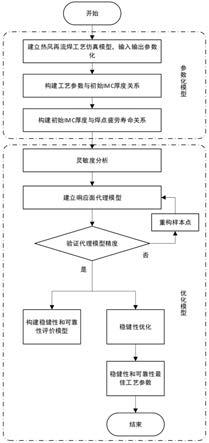
1.本发明涉及到一种热风再流焊工艺优化设计方法,涉及一种基于响应面模型的焊点稳健性与可靠性优化设计方法,尤其是一种热风再流焊工艺的稳健性与可靠性综合优化设计方法。
背景技术:2.热风再流焊工艺是电子产品表面贴装技术(surface mounted technology,简称smt)组装中的一种非常重要且常用的工艺。随着电子产品smt组装集成度越来越高,对热风再流焊工艺的要求也越来越高。目前在热风再流焊工艺设计中普遍采用“实物试验结合经验进行工艺参数调整为主”的工艺设计方法。这种方法是以工艺曲线是否符合工艺性能指标或指定的工艺窗口来不断调整工艺设计参数,不能在工艺设计中综合考虑工艺稳健性指标和工艺可靠性指标。
技术实现要素:3.本发明的目的是提供一种热风再流焊工艺稳健性与可靠性综合设计方法,该方法在考虑现有工艺性能指标的基础上,可以综合考虑工艺的稳健性与可靠性指标来进行工艺参数设计。
4.实现本发明目的的技术方案是:
5.一种热风再流焊工艺的稳健性与可靠性综合优化设计方法,包括以下步骤:
6.步骤一:通过数值仿真方法,建立热风再流焊工艺仿真模型,得到工艺参数与焊点温度曲线之间的对应关系,并将工艺参数和焊点温度曲线进行参数化;
7.步骤二:以焊点的热疲劳寿命作为可靠性评价指标,优化热疲劳寿命至最大的同时进行稳健性优化设计,以焊点的峰值温度、超液相线时间、冷却速率、加热因子、升温速率和保温时间工艺性能参数作为稳健性评价指标,将其作为综合优化设计的约束条件,约束规则设置为:
8.峰值温度+6σ1≤峰值温度上限值;
9.超液相线时间+6σ2≤超液相线时间上限值;
10.冷却速率+6σ3≤冷却速率上限值;
11.加热因子+6σ4≤加热因子上限值;
12.升温速率+6σ5≤升温速率上限值;
13.保温时间+6σ6≤保温时间上限值;
14.峰值温度
‑
6σ1≥峰值温度下限值;
15.超液相线时间
‑
6σ2≥超液相线时间下限值;
16.冷却速率
‑
6σ3≥冷却速率下限值;
17.加热因子
‑
6σ4≥加热因子下限值;
18.升温速率
‑
6σ5≥升温速率下限值;
19.保温时间
‑
6σ6≥保温时间下限值;
20.其中,σ1为峰值温度的标准差,σ2为超液相线时间的标准差,σ3为冷却速率的标准差,σ4为加热因子的标准差,σ5为升温速率的标准差,σ6为保温时间的标准差;
21.步骤三:基于金属间化合物(intermetallic compound,简称imc)工艺生长实验,根据imc厚度生长实验结果,构建冷却时间、超液相线时间和峰值温度工艺参数与焊点初始imc厚度的关系式;
22.步骤四:根据实验或数值仿真结果,得到不同初始imc厚度与焊点热疲劳寿命的关系式;
23.步骤五:计算焊点的热疲劳寿命,采用空间填充拉丁超立方抽样方法,对焊点抽样后,进行灵敏度分析,建立响应面代理模型;
24.步骤六:对代理模型进行确定性优化,并对优化后的模型进行精度验证,各工艺参数响应值误差若满足精度要求,则对该工艺设计方案进行稳健性和可靠性评价;若不满足精度要求则重新构建样本点;
25.步骤七:对确定性优化后的模型和原参数化模型进行稳健性和可靠性综合评价;
26.步骤八:采用自适应响应面优化方法,对代理模型进行稳健性与可靠性综合优化设计,以6σ为设计准则,迭代计算,最终得到一组最为稳健和可靠的工艺参数。
27.与现有的方法相比,本发明的有益效果是:
28.本发明为解决热风再流焊实际工艺过程中工艺参数波动造成的焊接不良问题,提出一种热风再流焊稳健性与可靠性综合优化设计方法,在满足实际工艺设计参数要求的前提下,能够得到一组满足稳健性指标与可靠性指标的最佳工艺参数。
附图说明
29.图1是本发明实施例中热风再流焊工艺的稳健性和可靠性优化设计方法流程图;
30.图2
‑
1是实施例中原参数化模型与确定性优化的超液相线时间最小值的稳健性评估σ水平;
31.图2
‑
2是实施例中原参数化模型与确定性优化的冷却速率最小值的稳健性评估σ水平;
32.图2
‑
3是实施例中原参数化模型与确定性优化的加热因子最小值的稳健性评估σ水平;
33.图3
‑
1是实施例中综合优化设计后的超液相线时间最小值的稳健性评估σ水平;
34.图3
‑
2是实施例中综合优化设计后的冷却速率最小值的稳健性评估σ水平;
35.图3
‑
3是实施例中综合优化设计后的加热因子最小值的稳健性评估σ水平;
36.图4
‑
1是实施例中原参数化模型计算的热疲劳寿命值;
37.图4
‑
2是实施例中确定性优化后的热疲劳寿命值;
38.图4
‑
3是实施例中综合优化设计后的热疲劳寿命值。
具体实施方式
39.下面结合实施例和附图对本发明内容作进一步的阐述,显然,所描述的实施例仅仅是本发明一部分实施例,而不是全部的实施例。基于本发明中的实施例,本领域普通技术
人员在没有作出创造性劳动前提下所获得的所有其他实施例,都属于本发明保护的范围。
40.实施例:
41.如图1所示,本发明提出了一种热风再流焊工艺的稳健性与可靠性综合优化设计方法,包括以下步骤:
42.步骤一:采用ansys workbench建立数值仿真模型,使用的有限元模型的再流焊工艺过程中共包括2个预热区、4个保温区、3个再流区和2个冷却区共11个温区,温区的温度从室温到275℃,将11个温区温度作为参数化模型的关键设计变量,将仿真模型的输出:峰值温度、超液相线时间、冷却速率、加热因子、升温速率和保温时间作为参数化模型的响应;
43.步骤二:根据再流焊工艺并结合具体要求,本方法约束条件包括保温时间60~90s,超液相线时间60~90s,冷却速率1.2~4℃/s,升温速率1.2~2℃/s,峰值温度210~230℃以及加热因子在800~1600s
·
℃,为简化计算,本方法采用单目标优化,优化目标为热疲劳寿命,使热疲劳寿命最大化的同时进行稳健性优化,可保障稳健性和可靠性要求的目的;
44.步骤三:将再流焊曲线的三个参量冷却时间、超液相线时间和峰值温度作为自变量,将imc厚度作为因变量,进行最小二乘拟合,得到的初始imc厚度d与imc温度曲线的关系如下式:
[0045][0046]
其中x1为冷却时间,x2为超液相线时间,x3为峰值温度,d为初始imc厚度;
[0047]
本方法使用optislang作为优化设计平台,在optislang求解器中加入一个计算单元,该计算单元根据拟合的公式计算出初始imc的厚度,并将其作为计算单元的输出;
[0048]
步骤四:在optislang搭建的参数化求解系统中嵌入python模块,该python程序通过上一步计算单元传递过来的初始imc厚度计算焊点的热疲劳寿命,构建的焊点初始imc厚度与焊点热疲劳寿命的关系式如下式所示:
[0049]
n
f
=12954.737
‑
6370.299
×
ln(d)其中n
f
为焊点热疲劳寿命,d为初始imc厚度;
[0050]
步骤五:将搭建好的原参数化模型采用空间填充拉丁超立方抽样100次后进行灵敏度分析,构建代理模型,主要以决定系数(coefficient of determination,简称cod)和预测系数(coefficient of prediction,简称cop)为评判指标,cod和cop越接近1,说明代理模型拟合精度越高,评判拟采用的代理模型,包括线性多项式回归模型、二次多项式回归模型、移动最小二乘和克里金法(kriging)中的一种或多种组合,采用不同的代理模型拟合,使得各约束函数以及目标函数都选用拟合程度最高的代理模型,以减少模型选择不合理造成的误差,最终代理模型见表1所示:
[0051]
表1约束、目标代理模型选择表
[0052][0053]
步骤六:基于确定性结果与同参数下原参数化模型的结果对比,保证各响应误差不大于10%,此过程即为确定性优化分析,采用粒子群优化对基于代理模型拟合的响应面进行快速的局部搜索,构建基于响应面的梯度的优化模块,以基于响应面优化获得的最优变量带入原参数化模型,获得对应的响应值,结果见表2所示:
[0054]
表2精度验证
[0055][0056]
根据精度验证表的结果表明:基于响应面优化结果下各约束值、目标值与原温度场仿真模型的偏差都小于10%,故满足精度要求;
[0057]
步骤七:对满足精度要求的代理模型进行稳健性和可靠性综合设计,根据焊点热疲劳寿命评价模型的可靠性,依照6σ稳健性评价指标评价模型的稳健性,本方法构建的模型部分工艺参数评价结果见图2
‑
1、图2
‑
2和图2
‑
3,评价标准如下:
[0058][0059]
本方法采用的有限元模型设置了8个监测点,共有8组工艺参数,在综合优化设计过程中分别选取各个工艺参数中的最大值与最小值用于稳健性优化设计,其中,n_f为热疲劳寿命;max_max_value为最大峰值温度;max_t为最大超液相线时间;max_coolrate为最大冷却速率;max_heatfactor为最大加热因子;max_preheatrate为最大升温速率;max_soaktime为最大保温时间;min_max_value为最小峰值温度;min_t为最小超液相线时间;min_coolrate为最小冷却速率;min_heatfactor为最小加热因子;min_preheatrate为最小升温速率;min_soaktime为最小保温时间;
[0060]
从图2
‑
1、图2
‑
2和图2
‑
3的结果可以发现,原参数化模型的部分工艺参数稳健性评估结果如冷却速率最小值为
‑
8.23σ,确定性优化后的部分工艺参数稳健性评估结果如超液相线时间最小值为4.78σ,冷却速率最小值为
‑
18.65σ,加热因子最小值为0.32σ,这些工艺参数均未能达到6σ稳健性设计准则,说明设计方案容易受到参数的波动等不确定因素的影响,设计结果稳健性不够,故需要对模型做进一步的稳健性优化设计;
[0061]
步骤八:采用optislang中基于自适应优化方法实现全局寻优,并使用蒙特卡洛方法进行稳健性及可靠性评估抽样,优化后的结果见图3
‑
1、图3
‑
2和图3
‑
3,分析对比的部分结果见表3所示:
[0062]
表3热风再流焊工艺参数稳健性评估对比表
[0063]
[0064][0065]
根据稳健性评估对比表3可以发现,初始设计的部分工艺参数评估结果σ水平为负值,其中最小的σ水平为
‑
8.23,而经过确定性优化设计后的工艺参数评估结果依然存在负σ水平,最小值为
‑
18.65,且有部分稳健性评价指标未能达到6σ;而经过综合优化设计后的各工艺参数稳健性评估结果都达到6σ及以上水平,说明综合优化后的工艺参数稳健性得到提升,并都能达到6σ稳健性设计准则;
[0066]
同时,综合优化后的热疲劳寿命与原参数化模型对比见图4
‑
1、图4
‑
2和图4
‑
3,具体结果见表4所示:
[0067]
表4可靠性评估对比表
[0068][0069]
根据可靠性评估对比表4可以发现,综合优化设计的可靠性指标即热疲劳寿命的均值为4330.08,相比于原模型计算出的3824.28提升了13.2%,优化效果明显,而与确定性优化计算出的4389.53对比,热疲劳寿命相差1.4%,但是相较于确定性优化,本发明提出的综合优化设计方法具有更高的稳健性。
[0070]
综合以上稳健性和可靠性指标的对比可以看出,综合优化设计的可靠性指标和稳健性指标都远优于初始设计;综合优化设计的可靠性指标与确定性优化相当、但稳健性得到明显提高,能够实现6σ稳健性设计准则。
[0071]
尽管已经示出和描述了本发明的实施例,对于本领域的普通技术人员而言,可以理解在不脱离本发明的原理和精神的情况下可以对这些实施例进行多种变化、修改、替换和变型,本发明的保护范围由所附权利要求及其等同物限定。