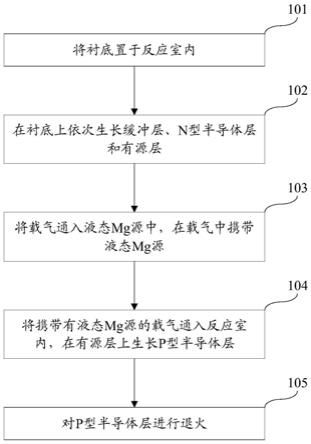
[0001]
本公开涉及半导体技术领域,特别涉及一种发光二极管外延片的制造方法及发光二极管外延片。
背景技术:[0002]
led(light emitting diode,发光二极管)是一种能发光的半导体元器件,具有体积小、使用寿命长、颜色丰富多彩、能耗低的特点。作为信息光电子产业中极具影响力的产品,led被广泛地应用于照明、显示屏、信号灯、背光源、手机、玩具等领域。
[0003]
led制造过程中最重要的是外延片的制造。相关技术中,led外延片的制造过程主要是利用载气将反应物输送到生长衬底上,反应物在生长衬底上反应生成外延材料,外延材料在生长衬底上沉积形成外延层。
[0004]
外延层包括n型半导体层、有源层和p型半导体层等。将电流注入外延片中,n型半导体层提供的电子和p型半导体层提供的空穴会迁移到有源层中进行复合发光。但是p型半导体层提供的空穴数量远小于n型半导体层提供的电子数量,因此led的光电性能(包括发光亮度、抗静电能力、正向电压等)还有待改善。
技术实现要素:[0005]
本公开实施例提供了一种发光二极管外延片的制造方法及发光二极管外延片,可以有效增加p型半导体层提供的空穴数量,提升led的发光亮度、抗静电能力、正向电压等光电性能。所述技术方案如下:
[0006]
一方面,本公开实施例提供了一种发光二极管外延片的制造方法,所述制造方法包括:
[0007]
将衬底置于反应室内;
[0008]
在所述衬底上依次生长缓冲层、n型半导体层和有源层;
[0009]
将载气通入液态mg源中,在所述载气中携带所述液态mg源;
[0010]
将携带有所述液态mg源的载气通入所述反应室内,在所述有源层上生长p型半导体层;
[0011]
对所述p型半导体层进行退火。
[0012]
可选地,所述将载气通入液态mg源中,在所述载气中携带所述液态mg源,包括:
[0013]
提供盛有所述液态mg源的容器,所述容器上设有进气管和出气口,所述进气管的第一端与所述容器外的空间连通,所述进气管的第二端插设在所述液态mg源中,所述出气口将所述容器内位于所述液态mg源上方的空间和所述容器外的空间连通;
[0014]
将所述载气从所述进气管通入所述容器内,所述载气携带所述液态mg源从所述出气口流出。
[0015]
可选地,所述提供盛有液态mg源的容器,包括:
[0016]
将固态mg源置于所述容器内;
[0017]
将所述容器置于恒温设备内,所述恒温设备的设定温度高于所述固态mg源的熔点,所述固态mg源变成所述液态mg源。
[0018]
可选地,所述固态mg源为固态的二甲基二茂镁。
[0019]
可选地,所述恒温设备的设定温度为30℃~40℃。
[0020]
可选地,所述进气管内的载气的压力为750torr~1200torr。
[0021]
可选地,通入所述反应室内的载气的流量为300sccm~400sccm。
[0022]
可选地,退火的温度为780℃~850℃。
[0023]
另一方面,本公开实施例提供了一种发光二极管外延片,所述发光二极管外延片包括衬底、缓冲层、n型半导体层、有源层和p型半导体层,所述缓冲层、所述n型半导体层、所述有源层和所述p型半导体层依次层叠在所述衬底上;所述p型半导体层是将携带有液态mg源的载气通入反应室内进行生长并在生长之后进行退火形成的,所述携带有液态mg源的载气是将载气通入液态mg源中形成的。
[0024]
可选地,所述p型半导体层中mg的掺杂浓度为5*10
19
/cm3~6*10
19
/cm3。
[0025]
本公开实施例提供的技术方案带来的有益效果是:
[0026]
通过将载气通入液态mg源中,可以有效增加载气与mg源的接触,从而增加载气中携带的液态mg源,提高p型半导体层中mg的掺杂浓度,增加p型半导体层提供的空穴数量,增加有源层中电子和空穴的复合发光,提高led的发光亮度,降低led的正向电压,防止电子溢流,提高led的抗静电能力,即led的发光亮度、抗静电能力、正向电压等光电性能均有改善。
附图说明
[0027]
为了更清楚地说明本公开实施例中的技术方案,下面将对实施例描述中所需要使用的附图作简单地介绍,显而易见地,下面描述中的附图仅仅是本公开的一些实施例,对于本领域普通技术人员来讲,在不付出创造性劳动的前提下,还可以根据这些附图获得其他的附图。
[0028]
图1是本公开实施例提供的反应室的结构示意图;
[0029]
图2是本公开实施例提供的石墨盘的俯视图;
[0030]
图3是本公开实施例提供的一种发光二极管外延片的制造方法的流程图;
[0031]
图4是本公开实施例提供的一种发光二极管外延片的制造方法的流程图;
[0032]
图5是本公开实施例提供的容器的结构示意图;
[0033]
图6是本公开实施例提供的恒温水槽的结构示意图;
[0034]
图7是本公开实施例提供的一种发光二极管外延片的结构示意图。
具体实施方式
[0035]
为使本公开的目的、技术方案和优点更加清楚,下面将结合附图对本公开实施方式作进一步地详细描述。
[0036]
外延片是led制造过程中的初级成品。目前应用最广泛的是gan基led外延片。gan基led外延片主要在反应室内制造。
[0037]
图1为本公开实施例提供的反应室的结构示意图。参见图1,反应室100内设有石墨盘10、多个第一出气口21和多个第二出气口22,石墨盘10可转动地设置在反应室100的底
部,多个第一出气口21和多个第二出气口22交替设置在反应室100的顶部并分别与石墨盘10相对。
[0038]
图2为本公开实施例提供的石墨盘的俯视图。参见图2,石墨盘10的表面间隔设有多个凹槽11,多个凹槽11中心的连线为以石墨盘10的中心为圆心的同心圆。例如,如图2所示,靠近石墨盘10的中心的4个凹槽11中心的连线为一个以石墨盘10的中心为圆心的圆形,靠近石墨盘10的边缘的10个凹槽11中心的连线为另一个以石墨盘10的中心为圆心的圆形。两个圆形都是以石墨盘10的中心为圆心且半径大小不同,属于同心圆。
[0039]
制备gan基led外延片时,将蓝宝石衬底放入凹槽11内,转动石墨盘10,通过多个第一出气口21向反应室100内通入mo源和载气,通过多个第二出气口22向反应室100内通入nh3和载气,载气将mo源和nh3传输到蓝宝石衬底上反应生成gan基材料,形成gan基led外延片。
[0040]
载气包括n2和h2中的至少一种;mo源包括ga源、in源、al源中的至少一种,mo源还可以包括si源或者mg源。不同的mo源设置在不同的容器内,每个容器上都设有进气口和出气口,进气口和出气口分别将容器内的空间和容器外的空间连通。当需要向反应室内通入mo源的时候,将载气从进气口通入容器内,载气携带mo源从出气口流出。
[0041]
相关技术中,mg源采用固态的二茂镁,载气与mg源的接触有限,载气能够携带的mg源较少,gan基材料中mg的掺杂浓度较低,gan基led外延片能够提供的空穴数量较少。在实际应用中,p型半导体层提供的空穴数量远小于n型半导体层提供的电子数量,大量的电子未进行复合发光,导致led的发光亮度较低,正向电压较高,而且还会造成电子溢流,降低led的抗静电能力。综上,led的发光亮度、抗静电能力、正向电压等光电性能均有待改善。
[0042]
基于上述情况,本公开实施例提供了一种发光二极管外延片的制造方法。图3为本公开实施例提供的一种发光二极管外延片的制造方法的流程图。参见图3,该制造方法包括:
[0043]
步骤101:将衬底置于反应室内。
[0044]
将衬底置于反应室内,利用载气向反应室内通入反应物,反应物在衬底上反应生成外延材料,外延材料在衬底上沉积形成外延层。外延层包括n型半导体层、有源层和p型半导体层等。
[0045]
步骤102:在衬底上依次生长缓冲层、n型半导体层和有源层。
[0046]
例如,缓冲层的材料采用未掺杂的gan,生长缓冲层时,利用载气向反应室内通入ga源和nh3,ga源和nh3反应生长gan,gan沉积形成缓冲层。
[0047]
n型半导体层的材料采用掺杂si的gan,生长n型半导体层时,利用载气向反应室内通入si源、ga源和nh3,si源、ga源和nh3反应生长掺杂si的gan,掺杂si的gan沉积形成n型半导体层。
[0048]
有源层包括交替层叠的量子阱和量子垒,量子阱的材料采用ingan,生长量子阱时,利用载气向反应室内通入in源、ga源和nh3,in源、ga源和nh3反应生长ingan,ingan沉积形成量子阱;生长量子垒时,利用载气向反应室内通入ga源和nh3,ga源和nh3反应生长gan,gan沉积形成量子垒。
[0049]
步骤103:将载气通入液态mg源中,在载气中携带液态mg源。
[0050]
将载气通入液态mg源中,载气与液态mg源接触,载气从液态mg源中出来的时候会
携带液态mg源,得到携带有液态mg的载气。与固态mg源的接触,载气与液态mg源的接触更大,能够携带的mg源更多。
[0051]
步骤104:将携带有液态mg源的载气通入反应室内,在有源层上生长p型半导体层。
[0052]
将携带有液态mg源的载气通入反应室内,由于载气中携带的mg源增多,因此p型半导体层中mg的掺杂浓度提高,能够提供的空穴数量增加,有源层中电子和空穴的复合发光增多,led的发光亮度提高,正向电压降低;同时未进行复合发光的电子减少,有利于避免电子溢流,led的抗静电能力提高。
[0053]
举例来说,p型半导体层的材料采用掺杂mg的gan,生长p型半导体层时,除了将携带有液态mg源的载气通入反应室内,还利用载气向反应室内通入ga源和nh3,mg源、ga源和nh3反应生长掺杂mg的gan,掺杂mg的gan沉积形成p型半导体层。
[0054]
步骤105:对p型半导体层进行退火。
[0055]
mg源和nh3反应的时候很容易形成mg-h键,影响p型半导体层中掺杂的mg提供空穴。通过对p型半导体层进行退火,可以将mg-h键断开,有利于p型半导体层中掺杂的mg提供空穴。
[0056]
本公开实施例通过将载气通入液态mg源中,可以有效增加载气与mg源的接触,从而增加载气中携带的液态mg源,提高p型半导体层中mg的掺杂浓度,增加p型半导体层提供的空穴数量,增加有源层中电子和空穴的复合发光,提高led的发光亮度,降低led的正向电压,防止电子溢流,提高led的抗静电能力,即led的发光亮度、抗静电能力、正向电压等光电性能均有改善。
[0057]
本公开实施例提供了一种发光二极管外延片的制造方法,特别适用于制造4inch、6inch、8inch等大尺寸的外延片。图4为本公开实施例提供的一种发光二极管外延片的制造方法的流程图。参见图4,该制造方法包括:
[0058]
步骤201:将衬底置于反应室内。
[0059]
示例性地,反应室为mocvd(metal-organic chemical vapor deposition,金属有机化合物化学气相沉淀)设备内的反应腔或者pvd(physical vapour deposition,物理气相沉积)设备内的反应腔。
[0060]
示例性地,衬底为蓝宝石衬底,如晶向为[0001]的蓝宝石。
[0061]
步骤202:在衬底上生长缓冲层。
[0062]
示例性地,缓冲层为aln层或者gan层。缓冲层的厚度为15nm~35nm。
[0063]
在本公开实施例的一种实现方式中,当缓冲层为aln层时,该步骤202包括:
[0064]
采用pvd技术在衬底上形成缓冲层。
[0065]
在本公开实施例的另一种实现方式中,当缓冲层为gan层时,该步骤202包括:
[0066]
采用mocvd技术在衬底上形成缓冲层。
[0067]
可选地,在步骤202之后,该制造方法还包括:
[0068]
在缓冲层上生长未掺杂gan层。
[0069]
通过未掺杂gan层缓解衬底材料与氮化镓之间晶格失配产生的应力和缺陷,为外延片主体结构提供晶体质量较好的生长表面。
[0070]
在本公开实施例中,缓冲层为首先在图形化衬底上低温生长的一层较薄的氮化镓,因此也称为低温缓冲层。再在低温缓冲层进行氮化镓的纵向生长,会形成多个相互独立
的三维岛状结构,称为三维成核层;然后在所有三维岛状结构上和各个三维岛状结构之间进行氮化镓的横向生长,形成二维平面结构,称为二维恢复层;最后在二维生长层上高温生长一层较厚的氮化镓,称为本征氮化镓层。本实施例中将三维成核层、二维恢复层和本征氮化镓层统称为未掺杂氮化镓层。
[0071]
示例性地,未掺杂gan层的厚度为1微米~1.5微米。
[0072]
步骤203:在缓冲层上生长n型半导体层。
[0073]
示例性地,n型半导体层为掺杂si的gan层。n型半导体层中si的掺杂浓度为10
19
/cm3~10
20
/cm3。n型半导体层的厚度为1微米~1.8微米。
[0074]
可选地,该步骤203包括:
[0075]
采用mocvd技术形成n型半导体层。
[0076]
可选地,在步骤203之后,该制造方法还包括:
[0077]
在n型半导体层上生长应力释放层。
[0078]
通过应力释放层改善衬底材料与氮化镓之间晶格失配产生的应力和缺陷,为外延片主体结构提供晶体质量较好的生长表面。
[0079]
示例性地,应力释放层包括交替层叠的ingan层和gan层。应力释放层中ingan层的数量和应力释放层中gan层的数量相同,应力释放层中ingan层的数量为2个~4个,如3个。应力释放层中ingan层的厚度为13nm~17nm,如15nm;应力释放层中gan层的厚度为40nm~50nm,如45nm。
[0080]
步骤204:在n型半导体层上生长有源层。
[0081]
示例性地,有源层包括交替层叠的ingan量子阱和gan量子垒。ingan量子阱的数量和gan量子垒的数量相同,ingan量子阱的数量为7个~9个,如8个。ingan量子阱的厚度为3nm~5nm,如4nm;gan量子垒的厚度为10nm~14nm,如13nm;ingan量子阱和gan量子垒的厚度之和为13nm~18nm。
[0082]
可选地,该步骤204包括:
[0083]
采用mocvd技术形成有源层。
[0084]
可选地,在步骤204之后,该制造方法还包括:
[0085]
在有源层上生长电子阻挡层。
[0086]
示例性地,电子阻挡层为掺杂mg的algan层。
[0087]
在本公开实施例的一种实现方式中,在有源层上生长电子阻挡层,包括:
[0088]
将载气通入液态mg源中,在载气中携带液态mg源;
[0089]
将携带有液态mg源的载气通入反应室内,在有源层上生长电子阻挡层。
[0090]
在本公开实施例的另一种实现方式中,在有源层上生长电子阻挡层,包括:
[0091]
将载气通入固态mg源中,在载气中携带固态mg源;
[0092]
将携带有固态mg源的载气通入反应室内,在有源层上生长电子阻挡层。
[0093]
电子阻挡层的主要作用是阻挡电子,对空穴浓度要求不高,因此采用固态mg源或者液态mg源形成都可以。
[0094]
示例性地,电子阻挡层的生长温度为930℃~970℃,生长压力为100torr。
[0095]
可选地,在有源层上生长电子阻挡层之前,该制造方法还包括:
[0096]
在有源层上生长低温p型层。
[0097]
通过在有源层和电子阻挡层之间设置低温p型层,避免电子阻挡层较高的生长温度造成有源层中的铟原子析出,影响发光二极管的发光效率。
[0098]
示例性地,低温p型层为掺杂mg的gan层。低温p型层中mg的掺杂浓度为5*10
19
/cm3~6*10
19
/cm3。低温p型层的厚度为10nm~50nm。
[0099]
可选地,在有源层上生长低温p型层,包括:
[0100]
将载气通入液态mg源中,在载气中携带液态mg源;
[0101]
将携带有液态mg源的载气通入反应室内,在有源层上生长低温p型层。
[0102]
低温p型层会为有源层提供空穴,需要采用液态mg源提高空穴浓度。
[0103]
示例性地,低温p型层的生长温度为600℃~850℃,生长压力为100torr~600torr。
[0104]
步骤205:将载气通入液态mg源中,在载气中携带液态mg源。
[0105]
可选地,该步骤205包括:
[0106]
提供盛有液态mg源的容器,容器上设有进气管和出气口,进气管的第一端与容器外的空间连通,进气口的第二端插设在液态mg源中,出气口将容器内位于液态mg源上方的空间和容器外的空间连通;
[0107]
将载气从进气管通入容器内,载气携带液态mg源从出气口流出。
[0108]
图5为本公开实施例提供的容器的结构示意图。参见图5,容器200内盛有液态mg源30,容器上设有进气管41和出气口42,进气管41的第一端与容器200外的空间连通,进气管41的第二端插设在液态mg源30中,出气口42将容器200内位于液态mg源30上方的空间和容器200外的空间连通。
[0109]
通过在容器上设置进气管,进气管的第一端与容器外的空间连通,进气管的第二端插设在容器内的液态mg源中,将载气从容器外通过进气管通入容器内,可以确保载气先与液态mg源接触,载气从液态mg源上方离开液态mg源的时候会携带液态mg源,变成携带有液态mg的载气。同时容器上还设有出气口,出气口将容器内位于液态mg源上方的空间和容器外的空间连通,因此携带有液态mg的载气离开液态mg源之后,可以通过出气口流到容器外,方便得到携带有液态mg源的载气。
[0110]
可选地,提供盛有液态mg源的容器,包括:
[0111]
将固态mg源置于容器内;
[0112]
将容器置于恒温设备内,恒温设备的设定温度高于固态mg源的熔点,固态mg源变成液态mg源。
[0113]
目前发现的mg源在常温下都为固态,先将固态mg源置于容器内,再将容器置于恒温设备内,利用恒温设备的设定温度高于固态mg源的熔点,使得固态mg源的温度升高到熔点之上,固态mg源熔化为液态,并且保持为液态,从而得到液态mg源。实现简单方便,而且可靠性高。
[0114]
可选地,固态mg源为固态的二甲基二茂镁。
[0115]
二甲基二茂镁的熔点低于30℃,比常温高不了多少,高于熔点的温度很容易实现。实现简单方便,而且可靠性高、成本低廉。
[0116]
可选地,恒温设备的设定温度为30℃~40℃,如36℃。
[0117]
二甲基二茂镁的熔点低于30℃,恒温设备的设定温度高于30℃即可,设定温度略
高于二甲基二茂镁的熔点,可以有效降低实现成本。
[0118]
示例性地,恒温设备为恒温水槽。
[0119]
恒温水槽保持恒温的实现难度较低,可靠性较高。
[0120]
图6为本公开实施例提供的恒温水槽的结构示意图。参见图6,恒温水槽300内设有隔板51,隔板51将恒温水槽300内的空间分为上下两个部分。恒温水槽300位于下面的空间内设置有水52和加热器53,将容器200可以置于恒温水槽300位于上面的空间内,利用加热器53对水52进行加热,即可使容器200的温度保持为设定温度。
[0121]
可选地,进气管内的载气的压力为750torr~1200torr,如1000torr。
[0122]
进气管内的载气的压力为750torr~1200torr,可以为p型半导体层的生长提供充足的mg源,同时不会造成反应室内的压力过高而影响到p型半导体层的生长。
[0123]
步骤206:将携带有液态mg源的载气通入反应室内,在有源层上生长p型半导体层。
[0124]
可选地,通入反应室内的载气的流量为300sccm~400sccm。
[0125]
与固态mg源相比,载气与液态mg源的接触更充分,相同载气携带的液态mg源将远大于固态mg源。在本公开实施例中,携带有液态mg源的载气的流量为300sccm~400sccm,与携带有固态mg源的载气1000sccm~3000sccm的流量相比,载气的流量下降至原来的10%~40%,如300sccm为2000sccm的15%,说明p型半导体层中mg的掺杂效率得到大幅提升,实现上更为方便,可靠性也更高。
[0126]
示例性地,p型半导体层为掺杂mg的gan层。p型半导体层中mg的掺杂浓度为5*10
19
/cm3~6*10
19
/cm3。p型半导体层的厚度为200nm~400nm,如300nm。
[0127]
示例性地,p型半导体层的生长温度为900℃~1050℃,如1000℃。
[0128]
可选地,在步骤206之后,该制造方法还包括:
[0129]
在p型半导体层上生长p型接触层。
[0130]
通过p型接触层与芯片制作工艺中形成的电极或者透明导电薄膜之间形成欧姆接触。
[0131]
示例性地,p型接触层为掺杂mg的ingan层。p型接触层的厚度为50nm~300nm,如175nm;p型接触层中mg的掺杂浓度为5*10
19
/cm3~10
22
/cm3,如6*10
20
/cm3。
[0132]
可选地,在p型半导体层上生长p型接触层,包括:
[0133]
将载气通入液态mg源中,在载气中携带液态mg源;
[0134]
将携带有液态mg源的载气通入反应室内,在p型半导体层上生长p型接触层。
[0135]
p型接触层的主要作用是降低接触电阻,采用液态mg源提高空穴浓度,有利于电流的注入。
[0136]
示例性地,p型接触层的生长温度为850℃~1000℃,生长压力为100torr~300torr,
[0137]
步骤207:对p型半导体层进行退火。
[0138]
可选地,退火的温度为780℃~850℃,如800℃。
[0139]
与固态mg源相比,载气与液态mg源的接触更充分,载气中携带的mg源更多,mg源和nh3反应形成mg-h键更多,将mg-h键断开需要的能量较多。在本公开实施例中,液态mg源形成的p型半导体层的退火温度为780℃~850℃,与固态mg源形成的p型半导体层的650℃~750℃的退火温度相比,退火温度升高,可以为mg-h键断开提供足够的能量,有利于p型半导
体层中掺杂的mg提供空穴。
[0140]
示例性地,退火在氮气气氛下进行。
[0141]
需要说明的是,在上述外延生长结束之后,会先将温度降低至650℃~850℃,在氮气气氛中对外延片进行5分钟~15分钟的退火处理,然后再将外延片的温度降低至室温。
[0142]
实现时,采用氢气、或者氮气、或者氢气和氮气的混合气体作为载气,以三甲基镓或三乙基镓作为镓源,高纯氨气作为氮源,三甲基铟作为铟源,三甲基铝作为铝源,硅烷作为硅源,二茂镁作为镁源。
[0143]
表一 固态mg源和液态mg源形成p型半导体层的对比情况表
[0144]
项目流量空穴浓度/cm3迁移率cm2/vs固态mg源2000sccm2.36*10
17
10.25液态mg源300sccm6.52*10
17
16.53
[0145]
由表一可知,与固态mg源相比,液态mg源形成的p型半导体层的空穴浓度和迁移率均有大幅提升。
[0146]
本公开实施例提供了一种发光二极管外延片,适用于采用图3或图4所示的制造方法进行制造。图7为本公开实施例提供的一种发光二极管外延片的结构示意图。参见图7,该发光二极管外延片包括衬底301、缓冲层302、n型半导体层303、有源层304和p型半导体层305,缓冲层302、n型半导体层303、有源层304和p型半导体层305依次层叠在衬底301上。p型半导体层305是将携带有液态mg源的载气通入反应室内进行生长并在生长之后进行退火形成的,携带有液态mg源的载气是将载气通入液态mg源中形成的。
[0147]
可选地,p型半导体层305中mg的掺杂浓度为5*10
19
/cm3~6*10
19
/cm3。
[0148]
在本公开实施例中,衬底301为蓝宝石衬底,如晶向为[0001]的蓝宝石。
[0149]
缓冲层302为aln层或者gan层。缓冲层的厚度为15nm~35nm。
[0150]
n型半导体层303为掺杂si的gan层。n型半导体层303中si的掺杂浓度为10
19
/cm3~10
20
/cm3。n型半导体层303的厚度为1微米~1.8微米。
[0151]
有源层304包括交替层叠的ingan量子阱和gan量子垒。ingan量子阱的数量和gan量子垒的数量相同,ingan量子阱的数量为7个~9个,如8个。ingan量子阱的厚度为3nm~5nm,如4nm;gan量子垒的厚度为10nm~14nm,如13nm;ingan量子阱和gan量子垒的厚度之和为13nm~18nm。
[0152]
以上所述仅为本公开的可选实施例,并不用以限制本公开,凡在本公开的精神和原则之内,所作的任何修改、等同替换、改进等,均应包含在本公开的保护范围之内。