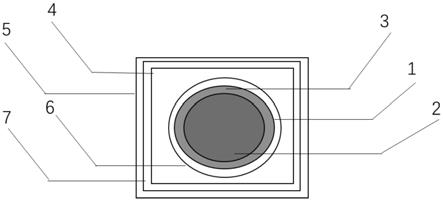
1.本发明涉及一种提高作业效率及产出率的芯片翻膜方法,属于led制程的后道作业技术领域。
背景技术:2.led作为21世纪的照明新光源,同样亮度下,半导体灯耗电仅为普通白炽灯的l/10,而寿命却可以延长100倍。led器件是冷光源,光效高,工作电压低,耗电量小,体积小,可平面封装,易于开发轻薄型产品,结构坚固且寿命很长,光源本身不含汞、铅等有害物质,无红外和紫外污染,不会在生产和使用中产生对外界的污染。因此,半导体灯具有节能、环保、寿命长等特点,如同晶体管替代电子管一样,半导体灯替代传统的白炽灯和荧光灯,也将是大势所趋。无论从节约电能、降低温室气体排放的角度,还是从减少环境污染的角度,led作为新型照明光源都具有替代传统照明光源的极大潜力。led芯片发光效率高,颜色范围广,使用寿命长,已被广泛应用于大屏显示、景观照明、交通信号灯、汽车状态显示等各个领域。
3.在led芯片制备工艺中,芯片经过制程中最后的切割作业,由芯片变成一颗颗独立的管芯粘附在蓝膜上,然后经过最后一道人工的检验、倒膜、画片分档、翻膜后变成最后的成品入库。因此,在切割后芯片还需要进一步经过人工的p面(电极面)检验,翻p面粘膜、n面(无电极面)检验,翻n面粘膜,画片参数分档,边缘不良品去除(外观不良或参数不良),翻成品膜,入库等作业,才能变成最终的入库产品。在实际的人工倒膜作业过程中,因为是纯人工的手动作业,来回的翻膜大小、边缘的异常管芯去除等需要人为控制,经常性出现翻膜大小不一致或翻去异常管芯时翻去的面积大等造成的产品损失,再加上来回人工作业的繁琐性,作业效率也比较低。
技术实现要素:4.针对现有作业流程(p面检验-翻p面粘膜-n面检验-翻n面粘膜-画片参数分档-翻成品膜(包含吸出不良品)-入库)存在的不足,本发明提供了一种提高作业效率及产出率的芯片翻膜方法。
5.本发明的技术方案为:
6.一种提高作业效率及产出率的芯片翻膜方法,提前裁剪出贴合芯片的从全覆盖芯片到漏出芯片边缘1至20圈的若干个挡板,包括步骤如下:
7.(1)边缘参数记录确认:对测试后的芯片数据进行统计分析,确认要翻膜作业的芯片的边缘不良参数的圈数并做记录;
8.(2)翻p面粘膜去除边缘不良品:根据步骤(1)记录的边缘不良参数的圈数,通过提前裁剪好的挡板,覆盖到芯片上,遮住不需要翻除的芯片,漏出边缘不良参数的圈数的芯片,整圈翻掉去除边缘不良品;
9.(3)n面检验:通过显微镜对步骤(2)切割后的芯片的n面外观进行有无崩裂的检验;
10.崩裂的检验主要是人借助显微镜的检验,主要是人主观常规检测。
11.(4)翻n面粘膜:步骤(3)检验结束后,借助翻膜机、白膜、圆形贴片等将管芯颠倒方向,变成n面粘膜,p面向上;
12.(5)p面检验:对芯片的p面外观进行有无崩裂的检验;
13.(6)画片参数分档:将检验完p/n面外观及去除边缘不良品的芯片,根据测试生成的数据晶圆图进行参数的分档作业,将管芯划分成不同参数要求的区域范围;
14.根据本发明优选的,步骤(6)中,画片参数分档,是指:根据参数的需求范围,例电压:1.9-2.1v;亮度:180-210mcd;波长620-625nm;将电压按0.1v、亮度按20mcd、波长620-625nm之间都允许的标准下,将参数分割成电压:1.9-2.0v/2.0-2.1v,亮度:180-200mcd/190-210mcd的范围,将芯片覆盖在通过软件生成的晶圆图上,晶圆图大小调整成与待画片的芯片大小一致,将晶圆图呈现出来的参数结果按参数范围在芯片表面覆盖的蓝膜上进行描摹,将不同的参数区域描摹在芯片蓝膜上,区分开来,即为画片分档。
15.将剩下的芯片根据测试生成的数据参数进行不同参数段内的分档作业,将管芯划分成不同参数要求的区域范围,通常的参数要求的范围为:电压:1.9-2.1v;亮度:180-210mcd;波长620-625nm。
16.(7)翻成品膜:根据画片后的参数范围,将芯片再次通过翻膜分到不同的成品膜上去,变成待入库的产成品;
17.(8)入库:将相同参数范围的成品膜放在一个包装袋内,并提供片源明细,完成入库。
18.led芯片越临近芯片边缘参数不良的频次越高且比较离散,本发明针对这种情况优先对边缘不良参数进行分析归类(例参数不良的区域最大有几圈),确认不良区域的最大圈数,然后通过一次翻膜将边缘不良参数按整圈的形式整个翻掉,一次翻膜去除边缘不良品,剩下的芯片按步骤(6)中的画片直接进行作业即可,彻底取代了现行作业中因边缘参数不良画片时需要多次描摹不同的参数范围区域,然后再根据描摹的多个不良区域进行逐个的翻膜去掉,流程上更为严谨、流畅,明显减少了翻膜次数及边缘不良品的去除。
19.根据本发明优选的,步骤(2)中,翻p面粘膜去除边缘不良品,包括步骤如下:
20.a、确认芯片的边缘不良参数的圈数,对应选取已裁剪好的挡板贴在芯片上;
21.裁剪好的挡板形状与芯片一致,对应边缘不良品的圈数挡板的直径对应比芯片直径小相应的圈数距离。
22.b、挡板上方覆盖一层膜,通过翻膜机进行加热压膜,将漏在挡板外的边缘管芯整圈的翻到膜上,去除边缘不良品。
23.翻膜是把管芯从一张膜上翻到另外一张膜上进行换膜操作,且在翻膜的过程中需要把边缘参数不良的管芯翻掉,通过步骤a中涉及制作的挡板夹在两张膜之间,这样未被挡板覆盖漏在最外圈的管芯会直接处在两张膜之间,通过加热挤压两张膜,这样漏在最外圈的管芯就会被粘附到另一张膜上,被挡板覆盖的管芯继续留在原膜上,完成对边缘不良品的去除。
24.根据本发明优选的,所述挡板的材质为玻璃纸或铝片薄板。
25.玻璃纸材质跟纸张类似可以直接用剪刀裁剪,制作对应不同圈数的膜时更容易制备。
26.根据本发明优选的,所述挡板的厚度为0.01-0.05cm。
27.厚度越趋向于薄越好,翻膜是把管芯从一张膜上翻到另外一张膜上进行换膜操作,玻璃纸或铝片厚度越薄,两张膜之间粘附性就越高,更容易提高管芯倒膜的概率。
28.进一步优选的,步骤b中,在45℃-55℃温度条件下通过翻膜机进行加热压膜。
29.温度的选取根据膜的耐温性设置,在该温度范围内,膜受热后形变及粘度最合适。
30.进一步优选的,步骤b中,所述膜为蓝膜或白膜,厚度为60-80μm。
31.根据本发明优选的,n面检验及p面检验的实现过程为:将芯片放在20x目镜的显微镜下检查芯片n面或p面有无崩裂的异常。
32.根据本发明优选的,步骤(1)中,对测试后的芯片数据进行统计分析,确认要翻膜作业的芯片的边缘不良参数的圈数并做记录,是指:芯片数据包括芯片亮度、电压、波长;芯片数据包括亮度、电压、波长、反向漏电流、反向电压等多个参数,业界中主要用到亮度、电压、波长等参数。将芯片数据转化成对应的晶圆图;将生成的芯片数据通过相应的分析软件,通过对亮度、电压、波长等具体参数的需求设置,软件将表格数据转化成晶圆图(图片格式),通过晶圆图来代替数字的分析。在晶圆图上确认不良参数,即正常参数范围之外的参数即为不良参数,例如,正常参数范围是指:亮度为150-210mcd,电压为1.9-2.1v且波长为620-625nm;根据不良参数确认芯片的边缘不良参数的圈数。通过软件生成的晶圆图可以进行圈数的确认识别。
33.将测试形成的测试数据,进行查看确认芯片的参数情况,并记录边缘不符合要求的参数圈数。
34.根据本发明优选的,步骤(4)中,翻n面粘膜,是指:将翻膜用的铝片覆盖在步骤(3)处理后的芯片上,在铝片上覆盖一层膜。新覆盖的膜就是要用来粘附管芯的膜,将原来的膜去掉。
35.铝片作为中间层将两张膜隔离,通过翻膜机进行加热压膜,将步骤b覆盖的膜揭下来,将芯片翻成p面粘膜。
36.led芯片切割后粘附在膜上时,是p面(电极面)朝上,n面(无电极面)粘附在膜上,通过步骤(2)中去除边缘不良品时进行一次翻膜作业,变成了n面朝上,p面粘附在膜上,考虑到芯片测试时是测试p面电极,生成的数据晶圆图是对应着芯片p面的,以及p面检验的需求,所以通过步骤(4)的操作,将芯片进行另外一次倒膜,再变成p面朝上,n面粘附在膜上。
37.进一步优选的,步骤(4)中,在45℃-55℃温度条件下通过翻膜机进行加热压膜;
38.所述铝片是中空的,形状与步骤(3)处理后的芯片相同,并且所述铝片的直径大于步骤(3)处理后的芯片的直径1-5cm。
39.翻膜过程中两张膜直接相接触粘附在一起,经过加热挤压后在分开的时候会因粘度大比较难分开,降低作业效率,本发明中引入铝片的使用,将铝片裁剪成一定尺寸长度的正方形或圆形,中间挖出一个直径大于芯片直径长度的圆形,翻膜时先将铝片覆盖在待翻膜的芯片膜上,芯片处于铝片中间的圆形孔内,然后在铝片上再覆盖新的翻膜用膜,这样就可以把没有芯片的区域隔离开来,经过加热挤压后由于膜与铝片接触,不存在两张膜之间的粘度变大的问题,而铝片中间中空无遮挡,芯片就非常容易进行膜与膜之间的翻膜。
40.根据本发明优选的,步骤(7)中,翻成品膜,是指芯片经过前边步骤的作业后,需要被翻膜到专用的产品成品膜上(膜的一种),与步骤(4)的作业一样,撕下成品膜覆盖在芯片
上,芯片在成品膜中央,赶出n面的气泡,翻转擦拭p面,从成品膜一角(对角线位置)匀速撕下p面朝上。
41.根据本发明优选的,步骤(8)中,入库,是指:将相同参数范围内的成品膜放在一个包装袋内,打上对应的标签贴上,送检入库。
42.本发明的有益效果为:
43.1、本发明所述用于提高作业效率及产出率的芯片翻膜方法,替代现通用常规的作业方法,先确认参数然后将边缘不良品整圈的翻掉,替代了常规作业方法中画片后按参数划分区域一块一块翻掉不良品的繁琐(化琐碎为整圈),不良品去除后也提高了p面检验。画片等后续作业的效率,从实际运用的结果看,整体作业效率提高10%左右。
44.2、本发明所述用于提高作业效率及产出率的芯片翻膜方法,根据参数翻整圈的方式也减少了原常规作业中去除不良品时来回多次不同小块区域翻膜出现的翻膜异常损失及原p面检验时吸除不良品把控不准多吸的概率,又提高了实际的产出数。
附图说明
45.图1为本发明中翻p面粘膜去除边缘不良品的示意图;
46.1、切割后的芯片,2、玻璃纸,3、边缘不良品,4、粘附切割后芯片的膜,5、铝片,6、圆形孔,7、新膜。
具体实施方式
47.下面结合说明书附图和实施例对本发明作进一步限定,但不限于此。
48.实施例1
49.一种提高作业效率及产出率的芯片翻膜方法,提前裁剪出贴合芯片的从全覆盖芯片到漏出芯片边缘1至20圈的若干个玻璃纸2,如图1所示,包括步骤如下:
50.(1)边缘参数记录确认:对测试后的芯片数据进行统计分析,确认要翻膜作业的芯片的边缘不良参数的圈数并做记录;芯片数据包括芯片亮度、电压、波长;芯片数据包括亮度、电压、波长、反向漏电流、反向电压等多个参数,业界中主要用到亮度、电压、波长等参数。将芯片数据转化成对应的晶圆图;将生成的芯片数据通过相应的分析软件,通过对亮度、电压、波长等具体参数的需求设置,软件将表格数据转化成晶圆图(图片格式),通过晶圆图来代替数字的分析。在晶圆图上确认不良参数,即正常参数范围之外的参数即为不良参数,例如,正常参数范围是指:亮度为150-210mcd,电压为1.9-2.1v且波长为620-625nm;根据不良参数确认芯片的边缘不良参数的圈数。通过软件生成的晶圆图可以进行圈数的确认识别。
51.将测试形成的测试数据,进行查看确认芯片的参数情况,并记录边缘不符合要求的参数圈数。
52.(2)翻p面粘膜去除边缘不良品3根据步骤(1)记录的边缘不良参数的圈数,通过提前裁剪好的玻璃纸2,覆盖到芯片上,遮住不需要翻除的芯片,漏出边缘不良参数的圈数的芯片,整圈翻掉去除边缘不良品3;包括步骤如下:
53.a、确认芯片的边缘不良参数的圈数,对应选取已裁剪好的玻璃纸2贴在芯片上;本实施例中确认芯片的边缘不良参数圈数为5圈;对应选取已裁剪好的直径比芯片直径小5圈
距离的玻璃纸2贴在芯片上;裁剪好的玻璃纸2形状与芯片一致,对应边缘不良品3的圈数玻璃纸2的直径对应比芯片直径小相应的圈数距离。
54.b、玻璃纸上方覆盖一层膜,即粘附切割后芯片的膜4,通过翻膜机进行加热压膜,将漏在玻璃纸2外的边缘管芯整圈的翻到膜上,去除边缘不良品3。翻膜机的温度维持在45℃,借助翻膜机加热压膜后将漏出玻璃纸2外的5圈的边缘管芯整圈的翻到新覆盖的膜上,完成边缘不良品3的去除。
55.翻膜是把管芯从一张膜上翻到另外一张膜上进行换膜操作,且在翻膜的过程中需要把边缘参数不良的管芯翻掉,通过步骤a中涉及制作的玻璃纸2夹在两张膜之间,这样未被玻璃纸2覆盖漏在最外圈的管芯会直接处在两张膜之间,通过加热挤压两张膜,这样漏在最外圈的管芯就会被粘附到另一张膜上,被玻璃纸2覆盖的管芯继续留在原膜上,完成对边缘不良品3的去除。
56.(3)n面检验:通过显微镜对步骤(2)切割后的芯片1的n面外观进行有无崩裂的检验;芯片放在20x目镜的显微镜下检查芯片n面无崩裂的异常;崩裂的检验主要是人借助显微镜的检验,主要是人主观常规检测。
57.(4)翻n面粘膜:步骤(3)检验结束后,借助翻膜机、白膜、圆形贴片等将管芯颠倒方向,变成n面粘膜,p面向上;将翻膜用的铝片5覆盖在芯片上,在铝片5上覆盖一层新膜7,铝片5作为中间层将两张膜隔离,翻膜机的温度维持在45℃,借助翻膜机进行加热压膜后,将原来的膜揭下来就将芯片翻成p面粘膜,铝片5中间是中空的,形状跟芯片一样直径大于芯片1cm。
58.(5)p面检验:对芯片的p面外观进行有无崩裂的检验;芯片放在20x目镜的显微镜下检查芯片p面无崩裂的异常。
59.(6)画片参数分档:将检验完p/n面外观及去除边缘不良品3的芯片,根据测试生成的数据晶圆图进行参数的分档作业,将管芯划分成不同参数要求的区域范围;参数要求的范围为:电压:1.9-2.0v;亮度:170-190mcd/180-200mcd/190-210mcd;波长621-623nm/620-622nm;
60.将剩下的芯片根据测试生成的数据参数进行不同参数段内的分档作业,将管芯划分成不同参数要求的区域范围,通常的参数要求的范围为:电压:1.9-2.1v;亮度:180-210mcd;波长620-625nm。
61.(7)翻成品膜:根据画片后的参数范围,将芯片再次通过翻膜分到不同的成品膜上去,变成待入库的产成品;成品膜的直径要求(优极品、合格品直径8cm,等外品直径10cm),将玻璃纸2剪成圆弧状,用圆弧状的玻璃纸2覆盖在芯片上遮住边缘部分,形状与图形相符;撕下成品膜放在芯片上,芯片在成品膜中央,n面的气泡赶出,翻转擦拭p面;从膜一角(对角线位置)匀速撕下p面朝上;
62.(8)入库:将相同参数范围的成品膜放在一个包装袋内,并提供片源明细,完成入库。
63.led芯片越临近芯片边缘参数不良的频次越高且比较离散,本发明针对这种情况优先对边缘不良参数进行分析归类(例参数不良的区域最大有几圈),确认不良区域的最大圈数,然后通过一次翻膜将边缘不良参数按整圈的形式整个翻掉,一次翻膜去除边缘不良品3,剩下的芯片按步骤(6)中的画片直接进行作业即可,彻底取代了现行作业中因边缘参
数不良画片时需要多次描摹不同的参数范围区域,然后再根据描摹的多个不良区域进行逐个的翻膜去掉,流程上更为严谨、流畅,明显减少了翻膜次数及边缘不良品3的去除。
64.原方法与本实施例中芯片翻膜方法相比,如表1及表2所示:
65.表1
66.工步原有工艺方法新工艺方法参数确认 2n面去边 5n面检验1010翻n面8 翻p面2.52.5p面检验32.5画片5.84.8翻成品膜1511入库2020单位:分64.357.8
67.表2
[0068][0069][0070]
由表1对比可知,本实施例方法明显减少了翻膜次数及边缘不良品3的去除。由表2可知,从实际运用的结果看,按照本实施例芯片翻膜方法,整体单片多产出3200粒左右。
[0071]
实施例2
[0072]
根据实施例1所述的一种提高作业效率及产出率的芯片翻膜方法,其区别在于:
[0073]
步骤(2)中,确认芯片的边缘不良参数圈数为15圈,对应选取已裁剪好的直径比芯片直径小15圈距离的玻璃纸2贴在芯片上,然后玻璃纸2上方再覆盖一层膜,翻膜机的温度维持在50℃,借助翻膜机加热压膜后将漏出玻璃纸2外的15圈的边缘管芯整圈的翻到新覆盖的膜上,完成边缘不良品3的去除;
[0074]
步骤(6)中,参数要求的范围为:电压:1.95-2.05v;亮度:170-200mcd/180-210mcd;波长621-623nm/620-622nm。
[0075]
实施例3
[0076]
根据实施例1或实施例2所述的一种提高作业效率及产出率的芯片翻膜方法,其区别在于:
[0077]
挡板的材质为铝片薄板。
[0078]
挡板的厚度为0.01-0.05cm。
[0079]
厚度越趋向于薄越好,翻膜是把管芯从一张膜上翻到另外一张膜上进行换膜操作,挡板越薄,两张膜之间粘附性就越高,更容易提高管芯倒膜的概率。
[0080]
步骤b中,在45℃-55℃温度条件下通过翻膜机进行加热压膜。
[0081]
温度的选取根据膜的耐温性设置,在该温度范围内,膜受热后形变及粘度最合适。
[0082]
步骤b中,膜为蓝膜或白膜,厚度为60-80μm。
[0083]
步骤(4)中,在45℃-55℃温度条件下通过翻膜机进行加热压膜;铝片5是中空的,形状与步骤(3)处理后的芯片相同,并且铝片5的直径大于步骤(3)处理后的芯片的直径1-5cm。
[0084]
翻膜过程中两张膜直接相接触粘附在一起,经过加热挤压后在分开的时候会因粘度大比较难分开,降低作业效率,本发明中引入铝片5的使用,将铝片5裁剪成一定尺寸长度的正方形或圆形,中间挖出一个直径大于芯片直径长度的圆形,翻膜时先将铝片5覆盖在待翻膜的芯片膜上,芯片处于铝片5中间的圆形孔6内,然后在铝片5上再覆盖新的翻膜用膜,这样就可以把没有芯片的区域隔离开来,经过加热挤压后由于膜与铝片5接触,不存在两张膜之间的粘度变大的问题,而铝片5中间中空无遮挡,芯片就非常容易进行膜与膜之间的翻膜了。