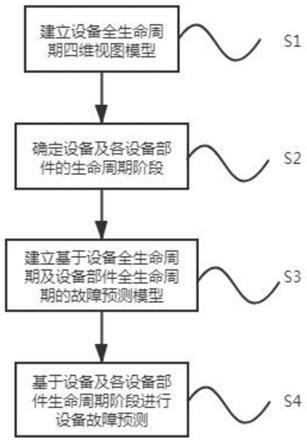
1.本发明涉及设备管理技术领域,尤其是涉及一种基于设备全生命周期模型的设备故障预测方法。
背景技术:2.大型设备结构复杂,同时在投入运行后有着有着运行连续性、精密性和自动化方面的要求,因此对设备的管理和维修提出了更高的要求。设备在全生命周期的不同阶段,故障的机理特征表现和故障的原因各不相同,同时设备部件在设备的全生命周期内存在维修、报废、替换等情况,设备部件有着自己独立是生命周期的同时对设备的全生命周期属性产生影响。因此对设备进行故障预测,不仅要考虑设备生命周期阶段的因素,还要考虑设备部件生命周期阶段的因素。
3.在中国专利文献中公开的“基于模型全生命周期管理的设备故障预警系统”,其公开号为cn109947088b,公开日期为2020-09-08,包括数据准备模块、实时故障预警模块、模型风险管理模块、模型自学习模块和模型库;数据准备模块读入外部实时数据并进行预处理,把处理好的外部实时数据传递至实时故障预警模块和模型风险管理模块进行分析;实时故障预警模块对故障风险进行预测,生成预警信息和维护建议;模型风险管理模块对模型结果可靠性进行评估;模型自学习模块读入积累的标注样本,对实时故障预警模块中的模型进行重新训练。本技术能够实现对设备的故障预警和模型全生命周期的在线监控,并且能够实现模型的动态更新,保证了模型结果的持续可靠性;并且同时引入了运行数据和运营数据,使得预警误差更小。但是该技术中并没有考虑到设备中的不同设备部件存在各自独立的生命周期,会使得实际的预测产生较大偏差或失效。
技术实现要素:4.本发明是为了克服现有技术中进行故障预测时没有考虑设备部件的生命周期因素从而导致实际预测偏差较大或失效的问题,提供了一种基于设备全生命周期模型的设备故障预测方法,对设备以及设备部件在其全生命周期的各个阶段进行故障预测,从而提高故障预测的准确性。
5.为了实现上述目的,本发明采用以下技术方案:
6.一种基于设备全生命周期模型的设备故障预测方法,包括:
7.s1、建立设备全生命周期四维视图模型;
8.s2、确定设备及各设备部件的生命周期阶段;
9.s3、建立基于设备全生命周期及设备部件全生命周期的故障预测模型;
10.s4、基于设备及各设备部件生命周期阶段进行设备故障预测。
11.本发明中首先建立设备全生命周期四维视图模型,四维分别是静态属性维、动态属性维、设备生命周期属性维、设备部件生命周期属性维,包含了设备及设备部件在各个阶段的所有数据。然后从被预测设备和设备部件的全生命周期模型中提取生命周期评价指标
数据,通过模糊综合评价模型确定设备和设备部件得生命周期阶段。从同品牌同型号设备的全生命周期模型中按设备生命周期阶段和设备部件生命周期阶段采集样本数据,建立和验证故障预测模型,归入故障预测模型库。再从故障预测模型库选择匹配故障预测模型进行故障预测。
12.所述四维视图模型包括:
13.静态属性维,包含设备的基础信息和技术属性;
14.动态属性维,包含设备的维修、保养和运行记录以及状态属性;
15.设备生命周期维,包含设备全生命周期的阶段属性;
16.设备部件生命周期维,包含了设备部件的全生命周期的阶段属性。
17.本发明中,静态属性维是指设备固有的基础信息和技术属性,基本不变或变动幅度微小;动态属性维是指设备运行的整个生命周期中不断变动的维修保养记录、运行记录和状态属性,随时间变化而不断变化;设备生命周期为和设备部件生命周期维包含了设备和设备部件的全生命周期的阶段属性,由于在设备的全生命周期阶段内,设备部件会存在完全更换的情况,设备部件的全生命周期阶段属性会随着部件的更换而刷新,从而影响设备的各项属性。
18.所述s2包括以下步骤:
19.s21、确定设备生命周期评价指标体系;
20.s22、层次分析法确定设备生命周期指标权重;
21.s23、模糊综合评价模型确定设备生命周期阶段。
22.本发明中设备生命周期评价指标体系包括设备生命周期评价等级集、设备生命周期划分因素集、等级评价表,用于对设备生命周期进行定量划分;利用一级指标判断矩阵和二级指标判断矩阵计算设备生命周期指标权重,并利用得到的权重确定设备生命周期阶段。对于设备部件的生命周期阶段的确定方法与设备生命周期阶段相同。
23.所述确定设备生命周期指标权重包括:
24.s221、确定一级指标判断矩阵c以及二级指标判断矩阵ck;
25.s222、计算一级指标判断矩阵c和二级指标判断矩阵ck的最大特征根值;
26.s223、计算一级指标判断矩阵c和二级指标判断矩阵ck的一致性比率cr;
27.s224、进行一致性验证,当cr小于设定值时进入下一步,否则返回s221;
28.s225、计算一级指标权重集a和二级指标权重集ai。
29.本发明中判断矩阵内的各项数值用来表示一个因素相对另一个因素的重要程度,通过计算得到的最大特征根值来推算出一致性指标,根据一致性指标与查表得到的随机一致性指标的比值得到一致性比率cr,并判断是否通过一致性验证。通过验证后计算一级指标权重集和二级指标权重集,一级指标权重集通过一级判断矩阵运算得到,二级指标权重集通过二级判断矩阵运算得到。对于设备部件生命周期指标权重的确定方法与设备生命周期指标权重相同。
30.所述确定设备生命周期阶段包括:
31.s231、建立因素评价矩阵;
32.s232、依次计算二级指标评价向量和一级指标评价向量;
33.s233、计算评价值并根据评价值确定设备生命周期阶段。
34.所述s2中设备部件生命周期阶段的确定方法与设备生命周期阶段的确定方法相同。
35.本发明中因素评价矩阵由等级评价表经过转换得到,运用模糊矩阵合成运算得到二级指标评价向量,在获得二级指标评价向量的基础上继续运用模糊矩阵合成运算得到一级指标评价向量,根据一级指标评价向量计算得到评价值,根据评价值在等级评价表中确定对应的设备生命周期阶段。对于设备部件生命周期阶段的确定方法与设备生命周期阶段相同。
36.所述故障预测模型的建立包括以下步骤:
37.s31、采集同品牌同型号设备的运行数据;
38.s32、筛选数据并处理形成时间样本序列;
39.s33、根据时间样本序列建立故障预测模型;
40.s34、验证故障预测模型,通过验证则加入故障预测模型库,不通过验证则返回s33。
41.本发明中根据选取的样本的数据类型建立对应的预测模型,根据需要进行预测的设备以及设备部件所处的生命周期阶段选取处于相同生命周期阶段以及同品牌同型号的设备采集数据来建立模型,从而排除而外因素的干扰,提高预测模型进行预测的准确性。
42.所述s4中设置有故障偏移度阈值和权重,通过故障预测模型对设备或设备部件进行故障预测,将得到的预测值与采集的实际值对比得到偏移度,以单个偏移度或多个偏移度加权后的值作为故障偏移度,当故障偏移度超过故障偏移度阈值时进行故障预警。
43.本发明中对设备进行预测时不仅考虑设备本身整体的生命周期阶段,同时还需要考虑设备中各个部件生命周期阶段对设备工作以及发生故障的影响。一个设备由若干个设备部件组合而成,每个设备部件进行预测时都有其对应的故障预测模型,从而会有多个偏移度结果,因此考虑偏移度的权重将多个偏移度综合成总的故障偏移度来对整个设备进行故障预测。
44.本发明具有如下有益效果:通过建立设备的全生命周期模型,在进行预测前先确定设备的生命周期阶段和机理特征值所在设备部件的生命周期阶段,基于两者采用匹配的故障预测模型进行预测,从而提高故障预测的准确度和适用性;对设备及设备部件的生命周期阶段进行定量划分,取代了人为经验对设备生命周期的划分和判断,更加科学准确。
附图说明
45.图1是本发明基于设备全生命周期模型的设备故障预测方法的流程图;
46.图2是本发明实施例中建立设备全生命周期四维视图模型的流程图;
47.图3是本发明实施例中确定设备生命周期阶段的整体流程图;
48.图4是本发明实施例中确定设备生命周期指标权重的流程图;
49.图5是本发明实施例中确定设备生命周期阶段的流程图;
50.图6是本发明实施例中确定各设备部件生命周期阶段的整体流程图;
51.图7为本发明实施例中建立故障预测模型库的流程图。
具体实施方式
52.下面结合附图与具体实施方式对本发明做进一步的描述。
53.如图1所示,一种基于设备全生命周期模型的设备故障预测方法,包括:
54.s1、建立设备全生命周期四维视图模型;
55.四维视图模型包括:静态属性维,包含设备的基础信息和技术属性;动态属性维,包含设备的维修、保养和运行记录以及状态属性;设备生命周期维,包含设备全生命周期的阶段属性;设备部件生命周期维,包含了设备部件的全生命周期的阶段属性。
56.s2、确定设备及各设备部件的生命周期阶段;
57.s21、确定设备生命周期评价指标体系;
58.s22、层次分析法确定设备生命周期指标权重;
59.确定设备生命周期指标权重包括:
60.s221、确定一级指标判断矩阵c以及二级指标判断矩阵ck;
61.s222、计算一级指标判断矩阵c和二级指标判断矩阵ck的最大特征根值;
62.s223、计算一级指标判断矩阵c和二级指标判断矩阵ck的一致性比率cr;
63.s224、进行一致性验证,当cr小于设定值时进入下一步,否则返回s221;
64.s225、计算一级指标权重集a和二级指标权重集ai;
65.s23、模糊综合评价模型确定设备生命周期阶段;
66.确定设备生命周期阶段包括:
67.s231、建立因素评价矩阵;
68.s232、依次计算二级指标评价向量和一级指标评价向量;
69.s233、计算评价值并根据评价值确定设备生命周期阶段;
70.s2中设备部件生命周期阶段的确定方法与设备生命周期阶段的确定方法相同。
71.s3、建立基于设备全生命周期及设备部件全生命周期的故障预测模型;
72.故障预测模型的建立包括以下步骤:
73.s31、采集同品牌同型号设备的运行数据;
74.s32、筛选数据并处理形成时间样本序列;
75.s33、根据时间样本序列建立故障预测模型;
76.s34、验证故障预测模型,通过验证则加入故障预测模型库,不通过验证则返回s33。
77.s4、基于设备及各设备部件生命周期阶段进行设备故障预测;
78.s4中设置有故障偏移度阈值和权重,通过故障预测模型对设备或设备部件进行故障预测,将得到的预测值与采集的实际值对比得到偏移度,以单个偏移度或多个偏移度加权后的值作为故障偏移度,当故障偏移度超过故障偏移度阈值时进行故障预警。
79.本发明中首先建立设备全生命周期四维视图模型,四维分别是静态属性维、动态属性维、设备生命周期属性维、设备部件生命周期属性维,包含了设备及设备部件在各个阶段的所有数据。然后从被预测设备和设备部件的全生命周期模型中提取生命周期评价指标数据,通过模糊综合评价模型确定设备和设备部件得生命周期阶段。从同品牌同型号设备的全生命周期模型中按设备生命周期阶段和设备部件生命周期阶段采集样本数据,建立和验证故障预测模型,归入故障预测模型库。再从故障预测模型库选择匹配故障预测模型进
行故障预测。
80.本发明中,静态属性维是指设备固有的基础信息和技术属性,基本不变或变动幅度微小;动态属性维是指设备运行的整个生命周期中不断变动的维修保养记录、运行记录和状态属性,随时间变化而不断变化;设备生命周期为和设备部件生命周期维包含了设备和设备部件的全生命周期的阶段属性,由于在设备的全生命周期阶段内,设备部件会存在完全更换的情况,设备部件的全生命周期阶段属性会随着部件的更换而刷新,从而影响设备的各项属性。
81.本发明中设备生命周期评价指标体系包括设备生命周期评价等级集、设备生命周期划分因素集、等级评价表,用于对设备生命周期进行定量划分;利用一级指标判断矩阵和二级指标判断矩阵计算设备生命周期指标权重,并利用得到的权重确定设备生命周期阶段。对于设备部件的生命周期阶段的确定方法与设备生命周期阶段相同。
82.本发明中判断矩阵内的各项数值用来表示一个因素相对另一个因素的重要程度,通过计算得到的最大特征根值来推算出一致性指标,根据一致性指标与查表得到的随机一致性指标的比值得到一致性比率cr,并判断是否通过一致性验证。通过验证后计算一级指标权重集和二级指标权重集,一级指标权重集通过一级判断矩阵运算得到,二级指标权重集通过二级判断矩阵运算得到。对于设备部件生命周期指标权重的确定方法与设备生命周期指标权重相同。
83.本发明中因素评价矩阵由等级评价表经过转换得到,运用模糊矩阵合成运算得到二级指标评价向量,在获得二级指标评价向量的基础上继续运用模糊矩阵合成运算得到一级指标评价向量,根据一级指标评价向量计算得到评价值,根据评价值在等级评价表中确定对应的设备生命周期阶段。对于设备部件生命周期阶段的确定方法与设备生命周期阶段相同。
84.本发明中根据选取的样本的数据类型建立对应的预测模型,根据需要进行预测的设备以及设备部件所处的生命周期阶段选取处于相同生命周期阶段以及同品牌同型号的设备采集数据来建立模型,从而排除而外因素的干扰,提高预测模型进行预测的准确性。
85.本发明中对设备进行预测时不仅考虑设备本身整体的生命周期阶段,同时还需要考虑设备中各个部件生命周期阶段对设备工作以及发生故障的影响。一个设备由若干个设备部件组合而成,每个设备部件进行预测时都有其对应的故障预测模型,从而会有多个偏移度结果,因此考虑偏移度的权重将多个偏移度综合成总的故障偏移度来对整个设备进行故障预测。
86.本发明实施例中的具体实施过程如下:
87.如图2所示,首先建立设备全生命周期四维视图模型;
88.s11、设备基础信息、技术属性转换为四维视图模型的静态属性维(d1);
89.s12、设备维修、保养和运行记录以及状态属性转换为四维视图模型的动态属性维(d2);
90.s13、设备的生命周期属性转换为四维视图模型的设备生命周期维(d3);
91.s14、设备部件的生命周期属性转换为四维视图模型的部件生命周期维(d4);
92.s15、建立设备全生命周期四维视图模型。
93.如图3所示,确定设备生命周期阶段,共分为三个大的步骤。
94.s21、综合专家意见确定设备生命周期评价指标体系。
95.s211、确定设备生命周期评价等级集为va=[磨合运行期,稳定运行期,衰退运行期];
[0096]
s212、确定设备生命周期划分因素集,其中u1,un,......um中的n值可以不同;
[0097]
u=[u1,u2,......,um]
[0098]
u1=[u
11
,u
12
,......,u
1n
]
[0099]
......
[0100]
um=[u
m1
,u
m2
,......,u
mn
]
[0101]
s213、确定设备与va和u的等级评价表,其中其中i∈[1,m],j∈[1,n],同时对va进行定量,以百分制对设备生命周期进行划分100-90为磨合运行期,90-30为稳定运行期,30-0为衰退运行期。
[0102][0103]
如图4所示,利用ahp层次分析法确定设备生命周期指标权重。
[0104]
s221、综合专家意见确定一级指标判断矩阵c以及二级指标判断矩阵ck;
[0105]
c=[c
ij
],其中数值c
ij
采用1-9标度法表示因素i相对于因素j的重要程度,c
ii
=1,一级判断矩阵针对设备的因素集u1到um,c
ij
表示因素集ui对于uj的重要程度,在这里i和j的范围都是1到m。如u2对比u3的重要程度是3则c
23
=3,u3对比u2的重要程度就是1/3则c
32
=1/3,u2对比u2因为是同一个因素集,所以就是1即c
22
=1。
[0106]ck
=[c
kij
],其中数值c
kij
采用1-9标度法表示因素i相对于因素j的重要程度,c
kii
=1,二级判断矩阵针对的是uk(1≤k≤m)因素集的因素,如u1的因素集的因素u
11
到u
1n
。ck的k取值与uk相同,如u1的二级判断矩阵就是c
1ij
,i和j的取值就是u1的因素个数,根据s21可知是i和j的范围都是1到n,如u1一共3个因素(n=3)u
11
,u
12
,u
13
,i和j的取值就是1到3。
[0107]
s222、计算一级指标判断矩阵和二级指标判断矩阵的最大特征根值λ
max
。
[0108]
下面以n阶一级判断矩阵c=[c
ij
]为例进行说明,首先计算判断矩阵行元素乘积
然后计算mi的n次方根进行归一化计算得到计算得到最大特征根近似值其中(cw)i表示向量cw的第i个分量。
[0109]
s223、计算一级指标判断矩阵和二级指标判断矩阵的一致性比率cr。
[0110]
利用最大特征根值计算一致性指标查询随机一致性指标ri
[0111]
n12345...ri000.580.901.12...
[0112]
计算得到一致性比率cr=ci/ri。
[0113]
s224、进行一致性验证,当cr小于0.1时一致性验证通过进入下一步,否则返回s221;
[0114]
s225、计算一级指标权重集a和二级指标权重集ai。
[0115]
一级指标权重集a=[a1,a2,
……
,am],其中ai=wi,即根据一级判断矩阵c计算得到的各个归一化的值且其中的m对应s21中的m个因素集。
[0116]
二级指标权重集ai=[a
i1
,a
i2
,
……
,a
in
],其中a
ij
=w
ij
,即根据二级判断矩阵ck计算得到的各个归一化的值且其中n对应s21中因素集ui中的因素个数n。
[0117]
如图5所示,通过模糊综合评价模型确定设备生命周期阶段。
[0118]
s231、建立因素评价矩阵,将等级评价表的u1,u2,......,um转换为r1,r2,......,rm,其中ri=[r
ij
]m×3。
[0119]
s232、计算二级指标评价向量,模糊矩阵合成运算获取评价向量,其中ai为二级指标权重集,得到二级指标评价向量bi=ai×ri
;
[0120]
利用二级指标评价向量计算一级指标评价向量,模糊矩阵合成运算获取评价向量,其中a为一级指标权重集,得到一级指标评价向量
[0121]
s233、计算评价值,向量乘积计算得出评价结果,其中95、60、15为等级评价表中各等级百分制评价值的中间值,根据评价结果即最终得到的评价值z查找等级评价表中对应的磨合运行期100-90,稳定运行期90-30,衰退运行期30-0来确定设备生命周期阶段。
[0122]
如图6所示,是确定各设备部件生命周期阶段的整体流程,包括:
[0123]
s21-1、综合专家意见确定设备部件生命周期评价指标体系;
[0124]
s22-1、ahp层次分析法确定设备部件生命周期指标权重;
[0125]
s23-1、模糊综合评价模型确定设备部件生命周期阶段;
[0126]
在本实施例中确定各设备部件生命周期阶段的方法流程与确定设备生命周期阶
段的方法流程相同。
[0127]
如图7所示,是建立及验证故障预测模型库的整体流程,以某设备某部件为例,该部件采用振动数据做为单元时间序列进行故障预测,设备及该部件均处于磨合运行期。由于部件摩擦面粗糙不平,承压状况不均,磨损速度快,振动数据在整个磨合期由高及低趋向稳定,因此采用arima(p,q,d)模型进行预测。
[0128]
具体步骤包括:
[0129]
s31、采集数据,提取同品牌同型号设备与该部件均处于磨合期的振动数据;
[0130]
s32、筛选处理数据形成样本时间序列x
t
;
[0131]
s33、根据时间样本序列建立故障预测模型,观测样本数据呈指数下降趋势,对时间序列取对数转化为线性趋势序列log(x
t
);对取对数后的时间序列进行循环差分处理,直到d次差分形成平稳序;对d次差分后的时间序列采用acf图和pacf图确定模型中的p,q值;存在多组参数时通过aic,bic准测筛选。
[0132]
s34、验证模型,进行arima模型残差值检验,检验未通过则返回s33重新调整模型,检验通过则加入故障预测模型库。
[0133]
完成故障预测模型库的建立后,开始对设备进行故障预测。首先综合专家意见确定设备及各设备部件机理特征值的故障偏移度阈值和权重;然后基于设备及各设备部件生命周期阶段选择各机理特征的故障预测模型;再从设备全生命周期四位视图模型中提取机理特征的数据,筛选处理形成时间序列;使用故障预测模型对对应的机理特征值进行预测;将预测得到的预测值与采集的实际值比对做差计算获得该机理特征值的偏移度;若只有单个偏移度则作为最终的故障偏移度,若有多个偏移度则在使用权重进行加权计算后得到的偏移度做为设备或各设备部件的故障偏移度;当故障偏移度超过故障偏移度阈值时进行故障预警提示。
[0134]
上述实施例是对本发明的进一步阐述和说明,以便于理解,并不是对本发明的任何限制,凡在本发明的精神和原则之内所作的任何修改、等同替换和改进等,均应包含在本发明的保护范围之内。