)、选择性激光烧结(sls)以及熔融沉积或熔丝制造(fdm/fff)。
3.熔融沉积(fdm)成形耗材是如丙烯腈-丁二烯-苯乙烯共聚物(abs)、聚乳酸(pla)、聚醚醚酮(peek)等聚合物丝材,fdm成形技术的完整过程为:(1)首先建立目标零件的三维模型;(2)然后对零件三维模型进行离散化,即分层切片及路径规划,获得零件成形的程序代码g-code;(3)将程序写入fdm打印设备,设备读取程序,将聚合物丝材送至挤出喷头,喷头加热熔融丝材聚合物;(4)喷头按一定速度挤出熔融聚合物,同时运动机构驱动喷头按照规划好的路径运动;(5)熔融聚合物快速固化,逐层沉积打印得到最终实体。
4.目前,fdm成形设备有多样形式,均是运动机构上集成沉积头模块的方式,主要有三轴式、delta并联机构式、串联拟人臂多轴机器人式等,三轴式和delta并联机构式成形设备目前相对已经很成熟,串联式拟人臂多轴机器人成形设备目前研究和应用较少,目前仍存在如下不足与问题:(1)串联式多轴机器人的运动和控制方式与机械数控不同,传统的路径程序g代码不再适用机器人控制系统,目前大部分主流机器人控制系统都有各自的编程语言,g代码路径程序不再适用,对路径的分层规划的提出了新的要求,路径规划的程序必须适应机器人系统并且能够方便传输至机器人;(2)成形过程中打印速度与挤料速度需要进行耦合与匹配,必须建立合理的数值匹配关系,机器人系统是对外封装的,内部系统不可更改、扩展,只提供对外接口进行通信,fdm打印头模块单独集成在机器人机构末端,打印头控制系统与机器人控制系统相互独立,打印速度与挤料速度之间没有关联,如果进行独立的控制,易出现程序的不同步以及行程冲突的问题,控制难度大,并且严重影响成形质量;(3)两个相对独立的系统进行同时的控制,同步挤料控制是一个十分关键的问题,也就是机器人运动与挤料速度不匹配,挤料量不精确,从而影响精度,并且误差会随着时间累积,这将严重影响到整个零件的成形质量与精度。
技术实现要素:5.针对现有技术的以上缺陷或改进需求,本发明提供了一种实时同步沉积的工业机器人熔融沉积制造系统及应用,实现沉积头与机器人的同步控制,解决了打印速度与挤料速度的耦合和匹配问题。
6.为实现上述目的,按照本发明的一个方面,提供了一种实时同步沉积的工业机器
人熔融沉积制造系统,所述系统包括:工业机器人,所述工业机器人包括机械臂、变位机、成形基板以及熔融沉积头,其中,所述熔融沉积头设于所述机械臂的端部;所述变位机设于所述成形基板的下部,用于调整所述成形基板的位姿;所述成形基板用于承载所述熔融沉积头的沉积浆料;沉积头控制系统,用于控制和监测熔融沉积头的作动;工业机器人控制系统,用于控制和监测所述机械臂和变位机的作动;上位机控制系统与所述沉积头控制系统和工业机器人控制系统通信连接,所述沉积头控制系统和工业机器人控制系统通信连接。
7.优选地,所述沉积头控制系统控制熔融沉积头的控制模型为:
[0008][0009]
0.25d≤h≤d
[0010]
(d+h)≤w≤(dw+h)
[0011]
其中,vm为熔融沉积头的送料电机的转速,w为沉积宽度,h为沉积层高,v2为机器人末端带动熔融沉积头运动的速度,d为被熔融沉积头中送入丝材的直径,d为熔融沉积头的喷嘴内径,dw为熔融沉积头的喷嘴外径,ratio为挤出倍率因子。
[0012]
优选地,所述沉积头控制系统还包括反馈模块,所述反馈模块用于修正所述机器人末端带动熔融沉积头运动的速度,所述反馈模块为:
[0013][0014][0015]
其中,为下一时刻机器人末端带动熔融沉积头运动修正后的速度;为下一时刻机器人末端带动熔融沉积头运动的实际速度;f
t
为上一时刻送丝电机控制脉冲频率;θ为每个脉冲下送丝电机轴转动的角度;k为修正因子,k=0~1;δt为沉积头控制系统和工业机器人控制系统之间传输数据的周期;p为预设修正开启门限。
[0016]
优选地,所述系统还包括以太网交换机,所述上位机控制系统通过所述以太网交换机与所述沉积头控制系统和工业机器人控制系统连接;所述沉积头控制系统和工业机器人控制系统之间通过i/o接口连接。
[0017]
优选地,所述工业机器人控制系统还包括模拟量输出模块,所述模拟量输出模块用于将机械臂的速度映射为电压;所述沉积头控制系统还包括模拟量输入模块,所述模拟量输入模块用于将所述电压映射为速度。
[0018]
优选地,所述上位控制系统包括服务器和显示器,所述上位控制系统用于对成形过程进行监测和控制。
[0019]
优选地,所述熔融沉积头包括沉积头信号集成接口固定板、送丝电机单元,散热风扇、加热块、喷头以及用于与机械臂末端连接的法兰。
[0020]
按照本发明的另一个方面,提供了一种实时同步沉积的工业机器人熔融沉积制造系统的应用,包括如下步骤:s1:采用所述上位机控制系统生成待制造零件的三维模型,并
规划成形路径和生成工序;s2:所述工业机器人控制系统接收所述成形路径和工序,并对应触发所述沉积头控制系统进行预热,待所述沉积头控制系统预热完成即向所述工业机器人控制系统发送执行信号,以使所述机械臂开始作动,逐层沉积,直至生成零件。
[0021]
总体而言,通过本发明所构思的以上技术方案与现有技术相比,本发明提供的实时同步沉积的工业机器人熔融沉积制造系统及应用具有如下有益效果:
[0022]
1.上位机控制系统与工业机器人控制系统和沉积头控制系统连接通信,实现沉积头与机器人的同步控制,解决了打印速度与挤料速度的耦合和匹配问题。
[0023]
2.通过建立机器人速度匹配挤料量模型,通过沉积头控制系统实时检测机器人运动速度,同时采用模拟量输出模块,将机械臂速度范围线形映射为连续的模拟量电压输出,快速跟随和响应机械臂速度,快速计算挤料速度,精准匹配控制挤料量,提高成形精度,实现工业机器人熔融沉积成形过程的高稳定性、快速响应性和零件的高精度和高质量。
[0024]
3.上位机控制系统生成的规划路径和控制工序通过以太网直接与机器人系统实时传输,由离线的代码模式转变为实时的数据传输,解决路径规划、g代码程序不兼容不适用、数据如何有效传输的问题。
[0025]
4.工业机器人控制系统与沉积头控制系统通过以太网以及i/o接口建立通信,通过快速互换信号来实现机器人系统运动控制与沉积头系统挤出控制的耦合与关联,依据机器人的实时运动状态来控制沉积头的挤出动作,保证系统关联性,解决打印速度与挤料速度的耦合和匹配问题,提高成形过程控制的稳定性、灵活性和精确性。
附图说明
[0026]
图1是本实施例实时同步沉积的工业机器人熔融沉积制造系统的结构示意图;
[0027]
图2是本实施例工业机器人的结构示意图;
[0028]
图3是本实施例熔融沉积头的结构示意图;
[0029]
图4a是本实施例构建的挤料计算的几何模型一示意图;
[0030]
图4b是本实施例构建的挤料计算的几何模型另一示意图;
[0031]
图5是本实施例所构建的控制系统拓扑关系示意图;
[0032]
图6是本实施例所构建的控制系统的控制逻辑流程图。
[0033]
在所有附图中,相同的附图标记用来表示相同的元件或结构,其中:
[0034]
1-工业机器人;2-上位机控制系统;3-以太网交换机;4-工业机器人控制系统;5-沉积头控制系统;6-熔融沉积头;7-网络电缆;1-1-机械臂;1-2-成形基板;1-3-变位机;6-1-集成接口;6-2-固定板;6-3-送丝电机单元;6-4-散热风扇;6-5-加热块;6-6-喷头;6-7-法兰。
具体实施方式
[0035]
为了使本发明的目的、技术方案及优点更加清楚明白,以下结合附图及实施例,对本发明进行进一步详细说明。应当理解,此处所描述的具体实施例仅仅用以解释本发明,并不用于限定本发明。此外,下面所描述的本发明各个实施方式中所涉及到的技术特征只要彼此之间未构成冲突就可以相互组合。
[0036]
请参阅图1,本发明提供了一种实时同步沉积的工业机器人熔融沉积制造系统,所
述系统包括工业机器人1、沉积头控制系统5、工业机器人控制系统4、上位机控制系统2等,其中:
[0037]
如图2所示,工业机器人1包括机械臂1-1、变位机1-3、成形基板1-2以及熔融沉积头6,其中,所述熔融沉积头6设于所述机械臂1-1的端部;所述变位机1-3设于所述成形基板1-2的下部,用于调整所述成形基板1-2的位姿;所述成形基板1-2用于承载所述熔融沉积头6的沉积熔融聚合物。其是fdm成形工艺的运动执行机构,具有超过3个数量的自由度,能高精度实现复杂的路径轨迹,用于带动沉积头进行沉积路径运动。机械臂1-1与变位机1-3连接组成具有8个自由度的运动机构,其中机械臂6个轴的自由度,变位机有2个轴的自由度,几乎任意的角度和轨迹的运动都能控制实现,能够完成复杂的轨迹运动,可实现平面运动,也可以实现曲面运动,可以满足实际的熔融沉积制造,工业机器人具有很高的重复定位精度与运动精度,能够进行自由编程,并且能够与如matlab、c/c++等多种通编程语言兼容,具有良好的可控性与扩展性。
[0038]
如图3所示,所述熔融沉积头6包括沉积头信号集成接口6-1、固定板6-2、送丝电机单元6-3,散热风扇6-4、加热块6-5、喷头6-6以及用于与机械臂末端连接的法兰6-7。沉积头所有的信号集成在集成接口6-1上,与沉积头控制形态连接,实现聚合物丝材的送入、熔融、挤出动作以及喷头的散热、基材的加热、温度的检测与反馈操作。
[0039]
工业机器人控制系统4是与工业机器人1配套集成的独立控制系统,直接与工业机器人1相连接,用于机器人的所有运动的计算与控制,例如,控制和监测所述机械臂1-1和变位机1-3的作动,并且具有通信接口与外界设备进行通信。
[0040]
上位机控制系统2包括微型服务器和显示器,作为工艺控制和监测窗口,实现成形零件的建模、路径规划、工艺规划、输出成形程序、可视化等前置工作,并在程序执行时监测成形过程。
[0041]
沉积头控制系统5用于控制和监测熔融沉积头6的作动。
[0042]
所述系统还包括以太网交换机3,所述上位机控制系统2通过所述以太网交换机3与所述沉积头控制系统5和工业机器人控制系统4连接;所述沉积头控制系统5和工业机器人控制系统4之间通过i/o接口连接,可以实现快速通信,使得机器人能够直接发送控制信号到沉积头控制系统,控制沉积头的各个动作。具体的,上位机控制系统2、沉积头控制系统5以及工业机器人控制系统4之间通过网络电缆7相连,共享和传输数据,实现三个系统的互相通信,使得上位机系统数据与信号能够快速传输至机器人控制系统和沉积头控制系统,达到上位机总控制和监测的目的。
[0043]
所述工业机器人控制系统4还包括模拟量输出模块,所述模拟量输出模块用于将机械臂的速度映射为电压;所述沉积头控制系统5还包括模拟量输入模块,所述模拟量输入模块用于将所述电压映射为速度。在控制过程中,机器人控制系统通过本身的接口,实时输出机械臂的运动速度,速度通过模拟量输出模块线形映射为相应的电压值,沉积头控制系统监测机械臂运动速度对应的模拟量电压值,依据机械臂速度,根据建立好的挤料模型计算严格匹配的挤料速度,使得机械臂运动速度能够耦合控制挤料速度,在成形过程中实现和机械臂运动同步的挤料速度控制,保证和提高挤料量的精确性。
[0044]
所述沉积头控制系统5控制熔融沉积头6的控制模型为:
[0045][0046]
0.25d≤h≤d
[0047]
(d+h)≤w≤(dw+h)
[0048]
其中,vm为熔融沉积头6的送料电机的转速,w为沉积宽度,h为沉积层高,v2为机器人末端带动熔融沉积头6运动的速度,d为被熔融沉积头6中送入丝材的直径,d为熔融沉积头6的喷嘴内径,dw为熔融沉积头6的喷嘴外径,ratio为挤出倍率因子,如图4a和4b所示。
[0049]
所述沉积头控制系统5还包括反馈模块,所述反馈模块用于修正所述机器人末端带动熔融沉积头6运动的速度,所述反馈模块为:
[0050][0051][0052]
其中,为下一时刻机器人末端带动熔融沉积头6运动修正后的速度;为下一时刻机器人末端带动熔融沉积头6运动的实际速度;f
t
为上一时刻送丝电机控制脉冲频率;θ为每个脉冲下送丝电机轴转动的角度;k为修正因子,k=0~1;δt为沉积头控制系统5和工业机器人控制系统4之间传输数据的周期;p为预设修正开启门限。
[0053]
最终,基于给定的工艺参数层高h、沉积宽度w、材料参数丝材直径d以及其他参数,根据机器人的运动速度v2可计算确定一个精确的挤料速度vm,获得匹配的精确挤料量。该模型将挤料速度与机器人运动速度关联匹配,挤料速度将时刻跟随机械臂运动速度的变化而变化和修正,并且采用模拟量输出模块将机械臂速度范围线形映射为连续变化的电压值,利用模拟量输出电压能够快速、良好地跟随速度变化以及延迟可编程的特性,通过实时监测获取的机械臂速度v2变化对应的电压来连续计算挤料速度vm,能进一步获得稳定的、精确的、符合参数设定的沉积量,实现机器人运动和材料沉积的同步控制,提高沉积精度和稳定性。同时通过调节挤出倍率因子ratio,实际工艺过程中不同的工艺方案可以灵活调节速度比例,进而调节控制挤料量,适应不同的材料、工艺以及其他参数的耦合影响,提高成形工艺的可控性、灵活性和适应性。
[0054]
图5是按照本发明的优选实施例所构建的控制系统拓扑关系示意图,如图5所示,工业机器人熔融沉积系统由上位机系统、机器人控制系统、沉积头控制系统组成,系统各自封装,通过接口通信,协同工作。上位机系统作为熔融沉积成形工艺控制及检测窗口,实现建模
→
路径规划
→
工艺规划
→
路径程序的流程并通过gui实现可视化,然后将程序通过以太网传输给机器人控制系统,机器人控制系统作为整个系统的核心部分,接收来自上位机系统的数据与指令,控制机械臂运动,输出机器人的实时状态,特别是机械臂运动的实时速度,同时也向沉积头控制系统发送指令,控制沉积头执行所有的动作;沉积头控制系统接收机器人控制系统的信号和指令,直接输出信号控制沉积头进行相应的动作,沉积头控制系统中分为挤出控制和温度控制两个模块,挤出控制模块通过监测机器人输出的实时速度对
应的电压值,并在满足修正条件时修正速度,依据挤料模型连续计算挤料速度,直接输出与机械臂速度匹配的挤料速度,实现机械臂速度和挤料速度的关联耦合控制,使得机械臂运动和沉积头挤料高度同步,稳定、高精度控制挤料流量。温度控制模块采用闭环控制,温度加热至目标温度并维持,通过热电偶测量温度并反馈至控制系统,散热风扇在加热启动时开,当喷头温度降低到室温时关。
[0055]
图6是按照本发明的优选实施例所构建的控制系统的控制逻辑流程图,如图6所示,上位机运行程序,指令与数据通过以太网发送至机器人控制系统,机器人控制系统收到数据后,同时将指令和数据分别发送给机械臂和沉积头控制系统,机械臂按照路径数据执行运动,同时向外反馈运动的实时速度;沉积头控制系统根据接收的指令和监控的机械臂速度,并在满足修正条件时根据修正模型修正速度,匹配计算挤料速度,使得挤料速度与机械臂运动速度保持同步。在成形过程中传输数据时,反复循环上述过程,实现实时的速度同步,解决同步精确挤料难题,极大地提高机器人与挤料的同步性、稳定性和控制的灵活性,精准控制挤料量,进而提高熔融沉积成形的精度和质量。
[0056]
所述的三个控制系统通过以太网交换机连接,所有控制系统一体化、协同化控制,保证所有系统和模块协同配合,按照成形工艺过程的逻辑和顺序稳定运行。
[0057]
按照本技术的另一方面,提供了一种实时同步沉积的工业机器人熔融沉积制造系统的应用,包括如下步骤:
[0058]
s1:采用所述上位机控制系统2生成待制造零件的三维模型,并规划成形路径和生成工序。
[0059]
在上位机系统中,建立打印零件三维模型,对模型进行离散处理,规划成形路径,生成工艺程序,通过gui在显示屏上可视化工艺控制窗口,在所有系统准备就绪后将数据与指令通过以太网络在线传输给工业机器人控制系统;
[0060]
s2:所述工业机器人控制系统4接收所述成形路径和工序,并对应触发所述沉积头控制系统5进行预热,待所述沉积头控制系统5预热完成即向所述工业机器人控制系统4发送执行信号,以使所述机械臂1-1开始作动,逐层沉积,直至生成零件。
[0061]
工业机器人控制系统接受来自上位机系统的数据与指令,将沉积头控制部分的指令通过i/o通信接口分发给沉积头控制系统,机械臂运动控制指令代码发送至机械臂,机械臂定位至原点准备就绪,等待开始运动的执行信号;
[0062]
沉积头接收机器人发送的指令,沉积头开始加热,温度测量开始,散热风扇开,检测温度达到设置的目标温度时,向机器人控制系统发送“可执行运动”信号,工业机器人控制系统接收信号后,立即执行路径运动,按照传输的路径数据进行运动,开始成形打印;
[0063]
机械臂按照路径运动时,模拟量输出模块将机械臂速度范围线形映射为连续变化的电压值,沉积头控制系统监测获取机器人速度对应的电压值,据挤料模型计算目前机械臂速度对应的挤料速度,同步输出匹配的挤料量,成形过程中保持实时检测和连续计算挤料速度,保持高同步性、高稳定性和高精度的挤料流量。
[0064]
保持成形过程中的同步控制,重复每层的打印,稳定逐层沉积熔融材料,直至零件原型完成成形。完成打印后,机械臂停止,随即挤料停止,加热关闭,散热风扇散热至室温后关闭,程序执行完毕,关闭通信。
[0065]
本领域的技术人员容易理解,以上所述仅为本发明的较佳实施例而已,并不用以
限制本发明,凡在本发明的精神和原则之内所作的任何修改、等同替换和改进等,均应包含在本发明的保护范围之内。