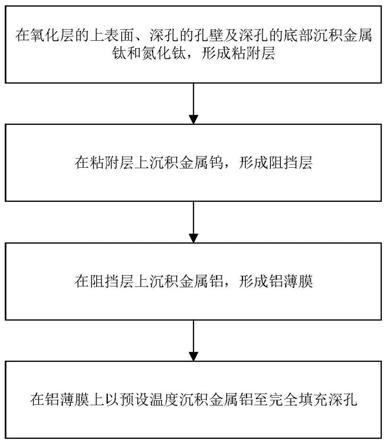
[0001]
本发明涉及半导体制造技术领域,具体地,涉及一种氧化物层中深孔铝的填充方法。
背景技术:[0002]
功率器件是半导体工业界最重要的元器件之一,其为节能减排的基础技术,电力控制核心器件,具有高耐压、大电流和并联应用等特点。绝缘栅双极晶体管(igbt)是功率半导体器件第三次技术革命的代表性产品。图1示出了现有技术中绝缘栅双极型晶体管结构示意图,igbt的元胞结构如图1所示,为金属-氧化物-半导体场效应晶体管(mosfet)和双极晶体管的复合结构,其为一个电压控制的功率开关器件,开关作用是通过加正向栅极电压形成沟道,给pnp(原来为npn)晶体管提供基极电流,使igbt导通。反之,加反向门极电压消除沟道,切断基极电流,使igbt关断。
[0003]
研究表明,薄膜沉积是igbt芯片的关键技术之一,通过低温气相沉积、金属溅射等工艺形成低温氧化层、多晶硅、氮化硅、钛、铝金属层等膜层。铝金属层作为发射极,其质量对器件的性能有显著影响。图2示出了现有技术中绝缘栅双极型晶体管发射极的结构示意图,如图2所示,其中,氧化层2在硅片1上,氧化层2通常为sio2,热铝填充的工艺流程通常是以ti为粘附层3,tin为阻挡层4,然后冷铝5作为仔晶层,最后沉积热铝6。然而,为了提高热铝的深孔填充性能,通常会通过加热基座提高热铝沉积时的温度使热铝具备流动性。但是温度提高会增加热铝的扩散性能,导致热铝极易扩散到其他层内,为防止其扩散,必须增加tin的厚度,而增加tin的厚度会影响接触电阻,影响器件的电学性能。
技术实现要素:[0004]
本发明的目的是提供一种氧化物层中深孔铝的填充方法,能够提高对热铝扩散的阻碍作用。
[0005]
为了实现上述目的,本发明提供一种氧化物层中深孔铝的填充方法备,包括:在所述氧化层的上表面、所述深孔的孔壁及所述深孔的底部沉积金属钛和氮化钛,形成粘附层;
[0006]
在所述粘附层上沉积金属钨,形成阻挡层;
[0007]
在所述阻挡层上沉积金属铝,形成铝薄膜;
[0008]
在所述铝薄膜上以预设温度沉积金属铝至完全填充所述深孔。
[0009]
优选地,所述填充方法还包括:在形成所述阻挡层之后,在所述阻挡层上沉积金属钛,形成润滑层。
[0010]
优选地,所述润滑层采用磁控溅射的方法沉积,沉积所述润滑层的工艺参数为:通入氩气流量范围为0~100sccm,dc功率范围为0~20000w。
[0011]
优选地,所述润滑层的厚度为600a~700a。
[0012]
优选地,所述粘附层采用磁控溅射的方法沉积,所述粘附层包括厚度为600a~700a的金属钛层和厚度为600a~700a的氮化钛层,沉积所述粘附层的工艺参数为:先通入
氩气流量范围为0~100sccm,dc功率范围为0~20000w,沉积所述金属钛层,然后通入氮气流量范围为0~500sccm,dc功率范围为0~20000w,沉积所述氮化钛层。
[0013]
优选地,所述阻挡层采用磁控溅射的方法沉积,所述阻挡层的厚度为600a~800a,沉积所述阻挡层的工艺参数为:通入氩气流量范围为0~100sccm,dc功率范围为0~20000w。
[0014]
优选地,所述铝薄膜在加热基座不施加静电力吸附的条件下,采用磁控溅射的方法沉积,所述铝薄膜的厚度为100a~1200a,沉积所述铝薄膜的工艺参数为:通入氩气流量范围为0~100sccm,dc功率范围为0~30000w。
[0015]
优选地,完全填充所述深孔是在加热基座施加400-800v的静电力吸附的条件下,采用磁控溅射的方法沉积所述金属铝来实现,沉积所述金属铝至完全填充所述深孔的工艺参数为:通入氩气流量范围为0~100sccm,dc功率范围为0~30000w。
[0016]
优选地,所述预设温度大于等于440℃且小于等于540℃。
[0017]
优选地,所述深孔的尺寸为开孔深小于1um,所述深孔的宽大于0.5um,所述深孔的深宽比小于2。
[0018]
本发明具有以下有益技术效果:
[0019]
1、在粘附层沉积金属钨作为阻挡层,可以在阻挡层相对较薄的厚度下,提高对热铝扩散的阻碍作用,同时金属钨的接触电阻率相较于氮化钛低,对铝的电学性能影响较小。
[0020]
2、在形成阻挡层之后,在阻挡层上沉积金属钛作为润滑层,提高了铝的流动性,可在相对较低的温度下填充铝薄膜。
[0021]
本发明的方法具有其它的特性和优点,这些特性和优点从并入本文中的附图和随后的具体实施例中将是显而易见的,或者将在并入本文中的附图和随后的具体实施例中进行详细陈述,这些附图和具体实施例共同用于解释本发明的特定原理。
附图说明
[0022]
通过结合附图对本发明示例性实施例进行更详细的描述,本发明的上述以及其它目的、特征和优势将变得更加明显,其中,在本发明示例性实施例中,相同的参考标号通常代表相同部件。
[0023]
图1示出了现有技术中绝缘栅双极型晶体管结构示意图。
[0024]
图2示出了现有技术中绝缘栅双极型晶体管发射极的结构示意图。
[0025]
图3示出了现有技术中深孔填充的技术路线图。
[0026]
图4示出根据本发明实施例的氧化物层中深孔铝的填充方法的流程图。
[0027]
图5示出根据本发明实施例的粘附层的结构示意图。
[0028]
图6示出根据本发明实施例的阻挡层的结构示意图。
[0029]
图7示出根据本发明实施例的润滑层的结构示意图。
[0030]
图8示出根据本发明实施例的氧化物层中深孔铝填充的结构示意图。
[0031]
图9示出根据本发明实施例的氧化物层中深孔铝填充的扫描式电子显微镜的结构示意图。
[0032]
主要附图标记说明:
[0033]
1、硅片;2、氧化层;3、粘附层;4、阻挡层;5、冷铝;6、热铝;7、粘附层;8、阻挡层;9、
润滑层;10、铝薄膜;11、金属铝。
具体实施方式
[0034]
下面将参照附图更详细地描述本发明。虽然附图中显示了本发明的优选实施例,然而应该理解,可以以各种形式实现本发明而不应被这里阐述的实施例所限制。相反,提供这些实施例是为了使本公开更加透彻和完整,并且能够将本公开的范围完整地传达给本领域的技术人员。
[0035]
图3示出了现有技术中深孔填充的技术路线图。如图3所示,现有技术的igbt中发射极的制备路线可分为以下四步:步骤1:沉积厚度600a左右的金属钛,作为粘附层;步骤2:沉积厚度1000a左右的氮化钛,作为阻挡层,防止热铝扩散;步骤3:沉积冷铝厚度1000a左右作为仔晶层;步骤4:沉积满足器件所需厚度的热铝。
[0036]
上述现有技术中存在以下问题:
[0037]
(1)为提高热铝的流动性,提高加热基座的温度造成成本提高;
[0038]
(2)高温会增加热铝的扩散性能,导致热铝极易扩散到其他层内,影响器件性能;
[0039]
(3)为防止其扩散,必须增加氮化钛的厚度,影响接触电阻,进而影响器件性能。
[0040]
图4示出根据本发明实施例的氧化物层中深孔铝的填充方法的流程图。
[0041]
为解决上述现有技术中存在的问题,本发明实施例的一种氧化物层中深孔铝的填充方法,如图4所示,该方法包括:
[0042]
步骤1:在氧化层的上表面、深孔的孔壁及深孔的底部沉积金属钛和氮化钛,形成粘附层。
[0043]
作为优选方案,粘附层采用磁控溅射的方法沉积,粘附层包括厚度为600a~700a的金属钛层和厚度为600a~700a的氮化钛层。
[0044]
作为一个示例,沉积粘附层的工艺参数为:先通入氩气流量范围为0~100sccm,氩气流量优选为15~35sccm;dc功率范围为0~20000w,dc功率优选为3000~5000w;控制金属钛层的厚度在600a~700a;然后通入氮气流量范围为0~500sccm,氮气流量优选为80~120sccm,dc功率范围为0~20000w,dc功率优选为3000~12000w,控制氮化钛层的厚度在600a~700a。
[0045]
作为一个示例,图5示出根据本发明实施例的粘附层的结构示意图。如图5所示,在硅片1的氧化层2上刻蚀深孔,对氧化层的上表面、深孔的孔壁及深孔的底部采用磁控溅射的方法沉积粘附层7,包括如下工艺步骤,具体工艺参数如表1所示:
[0046]
s1、向腔室通入工作气体;
[0047]
s2、起辉(ignition),腔室加载一定dc功率,例如1000w,将工艺气体电离,产生等离子体;
[0048]
s3、加载高dc功率,例如3000w,吸引氩气正离子轰击靶材,实现金属钛的薄膜沉积;
[0049]
s4、腔室通入工作气体;
[0050]
s5、腔室加载一定dc功率,例如1000w,将工艺气体电离,产生等离子体;
[0051]
s6、加载高dc功率,例如11000w,吸引氩气正离子轰击靶材,实现氮化钛薄膜沉积;
[0052]
s7、关闭所有工艺气体及加载的dc功率,结束步骤。
[0053]
表1为沉积粘附层的工艺参数
[0054]
parameter1234567step namegasignti depgasigntin deppumptime/s1513315118.50.1source dc/w01000300001000110000ar/sccm1815151815150n2/sccm0001101101100gate valvefullfullfullfullfullfullfull
[0055]
步骤2:在粘附层上沉积金属钨,形成阻挡层。
[0056]
金属钨作为阻挡层,可以在相对较薄的厚度下,提高对热铝扩散的阻碍作用,同时金属钨的电阻率较氮化钛低,对金属铝的电学性能影响较小。
[0057]
作为优选方案,阻挡层采用磁控溅射的方法沉积,阻挡层的厚度为600a~800a。
[0058]
沉积阻挡层的工艺参数为:通入氩气流量范围为0~100sccm,优选为45~80sccm,dc功率范围为0~20000w,优选1000~5000w,控制w层的厚度在600a~800a。
[0059]
作为一个示例,图6示出根据本发明实施例的阻挡层的结构示意图。如图6所示,在粘附层7上采用磁控溅射的方法沉积阻挡层8,包括如下工艺步骤,具体工艺参数如表2所示:
[0060]
s1、加静电力,将硅片通过静电吸附在加热基座的陶瓷盘上;
[0061]
s2、向腔室通入工作气体,硅片与陶瓷盘之间通背吹气体;
[0062]
s3、腔室加载一定dc功率,例如500w,将工艺气体电离,产生等离子体;
[0063]
s4、加载高dc功率,例如4000w,吸引氩气正离子轰击靶材,实现金属钨薄膜沉积;
[0064]
s5、关闭所有工艺气体及加载dc功率,结束步骤。
[0065]
表2为沉积阻挡层的工艺参数
[0066]
parameter12345step namechuckgasigndependtime/s2153360.1source dc/w0050040000ar/sccm08045450esc voltage/v8008008008000backside pressure/torr00330backside ar/sccm03.1330gate valvefullfullfullfullfull
[0067]
步骤3:在形成阻挡层之后,在阻挡层上沉积金属钛,形成润滑层,金属钛作为润滑层,可以提高沉积铝薄膜的流动性。
[0068]
作为优选方案,润滑层可以采用磁控溅射的方法沉积,润滑层的厚度为600a~700a。
[0069]
作为一个示例,沉积润滑层的工艺配方为:通入氩气流量范围为0~100sccm,优选为氩气流量15~35sccm;dc功率范围为0~20000w,优选dc功率3000~5000w,控制润滑层金属钛的厚度在600a~700a。
[0070]
作为一个示例,图7示出根据本发明实施例的润滑层的结构示意图。如图7所示,在阻挡层8上采用磁控溅射的方法沉积润滑层9,包括如下工艺步骤,具体工艺参数如表4所示:
[0071]
s1、向腔室通入工作气体;
[0072]
s2、腔室加载一定dc功率,例如1000w,将工艺气体电离,产生等离子体;
[0073]
s3、加载高dc功率,例如3000w,吸引氩气正离子轰击靶材,实现金属钛薄膜沉积;
[0074]
s4、关闭所有工艺气体及加载dc功率,结束步骤。
[0075]
表4为沉积润滑层的工艺参数
[0076]
parameter1234step namegasignti deppumptime/s151330.1source dc/w0100030000ar/sccm1815150n2/sccm0000gate valvefullfullfullfull
[0077]
步骤4:在润滑层上沉积金属铝,形成铝薄膜;在铝薄膜上以预设温度沉积金属铝至完全填充深孔。
[0078]
作为优选方案,铝薄膜在加热基座不施加静电力吸附的条件下,采用磁控溅射的方法沉积。作为一个示例,沉积铝薄膜的工艺参数为:通入氩气流量范围为0~100sccm,优选为氩气流量60~70sccm,优选1000~22000w dc功率范围为0~30000w,优选为dc功率1000~22000w,控制铝薄膜的厚度在100a~1200a。
[0079]
作为优选方案,完全填充所述深孔是在加热基座施加400-800v的静电力吸附的条件下,预设温度大于等于440℃且小于等于540℃,采用磁控溅射的方法沉积金属铝来实现。作为一个示例,沉积金属铝至完全填充深孔的工艺参数为:通入氩气流量范围为0~100sccm,dc功率范围为0~30000w。
[0080]
作为一个示例,图8示出根据本发明实施例的氧化物层中深孔铝填充的结构示意图,图9示出根据本发明实施例的氧化物层中深孔铝填充的扫描式电子显微镜的结构示意图。
[0081]
如图8所示,在润滑层9上采用磁控溅射的方法沉积铝薄膜10和金属铝11至完全填充深孔,包括如下工艺步骤实现单腔室沉积铝薄膜10和金属铝11,具体工艺参数如表5所示:
[0082]
s1、在不加静电力吸附的条件下沉积铝薄膜10,将已沉积润滑层9的晶片传送至工艺腔室放置在440℃的基座上,由于加热基座的陶瓷盘未与晶片接触,未对晶片加热,反应腔室在室温下通入工作气体;
[0083]
s2、腔室加载一定dc功率,例如1000w,将工艺气体电离,产生等离子体;
[0084]
s3、加载高dc功率,例如1000w,吸引氩气正离子轰击靶材,实现铝薄膜10沉积;
[0085]
s4、加静电力,将硅片1通过加热基座的静电吸附在陶瓷盘上,预设温度为440℃;
[0086]
s5、腔室通入工作气体,硅片1与陶瓷盘之间通入背吹气体;
[0087]
s6、腔室加载一定dc功率,例如1000w,将工艺气体电离,产生等离子体;
[0088]
s7、加载高dc功率,例如1000w,吸引氩气正离子轰击靶材,实现金属铝薄膜沉积;
[0089]
s8、停止加载功率,减少等离子体带来的热量累积;
[0090]
s9、重复s6至s8,循环3次,直至金属铝11达到所需求的厚度。
[0091]
s10、关闭所有工艺气体及加载功率,结束步骤。
[0092]
表5为沉积润滑层的工艺参数
[0093]
parameter123456789[6-8:3]18step namegasigndepchuckgasigndepcooldependtime/s15120021513003000.1source dc/w0100010000010001000000ar/sccm656565656565656500esc voltage/v00080080080080080000backside pressure/torr0000033300backside ar/sccm0000333300gate valvefullfullfullfullfullfullfullfullfullfull
[0094]
本发明的实施例获得的深孔铝填充的效果,如图9所示,在深1um、上开口0.5um和下开口0.25um的孔中填充的薄膜堆叠,至深孔完全填充,不存在孔洞,填充率高约95%,在阻挡层上沉积金属钛,提高了铝的流动性,可在相对较低的温度下填充铝薄膜,采用金属钨作为阻挡层,使沉积的金属铝在其它膜层和氧化物层没有扩散。
[0095]
以上已经描述了本发明的各实施例,上述说明是示例性的,并非穷尽性的,并且也不限于所披露的各实施例。在不偏离所说明的各实施例的范围和精神的情况下,对于本技术领域的普通技术人员来说许多修改和变更都是显而易见的。本文中所用术语的选择,旨在最好地解释各实施例的原理、实际应用或对市场中的技术的改进,或者使本技术领域的其它普通技术人员能理解本文披露的各实施例。