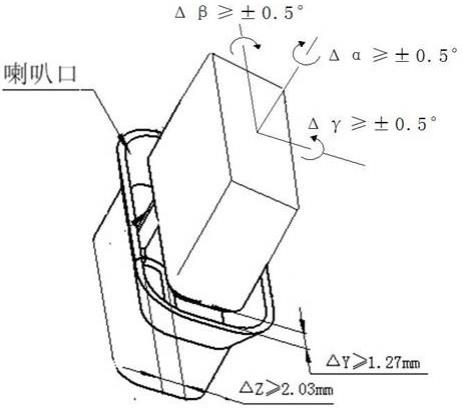
[0001]
本发明涉及一种可以浮动的电连接器。
背景技术:[0002]
申请人于2013年研发了一款可以自由浮动的电连接器,具体结构见中国专利cn103633492b,该连接器可以实现六个自由度的浮动,可以在对接不是很精确情况下完成连接。现在需要将该结构应用到空间飞行器中,在空间中连接器的对接是用机械手来完成,而机械手只会按照程序设定的固定轨迹运动,当两个连接器的位置误差较大时,机械手强行对接会带来损伤,并且在飞行器上长期存在振动、冲击等力学环境,产品相对于浮动安装机构处于自由运动状态,易产生剧烈晃动、撞击,导致产品损伤、失效,因此要求两个连接器的配合能够容许较大的浮动,所以需要对现有的结构进行优化设计,使之能够满足较大的浮动要求。另外,原有的结构还存在限位柱下段连接的螺母松脱的问题。
技术实现要素:[0003]
本发明要解决的技术问题是:现有浮动连接器浮动范围不足的问题,以及连接器限位柱螺母松脱的问题。
[0004]
本发明的技术方案是:一种空间用矩形自浮动连接器,包括罩壳和浮动的喇叭形接口,喇叭形接口相对于罩壳具有x向浮动、y向浮动、z向浮动、α向转动、β向转动及γ向转动六个自由度,且δα≥
±
0.5
°
、δβ≥
±
0.5
°
、δγ≥
±
0.5
°
,δx≥2.29mm、δy≥1.27mm、δz≥2.03mm。
[0005]
罩壳内通过扁簧安装固定板,固定板两端的沉孔中安装卷簧,喇叭形接口的法兰两端安装限位柱,限位柱中段和卷簧配合,限位柱下段连接螺母,螺母侧面有固定钉组装孔,固定钉旋入固定钉组装孔后顶住限位柱。
[0006]
喇叭形接口的喇叭形开口倾角为30
°
。
[0007]
喇叭形接口相对于罩壳在x方向上运动时,限位柱首先达到极限位移碰到其正下方的挡块,限位柱尺寸为16.1mm,扁簧未受压缩状态下限位柱距挡块距离大于δx,为3.1mm。
[0008]
当喇叭形接口相对于罩壳在y方向上运动时,喇叭形接口外壳的尾端首先达到极限位移碰到罩壳内部的挡板,y方向上喇叭形接口外壳尾端距挡板的距离大于δy,为2.15mm。
[0009]
当喇叭形接口相对于罩壳在z方向运动时,卷簧首先达到极限压缩位置自身贴紧,喇叭形接口外壳法兰侧边距罩壳的距离大于卷簧自身贴紧需移动的距离,为2.95mm;卷簧自身贴紧需移动的距离大于δz,为2.7mm。
[0010]
喇叭形接口外壳绕x轴转动的最大角度为9
°
。
[0011]
喇叭形接口外壳绕y轴转动的最大角度为2.2
°
。
[0012]
喇叭形接口外壳绕z轴转动的最大角度为1.6
°
。
[0013]
扁簧装配时具备一个初始变形量,初始变形量产生的反力大于连接器的最大插合力。
[0014]
扁簧顶端的半圆形凸起部分加工为弯曲的圆柱体。本发明的有益效果:本产品可以用在空间飞行器上,在空间环境下,连接器的对接是由机械手操作,产品所在的工作环境较恶劣,通常伴随着振动、极冷、极热等条件,因此对与对接时可允许的误差要求很高,本产品需满足的对准差δα≥
±
0.5
°
,δβ≥
±
0.5
°
,δγ≥
±
0.5
°
,δx≥2.29mm(超行程量),δy≥1.27mm,δz≥2.03mm。也即是说,当插头、插座之间存在上述对准差时,本产品的导向结构应能补偿该误差,确保插头、插座的正常对接。
[0015]
为便于产品浮动导向,减少导向过程对壳体的摩擦磨损和减小摩擦反力,满足产品长寿命和自浮动的功能需求,需要同时对喇叭口导向角度进行合理设计,最佳角度为30
°
。
[0016]
螺母与限位柱调整好位置后,将固定钉拧入抵紧限位柱,避免螺母从限位柱上松动、脱落,扁簧顶端的半圆形凸起部分加工为弯曲的圆柱体可以降低浮动时β向的阻力使转动更顺畅。
[0017]
附图说明:图1为本结构自由度示意图。
[0018]
图2为喇叭形接口角度示意图。
[0019]
图3为x向自由度尺寸设计示意图。
[0020]
图4为限位柱结构示意图。
[0021]
图5为螺母结构示意图。
[0022]
图6为y向自由度尺寸设计示意图。
[0023]
图7为卷簧最大压缩位置示意图。
[0024]
图8为z向自由度尺寸设计示意图。
[0025]
图9为α向转动自由度设计示意图。
[0026]
图10是β向转动分析模型。
[0027]
图11是模拟得到的β向转动位移分布图。
[0028]
图12是γ向转动分析模型。
[0029]
图13是模拟得到的γ向转动位移分布图。
[0030]
图14是扁簧的结构示意图。
具体实施方式
[0031]
实施例1:本实施例中连接器的组成结构和现有技术(中国专利cn103633492b)相比仅仅是在限位柱下端的螺母侧面增设了限位钉以抵紧限位柱。罩壳内通过扁簧安装固定板,固定板两端的沉孔中安装卷簧,喇叭形接口的法兰两端安装限位柱,限位柱中段和卷簧配合,限位柱下段连接螺母,螺母侧面有固定钉组装孔,固定钉旋入固定钉组装孔后顶住限位柱。扁簧用于实现x向浮动、β向转动及γ向转动的自动复位,机构内部的卷簧用于实现y向浮动、z向浮动及α向转动的自动复位,由此实现6个方向上的自动复位功能。
[0032]
扁簧预压紧状态下的弹力应高于插头、插座插合时的弹力,才能确保插头、插座先对接到位,继而实现对接超行程的功能,因此,对扁簧需要结合产品插合力进行装配预紧力的设计,在建模设计过程中开展综合应力分析设计合理的安全余量。扁簧顶端的半圆形凸起部分加工为弯曲的圆柱体可以降低浮动时β向的阻力使转动更顺畅。
[0033]
扁簧在对准互插装置中起到支撑插座外壳的作用,在连接器插合过程中,扁簧应能克服插头与插座插合时接触件插合产生的插合力,直至头座外壳对接到位,接触件啮合到位;外壳对接到位后,继续在对接方向上施加插合力将使扁簧受到压缩产生变形,从而实现超行程量的对准差指标。因此,扁簧装配时应具备一个初始变形量x,初始变形产生的反力应大于连接器的最大插合力指标要求。
[0034]
如图1,本连接需要在六个自由度上满足浮动要求:δα≥
±
0.5
°
、δβ≥
±
0.5
°
、δγ≥
±
0.5
°
,δx≥2.29mm、δy≥1.27mm、δz≥2.03mm。为便于产品浮动导向,减少导向过程对壳体的摩擦磨损和减小摩擦反力,满足产品长寿命和自浮动的功能需求,需要同时对导向角度进行合理设计,最佳角度为30
°
(见图2,即喇叭口张角为60
°
)。
[0035]
1)超行程量(δx)设计超行程量(δx)即插座外壳受力相对于罩壳向x反方向后退的最大位移。由本产品的结构可知,其超行程量(δx)由限位柱的长度确定。由图3可知,当限位柱尺寸控制在16.1mm时,在初始状态(扁簧未受压缩)下限位柱距挡块距离为3.1mm,也即插座外壳可向x反方向移动的最大位移,此位移即是互插装置的超行程量,满足产品技术指标要求的δx≥2.29mm。
[0036]
限位柱的结构如图4,分为上中下三段,上端螺纹1与插座外壳安装孔配合固定;中段2与卷簧中心孔配合;下段螺纹3与螺母配合,通过调整螺母旋拧长度调整外壳与螺母间的间隙,要求具有一定间隙保证挡板不被夹紧而可浮动;在初始状态下,限位柱底面4与下方挡块之间有3.4mm距离,也即产品向x向的移动极限为3.4mm,超过超行程量δx=2.29mm的要求。
[0037]
螺母的结构如图5,除了中心用于和限位柱配合的螺孔以外,还在侧面开设了固定钉组装孔,螺母与限位柱调整好位置后将固定钉旋入固定钉组装孔后顶住限位柱。
[0038]
2)y向对准差(δy)设计y向即沿连接器矩形截面长度方向的对准差(δy)与两个因素有关,一个是卷簧自身的浮动距离,另一个是y方向上插座外壳尾端距挡板的距离,该两个距离中的较小者即为y向对准差的大小。y方向上插座外壳尾端距挡板的距离见图8所示,为2.15mm,满足产品技术指标要求的δy≥1.27mm。
[0039]
卷簧的外径和内径根据挡板及限位柱的尺寸给定,若卷簧的厚度设计为0.4mm,根据仿真分析卷簧自身贴紧需移动的距离约为2.7mm。
[0040]
3)z向对准差(δz)设计z向即沿连接器矩形截面宽度方向的对准差(δz)也与两个因素有关,一个是卷簧自身的浮动距离,情况与y向完全相同,另一个则是z方向上插座外壳法兰侧边距罩壳的距离,该两个距离中的较小者即为y向对准差的大小。z方向上插座外壳法兰侧边距罩壳的距离见图7所示,为2.95mm,超过卷簧自身贴紧需移动的2.7mm的距离,也即实际δz=2.7mm,设计尺寸满足产品技术指标要求的δz≥2.03mm。
[0041]
4)α向对准差(δα)设计α向即绕连接器轴线转动的对准差(δα)由卷簧实现,当插座外壳法兰盘的两端分别向z轴的两个方向运动时,则实现α向的转动,α向的转动受到卷簧压缩移动距离的限制,当δx≥2.29mm、δy≥1.27mm、δz≥2.03mm满足时,其简化的运动轨迹见图9所示,当插座法兰盘安装孔的中心只能在图示半径2.7mm的圆内移动,可以看出插座外壳绕x轴(α向)转动的最大角度为9
°
,满足产品技术指标要求的δα≥
±
0.5
°
。
[0042]
5)β向对准差(δβ)设计β向即绕y向(连接器矩形截面长度方向)转动的对准差(δβ)由扁簧实现,当两件扁簧压缩量不一致时则可能形成转动,直到挡板边缘与罩壳内腔接触抵死,建立如图10所示的仿真分析模型,固定外部零件,给挡板中间的轴上加载1n
•
m的转矩,因为整体在转动时需要向下压缩,因此不限制中间部分的上下位移。在满足xyz三轴浮动量的情况下,即在上述尺寸得到满足时,得出最终的位移分布如图11,通过比较得出图中标出两点的位移差0.33mm,而挡板宽度的一半为8.5mm,可以得出转动角度为arcsin(0.33/8.5)=2.2
°
。也即产品实际能达到的β向对准差为δβ=
±
2.2
°
,满足产品技术指标要求的δβ≥
±
0.5
°
。
[0043]
6)γ向对准差(δγ)设计γ向即绕z向(连接器矩形截面宽度方向)转动的对准差(δγ)也由扁簧实现,由于扁簧中部与挡板为圆面接触,挡板则可以在有限位置内发生偏斜,转动极限位置为挡板边缘与罩壳台阶接触抵死。建立如图12所示的仿真分析模型,固定外部零件,给挡板中间的轴上加载1n
•
m的转矩,因为整体在转动时需要向下压缩,因此不限制中间部分的上下位移。在满足xyz三轴浮动量的情况下,即在上述尺寸得到满足时,得出最终的位移分布如图13,极限位置下边线上的位移为1mm左右,挡板长度的一半为35mm,因此可以得出转动角度为arcsin(1/35)=1.6
°
。也即产品实际能达到的γ向对准差为δγ=
±
1.6
°
,满足产品技术指标要求的δγ≥
±
0.5
°
。