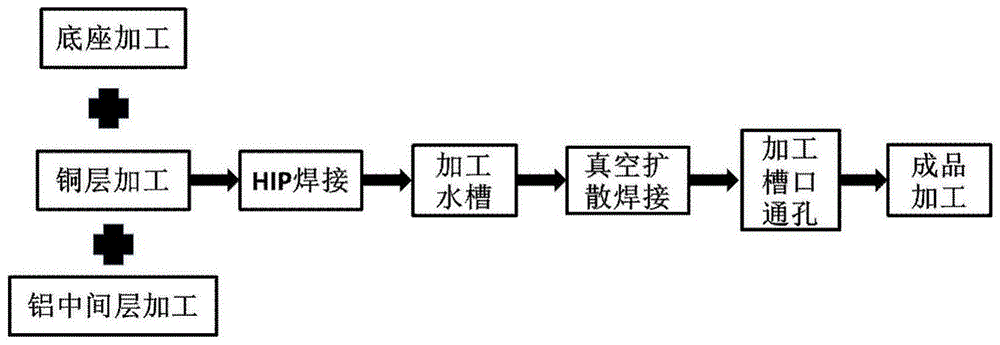
本发明涉及半导体设备
技术领域:
,尤其涉及一种复合型冷却水盘及其制作方法和用途。
背景技术:
:半导体芯片制造过程中,温度管控是一个非常重要的工作。温度不仅在晶圆的工艺生产过程中发挥重要影响,而且在相关制程工艺结束后,对晶圆上的器件性能影响仍然“发挥余热”。比如,刚从干刻腔室、气相沉积腔室或炉管腔室等高温制程腔室移出的晶圆,由于晶圆上各处分布的器件密度不同,使得晶圆表面各处的温度呈现出差异,如果不及时解决这种温度差异而让晶圆自然暴露在大气环境中,那晶圆表面就可能因热胀冷缩等原因导致器件性能下降甚至失效,而且还可能造成晶圆污染。因而晶圆从高温制程腔室移出之后,通常需要送到冷却室进行冷却。cn109817544a公开了一种半导体设备加热冷却复合盘装置,该装置通过减少晶圆在加热区和冷却区之间的传递路径来提高晶圆的处理和冷却效率,但该装置结构复杂,且冷却区的传热系数仍然较高。cn202205717u公开了一种晶圆冷却装置,该装置通过增设的气体喷吹元件向晶圆喷吹气体,不但避免了晶圆冷却之后表面残留水分,并且减少了晶圆冷却的时间,提高了晶圆冷却的效率,但气体喷吹的方法传热系数仍然较低,且能耗较高。cn208738190u公开了一种晶圆冷却室,通过采用多个传动装置分别将晶圆输送至冷却室内,从而避免晶圆之间散热不均的问题,但该装置的传热系数并没有提高。综上,目前人们并未想到通过改进冷却水盘的材质来提升冷却效率,这是因为目前制作冷却盘体的材料普遍为铝合金,若在半导体设备中冷却装置普遍采用铜,尽管铜的导热系数是铝的1.5倍,冷却能力会大幅度提高,但在半导体设备中,铜不能裸露在外,否则会出现铜离子泄漏,晶圆报废的现象。因此,需要开发一种高传热系数的冷却水盘及其制作方法,在解决冷却水盘传热系数低的问题的同时不出现铜离子泄露现象。技术实现要素:鉴于现有技术中存在的问题,本发明提供一种复合型冷却水盘,所述冷却水盘包括铝外壳和包裹在铝外壳内的铜层,其中,铜层可提升冷却水盘的传热系数,铝外壳可确保铜金属不会漏出,应用在半导体领域中,可保障芯片制作的稳定性;本发明还提供所述冷却水盘的制作方法,通过将未加工出的水槽的铜层与铝进行热等静压焊接后再加工出水槽,最后再与铝上层组合进行真空扩散焊接,得到冷却水盘,热等静压焊接可实现铜与铝的牢固焊接,而真空扩散焊可将铝上层与组件中的铝中间层焊接,且不会堵塞水槽,可得到冷却效率高的冷却水盘。为达此目的,本发明采用以下技术方案:第一方面,本发明提供一种复合型冷却水盘,所述冷却水盘包括铝外壳和包裹在铝外壳内的铜层。本发明提供的复合型冷却水盘通过设置铝外壳和包裹在铝外壳内的铜层,解决了现有冷却水盘传热系数低的问题,且铜完全被包裹在铝外壳中,可确保铜金属不会漏出,具有较高的工业应用价值。优选地,所述铝外壳包括铝上层、铝中间层和凹槽型铝底座;在所述凹槽型铝底座的凹槽部位从下向上依次设置铜层和所述铝中间层。优选地,所述铝中间层的上表面与凹槽型铝底座的凸出面齐平。优选地,所述铝中间层和铜层中设置有水槽。优选地,所述水槽的上端与铝中间层的上表面齐平。优选地,所述水槽的底部在铜层的下表面上0.5~1.5mm处,例如可以是0.5mm、0.6mm、0.7mm、0.8mm、0.9mm、1.0mm、1.1mm、1.2mm、1.3mm、1.4mm或1.5mm,优选在下表面上0.8~1.2mm处。优选地,所述水槽的深度为4.5~5.5mm,例如可以是4.5mm、4.6mm、4.7mm、4.8mm、4.9mm、5.0mm、5.2mm、5.3mm、5.4mm或5.5mm,优选为4.8~5.2mm。优选地,所述水槽的宽度为1.5~2.5mm,例如可以是1.5mm、1.6mm、1.7mm、1.8mm、1.9mm、2.0mm、2.1mm、2.2mm、2.3mm、2.4mm或2.5mm,优选为1.8~2.3mm。优选地,所述水槽之间的间隙宽度为1.4~1.6mm,例如可以是1.4mm、1.42mm、1.45mm、1.47mm、1.5mm、1.52mm、1.53mm、1.54mm、1.55mm、1.58mm或1.6mm。优选地,所述凹槽型铝底座的凹槽部位的厚度为0.5~1.5mm,例如可以是0.5mm、0.6mm、0.7mm、0.8mm、0.9mm、1.0mm、1.1mm、1.2mm、1.3mm、1.4mm或1.5mm,优选为0.8~1.2mm。优选地,所述冷却水盘设置有通孔或上端开口的槽口。优选地,所述通孔或上端开口的槽口在铜层的部位表面覆盖有铝层。本发明提供的复合型冷却水盘的通孔或上端开口的槽口经过铜层的部位表面覆盖有铝层,确保所有的铜均被铝包裹在里面,更有效地防止铜的泄露。优选地,所述铜层的厚度为4.5~5.5mm,例如可以是4.5mm、4.6mm、4.7mm、4.8mm、4.9mm、5.0mm、5.1mm、5.2mm、5.3mm、5.4mm或5.5mm,优选为4.8~5.2mm。优选地,所述铝中间层的厚度为0.5~1.5mm,例如可以是0.5mm、0.6mm、0.7mm、0.8mm、0.9mm、1.0mm、1.1mm、1.2mm、1.3mm、1.4mm或1.5mm,优选为0.8~1.2mm。优选地,所述铝上层的厚度为0.5~1.5mm,例如可以是0.5mm、0.6mm、0.7mm、0.8mm、0.9mm、1.0mm、1.1mm、1.2mm、1.3mm、1.4mm或1.5mm,优选为0.8~1.2mm。优选地,所述铝上层的材质为铝合金6061。优选地,所述铝中间层的材质为铝合金6061。优选地,所述凹槽型铝底座的材质为铝合金6061。优选地,所述铜层的材质为tu1无氧铜。本发明中tu1无氧铜是一种氧和杂质含量极低,纯度高,导电导热性极好的铜的材料,本发明优选采用该材料,可有效提高铜与铝的焊接效果以及冷却水盘的冷却效率。第二方面,本发明提供一种复合型冷却水盘的制作方法,所述方法包括如下步骤:(1)在凹槽型铝底座的凹槽部位从下向上依次设置铜层和铝中间层,得到装配好的组件,对所述装配好的组件进行热等静压焊接,得到焊接好的组件;(2)在所述焊接好的组件的铜层和铝中间层中加工出水槽,得到预工件;(3)将铝上层置于所述预工件靠近铝中间层的表面上,进行真空扩散焊接,得到冷却水盘;或所述方法包括如下步骤:(1)在铜层上表面、左表面、右表面和下表面分别覆盖铝中间层、第一铝块,第二铝块和铝底层,得到装配好的组件,对所述装配好的组件进行热等静压焊接,得到焊接好的组件;(2)在所述焊接好的组件的铜层和铝中间层中加工出水槽,得到预工件;(3)将铝上层置于所述预工件靠近铝中间层的表面上,进行真空扩散焊接,得到冷却水盘。本发明第一方面提供的复合型冷却水盘由于铝合金和铜两种材料间的扩散性能较差,且带有窄水槽结构的产品直接进行钎焊,水槽会出现堵塞;因此想要制得冷却效果好的冷却水盘,需要使铝合金和铜焊接效果好且同时不堵塞水槽。为此,本发明提供的方法通过先将铜层通过热等静压焊接在铝壳中得到焊接好的组件,再将组件加工出水槽后与铝上层组合经真空扩散焊接得到冷却水盘,既实现了将铜层完全包裹在铝外壳中,又不会堵塞水道,制作出的冷却水盘冷却效率高,具有较高的工业应用价值。优选地,在步骤(1)之前,还包括所述铜层的预加工。优选地,所述预加工包括在铜层上打出通孔。本发明预先在需要打通孔或开槽口的部位打出通孔,以免出现加工后再在冷却水盘上打通孔或开槽口铜层裸漏在外的问题。优选地,所述预加工包括在铜层表面进行物理气相沉积镀膜。本发明通过在铜层表面进行物理气相沉积镀膜可有效促进铜层与铝的热等静压焊接效果。优选地,所述镀膜的膜成分包括纯度为99.95%的钛。优选地,所述镀膜的膜厚度为8~10μm,例如可以是8μm、8.1μm、8.2μm、8.3μm、8.4μm、8.5μm、8.6μm、8.7μm、8.8μm、8.9μm、9.0μm、9.1μm、9.2μm、9.3μm、9.4μm、9.5μm、9.6μm、9.7μm、9.8μm或10μm,优选为8.5~9.5μm。优选地,所述铜层的材质为tu1无氧铜。优选地,所述预加工包括将铝销子打入通孔内。本发明预先在铜层的通孔处打入铝销子,后续对冷却水盘进行通孔和槽口加工时可直接在铝销子上开孔,从而实现铜层的完全包裹,避免了铜的泄露。优选地,所述铝销子与通孔的单边配合间隙为0.02~0.03mm,例如可以是0.02mm、0.021mm、0.022mm、0.023mm、0.024mm、0.025mm、0.026mm、0.027mm、0.028mm、0.029mm或0.03mm。本发明的铝销子与通孔的单边配合间隙为0.02~0.03mm,为焊接加热膨胀预留出一定的空间。优选地,在步骤(1)之前,所述铜层的预加工之后,还包括热等静压焊接预处理步骤。优选地,所述热等静压焊接预处理包括:清洗铜层、凹槽型铝底座和铝中间层。优选地,所述清洗液包括异丙醇和/或酒精。优选地,所述清洗包括超声波清洗。优选地,所述超声波清洗的时间为5~10min,例如可以是5min、5.5min、6min、6.5min、7min、7.5min、8min、8.5min、9min、9.5min或10min,优选为7~9min。优选地,所述热等静压焊接预处理包括:干燥铜层、凹槽型铝底座和铝中间层。优选地,所述干燥包括真空干燥。优选地,步骤(1)中对装配好的组件进行包套焊接。优选地,对所述包套焊接后的组件进行脱气处理。优选地,所述脱气的温度为300~400℃,例如可以是300℃、310℃、320℃、330℃、340℃、350℃、360℃、370℃、380℃、390℃或400℃,优选为320~380℃。优选地,所述脱气的时间为2~3h,例如可以是2h、2.1h、2.2h、2.3h、2.4h、2.5h、2.6h、2.7h、2.8h、2.9h或3.0h,优选为2.3~2.7h。优选地,对所述脱气后的组件进行热等静压焊接,得到焊接好的组件。本发明采用热等静压焊接的方法将铜层与铝焊接,较其他焊接方法而言,热等静压焊接方法能够使铜层与铝焊接达到技术要求且焊接效果好。优选地,所述热等静压焊接的温度为450~500℃,例如可以是450℃、455℃、460℃、465℃、470℃、475℃、480℃、485℃、490℃、495℃或500℃,优选为460~480℃。优选地,所述热等静压焊接的时间为3~5h,例如可以是3h、3.2h、3.4h、3.5h、3.7h、3.8h、4.0h、4.2h、4.4h、4.5h、4.8h或5.0h,优选为3.5~4.5h。优选地,所述热等静压焊接的压力为100~150mpa,例如可以是100mpa、105mpa、110mpa、115mpa、120mpa、125mpa、130mpa、135mpa、140mpa、145mpa或150mpa,优选为120~140mpa。优选地,步骤(2)中将所述焊接好的组件的铝中间层加工至0.5~1.5mm,例如可以是0.5mm、0.6mm、0.7mm、0.8mm、0.9mm、1.0mm、1.1mm、1.2mm、1.3mm、1.4mm或1.5mm,优选加工至0.8~1.2mm。本发明将铝中间层的厚度加工至0.5~1.5mm,为后续开水槽和加铝上层提供了基础,可有效保障冷却水盘的厚度,提高冷却效率。优选地,将所述焊接好的组件的铝中间层铣至0.5~1.5mm,例如可以是0.5mm、0.6mm、0.7mm、0.8mm、0.9mm、1.0mm、1.1mm、1.2mm、1.3mm、1.4mm或1.5mm,优选铣至0.8~1.2mm。优选地,在所述焊接好的组件的铜层和铝中间层中铣出水槽。优选地,所述水槽的上端开口与铝中间层的上表面齐平。优选地,所述水槽的底部在铜层的下表面上0.5~1.5mm处,例如可以是0.5mm、0.6mm、0.7mm、0.8mm、0.9mm、1.0mm、1.1mm、1.2mm、1.3mm、1.4mm或1.5mm,优选在下表面上0.8~1.2mm处。优选地,所述水槽的深度为4.5~5.5mm,例如可以是4.5mm、4.6mm、4.7mm、4.8mm、4.9mm、5.0mm、5.2mm、5.3mm、5.4mm或5.5mm,优选为4.8~5.2mm。优选地,所述水槽的宽度为1.5~2.5mm,例如可以是1.5mm、1.6mm、1.7mm、1.8mm、1.9mm、2.0mm、2.1mm、2.2mm、2.3mm、2.4mm或2.5mm,优选为1.8~2.3mm。优选地,所述水槽之间的间隙宽度为1.4~1.6mm,例如可以是1.4mm、1.42mm、1.45mm、1.47mm、1.5mm、1.52mm、1.53mm、1.54mm、1.55mm、1.58mm或1.6mm。优选地,在步骤(2)和步骤(3)之间,还包括真空扩散焊接预处理步骤。优选地,所述真空扩散焊接预处理包括:对所述铝中间层的上表面、凹槽型铝底座的凸出面和铝上层的表面进行抛光处理。优选地,所述抛光处理后铝中间层的上表面、凹槽型铝底座的凸出面和铝上层的表面的粗糙度为0.08~0.1μm,例如可以是0.08μm、0.082μm、0.084μm、0.085μm、0.088μm、0.09μm、0.092μm、0.094μm、0.095μm、0.098μm或0.1μm。本发明中真空扩散焊接前各表面的粗糙度控制为0.08~0.1μm,确保真空扩散焊接的效果。优选地,所述真空扩散焊接预处理包括:对所述铝中间层的上表面、凹槽型铝底座的凸出面和铝上层的表面进行清洗处理。优选地,所述清洗液包括氢氟酸溶液。优选地,所述氢氟酸溶液的质量浓度为10~15%,例如可以是10%、10.5%、11%、11.5%、12%、12.5%、13%、13.5%、14%、14.5%或15%,优选为12~14%。优选地,所述清洗的时间为15~30s,例如可以是15s、16s、17s、18s、19s、20s、21s、22s、23s、24s、25s、26s、27s、28s、29s或30s。优选地,所述真空扩散焊接预处理包括:对所述铝中间层的上表面、凹槽型铝底座的凸出面和铝上层的表面进行干燥处理。优选地,所述干燥为真空干燥。优选地,步骤(3)中,所述真空扩散焊接的装置为真空扩散炉。优选地,所述真空扩散焊接的温度为510~530℃,例如可以是510℃、512℃、513℃、515℃、516℃、518℃、520℃、522℃、525℃、526℃或530℃,优选为515~525℃。优选地,所述真空扩散焊接的时间为60~80min,例如可以是60min、62min、63min、64min、65min、66min、68min、70min、72min、75min、76min、78min或80min,优选为65~75min。优选地,所述真空扩散焊接的真空度≤3.0×10-3mpa,例如可以是3.0×10-3mpa、2.9×10-3mpa、2.8×10-3mpa、2.5×10-3mpa、2.0×10-3mpa、1.9×10-3mpa、1.8×10-3mpa或1.5×10-3mpa。优选地,所述真空扩散焊接中对预工件施加的压力为10~15mpa,例如可以是10mpa、10.5mpa、11mpa、11.5mpa、12mpa、12.5mpa、13mpa、13.5mpa、14mpa、14.5mpa或15mpa,优选为12~14mpa。本发明优选在真空扩散焊接中对预工件施加的压力控制为10~15mpa,在保障焊接效果,使铜层不泄露的同时,可有效防止出现水槽部分压塌的情况,保证冷却水的流通,提高了冷却水盘的冷却效率。作为本发明优选地技术方案,所述方法包括如下步骤:(1)在铜层上打出通孔后在铜层表面进行物理气相沉积镀膜,膜厚度为8~10μm,将铝销子打入通孔内,所述铝销子与通孔的单边配合间隙为0.02~0.03mm;(2)超声波清洗铜层、凹槽型铝底座和铝中间层5~10min,真空干燥,完成预处理;(3)在凹槽型铝底座的凹槽部位从下向上依次设置铜层和铝中间层,得到装配好的组件,对所述装配好的组件依次进行包套焊接、脱气处理和热等静压焊接,得到焊接好的组件;所述脱气的温度为300~400℃,时间为2~3h,所述热等静压焊接的温度为450~500℃,时间为3~5h,压力为100~150mpa;(4)将所述焊接好的组件的铝中间层铣至0.5~1.5mm,在所述焊接好的组件的铜层和铝中间层中铣出深度为4.5~5.5mm,宽度为1.5~2.5mm的水槽,得到预工件;(5)对所述铝中间层的上表面、凹槽型铝底座的凸出面和铝上层的表面进行抛光处理、清洗处理和真空干燥处理;其中,所述抛光处理后铝中间层的上表面、凹槽型铝底座的凸出面和铝上层的表面的粗糙度为0.08~0.1μm,所述清洗处理的时间为15~30s;(6)将铝上层置于所述预工件靠近铝中间层的表面上,在真空扩散炉中,510~530℃,真空度≤3.0×10-3mpa的环境下进行真空扩散焊接,得到冷却水盘,其中,所述真空扩散焊接的时间为60~80min,对预工件施加的压力为10~15mpa。本发明的冷却水盘经真空扩散焊接后还包括冷却水盘槽口和通孔的加工以及成品的加工步骤,可采用本领域技术人员熟知任何可用于槽口和通孔加工的操作,在此不做赘述。第三方面,本发明提供第一方面所述的复合型冷却水盘在半导体领域中的用途。本发明第一方面提供的复合型冷却水盘,不仅传热系数高,提高了冷却效率,而且铜完全被包裹在铝外壳中,可确保铜金属不会漏出,应用在半导体领域中,可保障芯片制作的稳定性。与现有技术相比,本发明至少具有以下有益效果:(1)本发明提供的复合型冷却水盘采用了铜层,冷却效率高,其中,将晶圆从100℃冷却至25℃的时间均≤35s,可防止晶圆局部过热出现内部缺陷,保障芯片制作过程的稳定性;(2)本发明提供的复合型冷却水盘的制作方法,可有效实现对铜层的全部包裹,采用热等静压焊接铜与铝的焊接效果好,铜完全被包裹在铝外壳中,可确保铜金属不会漏出;(3)本发明提供的复合型冷却水盘的制作方法,可制作出的冷却效率高的冷却水盘,制作过程不会堵塞水槽,具有较好的工业应用前景。附图说明图1是本发明提供的复合型冷却水盘的制作方法的工艺流程图。图2是本发明实施例1提供的复合型冷却水盘的局部示意图。图3是本发明实施例1提供的复合型冷却水盘的制作方法中组件的示意图。图4是本发明实施例1提供的复合型冷却水盘的制作方法中预工件的示意图。图5是本发明实施例1提供的复合型冷却水盘的制作方法中预工件与铝上层装配的示意图。图中:1-铝外壳;101-铝上层;102-铝中层;1021-铝中层的上表面;103-凹槽型铝底座;1031-凹槽型铝底座的凸出面;1032-凹槽型铝底座的凹槽部位;2-铜层;201-铜层的下表面;3-水槽;4-槽口;5-通孔。具体实施方式下面结合附图并通过具体实施方式来进一步说明本发明的技术方案。下面对本发明进一步详细说明。但下述的实例仅仅是本发明的简易例子,并不代表或限制本发明的权利保护范围,本发明的保护范围以权利要求书为准。本发明提供的复合型冷却水盘的制作流程如图1所示,包括如下步骤:(1)分别对底座、铜层和铝中间层按照图纸进行加工,其中铜层的加工步骤还包括在铜层上打通孔以及镀膜;(2)将底座、铜层和铝中间层装配好后进行热等静压焊接,得到焊接好的组件;(3)在焊接好的组件上加工出水槽,得到预工件;(4)将预工件与铝上层装配好进行真空扩散焊接,得到冷却水盘粗品;(5)在冷却水盘粗品上加工出槽口和通孔,并进行进一步的成品加工,得到冷却水盘成品。一、实施例实施例1本实施例提供一种复合型冷却水盘,如图2所示,所述冷却水盘包括铝外壳1和包裹在铝外壳1内的铜层2;所述铝外壳包括铝上层101、铝中间层102和凹槽型铝底座103;在所述凹槽型铝底座103的凹槽部位从下向上依次设置铜层2和所述铝中间层102,铝中间层102的上表面1021与凹槽型铝底座103的凸出面1031齐平,所述凹槽型铝底座103的凹槽部位1032的厚度为1mm,铝上层101的厚度为1mm,铜层2的厚度为5mm,铝中间层102的厚度为1mm,铝上层101、铝中间层102和凹槽型铝底座103的材质为铝合金6061,铜层2的材质为tu1无氧铜;所述铝中间层102和铜层2中设置有水槽3,水槽3的上端与铝中间层102的上表面齐平,水槽3的底部在铜层2的下表面201上1.0mm处,水槽3的深度为5mm,宽度为2mm,水槽3之间的间隙宽度为1.6mm;所述冷却水盘还设置有通孔5或上端开口的槽口4,通孔5或上端开口的槽口4在铜层2的部位表面覆盖有铝层。本实施例提供的复合型冷却水盘的制作方法包括如下步骤:(1)在铜层2上打出通孔后在铜层2表面进行物理气相沉积镀膜,膜厚度为8μm,膜成分为纯度为99.95%的钛,将铝销子打入通孔内,所述铝销子与通孔的单边配合间隙为0.02mm;(2)超声波清洗铜层2、凹槽型铝底座103和铝中间层102,时间为5min,真空干燥,完成预处理;(3)如图3所示,在凹槽型铝底座103的凹槽部位从下向上依次设置铜层2和铝中间层102,得到装配好的组件,对所述装配好的组件依次进行包套焊接、脱气处理和热等静压焊接,得到焊接好的组件;所述脱气的温度为300℃,时间为3h,所述热等静压焊接的温度为450℃,时间为5h,压力为150mpa;(4)如图4所示,将所述焊接好的组件的铝中间层102铣至1mm,在所述焊接好的组件的铜层2和铝中间层102中铣出深度为5mm,宽度为2mm的水槽3,得到预工件;(5)对所述铝中间层102的上表面、凹槽型铝底座103的凸出面和铝上层102的表面进行抛光处理、清洗处理和真空干燥处理;其中,所述抛光处理后铝中间层102的上表面、凹槽型铝底座103的凸出面和铝上层101的表面的粗糙度为0.08μm,所述清洗处理的时间为30s;(6)如图5所示,将铝上层101置于所述预工件靠近铝中间层102的表面上,真空扩散炉中,在530℃,真空度3.0×10-3mpa的环境下进行真空扩散焊接,得到冷却水盘粗品,其中,所述真空扩散焊接的时间为80min,对预工件施加的压力为10mpa;(7)在冷却水盘粗品上加工出槽口和通孔,并进行进一步的成品加工,得到冷却水盘成品。实施例2本实施例提供一种复合型冷却水盘,所述冷却水盘包括铝外壳和包裹在铝外壳内的铜层;所述铝外壳包括铝上层、铝中间层和凹槽型铝底座;在所述凹槽型铝底座的凹槽部位从下向上依次设置铜层和所述铝中间层,铝中间层的上表面与凹槽型铝底座的凸出面齐平,所述凹槽型铝底座的凹槽部位的厚度为1.5mm,铝上层的厚度为1.5mm,铜层的厚度为4.5mm,铝中间层的厚度为0.5mm,铝上层、铝中间层和凹槽型铝底座的材质为铝合金6063,铜层的材质为tu2无氧铜;所述铝中间层和铜层中设置有水槽,水槽的上端与铝中间层的上表面齐平,水槽的底部在铜层的下表面上0.5mm处,水槽的深度为4.5mm;宽度为2.5mm,水槽之间的间隙宽度为1.4mm;所述冷却水盘还设置有通孔或上端开口的槽口,通孔或上端开口的槽口在铜层的部位表面覆盖有铝层。本实施例提供的复合型冷却水盘的制作方法包括如下步骤:(1)在铜层上打出通孔后在铜层表面进行物理气相沉积镀膜,膜厚度为10μm,膜成分为纯度为99.95%的钛,将铝销子打入通孔内,所述铝销子与通孔的单边配合间隙为0.03mm;(2)超声波清洗铜层、凹槽型铝底座和铝中间层10min,真空干燥,完成预处理;(3)在凹槽型铝底座的凹槽部位从下向上依次设置铜层和铝中间层,得到装配好的组件,对所述装配好的组件依次进行包套焊接、脱气处理和热等静压焊接,得到焊接好的组件;所述脱气的温度为400℃,时间为2h,所述热等静压焊接的温度为500℃,时间为3h,压力为100mpa;(4)将所述焊接好的组件的铝中间层铣至1.5mm,在所述焊接好的组件的铜层和铝中间层中铣出深度为4.5mm,宽度为2.5mm的水槽,得到预工件;(5)对所述铝中间层的上表面、凹槽型铝底座的凸出面和铝上层的表面进行抛光处理、清洗处理和真空干燥处理;其中,所述抛光处理后铝中间层的上表面、凹槽型铝底座的凸出面和铝上层的表面的粗糙度为0.1μm,所述清洗处理的时间为15s;(6)将铝上层置于所述预工件靠近铝中间层的表面上,在真空扩散炉中,510℃,真空度2.0×10-3mpa的环境下进行真空扩散焊接,得到冷却水盘,其中,所述真空扩散焊接的时间为60min,对预工件施加的压力为15mpa;(7)在冷却水盘粗品上加工出槽口和通孔,并进行进一步的成品加工,得到冷却水盘成品。实施例3本实施例提供一种复合型冷却水盘,所述冷却水盘结构与实施例1相同,其制作方法包括如下步骤:(1)在铜层上打出通孔后在铜层表面进行物理气相沉积镀膜,膜厚度为9μm,膜成分为纯度为99.95%的钛,将铝销子打入通孔内,所述铝销子与通孔的单边配合间隙为0.025mm;(2)超声波清洗铜层、凹槽型铝底座和铝中间层,时间为8min,真空干燥,完成预处理;(3)在凹槽型铝底座的凹槽部位从下向上依次设置铜层和铝中间层,得到装配好的组件,对所述装配好的组件依次进行包套焊接、脱气处理和热等静压焊接,得到焊接好的组件;所述脱气的温度为350℃,时间为2.5h,所述热等静压焊接的温度为470℃,时间为4h,压力为130mpa;(4)将所述焊接好的组件的铝中间层铣至1mm,在所述焊接好的组件的铜层和铝中间层中铣出深度为5mm,宽度为2mm的水槽,得到预工件;(5)对所述铝中间层的上表面、凹槽型铝底座的凸出面和铝上层的表面进行抛光处理、清洗处理和真空干燥处理;其中,所述抛光处理后铝中间层的上表面、凹槽型铝底座的凸出面和铝上层的表面的粗糙度为0.09μm,所述清洗处理的时间为20s;(6)将铝上层置于所述预工件靠近铝中间层的表面上,真空扩散炉中,在520℃,真空度1.5×10-3mpa的环境下进行真空扩散焊接,得到冷却水盘粗品,其中,所述真空扩散焊接的时间为70min,对预工件施加的压力为12mpa;(7)在冷却水盘粗品上加工出槽口和通孔,并进行进一步的成品加工,得到冷却水盘成品。实施例4本实施例提供一种复合型冷却水盘,所述冷却水盘结构与实施例1相同,其制作方法除将步骤(6)中“对预工件施加的压力为10mpa”替换为“对预工件施加的压力为20mpa”外,其余均与实施例1相同。二、对比例对比例1本对比例提供一种纯铝型冷却水盘,所述冷却水盘除将铜层替换为铝层外,其余均与实施例1相同。本对比例提供的纯铝型冷却水盘的制作方法除将铜层替换为铝层外,其制作流程和工艺参数均与实施例1相同。三、测试及结果对实施例1~4和对比例1提供的冷却水盘进行降温时间的测试,将晶圆放在水盘上面,观察晶圆温度从100℃冷却到25℃所需要的时间,并检测实施例1~4的铜泄露情况,具体情况如表1所示。表1样品冷却时间(s)铜泄露情况实施例130无泄漏实施例235无泄漏实施例334无泄漏实施例435无泄漏对比例140/从表1可以看出以下几点:(1)综合实施例1~4可知,本发明提供的冷却水盘冷却效果好,对晶圆的冷却时间短,将晶圆从100℃冷却至25℃的时间均≤35s,可有效防止晶圆局部过热,造成内部缺陷的现象,且铜层很好地包裹在铜层中,未检测到铜泄露的情况,具有较好地应用前景;(2)综合实施例1与对比例1可知,实施例1通过在铝壳中包裹铜层,较对比例1采用相同的制作方法在铝壳中包裹铝层而言,实施例1提供的冷却水盘将晶圆从100℃冷却至25℃的时间仅为30s,而对比例1提供的冷却水盘将晶圆从100℃冷却至25℃的时间为40s,较实施例1的时间长了10s,占实施例1冷却总时间的33.33%,由此说明,本发明通过在冷却水盘的铝壳中包裹铜层,使冷却水盘传热系数高,缩短了晶圆冷却的时间,提高了冷却效率,可有效防止晶圆局部过热出现内部缺陷的情况;(3)综合实施例1与实施例4可知,实施例1提供的冷却水盘的制作方法通过将对预工件施加的压力控制为10mpa,较实施例4中对预工件施加的压力为20mpa而言,实施例1提供的冷却水盘将晶圆从100℃冷却至25℃的时间仅为30s,而实施例4提供的冷却水盘将晶圆从100℃冷却至25℃的时间为35s,由此说明,本发明通过将真空扩散焊中对预工件施加的压力控制在一定范围,不仅能够保障焊接效果,使铜层不泄露,而且可有效防止出现水槽部分压塌的情况,保证冷却水的流通,提高了冷却水盘的冷却效率,缩短了晶圆冷却时间。综上,本发明提供的复合型冷却水盘通过设置铝外壳和包裹在铝外壳内的铜层,提高了冷却水盘的冷却效率,其中,将晶圆从100℃冷却至25℃的时间均≤35s;同时本发明提供的冷却水盘的制作方法可保障铜完全被包裹在铝外壳中,确保铜金属不会漏出,应用在半导体领域中,可保障芯片制作的稳定性,具有较高的工业应用价值。申请人声明,本发明通过上述实施例来说明本发明的详细结构特征,但本发明并不局限于上述详细结构特征,即不意味着本发明必须依赖上述详细结构特征才能实施。所属
技术领域:
的技术人员应该明了,对本发明的任何改进,对本发明所选用部件的等效替换以及辅助部件的增加、具体方式的选择等,均落在本发明的保护范围和公开范围之内。当前第1页1 2 3