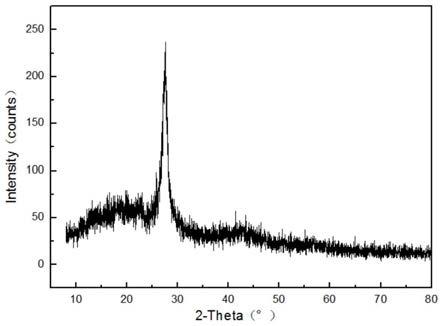
[0001]
本发明涉及一种铅酸蓄电池负极铅膏及负极板的制备方法,属于铅酸蓄电池技术领域。
背景技术:[0002]
随着我国经济的迅猛发展和人民生活水平的提高,汽车保有量越来越高,尤其在城市早晚高峰时,汽车在行驶过程中会经历多次的起动。这导致汽车中的铅酸电池长时间处于未充满电的部分荷电状态,对铅酸电池的使用寿命造成影响。
[0003]
一般来说,铅酸电池主要由正极板、负极板、电解液、隔板和壳体等部分组成。这其中,通过将铅膏涂覆在板栅上制得的极板,对铅酸电池的电学性能起着至关重要的作用。铅酸电池的负极中主要的活性物质是海绵状铅,当电池放电时铅负极作为阳极,单质铅被氧化成pb
2+
,并与电解液中的so
42-发生反应,形成溶解度很小的pbso4,并沉积到负极板中。
[0004]
铅酸电池长期处于未充满电的部分荷电状态时,极易导致负极板中pbso4不断生长成为晶型完整且粗大的晶粒,使得其电化学活性降低,进而导致电池的使用寿命结束。这种现象在行业内被称作为“负极板硫酸盐化”。为了减缓这种现象,一般会在负极中加入各种膨胀剂。目前,常用的负极膨胀剂分为有机膨胀剂和无机膨胀剂两类,有机膨胀剂主要为木素磺酸盐、腐植酸和鞣剂等,其主要目的是为了保证负极活性物质有较大的比表面积;无机膨胀剂主要是炭黑、硫酸钡、硫酸亚锡等,除了保持负极较大的比表面积外,还起到细化硫酸铅晶粒的作用,并在一定程度上提高活性物质的导电性。
[0005]
目前行业上经典的起动型铅酸电池的负极铅膏配方中,除去铅粉、纯水和稀硫酸等基础原材料外,还有短纤维、硫酸钡、木素磺酸钠、腐植酸和炭黑等添加剂。但对铅酸电池当前越加严苛的使用工况下,其负极耐硫酸盐化能力和使用寿命,还需要进一步地提高。
技术实现要素:[0006]
本发明为克服现有技术弊端,提供一种铅酸蓄电池负极铅膏及负极板的制备方法,在负极铅膏的添加剂中添加钡掺杂的氮化碳,有效地抑制了负极的硫酸盐化现象,延长了铅酸蓄电池的使用时间。
[0007]
本发明解决其技术问题所采用的技术方案是:
[0008]
一种铅酸蓄电池负极铅膏,所述负极铅膏包括如下质量添加比的组分,铅粉:短纤维:木素:腐植酸:硫酸钡:钡掺杂氮化碳:碳材料:纯净水:稀硫酸=100:(0.05-0.5):(0-1.0):(0-1.0):(0-2.0):(0.1-1.0):(0-1.0):(10-15):(6-10)。
[0009]
上述铅酸蓄电池负极铅膏,所述钡掺杂氮化碳的主要成分为石墨相氮化碳,钡元素为成核剂,所述钡掺杂氮化碳的平均粒径小于5μm,比表面积为10-500m2/g,其制备方法包括如下步骤:
[0010]
①
称取一定量的ba(oh)2,加入到溶剂中,充分搅拌至完全溶解,得到ba(oh)2溶液,ba(oh)2溶液的浓度为0.01-5wt%;
[0011]
②
称取一定量的三聚氰胺,加入到ba(oh)2溶液中,得到钡掺杂三聚氰胺前躯体混浊液,三聚氰胺与ba(oh)2的质量比控制在100:(0.1-10),对混浊液进行充分搅拌0.1-300min后,静置0.1-12h;
[0012]
③
将静置好的钡掺杂三聚氰胺前躯体混浊液在40-120℃下烘干1-24h,得到钡掺杂三聚氰胺前躯体粉末;
[0013]
④
将得到的钡掺杂三聚氰胺前躯体粉末加热至400-800℃,并保温焙烧0.5-6h,得到钡掺杂氮化碳颗粒;
[0014]
⑤
将得到的钡掺杂氮化碳颗粒进行研磨,得到用于铅酸电池的钡掺杂氮化碳材料。
[0015]
上述铅酸蓄电池负极铅膏,所述步骤
①
中,溶剂为甲醇、乙醇、水中的一种或多种。
[0016]
上述铅酸蓄电池负极铅膏,所述步骤
④
中,焙烧时钡掺杂三聚氰胺前躯体粉末置于带盖的坩埚中,或处于保护气氛下,保护气氛为co2、n2、he和ar中的一种或几种。
[0017]
上述铅酸蓄电池负极铅膏,所述铅粉的氧化度为60-98%,其中pbo和pb的质量比为(60-98):(40-2)。
[0018]
上述铅酸蓄电池负极铅膏,所述短纤维为腈纶纤维、聚酯纤维和聚丙烯腈纤维中的一种或多种,长度为1-15mm。
[0019]
上述铅酸蓄电池负极铅膏,所述纯净水的导电率≤0.33μs/cm,稀硫酸为分析纯,其密度为1.1-1.6g/cm3。
[0020]
上述铅酸蓄电池负极铅膏,所述碳材料为炭黑、活性炭和石墨中的一种或多种。
[0021]
一种负极板的制备方法,利用上述铅酸蓄电池负极铅膏制备负极板,包括如下步骤:
[0022]
①
铅粉、短纤维、木素、腐植酸、硫酸钡、钡掺杂氮化碳、碳材料按100:(0.05-0.5):(0-1.0):(0-1.0):(0-2.0):(0.1-1.0):(0-1.0)的质量比例进行搅拌混合均匀;
[0023]
②
向步骤
①
中得到的混合物中依次加入水和硫酸水溶液,分别充分搅拌1-30min得到铅膏;
[0024]
③
将铅膏平整地刮涂在板栅上,铅膏厚度为0.5-10mm,20-80℃固化1~50h,固化过程中的相对湿度为90-100%,然后50-100℃下干燥0.5-24h,干燥过程中的相对湿度为0-20%,得到负极板。
[0025]
上述负极板的制备方法,所述步骤
②
中得到的负极铅膏的密度为3.5-4.5g/cm3。
[0026]
本发明的有益效果是:
[0027]
本发明负极铅膏中添加有钡掺杂氮化碳添加剂,其有利于避免“负极板硫酸盐化”,起到延长铅酸电池使用寿命的作用。以此制备的蓄电池比普通蓄电池(负极铅膏中未添加钡掺杂氮化碳)具有更高的部分荷电状态循环寿命和静态充电接受能力,例如,在放电容量不降低的情况下,电池的0℃充电接受能力提高4~5%,而连续17.5%循环寿命提高25%以上。
[0028]
本发明钡掺杂氮化碳材料的制备方法,即直接使用三聚氰胺作为碳源和氮源,通过浸渍法使ba元素均匀分布,经过干燥和高温焙烧,一步实现氮化碳中ba元素的掺杂,得到钡掺杂氮化碳材料,避免引入会对铅酸电池造成不良影响的fe、co、ni等元素和cl-、no
3-等离子。制备过程省去了对材料的酸洗、碱洗等工序,减少能耗和水耗,降低成本。
附图说明
[0029]
图1为钡掺杂氮化碳材料的xrd测试图;
[0030]
图2为钡掺杂氮化碳材料的元素分布照片(a为整体电镜照片,b为c元素分布,c为n元素分布,d为ba元素分布);
[0031]
图3为钡掺杂氮化碳材料的edx能谱分析结果。
具体实施方式
[0032]
g-c3n4是一种典型的聚合物半导体,主要存在两种化学结构。一种以三嗪环(c3n3)为结构单元的g-c3n4属于r3m空间群,另一种以3-s-三嗪环(c6n7)为结构单元的g-c3n4属于p6m2空间群。在这两种结构中,c、n原子均发生sp2杂化,通过pz轨道上的孤对电子形成一个类似于苯环结构的大π键,组成一个高度离域的共轭体系。由于g-c3n4独特的电子结构和热力学稳定性,其具有非常合适的半导体带边位置,同时具有优异的耐高温、耐酸碱能力和良好的比表面积,非常适合作为非金属催化剂和金属催化剂与成核剂的载体。
[0033]
本发明铅酸电池负极添加剂中添加的钡掺杂氮化碳,其主要成分为g-c3n4,本发明g-c3n4指石墨相氮化碳,且掺杂有作为硫酸铅成核剂的ba元素,ba元素在硫酸电解液环境中,与电解液中的so
42-发生反应,在g-c3n4表面生成微小的baso4。g-c3n4表面的baso4在铅酸电池负极板发生阳极氧化反应时,可以作为pbso4的成核剂,使pbso4在g-c3n4材料表面分散生长,避免形成过大的pbso4晶粒而降低电化学活性。同时,由于g-c3n4材料本身的催化活性,在铅酸电池负极板发生阴极还原反应时,降低局部还原反应能垒,促进附近游离的pb
2+
还原成pb,进而减缓由于pbso4晶粒本身电化学活性降低带来的反应难度,有利于避免“负极板硫酸盐化”,起到延长铅酸电池使用寿命的作用。
[0034]
下面结合实施例对本发明作进一步说明。
[0035]
本发明利用三聚氰胺作为主要前躯体,经高温固相反应得到的g-c3n4主要为热力学更稳定的以3-s-三嗪环(c6n7)为结构单元的g-c3n4。具体制备过程为:
[0036]
①
称取一定量的ba(oh)2,加入到溶剂中,充分搅拌至完全溶解,得到ba(oh)2溶液,ba(oh)2溶液的浓度为0.01-5wt%;所述溶剂为甲醇、乙醇、水中的一种或多种。
[0037]
②
称取一定量的三聚氰胺,加入到ba(oh)2溶液中,得到钡掺杂三聚氰胺前躯体混浊液,三聚氰胺与ba(oh)2的质量比控制在100:(0.1-10),对混浊液进行充分搅拌0.1-300min后,静置0.1-12h;
[0038]
③
将静置好的钡掺杂三聚氰胺前躯体混浊液在40-120℃下烘干1-24h,得到钡掺杂三聚氰胺前躯体粉末;
[0039]
④
将得到的钡掺杂三聚氰胺前躯体粉末加热至400-800℃,并保温焙烧0.5-6h,得到钡掺杂氮化碳颗粒;焙烧时钡掺杂三聚氰胺前躯体粉末置于带盖的坩埚中,或处于保护气氛下,保护气氛为co2、n2、he和ar中的一种或几种。
[0040]
⑤
将得到的钡掺杂氮化碳颗粒进行研磨,平均粒径小于5μm,得到用于铅酸电池的钡掺杂氮化碳材料。
[0041]
电池负极铅膏中添加制备的钡掺杂氮化碳作为添加剂材料,负极板的制备方法包括如下步骤:
[0042]
①
铅粉、短纤维、木素、腐植酸、硫酸钡、钡掺杂氮化碳、碳材料按100:(0.05-0.5):
(0-1.0):(0-1.0):(0-2.0):(0.1-1.0):(0-1.0)的质量比例进行搅拌混合均匀;
[0043]
②
向步骤
①
中得到的混合物中依次加入水和硫酸水溶液,分别充分搅拌1-30min得到负极铅膏,负极铅膏的密度为3.5-4.5g/cm3;
[0044]
③
将铅膏平整地刮涂在板栅上,铅膏厚度为0.5-10mm,20-80℃固化1~50h,固化过程中的相对湿度为90-100%,然后50-100℃下干燥0.5-24h,干燥过程中的相对湿度为0-20%,得到负极板。
[0045]
本发明负极铅膏中控制钡掺杂氮化碳的添加比,因为,钡掺杂氮化碳材料的主要作用是成核剂和稳定催化剂,若添加比例太小,钡掺杂氮化碳不能在铅膏中均匀有效地分散,起不到延长电池使用寿命的效果;若加入量过大,因氮化碳本身的催化剂属性会导致极板的析气风险增大,同时该材料不作为电化学反应的物质,会导致极板的比能量明显降低。
[0046]
实施例1
[0047]
将1000g氧化度为80%的铅粉、3g的钡掺杂氮化碳添加剂、0.6g长度为3mm的聚酯纤维、2.0g木素磺酸钠、3.0g腐植酸、5.0g精细硫酸钡、2.0g碳材料均匀混合,加入110g纯水和85g密度为1.4g/cm3的稀硫酸,经搅拌得到所需要的负极铅膏,然后按上述方法制成负极板,将负极板与正极板以及pe隔膜配组焊接,经过化成后得到2v12ah的铅酸单体电池,正负极片数为正极3片,负极2片,电池编号为1#,进行20hr、0℃充电接受能力和连续17.5%循环寿命测试。实验结果参见表1。
[0048]
实施例2
[0049]
将1000g氧化度为80%的铅粉、5g的钡掺杂氮化碳添加剂、0.6g长度为3mm的聚酯纤维、2.0g木素磺酸钠、3.0g腐植酸、5.0g精细硫酸钡、2.0g碳材料均匀混合,加入110g纯水和85g密度为1.4g/cm3的稀硫酸,经搅拌得到所需要的负极铅膏,然后按上述方法制成负极板,将负极板与正极板以及pe隔膜配组焊接,经过化成后得到2v12ah的铅酸单体电池,正负极片数为正极3片,负极2片,电池编号为2#,进行20hr、0℃充电接受能力和连续17.5%循环寿命测试。实验结果参见表1。
[0050]
对比例1
[0051]
将1000g氧化度为80%的铅粉、0.6g长度为3mm的聚酯纤维、2.0g木素磺酸钠、3.0g腐植酸、5.0g精细硫酸钡、2.0g碳材料均匀混合,加入110g纯水和85g密度为1.4g/cm3的稀硫酸,经搅拌得到所需要的负极铅膏,然后按上述方法制成负极板,将负极板与正极板以及pe隔膜配组焊接,经过化成后得到2v12ah的铅酸单体电池,正负极片数为正极3片,负极2片,电池编号为3#,进行20hr、0℃充电接受能力和连续17.5%循环寿命测试。实验结果参见表1。
[0052]
表1实施例1、实施例2和对比例1制成的蓄电池性能进行对比
[0053]
电池编号20hr容量(ah)0℃充电接受(a)连续17.5寿命(次)1#12.563.6713162#12.623.6513493#12.553.491077
[0054]
由表1可知,采用本发明负极铅膏配方制作的铅酸蓄电池,在保证放电容量不降低的情况下,0℃充电接受能力提高4-5%,而连续17.5%循环寿命提高25%以上。
[0055]
实施例3
[0056]
称取3.0g的ba(oh)2,加入到100g纯净水中,充分搅拌至完全溶解,得到ba(oh)2溶液。称取10.0g三聚氰胺,加入到ba(oh)2溶液中,得到钡掺杂三聚氰胺前躯体混浊液。对混浊液搅拌10min,静置2h。将静置好的钡掺杂三聚氰胺前躯体混浊液在100℃下烘干24h,得到钡掺杂三聚氰胺前躯体粉末。将得到的钡掺杂三聚氰胺前躯体粉末加热至550℃,并保温焙烧2.0h,得到钡掺杂氮化碳颗粒。焙烧时前躯体粉末置于带盖的坩埚中,并处于co2保护气氛下。将得到的钡掺杂氮化碳颗粒进行研磨成平均粒径小于5μm的粉末,得到用于铅酸电池的钡掺杂氮化碳材料。
[0057]
对得到的钡掺杂氮化碳材料进行xrd、sem、edx观测分析,结果如图1~3所示。图1为钡掺杂氮化碳材料的xrd测试图,其中衍射角为27.7
°
的峰属于g-c3n4芳香环间堆积的(002)晶面的特征峰,其对应的层间距为d=0.323nm,另一个在13.0
°
处的峰对应3-s-三嗪结构的特征峰。可以证明材料中主要为3-s-三嗪结构的的g-c3n4物质,由于ba元素在其中处于分散掺杂,没有出现单独的ba元素特征峰。
[0058]
图2中a为钡掺杂氮化碳材料的sem观测照片,图2中b、c、d分别为c元素、n元素和ba元素的元素分布图。可以看出,材料为微小的粉末固体材料,同时c、n和ba元素均匀地分布在材料中,这也可以进一步证明材料中的ba元素是均匀地分散的。
[0059]
图3为钡掺杂氮化碳材料的edx能谱图及定量计算结果。可以进一步证明元素中含有一定量的ba元素。由于c、n和o元素在空气中大量存在,因此会导致样品表面的能谱结果略微偏高。