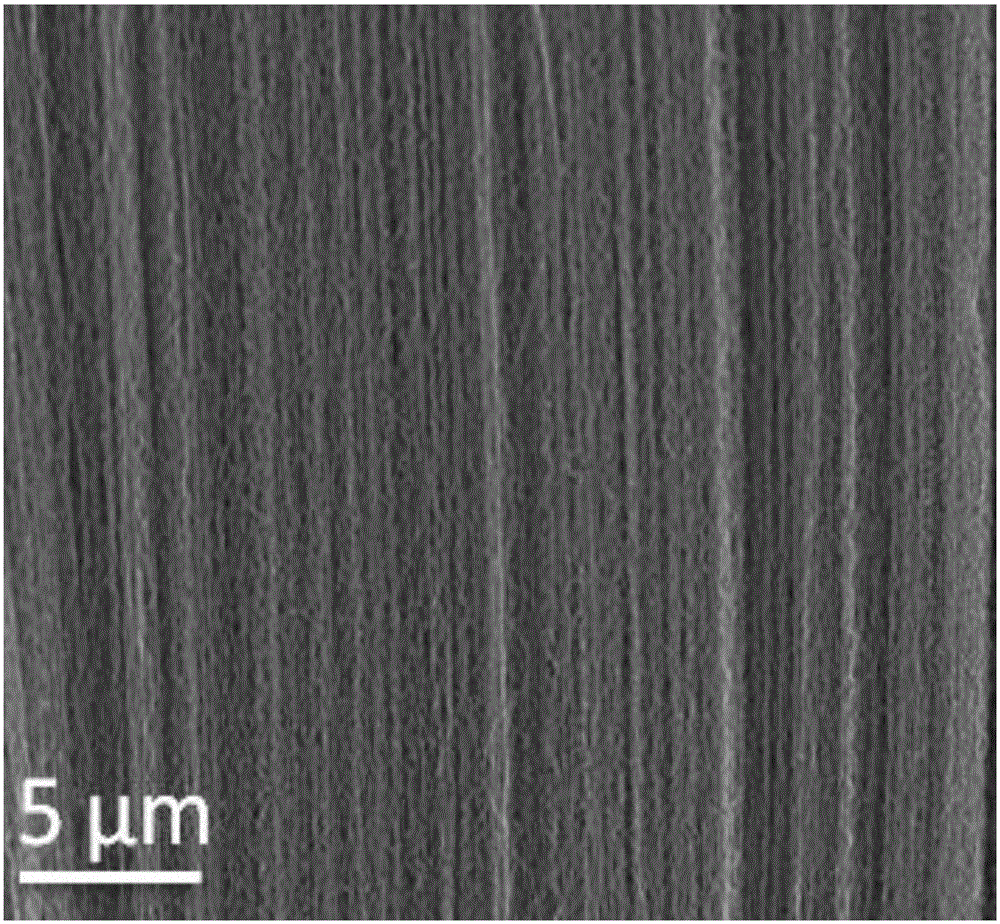
本发明属于纳米材料的制备与改性领域,更具体地,涉及一种超高纯度碳纳米管导电浆料及其制备方法,其能够避免催化剂中毒并提升催化剂的催化效率。
背景技术:
碳纳米管是近年来逐步开始尝试应用的一种新导电剂,相比之前常见的导电剂,如炭黑、乙炔黑、导电石墨等,它具有一些显著的优点。首先,碳纳米管具有很高的理论电子导电率,纯化后的碳纳米管室温下的电导率超过5×105S/m,而炭黑的电导率在103-104S/m之间。其次,碳纳米管具有巨大的长径比,一般在1000以上,较低的添加量即可达到类似于其他导电剂的渗流阈值,其一维的形态决定着它与电极活性材料采用的是“网与点”的接触模式,能与活性物质颗粒形成高导电性的三维网络式结构,显著降低电子传输阻抗,提高材料的电化学反应活性,再次,碳纳米管具有良好的导热性能,有利于电池充放电时的散热,此外,碳纳米管具有较好的强度和柔性,在电池运行或环境变化时,可以防止其破裂并缠绕在活性物质颗粒上,从而提高了电池的循环性能。
目前,用于导电浆料的碳纳米管主要采用流化床法制备。2011年,用流化床法生产出的碳纳米管产量就已经超过2千吨。但使用流化床法生长出来的碳纳米管一般含有较高比例的金属催化剂,会造成电池隔膜穿孔短路。通常采用的有酸洗处理和高温处理等方法去除这些金属催化剂颗粒,这些后续的步骤无疑增大了生产工艺的复杂程度并增加了碳纳米管导电浆料的成本。更为可惜的是这些处理会破坏碳纳米管的结构并降低其性能。
大规模生产碳纳米管的工艺开发中,除了要保证碳纳米管的纯度,又要同时提高生产效率,尽可能地降低成本,催化剂的活性必然是关注的焦点。但是,使用传统的固定床法制备碳纳米管时,催化剂活性、生长速率和生长时间三者往往不能同时兼顾。这是因为在固定床法中,碳氢化学物在催化剂的作用下形成碳纳米管的同时,会生成无定形的碳薄膜沉积于催化剂颗粒表面。无定形的杂质直接导致催化剂失去活性,也称催化剂中毒,致使碳纳米管的生长效率降低甚至停止。因此如何避免催化剂中毒并提升催化剂的催化效率也就同时成为固定床法实现大规模量产化的关键问题之一。
针对上述技术问题,目前还没有看到一套完整、有效、方便的固定床法制备碳纳米管的方法,如何解决上述技术难点,设计一套行而有效的制备方法,利用固定床催化剂自洁净化学气相沉积法来优化碳纳米管的制备工艺,同时优化其性能,是本发明要解决的问题。
技术实现要素:
针对现有技术的以上缺陷或改进需求,本发明提出了一种超高纯度碳纳米管导电浆料制备方法,其目的在于利用固定床催化剂自洁净化学气相沉积法来优化碳纳米管的制备工艺,同时优化其性能。
为实现上述目的,按照本发明的一个方面,提供了一种超高纯度碳纳米管导电浆料,包括纯度大于99.9%的阵列碳纳米管,所述阵列碳纳米管可控长度为100μm-2000μm,直径为5nm-10nm。
优选地,所述阵列碳纳米管的长度为100μm-500μm。
按照本发明的另一方面,提供了上述的超高纯度碳纳米管导电浆料的制备方法,其特征在于,其包括以下步骤:
(a)选取单面抛光的硅片,将硅片表面清洗干净并晾干,采用反应磁控溅射法,在硅片表面沉积一层氧化铝薄膜,所述氧化铝薄膜厚度为10nm-60nm,主要成分为三氧化二铝;
(b)采用直流磁控溅射法,在所述氧化铝薄膜表面沉积一层铁薄膜催化剂,所述铁薄膜催化剂厚度范围为1nm-3nm;
(c)采用水辅助超级生长法,将带有所述铁薄膜催化剂的硅片放入管式炉中退火,硅片表面的铁薄膜催化剂形成均匀的铁纳米颗粒,并在水分辅助下,催化乙烯在铁纳米颗粒表面生成100μm-500μm的阵列碳纳米管;
(d)将阵列碳纳米管从纳米颗粒表面剥离,得到阵列碳纳米管;
(e)在步骤(d)剥离得到的阵列碳纳米管中添加溶剂N-甲基吡咯烷酮(NMP)中,采用超声法和球磨法,使所述阵列碳纳米管分散于溶剂N-甲基吡咯烷酮(NMP)中,即获得所述超高纯度碳纳米管导电浆料。
进一步优选的,所述步骤(a)中反应磁控溅射法的温度为20℃-50℃,溅射功率为100W-300W,溅射气压为10sccm-30sccm,氩气与氧气比例为(5-20):1,反应时间为30s-360s。
优选的,所述氩气与氧气比例优选为(7-15):1,反应时间为60s-180s,从而生成的氧化铝薄膜厚度为10nm-30nm。
采用上述范围内的温度、溅射功率和溅射气压进行反应磁控溅射,能够保证溅射反应的顺利进行,同时氧化铝成分主要和氩气与氧气比相关,将氩气与氧气比例控制在一定的范围内,能够生成所需的三氧化二铝,而氧化铝薄膜厚度主要与反应时间相关,将反应时间进行控制,可以得到预期的薄膜厚度。
优选的,所述步骤(b)中直流磁控溅射法的温度为20℃-50℃,溅射功率为10W-200W,溅射气压为10sccm-20sccm,溅射反应时间为15-60s。
采用上述范围内的温度、溅射功率和溅射气压进行直流磁控溅射,能够保证直流溅射反应的顺利进行,得到铁薄膜,同时铁薄膜厚度主要与反应时间相关,将反应时间进行控制,可以得到预期的薄膜厚度。
优选的,所述步骤(c)中退火温度为650℃-800℃,退火时间为3min-15min。
将退火的温度和时间控制在合适的范围内,能够使铁薄膜顺利退火形成所需要的纳米颗粒状态,便于后续的碳纳米管生长。
优选的,所述步骤(c)中所述碳纳米管生长的过程中通入水、乙烯和氢气,其中通入水分的值为30ppm-400ppm,乙烯流量为50sccm-200sccm,氢气流量为0sccm-700sccm。
上述参数值范围能保证生成纯度符合要求的碳纳米管。在生长碳纳米管的过程中加入了水分,实现了催化剂的自清洁,催化效率大幅提高,在保证合成碳纳米管质量的前提下,提高了原料利用率并可获得高产量,便于大规模量产。
优选的,所述步骤(e)中超声时间为20min-60min,超声功率为200W-600W,球磨时间为2h-10h,球磨转速为100r/min-600r/min。
在上述参数下,将上述所得阵列碳纳米管分散于溶剂N-甲基吡咯烷酮(NMP)中,从而获得所需的超高纯度碳纳米管导电浆料。
按照本发明的另一方面,提供了一种超高纯度的碳纳米管导电浆料在锂电池中的应用。
总体而言,通过本发明所构思的以上技术方案与现有技术相比,由于利用固定床催化剂自洁净化学气相沉积法来优化碳纳米管的制备工艺,能够取得下列有益效果:
1.氧化铝/铁催化剂体系的选用实现了铁催化剂与基底材料的高附着力,保证了剥离后收集的碳纳米管具有超高纯度,完全可以达到实际应用的要求。解决了目前导电浆料中由于金属催化剂而导致的电池自放电现象,消除这一安全隐患。
2.改进后的固定床化学气相沉积法在生长碳纳米管的过程中加入了水分,实现了催化剂的自清洁,催化效率大幅提高,在保证合成碳纳米管质量的前提下,提高了原料利用率并可获得高产量,便于大规模量产。
3.采用自洁净化学气相沉积工艺可以进行多参数调节,通过调节这些工艺参数,可以控制所合成的碳纳米管的直径、壁数和长度等重要参数,便于实现碳纳米管导电浆料的性能最优化。
4.本发明的碳纳米管的制备方法制备出的碳纳米管纯度能够达到99.9%以上,且该制备方法简单易操作、利于大规模应用,十分适用于工业化生产碳纳米管。
附图说明
图1为本发明中高纯度碳纳米管的制备示意图;
图2为得到的碳纳米管的扫描电镜图;
图3为得到的碳纳米管浆料的透射电镜图;
图4为得到的碳纳米管的热重分析曲线;
图5为实施例1-5中制备碳纳米管的拉曼图谱;
图6为实施例1与实施例6用于锂电池后的电池倍率性能图;
图7为实施例1与对比例1用于锂电池后的电池倍率性能图;
在所有附图中,相同的附图标记用来表示相同的元件或结构,其中:
具体实施方式
为了使本发明的目的、技术方案及优点更加清楚明白,以下结合附图及实施例,对本发明进行进一步详细说明。应当理解,此处所描述的具体实施例仅仅用以解释本发明,并不用于限定本发明。此外,下面所描述的本发明各个实施方式中所涉及到的技术特征只要彼此之间未构成冲突就可以相互组合。
本发明的一个方面,提供了一种超高纯度碳纳米管导电浆料,包括纯度大于99.9%的阵列碳纳米管,所述阵列碳纳米管长度为100μm-2000μm,直径为5nm-10nm,该超高纯度碳纳米管导电浆料可应用于锂电池电极的制备中。
本发明的另一个方面,提供了一种上述超高纯度碳纳米管导电浆料的制备方法,其包括以下步骤:
(a)选取单面抛光的硅片,将硅片表面清洗干净并晾干,采用反应磁控溅射法,在硅片表面沉积一层氧化铝薄膜,所述氧化铝薄膜厚度为10nm-60nm,主要成分为三氧化二铝;
(b)采用直流磁控溅射法,在氧化铝薄膜表面沉积一层铁薄膜催化剂,所述铁薄膜催化剂厚度范围为1nm-3nm;
(c)采用水辅助超级生长法,将带有所述铁薄膜催化剂的硅片放入管式炉中退火,硅片表面的铁薄膜催化剂形成均匀的铁纳米颗粒,并在水分辅助下,催化乙烯在铁纳米颗粒表面生成100μm-500μm的阵列碳纳米管;
(d)将阵列碳纳米管从纳米颗粒表面剥离,得到阵列碳纳米管;
(e)在步骤(d)中剥离得到的阵列碳纳米管中添加溶剂N-甲基吡咯烷酮(NMP)中,采用超声法和球磨法,使所述阵列碳纳米管分散于溶剂N-甲基吡咯烷酮(NMP)中,即获得所述超高纯度碳纳米管导电浆料。
在本发明的一个具体实施例中,所述步骤(a)中反应磁控溅射法的温度为20℃-50℃,溅射功率为100W-300W,溅射气压为10sccm-30sccm,氩气与氧气比例为(5-20):1,反应时间为30s-360s。
在本发明的一个具体实施例中,优选的,所述氩气与氧气比例优选为(7-15):1,反应时间为60s-180s,从而生成的氧化铝薄膜厚度为10nm-30nm。
在本发明的一个具体实施例中,所述步骤(b)中直流磁控溅射法的温度为20℃-50℃,溅射功率为10W-200W,溅射气压为10sccm-20sccm,溅射反应时间为15-60s。
在本发明的一个具体实施例中,所述步骤(c)中退火温度为650℃-800℃,退火时间为3min-15min。
在本发明的一个具体实施例中,所述步骤(c)中所述碳纳米管生长的过程中通入水、乙烯和氢气,其中通入水分的值为30ppm-400ppm,乙烯流量为50sccm-200sccm,氢气流量为0sccm-700sccm。
在本发明的一个具体实施例中,所述步骤(e)中超声时间为20min-60min,超声功率为200W-600W,球磨时间为2h-10h,球磨转速为100r/min-600r/min。
本发明的另一方面提供了一种超高纯度的碳纳米管导电浆料在锂电池中的应用。
以下内容为实施例:
实施例1
(1)将单面抛光的硅片在丙酮中超声30min,去除表面有机物,再在乙醇中超声30min,去除表面颗粒,最后使用氮气吹干。在25℃下,设置200w的射频溅射功率,11sccm的溅射气压,氩气与氧气比10,反应180s,得到30nm厚的氧化铝薄膜。
(2)反应磁控溅射氧化铝后,在25℃下,设置20w的直流溅射功率,12sccm的溅射气压,反应15s,得到1nm厚的铁薄膜。
(3)在750℃的退火温度下,退火5min,将所述附有催化剂体系的硅片放入在管式炉,使铁膜退火形成均匀的纳米颗粒,在水分值150ppm,乙烯流量100sccm,氢气流量700sccm下,生长15min,在铁纳米颗粒表面生成100μm的阵列碳纳米管。
(4)使用机械剥离法将阵列碳纳米管从基底上剥离,。
(5)在超声时间为60min,超声功率为300W,球磨时间为4h,转速为400r/min下,添加分散剂聚乙烯吡咯烷酮(PVP),将上述所得阵列碳纳米管分散于溶剂N-甲基吡咯烷酮(NMP)中,即获得所述超高纯度碳纳米管导电浆料。
(6)按LiFePO4:VACNT:PVDF=88:2:10的比例将所述超高纯度碳纳米管导电浆料与LiFePO4混合后制备正极片,组装成2032型锂电池。
实施例2
以所述的相同步骤重复实施例1,区别在于,所述步骤(2)中的溅射时间为20s。
实施例3
以所述的相同步骤重复实施例1,区别在于,所述步骤(2)中的溅射时间为30s。
实施例4
以所述的相同步骤重复实施例1,区别在于,所述步骤(2)中的溅射时间为60s。
实施例5
以所述的相同步骤重复实施例1,区别在于,所述步骤(2)中的溅射时间为120s。
实施例6
(1)在25℃下,设置200w的射频溅射功率,11sccm的溅射气压,氩气与氧气比10,反应60s,在洗净的硅片上得到30nm厚的氧化铝薄膜。
(2)反应磁控溅射氧化铝后,在25℃下,设置20w的直流溅射功率,12sccm的溅射气压,反应15s,得到1nm厚的铁薄膜。
(3)在750℃的退火温度下,退火5min,将所述附有催化剂体系的硅片放入在管式炉,使铁膜退火形成均匀的纳米颗粒,在水分值150ppm,乙烯流量100sccm,氢气流量700sccm下,生长15min,在铁纳米颗粒表面生成100μm的阵列碳纳米管。
(4)使用机械剥离法将阵列碳纳米管从基底上剥离。
(5)在超声时间为60min,超声功率为300W,添加分散剂聚乙烯吡咯烷酮(PVP),将上述所得阵列碳纳米管分散于溶剂N-甲基吡咯烷酮(NMP)中,即获得所述超高纯度碳纳米管导电浆料,其中碳纳米管长度为500μm,直径为10nm。
(6)按LiFePO4:VACNT:PVDF=88:2:10的比例将所述超高纯度碳纳米管导电浆料与LiFePO4混合后制备正极片,组装成2032型锂电池。
实施例7
(1)将单面抛光的硅片在丙酮中超声30min,去除表面有机物,再在乙醇中超声30min,去除表面颗粒,最后使用氮气吹干。在20℃下,设置100w的射频溅射功率,10sccm的溅射气压,氩气与氧气比5,反应30s,得到10nm厚的氧化铝薄膜。
(2)反应磁控溅射氧化铝后,在20℃下,设置30w的直流溅射功率,10sccm的溅射气压,反应18s,得到2nm厚的铁薄膜。
(3)在650℃的退火温度下,退火3min,将所述附有催化剂体系的硅片放入在管式炉,使铁膜退火形成均匀的纳米颗粒,在水分值30ppm,乙烯流量50sccm,氢气流量0sccm下,生长5min,在铁纳米颗粒表面生成100μm的阵列碳纳米管。
(4)使用机械剥离法将阵列碳纳米管从基底上剥离。
(5)在超声时间为20min,超声功率为200W,球磨时间为2h,转速为100r/min下,添加分散剂聚乙烯吡咯烷酮(PVP),将上述所得阵列碳纳米管分散于溶剂N-甲基吡咯烷酮(NMP)中,即获得所述超高纯度碳纳米管导电浆料,其中碳纳米管长度为2000μm,直径为10nm。
(6)按LiFePO4:VACNT:PVDF=88:2:10的比例将所述超高纯度碳纳米管导电浆料与LiFePO4混合后制备正极片,组装成2032型锂电池。
实施例8
(1)将单面抛光的硅片在丙酮中超声30min,去除表面有机物,再在乙醇中超声30min,去除表面颗粒,最后使用氮气吹干。在50℃下,设置300w的射频溅射功率,30sccm的溅射气压,氩气与氧气比15,反应60s,得到30nm厚的氧化铝薄膜。
(2)反应磁控溅射氧化铝后,在50℃下,设置50w的直流溅射功率,200sccm的溅射气压,反应60s,得到3nm厚的铁薄膜。
(3)在800℃的退火温度下,退火15min,将所述附有催化剂体系的硅片放入在管式炉,使铁膜退火形成均匀的纳米颗粒,在水分值400ppm,乙烯流量200sccm,氢气流量700sccm下,生长15min,在铁纳米颗粒表面生成300μm的阵列碳纳米管。
(4)使用机械剥离法将阵列碳纳米管从基底上剥离。
(5)在超声时间为40min,超声功率为600W,球磨时间为10h,转速为600r/min下,添加分散剂聚乙烯吡咯烷酮(PVP),将上述所得阵列碳纳米管分散于溶剂N-甲基吡咯烷酮(NMP)中,即获得所述超高纯度碳纳米管导电浆料,其中碳纳米管长度为100μm,直径为5nm。
(6)按LiFePO4:VACNT:PVDF=88:2:10的比例将所述超高纯度碳纳米管导电浆料与LiFePO4混合后制备正极片,组装成2032型锂电池。
实施例9
(1)将单面抛光的硅片在丙酮中超声30min,去除表面有机物,再在乙醇中超声30min,去除表面颗粒,最后使用氮气吹干。在50℃下,设置200w的射频溅射功率,20sccm的溅射气压,氩气与氧气比20,反应360s,得到60nm厚的氧化铝薄膜。
(2)反应磁控溅射氧化铝后,在50℃下,设置10w的直流溅射功率,120sccm的溅射气压,反应200s,得到10nm厚的铁薄膜。
(3)在700℃的退火温度下,退火12min,将所述附有催化剂体系的硅片放入在管式炉,使铁膜退火形成均匀的纳米颗粒,在水分值300ppm,乙烯流量200sccm,氢气流量300sccm下,生长10min,在铁纳米颗粒表面生成300μm的阵列碳纳米管。
(4)使用机械剥离法将阵列碳纳米管从基底上剥离。
(5)在超声时间为40min,超声功率为400W,球磨时间为10h,转速为400r/min下,添加分散剂聚乙烯吡咯烷酮(PVP),将上述所得阵列碳纳米管分散于溶剂N-甲基吡咯烷酮(NMP)中,即获得所述超高纯度碳纳米管导电浆料,其中碳纳米管长度为500μm,直径为8nm。
(6)按LiFePO4:VACNT:PVDF=88:2:10的比例将所述超高纯度碳纳米管导电浆料与LiFePO4混合后制备正极片,组装成2032型锂电池。
实施例10
(1)将单面抛光的硅片在丙酮中超声30min,去除表面有机物,再在乙醇中超声30min,去除表面颗粒,最后使用氮气吹干。在20℃下,设置100w的射频溅射功率,20sccm的溅射气压,氩气与氧气比7,反应300s,得到20nm厚的氧化铝薄膜。
(2)反应磁控溅射氧化铝后,在20℃下,设置200w的直流溅射功率,120sccm的溅射气压,反应10s,得到1nm厚的铁薄膜。
(3)在700℃的退火温度下,退火3min,将所述附有催化剂体系的硅片放入在管式炉,使铁膜退火形成均匀的纳米颗粒,在水分值30ppm,乙烯流量200sccm,氢气流量100sccm下,生长15min,在铁纳米颗粒表面生成500μm的阵列碳纳米管。
(4)使用机械剥离法将阵列碳纳米管从基底上剥离。
(5)在超声时间为30min,超声功率为400W,球磨时间为10h,转速为400r/min下,添加分散剂聚乙烯吡咯烷酮(PVP),将上述所得阵列碳纳米管分散于溶剂N-甲基吡咯烷酮(NMP)中,即获得所述超高纯度碳纳米管导电浆料,其中碳纳米管长度为300μm,直径为8nm。
(6)按LiFePO4:VACNT:PVDF=88:2:10的比例将所述超高纯度碳纳米管导电浆料与LiFePO4混合后制备正极片,组装成2032型锂电池。
对比例1
按LiFePO4:CNT:PVDF=88:2:10的比例将市售碳纳米管导电浆料与LiFePO4混合后制备正极片,组装成2032型纽扣锂电池。
实验结果分析
实施例1中制备得到的碳纳米管扫描电镜图片如图2所示,可以看到碳纳米管排列有序,阵列度较高,浆料透射电镜如图3所示,热重曲线如图4所示,从图4可以看出所得碳纳米管在750℃后重量几乎为零,说明碳纳米管的纯度很高,在99.9%以上,从透射电镜图片也可以看出所得碳纳米管纯度较高,并未发现金属颗粒。
图5为实施例1-5中制备的碳纳米管的拉曼图谱,可以看到,当铁膜参数为20w 15s时得到的碳纳米管缺陷率较低。
图6为实施例1与实施例6中浆料用于锂电池后的倍率性能,可以看到实施例1得到的锂电池比容量较高,不同倍率下衰减较小,倍率性能更优,说明实施例1中浆料的分散性能优于实施例6,说明球磨与超声结合的混合分散法效果更优。
图7为实施例1与对比例1中浆料用于锂电池后的倍率性能,可以看到实施例1得到的锂电池比容量较高,大倍率下衰减较小,在10C的大倍率下仍能保持108mAh/g的比容量,而对比例1中市售浆料得到的锂电池比容量低于实施例1,大倍率下衰减较小快,在10C的大倍率下比容量几乎为零。
本领域的技术人员容易理解,以上所述仅为本发明的较佳实施例而已,并不用以限制本发明,凡在本发明的精神和原则之内所作的任何修改、等同替换和改进等,均应包含在本发明的保护范围之内。