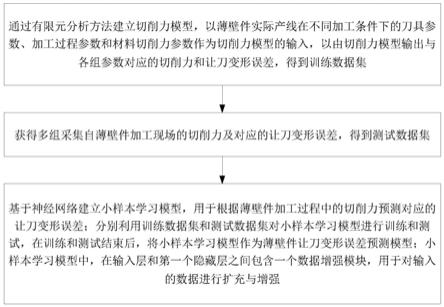
1.本发明属于加工误差预测领域,更具体地,涉及一种薄壁件让刀变形误差预测模型建立方法及其应用。
背景技术:2.在薄壁件加工过程中,让刀变形误差与切削力信号、振动信号等各种可测量信号之间呈现显著的非线性关系。薄壁件零部件广泛应用于航空航天领域中,其产品种类多,更新换代快,对加工过程中的快速响应提出了较高的需求。薄壁零部件的服役性能的好坏很大程度上取决于加工精度的高低。航空航天类零部件大多属于空间自由曲面,由难加工材料制成,加工依赖多轴联动数控机床,切削过程中载荷较大,制造工艺稳定性差,工件以及刀具都会不可避免的产生加工变形,从而导致加工误差,影响最终的加工精度与加工质量。薄壁件最终的误差值来源于工件端和刀具端。在薄壁零件加工过程中,常会使用直径较小的刀具进行微细加工,因此在薄壁件微细加工中,让刀变形误差值是引起整体加工误差值的重要原因之一。通过对让刀变形误差等加工误差进行预测,使得在加工过程中可以进行误差控制,从而有效减小加工误差,提高加工精度。因此,加工误差的预测尤为重要。
3.随着深度学习的快速发展,已有研究将深度学习应用到了机械领域中,但是,当前深度学习的研究大多是基于充足的数据样本,而在机械领域中,尤其是在面向航空航天复杂薄壁件加工的工业场景中,薄壁件属于小批量加工,但是加工精度要求很高。因此,在航空航天领域中所能获取到的实际真实加工样本数据一般较少。同时,航空航天领域中薄壁加工件受限于实验成本,使得研究中的样本稀疏问题变得更加突出。数据样本量少,会使得模型训练次数下降,会使得加工预测拟合结果的可信度下降。因此数据驱动模型所存在的较小输入样本量问题成为当前薄壁件加工误差预测中的难点之一。
4.在传统的实验方法中,主要是对加工工件进行有限元建模,对建模后的有限元模型进行仿真,得到大量的仿真数据,并利用所得到的大量仿真数据来替代真实加工样本数据,由此解决真实加工样本数据少的问题。有限元仿真方法能够有效解决实际加工中数据测量与获取困难问题,但是有限元仿真方法在边界条件设定等方面存在着一定的局限性。最终的加工误差预测结果精度不高。
技术实现要素:5.针对现有技术的缺陷和改进需求,本发明提供了一种薄壁件让刀变形误差预测模型建立方法及其应用,其目的在于,提高对薄壁件加工过程中让刀变形误差的预测精度。
6.为实现上述目的,按照本发明的一个方面,提供了一种薄壁件让刀变形误差预测模型建立方法,包括:
7.通过有限元分析方法建立切削力模型,以薄壁件实际产线在不同加工条件下的刀具参数、加工过程参数和材料切削力参数作为切削力模型的输入,以由切削力模型输出与各组参数对应的切削力和让刀变形误差,得到训练数据集;
8.获得多组采集自薄壁件加工现场的切削力及对应的让刀变形误差,得到测试数据集;
9.基于神经网络建立小样本学习模型,用于根据薄壁件加工过程中的切削力预测对应的让刀变形误差;分别利用训练数据集和测试数据集对小样本学习模型进行训练和测试,在训练和测试结束后,将小样本学习模型作为薄壁件让刀变形误差预测模型;
10.其中,小样本学习模型中,在输入层和第一个隐藏层之间包含一个数据增强模块,用于对输入的数据进行扩充与增强。
11.本发明按照薄壁件实际加工中给定的加工刀具参数、加工过程参数和材料切削力系数设置有限元仿真的初始条件,仿真得到的切削力和对应的让刀变形误差能够很好地贴合航空航天现场产线的实际生产情况,从而保证模型的训练效果;由于仿真得到的训练数据集与实际加工现场中的数据集规模相同,同样存在着数据样本数较少的问题,本发明在神经网络的基础上,在输入层和第一个隐藏层之间加入用于对输入数据进行扩充与增强的数据增强模块,能够更高效地使用所获得的小样本数据产生大量的训练数据,从而缓解小样本数据下的数据欠定情况,保证训练得到的模型预测结果的可信度;本发明利用来自实际加工现场的真实切削力及对应的让刀变形误差构架测试数据集,对训练后的模型进行测试,能够进一步提高模型的预测精度。
12.进一步地,数据增强模块通过对抗生成式网络对输入的数据进行扩充与增强。
13.标准的数据增强只产生有限的貌似真实的可替代数据,本发明通过生成对抗式网络对输入的数据进行扩充与增强,能够产生更多有效的训练样本,保证模型的训练效果。
14.进一步地,对抗生成式网络中的生成器对输入的数据进行扩充与增强,包括:
15.(s1)对于原始输入的数据点,将其作为原数据点q,并转入步骤(s2);
16.(s2)根据生成一个新的数据点ω,并按照q=g(p,ω)对原数据点q进行更新;
17.(s3)重复执行步骤(s2),直至达到预设的迭代次数,将原始输入的数据点和所有生成的新的数据点组成增强后的数据集,由此实现对输入数据的扩充与增强;
18.其中,为生成器的生成函数,p是隐含的使数据生成变化的高斯变量,g为用于对原数据点q进行更新的函数。
19.本发明通过上述迭代方式,对输入的数据进行扩充和增强,在每次迭代开始前,都借助于一个高斯变量对生成器的生成函数的输入进行更新,能够降低对生成函数的要求,保证能够产生更多有效的训练样本。
20.进一步地,小样本学习模型中,每两个相邻的隐藏层之间包含一个泛化模块;
21.泛化模块,用于通过快慢权重算法对其所连接的隐藏层参数进行调整。
22.本发明通过在小样本学习模型中,每两个相邻的隐藏层之间加入一个泛化模块,以通过快慢权重算法对泛化模块所连接的隐藏层参数进行调整,能够增加模型的泛化能力,进一步保证模型的预测精度。
23.进一步地,小样本学习模型中,最后一个隐层与输出层之间包含一个注意力模块;
24.注意力模块,用于通过注意力机制对最后一个隐藏层输出的数据中每一维元素被选择的概率进行调整,以筛选出感兴趣的元素。
25.本发明在小样本学习模型中的最后一个隐层与输出层之间增加一个注意力模块,
以通过注意力机制对最后一个隐藏层输出的数据中每一维元素被选择的概率进行调整,调整结果为使得薄壁件加工误差最小的局部最优解,由此能够准确筛选出感兴趣的元素,进一步保证模型的预测精度。
26.进一步地,刀具参数包括:刀具直径、切削刃螺旋角和刀具径向柔度;
27.加工过程参数包括:主轴转速、每齿进给量、法向切深和行距;
28.材料切削力参数系数包括:切向剪切力系数、径向剪切力系数和轴向剪切力系数。
29.本发明以上述薄壁件实际加工中给定的加工刀具参数、加工过程参数和材料切削力系数设置有限元仿真的初始条件,能够准确通过有限元仿真的方法获得各组参数对应的切削力和让刀变形误差。
30.进一步地,本发明提供的薄壁件让刀变形误差预测模型建立方法,还包括:
31.在实验室条件下使用刀具,对与实际加工薄壁件相同的材料进行刚度校准测量,得到刀具的动刚度值dt;
32.根据刚度校准测量得到的刀具的动刚度值dt,对输入切削力模型的加工过程参数进行调整,以减小基于刀具的动刚度值dt计算的让刀变形误差,与切削力模型输出的让刀变形误差之间的差距。
33.本发明借助刚度校准测量得到的动刚度值dt对输入切削力模型的加工过程参数进行调整,以减小基于刀具的动刚度值dt计算的让刀变形误差,与切削力模型输出的让刀变形误差之间的差距,保证了利用切削力模型所获得的训练数据集中样本的准确性,从而保证了训练结束后,模型具有较高的预测精度。
34.按照本发明的另一个方面,提供了一种薄壁件让刀变形误差预测方法,包括:
35.将薄壁件加工现场测得的真实切削力输入由本发明提供的薄壁件让刀变形误差预测模型建立方法所建立的薄壁件让刀变形误差预测模型,以由薄壁件让刀变形误差预测模型预测出对应的让刀变形误差。
36.由于本发明所提供的薄壁件让刀变形误差预测模型建立方法所建立的薄壁件让刀变形误差预测模型具有较高的预测精度,本发明所提供的薄壁件让刀变形误差预测方法能够准确预测出薄壁件加工过程中的让刀变形误差,从而为后续的误差控制提供明确的指示,有效保证了薄壁件的加工精度和加工质量。
37.按照本发明的又一个方面,提供了一种计算机可读存储介质,包括存储的计算机程序;计算机程序被处理器执行时,控制计算机可读存储介质所在设备执行本发明提供的薄壁件让刀变形误差预测模型建立方法,和/或本发明提供的薄壁件让刀变形误差预测方法。
38.总体而言,通过本发明所构思的以上技术方案,能够取得以下有益效果:
39.(1)本发明按照薄壁件实际加工中给定的加工刀具参数、加工过程参数和材料切削力系数设置有限元仿真的初始条件,仿真得到的切削力和对应的让刀变形误差能够很好地贴合航空航天现场产线的实际生产情况,从而保证模型的训练效果;在神经网络的基础上,在输入层和第一个隐藏层之间加入用于对输入数据进行扩充与增强的数据增强模块,能够更高效地使用所获得的小样本数据产生大量的训练数据,从而缓解小样本数据下的数据欠定情况,保证训练得到的模型预测结果的可信度;利用来自实际加工现场的真实切削力及对应的让刀变形误差构架测试数据集,对训练后的模型进行测试,能够进一步提高模
型的预测精度。
40.(2)本发明通过在小样本学习模型中,每两个相邻的隐藏层之间加入一个泛化模块,以通过快慢权重算法对泛化模块所连接的隐藏层参数进行调整,能够增加模型的泛化能力,进一步保证模型的预测精度。
41.(3)本发明通过在小样本学习模型中的最后一个隐层与输出层之间增加一个注意力模块,以通过注意力机制对最后一个隐藏层输出的数据中每一维元素被选择的概率进行调整,调整结果为使得薄壁件加工误差最小的局部最优解,由此能够准确筛选出感兴趣的元素,进一步保证模型的预测精度。
附图说明
42.图1为本发明实施例提供的薄壁件让刀变形误差预测模型建立方法流程图;
43.图2为本发明实施例提供的切削力模型示意图;
44.图3为本发明实施例提供的小样本学习模型示意图;
45.图4为现有的快慢权重算法中的元网络结构示意图。
具体实施方式
46.为了使本发明的目的、技术方案及优点更加清楚明白,以下结合附图及实施例,对本发明进行进一步详细说明。应当理解,此处所描述的具体实施例仅仅用以解释本发明,并不用于限定本发明。此外,下面所描述的本发明各个实施方式中所涉及到的技术特征只要彼此之间未构成冲突就可以相互组合。
47.在本发明中,本发明及附图中的术语“第一”、“第二”等(如果存在)是用于区别类似的对象,而不必用于描述特定的顺序或先后次序。
48.为了解决现有的薄壁件加工误差预测方法因真实加工样本数据少,预测精度不高的技术问题,本发明提供了一种薄壁件让刀变形误差预测模型建立方法及其应用,其整体思路在于:利用有限元仿真的方法建立切削力模型,以实际加工中给定的加工刀具参数、加工过程参数和材料切削力系数作为切削力模型,得到切削力和对应的让刀变形误差,得到与实际加工现场中的数据规模相同的小样本训练数据集,利用训练数据集对小样本学习模型进行训练;小样本学习模型中,在输入层和第一个隐藏层之间插入了数据增强模块,用于对输入的数据进行扩充与增强,以缓解小样本数据下的数据欠定情况,保证模型的训练效果;在模型训练结束后,利用从采集自实际加工现场的切削力及对应的让刀变形误差构建测试数据集,对小样本学习模型进行测试,进一步保证模型的预测精度。
49.以下为实施例。
50.实施例1:
51.一种薄壁件让刀变形误差预测模型建立方法,如图1所示,包括:
52.通过有限元分析方法建立切削力模型,切削力模型用于以加工过程中的参数为输入,输出对应的切削力和让刀变形误差;以薄壁件实际产线在不同加工条件下的刀具参数、加工过程参数和材料切削力参数作为切削力模型的输入,以由切削力模型输出与各组参数对应的切削力和让刀变形误差,得到训练数据集;
53.获得多组采集自薄壁件加工现场的切削力及对应的让刀变形误差,得到测试数据
集;
54.基于神经网络建立小样本学习模型,用于根据薄壁件加工过程中的切削力预测对应的让刀变形误差;分别利用训练数据集和测试数据集对小样本学习模型进行训练和测试,在训练和测试结束后,将小样本学习模型作为薄壁件让刀变形误差预测模型;
55.本实施例所建立的切削力模型如图2所示,其中,刀具参数包括:刀具直径d、切削刃螺旋角β和刀具径向柔度p;
56.加工过程参数包括:主轴转速n、每齿进给量f、法向切深a和行距m;
57.材料切削力参数系数包括:切向剪切力系数k
tc
、径向剪切力系数k
rc
和轴向剪切力系数k
ac
;
58.通过该切削力模型,在有限元仿真过程中,将刀具离散成许多刀具微元,每一个刀具微元可看作为独立的切削过程,构建刀具微元的切削力模型表达式如下:
[0059][0060]
其中,切向、径向、轴向的三个方向的切削力微元值以df
t
、df
r
、df
a
表示,h
a
表示刀具微元对应的瞬时未变形的切厚,db表示切屑微元的宽度,切向、径向、轴向的三个方向的切削力系数以k
tc
、k
rc
、k
ac
表示;对切向、径向、轴向的切削力微元进行积分,得到切向、径向、轴向的切削力值f
t
、f
r
、f
a
;
[0061]
刀具坐标系的三个方向是刀具的切向、径向、轴向,三轴方向两两正交;工件坐标系为自然坐标系,由x、y、z三轴构成,三轴方向两两正交;与工件坐标系之间的夹角是α,通过坐标变换,可以得到工件坐标系下的三向切削力f
x
、f
y
、f
z
,两类坐标系下的切削力转换方程为:
[0062][0063]
通过输入刀具参数,即刀具直径d、切削刃螺旋角β和刀具径向柔度p,并且输入加工过程参数,即主轴转速n、每齿进给量f、法向切深a、行距m,可以在实验室条件下使用加工薄壁件的刀具,对与实际加工工件相同的材料进行刚度校准测量;
[0064]
刚度校准测量的具体的测量过程为:通过移动加工机床,使得刀具的刀尖点接触到待加工表面,使得刀具与工件恰好接触,调整测力仪,使得读数为零。向工件方向移动机床,使得工件与刀具接触,每移动等距离后,对测力仪示数进行记录,直到测力仪示数增加到3牛顿左右,停止移动机床;绘制测力仪下的接触力示数与移动距离之间的关系曲线,根据求解曲线的斜率,以及加工过程参数主轴转速n、每齿进给量f、法向切深a,得到刀具的动刚度值dt;
[0065]
让刀变形误差值e可以通过切削力f与刀具的动刚度值dt计算得到,其中切削力f是通过刀具微元的切削力模型沿工件坐标系分解后得到的,刀具让刀误差值e的计算可以简化为如下的方程表达式:
[0066][0067]
在实际现场的薄壁件加工让刀误差预测中,很难直接获取到对应刀具的动刚度;
[0068]
本实施例按照薄壁件实际加工中给定的加工刀具参数、加工过程参数和材料切削力系数设置有限元仿真的初始条件,仿真得到的切削力和对应的让刀变形误差能够很好地贴合航空航天现场产线的实际生产情况,从而保证模型的训练效果;
[0069]
本实施例通过有限元仿真软件,将实际加工场景中有限个数的加工参数条件输入有限元仿真软件,仿真软件会输出刀位点行、刀位点列、仿真周期、刀路行数、刀路列数。通过刀位点行、刀位点列、仿真周期,可以由有限元仿真软件计算得到切削力值;通过刀路行数、刀路列数,可以由有限元仿真软件计算得到让刀变形误差值。最终,有限元仿真软件可以输出切削力与让刀变形误差值,由此构建后续中小样本学习模型的数据集d
fl
,该数据集中包含有限元仿真模型输出的切削力数据f与让刀变形误差数据e,因此可以将数据集d
fl
写作为:d
fl
={f、e}。
[0070]
本实施例所建立的小样本学习模型如图3所示,小样本学习模型中,在输入层和第一个隐藏层之间包含一个数据增强模块,用于对输入的数据进行扩充与增强;
[0071]
由于标准的数据增强只产生有限的貌似真实的可替代数据,为了能够更高效地使用所获得的小样本数据产生大量的训练数据,从而缓解小样本数据下的数据欠定情况,保证训练得到的模型预测结果的可信度,作为一种优选的实施方式,本实施例中,数据增强模块通过对抗生成式网络对输入的数据进行扩充与增强;
[0072]
可选地,本实施例中,对抗生成式网络中的生成器对输入的数据进行扩充与增强,包括:
[0073]
(s1)对于原始输入的数据点,将其作为原数据点q,并转入步骤(s2);
[0074]
(s2)根据生成一个新的数据点ω,并按照q=g(p,ω)对原数据点q进行更新;
[0075]
(s3)重复执行步骤(s2),直至达到预设的迭代次数,将原始输入的数据点和所有生成的新的数据点组成增强后的数据集,由此实现对输入数据的扩充与增强;
[0076]
其中,为生成器的生成函数,p是隐含的使数据生成变化的高斯变量,g为用于对原数据点q进行更新的函数;本实施例中,高斯变量p所服从的高斯模型的均值为0,方差为i,即p=n(0,i);
[0077]
本实施例通过上述迭代方式,对输入的数据进行扩充和增强,在每次迭代开始前,都借助于一个高斯变量对生成器的生成函数的输入进行更新,能够降低对生成函数的要求,保证能够产生更多有效的训练样本。
[0078]
作为一种优选的实施方式,如图3所示,本实施例中,小样本学习模型中,每两个相邻的隐藏层之间包含一个泛化模块;
[0079]
泛化模块,用于通过快慢权重算法对其所连接的隐藏层参数进行调整,由此能够增加模型的泛化能力,进一步保证模型的预测精度;
[0080]
快慢权重算法是基于元学习算法的一种泛化形式:通过元网络,学习一个元层次
的知识跨越任务。如图4所示,元网络包含两个学习部分:一个基学习器(base learner)和一个元学习器(meta learner),并且装有一个外部记忆层,学习的过程在两个独立的空间中分别发生。基学习器在输入任务空间中运行,然而元学习器在一个任务不可知的元空间中运行。基学习器首先分析输入任务,同时,基学习器为元学习提供一个更高阶的元信息去阐述其自身在当前的任务空间的状态。基于元信息,元学习器对自身以及基学习器进行快速参数化,因此元网络模型能够辨识出输入任务的新概念。元网络的训练主要包括三个过程:
①
获取元信息;
②
生成快权重,快权重用于调整各隐藏层内部的参数;
③
优化慢权重,慢权重用于调整数隐藏层之间的关系。在快慢权重算法中,为了实现基学习器中的慢权重快速泛化扩展到相应的快权重值,可以使用层增强的方法。增强层的输入首先被快权重和慢权重转换,并且在通过非线性函数转换得到。在实施例中使用的非线性函数是sigmoid函数,对于输入的自变量t,该函数的基本表达式如下:
[0081][0082]
将每层经过sigmoid函数变换后的快、慢权重值进行求和,并作为新的输入,对下一层的快、慢权重值进行分配。以此类推,对最后一层快、慢权重进行求和之后,再经过softmax函数,可以将预测的结果以概率的形式输出。若设softmax函数层的上层输出为l={l1、l2、...、l
j
、...、l
j
},其中j是最后一层增强层的输出值个数,l
j
是所输出值的其中一个中间值。softmax函数的表达式为:
[0083][0084]
最终,通过softmax函数之后,所输出的φ(l
j
)是以概率的形式得到的预测量。
[0085]
作为一种优选的实施方式,如图3所示,本实施例中,小样本学习模型中,最后一个隐层与输出层之间包含一个注意力模块;
[0086]
注意力模块,用于通过注意力机制对最后一个隐藏层输出的数据中每一维元素被选择的概率进行调整,以筛选出感兴趣的元素,即注意力焦点,进而后续的加工精度预测会对这一部分数据进行更加详细且深入的分析;
[0087]
注意力机制中的注意力焦点因子设为u,假设注意力机制的原始输入有n维,注意力焦点因子的取值范围是u∈{0,1},表示每一维的注意力值是否被选择;或者是u∈[0,1],表示每一维注意力值被选择的概率。将监督约束误差与重构误差进行累加,所得的误差函数表达式为注意力机制的代价损失函数;对该代价函数求解偏导数,得到局部最优解u
*
,该最优解对应的是薄壁件加工误差最小的情况,实现对薄壁件让刀误差的预测。
[0088]
为了进一步保证模型的预测精度,作为一种优选的实施方式,本实施例还包括:
[0089]
在实验室条件下使用刀具,对与实际加工薄壁件相同的材料进行刚度校准测量,得到刀具的动刚度值dt;具体的刚度校准测量过程,可参考上述描述,在此将不作复述;
[0090]
根据刚度校准测量得到的刀具的动刚度值dt,对输入切削力模型的加工过程参数进行调整,以减小基于刀具的动刚度值dt计算的让刀变形误差,与切削力模型输出的让刀变形误差之间的差距。
[0091]
本实施例借助刚度校准测量得到的动刚度值dt对输入切削力模型的加工过程参
数进行调整,以减小基于刀具的动刚度值dt计算的让刀变形误差,与切削力模型输出的让刀变形误差之间的差距,保证了利用切削力模型所获得的训练数据集中样本的准确性,从而保证了训练结束后,模型具有较高的预测精度。
[0092]
实施例2:
[0093]
一种薄壁件让刀变形误差预测方法,包括:
[0094]
将薄壁件加工现场测得的真实切削力输入由上述实施例1提供的薄壁件让刀变形误差预测模型建立方法所建立的薄壁件让刀变形误差预测模型,以由薄壁件让刀变形误差预测模型预测出对应的让刀变形误差。
[0095]
由于上述实施例1所提供的薄壁件让刀变形误差预测模型建立方法所建立的薄壁件让刀变形误差预测模型具有较高的预测精度,实施例所提供的薄壁件让刀变形误差预测方法能够准确预测出薄壁件加工过程中的让刀变形误差,从而为后续的误差控制提供明确的指示,有效保证了薄壁件的加工精度和加工质量。
[0096]
实施例3:
[0097]
一种计算机可读存储介质,包括存储的计算机程序;计算机程序被处理器执行时,控制计算机可读存储介质所在设备执行上述实施例1提供的薄壁件让刀变形误差预测模型建立方法,和/或上述实施例2提供的薄壁件让刀变形误差预测方法。
[0098]
本领域的技术人员容易理解,以上所述仅为本发明的较佳实施例而已,并不用以限制本发明,凡在本发明的精神和原则之内所作的任何修改、等同替换和改进等,均应包含在本发明的保护范围之内。