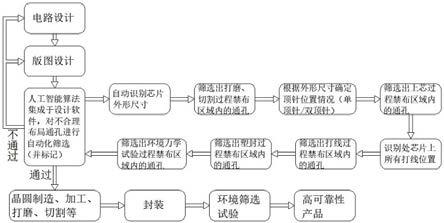
1.本发明属于砷化镓半导体芯片设计加工技术领域,具体地说,设计一种基于人工智能算法的封装芯片加工方法。
背景技术:2.砷化镓半导体具备高工作频率、电子迁移率、抗天然辐射及耗电量小等特性,在高频信号快速变化的情况下,砷化镓中的电子能及时跟随信号做出响应,用砷化镓作为衬底制作的芯片非常适合用于射频芯片领域。在砷化镓芯片电路设计及版图设计中,为了使芯片获得良好的接地性能及导热性能,会在芯片上设计一些金属通孔。
3.随着半导体技术的不断更新,砷化镓芯片朝着小型化,高集成度,低成本等方向发展,通孔在砷化镓芯片的作用也变得越来越重要,砷化镓芯片电路接地均是由通孔金属层与背部金属层导通实现,砷化镓芯片电路设计会使用通孔进行电路耦合或者隔离,甚至在通孔内进行功能电路设计(内部集成无源器件),当芯片热耗较大时,需要使用通孔金属层进行导热保证芯片散热性能,通孔成为砷化镓芯片不可缺失的组成部分。砷化镓晶圆制造时通常通过蚀刻等方式制作背部通孔再进行金属镀膜的方式实现加工。
4.砷化镓芯片结构通常比较薄(常规厚度75μm),且砷化镓材质力学强度远小于硅基材料。砷化镓半导体芯片从晶圆制造到成品芯片出货过程会经历一系列的复杂的力学条件。整个生产流程中主要包含晶圆减薄过程的打磨应力,晶圆切割的摩擦力,上芯过程顶针作用力,打线过程对焊盘作用力,塑封过程热应力,环境应力筛选等。经过对实际砷化镓芯片的设计制造过程总结及相关仿真研究分析得出砷化镓背孔的不合理分布会导致作用在芯片上的应力放大,最终产生裂片问题。
5.而目前行业背孔的设计中只考虑到实现芯片的电性能及导热性能,没有在设计阶段进行系统性考虑不合理的背孔布置所产生的裂片风险。现有砷化镓芯片设计时背孔的布置只是单层面的从电性能及导热性能方面进行考虑,没有在设计阶段进行背孔布置对芯片裂片风险的预判及筛选,导致实际生产过程中在不同的环节产生由于不合理的背孔布置位置应力集中出现裂片或者隐形裂纹缺陷。从而导致实际生产过程中成品率及产品可靠性降低。使企业生产成本增加,产品质量下降,设计生产周期加长。
技术实现要素:6.本发明针对现有技术的上述缺陷,提出了一种基于人工智能算法的封装芯片加工方法,通过对加工过程的区域进行划分,并对通孔进行调整,避免在加工通孔时容易出现芯片损坏的地方制造通孔,提高了芯片的抗应力性能,同时也提高了芯片的成品率。
7.本发明具体实现内容如下:本发明提出了一种基于人工智能算法的封装芯片加工方法,包括以下步骤:步骤1:进行电路设计;步骤2:根据电路设计进行对应的版图设计;
步骤3:筛选出版图设计内关于待加工芯片上在所有加工流程中需要加工的通孔;基于有限元分析和人工智能算法对版图设计进行分析,划分出关于通孔的禁部区域和非禁部区域;步骤4:判断版图设计中的通孔是否存在位于禁部区域内的情况;若判断为不存在,则认为版图设计的通孔布置合理;若判断为存在,则认为版图设计内位于禁部区域的通孔布置不合理,并对版图设计中布置不合理的通孔进行修改调整,然后再进行步骤3的步骤,直至通孔布置被判断为合理;对于版图设计中布置不合理的通孔无法进行修改的,重新进行步骤1的操作,直至通孔布置被判断为合理;步骤5:使用判断为通孔布置合理的版图设计对芯片进行加工、封装操作,得到生成的芯片产品。
8.为了更好地实现本发明,进一步地,所述步骤3的具体操作为:步骤3.1:识别待加工芯片的外形尺寸,得到完整的待加工区域数据;步骤3.2:根据提供的版图设计,筛选出每一步加工工艺流程中对应的通孔,汇总得到所有需要加工的通孔数据;步骤3.3:所述禁部区域分为两种,一种为加工过程禁部区域,还有一种为应力环境禁部区域;对于应力环境禁部区域,其设定过程为:首先,在每一步流程中,在没有设置通孔前,计算待加工芯片的待加工区域对应的最大应力值;其次,对待加工芯片的每一步工艺流程在设置通孔后都进行有限元分析,计算出在每一个加工流程的过程中,在待加工芯片的待加工区域上的应力值;最后,将设置通孔前的最大应力值与对应的设置通孔后的应力值进行比对,将应力值大于最大应力值的区域设定为禁部区域;对于加工过程禁部区域,其设定依据为:将整个加工工艺中,将在待加工芯片上进行打磨、切割操作的应力集中区域作为禁部区域,将在待加工芯片上进行上芯、打线、塑封操作时通孔导致应力放大的区域作为禁部区域。
9.为了更好地实现本发明,进一步地,所述步骤4中,对于判断版图设计中的通孔是否存在位于禁部区域内的情况的具体判断操作为:步骤4.1:在软件上建立待加工芯片的平面坐标系;步骤4.2:获取通孔在平面坐标系下的坐标位置;步骤4.3:获取每个禁部区域在平面坐标系下的坐标函数,汇总生成区域函数组;步骤4.4:依次计算判断每个通孔的坐标位置是否满足不落入到生成的区域函数组中;若有一个通孔的坐标位置满足区域函数组,则判断该通孔位于禁部区域内,反之则判断该通孔没有位于禁部区域内。
10.为了更好地实现本发明,进一步地,所述步骤3.3中,筛选加工过程禁部区域时,依次进行打磨、切割、上芯、打线、塑封操作的区域的筛选;且在进行了打磨和切割操作时的禁部区域的筛选后,需要确定加工使用的顶针类型及顶针与待加工芯片的接触点;在待加工
芯片的待加工区域上,以接触点为中心点,以一定距离为半径,将得到的圆形区域作为禁部区域。
11.为了更好地实现本发明,进一步地,所述顶针包括单端顶针和y字形双端顶针,根据实际加工需求选择不同类型的顶针;所述单端顶针与待加工芯片有一个接触点,所述y字形双端顶针与待加工芯片有两个接触点。
12.为了更好地实现本发明,进一步地,当待加工芯片的长宽比小于2.5:1且大于等于2:1时,选择y字形双端顶针;当待加工芯片的长宽比小于2:1且大于等于1:1时,选择单端顶针。
13.为了更好地实现本发明,进一步地,对于单端顶针,在所述步骤4中,需要将以下通孔判断为布置不合理的通孔:一:将在待加工芯片上位于顶针与待加工芯片的接触点处的通孔判断为布置不合理的通孔;二:存在两个通孔,两个通孔的连线在待加工芯片上穿过顶针与待加工芯片的接触点,则两个通孔判断为布置不合理的通孔。
14.为了更好地实现本发明,进一步地,对于y字形双端顶针,在所述步骤4中,还需要将以下通孔判断为布置不合理的通孔:一:将在待加工芯片上位于顶针与待加工芯片的接触点处的通孔判断为布置不合理的通孔;二:将在待加工芯片上,位于顶针与待加工芯片的两个接触点的连线上的通孔判断为布置不合理的通孔;三:存在两个通孔,两个通孔的连线在待加工芯片上穿过顶针与待加工芯片的一个以上的接触点,则两个通孔判断为布置不合理的通孔;四:以待加工芯片的几何中心为圆心,两个接触点以芯片竖向中轴线为对称轴互相,在以1/2顶针间距为半径且弧度为π/9的扇形对应的圆弧上出现的通孔判断为布置不合理的通孔。
15.为了更好地实现本发明,进一步地,在所述步骤3.3中,筛选加工过程禁部区域时,将待加工芯片的四角作为禁部区域。
16.为了更好地实现本发明,进一步地,所述待加工芯片的的四角的禁部区域为以芯片两边为腰的三角形区域。
17.本发明与现有技术相比具有以下优点及有益效果:本发明通过将识别通过的算法植入设计软件,对通孔设计是否合理实现自动化筛查,设计阶段排除导致裂片等缺陷的通孔布置,大大提高芯片设计成功率及可靠性,降低后期生产流程中由于不合理通孔设计导致的多次更新设计、多次流片的时间、设计及生产成本。通过该算法的运用可以提高产品成品率及用户端的可靠性表现、缩短产品出货周期。
附图说明
18.图1为目前现有技术的砷化镓封装芯片设计生产流程示意图;图2为本发明的完整流程示例图;图3为本发明算法生成禁部区域并判断通孔是否位于禁部区域的流程示意图;
图4为顶针上芯制程的操作示意图;图5为正方形的待加工芯片单端顶针上芯操作示意图;图6为长方形的待加工芯片单端顶针上芯操作示意图;图7为长方形的待加工芯片y字形双端顶针上芯操作示意图;图8为图5的情况下需要排除的一种通孔情形示例;图9为图5的情况下需要排除的一种通孔情形示例;图10为图6的情况下需要排除的一种通孔情形示例;图11为图6的情况下需要排除的一种通孔情形示例;图12为图7的情况下需要排除的一种通孔情形示例;图13为图7的情况下需要排除的一种通孔情形示例;图14为图7的情况下需要排除的一种通孔情形示例;图15为图7的情况下需要排除的一种通孔情形示例;图16为图7的情况下需要排除的一种通孔情形示例;图17为图7的情况下需要排除的一种通孔情形示例;图18为图7的情况下需要排除的一种通孔情形示例。
19.其中:1、吸嘴,2、晶粒背膜,3、顶针,4、顶针座,5、晶粒。
具体实施方式
20.为了更清楚地说明本发明实施例的技术方案,下面将结合本发明实施例中的附图,对本发明实施例中的技术方案进行清楚、完整地描述,应当理解,所描述的实施例仅仅是本发明的一部分实施例,而不是全部的实施例,因此不应被看作是对保护范围的限定。基于本发明中的实施例,本领域普通技术工作人员在没有做出创造性劳动前提下所获得的所有其他实施例,都属于本发明保护的范围。
21.在本发明的描述中,需要说明的是,除非另有明确的规定和限定,术语“设置”、“相连”、“连接”应做广义理解,例如,可以是固定连接,也可以是可拆卸连接,或一体地连接;可以是机械连接,也可以是电连接;也可以是直接相连,也可以是通过中间媒介间接相连,可以是两个元件内部的连通。对于本领域的普通技术人员而言,可以具体情况理解上述术语在本发明中的具体含义。
22.实施例1:本实施例提出了一种基于人工智能算法的封装芯片加工方法,如图2、图3所示,包括以下步骤:步骤1:进行电路设计;步骤2:根据电路设计进行对应的版图设计;步骤3:筛选出版图设计内关于待加工芯片上在所有加工流程中需要加工的通孔;基于有限元分析和人工智能算法对版图设计进行分析,划分出关于通孔的禁部区域和非禁部区域;步骤4:判断版图设计中的通孔是否存在位于禁部区域内的情况;若判断为不存在,则认为版图设计的通孔布置合理;若判断为存在,则认为版图设计内位于禁部区域的通孔布置不合理,并对版图设
计中布置不合理的通孔进行修改调整,然后再进行步骤3的步骤,直至通孔布置被判断为合理;对于版图设计中布置不合理的通孔无法进行修改的,重新进行步骤1的操作,直至通孔布置被判断为合理;步骤5:使用判断为通孔布置合理的版图设计对芯片进行加工、封装操作,得到生成的芯片产品。
23.步骤6:对生产的芯片产品进行环境应力筛选,筛选出符合要求的芯片作为工作原理:现有技术的流程如图1所示,其不能保证通孔尽可能低地对芯片造成影响,从而在各个流程中都存在较高的芯片报废风险。
24.而本技术主要通过以下步骤实现:1.对封装芯片生产过程中的打磨、切割、上芯、打线、塑封、环境应力筛选过程进行有限元分析,得出芯片通孔设计的禁布区域(条件作用时应力放大区域);2.将芯片通孔设置禁布区域与芯片外形尺寸关系按照一定算法植入设计软件中,实现禁布区域内通孔的筛选与标记;3.通过该人工智能算法的筛选标记对芯片通孔设计及版图进行针对性优化,避免禁布区域内出现通孔。
25.在上述技术方案中,封装芯片打磨、切割过程通孔的禁布区域通过有限元分析砷化镓材质晶圆在该过程中应力集中区域,并对相应区域设置通孔进行仿真分析,得出通孔导致应力放大区域即为禁布区域。
26.在上述技术方案中,上芯过程通孔的禁布区域需要先根据芯片外形尺寸确定上芯过程为单顶针还是双顶针从而判定顶针作用芯片位置,再通过有限元分析两种情况通孔导致应力放大区域即为该过程通孔禁布区域。
27.在上述技术方案中,打线过程通孔的禁布区域通过有限元分析打线作用位置附近区域内通孔布置导致应力放大的范围即为该过程通孔禁布区域。
28.在上述技术方案中,塑封过程通孔禁布区域需要通过有限元分析该过程热应力集中区域,并在区域内设置通孔进行仿真分析得出通孔导致应力放大区域即为该过程通孔禁布区域。
29.在上述技术方案中,环境应力筛选过程通孔禁布区域需要通过环境应力条件有限元分析得出应力集中区域,并在区域内设置通孔进行仿真分析得出通孔导致应力放大区域即为该过程通孔禁布区域。
30.在上述技术方案中,人工智能算法具体流程为识别设计软件坐标系或者重新建立坐标系,搜索出芯片边界位置,并搜索出芯片边界区域内通孔位置坐标(x,y),根据芯片外形尺寸识别出顶针作用位置(x1,y1,x2,y2……
)及打线作用位置(x
11
,y
11,
x
12
,y
12
……
)等,根据以上有限元分析结果通孔禁布区域生成禁布区域函数f(x,y)(如圆形区域为(x
‑ꢀ
x1)2+(y
‑ꢀ
y1)2<r或不等式函数组等),判断通孔位置坐标(x,y)是否满足禁布区域函数f(x,y),不满足说明通孔布置满足封装芯片可靠性设计算法执行结束,满足说明通孔布置不合理需要更改设计位置,则标记出不合理通孔及所有禁布区域,指导设计更新。
31.人工智能算法流程图如图3所示。
32.本发明的优点在于:通过人工智能算法植入相关设计软件,对电路设计及版图设
计中的通孔的不合理布置进行系统性筛选标记,反馈设计进一步设计优化避免后期生产过程由于通孔的不合理布置导致裂片及隐裂等缺陷问题。避免了之前在生产工程中发现缺陷再进行设计更改多次流片导致成品率降低,生产周期长,成本增加等问题。
33.设计方法流程如图2所示。
34.在上述技术方案中,砷化镓封装芯片制程过程中禁布区域的判定依据为通过对砷化镓芯片无通孔结构进行对应制程条件有限元分析,得出其应力分布云图及最大应力值,再通过在集中应力分布区域内不同位置布置通孔进行相同制程条件的有限元分析看设置了通孔的位置应力是否大于无通孔的状态时应力作用的最大应力值,如果有通孔位置应力大于无通孔状态时应力作用的最大应力(通孔对应力进行放大),则该位置不得布置通孔再通过多次仿真得到整个禁布区域(一般为以作用点为圆心的圆形区域内或者以离作用边一定距离的区域内,切割及打磨过程为砷化镓芯片加工过程故集中应力区域内均不得布置通孔)。
35.实施例2:本实施例在上述实施例1的基础上,为了更好地实现本发明,进一步地,如图2所示,所述步骤3的具体操作为:步骤3.1:识别待加工芯片的外形尺寸,得到完整的待加工区域数据;步骤3.2:根据提供的版图设计,筛选出每一步加工工艺流程中对应的通孔,汇总得到所有需要加工的通孔数据;步骤3.3:所述禁部区域分为两种,一种为加工过程禁部区域,还有一种为应力环境禁部区域;对于应力环境禁部区域,其设定过程为:首先,在每一步流程中,在没有设置通孔前,计算待加工芯片的待加工区域对应的最大应力值;其次,对待加工芯片的每一步工艺流程在设置通孔后都进行有限元分析,计算出在每一个加工流程的过程中,在待加工芯片的待加工区域上的应力值;最后,将设置通孔前的最大应力值与对应的设置通孔后的应力值进行比对,将应力值大于最大应力值的区域设定为禁部区域;对于加工过程禁部区域,其设定依据为:将整个加工工艺中,将在待加工芯片上进行打磨、切割操作的应力集中区域作为禁部区域,将在待加工芯片上进行上芯、打线、塑封操作时通孔导致应力放大的区域作为禁部区域。
36.所述步骤4中,对于判断版图设计中的通孔是否存在位于禁部区域内的情况的具体判断操作为:步骤4.1:在软件上建立待加工芯片的平面坐标系;步骤4.2:获取通孔在平面坐标系下的坐标位置;步骤4.3:获取每个禁部区域在平面坐标系下的坐标函数,汇总生成区域函数组;步骤4.4:依次计算判断每个通孔的坐标位置是否满足不落入到生成的区域函数组中;若有一个通孔的坐标位置满足区域函数组,则判断该通孔位于禁部区域内,反之则判断该通孔没有位于禁部区域内。
37.本实施例的其他部分与上述实施例1相同,故不再赘述。
38.实施例3:本实施例在上述实施例1-2任一项的基础上,为了更好地实现本发明,进一步地,所述步骤3.3中,筛选加工过程禁部区域时,依次进行打磨、切割、上芯、打线、塑封操作的区域的筛选;且在进行了打磨和切割操作时的禁部区域的筛选后,需要确定加工使用的顶针类型及顶针与待加工芯片的接触点;在待加工芯片的待加工区域上,以接触点为中心点,以一定距离为半径,将得到的圆形区域作为禁部区域。
39.本实施例的其他部分与上述实施例1-2任一项相同,故不再赘述。
40.实施例4:本实施例在上述实施例1-3任一项的基础上,为了更好地实现本发明,如图4、图5、图6、图7、图8、图9、图10、图11、图12、图13、图14、图15、图16、图17、图18所示,图中,叉号代表顶针的接触点,黑点代表通孔;进一步地,如图5、图6、图7所示,所述顶针包括单端顶针和y字形双端顶针,根据实际加工需求选择不同类型的顶针;所述单端顶针与待加工芯片有一个接触点,所述y字形双端顶针与待加工芯片有两个接触点。
41.为了更好地实现本发明,进一步地,如图7所示,当待加工芯片的长宽比小于2.5:1且大于等于2:1时,选择y字形双端顶针;如图5、图6所示,当待加工芯片的长宽比小于2:1且大于等于1:1时,选择单端顶针。
42.为了更好地实现本发明,进一步地,对于单端顶针,在所述步骤4中,需要将以下通孔判断为布置不合理的通孔:一:如图8、图10所示,将在待加工芯片上位于顶针与待加工芯片的接触点处的通孔判断为布置不合理的通孔;二:如图9、图11所示,存在两个通孔,两个通孔的连线在待加工芯片上穿过顶针与待加工芯片的接触点,则两个通孔判断为布置不合理的通孔。
43.为了更好地实现本发明,进一步地,对于y字形双端顶针,在所述步骤4中,还需要将以下通孔判断为布置不合理的通孔:一:如图12、图13、图14所示,将在待加工芯片上位于顶针与待加工芯片的接触点处的通孔判断为布置不合理的通孔;二:如图15所示,将在待加工芯片上,位于顶针与待加工芯片的两个接触点的连线上的通孔判断为布置不合理的通孔;三:如图16、图17所示,存在两个通孔,两个通孔的连线在待加工芯片上穿过顶针与待加工芯片的一个以上的接触点,则两个通孔判断为布置不合理的通孔;四:如图18所示,以待加工芯片的几何中心为圆心,两个接触点以芯片竖向中轴线为对称轴互相,在以1/2顶针间距为半径且弧度为π/9的扇形对应的圆弧上出现的通孔判断为布置不合理的通孔。
44.为了更好地实现本发明,进一步地,在所述步骤3.3中,筛选加工过程禁部区域时,将待加工芯片的四角作为禁部区域。
45.为了更好地实现本发明,进一步地,所述待加工芯片的的四角的禁部区域为以芯片两边为腰的三角形区域。
46.本实施例的其他部分与上述实施例1-3任一项相同,故不再赘述。
47.以上所述,仅是本发明的较佳实施例,并非对本发明做任何形式上的限制,凡是依
据本发明的技术实质对以上实施例所作的任何简单修改、等同变化,均落入本发明的保护范围之内。