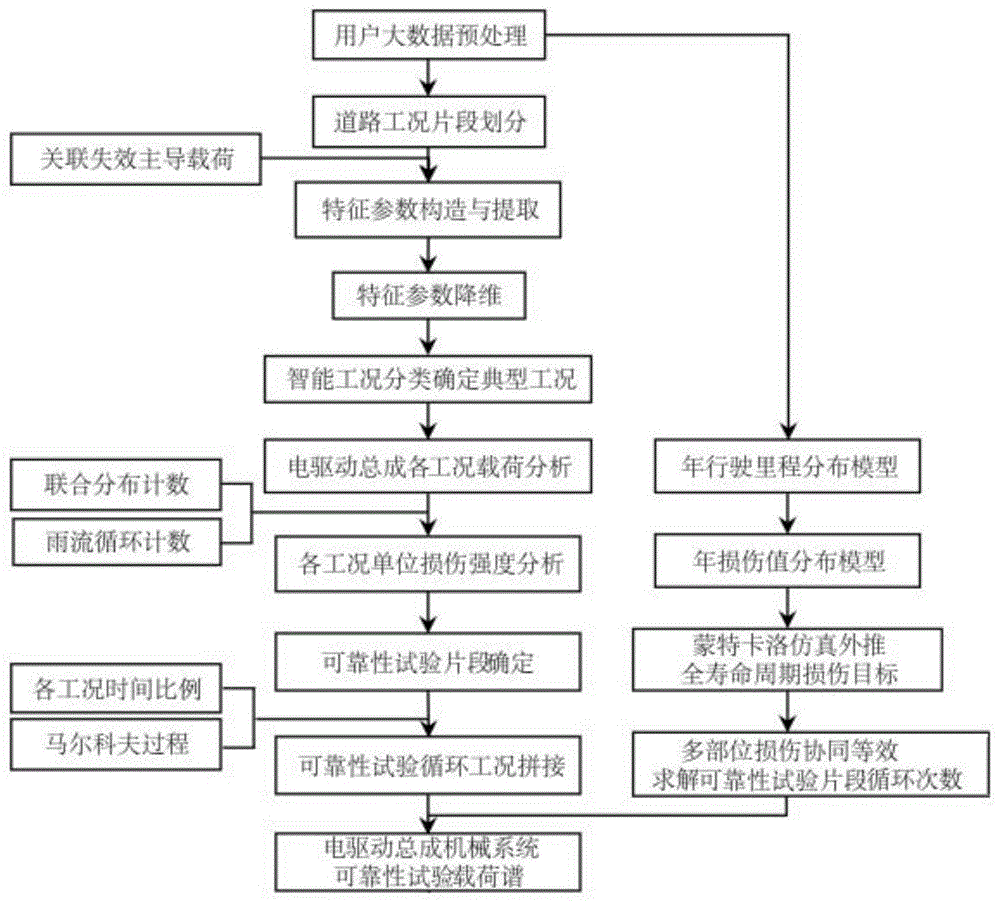
本发明属于电动汽车的可靠性分析
技术领域:
,具体涉及一种电驱动总成机械系统可靠性试验载荷谱的编制方法。
背景技术:
:电驱动总成作为汽车电动化的核心部件,是纯电动、氢燃料电池等多种新能源汽车的唯一动力系统,为车辆前进提供动力并回收部分制动能量。相对传统汽车,电动汽车动力性大幅提升,其转速与扭矩等载荷强度的增加相应加剧了电驱动总成失效的风险。在汽车开发体系中,零件/总成/整车等多层级的可靠性试验是验证并确保产品可靠性与耐久性的主要方式。目前面向传统内燃机车辆的可靠性试验规范难以有效覆盖电驱动总成机械系统实际服役载荷强度。因此,构建反映用户真实使用条件的电驱动总成机械系统可靠性试验载荷谱,能有效验证电驱动总成可靠性水平并支持其高质量开发。技术实现要素:本发明是为了解决上述问题而进行的,目的在于提供一种电驱动总成机械系统可靠性试验载荷谱的编制方法。本发明提供了一种电驱动总成机械系统可靠性试验载荷谱的编制方法,具有这样的特征,包括以下步骤:步骤1,基于实际用户道路采集得到用户载荷数据,对用户载荷数据进行预处理并划分道路工况片段为运行段与怠速段;步骤2,关联电驱动总成机械系统失效主导载荷构造运行段的多维度特征参数,对多维度特征参数降维后采用机器学习算法确定出五种典型工况;步骤3,对电驱动总成机械系统的主导载荷进行多维度特征分析,并基于损伤强度分布的连续性及拐点特征选取各个典型工况的最优代表片段作为可靠性试验片段;步骤4,通过用户载荷数据拟合用户年行驶里程分布模型,基于年行驶里程等效各零部件年损伤分布模型,采用蒙特卡洛仿真外推出全寿命周期下各零部件的损伤目标;步骤5,根据全寿命周期下各零部件的损伤目标以及五种可靠性试验片段下对各零部件造成的损伤,利用多目标优化方法计算出涵盖多损伤目标下各个可靠性试验片段的循环次数;步骤6,基于马尔科夫过程下的状态转移概率,采用伪随机数的方法确定用户运行条件下各个可靠性试验片段的拼接顺序,并拼接得到可靠性试验循环工况;步骤7,由可靠性试验片段的的循环次数和可靠性试验循环工况编制得到可靠性试验载荷谱。在本发明提供的电驱动总成机械系统可靠性试验载荷谱的编制方法中,还可以具有这样的特征:其中,步骤1中,用户载荷数据涵盖大量不同地域、车型的电动汽车行驶数据,对用户载荷数据进行预处理为剔除异常或无效载荷数据后生成新的载荷历程,运行段为汽车车速从零开始到下一个速度为零的片段,怠速段为车辆启动到车速为零的片段。在本发明提供的电驱动总成机械系统可靠性试验载荷谱的编制方法中,还可以具有这样的特征:其中,步骤2中确定五种典型工况时,包括以下子步骤:步骤2-1,以原始扭矩、转速、电流、电压作为基础数据,以每个运行段的速度、加速度、扭矩、扭矩波动、电流、电压、功率、损伤及时间里程作为特征构造多维度特征参数;步骤2-2,采用主成分分析法对多维度特征参数进行降维,提取主成分特征得到主成分得分矩阵;步骤2-3,采用k-means法对用户运行工况进行识别分类,以主成分得分矩阵为基础数据,以多维空间点与点之间的欧式距离作为分类依据,通过ch指标确定聚类数目,将运行段分为五种典型工况,分别为工况一、工况二、工况三、工况四以及工况五。在本发明提供的电驱动总成机械系统可靠性试验载荷谱的编制方法中,还可以具有这样的特征:其中,步骤2-2中,若多维度特征参数降维后为n维,则对多维度特征参数进行线性变换生成的主成分为yn,将90%累计贡献率作为阈值提取主成分特征,主成分特征包含电驱动总成机械系统失效主导载荷的特征信息量,该特征信息量包括扭矩、转速、电流、电压以及功率,步骤2-3中,任意两个n维向量x1=(x11,x12,…,x1n)和x1=(x11,x12,…,x1n)之间的欧式距离为d12,计算公式如下:ch指标的计算公式如下:公式(2)中,p为总聚类个数,k为当前的类,tr(b)为类间离差矩阵的迹,tr(w)为类内离差矩阵的迹,工况一为中高速加减速,对应大扭矩、中高转速低频波动工况,工况二为短时中低速加减速,对应大扭矩、中转速高频波动工况,工况三为长时间中速加减速工况,对应中扭矩、中转速低频波动工况,工况四为高速加减速,中扭矩、高转速低频波动运行工况,工况五为低速加减速,对应中小扭矩、低转速中低频波动工况。在本发明提供的电驱动总成机械系统可靠性试验载荷谱的编制方法中,还可以具有这样的特征:其中,步骤3中可靠性试验片段的选取还包括以下子步骤:步骤3-1,对于电驱动总成机械系统中受扭矩作用的零部件,通过雨流循环计数对每个运行段的扭矩时间历程提取载荷循环,对于电驱动总成机械系统中损伤由转速和扭矩联合循环载荷引起的齿轮系零件,通过对每个运行段的转速与扭矩时间历程进行联合分布计数,对于电驱动总成机械系统中的控制器和功率器件,对电流、电压及对应时间进行联合分布计数,并构造功率参数进行循环计数;步骤3-2,采用miner线性累积损伤准则得出每一个运行段对轴系零件和齿轮系零件的损伤,基于arrhenius模型计算电子元器件的高温老化损伤,基于广义eying模型计算电-热耦合损伤,基于coffin-manson计算力-热耦合下的损伤,基于rhee模型计算力-速耦合损伤,得到电驱动总成机械系统的电机、控制器以及减/变速器的主要部件损伤di,得到各典型工况下各零部件单位损伤强度累积分布;步骤3-3,综合各典型工况下各零部件单位损伤强度累积分布,以分布曲线拐点为准则选取各典型工况的最优代表片段。在本发明提供的电驱动总成机械系统可靠性试验载荷谱的编制方法中,还可以具有这样的特征:其中,步骤3-2中,针对miner线性累积损伤准则得出运行段对轴系零件和齿轮系零件造成的损伤,对于受扭矩作用的零部件,通过雨流循环计数得出第i级扭矩幅值sr,i下对应的频次nr,i,通过载荷寿命曲线得出第i级扭矩幅值下的疲劳寿命nf,i,第i级扭矩幅值下对应的损伤di=nr,i/nf,i,则每个运行段载荷历程经雨流循环计数后对受扭矩作用的零部件造成的总损伤di1=∑di,针对受到转速与扭矩联合作用的齿轮系零件,采用联合分布计数计算出第i级扭矩载荷下旋转圈数ri,除以第i级载荷下的疲劳寿命ni得出第i级扭矩载荷下对应的损伤,基于arrhenius模型计算电子元器件的高温老化损伤,通过arrhenius模型,将温度作为加速应力,得到加速寿命模型如下:l=a·e-e/kt(3)公式(3)中,l是寿命特征,a为常数、频数因子,e为激活能,与材料有关,单位为ev,k为波尔兹曼常数,t为温度应力,单位为开尔文,基于广义eying模型计算电-热耦合损伤,得到寿命预测模型如下:公式(4)中,tl为零件寿命,e为激活能,t为温度应力,si为除温度外的应力,如电流、电压,k为波尔兹曼常数,a、b、c、α为常数,基于coffin-manson计算力-热耦合下的损伤,采用coffin-manson模型分析温度循环与零件寿命之间的关系来涵盖电驱动总成机械系统热应力疲劳引起的零件材料失效,得到模型如下:nf=af-αδt-βg(tmax)(5)公式(5)中,nf为零件寿命,g(tmax)为最高温度应力的阿伦尼斯激活能,δt为最高温度与最低温度之间的温差,单位为开尔文,f为循环频率,单位为赫兹,a、α、β为常数,基于rhee模型计算力-速耦合损伤,采用rhee公式构建损伤模型如下:δw=kfavbtc(6)公式(6)中,δw为磨损重量损失,f为接触载荷,v为运行速度,t为时间,a、b、c为常数,单位损伤强度为运行段在单位里程下的损伤强度,通过第i个运行段的损伤除以第i个运行段的行驶里程得到。在本发明提供的电驱动总成机械系统可靠性试验载荷谱的编制方法中,还可以具有这样的特征:其中,步骤5中,对于电驱动总成机械系统中n个零部件,将筛选出的五种可靠性试验片段对第n个零部件造成的损伤分别为dn1,dn2,…,dn5,第n个零部件全寿命周期下的损伤目标为dn_t,采用多目标优化算法计算出涵盖多损伤目标下各个可靠性试验片段的循环次数,计算公式如下:公式(7)中,dn1,dn2,…,dn5为五种可靠性试验片段分别对第n个零部件造成的损伤,x1,x2,…,x5为五种可靠性试验片段的循环次数,d1_t,d2_t,…,dn_t为各零部件全寿命周期下的总损伤目标。在本发明提供的电驱动总成机械系统可靠性试验载荷谱的编制方法中,还可以具有这样的特征:其中,步骤6中,基于马尔科夫链过程,将五种典型工况作为马尔科夫过程的五个状态空间,从实际用户划分的道路工况片段的先后顺序出发,根据每个片段所属的典型工况构建马尔科夫链模型,在马尔科夫过程中,从状态r到状态s的转移概率为prs:式(8)中,nrs为当前时刻状态r转移到下一个时刻状态s的次数,r=1,2,…,5;s=1,2,…,5,根据对用户每次出行的第一个运行段进行统计,随机选取工况概率较高的可靠性试验片段作为初始片段,之后基于状态转移概率分布,利用马尔科夫链蒙特卡洛法产生伪随机数p,假设当前状态为r,若随机数p满足:则判断下一个状态为k,从第k个状态工况中选取可靠性试验片段进行拼接,之后将k值赋给r重复上述步骤,完成可靠性试验片段的拼接,各个可靠性试验片段的总时间满足实际用户下各典型工况时间比例,同时对怠速段的怠速时间进行拟合分布,选取50百分位下的怠速时长作为可靠性试验片段前后的一段怠速时长并进行拼接,得到可靠性试验循环工况。在本发明提供的电驱动总成机械系统可靠性试验载荷谱的编制方法中,还可以具有这样的特征:其中,电驱动总成机械系统可靠性试验载荷谱中具有包括速度时间历程、扭矩时间历程的可靠性试验循环工况以及针对电驱动总成机械系统各零部件损伤的可靠性试验片段的的循环次数。发明的作用与效果根据本发明所涉及的一种电驱动总成机械系统可靠性试验载荷谱的编制方法,基于实际用户道路采集得到用户载荷数据,通过电驱动总成失效主导载荷来构造多维度特征参数,采用机器学习方法完成工况分类确定电驱动总成的五种典型工况,以疲劳损伤理论确定各典型工况下损伤与分布特性,并基于损伤分布连续性选取可靠性试验片段,采用蒙特卡洛仿真确定全寿命周期下各零部件的损伤目标,基于各零部件损伤协同等效确定可靠性试验片段的循环次数,并基于马尔科夫过程下的状态转移概率对各典型工况的可靠性试验片段拼接,最终得到电驱动总成机械系统可靠性试验载荷谱,因此载荷谱完全源于用户行驶工况,通过智能分类后得到五种典型工况,且通过选取各典型工况下损伤强度较高的片段作为可靠性试验片段来进行载荷谱编制,能够加速试验过程、缩短试验时间,为电驱动总成乃至电动汽车的高质量开发提供支持。附图说明图1是本发明的实施例中一种电驱动总成机械系统可靠性试验载荷谱的编制方法的流程示意图;图2是本发明的实施例中的部分用户载荷数据图;图3是本发明的实施例中的用户道路工况片段类型示意图;图4是本发明的实施例中的各主成分特征值与贡献率结果图;图5是本发明的实施例中的聚类效果评价ch指标计算结果图;图6是本发明的实施例中的聚类结果点云图;图7是本发明的实施例中的工况一的典型片段特征图;图8是本发明的实施例中的工况二的典型片段特征图;图9是本发明的实施例中的工况三的典型片段特征图;图10是本发明的实施例中的工况四的典型片段特征图;图11是本发明的实施例中的工况五的典型片段特征图;图12是本发明的实施例中的工况一载荷雨流与联合分布计数图;图13是本发明的实施例中的工况二载荷雨流与联合分布计数图;图14是本发明的实施例中的工况三载荷雨流与联合分布计数图;图15是本发明的实施例中的工况四载荷雨流与联合分布计数图;图16是本发明的实施例中的工况五载荷雨流与联合分布计数图;图17是本发明的实施例中的工况一轴系损伤强度累积概率分布图;图18是本发明的实施例中的工况一齿轮系损伤强度累积概率分布图;图19是本发明的实施例中的年行驶里程的累积概率分布图;图20是本发明的实施例中的轴系年损伤值的累积概率分布图;图21是本发明的实施例中的齿轮系年损伤值的累积概率分布图;图22是本发明的实施例中的各典型工况总时间比例图;图23是本发明的实施例中的怠速时间累积概率分布图;图24是本发明的实施例中的可靠性试验循环工况的示意图。具体实施方式为了使本发明实现的技术手段与功效易于明白了解,以下结合实施例及附图对本发明作具体阐述。图1是本发明的实施例中一种电驱动总成机械系统可靠性试验载荷谱的编制方法的流程示意图。如图1所示,本实施例提供了一种电驱动总成机械系统可靠性试验载荷谱的编制方法,包括以下步骤:步骤1,基于实际用户道路采集得到用户载荷数据,对用户载荷数据进行预处理并划分道路工况片段为运行段与怠速段。步骤1中,用户载荷数据涵盖大量不同地域、车型的电动汽车行驶数据,针对在数据采集过程中由于gps信号不良、长时间怠速及剧烈加减速导致的异常数据,对用户载荷数据进行预处理为剔除异常或无效载荷数据后生成新的载荷历程。本实施例中,用户载荷数据包含国内华中、华北、华东、西北四个地区共300个用户1年的运行数据,部分用户载荷数据如图2所示。汽车行驶过程包含四种运行状态,在划分片段之前先对运行状态定义划分依据,如表1所示。表1运行状态划分依据运行状态速度加速度加速>5km/h>0.15m/s2减速>5km/h<-0.15m/s2匀速>5km/h≥-0.15m/s2&≤0.15m/s2怠速≤5km/h≥-0.15m/s2&≤0.15m/s2图3是本发明的实施例中的用户道路工况片段类型示意图。如图3所示,道路工况片段划分为运行段与怠速段,定义运行段为汽车车速从零开始到下一个速度为零为止,怠速段视为车辆启动,车速近似为零,本实施例中,基于编程对用户数据自动划分出m个运行段与q个怠速段。步骤2,关联电驱动总成机械系统失效主导载荷构造运行段的多维度特征参数,对多维度特征参数降维后采用机器学习算法确定出五种典型工况。步骤2中确定五种典型工况时,包括以下子步骤:步骤2-1,以原始扭矩、转速、电流、电压作为基础数据,以每个运行段的速度、加速度、扭矩、扭矩波动、电流、电压、功率、损伤及时间里程作为特征构造多维度特征参数。本实施例中,基于速度、加速度、扭矩、时间等统计量构造出18个表征运行工况的多维度特征参数,多维度特征参数如表2所示,并对m个运行段计算出18个参数的特征参数矩阵tm×18。表2工况特征参数序号特征参数特征参数意义1vmax/(km/h)最大速度2vm/(km/h)平均速度3vsd/(km/h)速度标准差4amax/(m/s2)最大加速度5amin/(m/s2)最小减速度6asd/(m/s2)加速度标准差7aamean/(m/s2)加速段平均加速度8admean/(m/s2)减速段平均减速度9trq_sd/(n.m)扭矩标准差10trq_pmean/(n.m)平均正扭矩11trq_nmean/(n.m)平均负扭矩12trq_range_max扭矩增加时最大波动量13trq_range_min扭矩减小时最大波动量14trq_range_sd扭矩波动标准差15pta/(%)加速时间比例16ptd/(%)减速时间比例17tz/(s)总时间18s/(km)行驶里程步骤2-2,采用主成分分析法对多维度特征参数进行降维,提取主成分特征得到主成分得分矩阵。步骤2-2中,若多维度特征参数降维后为n维,则对多维度特征参数进行线性变换生成的主成分为yn,将90%累计贡献率作为阈值提取主成分特征,主成分特征包含电驱动总成机械系统失效主导载荷的特征信息量,该特征信息量包括扭矩、转速、电流、电压以及功率。本实施例中,累计贡献率可根据实际情况选择,如85%、90%等。图4是本发明的实施例中的各主成分特征值与贡献率结果图。如图4所示,图中横坐标为18个主成分,左边纵坐标为每个主成分对应的特征值及贡献率,右边纵坐标代表主成分累积贡献率,按照累积贡献率大于90%的原则提取出前五个主成分特征m1,m2,…,m5。本实施例中,对多维度特征参数进行降维还可以采用线性判别分析、局部线性嵌入法等方法。步骤2-3,采用k-means法对用户运行工况进行识别分类,以主成分得分矩阵为基础数据,以多维空间点与点之间的欧式距离作为分类依据,通过ch指标确定聚类数目,将运行段分为五种典型工况,分别为工况一、工况二、工况三、工况四以及工况五。步骤2-3中,任意两个n维向量x1=(x11,x12,…,x1n)和x1=(x11,x12,…,x1n)之间的欧式距离为d12,计算公式如下:ch指标主要从簇间距离与簇内距离的比值来衡量聚类的有效性,ch指标的计算公式如下:公式(2)中,p为总聚类个数,k为当前的类,tr(b)为类间离差矩阵的迹,tr(w)为类内离差矩阵的迹。图5是本发明的实施例中的聚类效果评价ch指标计算结果图。如图5所示,图中横坐标为聚类数目,纵坐标为聚类数目对应的ch值,当聚类数目为5时ch值最大。图6是本发明的实施例中的聚类结果点云图。如图6所示,取主成分得分矩阵前三列分别作为聚类点云图的三个轴的坐标进行绘制。图7是本发明的实施例中的工况一的典型片段特征图,图8是本发明的实施例中的工况二的典型片段特征图,图9是本发明的实施例中的工况三的典型片段特征图,图10是本发明的实施例中的工况四的典型片段特征图,图11是本发明的实施例中的工况五的典型片段特征图。如图7-图11所示,图7-图11分别为工况一至工况五,工况一为中高速加减速,对应大扭矩、中高转速低频波动工况;工况二为短时中低速加减速,对应大扭矩、中转速高频波动工况;工况三为长时间中速加减速工况,对应中扭矩、中转速低频波动工况;工况四为高速加减速,中扭矩、高转速低频波动运行工况;工况五为低速加减速,对应中小扭矩、低转速中低频波动工况。本实施例中,对用户运行工况进行识别分类还可以采用k-近邻法、层次聚类法、模糊聚类法、高斯混合聚类法等方法;确定聚类数目还可以使用误差平方和sse、轮廓系数法等。步骤3,对电驱动总成机械系统的主导载荷进行多维度特征分析,并基于损伤强度分布的连续性及拐点特征选取各个典型工况的最优代表片段作为可靠性试验片段。步骤3中可靠性试验片段的选取还包括以下子步骤:步骤3-1,由于电驱动总成机械系统工作在动态交变载荷下,且转速与扭矩非同步变化,因此不同的零部件失效主导载荷需采用不同的计数方式,以进行损伤等效与关联对于电驱动总成机械系统中受扭矩作用的零部件,如轴系零部件、壳体等,通过雨流循环计数对每个运行段的扭矩时间历程提取载荷循环,对于电驱动总成机械系统中损伤由转速和扭矩联合循环载荷引起的齿轮系零件,如轴承、齿轮等,通过对每个运行段的转速与扭矩时间历程进行联合分布计数,对于电驱动总成机械系统中的控制器和功率器件,对电流、电压及对应时间进行联合分布计数,并构造功率参数进行循环计数。步骤3-2,采用miner线性累积损伤准则得出每一个运行段对轴系零件和齿轮系零件的损伤,基于arrhenius模型计算电子元器件的高温老化损伤,基于广义eying模型计算电-热耦合损伤,基于coffin-manson计算力-热耦合下的损伤,基于rhee模型计算力-速耦合损伤,得到电驱动总成机械系统的电机、控制器以及减/变速器的主要部件损伤di,得到各典型工况下各零部件单位损伤强度累积分布。步骤3-2中,针对miner线性累积损伤准则得出运行段对轴系零件和齿轮系零件造成的损伤,对于受扭矩作用的零部件,通过雨流循环计数得出第i级扭矩幅值sr,i下对应的频次nr,i,通过载荷寿命曲线得出第i级扭矩幅值下的疲劳寿命nf,i,第i级扭矩幅值下对应的损伤di=nr,i/nf,i,则每个运行段载荷历程经雨流循环计数后对受扭矩作用的零部件造成的总损伤di1=∑di,针对受到转速与扭矩联合作用的齿轮系零件,采用联合分布计数计算出第i级扭矩载荷下旋转圈数ri,除以第i级载荷下的疲劳寿命ni得出第i级扭矩载荷下对应的损伤,基于arrhenius模型计算电子元器件的高温老化损伤,通过arrhenius模型,将温度作为加速应力,得到加速寿命模型如下:l=a·e-e/kt(3)公式(3)中,l是寿命特征,a为常数、频数因子,e为激活能,与材料有关,单位为ev,k为波尔兹曼常数,t为温度应力,基于广义eying模型计算电-热耦合损伤,得到寿命预测模型如下:公式(4)中,tl为零件寿命,e为激活能,t为温度应力,si为除温度外的应力,k为波尔兹曼常数,a、b、c、α为常数,基于coffin-manson计算力-热耦合下的损伤,采用coffin-manson模型分析温度循环与零件寿命之间的关系来涵盖电驱动总成机械系统热应力疲劳引起的零件材料失效,得到模型如下:nf=af-αδt-βg(tmax)(5)公式(5)中,nf为零件寿命,g(tmax)为最高温度应力的阿伦尼斯激活能,δt为最高温度与最低温度之间的温差,f为循环频率,a、α、β为常数,基于rhee模型计算力-速耦合损伤,采用rhee公式构建损伤模型如下:δw=kfavbtc(6)公式(6)中,δw为磨损重量损失,f为接触载荷,v为运行速度,t为时间,a、b、c为常数,单位损伤强度为运行段在单位里程下的损伤强度,通过第i个运行段的损伤除以第i个运行段的行驶里程得到。图12是本发明的实施例中的工况一载荷雨流与联合分布计数图,图13是本发明的实施例中的工况二载荷雨流与联合分布计数图,图14是本发明的实施例中的工况三载荷雨流与联合分布计数图,图15是本发明的实施例中的工况四载荷雨流与联合分布计数图,图16是本发明的实施例中的工况五载荷雨流与联合分布计数图。如图12-图16所示,图12-图16中,a图均为各工况的载荷雨流循环计数range-mean分布平面图,纵坐标图例代表各级扭矩变程与均值下对应的循环次数,扭矩单位为n·m,b图均为各工况的转速扭矩联合分布计数平面图,纵坐标图例代表各级转速与扭矩下对应的频次,转速单位为r/min,扭矩单位为n·m。步骤3-3,考虑到电驱动总成机械系统不同零部件同步损伤效果,综合各典型工况下各零部件单位损伤强度累积分布,以分布曲线拐点为准则选取各典型工况的最优代表片段,从而保证损伤与用户总体水平接近,同时具有较好的加速系数。本实施例中,以工况一为例,通过载荷雨流循环计数计算载工况一下轴系零部件与齿轮系零部件的单位损伤强度。图17是本发明的实施例中的工况一轴系损伤强度累积概率分布图。如图17所示,横坐标为工况一轴系零部件的单位损伤强度,纵坐标为累积概率/%,服从3参数对数正态分布模型,工况一95百分下的轴系累积损伤强度为0.0966。图18是本发明的实施例中的工况一齿轮系损伤强度累积概率分布图。如图18所示,横坐标为工况一齿轮系单位损伤强度,纵坐标为累积概率/%,服从3参数对数正态分布模型,工况一95百分下的齿轮系累积损伤强度为2.7468。本实施例中,工况一的可靠性试验片段的选取综合轴系零部件与齿轮系零部件的95百分位下的累积损伤强度值进行选取。本实施例中,也可以根据不同用户载荷数据分析各典型工况损伤强度分布,选择其他百分位(如90%、99%)下的单位损伤强度来筛选出各典型工况的备选试验片段。步骤4,通过用户载荷数据拟合用户年行驶里程分布模型,基于年行驶里程等效各零部件年损伤分布模型,采用蒙特卡洛仿真外推出全寿命周期下各零部件的损伤目标。本实施例中,全寿命周期为24万公里或30万公里。图19是本发明的实施例中的年行驶里程的累积概率分布图,图20是本发明的实施例中的轴系年损伤值的累积概率分布图,图21是本发明的实施例中的齿轮系年损伤值的累积概率分布图。如图19-图21所示,图19中基于蒙特卡洛仿真后年行驶里程服从对数正态分布,90百分位下年行驶里程为21928km,图20为轴系零件年损失值的累积概率,图21为的齿轮系零件年损失值的累积概率。步骤5,根据全寿命周期下各零部件的损伤目标以及五种可靠性试验片段下对各零部件造成的损伤,利用多目标优化方法实现多部位损伤协同等效,通过多目标优化方法计算出涵盖多损伤目标下各个可靠性试验片段的循环次数。步骤5中,对于电驱动总成机械系统中n个零部件,将筛选出的五种可靠性试验片段对第n个零部件造成的损伤分别为dn1,dn2,…,dn5,第n个零部件全寿命周期下的损伤目标为dn_t,采用多目标优化算法计算出涵盖多损伤目标下各个可靠性试验片段的循环次数,计算公式如下:公式(7)中,dn1,dn2,…,dn5为五种可靠性试验片段分别对第n个零部件造成的损伤,x1,x2,…,x5为五种可靠性试验片段的循环次数,d1_t,d2_t,…,dn_t为各零部件全寿命周期下的总损伤目标。本实施例中,根据轴系零件和齿轮系零件的综合损伤效果确定出的各个可靠性试验片段为:工况一为1554次、工况二为1791次、工况三为1012次、工况四为2292次、工况五为971次。步骤6,基于马尔科夫过程下的状态转移概率,采用伪随机数的方法确定用户运行条件下各个可靠性试验片段的拼接顺序,并拼接得到可靠性试验循环工况。步骤6中,基于马尔科夫链过程,将五种典型工况作为马尔科夫过程的五个状态空间,从实际用户划分的道路工况片段的先后顺序出发,根据每个片段所属的典型工况构建马尔科夫链模型,在马尔科夫过程中,从状态r到状态s的转移概率为prs:式(8)中,nrs为当前时刻状态r转移到下一个时刻状态s的次数,r=1,2,…,5;s=1,2,…,5,根据对用户每次出行的第一个运行段进行统计,随机选取工况概率较高的可靠性试验片段作为初始片段,之后基于状态转移概率分布,利用马尔科夫链蒙特卡洛法产生伪随机数p,假设当前状态为r,若随机数p满足:则判断下一个状态为k,从第k个状态工况中选取可靠性试验片段进行拼接,之后将k值赋给r重复上述步骤,完成可靠性试验片段的拼接,各个可靠性试验片段的总时间满足实际用户下各典型工况时间比例,此外,由于怠速状态下仅存在少量待机电流、电压引起控制器与执行器的老化,在电驱动总成全寿命周期中损伤贡献量很小,为缩短总体试验时间在可靠性试验循环工况构建中,对怠速段的怠速时间进行拟合分布,选取50百分位下的怠速时长作为可靠性试验片段前后的一段怠速时长并进行拼接,得到可靠性试验循环工况。图22是本发明的实施例中的各典型工况总时间比例图。如图22所示,本实施例中,工况一的时间占比为12%,工况二的时间占比为5%,工况三的时间占比为38%,工况四的时间占比为14%,工况五的时间占比为31%。图23是本发明的实施例中的怠速时间累积概率分布图。如图23所示,50%怠速工况下时间小于12秒,95%怠速工况下时间小于105秒。步骤7,由可靠性试验片段的的循环次数和可靠性试验循环工况编制得到可靠性试验载荷谱。电驱动总成机械系统可靠性试验载荷谱中具有包括速度时间历程、扭矩时间历程的可靠性试验循环工况以及针对电驱动总成机械系统各零部件损伤的可靠性试验片段的的循环次数。图24是本发明的实施例中的可靠性试验循环工况的示意图。如图24所示,图中为本实施例在用户较高损伤强度下得到的一个随机载荷谱。图中,a图为载荷谱速度时间历程;b图为载荷谱扭矩时间历程。载荷谱包含五种典型工况特征,a图中,1表示工况一的可靠性试验片段、2表示工况二的可靠性试验片段、3表示工况三的可靠性试验片段、4表示工况四的可靠性试验片段、5表示工况五的可靠性试验片段,各工况总运行时间分别为:工况一为276秒、工况二为153秒、工况三为902秒、工况四为728秒、工况五为344秒。本实施例中,由多部件损伤协同等效确定各工况循环次数中,本实施例中涵盖机械系统主要部件(轴系零部件、齿轮系零部件)综合损伤效果确定出的各典型工况的可靠性试验片段的循环次数依次是:工况一为1554次、工况二为1791次、工况三为1012次、工况四为2292次、工况五为971次。本实施例中,将构建的可靠性试验载荷谱与标准循环工况或用户载荷谱进行单位损伤强度对比,更体现了构造出电驱动总成可靠性试验载荷谱的可靠性。实施例的作用与效果根据本实施例所涉及的一种电驱动总成机械系统可靠性试验载荷谱的编制方法,基于实际用户道路采集得到用户载荷数据,通过电驱动总成失效主导载荷来构造多维度特征参数,采用机器学习方法完成工况分类确定电驱动总成的五种典型工况,以疲劳损伤理论确定各典型工况下损伤与分布特性,并基于损伤分布连续性选取可靠性试验片段,采用蒙特卡洛仿真确定全寿命周期下各零部件的损伤目标,基于各零部件损伤协同等效确定可靠性试验片段的循环次数,并基于马尔科夫过程下的状态转移概率对各典型工况的可靠性试验片段拼接,最终得到电驱动总成机械系统可靠性试验载荷谱,因此载荷谱完全源于用户行驶工况,通过智能分类后得到五种典型工况,且通过选取各典型工况下损伤强度较高的片段作为可靠性试验片段来进行载荷谱编制,能够加速试验过程、缩短试验时间,为电驱动总成乃至电动汽车的高质量开发提供支持。上述实施方式为本发明的优选案例,并不用来限制本发明的保护范围。当前第1页12