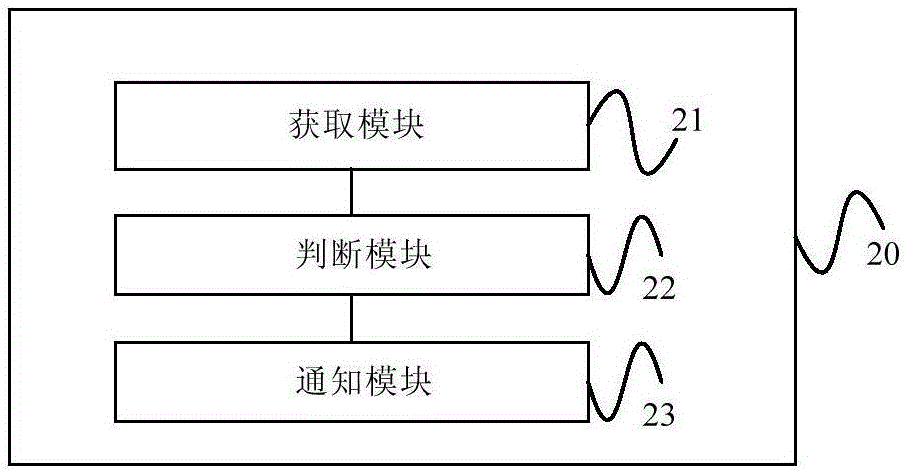
本发明实施例涉及半导体生产制造领域,尤其涉及一种半导体工艺流程控制方法及装置。
背景技术:
:半导体工艺流程涉及生产制造过程、数据采集分析过程和质量管理过程,在生产制造过程中工艺人员在生产制造执行系统里设置工艺标准,并按照该工艺标准生产制造半导体;半导体生产制造结束后,测试人员从所有的半导体中抽取样本,对样本进行数据采集检测,并依据检测标准判断样本是否合格达标,其中,检测标准由机台模组按机台标准设置在数据采集分析系统中;另外,品质管控人员按公司的质量标准在质量管理系统中设置质量管理标准,并判断生产制造的半导体是否符合公司的质量管理标准。在实际生产制造过程中,由于工艺标准、检测标准和质量管理标准分别由不同的人员制定,因此,三者可能会不相同,一旦出现三者不等情况,则半导体的生产制造过程将停止不前,甚至严重影响半导体的生产制造进度。技术实现要素:本发明实施例提供一种半导体工艺流程控制方法及装置,完善工艺设计,以免生产过程中对产品出现误判,而造成过多异常处理。本发明实施例的一个方面是提供一种半导体工艺流程控制方法,包括:获取半导体各个工艺步骤对应的工艺标准、检测标准和质量管理标准;判断所述工艺标准、所述检测标准和所述质量管理标准是否相等;若所述工艺标准、所述检测标准和所述质量管理标准不相等,则通知工艺人员修改所述工艺标准、通知测试人员修改所述检测标准和/或通知品质管控人员修改所述质量管理标准。本发明实施例的另一个方面是提供一种半导体工艺流程控制装置,包括:获取模块,用于获取半导体各个工艺步骤对应的工艺标准、检测标准和质量管理标准;判断模块,用于判断所述工艺标准、所述检测标准和所述质量管理标准是否相等;通知模块,用于若所述工艺标准、所述检测标准和所述质量管理标准不相等,则通知工艺人员修改所述工艺标准、通知测试人员修改所述检测标准和/或通知品质管控人员修改所述质量管理标准。本发明实施例提供的半导体工艺流程控制方法及装置,通过计算机获取半导体各个工艺步骤对应的工艺标准、检测标准和质量管理标准,并判断工艺标准、检测标准和质量管理标准是否相等,当工艺标准、检测标准和质量管理标准不等时,通知工艺人员修改工艺标准、通知测试人员修改检测标准和/或通知品质管控人员修改质量管理标准,完善工艺设计,以免生产过程中对产品出现误判,而造成过多异常处理。附图说明图1为本发明实施例提供的半导体工艺流程控制方法流程图;图2为本发明实施例提供的半导体工艺流程控制装置的结构图;图3为本发明另一实施例提供的半导体工艺流程控制装置的结构图。具体实施方式图1为本发明实施例提供的半导体工艺流程控制方法流程图。本发明实施例针对半导体工艺流程中工艺标准、检测标准和质量管理标准分别由不同的人员制定,因此,三者可能会不相同,一旦出现三者不等情况,则会对产品品质进行误判,这样势必造成错误的或者过多的异常处理(如:不该HOLD的产品被暂停生产、非达标的产品反而被放到下一工序),为了解决此问题本发明实施例提供了半导体工艺流程控制方法,该方法的执行主体具体为计算机,该方法的具体步骤如下:步骤S101、获取半导体各个工艺步骤对应的工艺标准、检测标准和质量管理标准;在本发明实施例中,半导体各个工艺步骤分别对应工艺标准、检测标准 和质量管理标准,工艺标准由工艺人员在生产制造执行系统中设置,检测标准由机台模组按机台标准设置在数据采集分析系统中,质量管理标准由品质管控人员按公司的质量标准在质量管理系统中设置。计算机具体从生产制造执行系统中获取工艺标准,从数据采集分析系统中获取检测标准,从质量管理系统中获取质量管理标准。步骤S102、判断所述工艺标准、所述检测标准和所述质量管理标准是否相等;计算机判断获取到的所述工艺标准、所述检测标准和所述质量管理标准是否相等。步骤S103、若所述工艺标准、所述检测标准和所述质量管理标准不相等,则通知工艺人员修改所述工艺标准、通知测试人员修改所述检测标准和/或通知品质管控人员修改所述质量管理标准。若计算机判断出所述工艺标准、所述检测标准和所述质量管理标准不相等,则通知工艺人员修改所述工艺标准、通知测试人员修改所述检测标准和/或通知品质管控人员修改所述质量管理标准,具体地,若所述工艺标准和所述检测标准相等,而与所述质量管理标准不相等,则通知品质管控人员修改所述质量管理标准;若所述工艺标准、所述检测标准和所述质量管理标准互不相等,则分别通知工艺人员修改所述工艺标准、通知测试人员修改所述检测标准和通知品质管控人员修改所述质量管理标准,同时阻止该工艺设计的后续进程,以免生产过程中对产品出现误判,而造成过多异常处理,直到所述工艺标准、所述检测标准和所述质量管理标准一致时再继续该工艺设计的后续进程,保证生产过程中产品的正常制造。本发明实施例通过计算机获取半导体各个工艺步骤对应的工艺标准、检测标准和质量管理标准,并判断工艺标准、检测标准和质量管理标准是否相等,当工艺标准、检测标准和质量管理标准不等时,通知工艺人员修改工艺标准、通知测试人员修改检测标准和/或通知品质管控人员修改质量管理标准,完善工艺设计,以免生产过程中对产品出现误判,而造成过多异常处理。在上述实施例的基础上,所述获取半导体各个工艺步骤对应的工艺标准、检测标准和质量管理标准之后,还包括:依据所述工艺标准计算所述工艺标准的上限值和下限值;依据所述检测标准计算所述检测标准的上限值和下限值;依据所述质量管理标准计算所述质量管理标准的上限值和下限值。在本发明实施例中,工艺标准、检测标准和质量管理标准分别对应一个数值范围,例如,半导体厚度的工艺标准为0.72±0.06μm,则半导体厚度的工艺标准的上限值为0.78μm,半导体厚度的工艺标准的下限值为0.66μm。同理,检测标准和质量管理标准分别对应一个数值范围,工艺标准、检测标准和质量管理标准可能相同,也可能不同。所述判断所述工艺标准、所述检测标准和所述质量管理标准是否相等,包括:判断所述工艺标准的上限值、所述检测标准的上限值和所述质量管理标准的上限值是否相等,以及判断所述工艺标准的下限值、所述检测标准的下限值和所述质量管理标准的下限值是否相等。例如,半导体厚度的工艺标准为0.72±0.06μm,则半导体厚度的工艺标准的上限值为0.78μm,半导体厚度的工艺标准的下限值为0.66μm;半导体厚度的检测标准为0.71±0.06μm,则半导体厚度的检测标准的上限值为0.77μm,半导体厚度的检测标准的下限值为0.65μm;半导体厚度的质量管理标准为0.70±0.06μm,则半导体厚度的质量管理标准的上限值为0.76μm,半导体厚度的质量管理标准的下限值为0.64μm,则计算机判断获知所述工艺标准的上限值、所述检测标准的上限值和所述质量管理标准的上限值不相等,且所述工艺标准的下限值、所述检测标准的下限值和所述质量管理标准的下限值不相等。所述判断所述工艺标准、所述检测标准和所述质量管理标准是否相等之后,还包括:生成半导体工艺流程控制表,所述半导体工艺流程控制表包括所述工艺标准、所述检测标准和所述质量管理标准,以及所述工艺标准、所述检测标准和所述质量管理标准的比较结果。计算机判断所述工艺标准、所述检测标准和所述质量管理标准是否相等之后,生成半导体工艺流程控制表,所述半导体工艺流程控制表包括所述工艺标准、所述检测标准和所述质量管理标准,以及所述工艺标准、所述检测标准和所述质量管理标准的比较结果,该半导体工艺流程控制表的结构如下表1所示:表1工艺标准检测标准质量管理标准比较结果0.72±0.06μm0.71±0.06μm0.70±0.06μm不同所述若所述工艺标准、所述检测标准和所述质量管理标准不相等,则通知工艺人员修改所述工艺标准、通知测试人员修改所述检测标准和/或通知品质管控人员修改所述质量管理标准,包括:若所述工艺标准、所述检测标准和所述质量管理标准不相等,则生成告警信息,并依据所述告警信息通知工艺人员修改所述工艺标准、通知测试人员修改所述检测标准和/或通知品质管控人员修改所述质量管理标准。若所述工艺标准、所述检测标准和所述质量管理标准不相等,则生成告警信息,告警信息具体指示所述工艺标准、所述检测标准和所述质量管理标准中哪两个标准不相同,或三者均不相同,依据上述表1该告警信息提示三者均不相同,则通知工艺人员修改所述工艺标准、通知测试人员修改所述检测标准和通知品质管控人员修改所述质量管理标准;若所述工艺标准和所述检测标准相等,而与所述质量管理标准不相等,则通知品质管控人员修改所述质量管理标准;若所述工艺标准和所述质量管理标准相等,而与所述检测标准不相等,则通知测试人员修改所述检测标准;若所述检测标准和所述质量管理标准相等,而与所述工艺标准不相等,则通知工艺人员修改所述工艺标准,具体通知方法为向相应人员的计算机或终端发送通知信息,告知相应人员修改相依的标准参数。本发明实施例通过计算机获取半导体各个工艺步骤对应的工艺标准、检测标准和质量管理标准,并判断工艺标准、检测标准和质量管理标准是否相等,当工艺标准、检测标准和质量管理标准不等时,通知工艺人员修改工艺标准、通知测试人员修改检测标准和/或通知品质管控人员修改质量管理标准,完善工艺设计,以免生产过程中对产品出现误判,而造成过多异常处理。图2为本发明实施例提供的半导体工艺流程控制装置的结构图。本发明实施例提供的半导体工艺流程控制装置可以执行半导体工艺流程控制方法实施例提供的处理流程,如图2所示,半导体工艺流程控制装置20包括获取模块21用于获取半导体各个工艺步骤对应的工艺标准、检测标准和质量管理标准;判断模块22用于判断所述工艺标准、所述检测标准和所述质量管理标准是否相等;通知模块23用于若所述工艺标准、所述检测标准和所述质量管理 标准不相等,则通知工艺人员修改所述工艺标准、通知测试人员修改所述检测标准和/或通知品质管控人员修改所述质量管理标准。本发明实施例通过计算机获取半导体各个工艺步骤对应的工艺标准、检测标准和质量管理标准,并判断工艺标准、检测标准和质量管理标准是否相等,当工艺标准、检测标准和质量管理标准不等时,通知工艺人员修改工艺标准、通知测试人员修改检测标准和/或通知品质管控人员修改质量管理标准,完善工艺设计,以免生产过程中对产品出现误判,而造成过多异常处理。图3为本发明另一实施例提供的半导体工艺流程控制装置的结构图。在上述实施例的基础上,获取模块21具体用于依据所述工艺标准计算所述工艺标准的上限值和下限值;依据所述检测标准计算所述检测标准的上限值和下限值;依据所述质量管理标准计算所述质量管理标准的上限值和下限值。判断模块22具体用于判断所述工艺标准的上限值、所述检测标准的上限值和所述质量管理标准的上限值是否相等,以及判断所述工艺标准的下限值、所述检测标准的下限值和所述质量管理标准的下限值是否相等。半导体工艺流程控制装置20还包括半导体工艺流程控制表生成模块24,用于生成半导体工艺流程控制表,所述半导体工艺流程控制表包括所述工艺标准、所述检测标准和所述质量管理标准,以及所述工艺标准、所述检测标准和所述质量管理标准的比较结果。通知模块23具体用于若所述工艺标准、所述检测标准和所述质量管理标准不相等,则生成告警信息,并依据所述告警信息通知工艺人员修改所述工艺标准、通知测试人员修改所述检测标准和/或通知品质管控人员修改所述质量管理标准。本发明实施例提供的发送设备可以具体用于执行上述图1所提供的方法实施例,具体功能此处不再赘述。本发明实施例通过计算机获取半导体各个工艺步骤对应的工艺标准、检测标准和质量管理标准,并判断工艺标准、检测标准和质量管理标准是否相等,当工艺标准、检测标准和质量管理标准不等时,通知工艺人员修改工艺标准、通知测试人员修改检测标准和/或通知品质管控人员修改质量管理标准,完善工艺设计,以免生产过程中对产品出现误判,而造成过多异常处理。综上所述,本发明实施例通过计算机获取半导体各个工艺步骤对应的工 艺标准、检测标准和质量管理标准,并判断工艺标准、检测标准和质量管理标准是否相等,当工艺标准、检测标准和质量管理标准不等时,通知工艺人员修改工艺标准、通知测试人员修改检测标准和/或通知品质管控人员修改质量管理标准,完善工艺设计,以免生产过程中对产品出现误判,而造成过多异常处理。在本发明所提供的几个实施例中,应该理解到,所揭露的装置和方法,可以通过其它的方式实现。例如,以上所描述的装置实施例仅仅是示意性的,例如,所述单元的划分,仅仅为一种逻辑功能划分,实际实现时可以有另外的划分方式,例如多个单元或组件可以结合或者可以集成到另一个系统,或一些特征可以忽略,或不执行。另一点,所显示或讨论的相互之间的耦合或直接耦合或通信连接可以是通过一些接口,装置或单元的间接耦合或通信连接,可以是电性,机械或其它的形式。所述作为分离部件说明的单元可以是或者也可以不是物理上分开的,作为单元显示的部件可以是或者也可以不是物理单元,即可以位于一个地方,或者也可以分布到多个网络单元上。可以根据实际的需要选择其中的部分或者全部单元来实现本实施例方案的目的。另外,在本发明各个实施例中的各功能单元可以集成在一个处理单元中,也可以是各个单元单独物理存在,也可以两个或两个以上单元集成在一个单元中。上述集成的单元既可以采用硬件的形式实现,也可以采用硬件加软件功能单元的形式实现。上述以软件功能单元的形式实现的集成的单元,可以存储在一个计算机可读取存储介质中。上述软件功能单元存储在一个存储介质中,包括若干指令用以使得一台计算机设备(可以是个人计算机,服务器,或者网络设备等)或处理器(processor)执行本发明各个实施例所述方法的部分步骤。而前述的存储介质包括:U盘、移动硬盘、只读存储器(Read-OnlyMemory,ROM)、随机存取存储器(RandomAccessMemory,RAM)、磁碟或者光盘等各种可以存储程序代码的介质。本领域技术人员可以清楚地了解到,为描述的方便和简洁,仅以上述各功能模块的划分进行举例说明,实际应用中,可以根据需要而将上述功能分配由不同的功能模块完成,即将装置的内部结构划分成不同的功能模块,以 完成以上描述的全部或者部分功能。上述描述的装置的具体工作过程,可以参考前述方法实施例中的对应过程,在此不再赘述。最后应说明的是:以上各实施例仅用以说明本发明的技术方案,而非对其限制;尽管参照前述各实施例对本发明进行了详细的说明,本领域的普通技术人员应当理解:其依然可以对前述各实施例所记载的技术方案进行修改,或者对其中部分或者全部技术特征进行等同替换;而这些修改或者替换,并不使相应技术方案的本质脱离本发明各实施例技术方案的范围。当前第1页1 2 3