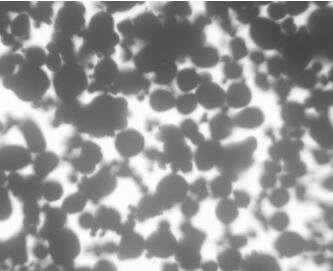
[0001]
本发明涉及锂电池领域,具体涉及一种锂电池硅碳负极的制备方法。
背景技术:[0002]
随着锂离子电池在电动汽车、储能电站等设备应用上的不断拓展,传统石墨负极已经很难满足人类对高能量密度电池的需求,因此寻找可以替代石墨的下一代锂离子电池阳极材料成为目前锂离子电池相关研究的热点之一。硅材料的理论比容量为4200mah/g,资源丰富,嵌锂电位较高。然而硅基材料在充放电过程中会具有较大的体积变化,容易导致电极材料粉碎,与集流体、电极导电网络脱离接触,同时体积变化带来新表面的产生,进而导致循环寿命的大幅度降低。
[0003]
目前解决循环性能的一个主流方向为对原料进行纳米化处理和包覆以降低其宏观体积膨胀,但纳米化处理后的原料在负极材料的合成过程中极易出现自发团聚。针对这一问题,专利cn110416500a提出一种硅碳负极材料及其制备方法,通过共价有机框架负载硅粉进行分散,专利cn110364735a提出了一种锂离子电池硅碳负极用粘合剂、制备及其应用,通过使用硅烷类化合物作为粘结剂调节硅碳负极浆料的分散性能,专利cn109935808a提出了一种基于微米硅片制备硅碳负极材料的方法,通过电子束蒸发形成的硅微米片在聚合物载体上进行负载,以实现硅的分散性能。但以上技术方案都是通过对原料进行改性调整,工艺难度较大,在产业化应用上较为困难,因此,提高硅碳负极的循环性能,抑制其体积膨胀在实际生产过程中具有十分重要的实际意义。针对现有硅碳负极材料循环性能较差的问题,本发明提出一种砂磨机-挤出机一体制备锂电池中空硅碳颗粒的方法。
技术实现要素:[0004]
针对现有硅碳负极材料循环性能较差的问题,本发明通过砂磨机使ga-in-fe液态金属与硅粉复合后对硅粉形成包覆,再在挤出机中使用有机碳源包覆液态金属后,在去离子水中升温使液态金属膨胀成多孔材料,之后通过固化剂使表面有机碳源固化后洗脱液态金属,通过高温碳化形成具有中空结构的硅碳负极材料。
[0005]
一种砂磨机-挤出机一体制备锂电池中空硅碳颗粒的方法,其特征在于具体步骤如下:步骤s1、将硅粉、分散剂、ga-in-fe液态金属加入砂磨机在惰性气体保护下砂磨1-3h,将砂磨获得的原料转移至冷却室,形成金属包覆硅颗粒;步骤s2、将步骤s1中获得的金属包覆硅颗粒与有机碳源、石蜡、造孔剂混合均匀,加入惰性气体保护下的螺杆挤出机,在室温下挤出3~10次,将获得的粉末与固化剂混合后加入造粒机进行球化处理,之后将获得的球形颗粒加入去离子水,在紫外辐照下,60~80℃水浴加热1-2h,之后在稀盐酸中浸泡1-2h,再在去离子水中浸泡15-20min,过滤、离心并收集固体颗粒;步骤s3、将步骤s2中获得的固体颗粒在管式炉中800~1100℃下碳化3-6h,获得具有中
空结构的硅碳负极颗粒。
[0006]
优选的,步骤s1中硅粉为微米级硅粉,使用微米级硅粉进行砂磨细化至纳米级,在砂磨中暴露出的新鲜表面更容易被液态金属包覆。
[0007]
优选的,步骤s1中分散剂为ctab。
[0008]
优选的,步骤s1中ga-in-fe液态金属中各金属质量比例为ga:in:fe=75:25:5-10,这种配比的液态金属具有优异的温度和紫外光敏感性,在水溶液中受热或紫外辐照下会膨胀形成多孔结构,由于液态金属包覆在硅粉表面,其外表面又包覆有含有环氧树脂的有机碳源,环氧树脂固化并且液态金属膨胀后除去中间的液态金属夹心层,环氧树脂和其它有机碳源经碳化处理后,形成碳-硅核壳结构,同时硅粉与碳外壳之间具有较大的间隙,能有效抑制硅碳负极中硅的体积膨胀效应,避免硅碳负极中硅由于体积膨胀产生的粉化和剥落。
[0009]
优选的,步骤s2中所述有机碳源为环氧树脂和甘蔗渣按照1:1比例混合而成,这种有机碳源可以在中低温下通过固化剂固化,并形成具有较高强度和韧性的膜层,在高温碳化过程中不易出现坍塌和破碎,碳化形成的碳壳具有多孔结构,便于电解液与硅粉的浸润。
[0010]
优选的,步骤s2中所述环氧树脂为e-51,固化剂为酚醛胺类环氧固化剂t-31。
[0011]
优选的,步骤s2中所述造孔剂为碱金属氧化物或碱土金属氧化物无机酸溶性造孔剂。这种造孔剂可以在环氧树脂膜内部辅助形成通孔,便于后续液态金属的分离。
[0012]
优选的,步骤s2中螺杆挤出机长径比为10-30,转速为10-40rpm。
[0013]
优选的,砂磨机、螺杆挤出机、管式炉中气氛为氩气保护。
[0014]
优选的,各原料质量份数为硅粉30-50份,分散剂3-5份,液态金属10-30份,有机碳源300-400份,石蜡10-20份,造孔剂3-5份,固化剂5-30份。
[0015]
本发明通过液态金属在水热和紫外辐照过程中反应膨胀,最外层包覆的固化环氧树脂形成具有较高机械强度的壳层,硅基材料与碳外壳之间具有由液态金属膨胀产生的较大的间隙,除去液态金属并在碳化后形成球形中空核壳结构硅碳负极,作为核的硅基材料与碳外壳之间具有较大孔隙,在循环充放电过程中,留有较大空间供硅产生膨胀,而不会导致负极材料在宏观尺度上产生膨胀。与现有技术相比,本发明制备的球形硅碳负极颗粒形状均匀,球形中空结构保持较好,在循环过程中可以有效缓解体积膨胀,从而有效提高硅碳负极循环性能。
[0016]
本发明工序为将硅粉、分散剂、液态金属真空球磨后,在硅粉细化的同时使用液态金属进行包覆,金属包覆后使用环氧树脂、甘蔗渣粉末再次包覆,形成双层核壳结构,在水热处理过程中,液态金属与热水反应放出大量气体,使液态金属在固化过程中发生体积膨胀,对表层包覆的环氧树脂层进行挤压,表层包覆的环氧树脂层在固化剂和水热处理时发生固化,液态金属经过处理被除去后,形成硅粉/环氧树脂/甘蔗渣的中空核壳结构,最后经过高温碳化,形成具有中空结构的硅/碳复合粉末。
[0017]
说明书附图图1为实施例1中产品的显微结构照片;图2为对比例1中产品的显微结构照片;图3为对比例2中产品的显微结构照片。
具体实施方式
[0018]
以下通过具体实施方式对本发明作进一步的详细说明,但不应将此理解为本发明的范围仅限于以下的实例。在不脱离本发明上述方法思想的情况下,根据本领域普通技术知识和惯用手段做出的各种替换或变更,均应包含在本发明的范围内。
[0019]
实施例1步骤s1、将微米级硅粉、ctab分散剂、ga-in-fe液态金属加入砂磨机在惰性气体保护下砂磨1h,将砂磨获得的原料转移至冷却室,形成金属包覆硅颗粒;各金属质量比例为ga:in:fe=75:25:5;各原料质量份数为硅粉30份,分散剂3份,液态金属10份。
[0020]
步骤s2、将步骤s1中获得的金属包覆硅颗粒与有机碳源、石蜡、造孔剂混合均匀,加入惰性气体保护下的螺杆挤出机,在室温下挤出3~10次,将获得的粉末与固化剂混合后加入造粒机进行球化处理,之后将获得的球形颗粒加入去离子水,在紫外辐照下,60℃水浴加热2h,之后在稀盐酸中浸泡1h,再在去离子水中浸泡15-20min,过滤、离心并收集固体颗粒;有机碳源为环氧树脂和甘蔗渣按照1:1比例混合而成;环氧树脂为e-51,固化剂为酚醛胺类环氧固化剂t-31;造孔剂为碱金属氧化物或碱土金属氧化物无机酸溶性造孔剂;螺杆挤出机长径比为10,转速为10rpm;各原料比例为有机碳源300份,石蜡10份,造孔剂3份,固化剂5份。
[0021]
步骤s3、将步骤s2中获得的固体颗粒在管式炉中800℃下碳化6h,获得具有中空结构的硅碳负极颗粒。
[0022]
实施例2步骤s1、将微米级硅粉、ctab分散剂、ga-in-fe液态金属加入砂磨机在惰性气体保护下砂磨1.5h,将砂磨获得的原料转移至冷却室,形成金属包覆硅颗粒;各金属质量比例为ga:in:fe=75:25:6.4;各原料质量份数为硅粉35份,分散剂3.5份,液态金属15份。
[0023]
步骤s2、将步骤s1中获得的金属包覆硅颗粒与有机碳源、石蜡、造孔剂混合均匀,加入惰性气体保护下的螺杆挤出机,在室温下挤出3~10次,将获得的粉末与固化剂混合后加入造粒机进行球化处理,之后将获得的球形颗粒加入去离子水,在紫外辐照下,65℃水浴加热1.75h,之后在稀盐酸中浸泡1.25h,再在去离子水中浸泡15-20min,过滤、离心并收集固体颗粒;有机碳源为环氧树脂和甘蔗渣按照1:1比例混合而成;环氧树脂为e-51,固化剂为酚醛胺类环氧固化剂t-31;造孔剂为碱金属氧化物或碱土金属氧化物无机酸溶性造孔剂;螺杆挤出机长径比为15,转速为18rpm;各原料比例为有机碳源325份,石蜡12份,造孔剂3.5份,固化剂11份。
[0024]
步骤s3、将步骤s2中获得的固体颗粒在管式炉中870℃下碳化5.2h,获得具有中空结构的硅碳负极颗粒。
[0025]
实施例3一步骤s1、将微米级硅粉、ctab分散剂、ga-in-fe液态金属加入砂磨机在惰性气体保护下砂磨2h,将砂磨获得的原料转移至冷却室,形成金属包覆硅颗粒;各金属质量比例为ga:in:fe=75:25:7.7;各原料质量份数为硅粉40份,分散剂4份,液态金属20份。
[0026]
步骤s2、将步骤s1中获得的金属包覆硅颗粒与有机碳源、石蜡、造孔剂混合均匀,加入惰性气体保护下的螺杆挤出机,在室温下挤出3~10次,将获得的粉末与固化剂混合后加入造粒机进行球化处理,之后将获得的球形颗粒加入去离子水,在紫外辐照下,70℃水浴
加热1.5h,之后在稀盐酸中浸泡1.5h,再在去离子水中浸泡15-20min,过滤、离心并收集固体颗粒;有机碳源为环氧树脂和甘蔗渣按照1:1比例混合而成;环氧树脂为e-51,固化剂为酚醛胺类环氧固化剂t-31;造孔剂为碱金属氧化物或碱土金属氧化物无机酸溶性造孔剂;螺杆挤出机长径比为20,转速为25rpm;各原料比例为有机碳源350份,石蜡15份,造孔剂4份,固化剂18份。
[0027]
步骤s3、将步骤s2中获得的固体颗粒在管式炉中950℃下碳化4.5h,获得具有中空结构的硅碳负极颗粒。
[0028]
实施例4步骤s1、将微米级硅粉、ctab分散剂、ga-in-fe液态金属加入砂磨机在惰性气体保护下砂磨2.5h,将砂磨获得的原料转移至冷却室,形成金属包覆硅颗粒;各金属质量比例为ga:in:fe=75:25:8.9;各原料质量份数为硅粉45份,分散剂4.5份,液态金属25份。
[0029]
步骤s2、将步骤s1中获得的金属包覆硅颗粒与有机碳源、石蜡、造孔剂混合均匀,加入惰性气体保护下的螺杆挤出机,在室温下挤出3~10次,将获得的粉末与固化剂混合后加入造粒机进行球化处理,之后将获得的球形颗粒加入去离子水,在紫外辐照下,75℃水浴加热1.25h,之后在稀盐酸中浸泡1.75h,再在去离子水中浸泡15-20min,过滤、离心并收集固体颗粒;有机碳源为环氧树脂和甘蔗渣按照1:1比例混合而成;环氧树脂为e-51,固化剂为酚醛胺类环氧固化剂t-31;造孔剂为碱金属氧化物或碱土金属氧化物无机酸溶性造孔剂;螺杆挤出机长径比为25,转速为33rpm;各原料比例为有机碳源375份,石蜡17份,造孔剂4.5份,固化剂24份。
[0030]
步骤s3、将步骤s2中获得的固体颗粒在管式炉中1020℃下碳化3.7h,获得具有中空结构的硅碳负极颗粒。
[0031]
实施例5步骤s1、将微米级硅粉、ctab分散剂、ga-in-fe液态金属加入砂磨机在惰性气体保护下砂磨3h,将砂磨获得的原料转移至冷却室,形成金属包覆硅颗粒;各金属质量比例为ga:in:fe=75:25:10;各原料质量份数为硅粉50份,分散剂5份,液态金属30份。
[0032]
步骤s2、将步骤s1中获得的金属包覆硅颗粒与有机碳源、石蜡、造孔剂混合均匀,加入惰性气体保护下的螺杆挤出机,在室温下挤出3~10次,将获得的粉末与固化剂混合后加入造粒机进行球化处理,之后将获得的球形颗粒加入去离子水,在紫外辐照下,80℃水浴加热1h,之后在稀盐酸中浸泡2h,再在去离子水中浸泡15-20min,过滤、离心并收集固体颗粒;有机碳源为环氧树脂和甘蔗渣按照1:1比例混合而成;环氧树脂为e-51,固化剂为酚醛胺类环氧固化剂t-31;造孔剂为碱金属氧化物或碱土金属氧化物无机酸溶性造孔剂;螺杆挤出机长径比为30,转速为40rpm;各原料比例为有机碳源400份,石蜡20份,造孔剂5份,固化剂30份。
[0033]
步骤s3、将步骤s2中获得的固体颗粒在管式炉中1100℃下碳化3h,获得具有中空结构的硅碳负极颗粒。
[0034]
对比例1步骤s1、将微米级硅粉、ctab分散剂加入砂磨机在惰性气体保护下砂磨1h,将砂磨获得的原料转移至冷却室,形成细分散硅颗粒;各原料质量份数为硅粉30份,分散剂3份。
[0035]
步骤s2、将步骤s1中获得的细分散硅颗粒与有机碳源、石蜡、造孔剂混合均匀,加
入惰性气体保护下的螺杆挤出机,在室温下挤出3~10次,将获得的粉末与固化剂混合后加入造粒机进行球化处理,之后将获得的球形颗粒加入去离子水,在紫外辐照下,60℃水浴加热2h,之后在稀盐酸中浸泡1h,再在去离子水中浸泡15-20min,过滤、离心并收集固体颗粒;有机碳源为环氧树脂和甘蔗渣按照1:1比例混合而成;环氧树脂为e-51,固化剂为酚醛胺类环氧固化剂t-31;造孔剂为碱金属氧化物或碱土金属氧化物无机酸溶性造孔剂;螺杆挤出机长径比为10,转速为10rpm;各原料比例为有机碳源300份,石蜡10份,造孔剂3份,固化剂5份。
[0036]
步骤s3、将步骤s2中获得的固体颗粒在管式炉中800℃下碳化6h,获得产品。
[0037]
对比例2步骤s1、将微米级硅粉、ctab分散剂、ga-in-fe液态金属加入砂磨机在惰性气体保护下砂磨1h,将砂磨获得的原料转移至冷却室,形成金属包覆硅颗粒;各金属质量比例为ga:in:fe=75:25:5;各原料质量份数为硅粉30份,分散剂3份,液态金属10份。
[0038]
步骤s2、将步骤s1中获得的金属包覆硅颗粒与有机碳源、石蜡、造孔剂混合均匀,加入惰性气体保护下的螺杆挤出机,在室温下挤出3~10次,将获得的粉末加入造粒机进行球化处理,之后将获得的球形颗粒加入去离子水,在紫外辐照下,60℃水浴加热2h,之后在稀盐酸中浸泡1h,再在去离子水中浸泡15-20min,过滤、离心并收集固体颗粒;有机碳源为沥青和甘蔗渣按照1:1比例混合而成;造孔剂为碱金属氧化物或碱土金属氧化物无机酸溶性造孔剂;螺杆挤出机长径比为10,转速为10rpm;各原料比例为有机碳源300份,石蜡10份,造孔剂3份,固化剂5份。
[0039]
步骤s3、将步骤s2中获得的固体颗粒在管式炉中800℃下碳化6h,获得产品。
[0040]
相关检测:1、使用实施例1、对比例1、对比例2样品与pdvf、super-p按照8:1:1比例混合配置为浆料,溶剂使用nmp,涂布于铜箔表面作为正极,锂片作为负极,六氟磷酸锂和碳酸酯作为电解液,制备cr2032扣式电池,对扣式电池进行循环性能测试,测试电流为0.4ma/g,循环次数为50次,测试结果如表1所示。
[0041]
2、使用显微镜观察实施例1、对比例1、对比例2样品形貌。
[0042]
3、通过比表面积测试仪使用氮气吸附法测试实施例1、对比例1、对比例2的比表面积。
[0043]
表1: 首次循环容量(mah/g)首次循环效率(%)50圈循环剩余容量(mah/g)比表面积(m2/g)实施例1488.483.7463.88.7468实施例2489.183.9465.08.7352实施例3487.683.1464.38.6981实施例4488.583.8464.98.7581实施例5488.083.3463.68.7443对比例1497.685.4408.91.4555对比例2479.382.9382.63.8057
通过检测,实施例1具有优异的多次充放电循环性能,这是由于环氧树脂/甘蔗渣经过固化后,在碳化过程中可以有效保持碳壳结构,表层的碳壳不会坍塌,如图1所示,在洗去液体金属后形成均匀的球状中空硅碳复合颗粒,而对比例1未使用液体金属进行膨胀,内部未形成中空结构,其比表面积远低于实施例1,且其硅基材料在充放电的过程中体积膨胀导致
电极材料粉化剥落,其多次充放电循环性能相对较差。对比例2未使用固化的有机碳源进行包覆,在烧结碳化过程中形成的碳壳坍塌,导致形成的颗粒未形成规则球状颗粒,如图3所示,因此其多次充放电循环性能同样相对较差。