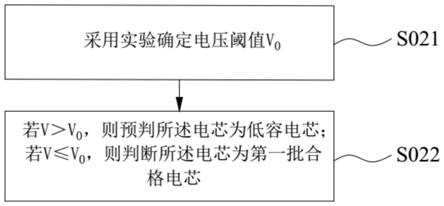
[0001]
本发明涉及锂离子电池制造技术领域,尤其涉及一种锂离子电池生产工艺。
背景技术:[0002]
锂离子电池以其能量密度高、使用寿命长、额定电压高、自放电率低及功率性能好等优点,作为一种重要的能源储存系统,广泛的应用于消费数码、储能系统、车船用动力等多个领域,随着市场竞争加剧,行业集中度提升,市场不断的提出降低锂离子电池制造成本的要求,对于锂离子电池生产企业而言,主要从材料端、制造端两方面进行调整。针对消费数码电池生产商而言,由于电池容量相对较小,电池制造过程的人工、设备成本相对较高,因此降低电池的工艺周期对于锂电池生产商有较大的意义。
[0003]
常规锂电池生产流程中的分容工序主要为电池容量的检测工序,本身对电池性能无影响,因制程中存在各种工序能力的波动、不良等,低容量比率一般<10%,为了避免低容量产品流出至客户,都会进行容量测试,但弊端就是增加了工艺周期、上下柜的生产周期及分容设备。
[0004]
因此,亟需一种缩短锂离子电池生产周期的锂离子电池生产工艺,以解决现有技术中存在的上述技术问题。
技术实现要素:[0005]
本发明的目的在于提出一种锂离子电池生产工艺,该锂离子电池生产工艺能够有效缩短锂离子电池生产周期,提升生产效率,降低制造成本。
[0006]
为达此目的,本发明采用以下技术方案:
[0007]
一种锂离子电池生产工艺,包括化成工序,所述化成工序包括以下流程:
[0008]
s01,采用0.01c~1.0c之间的恒流电流对多个电芯充电,充电时间为t0,充电完成后的soc位于30%~50%之间;
[0009]
s02,采用0.2c~1.0c之间的恒流电流对所述s01中的多个所述电芯充电,充电时间为t1,soc增加10%~50%,放置0~10min,记录多个所述电芯的电压值为v;
[0010]
s021,采用实验确定电压阈值v0;
[0011]
s022,若v>v0,则预判所述电芯为低容电芯;若v≤v0,则判断所述电芯为第一批合格电芯。
[0012]
作为一种锂离子电池生产工艺的优选技术方案,采用实验确定电压阈值v0的方法为:
[0013]
从所述s02中的多个所述电芯中随机取出部分所述电芯并进行分容,确定部分所述电芯的电压值为v所对应的容量值并记为cap;
[0014]
取容量标准下限为cap
spec
,设k为容量的富余量系数,设cap
min
=cap
spec
*(1+k),在cap<cap
min
的部分所述电芯中取找出最大电压即为v0。
[0015]
作为一种锂离子电池生产工艺的优选技术方案,所述容量的富余量系数k的取值
区间为1%~10%。
[0016]
作为一种锂离子电池生产工艺的优选技术方案,所述化成工序还包括以下流程:
[0017]
s03,采用0.2c~1.0c之间的恒流恒压电流对所述s02中的多个所述电芯充电至截止电压。
[0018]
作为一种锂离子电池生产工艺的优选技术方案,所述锂离子电池生产工艺还包括注液及静置工序,经过所述注液及静止工序后的电芯,进入所述化成工序。
[0019]
作为一种锂离子电池生产工艺的优选技术方案,所述锂离子电池生产工艺还包括标识工序,对所述s03中的所述第一批合格电芯及所述低容电芯进行区分标识。
[0020]
作为一种锂离子电池生产工艺的优选技术方案,所述锂离子电池生产工艺还包括抽气、封口工序,对完成所述标识工序的所述第一批合格电芯及所述低容电芯进行抽气、封口。
[0021]
作为一种锂离子电池生产工艺的优选技术方案,所述锂离子电池生产工艺还包括分容复测工序,所述分容复测工序用于对完成所述抽气、封口的所述低容电芯进行分容,确定第二批合格电芯。
[0022]
作为一种锂离子电池生产工艺的优选技术方案,所述锂离子电池生产工艺还包括老化工序,所述老化工序用于对所述第一批合格电芯和所述第二批合格电芯进行常规老化。
[0023]
作为一种锂离子电池生产工艺的优选技术方案,所述s01中的所述恒流电流充电过程可采用一步式恒流充电或者阶梯式充电。
[0024]
本发明提供了一种锂离子电池生产工艺,该锂离子电池生产工艺包括化成工序,通过在化成工序中的s02中,采用实验确定电压阈值v0,判断v与v0的关系,如果v≤v0,则判断这部分电芯为第一批合格电芯,这部分电芯可以免分容,从而减少了后续需分容的电芯的数量,进而缩短了分容的时间,从而缩短了电池生产周期,提升生产效率,降低了制造成本。
附图说明
[0025]
图1是本发明具体实施方式提供的锂离子电池生产工艺的流程图;
[0026]
图2是本发明具体实施方式提供的化成工序的流程图;
[0027]
图3是本发明具体实施方式提供的化成工序中容量预判的流程图;
[0028]
图4是本发明具体实施方式提供的分容容量与化成电压的关系图。
具体实施方式
[0029]
为使本发明解决的技术问题、采用的技术方案和达到的技术效果更加清楚,下面结合附图并通过具体实施方式来进一步说明本发明的技术方案。
[0030]
在本发明的描述中,除非另有明确的规定和限定,术语“相连”、“连接”、“固定”应做广义理解,例如,可以是固定连接,也可以是可拆卸连接,或成一体;可以是机械连接,也可以是电连接;可以是直接相连,也可以通过中间媒介间接相连,可以是两个元件内部的连通或两个元件的相互作用关系。对于本领域的普通技术人员而言,可以具体情况理解上述术语在本发明中的具体含义。
[0031]
在本发明中,除非另有明确的规定和限定,第一特征在第二特征之“上”或之“下”可以包括第一和第二特征直接接触,也可以包括第一和第二特征不是直接接触而是通过它们之间的另外的特征接触。而且,第一特征在第二特征“之上”、“上方”和“上面”包括第一特征在第二特征正上方和斜上方,或仅仅表示第一特征水平高度高于第二特征。第一特征在第二特征“之下”、“下方”和“下面”包括第一特征在第二特征正下方和斜下方,或仅仅表示第一特征水平高度小于第二特征。
[0032]
在本实施例的描述中,术语“上”、“下”、“左”、“右”等方位或位置关系为基于附图所示的方位或位置关系,仅是为了便于描述和简化操作,而不是指示或暗示所指的装置或元件必须具有特定的方位、以特定的方位构造和操作,因此不能理解为对本发明的限制。此外,术语“第一”、“第二”仅仅用于在描述上加以区分,并没有特殊的含义。
[0033]
如图2和图3所示,本实施例提供了一种锂离子电池生产工艺,该锂离子电池生产工艺包括化成工序,化成工序包括以下流程:s01,采用0.01c~1.0c之间的恒流电流对多个电芯充电,充电时间为t0,充电完成后的soc(state of charge,荷电状态)位于30%~50%之间,保证所有电芯此部分的充电容量相同;s02,采用0.2c~1.0c之间的恒流电流对s01中的多个电芯充电,充电时间为t1,soc增加10%~50%,放置0~10min,记录多个电芯的电压值为v,该电压值v用于电芯容量预判;s021,采用实验确定电压阈值v0;s022,若v>v0,则预判电芯为低容电芯;若v≤v0,则判断电芯为第一批合格电芯。
[0034]
通过在化成工序中的s02中,采用实验确定电压阈值v0,判断v与v0的关系,如果v≤v0,则判断这部分电芯为第一批合格电芯,这部分电芯可以免分容,从而减少了后续需分容的电芯的数量,进而缩短了分容的时间,从而缩短了电池生产周期,提升生产效率,降低了制造成本。
[0035]
优选地,s01中的恒流电流充电过程可采用一步式恒流充电或者阶梯式充电,例如:阶梯式充电可为:i1ma充电时间为t1、i2ma充电时间为t2、i3ma充电时间t3,必须确保每步均为恒流充电,并以时间截止,每次充电之间设置搁置工序,搁置时间可根据操作经验选择。
[0036]
采用实验确定电压阈值v0的方法为:从s02中的多个电芯中随机取出部分电芯并进行分容,确定部分电芯的电压值为v所对应的容量值并记为cap;取容量标准下限为cap
spec
,设k为容量的富余量系数,设cap
min
=cap
spec
*(1+k),在cap<cap
min
的部分电芯中取找出最大电压即为v0。优选地,容量的富余量系数k的取值区间为1%~10%。实验确定电压阈值v0过程需要对s02中的多个电芯中随机取出部分电芯并进行分容,也就是仅需要少量的电芯分容得到v0,从而在后续的电池生产过程,分成工序中的s02中能够完成电容预判,大批量电池就不需要进行分容了。
[0037]
进一步需要说明的是:锂电池一般用soc衡量其充电态,其等于充电容量/单个电池总容量,如对于3.0v-4.2v体系电池来说,100%soc表示电池已满电即电压为4.2v,0%soc为空电态即电压为3.0v,soc越高对应的电压就越高,在化成工序中s01和s02中的所有电池充电容量都是一样,根据soc计算公式,当该电池总容量偏低时对应的soc上升,电压也会升高,依据此原理可以建立电压与容量的对应关系进而可完成s021和s022中对电池的容量预判。
[0038]
基于上述锂离子电池生产工艺的化成工序,为便于理解,本实施例举例如下:
[0039]
化成工序包括以下流程:s01,采用0.2c之间的恒流电流对多个电芯充电,充电时间为t0=90min(soc累积30%);s02,采用1.0c之间的恒流电流对s01中的多个电芯充电,充电时间为t1=10min(soc增加10%),放置0~10min,记录多个电芯的电压值为v(分布在3.7-3.9v),该电压值v用于电芯容量预判;s021,采用实验确定电压阈值v0=3.8842v;s022,若v>v0,则预判电芯为低容电芯;若v≤v0,则判断电芯为第一批合格电芯。
[0040]
通过在化成工序中的s02中,采用实验确定电压阈值v0,判断v与v0的关系,如果v≤v0,则判断这部分电芯为第一批合格电芯,这部分电芯可以免分容,从而减少了后续需分容的电芯的数量,进而缩短了分容的时间,从而缩短了电池生产周期,提升生产效率,降低了制造成本。
[0041]
优选地,s01中的恒流电流充电过程除上述实例外也可采用者阶梯式充电,如
①
0.1c恒流充120min(累积soc20%),放置5min,
②
0.2c恒流充60min(累积soc40%),放置5min。
[0042]
采用实验确定电压阈值v0的方法为:从s02中的多个电芯中随机取出部分电芯并进行分容,确定部分电芯的电压值为v所对应的容量值并记为cap(分布在2040-2180mah),并作分容容量cap与化成电压v之间的关系图,如图4所示;取容量标准下限为cap
spec
=2020mah,设k=1.485%为容量的富余量系数,设cap
min
=cap
spec
*(1+k)=2050mah,在cap<cap
min
的部分电芯中取找出最大电压即为v0=3.8842v。实验确定电压阈值v0过程需要在该型号电池首次生产时验证得出v0,后续生产中不再需要验证v0,例如,型号18650生产约100,000pcs数量,在首次生产时取出500pcs数量电芯进行分容实验,验证出v0,在余下的99500pcs订单或其他订单生产过程中无需进行分容,只需要用v0进行预判即可完成容量合格与否的分选。
[0043]
如图2所示,化成工序还包括以下流程:s03,采用0.2c~1.0c之间的恒流恒压电流对s02中的多个电芯充电至截止电压,以便于后续对s02中的低容电芯进行分容复测工序。其中,需要说明的是,截止电压指的是:化成过程即是成膜添加剂在活性物质颗粒表面形成sei膜(solid electrolyte interface,固体电解质界面膜)的过程,而形成sei膜的过程是不可逆反应过程,因此仅需要将化成截止电压设定在成膜添加剂完全反应完全的电位之上,使得成膜反应充分进行即可。优选地,在本实施例中,截止电压的具体值与传统分容工序的截止电压保持一致。
[0044]
如图1所示,锂离子电池生产工艺还包括注液及静置工序,经过注液及静止工序后的电芯,进入化成工序。
[0045]
如图1所示,锂离子电池生产工艺还包括标识工序,对s03中的第一批合格电芯及低容电芯进行区分标识,以便于操作人员能够筛选出第一批合格电芯,这批电芯可以免去后续的分容复测工序,从而缩短锂离子电池生产周期,提高生产效率,降低制造成本。
[0046]
如图1所示,锂离子电池生产工艺还包括抽气、封口工序,对完成标识工序的第一批合格电芯及低容电芯进行抽气、封口。抽气、封口工序是现有技术中较为成熟的技术,在此不再赘述。
[0047]
如图1所示,锂离子电池生产工艺还包括分容复测工序,分容复测工序用于对完成抽气、封口的低容电芯进行分容,确定第二批合格电芯。此分容复测工序与传统的锂离子电池生产工艺中的分容工序相同,具体操作方式在此不再赘述。
[0048]
锂离子电池生产工艺还包括老化工序,老化工序用于对第一批合格电芯和第二批合格电芯进行常规老化。此老化工序与传统的锂离子电池生产工艺中的老化工序相同,具体操作方式在此不再赘述。
[0049]
综上,采用本实施例中的锂离子电池生产工艺,可实现90%~100%的电池免分容,缩短了工艺及生产周期,针对0~10%的不良电芯,通过分容复测工序也避免了出现标准过严,导致电芯报废率高的问题,通过免分容降低了电池的制造成本。
[0050]
以上内容仅为本发明的较佳实施例,对于本领域的普通技术人员,依据本发明的思想,在具体实施方式及应用范围上均会有改变之处,本说明书内容不应理解为对本发明的限制。