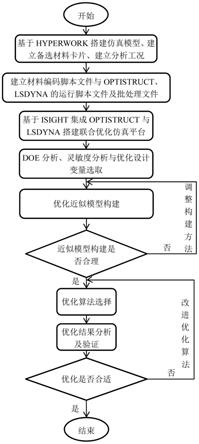
一种基于isight联合仿真的材料及结构优化设计方法
技术领域
1.本发明涉及汽车材料及结构设计技术领域,具体涉及一种基于isight联合仿真的材料及结构优化设计方法。
背景技术:2.轻量化是当今汽车设计的一种理念和手段,符合“安全、节能、环保”的发展方向。车身质量占汽车总质量的40%左右,车身的轻量化对于整车的轻量化起着举足轻重的作用,车身轻量化正成为21世纪汽车技术的前沿和热点。单一材料白车身结构,限于结构拓扑关系,不能很好地解决轻量化与高性能之间的矛盾。混合材料白车身采取材料替换与结构改进相结合的方法,在保证汽车整体性能不降低的前提下,最大限度地减轻各零部件的质量。
3.有限元仿真分析目前在汽车行业有着极为广泛的应用,汽车的cae分析能够完成静力分析、振动噪声分析、流体动力学分析、机械动力学分析和虚拟样机、可靠性分析、安全性分析、结构优化设计等产品设计。hyperwork作为应用广泛的有限元建模软件可以有效地完成各种工况的仿真模型建立及相关结构优化设计,但其无法实现部件的材料优化设计。
技术实现要素:4.本发明的目的是针对现有技术中的问题,提供一种基于isight联合仿真的材料及结构优化设计方法,该方法基于编码后的材料id在isight中联合车身结构进行多目标集成优化设计,用于白车身概念设计阶段的材料选取及材料与部件尺寸匹配,以提高工作效率,适用于混合材料车身开发及轻量化设计。
5.为达到上述目的,本发明采用的技术方案是:一种基于isight联合仿真的材料及结构优化设计方法,所述设计方法包括如下步骤:s1. 基于hyperwork建立白车身仿真模型及备选材料卡片;s2. 建立hyperwork运行的批处理文件及对材料编码的脚本文件;s3. 将步骤s1建立的白车身仿真模型,步骤s2建立的材料编码的脚本文件及批处理文件导入isight软件中,搭建仿真平台;s4. 在所述仿真平台中进行doe分析,利用doe分析灵敏度结果选取用于构建设计变量的零部件材料与结构信息;s5. 基于径向基函数神经网络模型构建近似模型及验证近似模型的准确性;s6. 基于改进遗传算法进行材料及结构的多目标、多工况优化设计;s7. 将优化设计的解分别带入相应的白车身仿真模型中进行优化结果的验证。
6.进一步地,步骤s1中包括如下步骤:(1)在optistruct中建立车身模态工况仿真分析模型,建立不同材料的材料卡片,材料卡片至少包含弹性模量e、密度ρ、泊松比σ的材料信息;
(2)在lsdyna中建立车身碰撞工况仿真分析模型,建立不同材料的材料卡片,材料卡片至少包含弹性模量e、密度ρ、泊松比σ、塑性应力-应变曲线、屈服强度、抗拉强度的材料信息。
7.更进一步地,建立的材料卡片至少包括钢的材料卡片、镁合金的材料卡片、铝合金的材料卡片和碳纤维的材料卡片。
8.进一步地,步骤s2中包括如下步骤:(1)利用.tcl格式的脚本文件中字段“*setvalue comps id=xxx materialid={mats x}”分别实现模态工况的材料编码及碰撞工况的材料编码,其中“xxx”为属性id,“x”为材料id;(2)建立调用optistruct与lsdyna求解器的.bat批处理文件。
9.更进一步地,基于ls-prepost的后处理流程文件,建立用于碰撞结果提取的.cfile脚本文件与调用该.cfile脚本文件的.bat批处理文件。
10.进一步地,所述仿真平台包括模态工况材料优化模块、模态工况结构优化及计算模块、碰撞工况材料优化模块、碰撞工况结构优化及计算模块、碰撞工况结果后处理模块、模态与碰撞工况结果汇总模块,所述模态工况材料优化模块与所述模态工况结构优化及计算模块串联连接形成上下级传递关系,所述碰撞工况材料优化模块、所述碰撞工况结构优化及计算模块与所述碰撞工况结果后处理模块串联连接形成上下级传递关系,所述模态工况材料优化模块、所述模态工况结构优化及计算模块与所述碰撞工况材料优化模块、所述碰撞工况结构优化及计算模块、所述碰撞工况结果后处理模块并联连接相互独立,所述模态与碰撞工况结果汇总模块与其他模块为串联连接关系,步骤s3包括:(1)将模态工况.fem模型文件、模态工况材料编码.tcl脚本文件、模态工况.bat批处理文件导入所述模态工况材料优化模块中,提取材料编码参数,输出修改后的模态工况.fem模型文件;(2)将修改后的模态工况.fem模型文件、模态工况.bat批处理文件导入所述模态工况结构优化及计算模块中,提取零部件尺寸、形状参数;(3)将碰撞工况.k模型文件、碰撞工况材料编码.tcl脚本文件、碰撞工况.bat批处理文件导入所述碰撞工况材料优化模块中,提取材料编码参数,输出修改后的碰撞工况.k模型文件;(4)将修改后的碰撞工况.k模型文件、碰撞工况.bat批处理文件导入所述碰撞工况结构优化及计算模块中,提取零部件尺寸、形状参数,输出碰撞结果文件;(5)将碰撞结果文件、后处理.cfile脚本文件与调用的.bat批处理文件导入所述碰撞工况结果后处理模块;(6)在所述模态与碰撞工况结果汇总模块中进行质量、成本的计算。
11.更进一步地,对于模态工况和碰撞工况,相同部件的材料编码、尺寸参数、形状参数建立到同一个设计变量中,设置尺寸、形状参数为连续变化,材料参数为不连续变化。
12.进一步地,步骤s4包括:(1)在所述仿真平台中基于拉丁超立方抽样方法生成多个训练样本,进行全局灵敏度分析,得出各部件的模态灵敏度与碰撞灵敏度;(2)根据灵敏度分析结果,进行优化设计变量的筛选。
13.更进一步地,步骤s5中,以随机方式生成多组优化设计变量的测试样本,所述测试样本与所述训练样本的数据不能重复,利用所述测试样本的计算结果验证近似模型的准确性。
14.进一步地,步骤s6包括:(1)根据s4步骤筛选的多个部件的材料、尺寸、形状作为优化的设计变量,其中材料参数为非连续变化,变化范围仅为1、2、3、4,尺寸与形状参数为连续变化;(2)选择一阶模态性能、碰撞总吸能、碰撞侵入量作为优化约束条件;(3)选择质量、成本最小作为优化目标;(4)基于多目标遗传算法进行优化设计,寻求全局最优解。
15.由于上述技术方案的运用,本发明与现有技术相比具有下列优点:本发明的基于isight联合仿真的材料及结构优化设计方法以乘用车白车身为研究对象,针对混合车身设计开发需求,建立一种白车身多材料、多目标、多工况集成的优化方案。通过在hyperwork中建立各种备选材料卡片,利用相关脚本文件对材料参数进行编码,实现材料各参数在优化设计过程中协同变化,达到材料优化的可能。同时利用isight搭建优化平台,对编码后的材料参数、cae模型中的零部件尺寸等进行doe分析,建立优化设计的近似数学模型,最终基于“amga”、“nlpql”等优化算法实现车身的材料与结构优化设计,实现整车质量、性能、成本等的多目标、多工况联合优化设计。
附图说明
16.附图1为本发明的基于isight联合仿真的材料及结构优化设计方法的流程图;附图2为本发明的材料编码与材料参数的映射关系示意图;附图3为本发明的isight优化设计流程图。
具体实施方式
17.下面结合附图来对本发明的技术方案作进一步的阐述。
18.如图1所示,本发明的基于isight联合仿真的材料及结构优化设计方法的流程图如图1所示,具体包括如下步骤:s1. 基于hyperwork建立白车身仿真模型及备选材料卡片。
19.具体包括如下步骤:(1)在optistruct中建立车身模态工况仿真分析模型,建立不同材料的材料卡片,材料卡片至少包含弹性模量e、密度ρ、泊松比σ的材料信息。
20.材料卡片至少包括钢的材料卡片id1、镁合金的材料卡片id2、铝合金的材料卡片id3和碳纤维的材料卡片id4。
21.(2)在lsdyna中建立车身碰撞工况仿真分析模型,建立不同材料的材料卡片,材料卡片至少包含弹性模量e、密度ρ、泊松比σ、塑性应力-应变曲线、屈服强度、抗拉强度的材料信息。
22.材料卡片同样至少包括钢的材料卡片id1、镁合金的材料卡片id2、铝合金的材料卡片id3和碳纤维的材料卡片id4。
23.s2. 建立hyperwork运行的批处理文件及对材料编码的脚本文件。
24.具体包括如下步骤:(1)建立.tcl格式的脚本文件用于模态工况的材料编码:利用.tcl脚本文件中字段“*setvalue props id=xxx materialid={mats x}”实现材料的编码,其中“xxx”为属性id,“x”为材料id,将材料标识参数与材料参数之间确定一个映射关系,如图2所示,以每个零部件所用的材料而不是材料参数作为设计变量。
25.(2)同步骤s2-(1),建立.tcl格式的脚本文件用于碰撞工况的材料编码,利用.tcl脚本文件中字段“*setvalue comps id=xxx materialid={mats x}”实现材料的编码,其中“xxx”为属性id,“x”为材料id。
26.(3)建立调用optistruct与lsdyna求解器的.bat批处理文件;由于碰撞工况的结果比较复杂,需要进行一些后处理提取所需要的结果参数,步骤s2还包括:(4)基于ls-prepost的后处理流程文件,建立用于碰撞结果提取的.cfile脚本文件与调用该.cfile脚本文件的.bat批处理文件。
27.s3. 将步骤s1建立的白车身仿真模型,步骤s2建立的材料编码的脚本文件及批处理文件导入isight软件中搭建仿真平台。
28.仿真平台包括模态工况材料优化模块1、模态工况结构优化及计算模块2、碰撞工况材料优化模块3、碰撞工况结构优化及计算模块4、碰撞工况结果后处理模块5、模态与碰撞工况结果汇总模块6。模态工况材料优化模块1、模态工况结构优化及计算模块2串联连接,形成上下级传递关系。碰撞工况材料优化模块3、碰撞工况结构优化及计算模块4、碰撞工况结果后处理模块5依次串联连接,形成上下级传递关系。模态工况材料优化模块1、模态工况结构优化及计算模块2与碰撞工况材料优化模块3、碰撞工况结构优化及计算模块4、碰撞工况结果后处理模块5并联连接相互独立,模态与碰撞工况结果汇总模块6与其他模块均为串联连接关系,如图3所示。
29.步骤s3具体包括如下步骤:(1)将模态工况.fem模型文件、模态工况材料编码.tcl脚本文件、模态工况.bat批处理文件导入模态工况材料优化模块1中,提取材料编码参数,输出修改后的模态工况.fem模型文件。
30.(2)将修改后的模态工况.fem模型文件、模态工况.bat批处理文件导入模态工况结构优化及计算模块2中,提取零部件尺寸、形状参数。
31.(3)将碰撞工况.k模型文件、碰撞工况材料编码.tcl脚本文件、碰撞工况.bat批处理文件导入碰撞工况材料优化模块3中,提取材料编码参数,输出修改后的碰撞工况.k模型文件。
32.(4)将修改后的碰撞工况.k模型文件、碰撞工况.bat批处理文件导入碰撞工况结构优化及计算模块4中,提取零部件尺寸、形状参数,输出碰撞结果文件;(5)将碰撞结果文件、后处理.cfile脚本文件与调用的.bat批处理文件导入碰撞工况结果后处理模块5。
33.(6)在模态与碰撞工况结果汇总模块6中进行质量、成本的计算。
34.为了确保模态模型与碰撞模型在优化设计过程中的设计变量变化一致性,对于模态工况和碰撞工况,相同部件的材料编码、尺寸参数、形状参数建立到同一个设计变量中,
设置尺寸、形状参数为连续变化,材料参数为不连续变化。
35.s4. 在仿真平台中进行doe分析,利用doe分析灵敏度结果选取用于构建设计变量的零部件材料与结构信息。
36.具体包括如下步骤:(1)基于步骤s3中获得的模态工况的材料编码参数、零部件尺寸形状参数和碰撞工况的材料编码参数、零部件尺寸、形状参数,在仿真平台中基于拉丁超立方抽样方法进行采样计算,生成100个训练样本,对100个训练样本进行全局灵敏度分析,得出各部件的模态灵敏度与碰撞灵敏度。
37.(2)根据模态灵敏度与碰撞灵敏度分析结果,进行优化设计变量的筛选:以一定的权重进行零部件各性能灵敏度的合计,筛选出灵敏度较大的前20个部件作为优化设计变量,优化设计变量包括材料、尺寸及形状。
38.s5. 基于径向基函数神经网络模型构建近似模型及验证近似模型的准确性。
39.具体包括如下步骤:(1)建立模态性能、碰撞性能对优化设计变量的数学模型,以径向基函数(rbf)方法建立合理的优化设计近似模型。
40.isight提供四种近似模型构建方法:kriging model、正交多项式模型orthogonal polynomial model、径向基函数神经网络模型rbf model、响应面模型response surface model。有限元模态分析与碰撞分析属于一种复杂的非线性模型,响应面模型与正交多项式模型对于非线性问题不能提供精确的近似,径向基函数神经网络能够逼近任意的非线性函数,因此选择径向基函数神经网络模型(rbf)建立车身质量、体积、模态、碰撞侵入量、碰撞吸能等性能对优化设计变量的近似模型。
41.(2)在仿真平台中以随机方式生成20组优化设计变量的测试样本,测试样本与步骤s4中的训练样本的数据不能重复,利用该20组测试样本的计算结果验证近似模型的准确性,若差距较大则转回步骤s5-(1),从新调整近似模型构建方法,构建新的近似模型,直至近似模型准确。
42.s6. 基于改进遗传算法进行材料及结构的多目标、多工况优化设计。
43.具体包括如下步骤:(1)根据s4步骤筛选的20个部件的材料、尺寸、形状作为优化的设计变量,其中材料参数为非连续变化,变化范围仅为1、2、3、4,尺寸与形状参数为连续变化。
44.(2)选择一阶模态性能、碰撞总吸能、碰撞侵入量作为优化约束条件。
45.(3)选择质量、成本最小作为优化目标。
46.(4)基于isight提供的优化算法进行优化设计,寻求全局最优解。
47.isight提供的优化算法主要包括:amga、asa、downhillsimplex、evol、hooke-jeeves、lsgrg、misqp、mmfd、most、multi-island ga、multi-objective particle swarm、ncga、nlpql、nsga-ii、pointer、stress ratio等,本技术采用的优化算法是多目标遗传算法nsga-ii。
48.s7. 将优化设计的解分别带入相应的白车身仿真模型中进行优化结果的验证。
49.将优化设计的pareto解分别带入步骤s1中相应的白车身仿真模型中进行优化结果的验证,判断是否为最优解。若优化结果并非最优解,则转至步骤s6-(4),重新选择优化
算法,直至验证结果为最优解。
50.上述实施例只为说明本发明的技术构思及特点,其目的在于让熟悉此项技术的人士能够了解本发明的内容并加以实施,并不能以此限制本发明的保护范围,凡根据本发明精神实质所作的等效变化或修饰,都应涵盖在本发明的保护范围内。