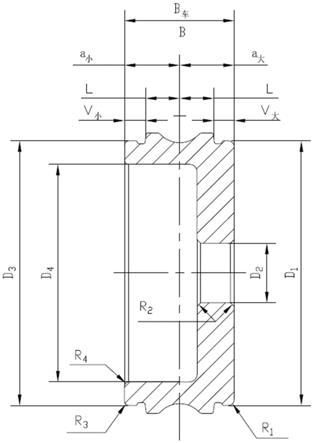
1.本发明涉及轴承生产领域,具体为一种双端面不对称轴承套圈端面磨削留量的设计方法。
背景技术:2.一般的球轴承都是标准零件,轴承套圈都属于对称形的,即轴承套圈两端形状、尺寸、端面宽窄都相同,这种对称的轴承套圈双端面加工,广泛采用立式双端面磨床或卧式双端面磨床进行磨削加工。由于对称轴承套圈端面宽窄相同,两个端面磨削留量设计相同,因此采用双端面磨削不会产生轴承套圈位置精度的变化。
3.但对于角接触轴承套圈、双半轴承内圈、异形轴承套圈等双端面不对称的轴承套圈,采用双端面磨削两个等磨削留量设计的端面时,很容易发生套圈位置尺寸(如沟的位置、密封槽的位置)的变化,这种变化主要是由于不对称轴承套圈的两个端面宽窄不同,在双端面磨削过程中,大端面磨削量少,小端面磨削量多,从而引起位置尺寸变化。为避免这种位置尺寸的变化,很多时候只能采用单端面磨削加工,即先磨削一个端面,然后再磨削另一端面。这样生产加工费时费力、效率低下。
技术实现要素:4.本发明提供了一种双端面不对称轴承套圈端面磨削留量的设计方法,解决双端面不对称轴承套圈采用双端面磨削加工位置尺寸变化的问题,避免采用单端面加工工艺。
5.为实现上述目的,本发明提供如下技术方案:一种双端面不对称轴承套圈端面磨削留量的设计方法,包括以下步骤:
6.s1:推导出磨削面积与磨削留量的比率关系表达式
7.通过对双端面磨削轴承套圈端面的试验,得到磨削时间、磨削速度、磨削留量和磨削面积的关系,表达式为:
[0008][0009]
式中:t——磨削时间,秒;
[0010]
s——磨削面积,mm2;
[0011]
ε——磨削余量,mm;
[0012]
v——磨削速度,mm/秒。
[0013]
采用双端面磨削不对称轴承套圈端面时,设大端面的面积为s
大
、磨削留量为ε
大
,小端面的面积为s
小
、磨削留量为ε
小
,当在同样的速度和时间下磨削双端面时,则有:
[0014][0015]
变换等式得到:
[0016][0017]
从而得到磨削面积与磨削留量的比率关系表达式;
[0018]
s2:计算不对称轴承套圈大、小端面的面积
[0019][0020][0021]
式中:s
大
——不对称轴承套圈大端面面积,mm2;
[0022]
s
小
——不对称轴承套圈小端面面积,mm2;
[0023]
d1——不对称轴承套圈大端面外径尺寸,mm;
[0024]
r1——不对称轴承套圈大端面外径径向倒角平均尺寸,mm;
[0025]
d2——不对称轴承套圈大端面内径尺寸,mm;
[0026]
r2——不对称轴承套圈大端面内径径向倒角平均尺寸,mm;
[0027]
d3——不对称轴承套圈小端面外径尺寸,mm;
[0028]
r3——不对称轴承套圈小端面外径径向倒角平均尺寸,mm;
[0029]
d4——不对称轴承套圈小端面内径尺寸,mm;
[0030]
r4——不对称轴承套圈小端面内径径向倒角平均尺寸,mm;
[0031]
s3:设计大、小两个端面的磨削留量
[0032]
根据公式(2)、(3)、(4),通过计算得到不对称轴承套圈的大端面和小端面的面积比,接着给不对称轴承套圈的大端面预设一个磨削留量ε
大
,从而根据公式(2)设计出不对称轴承套圈小端面的磨削留量ε
小
;
[0033]
s4:根据上面预设出的磨削留量ε
大
和ε
小
通过立式和卧式双端磨床进行端面磨削加工,再测量沟道相对轴承套圈的大端面位置尺寸或沟道中心相对轴承套圈的大、小两个端面的对称度的变化,以及密封槽相对沟中心对称度的变化,以验证预设的磨削留量ε
小
和ε
大
的正确性。
[0034]
与现有技术相比,本发明的有益效果是:
[0035]
通过对双端面磨削不对称轴承套圈位置尺寸变化的研究,发现在单位时间内不对称轴承套圈大端面与小端面的磨削量的变化具有规律。根据这种变化规律,针对性的设计大端面和小端面的磨削留量,从而达到不对称轴承套圈采用双端面磨削且不发生位置尺寸变化的目的,沟道中心相对端面、密封槽产生位置尺寸变化的难题,提高了双端面不对称轴承套圈端面磨削的加工效率,降低了生产成本。
附图说明
[0036]
图1为本发明的汽车张紧轮轴承用异型不对称轴承内圈的结构图;
[0037]
图2为本发明的角接触球轴承内圈的结构图。
具体实施方式
[0038]
下面将结合本发明实施例中的附图,对本发明实施例中的技术方案进行清楚、完整地描述。
[0039]
如图1
‑
2所示,本发明提供一种双端面不对称轴承套圈端面磨削留量的设计方法,包括以下步骤:
[0040]
首先,假设采用同一台双端面磨床磨削对称和不对称轴承套圈双端面时,双端面不对称轴承套圈除小端面宽度与对称轴承套圈端面宽度不同外,材料等均相同。由于采用同一台双端面磨床,因此砂轮规格、磨削压力、磨削速度、润滑等又都可以视为已知条件,此时唯一不同的只有不对称轴承套圈的端面宽度,即不对称套圈大端面和小端面面积的大小不同。
[0041]
s1:推导出磨削面积与磨削留量的比率关系表达式
[0042]
通过对双端面磨削轴承套圈端面的试验,得到磨削时间、磨削速度、磨削留量和磨削面积的关系,表达式为:
[0043][0044]
式中:t——磨削时间,秒;
[0045]
s——磨削面积,mm2;
[0046]
ε——磨削余量,mm;
[0047]
v——磨削速度,mm/秒。
[0048]
采用双端面磨削不对称轴承套圈端面时,设大端面的面积为s
大
、磨削留量为ε
大
,小端面的面积为s
小
、磨削留量为ε
小
,当在同样的速度和时间下磨削双端面时,则有:
[0049][0050]
变换等式得到:
[0051][0052]
从而得到磨削面积与磨削留量的比率关系表达式;
[0053]
s2:计算不对称轴承套圈大、小端面的面积
[0054][0055][0056]
式中:s
大
——不对称轴承套圈大端面面积,mm2;
[0057]
s
小
——不对称轴承套圈小端面面积,mm2;
[0058]
d1——不对称轴承套圈大端面外径尺寸,mm;
[0059]
r1——不对称轴承套圈大端面外径径向倒角平均尺寸,mm;
[0060]
d2——不对称轴承套圈大端面内径尺寸,mm;
[0061]
r2——不对称轴承套圈大端面内径径向倒角平均尺寸,mm;
[0062]
d3——不对称轴承套圈小端面外径尺寸,mm;
[0063]
r3——不对称轴承套圈小端面外径径向倒角平均尺寸,mm;
[0064]
d4——不对称轴承套圈小端面内径尺寸,mm;
[0065]
r4——不对称轴承套圈小端面内径径向倒角平均尺寸,mm;
[0066]
s3:设计大、小两个端面的磨削留量
[0067]
根据公式(2)、(3)、(4),通过计算得到不对称轴承套圈的大端面和小端面的面积比,接着给不对称轴承套圈的大端面预设一个磨削留量ε
大
,从而根据公式(2)设计出不对称轴承套圈小端面的磨削留量ε
小
;
[0068]
例如:大端面d1=36.5mm,r1=0.8mm,d2=8.3mm,r2=0.5mm;小端面d3=36.5mm,r3=0.6mm,d4=30mm,r4=0.6mm,则面积比为:
[0069][0070]
预设大端面磨削留量为ε
大
=0.03mm,则小端面磨削留量ε
小
为:
[0071][0072]
在本实施例中,不对称轴承套圈的公称宽度为b=15mm,生产控制要求为b=14.98
±
0.02mm,双端面磨削后,沟道中心相对大、小端面的对称度为≤0.06mm,则沟道中心相对大、小端面的尺寸可以设计为:
[0073][0074][0075]
式中:a
大
——不对称轴承套圈沟道中心到大端面的尺寸,mm;
[0076]
a
小
——不对称轴承套圈沟道中心到小端面的尺寸,mm;
[0077]
则车工件的总宽度b
车
为:
[0078]
b
车
=a
大
+a
小
=7.52+7.615=15.135mm;
[0079]
尺寸公差采用正负公差。
[0080]
非对称套圈大、小两个端面设计有密封槽的,其设计过程同上。
[0081]
以上设计过程和计算结果,是在条件假设的条件下建立的,如果假设条件成立,则以上设计过程和计算结果有效。假设条件为:采用同一台双端面磨削设备,除不对称轴承套圈小端面宽度不同外,材料等其他所有条件均相同。由实际生产过程可知,轴承的材料一般均为滚动轴承钢gcr15,而双端面mb4363(立式)、my7650(卧式)等设备在一定范围内均可以磨削不同型号的产品,所以假设条件非常容易满足,因此以上设计过程和计算结果有效。
[0082]
s4:根据上面预设出的磨削留量ε
大
和ε
小
通过立式和卧式双端磨床进行端面磨削加工,再测量沟道相对轴承套圈的大端面位置尺寸或沟道中心相对轴承套圈的大、小两个端面的对称度的变化,以及密封槽相对沟中心对称度的变化,以验证预设的磨削留量ε
小
和ε
大
的正确性;
[0083]
由于双端面不对称轴承套圈大、小两个端面的磨削留量设计不同,因此设计的车工件图纸上沟道和密封槽位置相对大、小两个端面为不称状态,即:沟道中心相对大端面距离尺寸小、相对小端面距离尺寸大;车工件密封槽位置相对沟道中心对称,但相对大端距离尺寸小,相对小端面距离尺寸大。
[0084]
主要验证采用本发明设计大、小两个端面磨削留量的产品,经双端面加工后:1)沟道中心相对大、小两个端面对称度数值符合预期或相对基准端面尺寸符合控制目标;2)密封槽位置相对沟道中心仍然对称,实验数据见下表1:
[0085]
表1
[0086][0087]
由上述表格可见:
[0088]
(1)1#和2#实验产品车工件沟道中心相对大、小端面不对称,磨削端面前数据为沟道中心距基准面的位置尺寸,磨削端面后的数据为沟道中心相对大、小端面的对称度数值。此数值越小,则说明设计效果符合预期,数值越大,则说明设计不符合预期。参考类似双端面对称轴承套圈车工件的对称度数值,预期数值为≤0.06mm。
[0089]
(2)3#实验产品端面磨削前后的数据均为沟道中心距基准面和密封槽的位置尺寸。
[0090]
实验数据表明,采用立式和卧式双端面磨床虽然数据上稍有差异,但综合产品的公差和测量误差,其结果仍然符合预期值,据此可认为本发明的设计方法可行。
[0091]
实施例一:汽车张紧轮轴承用异型不对称轴承内圈(如图1所示)
[0092]
参数:内圈公称宽度b=15mm,生产控制要求为b=14.98
±
0.02mm,大基准面a为大端面,端面d1=36.5mm,r1=0.8mm,d2=8.3mm,r2=0.5mm;小端面d3=36.5mm,r3=0.6mm,d4=30mm,r4=0.6mm。
[0093]
(1)大端面与小端面的面积比为:
[0094][0095]
(2)预设大端面磨削留量为ε
大
=0.03mm,根据公式2,小端面磨削留量ε
小
为:
[0096]
[0097]
(3)根据已设计的大、小端面的磨削留量,设计沟道中心相对大、小端面的尺寸为:
[0098][0099][0100]
(4)车工件的总宽度b
车
为:
[0101]
b
车
=a
大
+a
小
=7.52+7.615=15.135mm;
[0102]
尺寸公差采用正负公差。
[0103]
(5)密封槽设计以沟道中心对称,密封槽距离沟道中心的尺寸为l=4.7
±
0.03mm,根据a
大
和a
小
尺寸,通过计算便可以得到密封槽距大端面和小端面的尺寸,分别为:
[0104]
v
大
=a
大
‑
4.7=7.52
‑
4.7=2.82mm;
[0105]
v
小
=a
小
‑
4.7=7.615
‑
4.7=2.915mm;
[0106]
实施例二:角接触球轴承内圈(如图2所示)
[0107]
参数:内圈公称宽度b=15mm,生产控制要求为b=14.98
±
0.02mm,大基准面a为大端面,端面磨削后a
大
=8.14
±
0.02mm,大端面d1=26.1mm,r1=0.4mm,d2=19.86mm,r2=1mm;小端面d3=23.65mm,r3=0.7mm,d4=19.86mm,r4=0.5mm。
[0108]
(1)大端面与小端面的面积比为:
[0109][0110]
(2)预设大端面磨削留量为ε
大
=0.03mm,根据公式2,小端面磨削留量ε
小
为:
[0111][0112]
(3)根据已设计的大、小端面的磨削留量,设计沟道中心相对大、小端面的尺寸为:
[0113]
a
大
=8.14+0.03=8.17mm;
[0114]
a
小
=14.98
‑
8.14+0.08=6.92mm;
[0115]
(4)车工件的总宽度b
车
为:
[0116]
b
车
=a
大
+a
小
=8.17+6.92=15.09mm;
[0117]
尺寸公差采用正负公差。
[0118]
(5)密封槽位置,密封槽距离沟道中心的尺寸为l=6.09
±
0.03mm,根据a
大
尺寸,通过计算便可以得到密封槽距大端面的尺寸为:
[0119]
v
大
=a
大
‑
6.09=8.17
‑
6.09=2.08mm。
[0120]
虽然在上文中已经参考实施例对本发明进行了描述,然而在不脱离本发明的范围的情况下,可以对其进行各种改进并且可以用等效物替换其中的部件。尤其是,只要不存在结构冲突,本发明所披露的实施例中的各项特征均可通过任意方式相互结合起来使用,在本说明书中未对这些组合的情况进行穷举性的描述仅仅是出于省略篇幅和节约资源的考虑。因此,本发明并不局限于文中公开的特定实施例,而是包括落入权利要求的范围内的所有技术方案。